
12 minute read
The lithium conundrum
As demand grows for powerful, rechargeable batteries, companies around the world are developing projects to recover lithium from mineral ores, salar brines and other sources. Dubbed ‘white petroleum’, will this volatile metal solve the world’s energy dilemma?
Lithium is one of the lightest and softest metals known to man. A key component for the fastgrowing rechargeable battery market, lithium powers everything from consumer electronics like laptops and mobile phones to electric cars and energy storage systems. The metal is also used in aircraft manufacturing and in the preparation of some mental health medications.
Advertisement
Lithium is the 33rd most abundant element, but it does not occur naturally in its pure form due to its high reactivity. Swedish chemist Johan August Arfwedson discovered lithium in 1817, when he realized that petalite contained an unknown element, but he wasn’t able to isolate the metal. That was achieved in 1855 when British chemist Augustus Matthiessen and German chemist Robert Bunsen were successful in separating it.
Although lithium is a relatively abundant metal, high-purity lithium chemicals used by battery makers are not so common because lithium extraction, either from brines or hard-rock, involves a series of complex operations that make design production rates hard to achieve.
It has been estimated that demand for high-grade lithium by battery makers could double by 2025. A recent dip in prices has discouraged some investment, however, leading analysts to warn of a potential shortfall in supply in the near future.
But the availability of lithium is not the issue. The challenge lies in finding scientific and chemical solutions to enable the production of battery-grade lithium at the necessary scale.
Today, Chile and Australia are the world’s largest sources of lithium, although the US, Argentina and China are also major producers. The market for lithium is heavily dominated by four companies: Sociedad Química y Minera de Chile, Australia’s Talison, Chemetall in Germany and FMC in the United States.
For many years, commercial lithium production derived from mineral ore sources such as spodumene, petalite and lepidolite. The cost of extracting lithium from hard rock is significantly more expensive, however, than extracting it from lithium-containing brines.

Salars Salar brines occur as underground reservoirs containing high concentrations of dissolved salts including lithium, potassium and sodium. These are generally found below the surface of dried lakebeds known as salars.
Most of the lithium found today is extracted from brine reservoirs located in regions of southwestern South America and China. To extract lithium from brines, water is pumped to the surface into a series of evaporation ponds where solar evaporation occurs over a number of months. Solar evaporation is an ideal and cost-effective method for precipitating salts because salar brines tend to occur naturally at high altitudes, and in areas of low rainfall.
When an optimum concentration of lithium chloride is achieved, the solution is pumped to a recovery plant where any unwanted boron or magnesium is removed. It is then treated with sodium carbonate to precipitate lithium carbonate, which is filtered and dried ready for delivery. Excess residual brines are pumped back into the salar.
Lithium carbonate is a stable white powder which can be converted into specific industrial salts and chemicals — or processed into lithium metal. The Salar de Atacama, in Chile, is host to more than 15 per cent of the world’s known lithium reserves, and yet exploration and production of lithium has occurred only in the southern portion of the Salar, from two production facilities operated by Sociedad Quimica y Minera (SQM) and Rockwood Lithium. Atacama possesses a very high grade of both lithium (1,840mg/l) and potassium (22,630mg/l), has a high rate of evaporation (3,200 mm per year) and extremely low annual rainfall (15mm average per year). These characteristics make Atacama’s finished lithium carbonate easier and cheaper to produce than its peer group globally. A key factor in lithium production costs is evaporation time and Atacama Salar’s evaporation rate is the highest in the lithium industry.
Project potential Wealth Minerals has a large land position in the northern part of the Atacama Salar, in Region II of Chile. The concessions are adjacent to highway 23 which connects northern Chile with Argentina. Wealth believes that the proximity of the Project to existing producers strongly suggests that exploration potential is good for the discovery of brines in the northern portion of the Salar. The company filed an NI 43-101 technical report on the project in 2017.
The principal origin of lithium in the Salar de Atacama is interpreted to be the lithium-bearing geothermal waters from the El Tatio Geyser Field, located north of the salar. The geothermal fluids enter the northern part of the Salar de Atacama via surface and subsurface flow.
