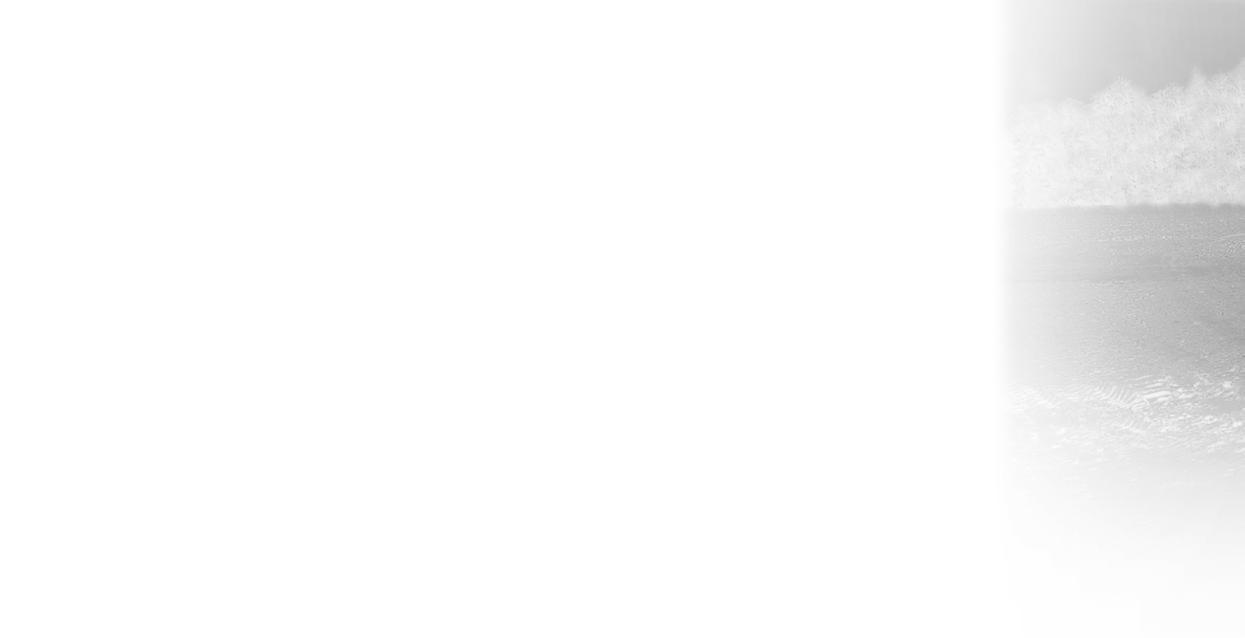
32 minute read
MAXAM TIRE: Setting the new standard
Setting the New Standard
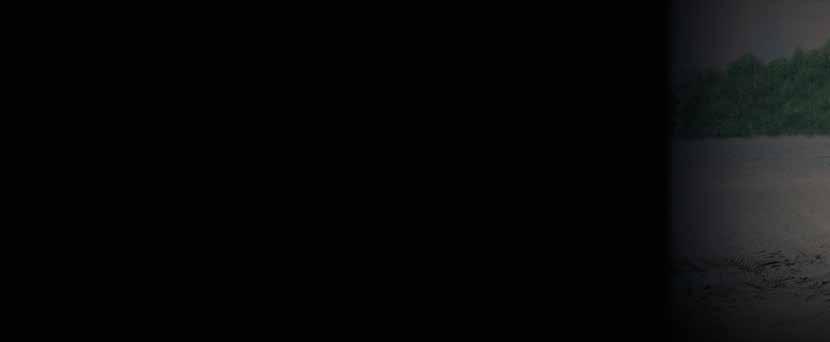
Advertisement
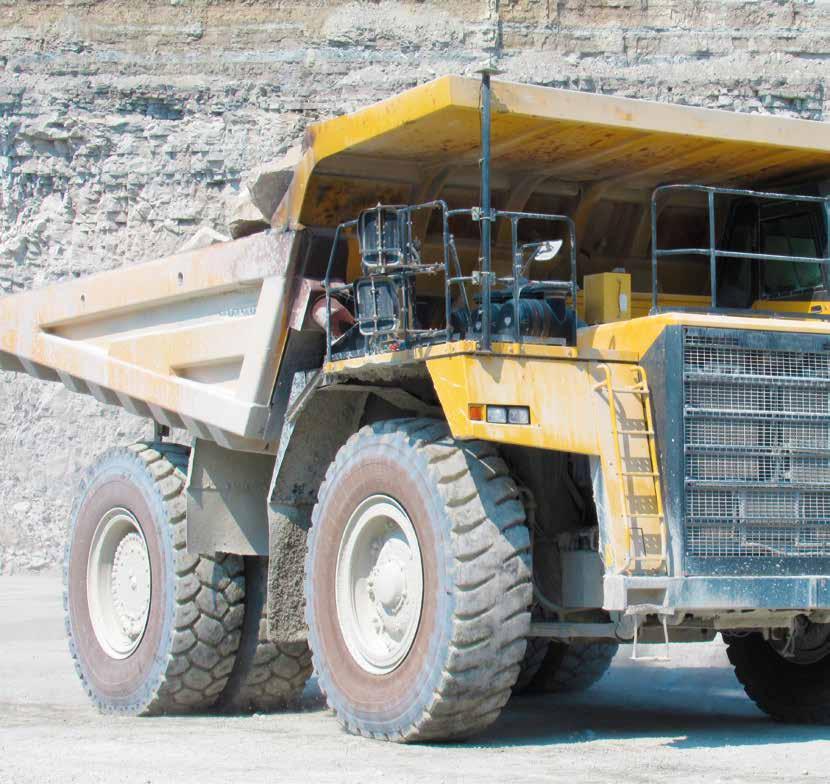
Visit MAXAMTIRE.COM
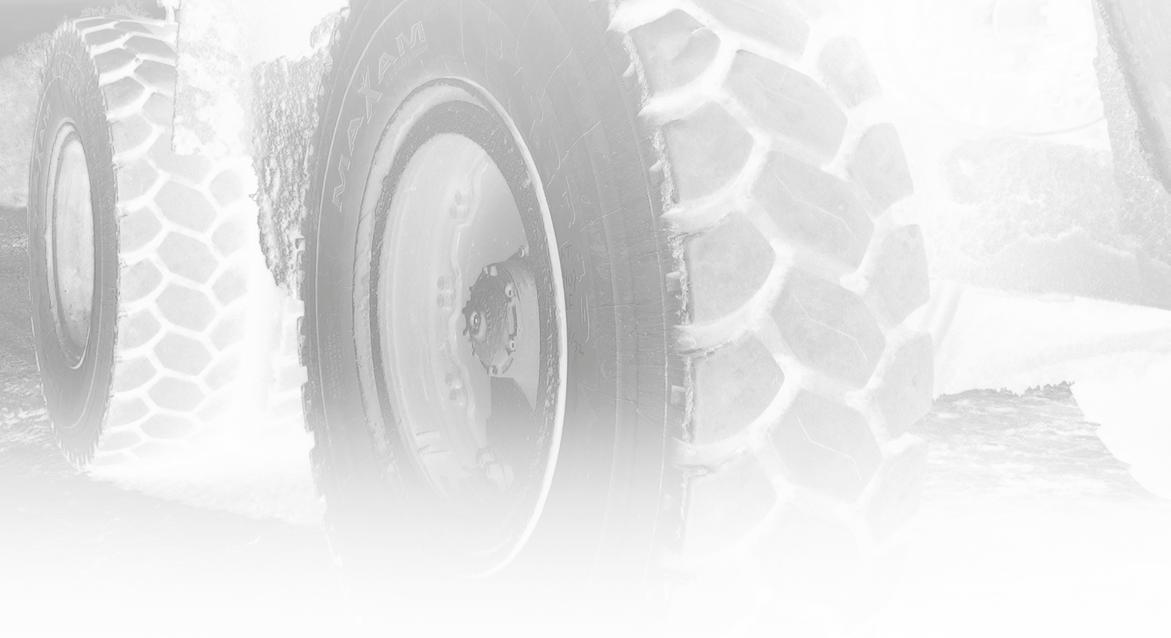


MAXAM Tire North America, a division of Sailun Group, designs, manufactures and distributes off-the-road specialty tire products globally. As a major global specialty tire manufacturer and distributor, MAXAM has a strong reputation for market leading quality, reliability and delivered value. To ensure superior product quality, the organization’s foundation is centered around world-class engineering and has the most advanced manufacturing platforms within the industry. As a rapidly growing global organization, MAXAM invests heavily in our people, progressive engineering processes and our manufacturing facilities to ensure unique business solutions are delivered to customers worldwide.
MAXAM MINING GROUP (MMG), a dedicated global group under MAXAM Tire, specifically focuses on the mining segment. The MMG’s core value is to provide superior support on all MAXAM products through partnerships with high-level dealers in conjunction with support from MAXAM MINING GROUP. Our goal is to ensure the best product performance and the highest level of overall customer satisfaction, while reducing the enduser’s operating costs.
The MMG has built a team of members across multiple continents responsible for serving regional market demands. Each member is an industry leading expert dedicated to providing the best customer experience and continuous improvement of market solutions. Innovative engineering, extensive testing, research and state-ofthe-art manufacturing differentiates the MAXAM MINING GROUP from our competitors.
