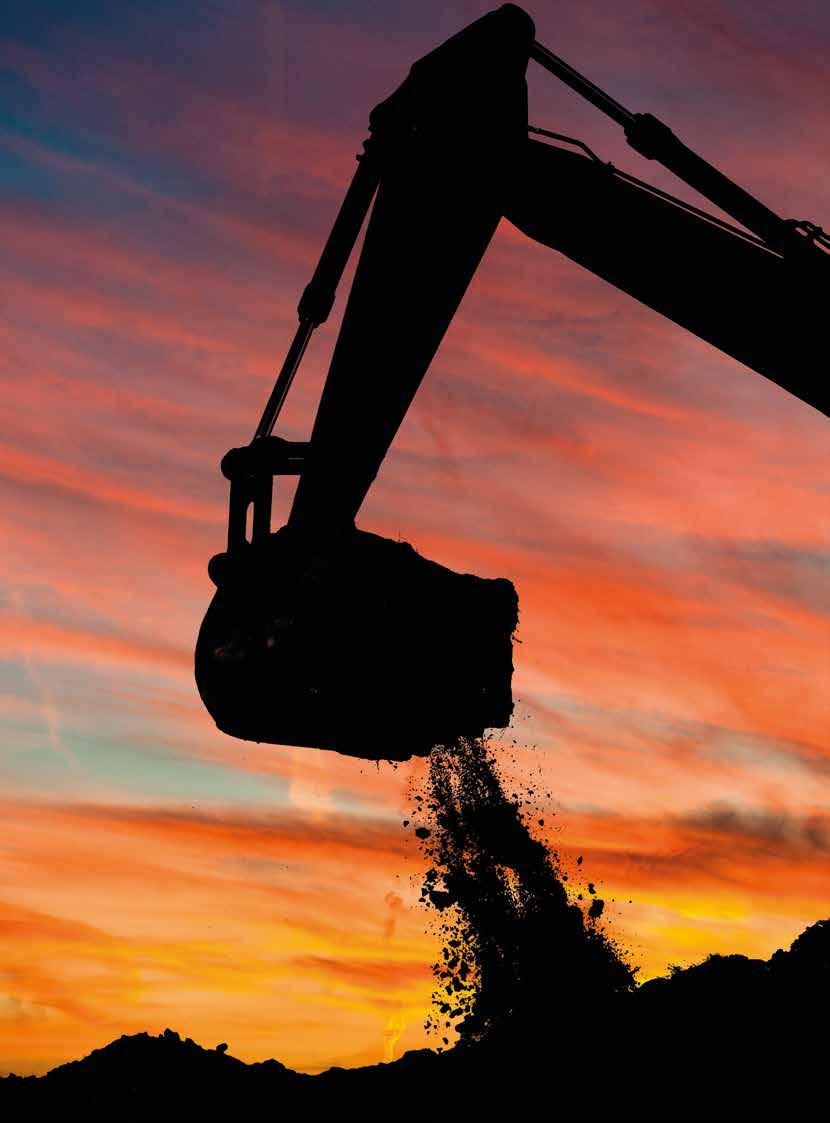
18 minute read
Cummins: Balance of power
Cummins
BALANCE OF POWER
Advertisement
Through technical innovation and world class customer service, the leading engine manufacturer, Cummins, is powering miners to balance their need for lowest cost of production with improved sustainability.
As the mining industry changes to accommodate new technology and social and environmental pressures, miners are adapting to prosper in a new business climate. Suppliers must change, too, to fulfil their customers’ evolving needs.
In 2019 and 2020, Cummins celebrated 100 years of manufacturing engines and generators, respectively. Longevity is its middle name, and one of the features that defines the brand. Asked to describe a Cummins engine, people tend to say things like ‘it’s a beast’, ‘it never stops’, and ‘it’ll run forever’.
However, in an industry which has historically tended to reward the biggest, the fastest, or the most powerful, customers are starting to want a more sophisticated mix of power solutions, giving Cummins the opportunity to demonstrate its leadership in more ways than one.
How does a brand with a reputation for power and endurance demonstrate innovation and sustainability? It’s all here.
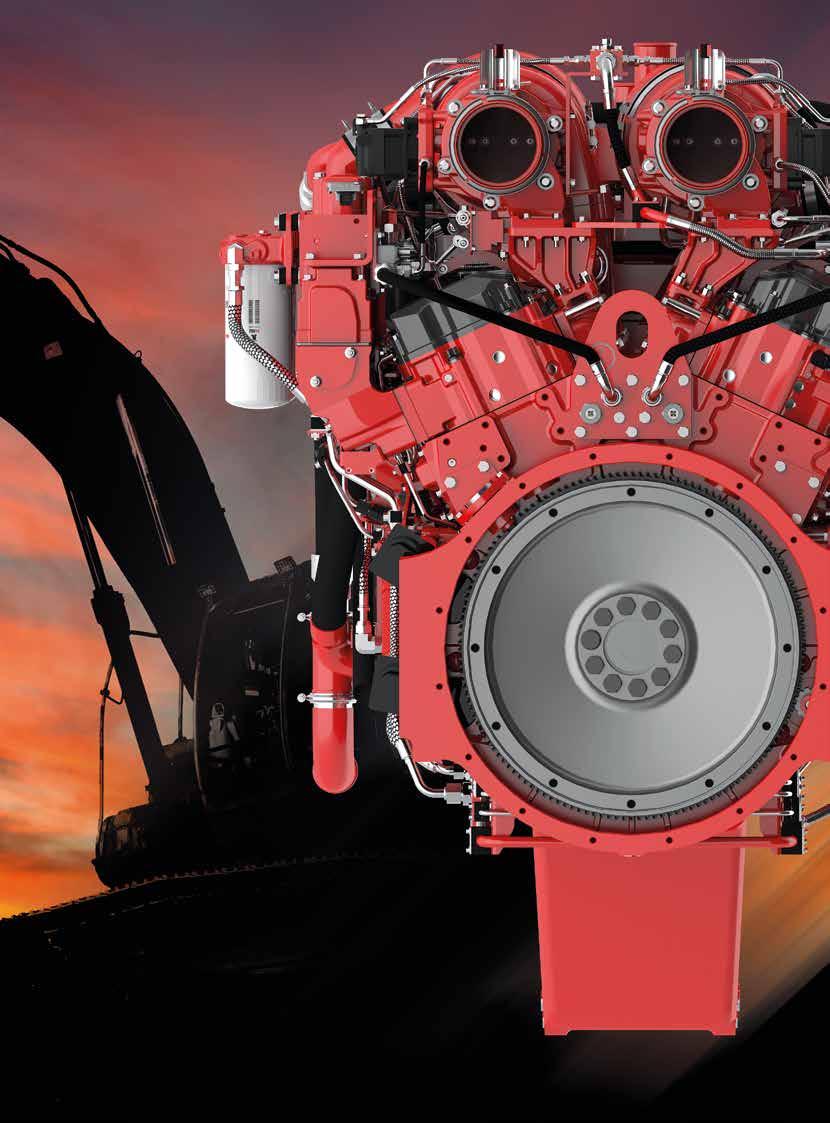
www.cummins.com
World class support
When a mine site operates 24 hours a day, every day, equipment availability is paramount. It could cost anywhere between $1,000-$10,000, an hour, to have a haul truck or an excavator out of action, and therefore, proper maintenance practices and prompt service support are crucial for ensuring high equipment availability.