Further, the chemistry of the salar brines is almost identical to the chemistry of the geothermal fluids of El Tatio, further strengthening the interpretation that the El Tatio geothermal fluids are the source of lithium and potassium in the salar. Though lithium-mining operations exist around the world, up to threequarters of the known lithium reserves are in the Altiplano-Puna Plateau, a 1,100-mile-long stretch in the Andes. The salt bed deposits are concentrated in Chile, Argentina and Bolivia, known as
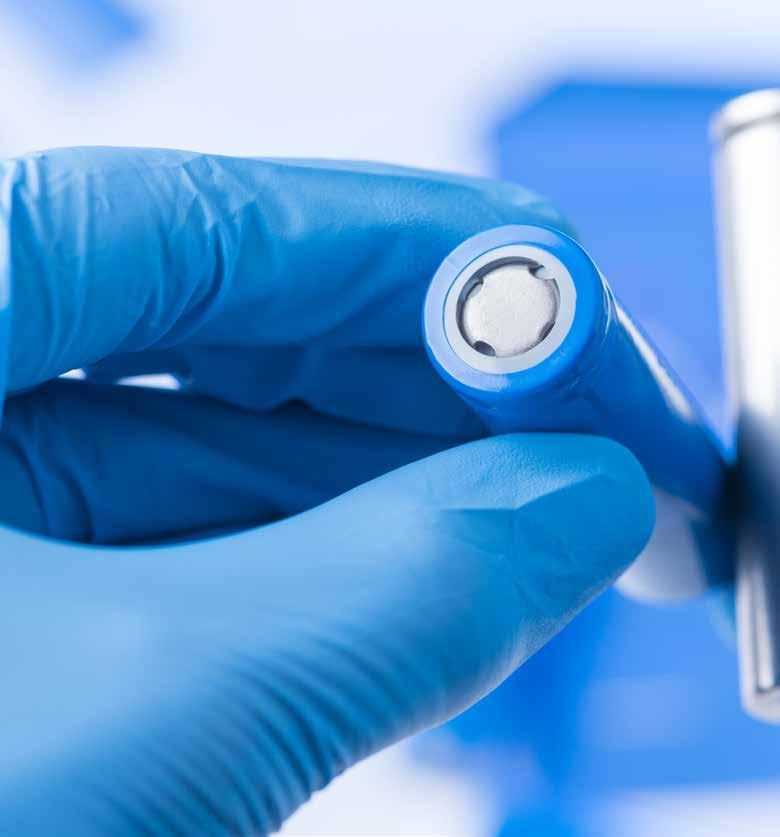
the ‘Lithium Triangle.’
Chile has produced lithium from brine since the 1980s, and its Salar de Atacama is now the preeminent source of the chemical in Latin America. Chile’s government has been the most hospitable to foreign investors, and its mining sector, as the world’s largest exporter of copper, has extensive experience. Argentina also began extracting lithium from brine in the late 1990s, exploiting its Salar del Hombre Muerto. Bolivia would love to do the same, and it has the lithium resources to do so. The Salar de Uyuni, at 4,000-square-miles the world’s biggest salt flat, is one of Bolivia’s most magnificent landscapes. It also happens to have one of the world’s greatest lithium deposits, possibly 17 per cent of the planet’s total.
But Bolivia has a number of challenges that put it at a disadvantage from its neighbours. Lithium mining is expensive and complicated, requiring significant capital and technological

sophistication. Bolivian governments have opposed private capital in the past, but the development of an industry on the scale required to make a difference will be a tall order for a state-owned organisation.
Producing battery-grade lithium from brine involves separating out sodium chloride, potassium chloride and magnesium chloride. The Salar de Uyuni itself has its own inherent disadvantages, receiving a lot more rain than its counterparts in Argentina and Chile, which tends to slow down the evaporation process. Its lithium deposits also have a higher magnesium content which is particularly expensive to remove. A multimillion-dollar plant at Llipi started producing lithium in January 2013, but that is all Bolivia has achieved over the last ten years.
Mining from minerals Despite the ores having a higher lithium content than salar brines, extraction of lithium from spodumene
and other minerals requires a range of hydrometallurgical processes involving considerable energy consumption, making it much more costly.
