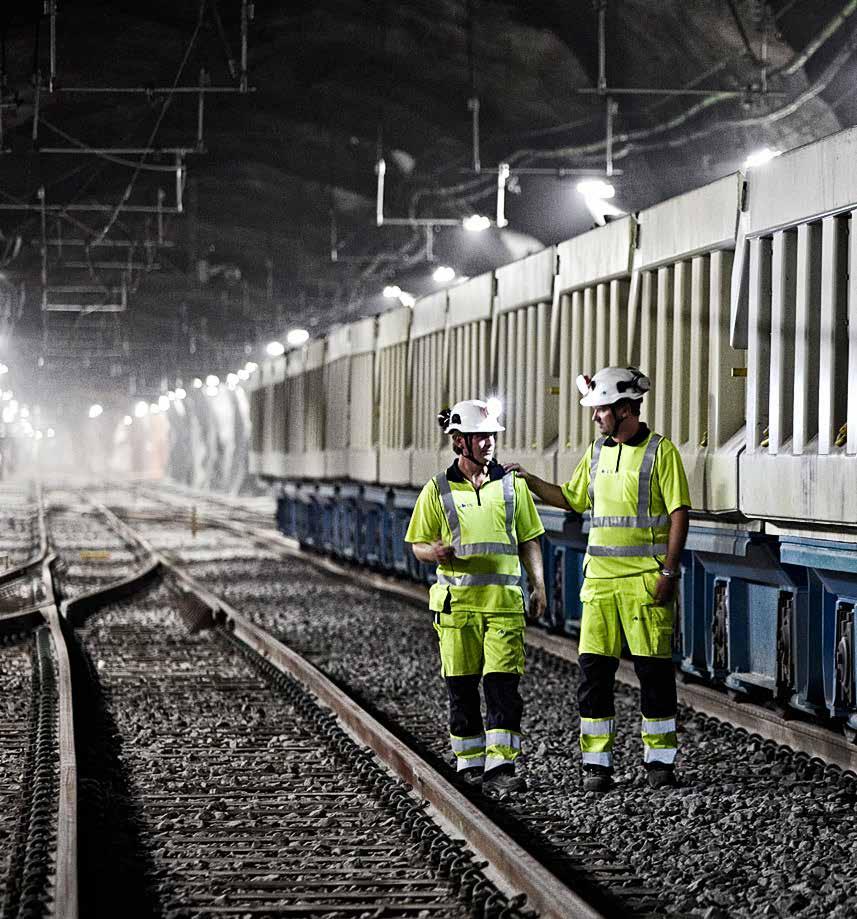
4 minute read
Midroc AB: The future of mining is remote
The future of mining is remote
Advertisement
In recent decades, the single most talked-about issue in the mining business is no doubt “automation”. A word that immediately makes us think of increasingly sophisticated information and communication systems.
Ultimately, the real key word here is rather “integration” and, in one sense, there is nothing new about that. To meet the ever-present need for productivity and workplace safety, especially underground, the world’s mining operators have always strived to optimize their production processes. Which, in turn, have always called for the bird’s-eyes point-of-view. And an integrated outlook, ensuring that every step along the production process contributes to a smooth, integrated workflow. The world’s most sophisticated automation systems and processes are, to a great extent, built on decades of more or less universal mining challenges, and a wealth of hands-on experience. A true pioneer in both automation and integration is LKAB in northern Sweden. Over the past 40 years or so they have paved the way for modern methods, combining the never-ending chase for competitive productivity with environmental awareness and innovative solutions for workplace safety.

Simplicity from A to Z
During the pioneering years of automation, LKAB made the most of the digital technology available at the time – which, by today’s standards, was anything but impressive. Since then, information and communication systems have developed way beyond anybody’s wildest expectations, and the world’s suppliers of mining automation systems are continually integrating new functions and features to simplify the operators’ workday. The one remaining challenge for many operators has been to make the systems provided by different companies talk freely with each other. True end-to-end integration of best-in-class equipment. And now we are getting there, one step at a time.
Midroc Remote Mining
Midroc Automation has been responsible for train control and parts of process control in some of the world’s largest underground mines. LKAB Sweden hired Midroc for efficient logistics at the transport level at 1365. This assignment paved the way for Midroc also being hired by the world’s largest gold mine in Indonesia – Grasberg. MIDROC’S operations in automation have been developed for more than a decade. The customer base is wide, from pharmaceutical industries to process industries and mines. Midroc performs electrical design, programming, and systemization regardless of which platform the customer uses for its control.
the future of mining
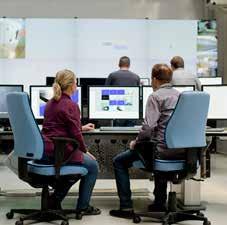
Kiruna - Sweden
When LKAB planned for a new main level in the Kiruna mine, a goal was far-reaching automation for high productivity. Seven driverless trains on the main level would transport the ore from 38 loading points. Midroc was hired to deliver the process control system Siemens PCS7 and the train control system Interflo 150. Midroc was responsible for all control from the trains being loaded at a drop, emptied automatically in emptying mode, even the ore being crushed. All this is managed from the control room on surface enabling LKAB to optimize the transports, with the video systems and screens that are the operators’ work tools.