One of the challenges that miners face is how to optimize their equipment in the face of changing needs and advances in technology. One way of doing this is through an engine rebuild, to take advantage of improvements in emissions performance and fuel consumption. Cummins has 12 Master Rebuild Centers strategically located in areas with high mining activity. “Once an engine has reached overhaul, the industry practice is to complete an engine rebuild,” says Lanre Ige, Director, Mining Strategic Accounts. “A mine truck, with proper maintenance, could see three to four engine rebuilds before the whole chassis needs to be rebuilt. During the rebuild process, Cummins will upgrade individual components of the engine to the latest technology and even offer zero hour rebuilds, which allows the engine to perform and last as well as a factory-built engine.
“Another thing that sets us apart is our relationship with the end users,” says Ige. “We have service capabilities all over the world, giving our customers access to distributor locations and certified technicians at their mine site, no matter how remote they are.” World class customer service encourages existing customers to develop long term relationships and attracts new ones with the potential to do the same.
With over 90 years of experience in the mining industry, Cummins has the product and service expertise to help miners maximize equipment availability and enhance profitability.
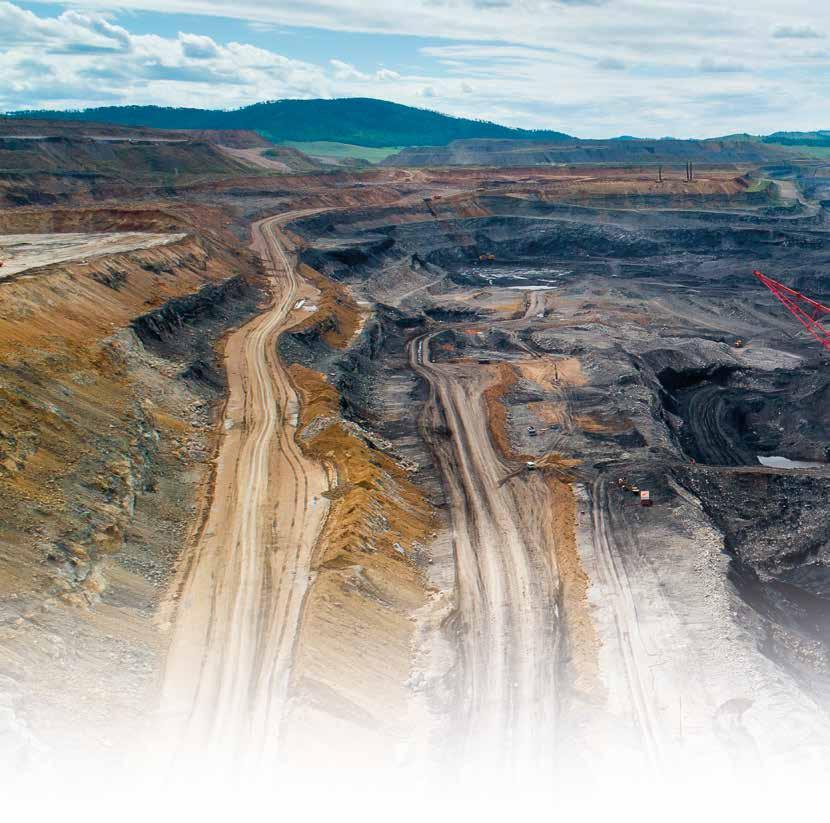
balance of power
www.cummins.com
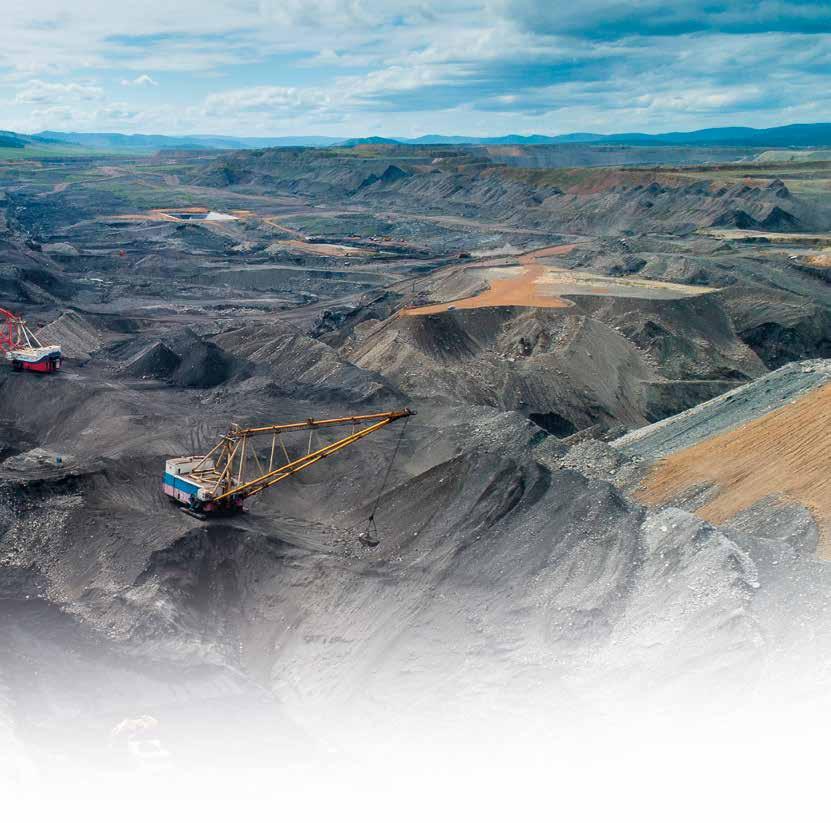
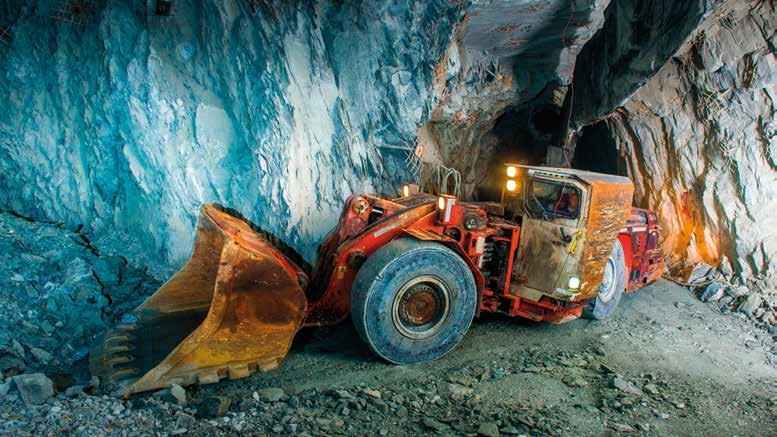
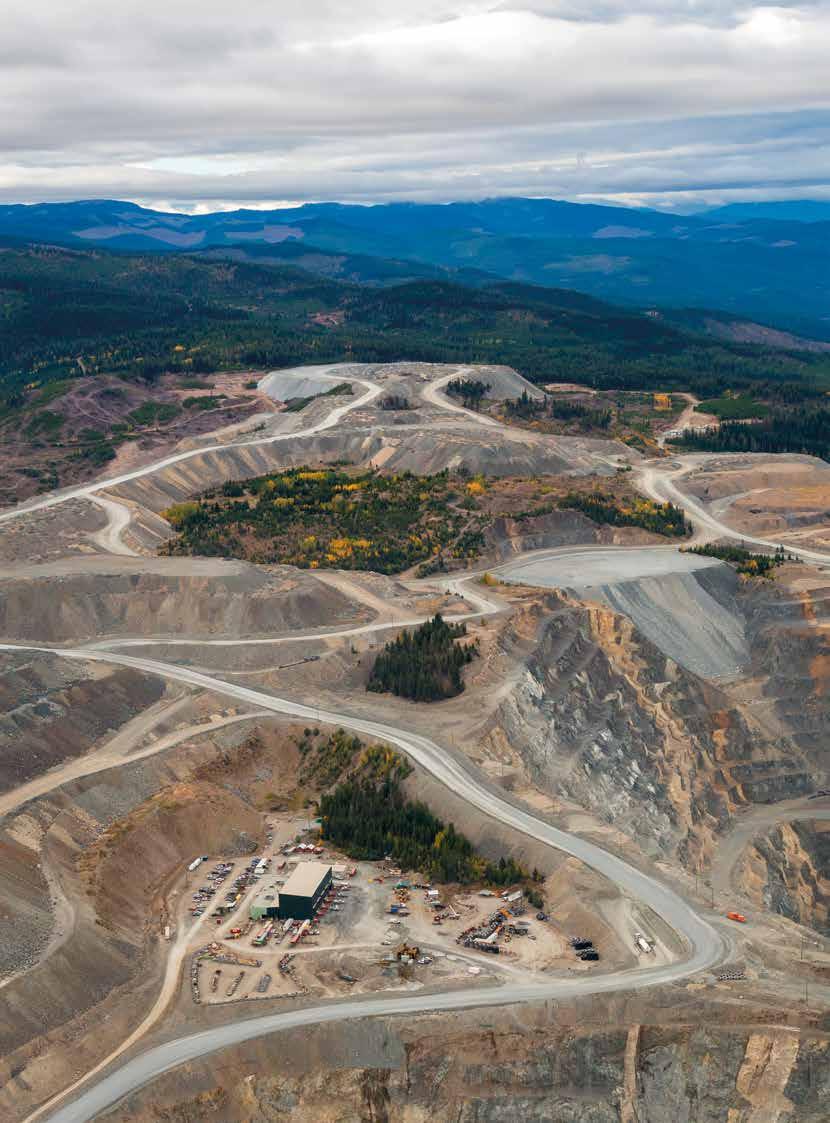
Innovation in technology
In a world that never stops, you need equipment that never stops, and then some. Miners demand the best equipment and engines, and today, that means engines that maximize productivity and availability, minimize operating costs, and help achieve increasingly important sustainability targets. “We went through a period when miners all wanted to maximize production,” says Robert Schaefer, Director, Mining Innovations and Growth Initiatives, “so they increased horsepower, they increased capacity, they added trucks and mines got deeper. After the financial crisis there was a phase where they were all desperate to cut costs. We supported them through all of that, finding ways to improve fuel economy and extend engine life.”