Nevertheless, mining from minerals continues apace, particularly in Australia, which hosts five of the world’s ten largest lithium mines (in terms of reserves). Two of those are in the Pilbara region of Western Australia.
The Pilgangoora lithium-tantalum project, 100% owned and operated by Pilbara Minerals, has proven and probable lithium reserves estimated at 108.2Mt. One of the world’s premier lithium development projects, a definitive feasibility study was completed in September 2016 and commercial production was achieved there in April 2019.
Right next door, as it were, in an adjoining tenement, is Altura Minerals’ 100% owned Altura Lithium Project. This mine is estimated to contain 34.2Mt of proven and probable reserves grading 1.04% Li2O. The mine is expected to have a life of 13 years.
Altura’s open-pit operation is being developed in two stages. The first stage was commissioned in early 2019 and is expected to produce 220,000tpa of lithium spodumene concentrate. Altura has completed a DFS for stage two expansion of the mine, which will increase the annual production capacity to 440,000tpa.
Despite being rivals to become the first lithium producer in the region, Altura and Pilbara Minerals signed a mutual access agreement and MoU to cooperate at their boundaries, sharing access roads and pipeline routes.
The Wodgina lithium project, 100km south-east of Port Hedland in Western Australia, was originally owned by Mineral Resources but in August 2019 the company entered an agreement with US lithium producer Albemarle Corporation to form a 60:40 joint venture to develop the mine. First ore from the mine was planned for the first quarter of 2020, but Albemarle announced in November 2019 that it would suspend the development of Wodgina until market conditions support production.
Western Australia is also home to the Greenbushes mine operated by Talison Lithium but owned by Tianqi
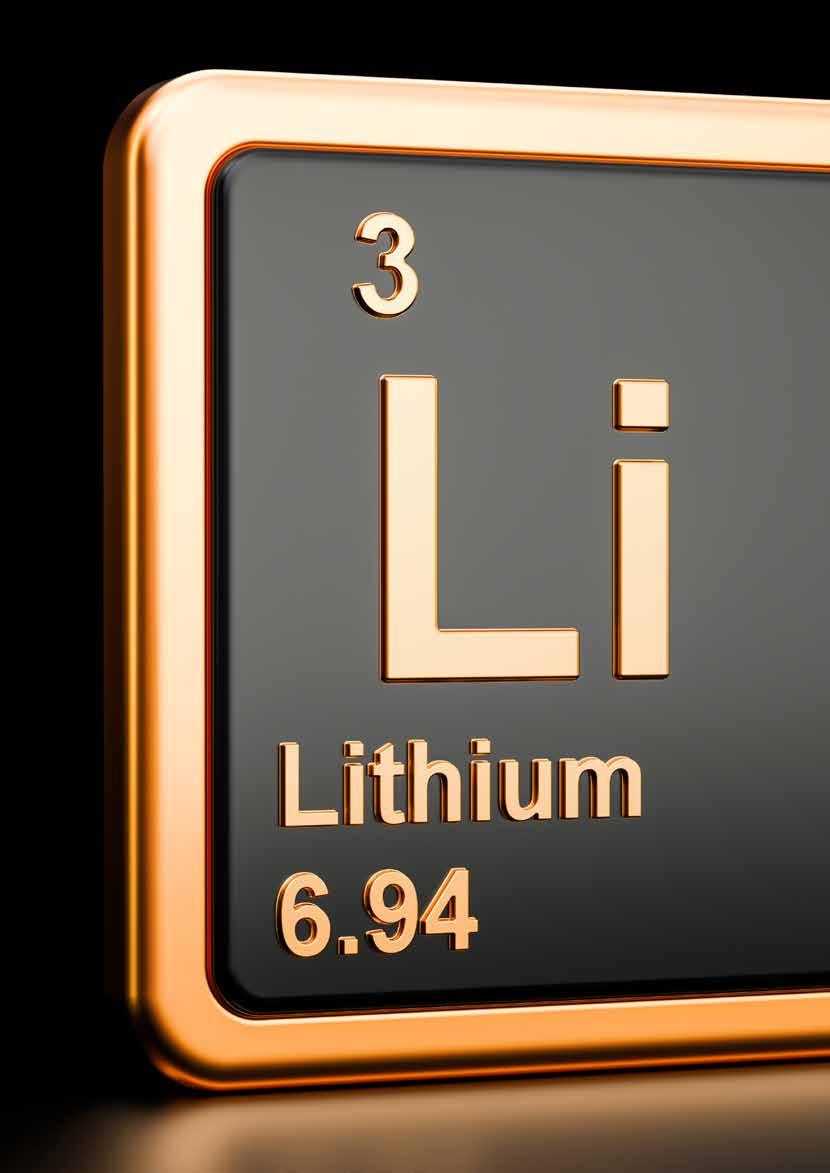
Corporation of China (51 per cent) and Albemarle (49 per cent). The lithium
orebody at Greenbushes was identified between 1977 and 1980 and the mine has
been producing and exporting lithium minerals for over 30 years. The site consists
of a number of open cut mining pits for spodumene and leading-edge lithium
concentrate production facilities.
