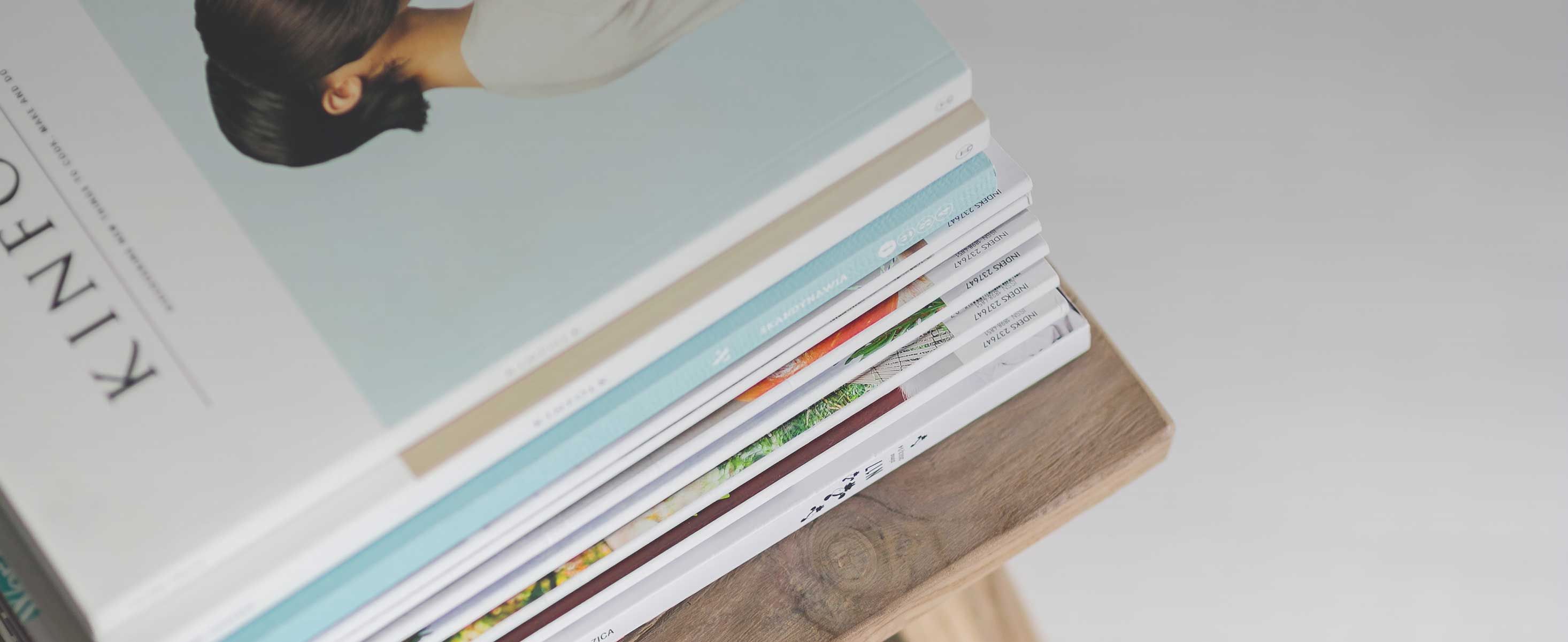
10 minute read
Insect Production Systems
TABLE 4.2 Key Factors Associated with the Costs of Small-Scale
and Commercial Insect Production Systems
Small-scale, rural production Commercial production
• substrate availability • labor cost • infrastructure costs • Quality and accessibility of roads and other transport infrastructure • transport costs • Fuel costs • substrate availability • Quality of transport infrastructure • transport costs • Fuel costs • Cost, availability, and quality of electricity • labor cost
Source: Original table for this publication.
significant of these factors are identified in table 4.2 and described in the following subsections.
Large-scale, commercial insect farming can exist in parallel with smallscale insect farming. For example, some small-scale farmers can farm for their own home or farm use or sell in local markets, while others could join producer groups, including as subcontractors, that act as commercial enterprises and compete with larger producers in broader markets. Some farmers may even choose to do both at the same time. The research team found examples of this with cricket farming in Thailand and mealworm farming in Korea. In other cases, a large commercial BSFL processor may outsource production to small farms in rural areas. Either way, this is not taking over a small-scale operation—it is outsourcing. When large-scale producers move into areas of more artisanal producers, the small-scale farmers may lose competitive access to local markets but could still produce to meet their own home or onfarm livestock needs. That said, even within the same country or local area, there may be different markets for farmed insects to which both large-scale and small-scale producers can cater. In Nairobi, Kenya, for example, there are farms around the capital that cater to BSF markets since these areas have access to food processors, waste resources, and feed companies. In rural Kenya, by contrast, small-scale cricket farming is more common as it can cater to the local market.