Now, miners are focused on achieving the lowest cost of production while satisfying investors, insurers, governments, and other stakeholders of their commitment to social and environmental issues. Suppliers must respond to these changing requirements. “We feel strongly that we have all the tools to help them with that,” says Schaefer, “not only from a performance standpoint, from the power inside their equipment, but also from how well they can maintain their operations and how they approach the sustainability aspects.”
It can cost over a million dollars a year to operate a mine haul truck, so even small improvements in efficiency can add up to a considerable sum. With roughly a third of the cost of operating mining equipment being spent on fuel, improvements in fuel efficiency bring the double benefit of reducing the emission of greenhouse gases and significant cost savings.
The engine of a regular mine truck might carry 100s of gallons of consumables. It also has filters that are changed every 500 to 1,000 hours (about once a month). “Potential savings add up quickly when you consider the frequency of changes,” says Schaefer. “We conducted a 12-month filter optimization program at Anglo American’s Dawson Coal Mine in Queensland, Australia,” he continued, “where a Komatsu 830E haul truck, powered by a Cummins QSK60 engine, was fitted with Fleetguard filters. They saved 60 percent of their filter and oil consumption. That would have added up to over $220,000 a year for their whole fleet of 14 trucks.” Add to that the savings in labor costs from fewer hours of service time, and the total annual savings for the 14-truck fleet would exceed $250,000. Service intervals of 2000 hours were subsequently established by installing the new Fleetguard NanoForce® air filters with nano-fiber technology.