Talison Lithium officially opened a new chemical grade lithium processing plant
at Greenbushes in October 2019, taking to three the number of lithium processing
plants at the operation and nearly doubling production capacity to 1.34mt of
concentrates a year.
The Mt Cattlin spodumene project, two kilometres north of the town of
Ravensthorpe in Western Australia, is wholly owned by Galaxy Resources. Ore is
processed on site to produce a spodumene concentrate and a tantalum by-product.
At full capacity, ore can be processed at a rate of 1.6 million tonnes per annum (tpa)
with lithium oxide concentrate production of 180,000 tpa.
The Mt Cattlin mine operations include open-pit mining of a flat-lying pegmatite
ore body. Mining is carried out using excavator and truck operations, delivering to
a conventional crushing and HMS gravity recovery circuit. Contract mining is used
for grade control drilling and earthmoving operations (drilling, blasting, load, haul
and ancillary work) for the open-cut mining operation.
The Earl Grey lithium project, also known as the Mt Holland lithium project,
is located in the Forestania Greenstone Belt in Mt Holland, Western Australia. It
is owned by Kidman Resources (50%) and Sociedad Química y Minera de Chile
(SQM, 50%) under a JV named Covalent Lithium.
The mine is estimated to contain proven and probable reserves of 94.5Mt grading
1.5% Li2O. The PFS for the project was completed in December 2018 while the DFS
is currently underway. The mine is expected to produce 411,233t of spodumene
concentrate a year over its 47-year mine life, upon commissioning in 2020.
The biggest lithium deposit in the world, however, is the Sonora Lithium Project
in Sonora, Mexico, a clay project being developed by a joint venture of Bacanora
Minerals (30%) and Cadence Minerals (70%).
The mine is estimated to hold proven and probable reserves of 243.8Mt, containing
4.5Mt of lithium carbonate equivalent (LCE). The bankable feasibility study for the
project estimates a mine life of 19 years.
Sonora is proposed to be an open-pit operation being developed in two stages with
the first stage having a production capacity of 17,500 tonnes per annum (tpa) of
lithium carbonate. Stage two will double the production capacity to 35,000tpa.
The company has secured one of the world’s biggest lithium producers, Ganfeng
Lithium, as a cornerstone investor and intends to start construction in 2020.
The Thacker Pass lithium project in Humboldt County, Nevada is 100% owned
and operated by Lithium Americas. Estimated to contain proven and probable
reserves of 179.4Mt containing 3.1Mt of lithium carbonate equivalent, it has an
estimated mine life of 46 years.
The pre-feasibility study (PFS) for the project was completed in August 2018,
which proposed the two-phase mine development using open-pit methods.
Phase one is expected to be commissioned in 2022 with a production capacity of
30,000tpa of battery-grade Li2CO3, while phase two will increase the capacity to
60,000tpa with a commissioning date of 2026.
Given the soft nature of the deposit, minimal blasting and crushing is anticipated.
The ore will then be processed in a leaching circuit using sulphuric acid to liberate
the lithium from the claystone. Following the leaching process, the lithium bearing
solution will be purified using crystallizers and reagents to produce battery-grade
Li2CO3.
