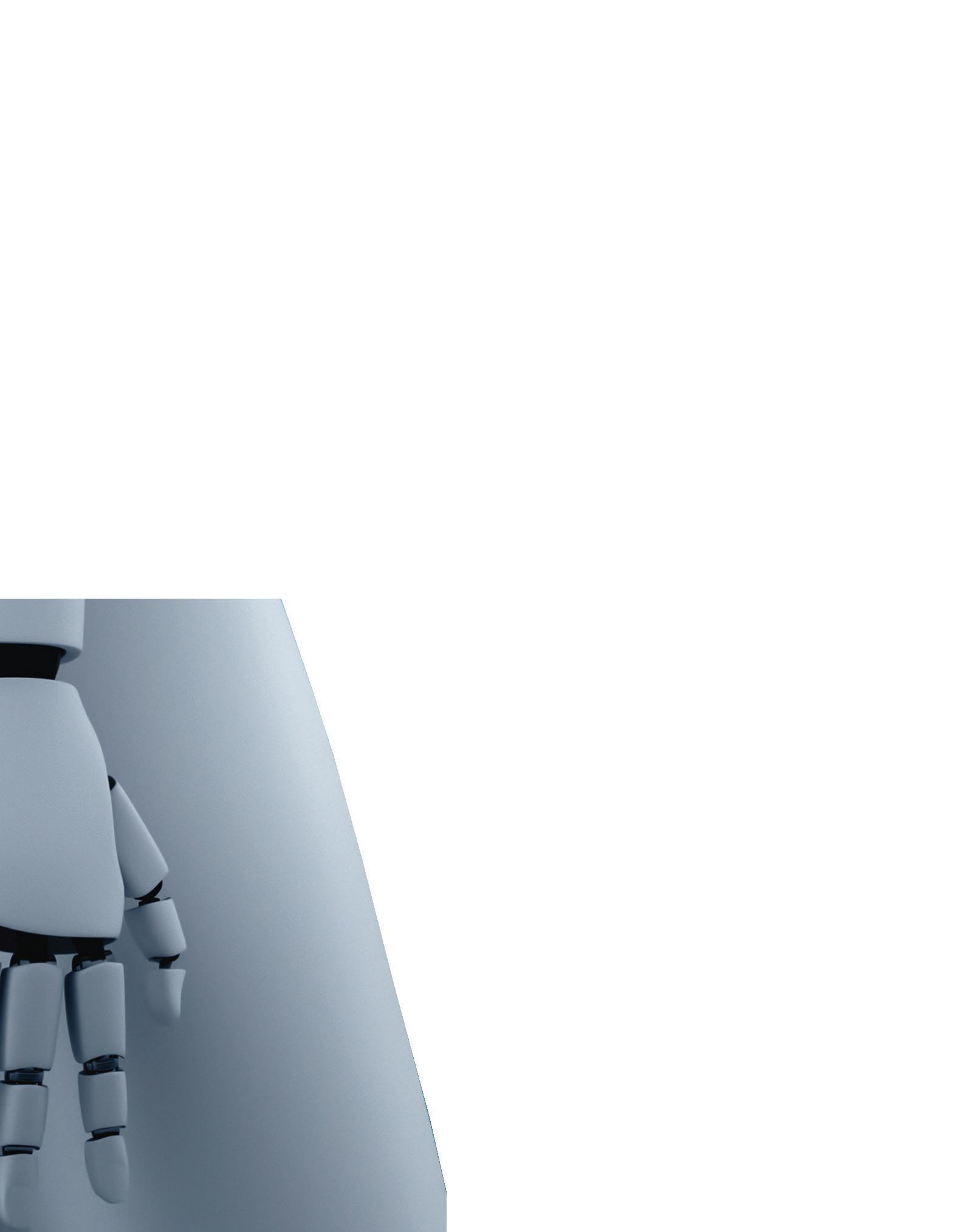
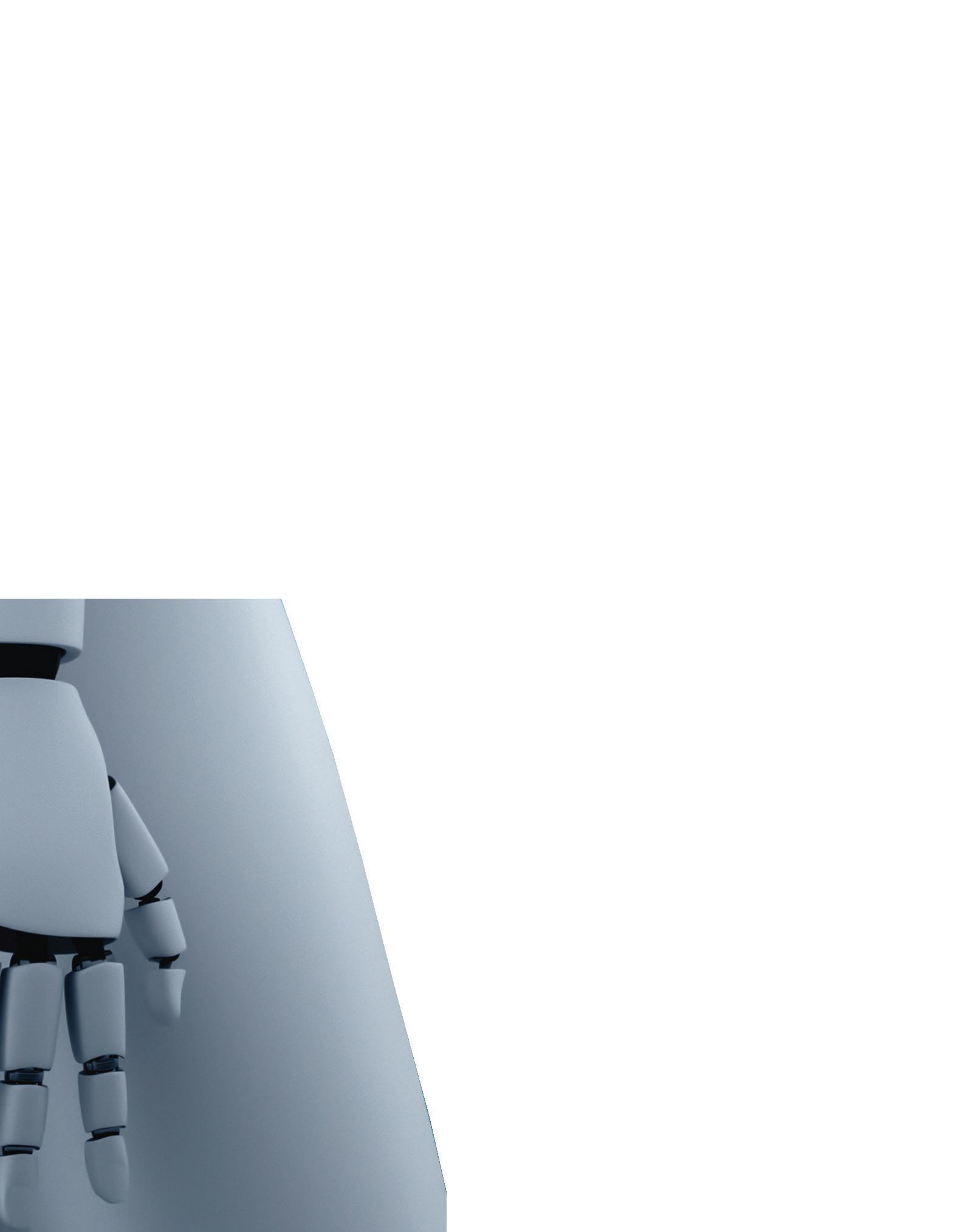
WAREHOUSE
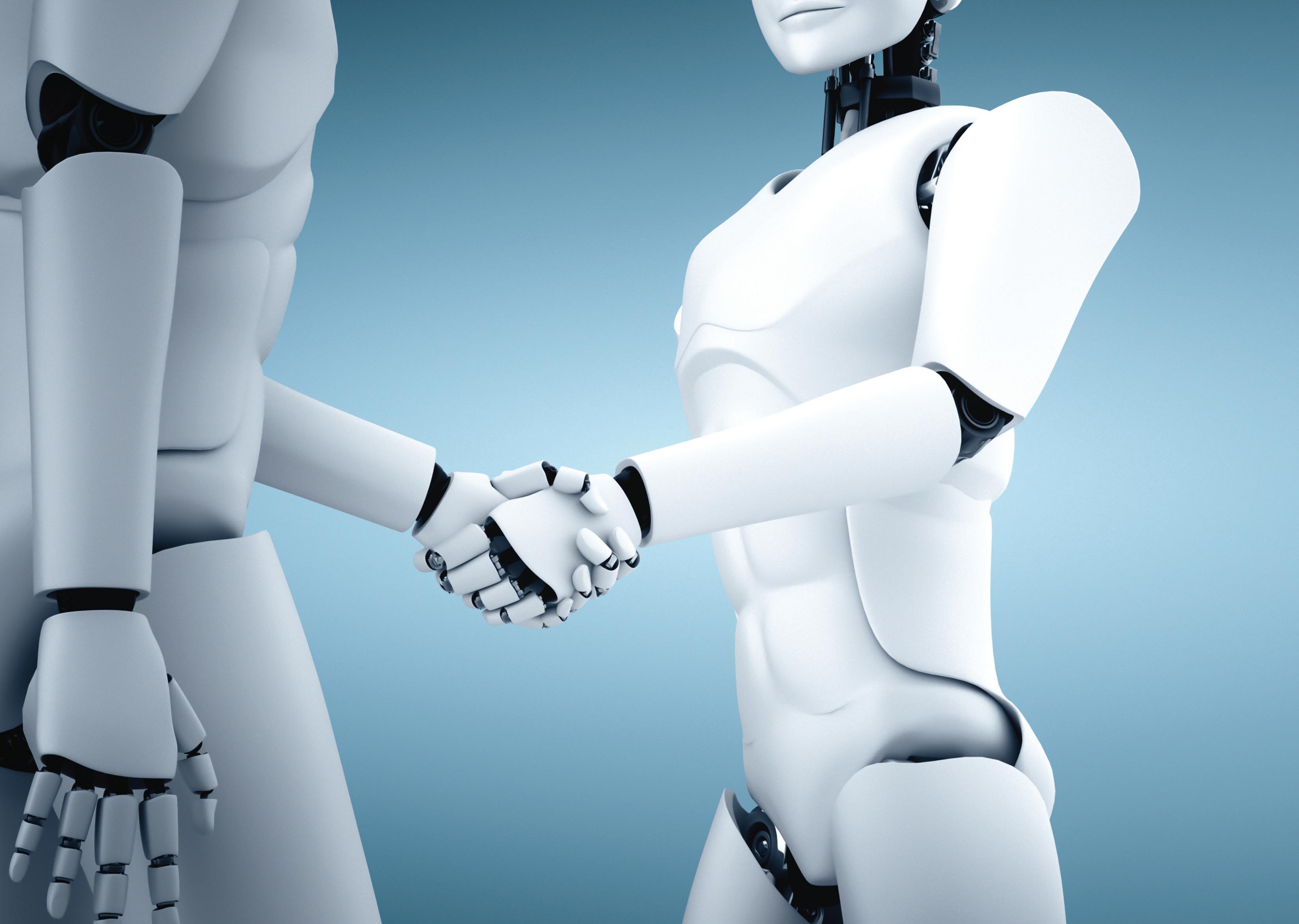
UMass Amherst designs a multirobot team that shares situational awareness.
A new kind of collaboration
in the warehouse
BY STEPHANIE NEIL • EXECUTIVE EDITOR
The capabilities of collaborative robots, commonly referred to as “cobots,” could soon expand beyond direct human-robot interaction to include heterogeneous robots intelligently coordinating and interacting with each other.
New research from the University of Massachusetts Amherst is proving robots can be programmed to create their own teams and voluntarily wait for their teammates to execute a set of dependent tasks. This new multi-team robot collaboration has the potential to improve manufacturing and warehouse productivity.
The research, funded by the U.S. Defense Advanced Research Projects
Agency (DARPA) Director’s Fellowship and a U.S. National Science Foundation Career Award, is led by Hao Zhang, associate professor in the UMass Amherst Manning College of Information and Computer Sciences and director of the Human-Centered Robotics Lab. Zhang’s research on “autonomous group introspective learning and coopetition for cross-capability multi-robot adaptation,” uses lessons from the social psychology of humans to help teams of robots with different capabilities work together and adapt to complex situations.
When Zhang was awarded the DARPA prize last year to improve robot teamwork, he was already focusing on
two main areas – group introspection and cooperative competition, dubbed “coopetition.”
Group introspection would allow robots in a team to be aware of all their other team members, so they have a shared situational awareness of the overall team’s capabilities. To accomplish that, Zhang is modeling robots in a team as a graph to enable group awareness, and using conditional models that identify backup robots with similar capabilities to replace failed teammates. They are solving the competition aspect by simultaneously modeling cooperation at the team level and competition at the individual level. Cooperation tackles tasks that are

Autonomously transport materials up to 4,200 lb with the industry’s most comprehensive autonomous mobile robots and fleet management software.