www.cummins.com balance of power
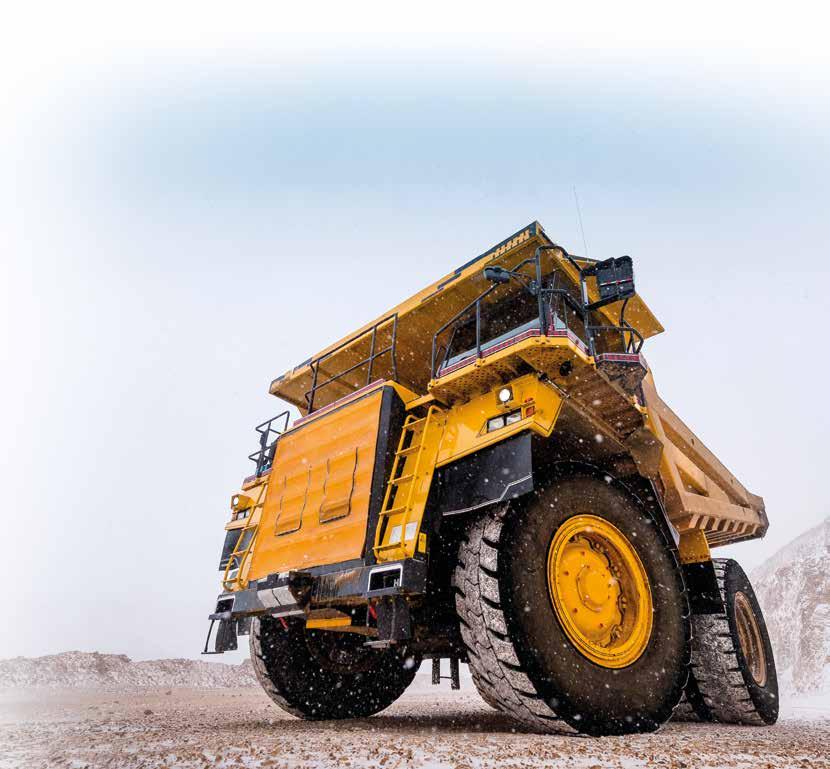
Another mine in Colombia extended its change intervals on fuel filters to 1,000 hours and air filters to 2,000 hours by using NanoNet™ fuel filters and NanoForce air filters. Other mine sites around the world have since followed suit.
As resources become harder to find, miners often find themselves operating in remote locations where exceptional conditions, such as high altitude and extreme temperatures, can affect the performance of mining equipment. While poor air quality and severe weather conditions can compromise engine power and fuel efficiency, Cummins engines adapt automatically in extreme conditions, allowing them to provide the optimum power solutions. This is done by the electronic control module (ECM) on engines continually sensing pressures and temperatures within the engine and adjusting fueling to compensate for changes like high altitude. There is standard derate protocol within the system as it goes up in altitude due to things like air density changes. This helps protect the engine by working as efficiently as possible within its surroundings.
At an altitude of 5,500 meters, higher than the base camp at Mount Everest, China’s Julong Mine is the largest copper mine in the country, and home to over 65 Cummins engines, varying in size from 19L to 60L, supporting applications such as excavators, dump trucks, generators, blasthole drills and bulldozers. The 240T ultra-class haul trucks powered by Cummins QSK60 engines enjoy continuous uptime in this severe environment, making it the natural choice at Julong. Cummins engines have demonstrated similarly high performance and dependability at highaltitude mines around the world.
Reducing the cost of energy while protecting the environment is a critical combination for the mining industry. Cummins understands this and has developed EPA Tier 4 and Euro Stage V compliant engines that deliver the lowest cost of production, while minimizing the impact on the environment. The latest Cummins Tier 4 high horsepower
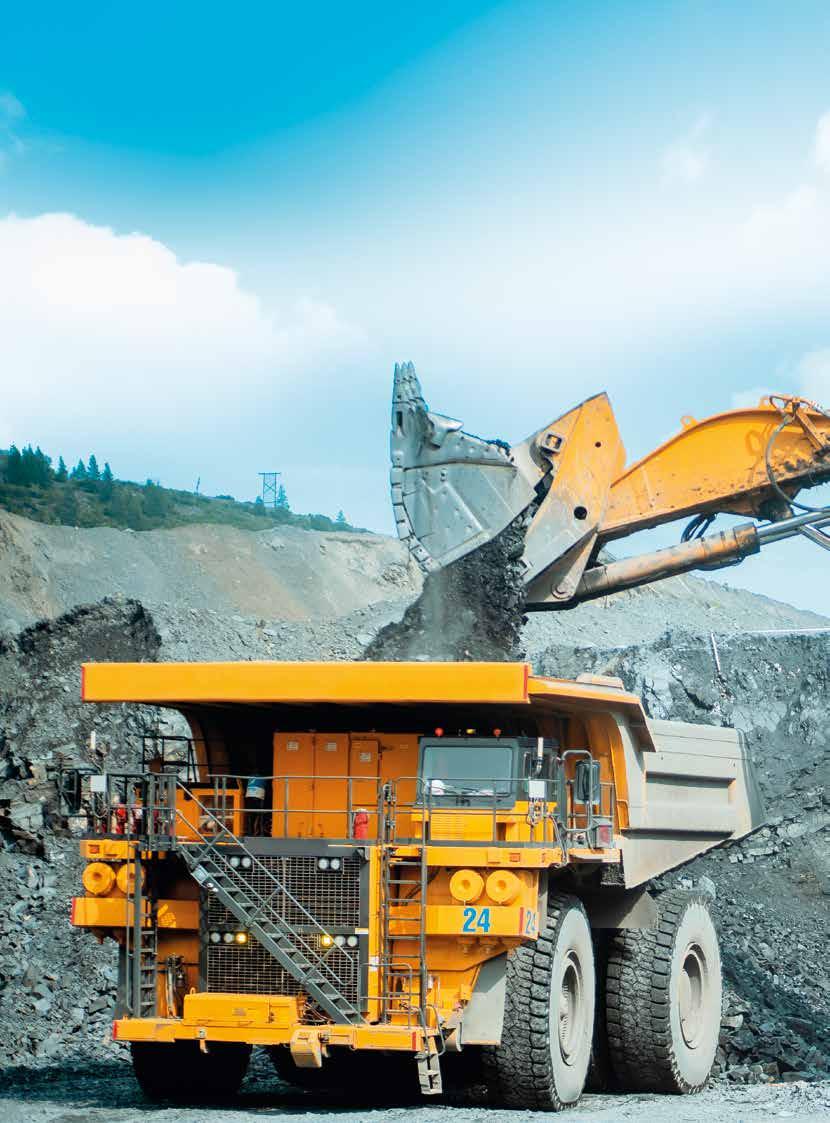
engines (over 751 horsepower) offer between three and five percent better fuel economy than Tier 2 engines, with no compromise to power and reliability. This fuel efficiency gain has been achieved through a combination of in-cylinder improvements and the use of Cummins Selective Catalytic Reduction (SCR) aftertreatment technology, which is used by over 400,000 engines around the world. SCR technology has proven to be a better choice for high-horsepower engines because it optimizes engine performance. This enables excellent fuel economy for the system avoids the need for major changes to the external engine platform. Using SCR also leaves a much higher performance threshold in-cylinder to focus on particulate matter reduction and improve fuel-efficiency. Optimized temperature management also minimizes DEF consumption. The SCR logic control is driven by the QSK electronic engine management system, upgraded with extra processing power for Tier 4 Final, so that the engine and SCR aftertreatment operate as a single, integrated system.
balance of power
the lowest cost per hour of operation, while delivering superior reliability and uptime.