Extracting lithium from brine is a slow process, but it’s cheap. By contrast,
extraction from spodumene is quicker, but expensive. Processing from clay is an
option being explored in a number of places, but has not yet been commercially
proven at scale. As we say in England, “you pays your money and you takes your
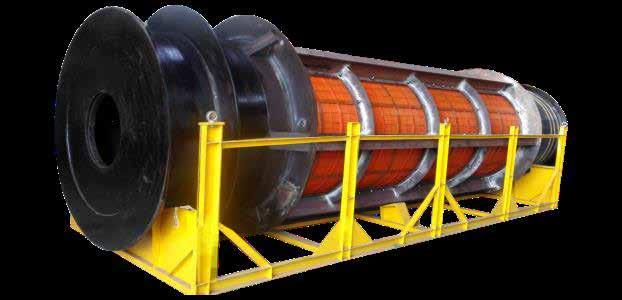



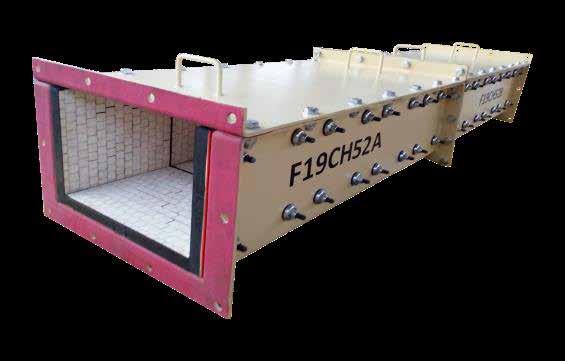
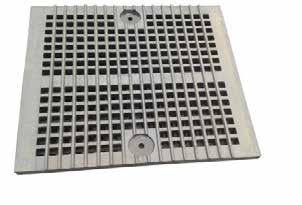
