
5 minute read
Considerations When Picking Your Airplane’s Base
Beyond the obvious decisions over hangarage, ground services, physical location and FBOs, what are some more subtle considerations aircraft owners and operators should weigh up in choosing a home airfield to base their airplane? Dave Higdon explores…
The operator had been happily based at an airport located a very convenient 20-minute drive from the company’s headquarters, helping to ensure key personnel could be flown quickly and efficiently to visit clients and prospects all around the United States in the Super Mid-Size Jet that had recently been acquired.
Advertisement
Fuel costs were competitive, and a friendly team at the onfield Fixed Base Operation were both capable and efficient. Nothing seemed to be too much trouble.
Operations seemed to run seamlessly for a while… until the day the jet had its first breakdown and the local maintenance shop seemed unequipped to identify the faulty part, replace it, and get it back in the air as quickly as the company needed.
Well-respected, and vastly experienced in many aircraft makes and models, that experience didn’t seem to be so deep when applied to the make/model of the company’s broken-down Super Mid-Size Jet. As the time and costs to fix the problem started to mount, a dream relationship with the local airport began to sour.
This example highlights how an operator must ensure their research of potential airfields is extensive, stretching beyond the obvious questions about the available facilities, and touches upon several 'What if?' scenarios.
While far from comprehensive, the following are just a few examples of areas requiring deeper thought to ensure you receive the service and support you need for your aircraft operations from a home-base airfield…
Maintenance Needs
While many airports enjoy the convenience of an on-field maintenance provider, not all maintenance shops are created equal – and this needs to be a consideration when thinking about where to base the aircraft.
For example, larger, more experienced shops may offer an Airframe and Powerplant (A&P) mechanic who holds an Inspection Authorization (IA). A&P mechanics who hold IAs are permitted to inspect and approve aircraft and parts for return to service following a major repair or alteration, and they may also perform annual and progressive inspections.
One operator I know suffered a breakdown during the preflight inspection one afternoon when they planned to fly the airplane home. An overnight package service delivered the needed part early the next morning, but the A&P/IA had to
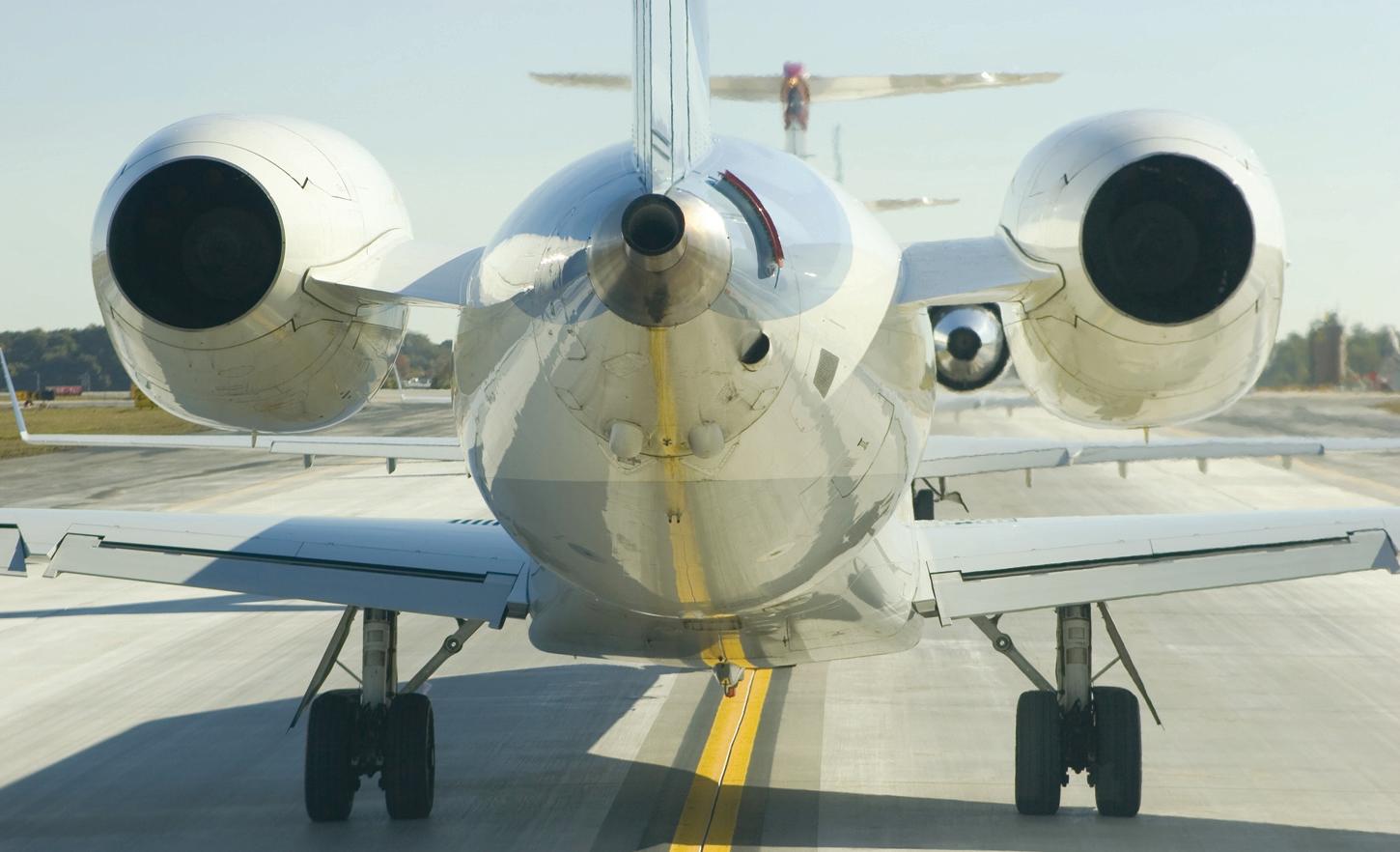
come from 150 nautical miles away, which the A&P/IA flew himself.
The A&P/IA had the new part installed, calibrated, tested and test-flown before lunch, and, having accompanied the A&P/IA on the post-maintenance flight check, the operator was airborne and en route home right after lunch.
Having quick access to an A&P/IA is certainly fortunate for the operator who is unlucky enough to suffer a breakdown. Thus, the proximity of an A&P/IA is one of the factors to consider when an operator weighs where to base the aircraft.