Designed and manufactured by Cummins Emission Solutions (CES), the SCR clean exhaust system features an integrated decomposition chamber and a Cummins airless diesel exhaust fluid (DEF) dosing system designed to last the life of the engine. By focusing NOx reduction within the exhaust rather than during in-cylinder combustion,
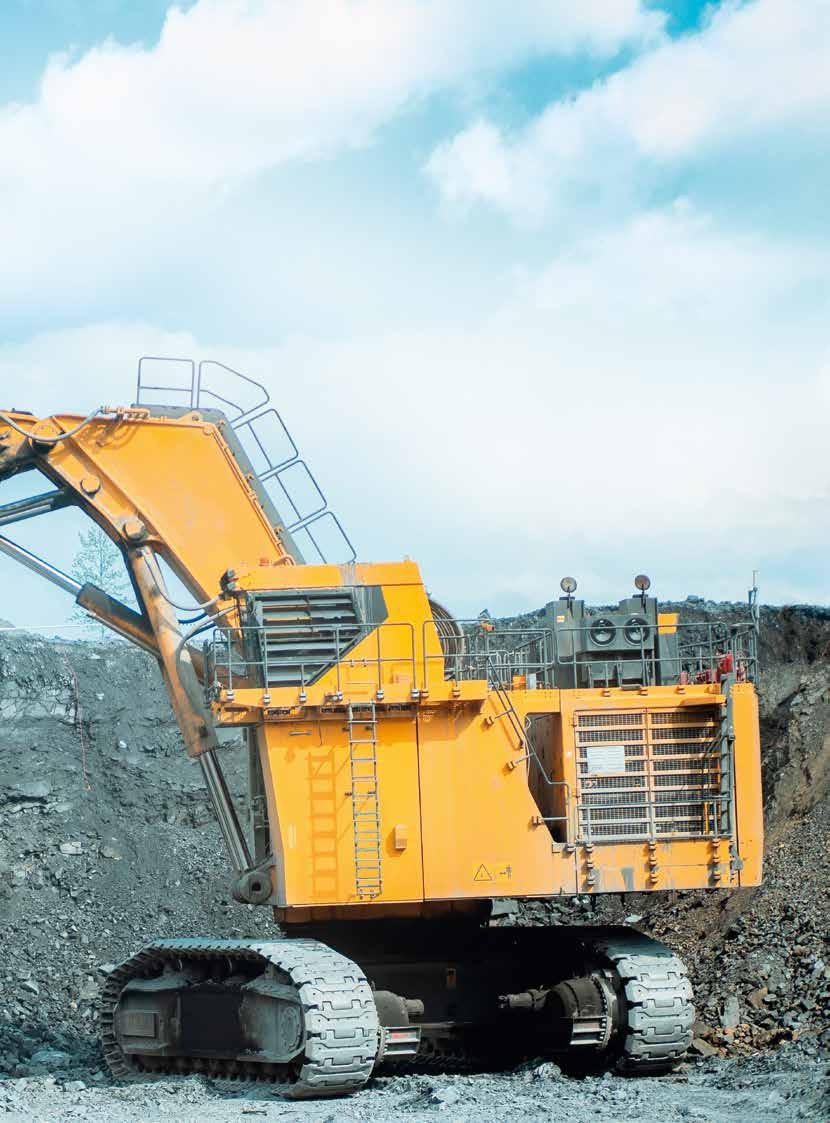
Miners benefit from working with partners that not only offer extensive aftermarket capabilities, but also engines that are designed for life in the harsh mining environment.
The QST30 is a good example of engine development. Built to handle the toughest environments, this model has sold over 30,000 engines around the world over the last 27 years to operate in haul trucks, blasthole drills and wheel loaders.
Life expectancy depends on emissions regulations and the workload involved, but in many applications the engine will run for 18,000 to 20,000 hours in mining applications and reach 500,000 gallons of fuel burned before overhaul. Over the years, improvements have been made in the engine’s turbochargers, fuel handling and power cylinder design, reducing emissions while maintaining the structural integrity, reliability and durability that have won the QST30 its reputation for low cost-of-operation and exceptional life-cycle value.
A mine site in Arizona was concerned last year that the engines powering their Komatsu 930E-1 haul trucks were not giving them the performance they expected, and the engine manufacturer was not providing the required customer support. The mine had seven Komatsu 930E-1 haul trucks going through a rebuild due to performance issues to satisfy the mine’s need for higher engine up-time and improved fuel efficiency.
Cummins Sales and Service team from the local distributor provided a large inventory of on-site parts as well as a dedicated on-site technician, supported by three field technicians in the local area, with immediate improvements. The mine’s operation manager then decided to repower two of the trucks with Cummins Tier 2 QSK60 engines to help lower fuel usage and improve equipment life. The QSK60 engine is installed in most 240T and 320T haul trucks available today and provides higher total truck availability hours and one to two percent more fuel efficiency than any other engine in its class. Since the switch, the mine site reported an improvement in mean time to failure of 43%, a decrease in mean time to repair of 69% and a 3-4% improvement in availability.
The mine site naturally decided to convert the remaining five trucks to Cummins QSK60 engines and to have all its mining products powered and serviced by Cummins by 2021.
