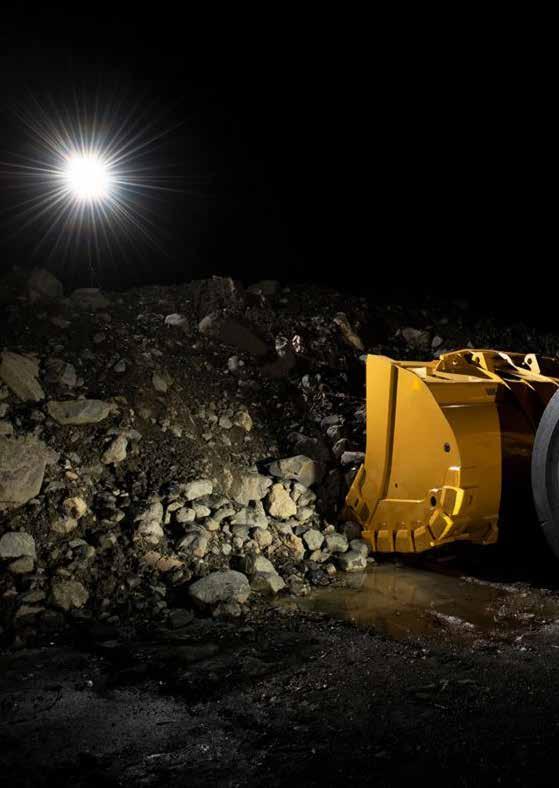
12 minute read
Caterpillar: Brand building
caterpillar
brand building
Advertisement
Caterpillar offers more equipment for mining than any other manufacturer. Its legacy of almost 100 years of knowledge and expertise combines with the latest in innovative technologies, wall-to-wall services, financing and a legendary dealer network, to produce a unique mix of solutions to meet sitespecific needs. Martin Ashcroft finds that when customers choose Caterpillar, they get more than the iron.
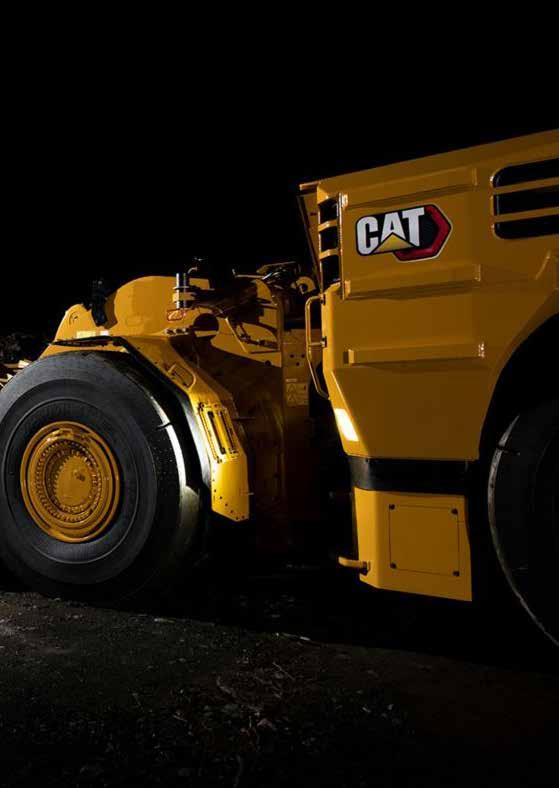

Caterpillar Tractor Company was created in 1925 by the merger of The Holt Manufacturing Company and CL Best Tractor. With sales and revenues of $41.7 billion in 2020, Caterpillar Inc is now the world’s largest manufacturer of construction and mining equipment. The Cat® brand itself was not registered for another 25 years, but it has since become the cornerstone of the Caterpillar brand portfolio.
The best brands have a universal quality, yet they also make a personal, emotional connection. Everyone knows Caterpillar. Tough, reliable, rugged, state-of-the-art, are words that immediately spring to mind. But why? I’ve never driven a dozer or a dump truck, let alone operated underground machinery, yet I perceive them to be such. How do they do that?