Who We Are and Our History
Sailun Group, the parent group of With true vertical integration from MAXAM Tire, was the first “A” raw materials, factory development, listed private tire company in on the R&D, tire building machinery to global Shanghai Stock Exchange and is located customer support, Sailun has achieved at the hub for the National Rubber and rapid growth in the past two decades. As Tire Engineering Technology Research of 2020, Sailun is now the 18th largest Center. Founded back in 1990, Sailun tire company globally and is sold in over Group was established to develop the 167 countries worldwide. Being a global automated equipment, along with intellectual capital to build tires for major manufacturer, Sailun boasts a investing in the MAXAM team. Most global market demand and to build full range of products in the passenger recently, Sailun Group has furthered machinery facilities for the largest tire, truck tire and off-the-road tire MAXAM manufacturing in Asia to manufacturers in the world. Centering industries with 19 categories in total. meet the increasing demand and to its mission in being a leading provider of In the past decade, Sailun Group elevate product performance and global value solutions with unsurpassed increased its investment further quality. Today, MAXAM Tire has product in the value segment and by expanding radial off-the-road become a top-tier manufacturer under delivering the best customer service (OTR) products, building patented Sailun Group’s innovation, leadership in the tire industry, Sailun Group set manufacturing processes and utilizing and investments. a significant precedent for MAXAM Tire on forming its mission of being a “Centering its mission in being a leading provider of business solutions provider. global value solutions with unsurpassed product in
the value segment and delivering the best customer service in the tire industry, Sailun Group set a significant precedent for MAXAM Tire on forming its mission of being a business solutions provider”
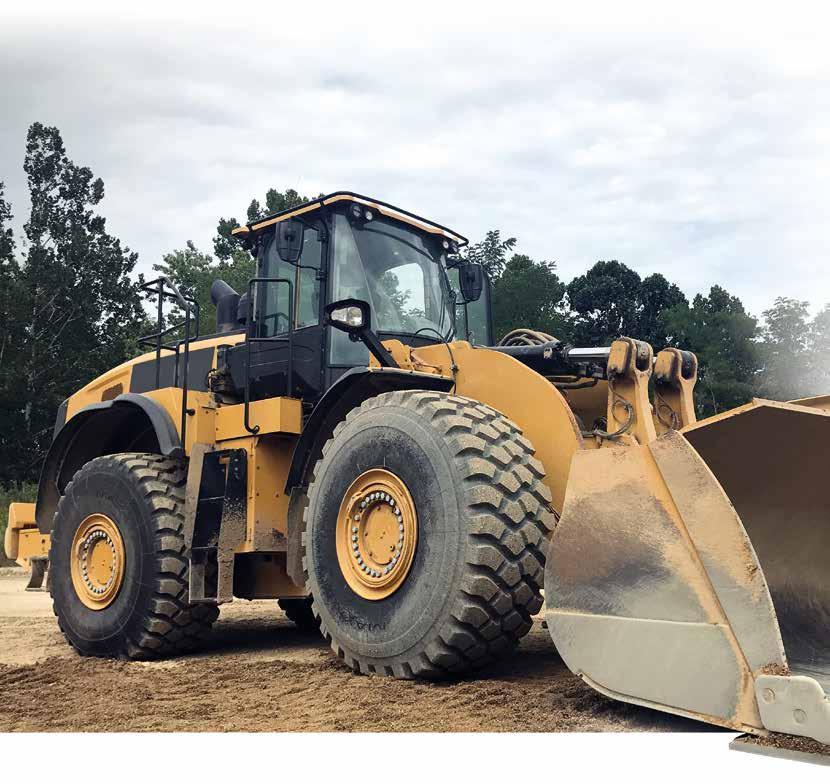

Technological Forefront and Philosophy
Sailun insists on technology R&D as the main driving force behind company development. Guided by the company’s technological advancements, Sailun has positioned itself at the forefront of tire technology and the exploration of tires striving to build a technology-based enterprise. Their R&D center concentrates on the many attributes that affect product performance: compounding, synthetic rubber technology, competitive analysis, tire design and simulation modeling.
With equipment and building capabilities that match tier one global manufacturers, Sailun boasts multiple well-established R&D centers globally: China (R&D Center HQ), Vietnam, Europe and Canada. Each dedicated R&D center provides a deeper understanding of the local user’s needs and utilizes cutting-edge technology to form a global R&D system. Sailun’s individual R&D centers also cover market research, product planning, formula development and process
development systems, from structural design to product verification testing, each with independent research and development capabilities. As the specialty tire division of Sailun, such support and commitment of the R&D team also emanates throughout MAXAM Tire.
Under Sailun’s groundbreaking vision, all engineering and R&D teams are fully integrated with factory quality assurance and product development operations to optimize quality and
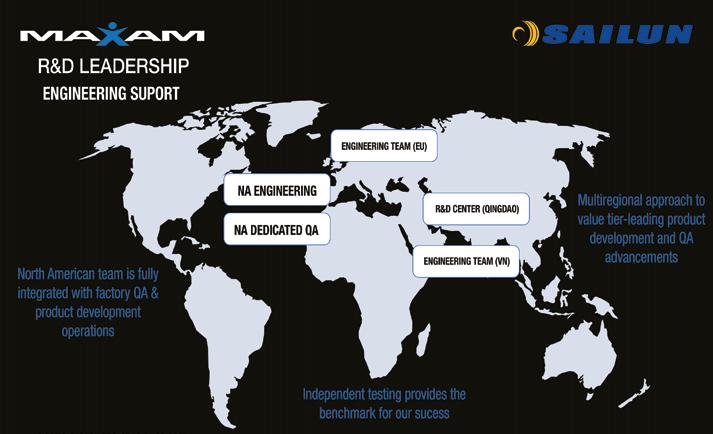
performance. Centering around intelligent and advanced manufacturing, Sailun ensures its standardized quality management in strict and strategic processes with professional finished equipment, complete transparency on quality including procurement reports and digital production management. In addition to a strict process on quality management, Sailun schedules routine internal quality audits and certification management to meet global compliances and protocols.
Sailun and MAXAM believe in continuous product testing and review, inspiring new products, development and techniques. As automotive, trucking and specialty equipment manufacturers continue to evolve, Sailun pushes for innovation and takes quantum technology leaps by designing tire building equipment and machinery that streamlines manufacturing with automation. It is this philosophy that allows Sailun to continue growing and accelerating its position as a global leader.
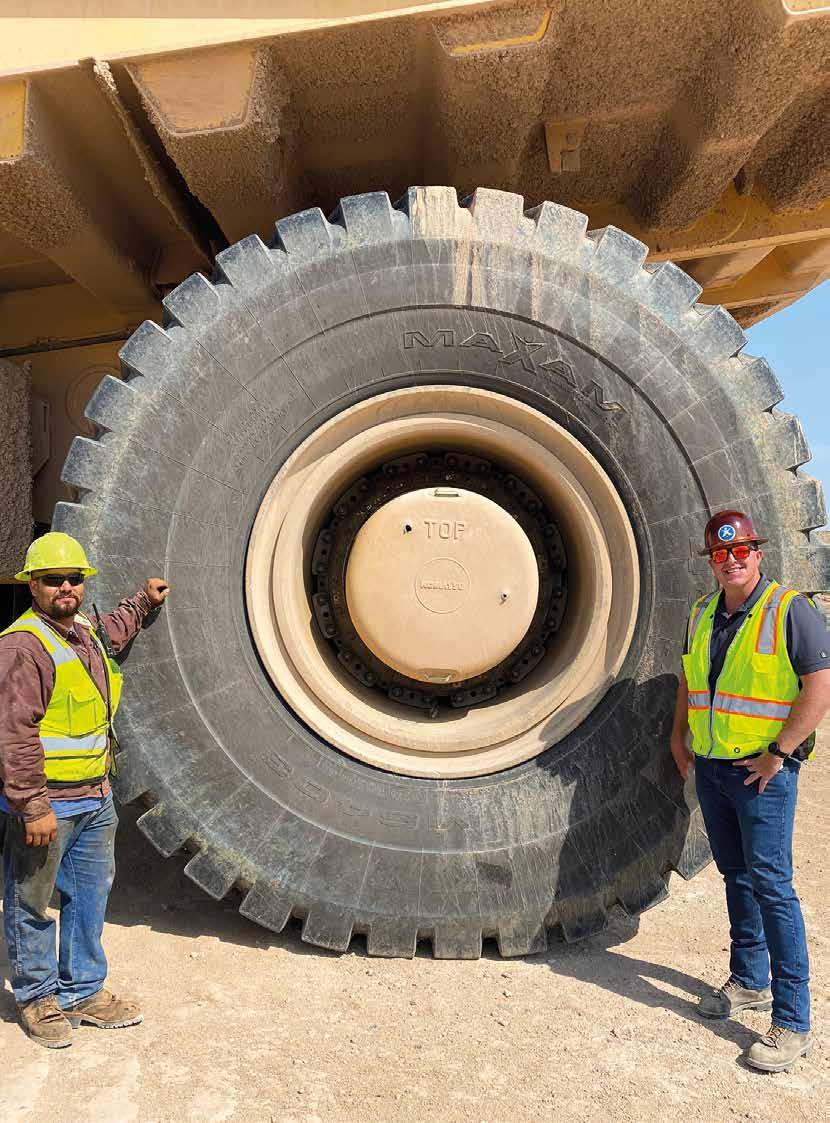
MAXAM OTR Achievements and Success
With years of proven performance, MAXAM Tire has built a strong reputation in the off-the-road and specialty tire market through leading-edge quality, reliability and exceptional value. Our team’s commitment to product quality, reliability and value has been acknowledged by some of the top original equipment manufacturers, including CATERPILLAR®. MAXAM has multiple OTR products that have been certified by CATERPILLAR® on medium wheel loaders and are recognized as one of the best performing tires for their equipment.
One of the key accomplishments in this certification is MAXAM’s 875/65R29 MS405, validated and approved for CAT® 982M Medium Wheel Loaders. Featuring a deep E4/ L4 lug pattern that combines excellent grip, stability and performance, the MS405 provides users a solution that meets all harsh demands. Developed with a cut-resistant tread compound and robust undertread, the puncture resistant MS405 allows superior productivity and minimal downtime. Thoughtfully designed to minimize vibration at higher cycle speeds, the MS405 provides loaders, graders and earthmovers the lowest cost-per-hour.
In addition, MAXAM’s MS302 is also approved as a factory fitment option on CAT® 950GC, 950L, 950M, 962L and 962M in certain regions. The MAXAM MS302 features a rugged E3/ L3+ heavy duty design for maximum traction and high heat resistance on loaders, graders and earthmovers. The MAXAM MS302 aims to minimize vibration at haul speeds and provide the lowest cost-per-hour, while the durable cut and tear resistant rubber compound eliminates the constant threat of downtime due to tire damage.