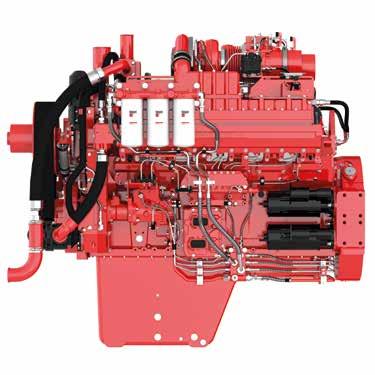
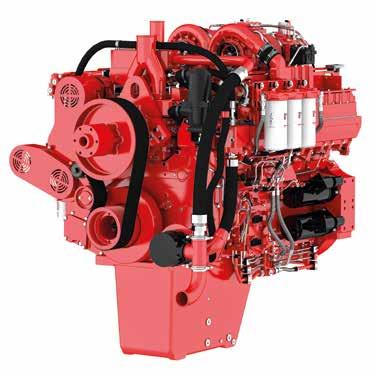
QST30
balance of power
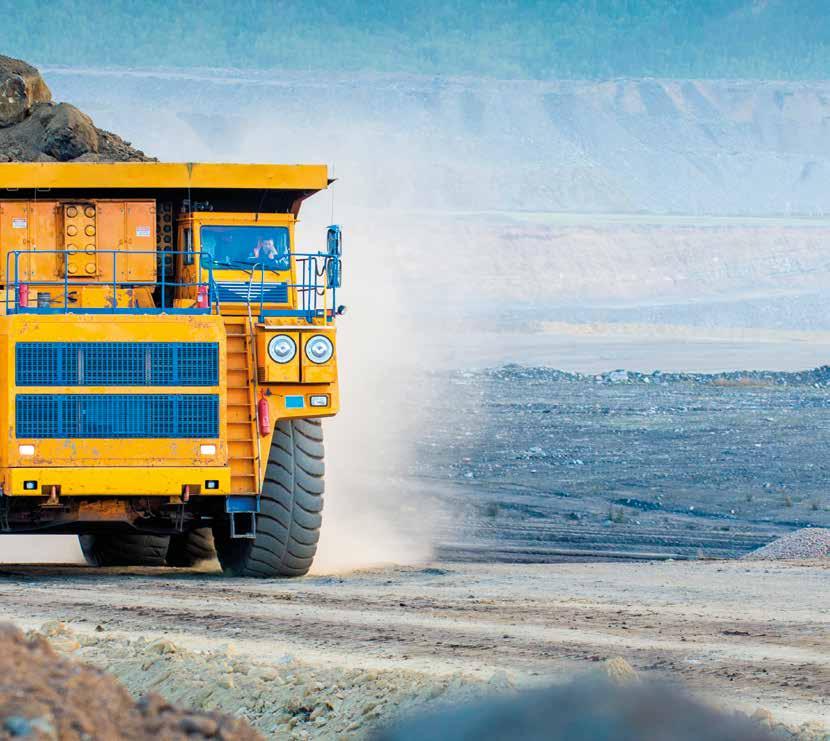
QST30
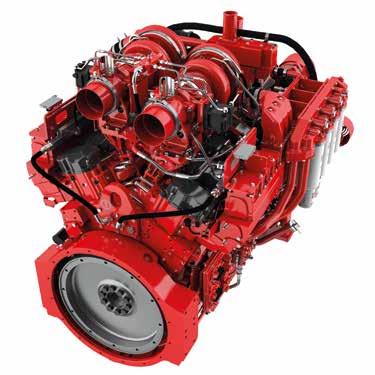
www.cummins.com
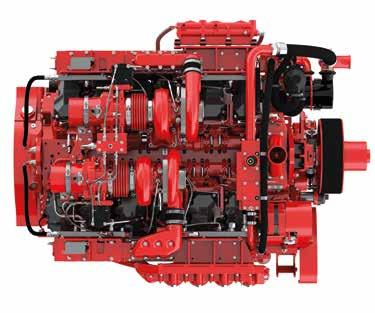
PrevenTech® Mining, an integrated digital solution for end-to-end equipment health management, is the flagship of Cummins customer service portfolio, harnessing connectivity, big data, advanced analytics, and internetof-things (IoT) to securely deliver remote engine monitoring and reporting of potential performance issues.
“PrevenTech extends engine life and reduces downtime,” says Dana Miller, Director, Digital and Service Solutions, “through alerts and assisted monitoring. By detecting potential equipment health issues before they become costly, miners can mitigate performance impacts and improve productivity.”
Designed to connect Cummins monitoring, support, and service functions, PrevenTech issues alerts and recommendations by email, telephone, and a web-based customer dashboard. With a simple and intuitive interface, the dashboard provides a high-level overview of equipment location and status. Alert notifications describe performance issues along with recommendations for repair and suggested remaining time to act. “The
equipment map shows the location of a customer’s connected equipment via GPS,” says Miller, “with a traffic light system to rank and prioritize alerts according to severity – green where all is well, yellow to indicate equipment that requires servicing within seven days, orange to warn that a service should be done within three days, and red for items requiring immediate attention.”
Using this interface, miners can see individual data about each piece of equipment, the last occurrence of an issue and a historical archive of equipment alerts. Gaining visibility into the real-time status of mining equipment allows miners to plan downtime and repair work more intelligently, for example, by customizing maintenance intervals according to actual equipment usage at each site.
A Chilean mine site improved its equipment availability and productivity, performance, and reduced its Total Cost of Ownership (TCO) using PrevenTech. The Chilean mine operator wanted to trial turbocharging telematics to eliminate unexpected high-pressure turbocharger failures. Halfway through the pilot, PrevenTech alerted the maintenance team 190 days in advance, providing ample time to plan for proactive maintenance and avoid unscheduled downtown, and caught 100 percent of potential failures in advance. The mine site saved $1.3 million in operating cost. The Chilean mine looks to save more in the future by also monitoring injectors and bearings; this will provide the mine maintenance supervisors with a clear picture of when service will be needed, months in advance, and allow for proactive scheduling at the most advantageous time.
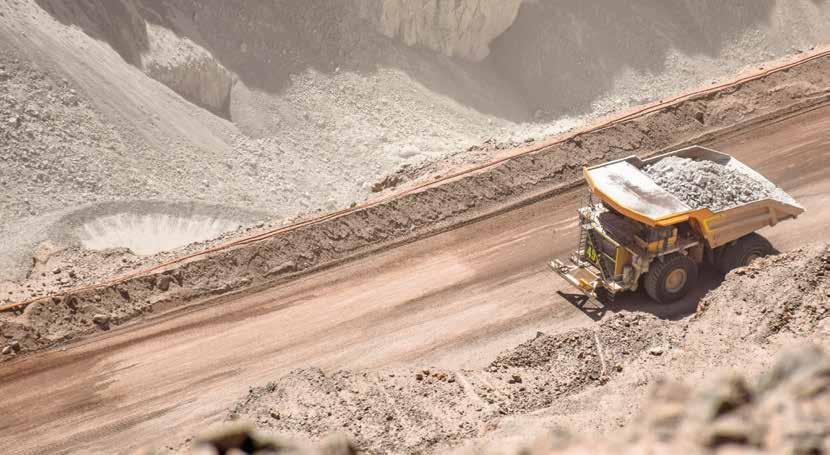
PrevenTech Mining offers three service options: Base, Plus and Premium. Features range from essential fault code alerts, custom rules, and thresholds, to advanced algorithms with FleetguardFIT™ prognostics, live monitoring from Cummins Care experts, and more. FleetguardFIT is a feature that helps extend maintenance intervals by monitoring consumables, including air filters, fuel filters, lube filters and engine oil quality, applying prognostics to interpret the remaining useful oil and filter life.
FEATURE
Data Encryption
Equipment Map & GPS Location Fault Alert Notification & Basic Reccommendations
FleetguardFIT Diagnostics Alert Reccommendations Alert History Engine Data Log and Export Self-Monitoring
Customer Alert Creation & Notification
Graphing Cummins Care Expert 24/7 Service Fault Alert Notification with Personalized Reccommendations
Cummins Proprietary Algorithm Cummins Proprietary Algorithm Alert Notification with Reccommendations FleetguardFIT Prognostics Alert Reccommendations Periodic Fleet Health Reports
balance of power
BASE PLUS PREMIUM
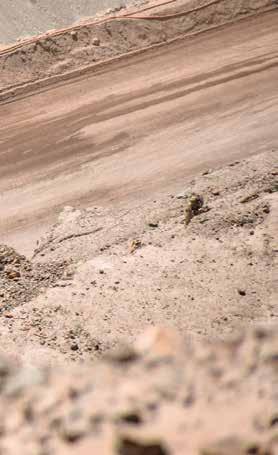
A graphing feature is available to Plus and Premium customers, providing charts representing engine parameter behaviour over time, where trends and correlations can be spotted. Custom rules can be created with the Plus and Premium options, too, allowing miners to develop performance alerts targeting specific parameters and behaviours, based on their own unique needs. Notifications can be managed to customize workflow by assigning specific users to receive immediate, periodic, and customer rule notifications.