Cat® is literally everywhere. You see the logo on clothing and items of personal adornment, not to mention phones, watches and toys. Licensed Cat brand products are sold in 150 countries and it’s said that over 50 million Cat items are purchased globally every year. Cat products can be purchased online from branded websites or in over 100 dedicated Cat brand stores as well as 100,000 other retail outlets.
The Caterpillar brand of mining equipment is geared towards total cost of ownership or the promise of ‘total life cycle value’. Cat products are designed to be reliable, durable, and of superior quality, allowing for multiple rebuilds, ease of serviceability, reparability and outstanding support, provided almost exclusively by Cat dealers – a network crucial to the brand’s sustainability.
Caterpillar offers machines, engines, components, services and solutions to meet the unique needs of a variety of industries and customers around the world. Cat® is the flagship brand for products and services, but other brands include Progress Rail, Solar Turbines, Turner Powertrain and SEM.
They’re made all over the world, too, from Brazil to China, from Europe to Australasia. The UK is one of the largest bases for
Caterpillar outside the US. Its first overseas plant was opened in Scotland in 1958 to manufacture parts for Caterpillar products being used in Europe. After playing a major role in the construction of American infrastructure, the company itself has become part of that infrastructure, with more than 60 primary locations in 25 states and dealers from coast to coast. Several of its US facilities are single source manufacturing locations for all global sales, including: • Large track-type tractors (East
Peoria, Illinois) • Large mining trucks (Decatur,
Illinois) • Large motor graders (North Little
Rock, Arkansas) • Gas turbines (San Diego,
California) • Smallest track-type tractors (Athens, Georgia) Over the years, other brands have been gathered under the Caterpillar umbrella, including Perkins in the UK, a leading provider of diesel and gas engines, acquired by Caterpillar in 1998. In 1996 Caterpillar purchased a 49% interest in FG Wilson, the Northern Ireland genset and power system manufacturer, before acquiring the remaining 51% in 1999. In Russia, Caterpillar has been operating a fully owned manufacturing facility in Tosno, near Saint Petersburg, since March 2000. The Tosno plant manufactures two models of offhighway mining trucks, two models of excavators and components for machines and equipment, which are exported to Caterpillar factories in Europe. Caterpillar has been in China for more than 45 years. Core products manufactured there include hydraulic excavators, track-type tractors, wheel loaders, soil compactors, motor graders, medium and large diesel engines and generator sets. Several Chinese facilities also manufacture components. Branding is big business, but no brand would last long if the product failed to live up to its reputation. Many elements must combine for a brand to succeed, not least of which are the parts that come together to assemble a piece of machinery.
brand building
Suppliers
In common with many manufacturers, Caterpillar has increasingly contracted its component production to third parties. The supplier base now contains something like 27,000 names. This has many advantages, including the encouragement of competition, which drives up quality and drives down prices. It also adds layers of risk, however, from supplier financial viability and business continuity to misuse of intellectual property and any number of practical difficulties which could cause business disruption, such as the ability to increase or decrease production levels in line with demand, maintain quality control and on-time delivery. For Caterpillar to remain world class, its suppliers must be world class, too, so the company takes a great interest in promoting continuous improvement in its supply base. Caterpillar actively encourages a partnership relationship with its key strategic suppliers, recognising their progress with an award under its Supplier Quality Excellence Program (SQEP). Caterpillar created the certification program to recognize those suppliers who demonstrate their commitment to excellence and drive a zero defects culture within their organizations. Suppliers are certified by meeting or exceeding stringent performance standards, including product quality and on time delivery.