Moving out of Necessity
It’s not exactly breaking news that many businesses are shortstaffed within Business Aviation. With skilled workers highly sought-after, it can be a struggle for an MRO shop to retain its most valued and experienced staff members.
Keep a close eye on the situation at your local MRO shop, since such staffing challenges may occasionally take an aircraft maintenance shop to below the level needed to meet its business and regulatory minima. At the very least, loss of core personnel can lead to inefficiencies and longer leadtimes in getting work completed, or even a drop-off in the quality of work produced, which can become problematic for the operator.
What's an operator to do when their local maintenance shop and its team leave the field, or if the level of maintenance provided on their home field leads to dissatisfaction at the standard of maintenance or more days on the ground than necessary?
Most likely, it’s time to look elsewhere, either outsourcing maintenance to another shop at another field, or relocating the aircraft altogether.
Runway Needs
If maintenance isn’t the driving factor in electing where to base a business aircraft, runway capabilities certainly will be. In fact, for operators flying under Part 135 especially, runway length can be a deal-breaker if it can’t facilitate the accelerate/stop requirements for the aircraft.
The aircraft OEM can help operators determine whether its aircraft and a particular runway can meet those factors. Of course, bad-weather operations must factor in this decision. Weather Factors
And, speaking of runways and weather, for many years an ILS was a significant factor in attracting operators to suitably equipped airports. Automatic Dependent SurveillanceBroadcast (ADS-B) has helped expand the number of runway ends that offer precision approach capabilities – all thanks to the dominance of WAAS GPS navigators predominantly used to inform the ADS-B system of position, altitude, ground speed, and more.
While there is other equipment than WAAS GPS that is capable of meeting the FAA’s requirements for position, speed, altitude, and flight vector, the most cost-effective, with the most use, is WAAS GPS.
While access to precision runway approach is getting better and more plentiful, there is a flip side to this coin. The FAA is shutting down scores of ILS systems as WAAS approaches grow in number, which raises the prospect of an operator moving because that ILS is the only precisionapproach system installed in the aircraft, and the cost of upgrading can be significant.
In Summary…
The above paragraphs are just a representative sample of multiple less-obvious factors business aircraft owners and operators must consider when making sure an airport is right for their operation – and that it continues to be for the duration of their tenure.
Remember, every aircraft owner’s requirements will be unique. What’s right for the operator next door may not be right for you. Spend time working through all your needs, and all of the possibilities. It’s the only way to make sure the support you receive to optimize your business tool is everything you need it to be. ❚
DAVE HIGDON