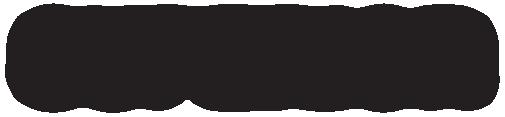
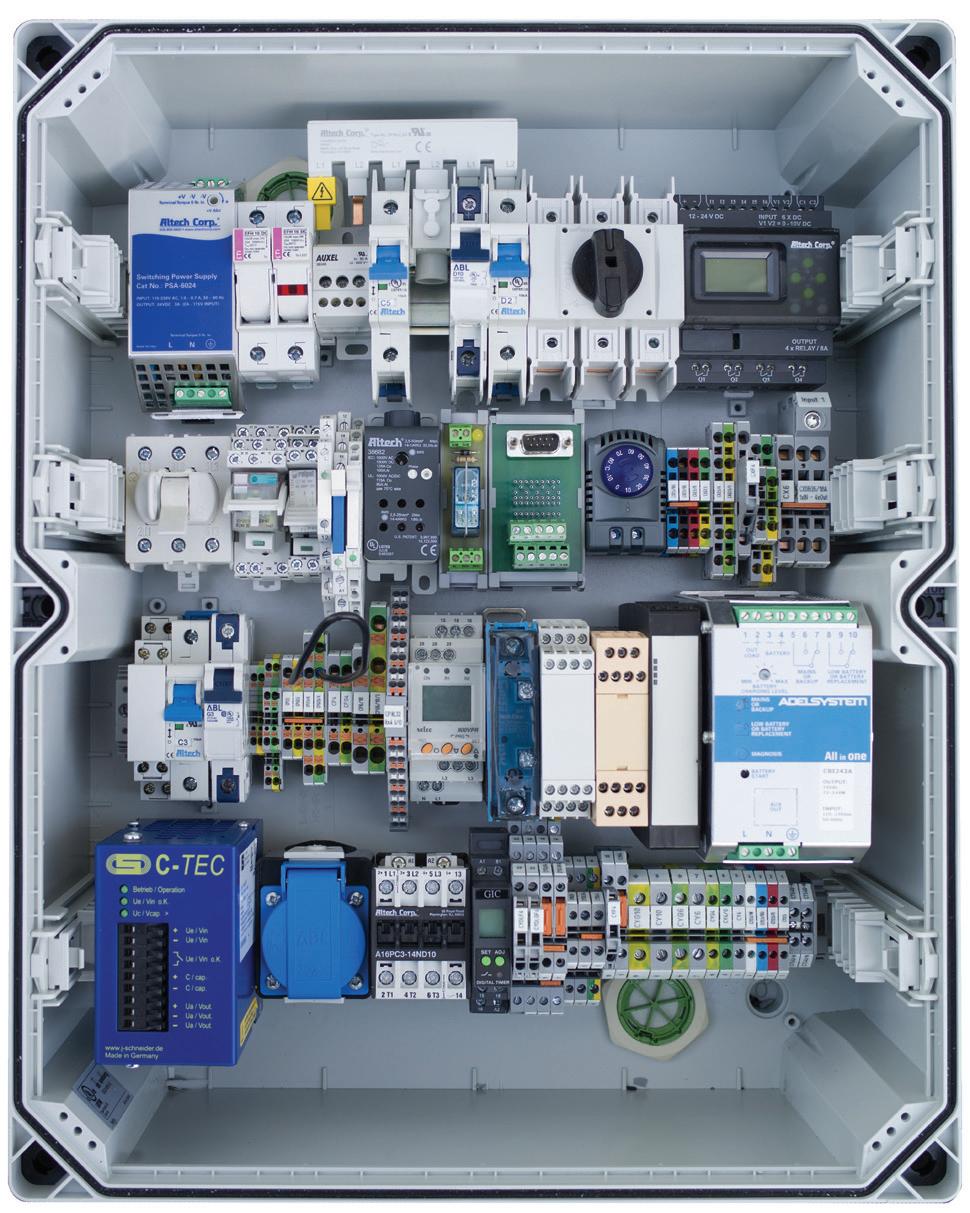

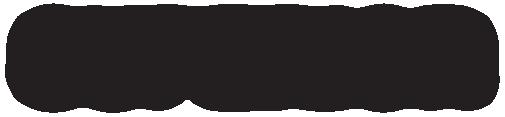
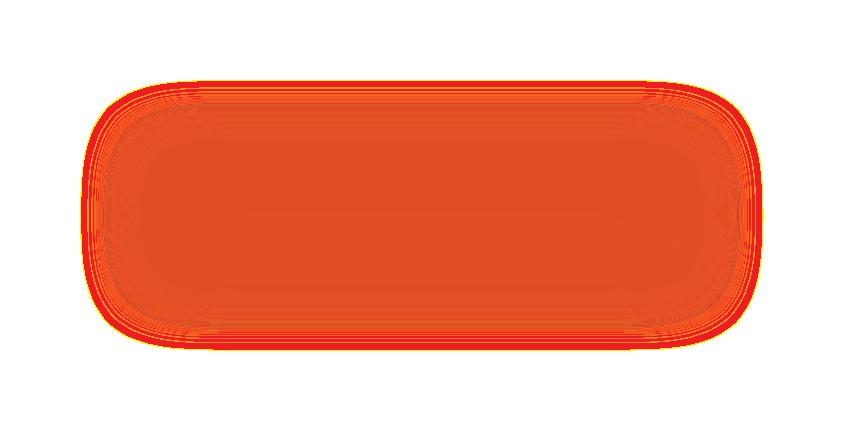
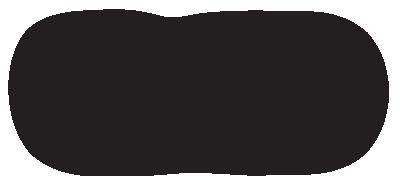

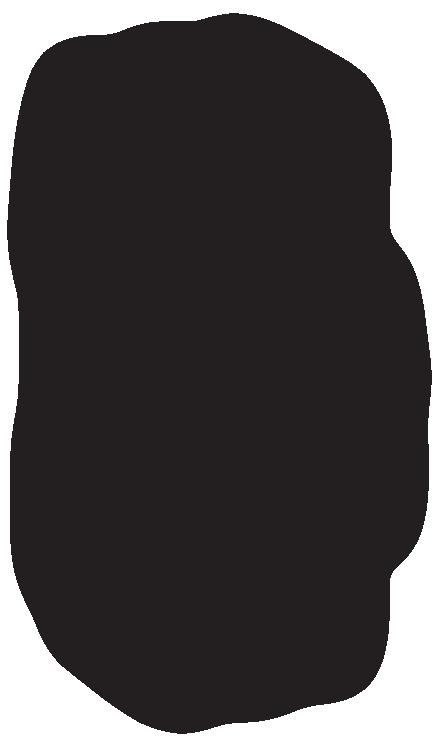
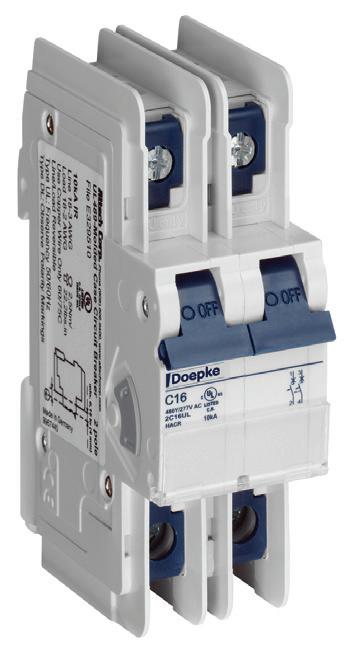
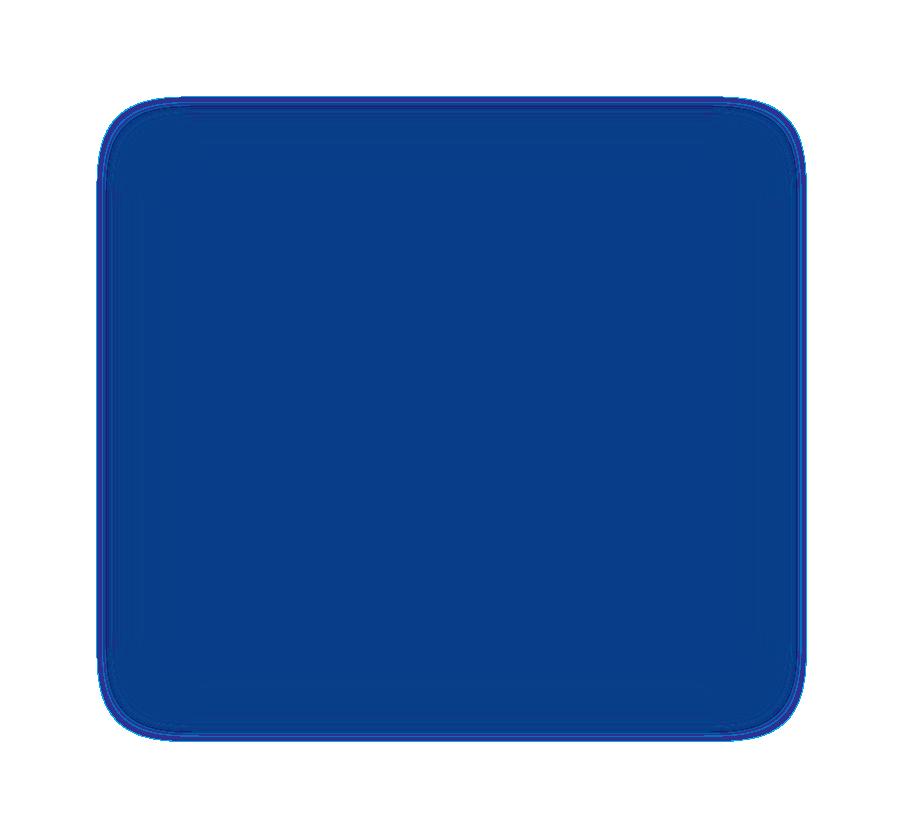