Automation
There’s more to Caterpillar equipment than size and strength, of course. Its machines are also getting smarter. Automation is changing the way
brand building

mines and quarries operate, and Caterpillar now offers equipment from fully autonomous haulage systems to remote control dozers to automation technologies that can be retrofitted to competitors’ machines. Miners are keen to adopt automation. Taking operators out of hazardous areas reduces the risk of accidents, which is not only important for the people who might otherwise have been hurt – it reduces downtime, too. Mine sites that put autonomous technologies to work have experienced a number of valuable benefits, including increased productivity, higher equipment utilization and less machine damage. Cat MineStar™ System is a comprehensive suite of mining technology products, consisting of a number of configurable capability sets for both surface and underground mines that allow customers to scale the system to their needs, from material tracking to sophisticated real-time fleet management, machine health systems, autonomous equipment systems and more. On surface mine sites, autonomous trucks help make cycle times more consistent while ensuring that equipment operates within prescribed parameters. Underground, operators based in remotely-located control stations load and dump material under tele-remote control. Then, their load-haul-dump machines steer autonomously during hauling, preventing accidental contact with mine walls. Productivity is also improved through improved equipment utilization, uninterrupted by shift changes or, in underground operations, the need to evacuate areas for ventilation after blasting.
Global footprint
Caterpillar’s global reach and presence is unmatched in the industry, serving customers in more than 180 countries with more than 300 products. More than half of the company’s sales are outside the United States, and it operates over 500 locations worldwide if you count manufacturing, marketing, logistics, service, R&D and related facilities. Cat products may be manufactured around the world, but they are all assembled in Caterpillar owned facilities, following the same stringent Cat Production System at every location to ensure consistent quality. Caterpillar established its first major facility outside the United States more than 60 years ago in the UK. Today, the company employs more than 10,000 people there in 20 major facilities. The UK is one of the largest bases for Caterpillar outside the US, and its UK businesses export a significant portion of their manufactured products to a wide