The rigorous validation process to achieve OEM approval is part of MAXAM’s commitment to continue bringing quality solutions to various specialty tire markets. Furthermore, MAXAM has the support of the over 1,800 strong and growing Global Dealer Servicing Network, allowing for ease of access to the full product line.
Innovative Engineering & Our Quantum Leaps
As mining applications continue to evolve, our innovative engineering team continuously develops new products utilizing leading technology that focuses on performance, safety standards, reliability and quality. By leveraging extensive research and testing in multiple mine locations around the world, our engineering team pays specific attention to tire compounding and casing design in order to exceed site requirements and enhance durability and performance.

Understanding the customer’s needs is of paramount importance to MAXAM’s core philosophy of being a leader in advanced technology. One aspect of MAXAM’s advancement is its dedication to engineering robust compounds for specific applications. Superior rubber compounding combined with world-class manufacturing technology will result in significant performance enhancements to the MAXAM radial product lines.
The MAXAM engineering team has a dedicated rubber compound research group to continue its advancement in this sector. Working directly with the sales team, who provide customers and product performance feedbacks, the rubber compound research engineers are constantly developing new ways to increase energy and savings in mixing and polymer structure advancement. The goal of our engineering team is to have better dispersion of the element in the compound, less agglomeration and high level of polymer interaction, resulting in superior performance of each type of compound.
Available in standard, heat resistant, cut resistant and ultra-cut resistant compounds, MAXAM MINING GROUP has radial open pit mining tires fitted at multiple mine sites that deliver maximum TKPH/TMPH and lowest cost-per-hour.
Superior Compounding
Constant innovation and technological advancement are the keys that drive our business and our customer’s success. Using leading engineering, industry knowledge, customer and performance feedback and data, MAXAM engineers and R&D teams are always finding new ways to create revolutionary designs and processes to predict performance characteristics before production. As mining and construction machinery continues to advance in delivering faster speeds, greater payloads and technological controls, so too must the tires. The pace of change in mining applications is ever-increasing, presenting new challenges to the tire manufacturers. At MAXAM, we take such formidable challenges as a push to continue our innovation and improvement on product performance with uncompromised value and costper-hour.
One of the pillars that established MAXAM’s reputation and standards on innovation is its compounding technology and process. Behind its compounding production, MAXAM works closely with EVE Rubber Research Institute (EVERI), a renowned rubber institute that collaborates with the largest research centers in polymer materials. EVERI is dedicated to the development and recycling of new types of rubber such as functional and green rubber, as well as employing ATCM technology (Advance Technology for Compound Manufacturing). Founded
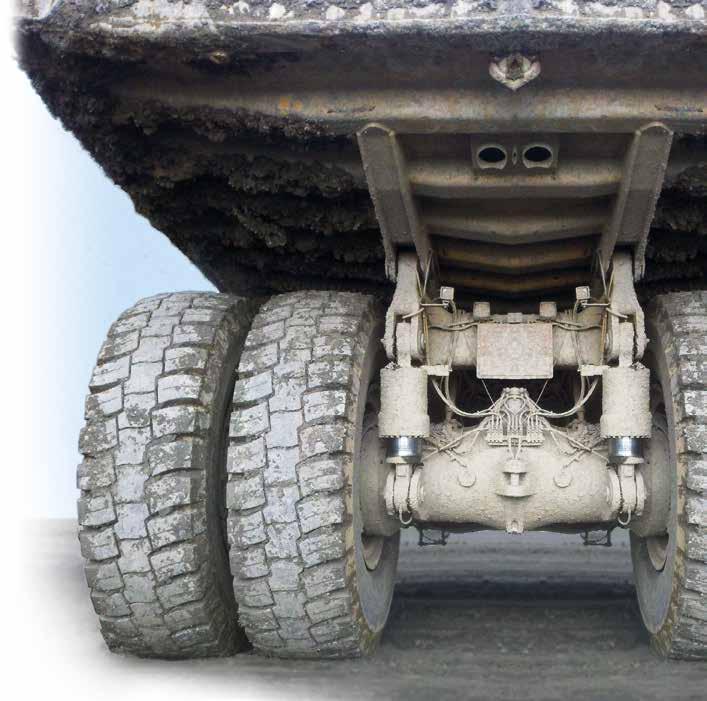
in 2013, EVERI serves as an important platform of innovative development.
EVERI has established several mature research areas including new rubber materials, environmentally friendly processing technology and tires, as well as research into new functions for rubber. EVERI owns close to 600 large-scale, sophisticated equipment patents including rubber mixing and processing equipment, vulcanized rubber testing equipment, material analysis and detection testing equipment etc. More than 120 experts from different fields work in EVERI, covering multiple areas including fundamental research, material research, product development, equipment research, technical service, and analytical testing.
With its rigorous innovations and pioneering vision, EVERI has obtained dozens of patents in the rubber and tire field. Several of its achievements have now become the industry standard. According to reports from the Spain IDIADA (the EU authoritative testing institution) and USA SMITHERS lab (the U.S. authoritative testing institution), EVERI has reached an internationally advanced level in the field of developing sustainable technology in manufacturing and providing functional rubber materials. EVERI is the first scientific institution satisfying the BB level of the EU tire label.
Recently, EVERI announced a joint technology agreement with Versalis, a major producer in the polymers
and elastomers industry, developing a production technology for advanced elastomer compounds designed for the tire market. By leveraging top-class technology and processes, the EVERI and Versalis partnership changes the landscape in the tire industry and allows MAXAM‘s tire production to set the new standard in manufacturing and innovation. With capabilities to elevate product quality and to add value to the supply chain, such technological innovation in the elastomers industry plays a fundamental role in ensuring MAXAM’s leading compounding position in the marketplace.
After production, MAXAM’s tire compounds pass through rigorous quality control measures. This control also applies to the testing of raw materials before entering the production process. State-of-the-Art Manufacturing
To meet our engineering team’s advanced innovation, the MAXAM MINING GROUP invests heavily in our state-of-the-art manufacturing process. With five fully owned and operated factories that have proprietary and patented manufacturing processes, MAXAM continues to pioneer advances in technology across all processes. All MAXAM radial tires are built in positive crown drums that build the tires in a shape closer to its finished profile, ensuring components are minimally disturbed during the curing process. To further ensure accuracy in the manufacturing process, MAXAM also uses Electron Bead Processing to increase molecular cross-linkage for improved component accuracy and stabilization during the manufacturing stage. The process also includes laser contour scanners and automated strip winders for absolute precision and consistency in all MAXAM tires.
MAXAM’s technical excellence is supplemented using premium materials. MAXAM owns its natural rubber processing plant in Asia to fully
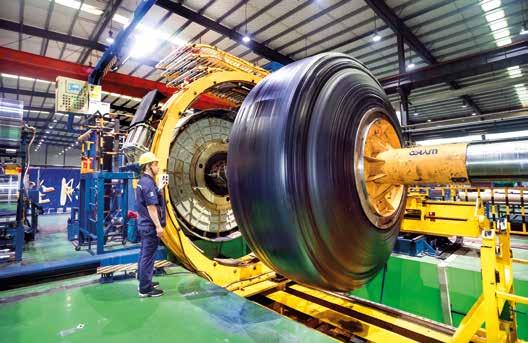
control the quality of our rubber in addition to working with the top-tier raw material suppliers. Combined with its highly skilled workforce, MAXAM manufactured radial tires perform well even in the toughest applications and site requirements. “Quality that drives productivity” is one of the fundamental beliefs at MAXAM and this belief is applied on every level, from manufacturing and logistics, to planning and distribution. The quality of the customer’s experience is of paramount importance to MAXAM and their satisfaction is what drives the company and its success.
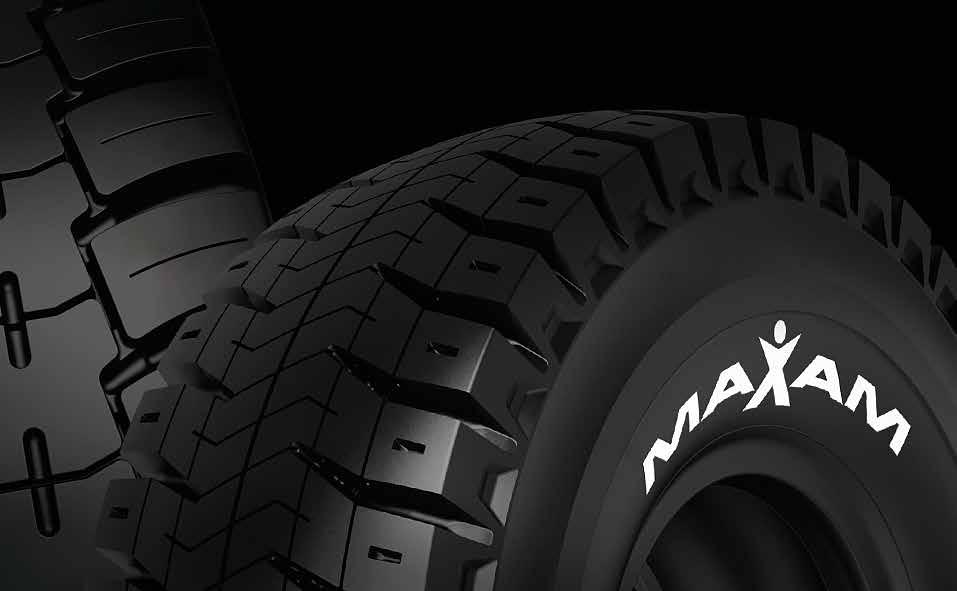
Raw Materials and Mixing Equipment
As a technological leader and innovator, MAXAM invests heavily in raw materials and mixing equipment as these processes play a vital role in product consistency and compound uniformity. To minimize errors and maximize productivity, MAXAM has created numerous patented automation and intelligent systems for our mixing processes. In one MAXAM factory alone, there is an operation with over fifteen mixers with different volumes (150-430 liters) capable of various mixing speeds.