A recent enhancement is the addition of Wi-Fi as a connectivity option. “The lack of cellular coverage at some mine sites can cause delays in data transmission and lead to customers being unable to use the PrevenTech product,” explains Dana Miller. “Using the mine’s mesh network Wi-Fi will enable ‘real-time’ data to be transmitted, utilizing PrevenTech to its full potential.” This option can also have the added benefit of saving the customer the cost of monthly cellular SIM card fees.
balance of power
Sustainability
Cummins thinks of sustainability as the lowest social cost of getting the job done, delivering results with the least environmental impact possible. On a mine site, sustainability has many aspects, including the emission of pollutants, disposal of consumables and preservation of water resources. It’s a question of efficiency. How can you maximise the output of a piece of equipment, while minimising the input?
Fuel consumption is an obvious target. It might take 1,000 gallons to fill the fuel tank of a large haul truck at a mine site, and each truck might need a refill every other day. Improvements in fuel consumption will reduce carbon emissions, as well as saving on the cost of fuel.
Emissions regulations have become increasingly stringent over recent years, and Cummins has been instrumental in helping miners comply. A typical Cummins engine used in a mining application today emits 90% fewer harmful gases compared to engines produced 20 years ago. In most cases, these engines are also more powerful and more fuel efficient than their predecessors.
“A mining contractor in Australia’s Bowen Basin has reduced the carbon
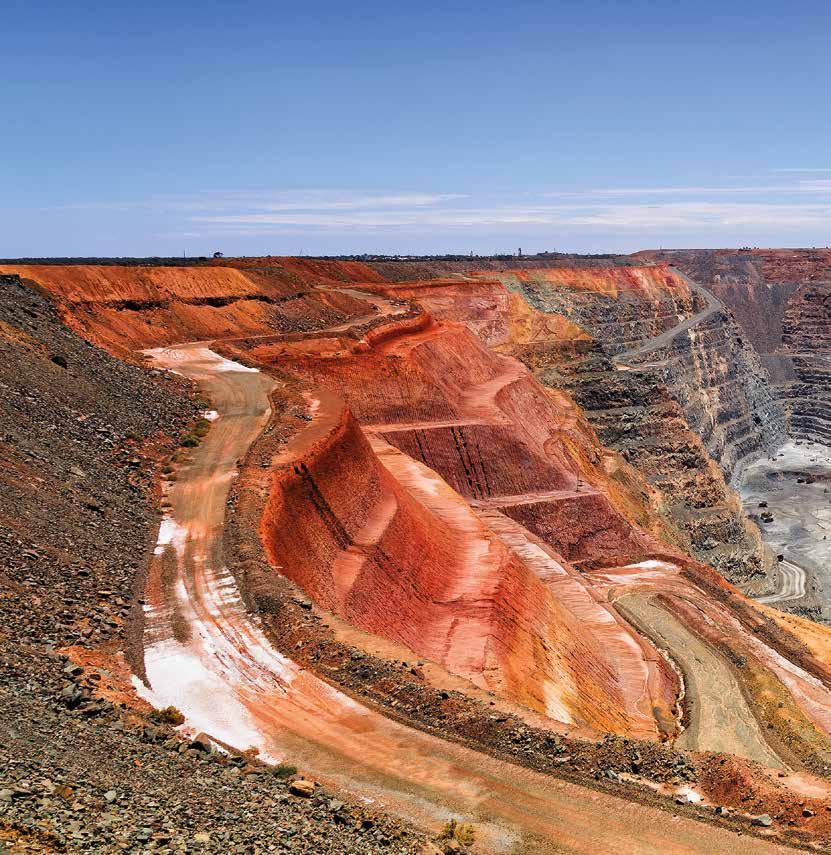
www.cummins.com
dioxide emissions of six trucks by over 500 metric tons a year,” says Robert Schaefer, Director, Mining Innovations and Growth Initiatives, “by replacing the old fuel system with a modular common rail fuel system (MCRS) and installing the latest innovations in combustion technology from our Tier 4 engineering programs.”
Greenhouse gases often dominate the headlines when people talk about sustainability, but for miners, consumables offer a great opportunity to reduce environmental footprint. A mine haul truck might have over 50 gallons of engine oil and need a refill every month or so, not to mention the fuel, lube oil, air and water filters that also need changing. With hundreds of haul trucks working 24/7 in some of the larger mines, that’s a huge quantity of consumables.
Customers taking advantage of Cummins’ advanced analytics and telematics technologies PrevenTech and FIT, can adopt a conditionbased maintenance routine, in which consumables are changed only when needed. Optimizing the maintenance intervals extends the life of the consumables and reduces the waste to be disposed.
“Whether it is air, water or noise, environmental considerations are increasingly becoming a top-of-mind topic for miners, and at Cummins we have bright and diverse minds bringing innovations to tackle these challenges daily,” said Schaefer.