variety of customers and markets. The company soon opened facilities in a number of other countries in the EAME region such as Belgium, France, Germany, Italy, The Netherlands, Switzerland, Russia, Poland, South Africa and the United Arab Emirates. The EAME Region is an important manufacturing base and the largest Caterpillar distribution division outside of the United States with approximately 25,000 employees, of whom most are in the European Union within 36 manufacturing locations.
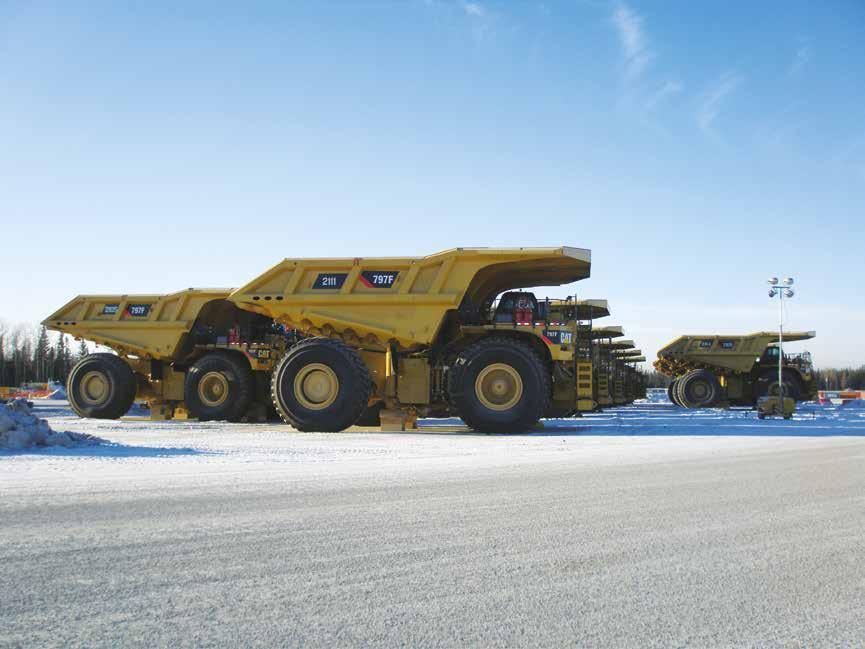
brand building
Caterpillar’s presence in the Asia Pacific region includes Australia, China, India, Japan, New Zealand, South Korea and Thailand. Nearly 20 per cent of Caterpillar’s employees and nearly 30 per cent of its global dealers are located in the Asia Pacific area. Caterpillar manufactures medium wheel loaders for the North American market in Aurora, Illinois, but also produces them in Japan, Brazil, India and China. Large wheel loaders are manufactured exclusively in the United States on three separate assembly lines in Aurora, Illinois. Caterpillar has four major plants in the Peoria area: the Mapleton Foundry, where diesel engine blocks and other large parts are cast; the East Peoria factory, which has assembled Caterpillar tractors for over 70 years; the Mossville engine plant, built after World War II; and the Morton parts facility. Major facilities in Europe include Grenoble and Echirolles in France, where track type tractors, track type loaders, wheeled excavators and undercarriage components are made. A facility in Hungary handles fabrications and buckets, and in the UK, mini excavators are made in Leicester, articulated dump trucks at Peterlee and Perkins engines in Peterborough. Cat underground products are made in four key locations: Luenen, Germany; Zhengzhou and Langfang, China, and Rayong, Thailand. Caterpillar has made significant investments in its manufacturing footprint in Thailand in recent years. The Underground Mining Facility started production in October 2012, while Caterpillar’s Rayong Tractor Facility started production in May 2013, mainly for export to global customers. Roof supports for underground coal mining are designed by an experienced team in Germany, from where the castings are also sourced. The roof supports are subsequently built and assembled by a skilled team in Zhengzhou, China. As weld quality is critical on roof supports, to ensure

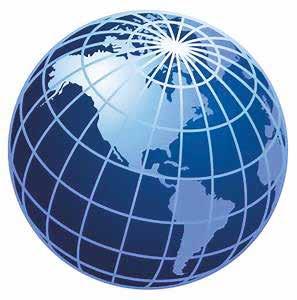
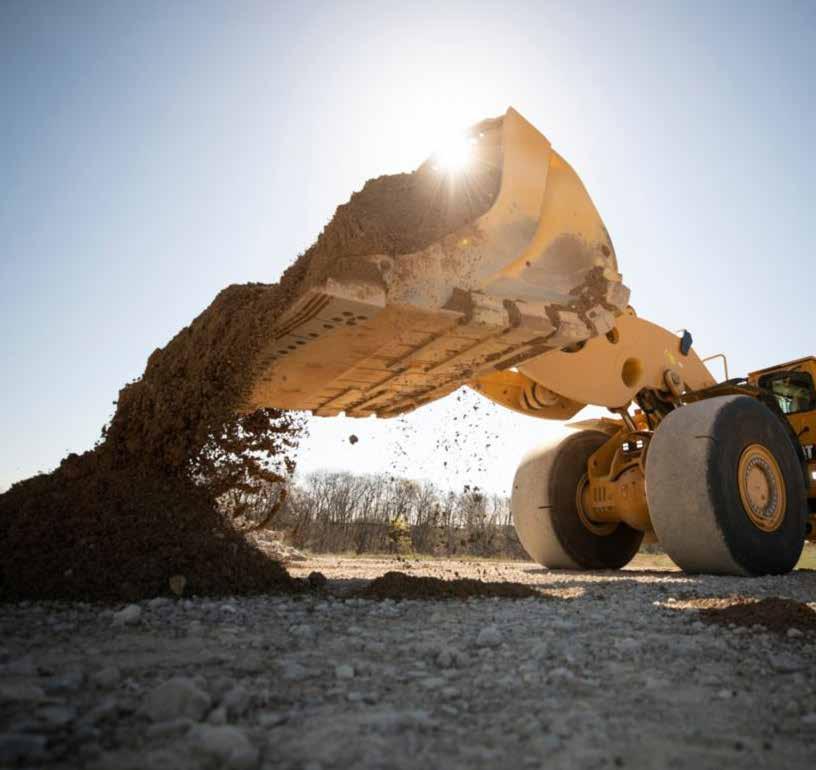
consistent high quality, the leadership team in Zhengzhou created a welding school within the facility.