A key mixing process that contributes to our product’s final quality is intelligent mixing, an automatic weighing and production system with bar code scanning, small chemical weighing and raw rubber cutting system. This advanced automation ensures: • improved uniformity of final product • tracing the material by bar code scanning • lower discharge temperature of the rubber compounds • increased accuracy and high-speed dosing of each chemical component • shorter mixing time and higher efficiency
Working with the R&D and engineering team, MAXAM manufacturing was also able to advance its raw material process significantly. MAXAM has created several systematic methodologies in perfecting its compounding and overall quality: • liquid rubber mixing phase (high-tech process of rubber mixing), providing masterbatch produced with continuous liquid phase. Mixing with natural rubber latex and carbon black slurry • high styrene content of SBR rubber for improved cutting resistance • customized carbon black for improved wear resistance and balanced tread compound heat generation • tear resistant resin for improved tear resistance for cut resistant tread compound
Visit MAXAMTIRE.COM
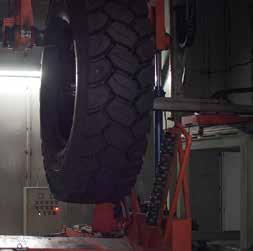
Strict and Rigorous Quality and Testing

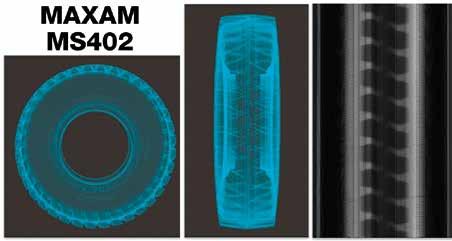
Every MAXAM MINING GROUP product goes through comprehensive lab and field testing with seamless procedures that feature strict quality control. All MAXAM product specifications, processes and tolerances are established and controlled by its group in all manufacturing facilities, ensuring product consistency. MAXAM’s quality assurance standards are maintained through technologically advanced equipment and skilled technicians.
Utilizing advanced shearography technology, all MAXAM utilizes EBP (Electron Bead Processing) as part of the testing process. MAXAM mining tires go through a rigorous quality EBP is used for increased molecular cross-linkage for improved component inspection process, eliminating the chances of trapped accuracy and stabilization during the manufacturing process). air in the casing, blisters or undercuring. MAXAM also utilizes EBP (Electron Bead Processing) as part of the MAXAM mining tire goes through a meticulous process to testing process. EBP is used for increased molecular cross- ensure quality that includes a visual inspection for uniformity linkage for improved component accuracy and stabilization and defects, x-ray for tire integrity validation, shearography for during the manufacturing process. internal construction confirmation and ultrasonic measurement
Another important aspect of quality is physical testing. for construction conformity. At MAXAM, we stand behind every MAXAM ensures its mining products’ top-tier performance product with guaranteed performance as every tire instills the by conducting TKPH tests, tread endurance and bead MAXAM core value of “quality that drives productivity”.endurance tests. During the TKPH test, heat buildup in the tire is measured using advanced technology, ensuring that every product is built to Using X-ray technology to examine steel belts, every radial tire must pass strict tolerances withstand heat buildup at a site. The tread during the production process as part of quality control protocol. endurance test qualifies the integrity of tread pattern and compound. The bead MS402 Example endurance test inspects the integrity of the carcass and bead package. All the components in every tire’s physical tests play a key role in ensuring MAXAM’s tierone products’ optimum performance and quality.
Using X-ray technology to examine steel belts, every radial tire must pass strict tolerances during the production process as part of quality control protocol. Every
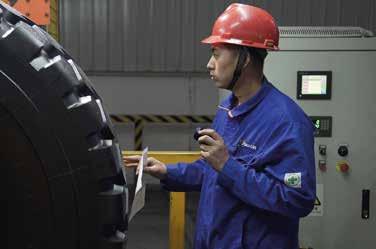

A Team that Goes Above and Beyond for Customers
MAXAM prides itself in being a business solutions provider that’s committed to the quality of the customer experience. With the mining segment as one of the toughest and most demanding industries, a team of experts with leading market knowledge is a necessity in order to provide the best customer experience and solution. The MAXAM MINING GROUP is a team of dedicated and knowledgeable experts that not only have decades of experience in the field but the ambition and drive to exceed expectations.
MAXAM has appointed the best global talent to meet the highest standards of customer experience. Each MMG team member has at least fifteen to twenty years of experience in the off-the-road tire industry with a proven record of delivering accelerated business performance and growth to our customers’ businesses. Each MMG sales member has years of experience working for top-tier tire manufacturers and dealers with the ability to provide knowledgeable support to our customers in every aspect of the mining business. To provide the best business solutions for the industry, MAXAM has selected Matt Johnson to lead the team as Vice President of MAXAM MINING GROUP.
As a highly qualified and experienced leader in managing a diverse leadership team and supply chain management, Matt believes that having the right people is the key to success. A passionate and enthusiastic leader, he focuses on building a group of worldclass teams that raise the bar for the industry. “We pride ourselves on providing solutions with the lowest cost-per-hour/ton while continuing our assistance to our customers with other cost saving recommendations and actions. We believe in fostering long-term, mutually beneficial business relationships with our customers,” says Matt.
Matt Johnson is Vice President of MAXAM MINING GROUP, a subgroup of MAXAM Tire, with responsibility for sales and support strategy implementation for MAXAM MINING GROUP globally. Matt has been with MAXAM Tire since October 2019. Prior to MAXAM Tire, he has held various field and management positions within two decades of his career in the tire industry. Matt began his career as a tire technician in a retail mining business in 1993 and advanced through multiple sales and management roles.
In the past decade, Matt led Purcell Tire’s Global Mine Group as Vice President, delivering high profit and growth to the business. He has proven to be a commercial expert who leads his teams strategically for sustainable growth. His past colleagues appreciate his ability to drive global turnaround and business development initiatives that raise sales and profit.
A highly qualified and experienced leader in managing a diverse leadership team and supply chain management, Matt believes that having the right people is the key to success. A passionate and enthusiastic leader, he focuses on building groups of world-class teams that raise the bar for the industry. Matt’s continuous drive to help build extraordinary organizations has been proven through many successes in previous leadership roles.
MAXAM MINING GROUP sets its foundation and philosophy on addressing customers’ needs and the requirements of each mine site. Every MAXAM MINING GROUP specialist works with the engineering team by learning each mine site’s requirements and goals. A strategic plan with specific products and compounds, along with expected performance and hours, is then proposed to customers for their consideration. Once a customer accepts MAXAM’s proposal and initial product placements, the company continues to make frequent visits to monitor its products for maximum assurance. Every site visit is concluded and submitted back to the customer with a data review and maintenance tips. The onsite review, proposal and monitoring demonstrates MAXAM’s commitment to its customers along with its ambition to earn their confidence. Many customers see MAXAM as more than a supplier focused on placing tires, but instead a trusted partner that delivers guaranteed performance and dedicated support.
The MAXAM MINING GROUP shares the same core values of MAXAM Tire, centering around innovation, business solutions and the commitment to provide an exceptional customer experience. In continuation to developing their long-term mutual beneficial business relationships with customers, its sales team is there during the entire journey: from in-depth site evaluations, GPS study reports, performance tracking to maintenance visits. These reports and performance evaluations are then shared with R&D and the engineering team to enable further improvements on product performance. The MAXAM MINING
GROUP’s core value in providing the relevant and ideal business solutions is applied to every aspect of its business, from sales, customer service, R&D, engineering, distribution, supply chain to manufacturing. Customer experience and feedback are the core that drives the MAXAM MINING GROUP’s innovation and advancement in performance and growth.
To differentiate themselves from other suppliers, every MAXAM MINING GROUP member is trained to gather the right information onsite. Followed up by sharing this information with the customer and strategizing an action plan, MMG has proven to be a knowledgeable supplier with “boots on the ground” experts, achieving daily established goals that the sites need.
Generally, mines have about 90 to 120 days of inventory on the ground. If the hauls change from a short haul to a longer haul, the ton-kilometer-perhour (TKPH) will most likely increase. Therefore, higher TKPH rating requires a cooler compound in the tire and/or a cut resistant compound for a lower TKPH rating. Similarly, shorter hauls require a cut resistant compound with a lower TKPH rating.
The correlation between TKPH and changes in the hauls is critical when placing the correct tire with the appropriate compound. Running the incorrect compound could lead to overheating in tires from a longer, faster haul. Similarly, the tires could also chunk out if a softer compound is placed in a harsh underfoot condition.