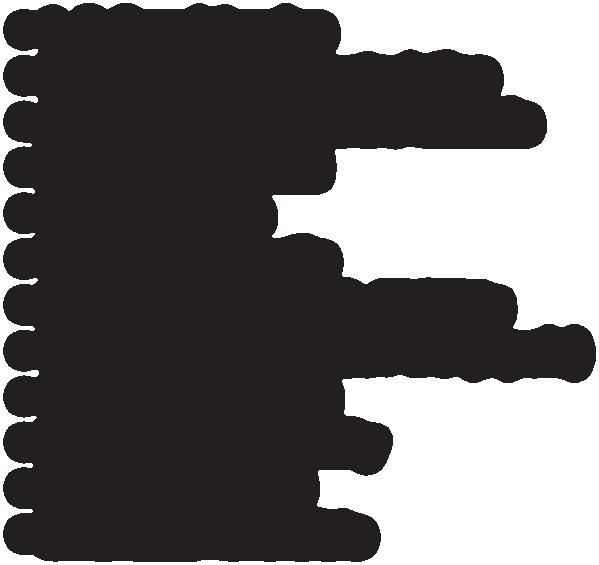
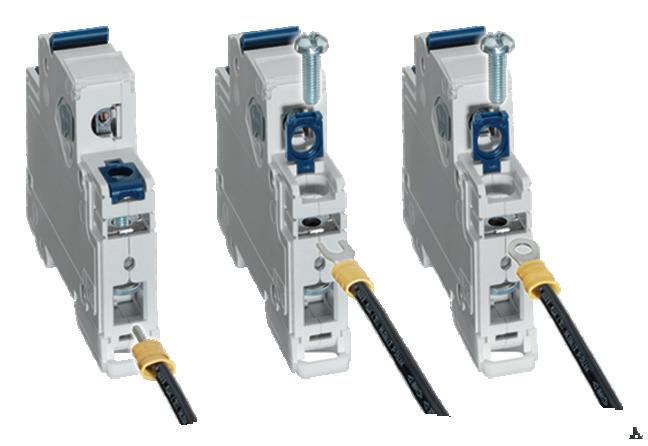


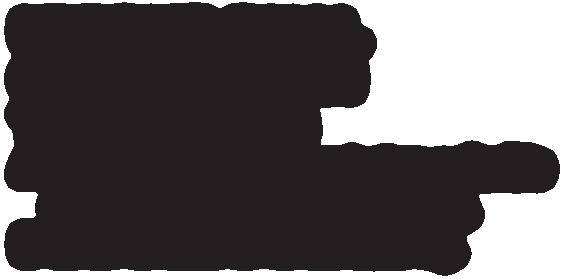
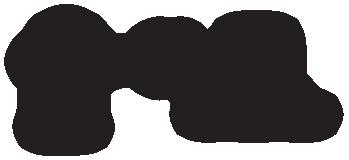
AUTOMATED WAREHOUSE
infeasible for individual robots to solve, while competition encourages each robot to perform better and adapt faster.
Multi-robot mix and match
In a warehouse setting there may be many different types of robots and payload capacities: fixed in place robotic arms, mobile automated guided vehicles (AGVs), heavy-lifting palletizers, etc. The challenge, however, is coordinating a diverse set of robots for a common purpose.