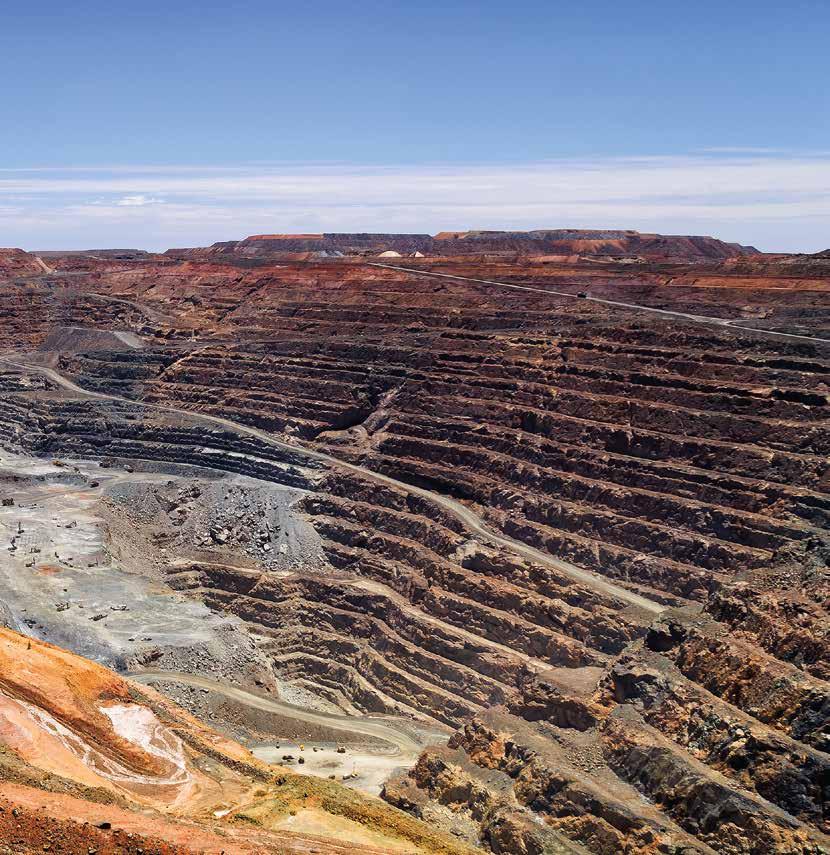
When sustainability first came to the attention of miners some years ago, it was seen as a cost; the price you had to pay to keep shareholders and local communities happy about your environmental impact. Nowadays, it’s integral to a miner’s social license to operate. The first official definition of sustainability was provided by the Brundtland Commission of the United Nations in 1987, formerly the World Commission on Environment and Development (WCED). Its report, Our Common Future, contains the oft-quoted sentence, “Sustainable development is development that meets the needs of the present without compromising the ability of future generations to meet their own needs.”
Mining companies around the world are now increasingly focused on sustainability. The annual reports of many mining companies contain whole chapters outlining their commitment to various projects aimed at reducing their environmental footprint. Some dedicate a separate publication to it.
Cummins, too, strives to reduce its impact on the environment, launching its Planet 2050 strategy in November 2019 to address climate change and conserve natural resources. Chairman and CEO Tom Linebarger described the initiative as both an environmental and a business imperative. Companies that grow, while using fewer of the world’s resources, he believes, will be the most successful in the future.
The company has eight goals aimed at 2030, and several aspirations for 2050, with the 2030 goals being divided between air emissions targets and the use of natural resources at its facilities, including all consolidated operations and joint ventures that are part of the Cummins Enterprise Environmental Management System. The company’s strategy also includes addressing environmental needs in the communities where its employees live and work and where the company does business.
The 2030 targets include reducing absolute greenhouse gas emissions from facilities and operations by 50 percent, reducing absolute lifetime GHG emissions from newly sold products by 25 percent, and reducing volatile organic compound emissions from paint and coating operations by 50 percent, as well as reducing absolute water consumption in facilities and operations by 30 percent.
“Our vision for 2050 is a world where Cummins powers the world’s really important work with carbon neutral products and operations,” said Brian Mormino, Executive Director, Worldwide Environmental Strategy and Compliance. “Since our communities and business depend on a healthier planet, we will take strong action on climate change and work toward a future where we waste nothing and ensure that our communities are better because we are there.”
www.cummins.com
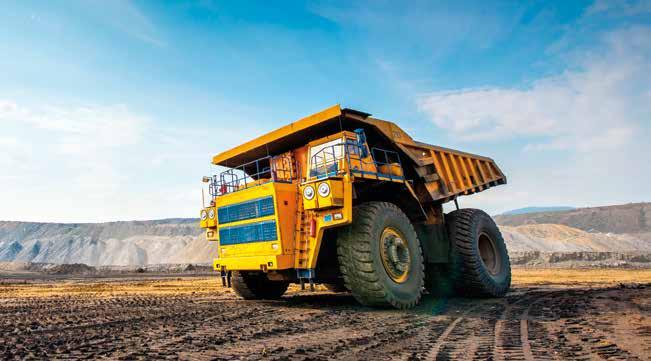
balance of power
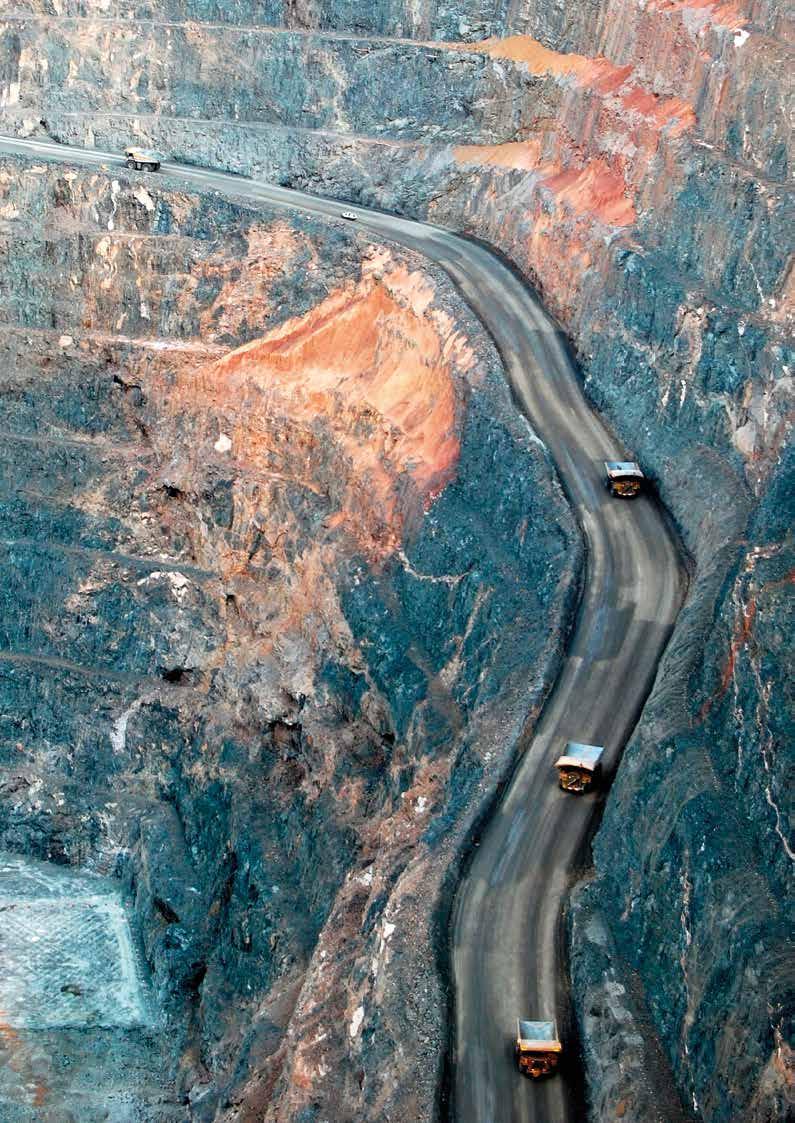