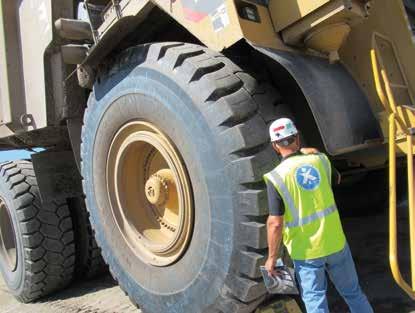
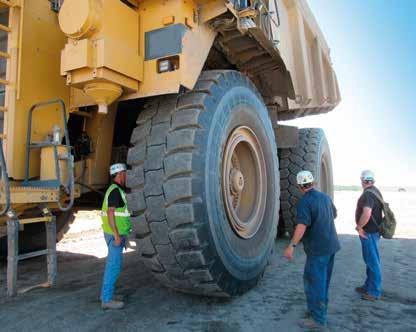

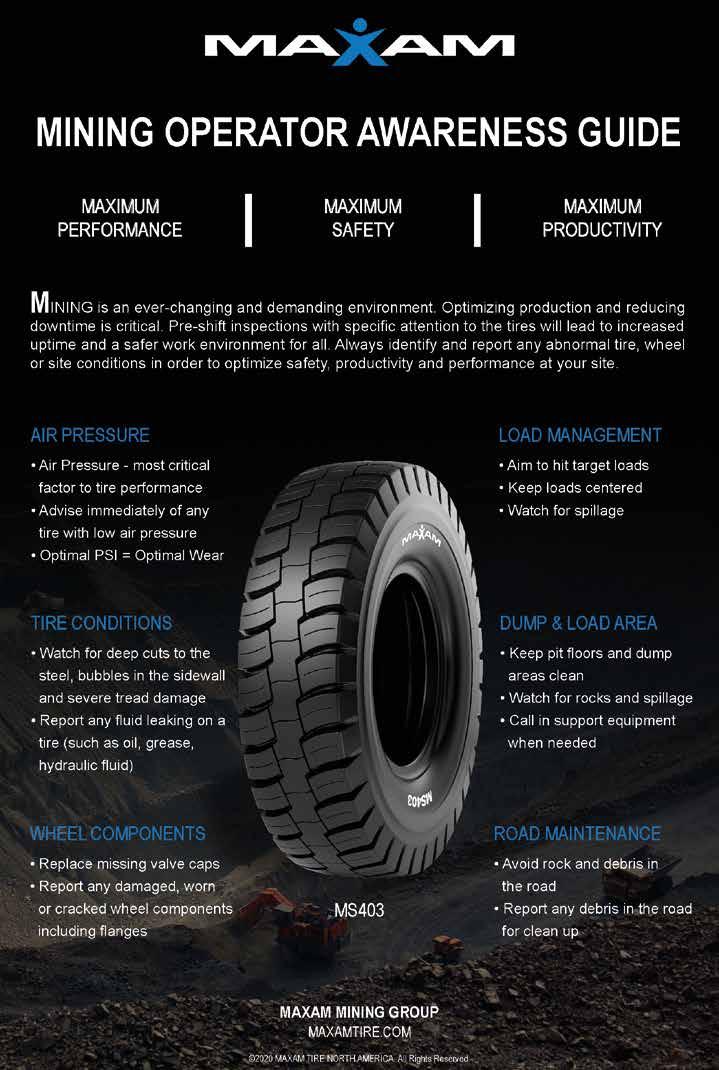
TKPH
MAXAM MINING GROUP follows the criteria below when understanding each site’s specific TKPH requirement: 1 Round trip distance 2 Number of cycles per shift 3 Shift duration, including all breaks 4 Average high temperature 5 Grades, uphill or downhill laden loads being hauled
Once this information is collected with the help of a GPS or V-Box, the numbers can be entered into the TKPH spreadsheet or the MAXAM Tire App. The TKPH requirement for both the front and rear axle will be produced and determine the best compound to be placed. Every tread pattern will have a different number depending on the design (for example, lug to void ratio and depth of the tread will determine an E3, E4 or E4+ pattern for extra tread depth).
Today, there are many options available to track tires and analyze hauls to obtain cycle data. Understanding the site and its potential development and changes in the future plays a vital role in selecting the right compound for the tire and matching the haul cycle requirements.
MAXAM Tire believes that a proper tire maintenance program and training for its customers will provide maximum productivity and tire longevity. MAXAM has developed many tools and performs constant site visits to ensure a consistent and effective maintenance program. One of the helpful tools they’ve developed is the Tire Life Indicators Chart. Each component serves a check point discussed at the driver’s monthly meetings. Acting on any one of these key indicators can positively impact the life of the tire and increase a site’s overall productivity.
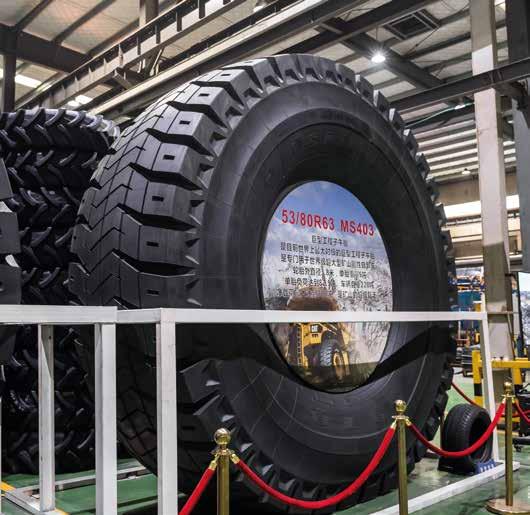
Product that Delivers the Lowest Cost-Per-Hour with Uncompromised Performance