Small-Scale Rural Insect Production Substrate Availability
Most existing insect farms are small-scale with costs determined by substrate availability. Of the farms reached by the farm-level survey, 76 percent are characterized as “small-scale,” 20 percent are “medium-scale,” and 4 percent are “large-scale.”3 This is aligned with the World Bank team’s observation from field visits that the African insect sector comprises many small producers. A
Kenyan insect farmer described this: “The crickets consume very little water and food and require a small amount of space for rearing and hence I can do it in my house.” For insects that require particular substrates to feed on, certain locations may have comparative advantages if the substrate is locally available. However, this is not true for many insects—such as crickets, BSF, and the common housefly—that consume a broader range of substrates, offering flexibility to small-scale producers.
Technology and Other Infrastructure
Small-scale insect farming infrastructure is limited in size, does not require climate control, and may require only an open pen or crate. The basic infrastructure needed for insect farming is an insect containment structure, which varies in size and sophistication depending on the farmer’s needs, the production system’s scale, and the insect species being farmed. The most common types of containment structures are a crate system (20 percent), in which containers are vertically stacked on top of one another, and open pens (30 percent), which are not stacked. Forty-seven percent of farms use some other kind of containment structure and 3 percent use multiple structures. According to the farm-level survey, only 4 percent of farms are fully contained and climate controlled, while 53 percent are without climate control. Another 39 percent of farms are operated under open air, while 4 percent use “another” form of housing. So far, small farms have not incorporated digital technologies.
Labor
Small-scale insect farming is low-tech and requires a limited amount of labor and processing to add value to farmed insects. According to the farm-level survey, insect farms in Africa tend to be low-tech and operated almost entirely by manual labor (97 percent). Only 3 percent of the surveyed farms had automated components, and none was fully automated. The survey found very few farms that process the insects, with only 6 percent drying the insects, 2 percent boiling them, and 1 percent grinding them. The other 91 percent of farms sell fresh, unprocessed insects. This limited processing reduces labor requirements. Several African farmers repeated this point. A male farmer from Rwanda said, “[Insect] farming requires much less work than other types of farming.” A female farmer from Madagascar said, “There is no need for male labor, I can do all the activities myself,” while another said, “Insect farming covers the needs of my family while leaving time to do other social responsibilities and obligations.”
Commercial Insect Production Local Substrate Availability
There are substantial cost implications if substrates must be imported, particularly for countries without internal resources. For example, if
Zimbabwe—a landlocked country with limited local substrate resources— sourced substrates from overseas, the shipment would have to transit through Durban, South Africa. The cost of transporting goods from Durban to Harare is US$0.14/kilometer-ton. This high transportation cost would account for 55 to 65 percent of the substrate’s value, making import costs prohibitively high. There are some local substrate options, but these are often used for other industries. For example, brewery waste can be used as a locally sourced substrate for BSFL. However, the livestock industry uses this waste to produce livestock feed. The number and variety of potential waste products is reduced if insect producers plan to export insect products to the European Union or the United States, where strict substrate requirements are in place. Even so, most insects have particular dietary needs and so rely on limited types of substrates. For example, the mopane worm feeds only on mopane tree leaves.
Connectivity
Poor-quality roads and low connectivity from producers to consumers can slow the advancement of any industry, including the farmed insect industry. Poor-quality roads and transport infrastructure are chronic problems throughout much of Africa, particularly in African FCV countries. Infrastructure inefficiencies and their impacts vary among Africa’s regions. However, according to a World Bank study, rehabilitating roads in East Africa’s transport corridor from fair to good would reduce transport costs by 15 percent and transport prices by up to 10 percent (Teravaninthorn and Raballand 2009). In Southern Africa’s transport corridor, rehabilitation would reduce costs by up to 5 percent and prices by up to 3 percent. In corridors in West and Central Africa, rehabilitation would reduce costs by 5 percent but, because of strongly regulated markets, would not affect transport prices. Thus, the development of insect supply chains and market linkages will be defined by the costs associated with reaching potential markets. In many African FCV countries, the supply chain and market reach of commercial insect producers are expected to be limited. In Zimbabwe, for example, 68 percent of the population lives in rural areas, which are also where most insects and insect-based products are consumed. Given the poor quality of road and transport infrastructure in these areas, certain analyses could inform commercial insect producers about which factors are under their control and define the economic viability of selling insects to rural markets.