Indonesia
The solutions in Kiruna were so good that they inspired the operators of the Grasberg mine when the open pit mine was to be replaced by an underground mine, located in Papua, Indonesia. Representatives from the Grasberg mine visited Kiruna for inspiration and really liked the solution.
“We were contracted to develop a similar solution as in Kiruna,” says Magnus Emanuelsson, the senior project manager, who previously was the project manager for the commitments in Kiruna. “In addition to eleven trains, the ore is transported by truck underground and we have built systems to load and optimize truck transport as well. Every day, 240,000 tons of ore are mined, 2.5 times more than in Kiruna, that is.” Midroc has designed three control rooms located outside the mine for Freeport. With joy sticks, the operators remotely handle both loading and rock breaking. The train dispatchers control the driverless trains. The communication is via fiber and wireless. Not least, the camera systems are very extensive, where everything that is controlled is also monitored, from loading all the way to the conveyor belt towards the concentrator. “The systems we have delivered also include traffic systems for all trucks, cars and buses that drive shift teams in and out of the mine. Ventilation on demand, gas and air quality monitoring in the mine is also included in the control,” says Magnus Emanuelsson. The Grasberg mine is the world’s largest gold mine and the third largest copper mine. Midroc Automation is happy to take on assignments for everything from small problem solutions to large turnkey deliveries including hardware. “The global technical competence from several industries and several system platforms is one of our strengths,” Magnus concludes.

the future of mining
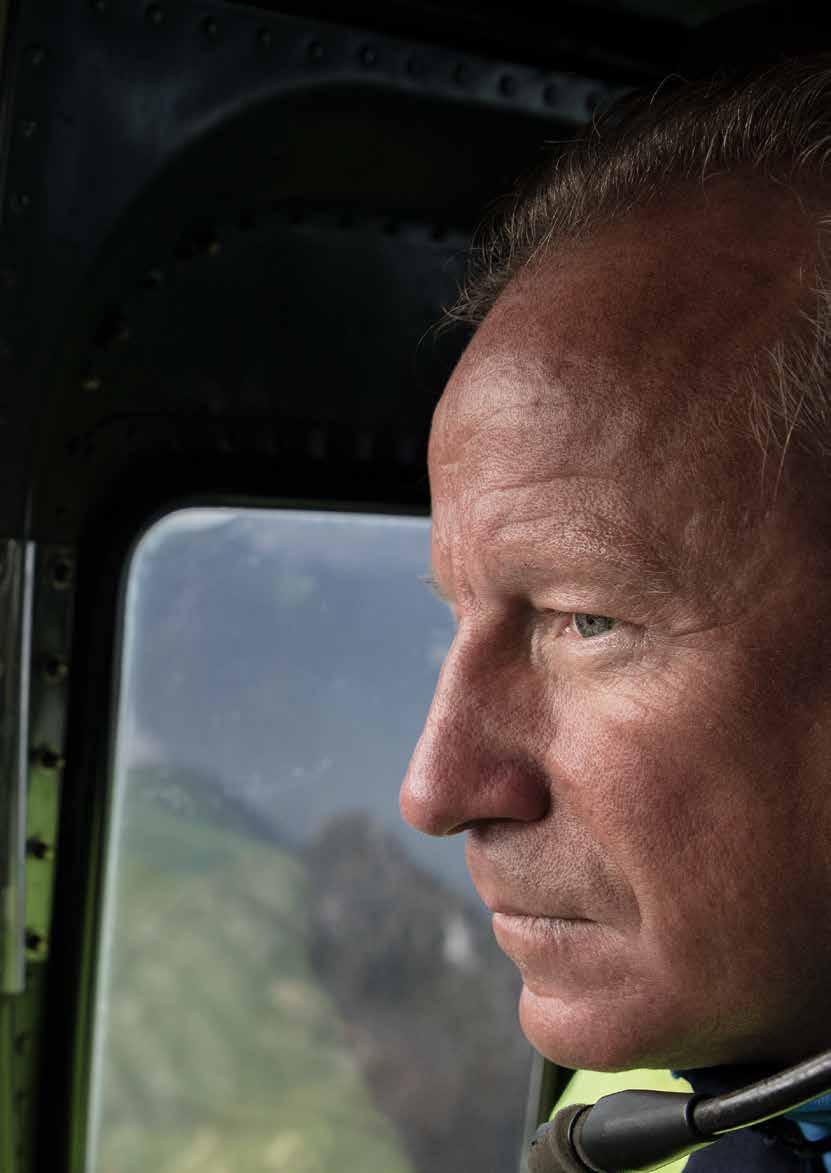