The latest open pit mining series tires have been in development for the past six years and are the result of extensive research and testing. With a dedicated team to focus on offering full support for the open pit mining product range, MAXAM MINING GROUP offers various tire sizes to fit trucks up to 400 tons. MAXAM offers a variety of compounds and up to five tread patterns (depending on the tire size) to meet specific mining site applications. As an innovative group, MAXAM’s engineers and R&D team are working on an enhanced compounding series to further optimize higher TKPH/TMPH values, improving overall performance with maximum heat resistance, cut resistance and abrasion resistance.

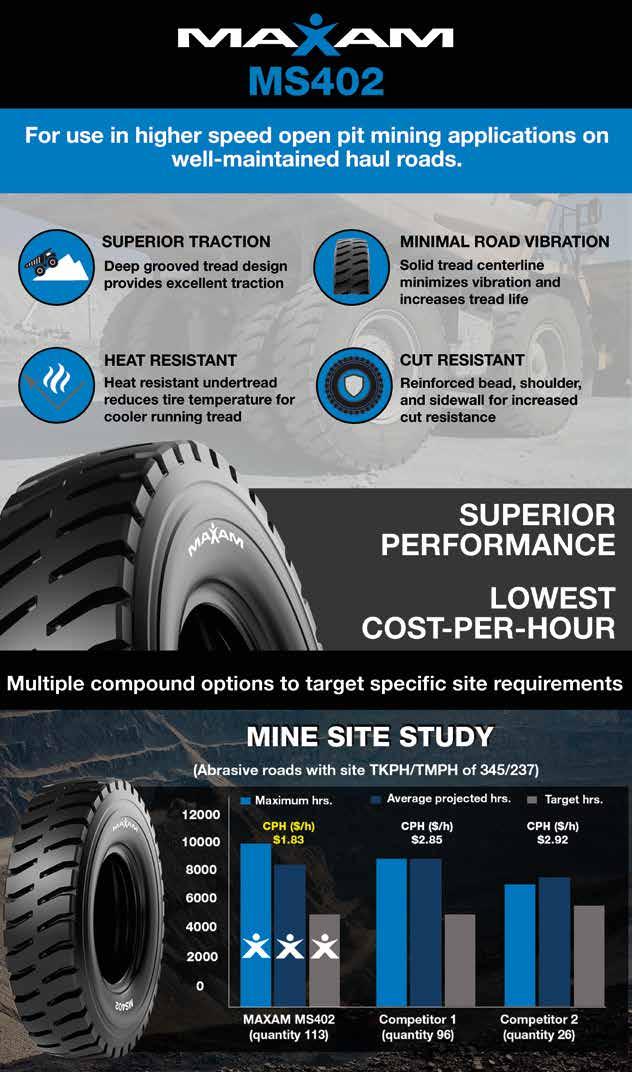
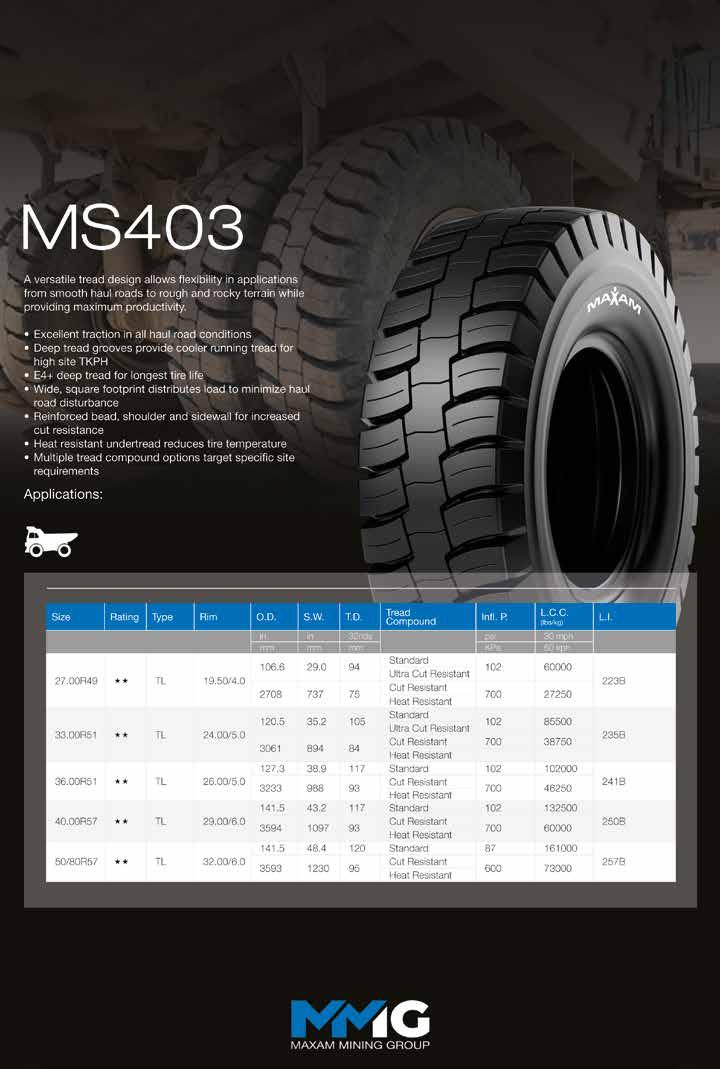
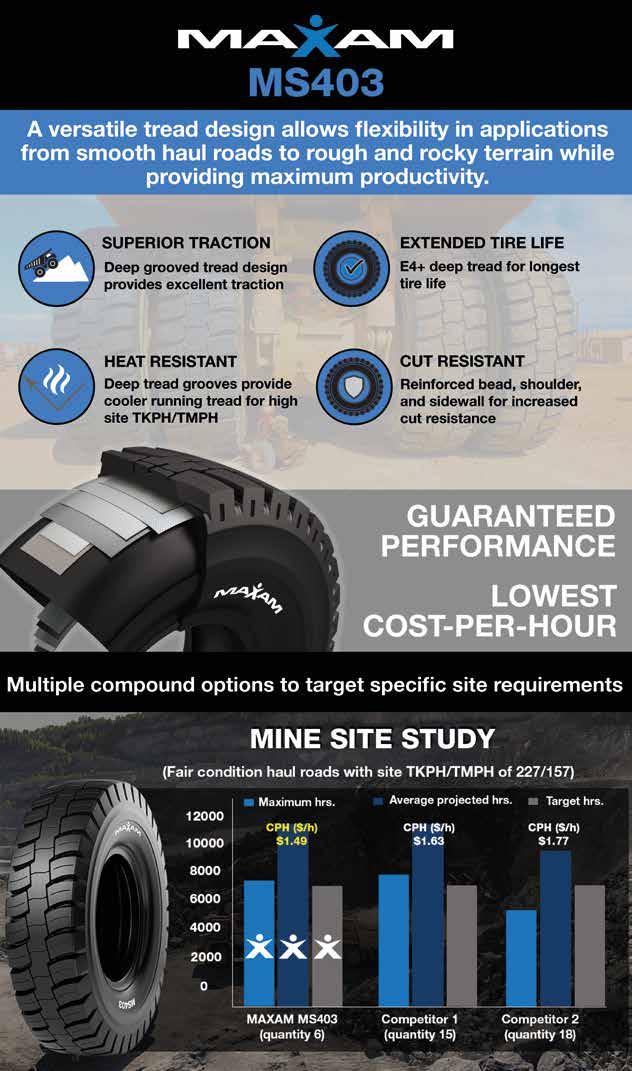
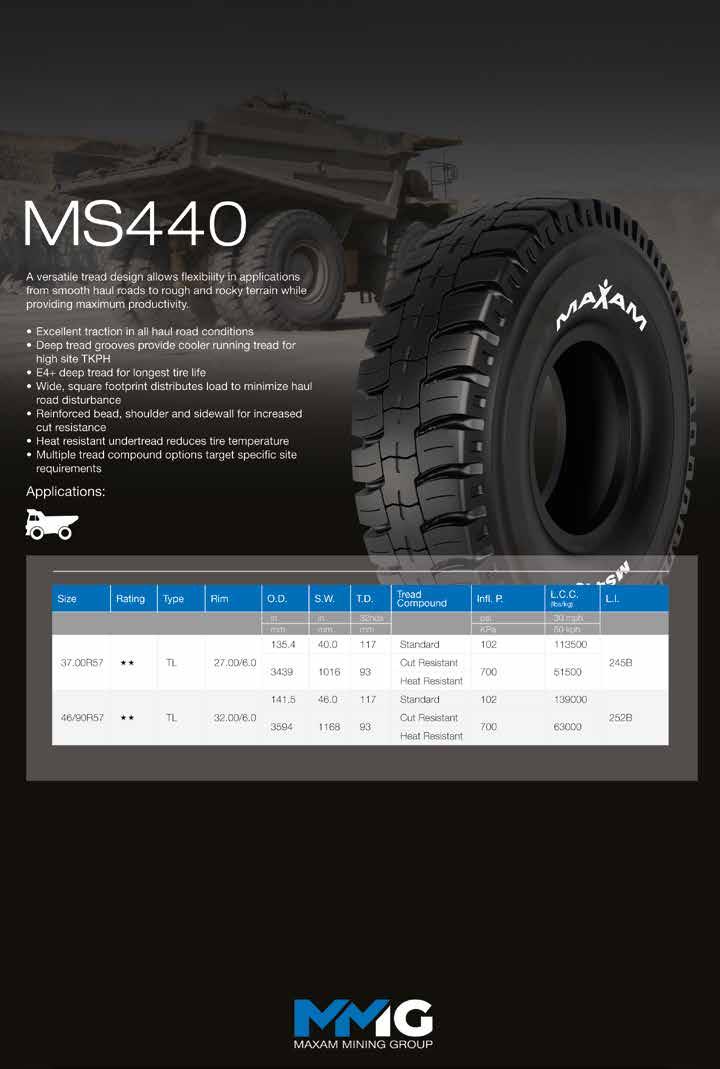
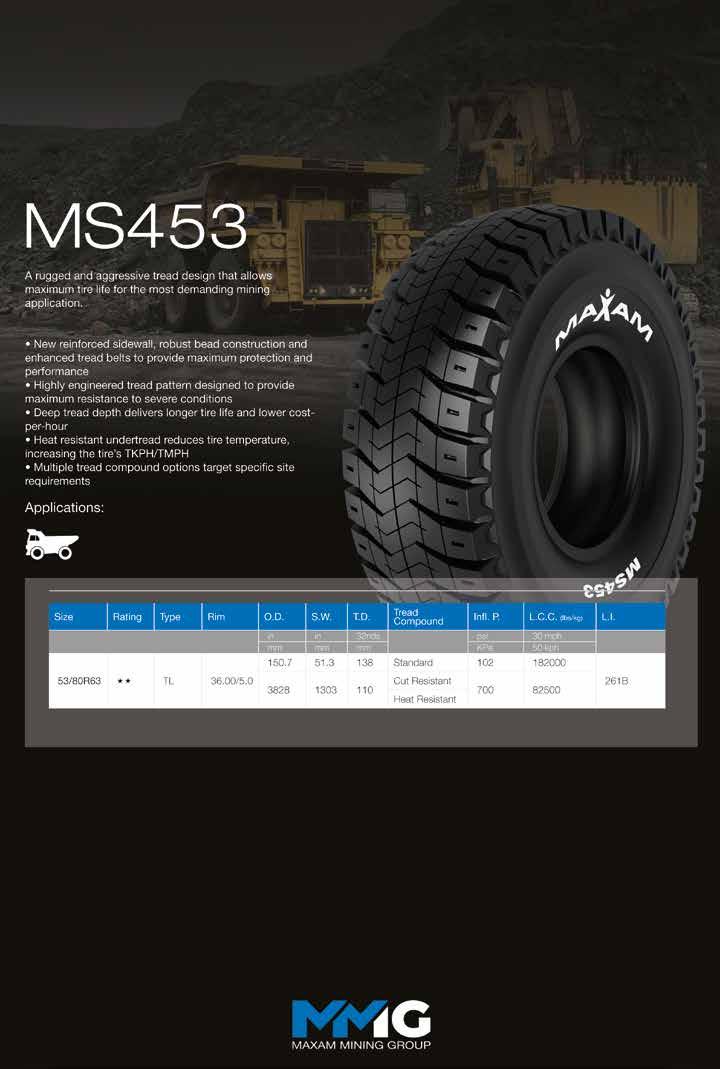
Mining Support Equipment
As mine sites continue to develop and evolve, numerous factors go into having an inclusive maintenance program in order to achieve optimum productivity each day. Having a staff of knowledgeable experts to perform proper daily pre-shift checks is a must in addition to tires that deliver the performance each application requires. As a full range tire supplier that has achieved significant performance and accomplishments in the off-the-road industry, MAXAM offers quality products for all other mining support equipment, providing a comprehensive program for mine sites across the world.
Visit MAXAMTIRE.COM


E3/L3

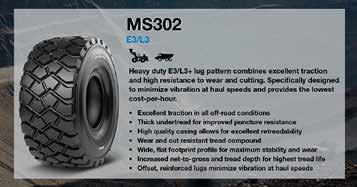

E4/L4
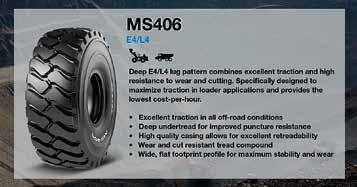
L5
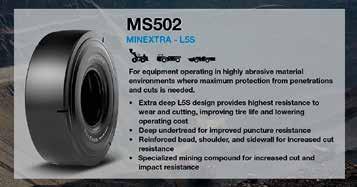
SKID STEER
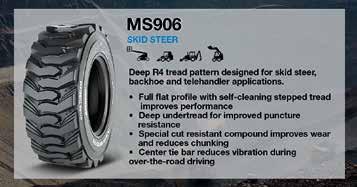
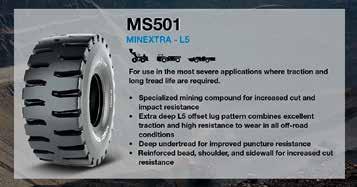
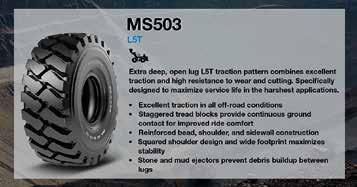
OTHERS
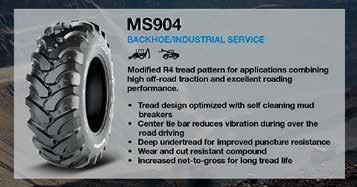
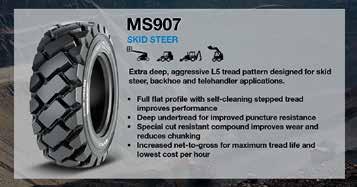
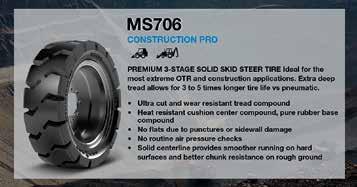
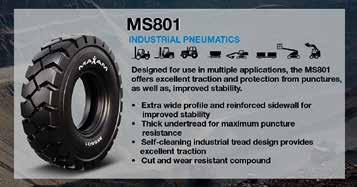
YOUR #1 OFF-THE-ROAD CHOICE FOR MINING SUPPORT EQUIPMENT TIRES
MS906
MS302
MS301
MS405
MS202
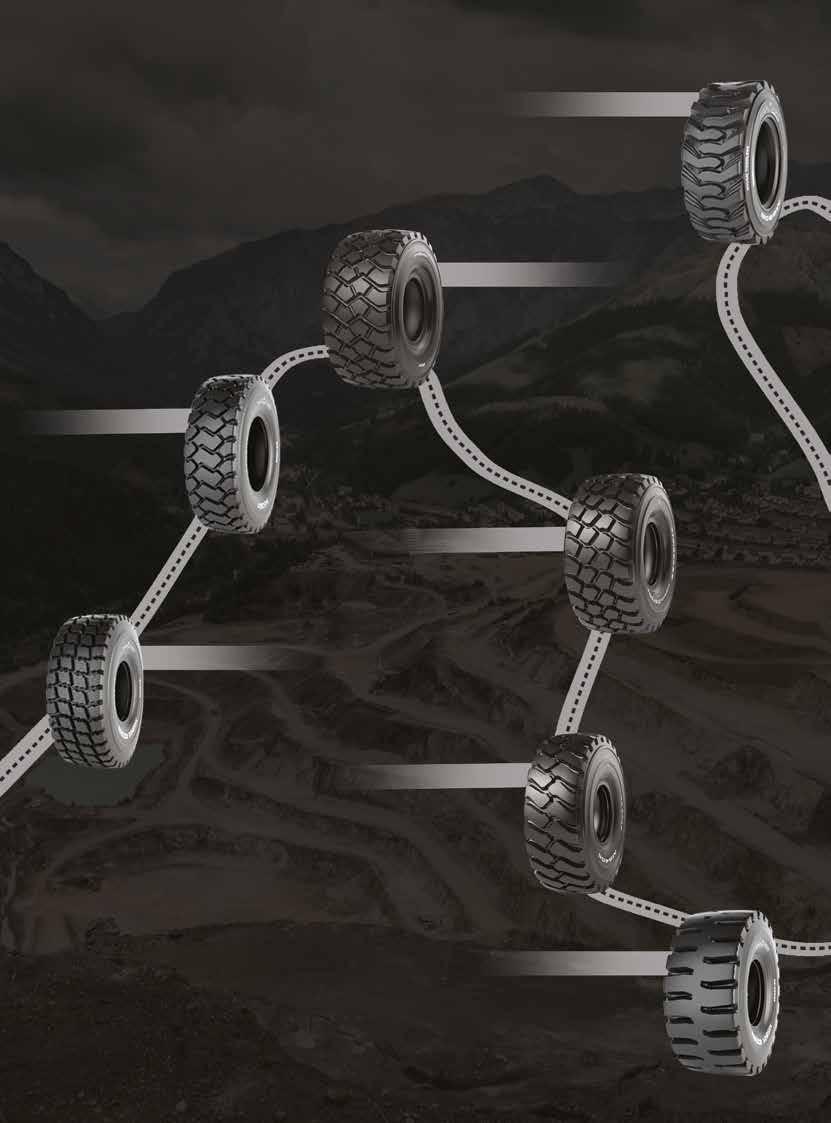
For loaders, graders, telehandlers and articulated dump trucks operating in soft underfoot conditions. Ideal for use in dirt, mud, snow and ice.