Sustainability
As befits an industry leader, Caterpillar places great emphasis on sustainability. The company has been named to the 2021 Dow Jones Sustainability Indices (DJSI), including the World and North America indices, the 22nd time Caterpillar has been included in the DJSI. The annual DJSI process evaluates numerous corporate economic, environmental and social performance factors. Caterpillar is actually integrating sustainability into its enterprise strategy by establishing 2030 sustainability goals, tying a portion of executive compensation to environmental, social and governance (ESG) and creating a new leadership position of Chief Sustainability & Strategy Officer. “Sustainability is one of our core values and an important element of our enterprise strategy for long-term profitable growth,” said Caterpillar Chairman and CEO Jim Umpleby. “We demonstrate our commitment to sustainability in many ways, including through our significant progress in reducing greenhouse gas emissions from our operations and our continued investment in new products, technologies and services to help our customers achieve their climate-related goals.” The development of zero emission machinery will play a major role in the sustainability of the mining industry. In June 2021, Caterpillar announced an agreement with Nouveau Monde Graphite to develop, test and produce zero-emission machines, with a view to becoming the exclusive supplier of an all-electric mining fleet for deployment at NMG’s Matawinie graphite mining
project in Saint-Michel-des-Saints, Québec, Canada. “The collaboration between Caterpillar and Nouveau Monde marks an important milestone in the mining industry,” said Denise Johnson, Caterpillar Group President. “Through integrated technology, machines and services, the entire Caterpillar team is proud to support Nouveau Monde as they work towards constructing and establishing their first zero emission mine.” Mining trucks are the lifeblood of mine sites around the world – which makes them a key component in plans to achieve sustainability and greenhouse gas (GHG) emissions goals. Caterpillar customer BHP has committed to being a net-zero operator by 2050, and has signed a similar agreement, giving it early access to the Caterpillar-developed zero-emissions equipment and input to the developing and testing processes. Caterpillar unveiled its latest advancements in safety, sustainability and technology at MINExpo 2021 in Las Vegas, Nevada in September. The exhibit was grouped under three areas: sustainability, technology and automation, and equipment lifecycle management solutions. The three-day expo celebrated Caterpillar’s collaboration with mines and the company’s commitment to its customers with the theme, “Together, We’re Mining Better.” “We look forward to sharing Caterpillar’s latest mining products and services portfolio with our customers. Our advancements extend from equipment, technology and services to helping customers mine more safely and sustainably,” said Caterpillar Chairman and CEO Jim Umpleby. “We’re committed to providing the solutions to help our customers achieve their climate-related objectives while meeting their requirements for performance, durability and economic value.” Highlights included the new Cat D11 XE electric drive dozer, the world’s largest, most powerful and efficient dozer in the industry, as well as the new Cat® R1700 XE LHD underground loader, featuring 100% battery electric propulsion that generates significantly less heat and noise, while offering a 16.5ton payload and 11.2 mph top speed. A broad range of renewable and storable power solutions featured in the Show, along with a Cat MineStar® stage focusing on Caterpillar’s state of the art technology.”
brand building
Services
As well as being the world’s leading manufacturer of equipment for the mining industry, Caterpillar is also the leading provider of a number of support products, services, knowledge and solutions that make it a definitive one-stop shop for miners. Its service portfolio includes financing, innovative trade arrangements, and rental and used products to help customers get the equipment they need. It also provides generator sets to help customers power their operations, rail products and services to transport materials around the world, and a line of on-highway and bare chassis trucks that can be customized to meet specific support needs. And then there’s the dealer network, one of the biggest differentiators for the brand. If the Cat product line is unmatched in the industry, when it comes to service and support, the global Cat dealer network is quite unparalleled, too, delivering expert service, integrated solutions, after-sales support, fast and efficient parts fulfillment, worldclass remanufacturing capabilities and more. One of the strengths of the Caterpillar brand, they say, is that they are as committed to the truck you bought yesterday as the one you’ll buy tomorrow. That’s why customers return to Caterpillar in such numbers.