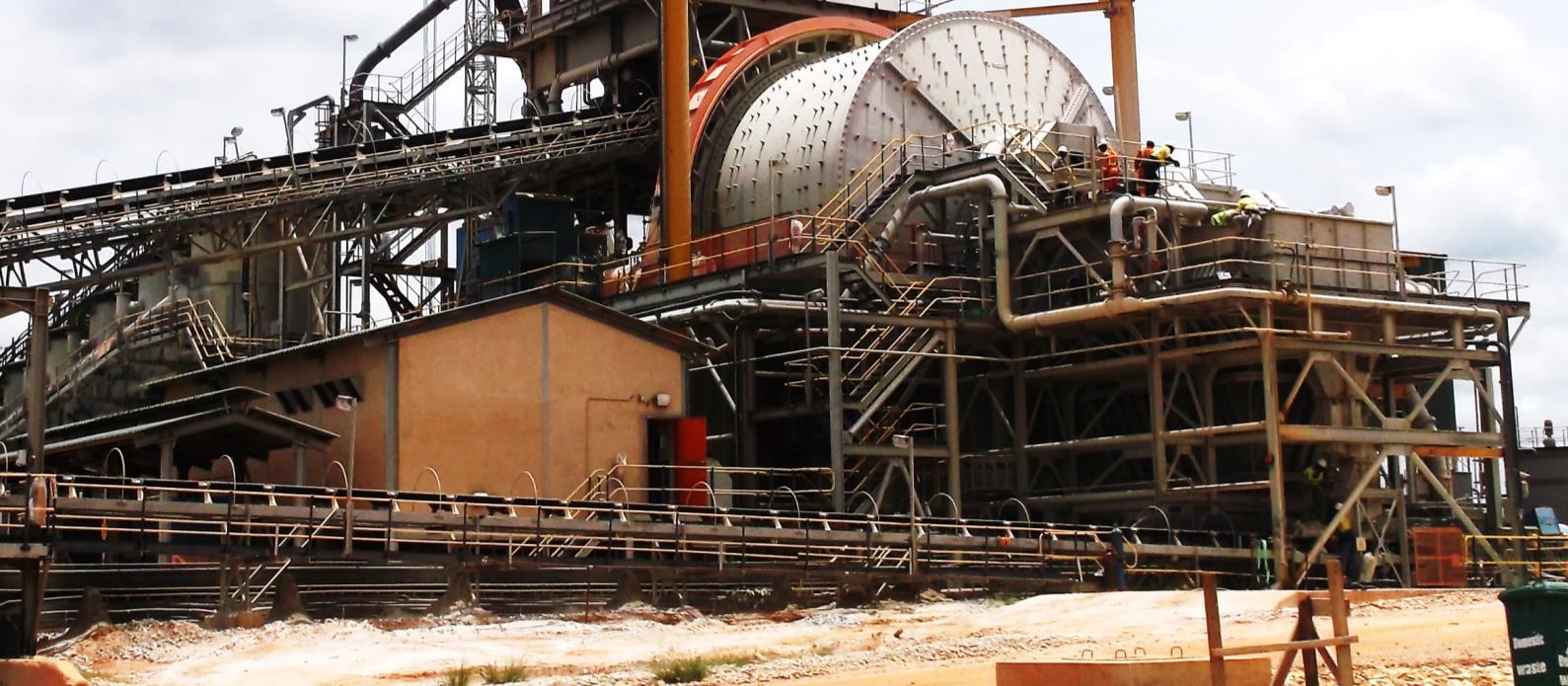
Wear & Abrasion Solutions
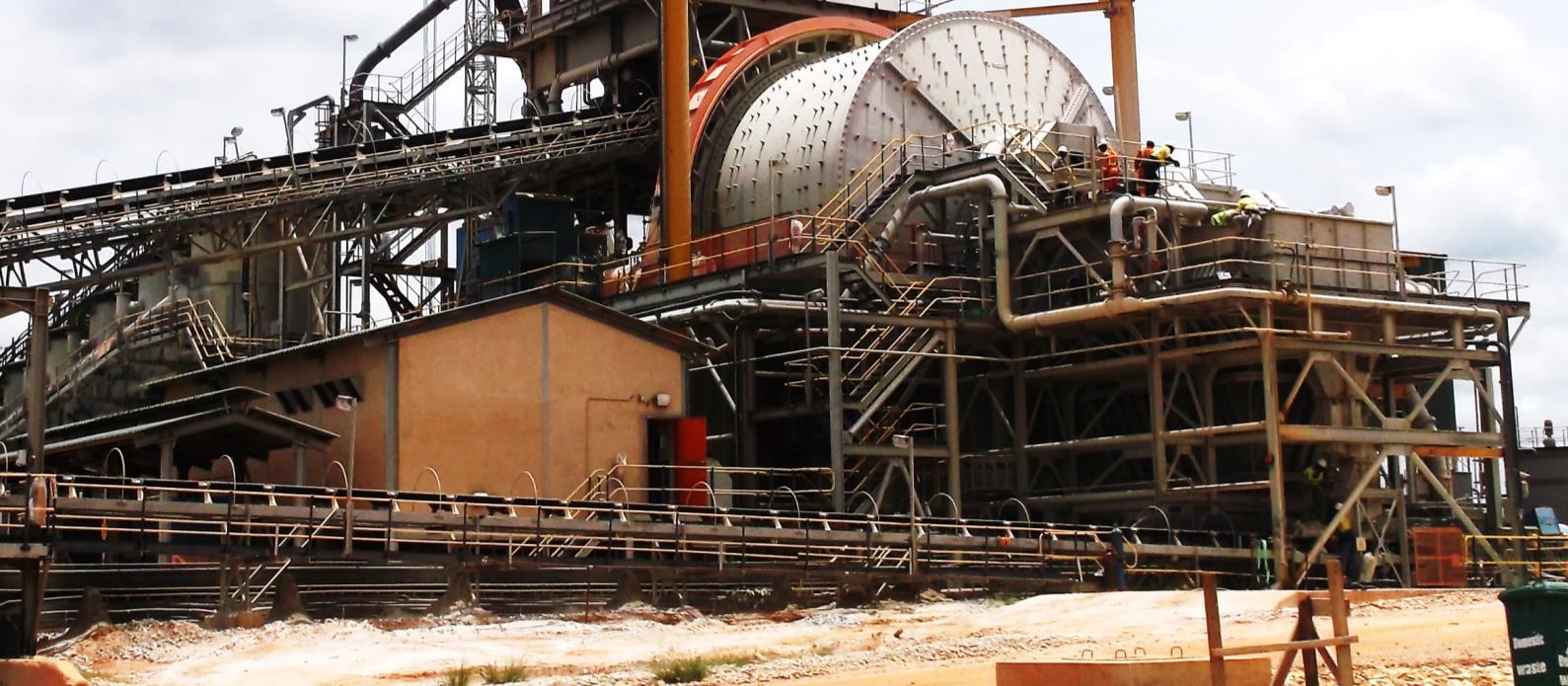

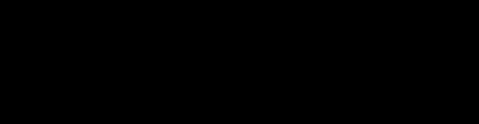


THOR® Mill Liners
WARDOG® Sheeting for Wet Abrasion
GRATOR® Screen Panels –Rubber, PU
RHINO® Liners –Rubber, Ceramic, PU
CERALINE® Ceramic Tiled Sheeting
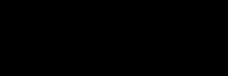
ANAKONDA® Hoses & Piping
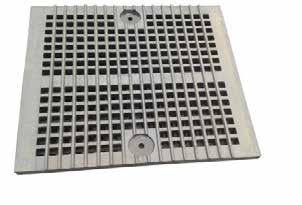