Transport and Fuel
Transportation and fuel costs will determine, in part, how supply chains for commercially produced insects and insect products will develop. In most African FCV countries, the availability and quality of transport logistics support are limited and expensive. This is because of the lack of transport options, which diminishes competition; high operating costs associated with the lack
of spare parts to repair and maintain vehicles; high fuel costs, particularly in landlocked states; and poor road conditions. The World Bank compared trucking costs in the European Union and several other countries against those in four African trade corridors. The average cost per kilometer-ton was 2 cents in Pakistan, 3.5 cents in Brazil, 5 cents in the United States and China, and 7 cents in Europe. By contrast, the average costs per kilometer-ton in the four African transport corridors were 6 cents in the Durban-Lusaka corridor, 7 cents in Lomé-Ouagadougou, 8 cents in Mombasa-Kampala, and 11 cents in Douala-N’Djamena (Teravaninthorn and Raballand 2009). Costs associated with transporting substrates to production facilities are an important consideration when developing a production system. These costs include the cost of transport and the acquisition cost of substrates. This is particularly true if the insects bred have specific dietary needs. For example, commercially producing mopane caterpillars may not be economically feasible if mopane trees are not within a reasonable proximity.
Energy
Commercial insect and insect product production requires a reliable energy source. This is necessary for lighting and climate control systems and processing, such as drying or milling. In many African FCV countries, expensive and unreliable electricity is an ongoing challenge, making backup generators necessary to maintain uninterrupted production. However, fuel-generated electricity costs are approximately three times that of on-grid electricity. In Zimbabwe, for example, the cost of on-grid electricity for a commercial operation is approximately US$0.05/kilowatt-hour compared with US$0.15/kilowatt-hour from a diesel generator. A commercial producer would also need to account for the cost of generator repairs and maintenance, which can be costly for imported generators with foreign parts. Renewable energy sources may provide economically viable alternatives to fuel-powered generators for off-grid electricity generation given the relatively low energy requirements, predominantly for lighting, for small-scale insect breeding. Agricultural systems are increasingly using solar photovoltaics (PV), or solar panels. Solar PV is competitive for offgrid or mini-grid applications where the main alternative is diesel or gasoline generators (IEA 2014). A small rooftop panel could generate enough electricity to power the few energy-efficient light bulbs necessary for insects. Micro-hydro power generation may be even less capital intensive than solar PV if the insect breeding system is situated near a source of consistently flowing water, like a river. Hydropower also has the advantage of being a 24-hour, 365-day power source, assuming the water flow is not seasonal (Sims et al. 2015).
Labor
Industrial-scale production of edible insects and insect products can be labor intensive and requires new skills. For example, 75 percent of cricket farming costs are for labor (Lynley 2018). Animal protein production was optimized
long ago, but the insect sector has not benefited from similar advances. Insect farming is a nascent field, so the technology is still developing. As such, many commercial producers hope to transition to automated production systems to produce insects efficiently without an expensive labor force. Moreover, the edible insect industry’s labor force requires new skills. According to the International Platform of Insects for Food and Feed, insect production requires knowledge of (1) insect behavior, (2) food and feed safety principles, (3) insect species, (4) farmed insect life cycles, and (5) insect handling and measures to prevent them from escaping (IPIFF 2019). In addition to these insect farming skills, a wide range of other skills are related to edible insects. For example, culinary academies, chefs in training, and other members of the hospitality industry must learn how to use insects to prepare tasty and nutritious meals. A study of aspiring chefs found that 86 percent were moderately or highly likely to use insects for dishes after undergoing a four-hour informational and tasting session (Halloran and Flore 2018).
Costs
Specialized insect production systems are more cost-effective than integrated, or generalized, systems. In a fully integrated insect production system, a single producer carries out all the steps in the insect production process. For example, the producer is responsible for acquiring substrates, producing and processing the insects, and marketing the final product. In a specialized system, specialists carry out the steps separately. For example, the producer is responsible for rearing insects, but a third party would acquire substrates. Commercial production systems are likely to be specialized systems, whereas small-scale, rural production systems are likely to be fully integrated. The cost per unit of production in integrated systems is expected to be higher than the cost per unit in a specialized system. These costs are largely determined by the system’s access to capital, information, and technology and equipment. In rural areas, particularly in African FCV countries, access to these inputs is limited; therefore, the unit cost of production is expected to remain high until the industry grows and matures, compared with large-scale, commercial production systems, which are expected to have access to all the factors of production and marketing. Figure 4.6 shows how unit costs fall as a production system becomes more specialized.
Small-scale, manually managed insect farms require minimal infrastructure. The main investment is for the insect containment structure. These can be simple like those of rural cricket farms in Thailand and, more recently, Kenya; farmers can easily contain crickets by surrounding them with tile and plastic walls or other slippery barriers that the crickets cannot pass. The farm infrastructure—which includes pens, roofs, and walls—can be a major investment. These costs depend on labor expenses and the types of materials used for the structures. For example, the crate used to contain BSFL can be any shallow container that is easy to handle and clean and stacks on other containers to save space. Larger-scale farms require greater investment to