MS406
Deep E4/L4 lug pattern combines excellent traction and high resistance to wear and cutting. Specifically designed to maximize traction in loader applications and provide the lowest cost-per-hour.
MS501
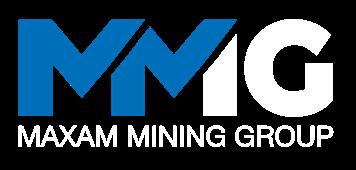
For use in the most severe applications where traction and long tread life are required.
MS907
MS503
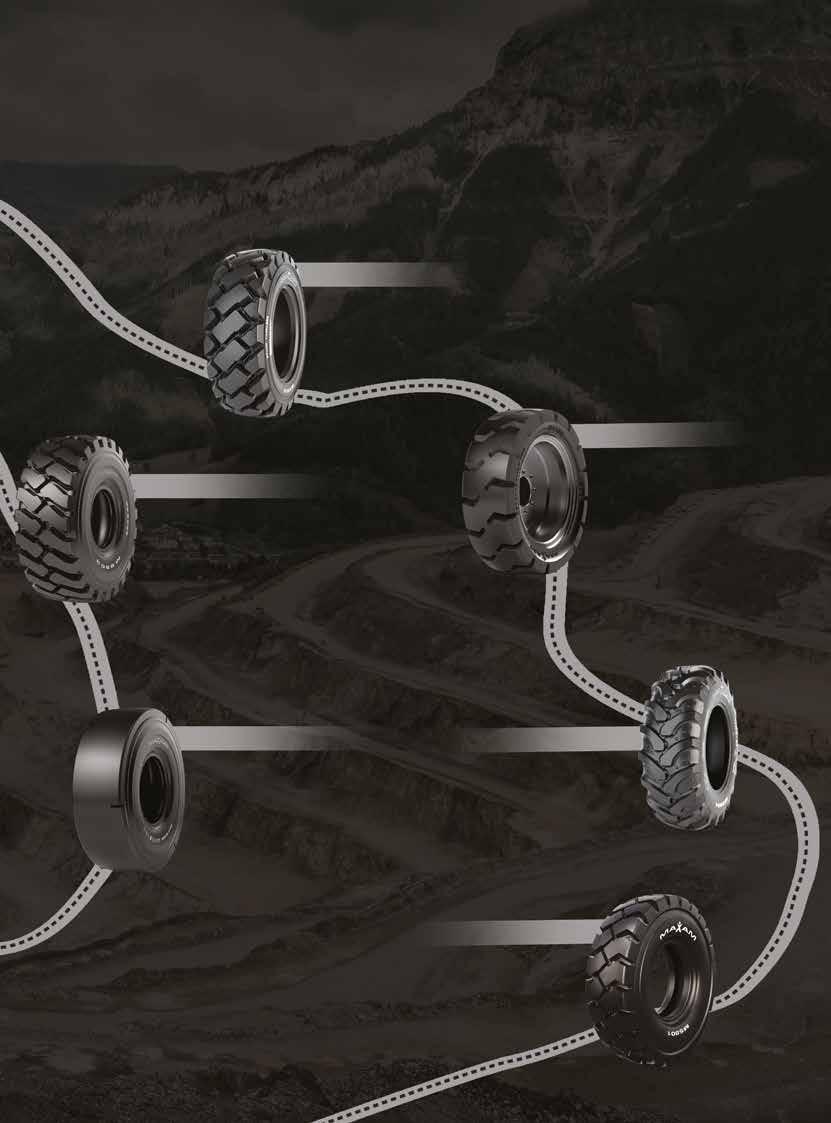
MS706
Premium 3-stage solid tire ideal for the most extreme OTR and construction applications. Extra deep tread allows for 3 to 5 times longer tire life vs pneumatic. 3-stage, 100% rubber construction.
MS502
MS904
Modified R4 tread pattern for applications combining high off-road traction and excellent roading performance.
MS801
Designed for use in multiple applications, the MS801 offers excellent traction and protection from punctures, as well as, improved stability
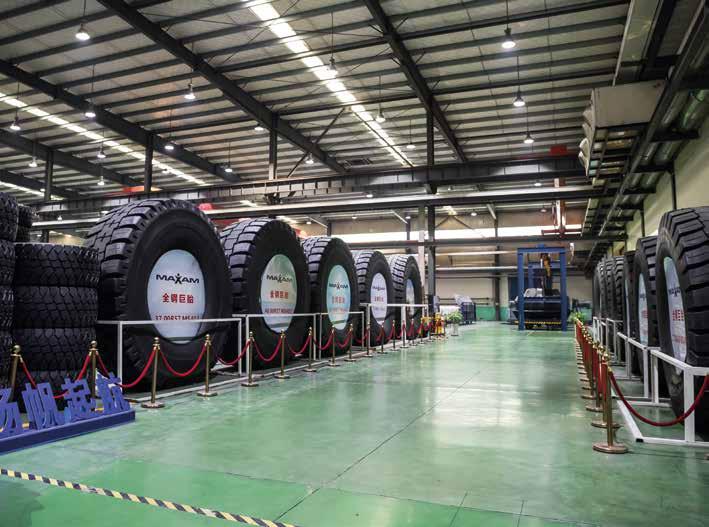
MAXAM Performance vs. Competition
In order to improve upon our products’ performance, MAXAM’s engineering and sales team are working together on every field visit to track data better. Based on much of the tracking data, MAXAM MINING GROUP’s products have provided the lowest cost-per-hour while maintaining exceptional performance on a par with tier-one competitors.
“The reality for mine sites is that our tires are just on a par with the top tier-one manufacturers in performance – we have seen 9,200 to 9,500 hours versus their 10,000 plus hours. Since our tires cost less than theirs, we are providing a significant increase in value and giving mine sites incredible savings,” says Matt Johnson, Vice President of MAXAM MINING GROUP.
Below is some of the comparative performance data from mines using MAXAM mining products. Such data is based on wear rate with cost-per-hour calculation provided.
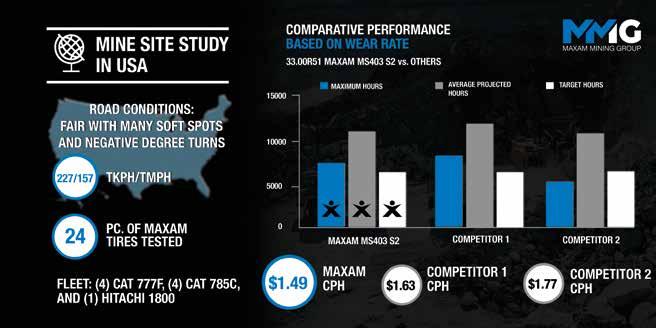
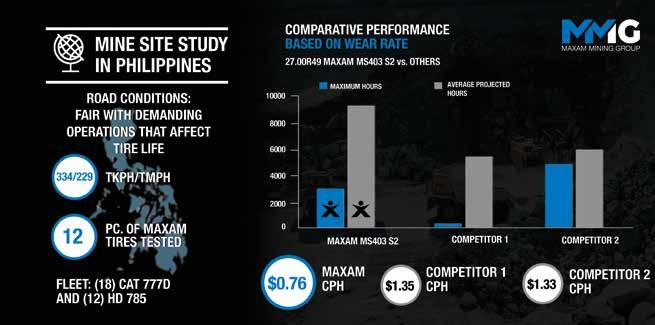


In-Depth Mine Site Study
Over the past few years, MAXAM MINING GROUP has been tracking every tire’s performance since its placement at mining sites around the world. Many customers have been pleased with the performance and value that MAXAM’s products have provided. One MAXAM customer, a large mine site located in Canada, has been achieving consistent performance and unbeatable value with the lowest cost-per-hour in the past several years. MAXAM has been tracking one specific tire pattern, the MS402, since the first tire placement back in 2015 on the two front positions.