“There’s a long history of debate on whether we want to build a single, powerful humanoid robot that can do all the jobs, or we have a team of robots that can collaborate,” stated Zhang. “Robots have big tasks, just like humans. For example, [if] they have a large box that cannot be carried by a single robot, the scenario will need multiple robots to collaboratively work on that.”
The other behavior is voluntary waiting. “We want the robot to be able to actively wait because, if they just choose a greedy solution to always perform smaller tasks that are immediately available, sometimes the bigger task will never be executed,” Zhang explains.
As a solution, Zhang created a learning-based approach for scheduling robots called learning for voluntary waiting and subteaming (LVWS) coupled
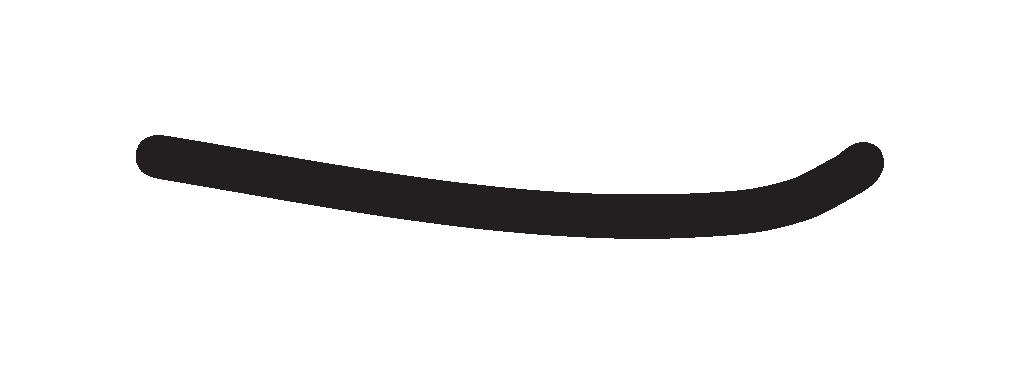



“There’s a long history of debate on whether we want to build a single, powerful humanoid robot that can do all the jobs, or we have a team of robots that can collaborate”
with a graph attention transformer network (GATN) that computes rewards for scheduling tasks to robots. LVWS includes nodes (robots) and edges (communication, relationships, or spatial positions).
According to the multi-robot research, collaborative scheduling is formulated as a bipartite matching problem where robots are assigned to tasks. These tasks are put into a GATN that integrates graph attention networks to encode the local graph structure and transformers to encode contextual information.