TWISTER® Cyclone & Pump Liners
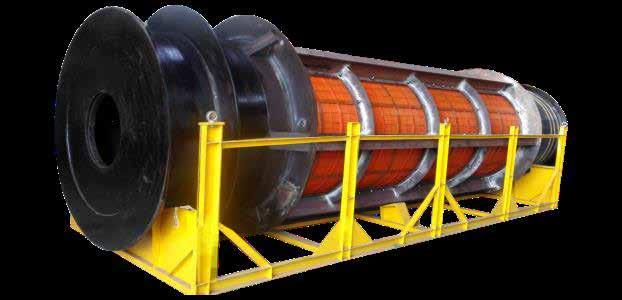
Australia | Brazil | Chile | India | Saudi Arabia Ghana | U.S.A | Germany
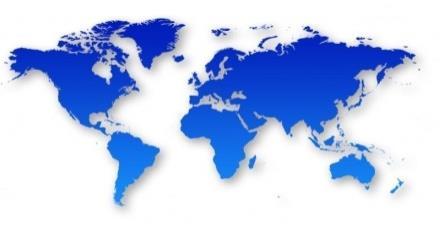
P. +61 2 6333 4500


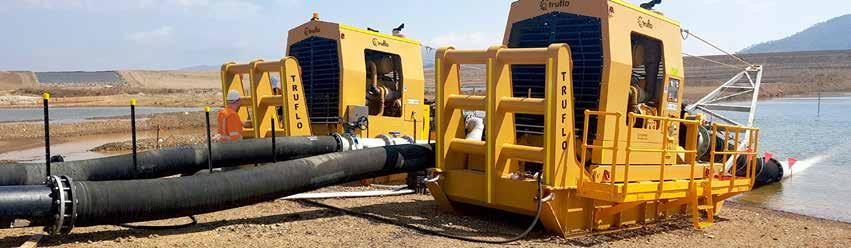
www.truflopumps.com.au
CUSTOM DESIGNED & BUILT PUMP PACKAGES
PUMPING WITH OVER 30 YEARS EXPERIENCE PUMPING WITH OVER 30 YEARS EXPERIENCE
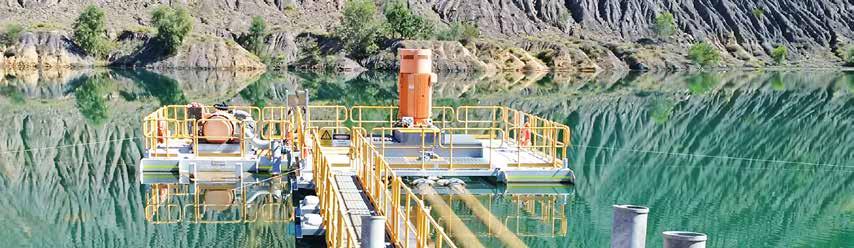