When the program was initiated, MAXAM’s target was to reach 4200 hours. Within the first nine months of initial placement, MAXAM’S tires have been proving their performance, according to customers, while competing against leading manufacturers in the mining tires industry at the same site. Based on the data gathered in the first nine months, MAXAM’s results were within 15-20% of tier-one manufacturers’ performance but at much lower cost-per-hour. In the first two years of placement, MAXAM has received excellent feedback and has positioned an additional 124 tires (112 units of the MAXAM MS402 and 12 units of the MAXAM MS401). By August of 2017, MAXAM MINING GROUP held approximately 75% of the entire CAT® 777 fleet in this mine.
Below is a brief data summary that shows MAXAM’s product vs. competitors.
PERIOD
January 2016 - September 2016
2015 - 2020 BRAND/PATTERN
Competitor 1A
Competitor 1A
Competitor 1A
Competitor 2
MAXAM MS402
MAXAM MS402 COMPOUND
Cut Resistant
Cut Resistant
Cut Resistant
Cut Resistant
S2 (Cut Resistant)
S2 (Cut Resistant) # OF SCRAP TIRES
11
6
1
18
5
113
AVG. HOURS
4972
3611
2748
3404
3687
6175 S/HOURS
2.85
2.81
3.82
4.65
2.33
1.38

Visit MAXAMTIRE.COM
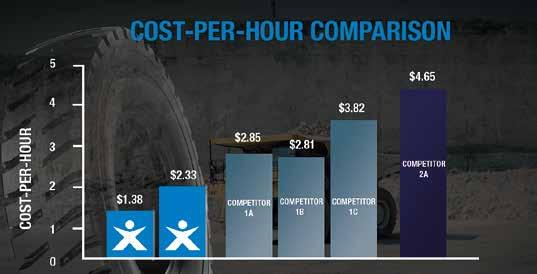
Based on the data provided above, below is the calculated result on cost-per-hour comparison.
Based on the data provided, below is the result on average scrap tire percentage.
Below indicate reasons of tire removals at the site from September 2015 to February 2020.
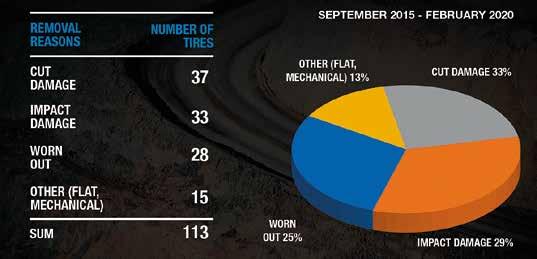
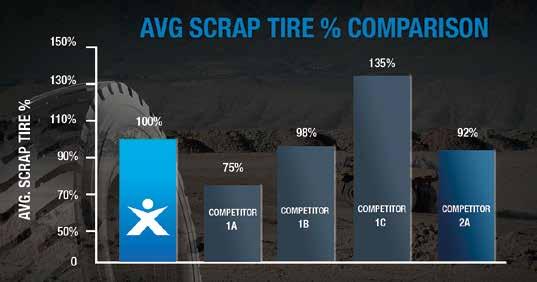
In conclusion, MAXAM has delivered products that performed beyond its customers’ expectations and continues to provide superior value to the mine with the lowest cost-per-hour. Overall, MAXAM’s products have reached 11,310 hours, delivering performance and tire life well beyond the initial 4200 target hours. There are no tires removed from service due to product issues. In addition, the nine installed tires are still in service, providing an average of $1.38 costper-hour, lower than any other manufacturer’s products.
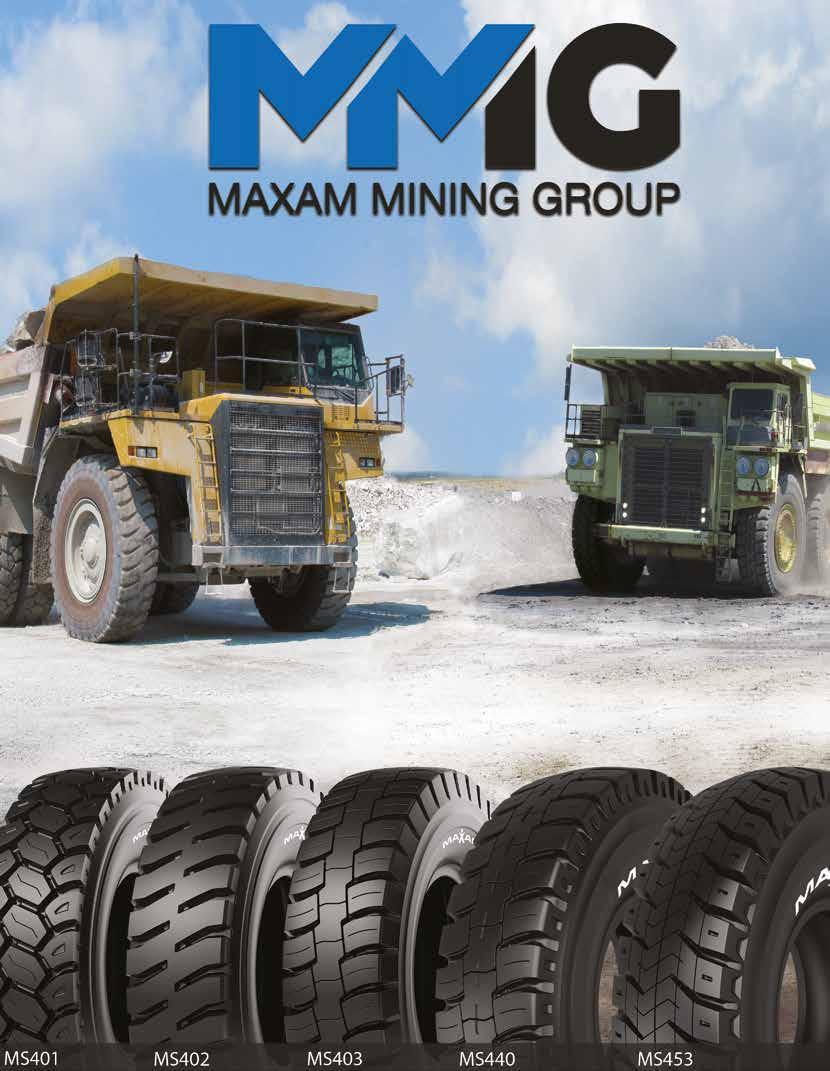
Why Choose MAXAM MINING GROUP?
In today’s competitive market, mining customers are looking for other viable large haulage tire options. With only a few tire manufacturers dominating the global haulage wheel segment, entry for a new player in the industry can be challenging. Upon initiating its mining program with prospects and customers, MAXAM MINING GROUP is focused on building confidence and trust in its partnerships by providing a full-scope analysis on each site’s requirements. With such a detail-oriented and dedicated team focused on fostering successful business relationships, along with guaranteed performance and products that deliver the lowest costper-hour, many MAXAM customers have turned to MAXAM MINING GROUP as another viable option for haulage and loading tires.
MAXAM MINING GROUP is currently working with many mining, aggregate and construction companies globally. By conducting in-depth site studies to ensure proper compound and product placements, following up with frequent monitoring and data performance, MMG is earning the respect from a broad customer base. They have positioned MAXAM as a trusted supplier and advisor that does more than deliver products with guaranteed performance - MAXAM is a true business solutions provider.
With a full range of off-the-road and other specialty products, MAXAM MINING GROUP specialists are always finding solutions to maximize customer’s savings on all the support equipment. While larger haulage tires remain an expensive investment, the expense and maintenance on the support tires can be far greater than the cost of larger haulage tires. The MAXAM team is trained to look for potential solutions to address any tire
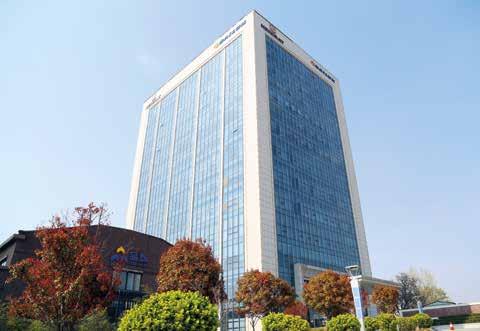
application, from big equipment to forklifts in warehouses.
One example was at a mine site that runs ash trailers. They were changing out tires about three times a year per wheel position, making the ash trailers’ tires one of the highest cost-per-hour investments. After analyzing the operation, MAXAM’s proposed solution was to change out the existing tire and rim and replace with a different size tire and rim. The customer accepted the proposal after the confirmation was made by the trailer manufacturer and that the trailer performance would remain steady. Since this change two years ago, the customer has projected a span of at least three years without removing the trailer tires. This move has dramatically decreased the ash trailer’s cost-per-hour and increased the site’s overall productivity. Providing solutions to customers with quality tires and knowledgeable technical support are just a sample of the key differentiators that make MAXAM Tire a viable choice for the mining industry.
MAXAM Tire is a global specialty tire supplier with a full range of products for construction, material handling, agricultural, forestry and other specialty segments. MAXAM boasts 14 haulage and support equipment models that have applications across multiple industries, bringing relevant and innovative solutions to customers in all segments. Innovative engineering, extensive testing, research and stateof-the-art manufacturing differentiates MAXAM from its competitors. At MAXAM, core values are centered around innovation and commitment to provide an exceptional customer experience. As a rapidly growing global organization, MAXAM invests heavily in its people, advanced engineering and manufacturing facilities to ensure unique business solutions are delivered to customers worldwide.
As the MAXAM MINING GROUP continues to expand globally, its customers’ satisfaction remains the foundation of MAXAM, so it continues to innovate in all aspects of the tire business. At MAXAM, it is its culture and people that truly differentiate it from its competitors. Driven by core values that are centered around innovation and commitment to create an exceptional customer experience, MAXAM’s people are committed to continued advancement and to exceed expectations. It is what makes the MAXAM difference – being your business solutions provider.