The resulting outputs are embeddings for each node, as well as global embedding for each graph which are used to compute a reward matrix used to perform bipartite matching.
To test their LVWS approach, the research team gave six robots 18 tasks in a computer simulation and compared
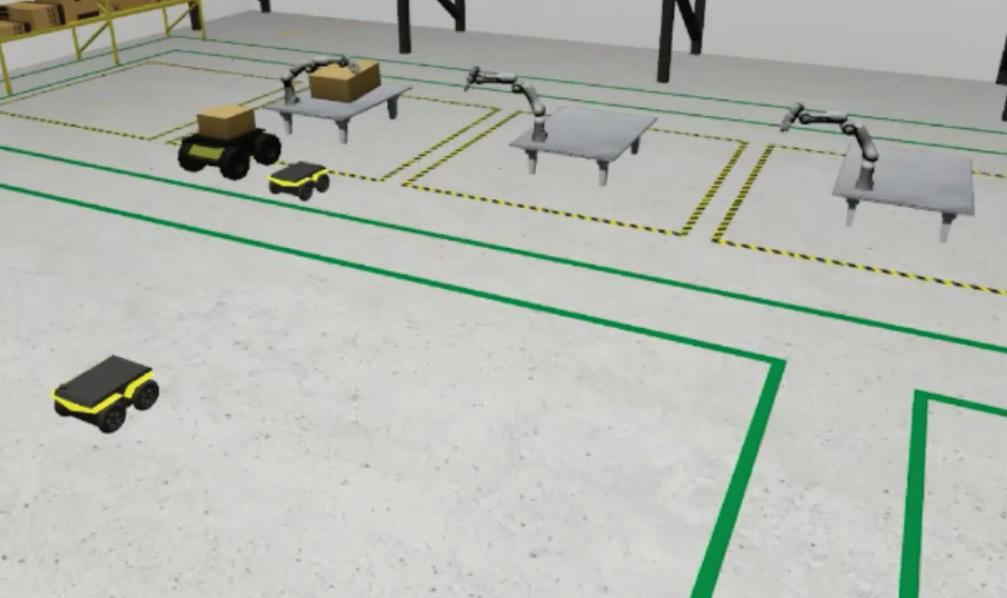
Group introspection and cooperative competition enables multi-robot teams to collaborate. | UMass Amherst
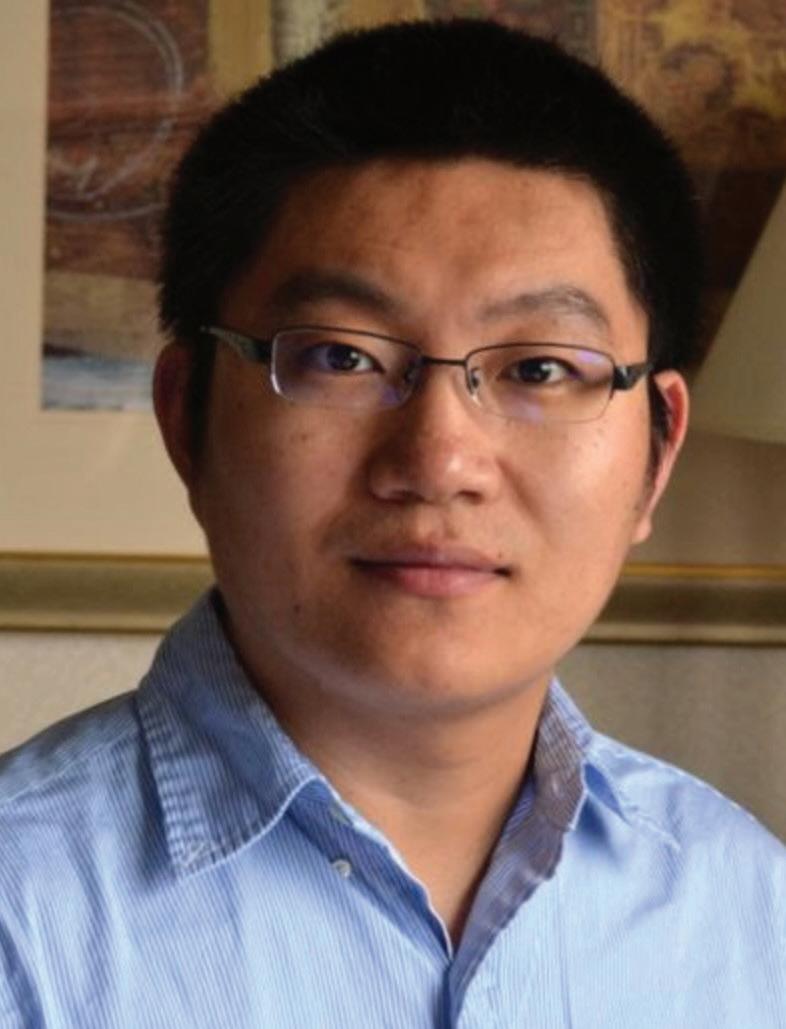
their LVWS approach to four other methods. In this computer model, there is a known, perfect solution for completing the scenario in the fastest amount of time. The researchers ran the different models through the simulation and calculated how much worse each method was compared to this perfect solution, a measure known as suboptimality.
The comparison methods ranged from 11.8% to 23% suboptimal. The new LVWS method was 0.8% suboptimal.
“So, the solution is close to the best possible or theoretical solution,” said Williard Jose, an author on the paper and a doctoral student in computer science at the Human-Centered Robotics Lab, in a statement.
The team has also demonstrated this method running on real-world robots.
Worth the wait
A common question the research team has received is, “How does making a robot wait make the whole team faster?”
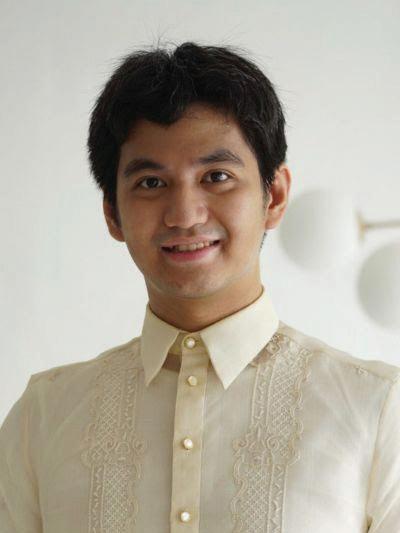
Jose responds by describing this scenario: There are three robots — two that can lift four pounds each and one that can lift 10 pounds. One of the small robots is busy with a different task and there is a seven-pound box that needs to be moved.
“Instead of that big robot performing that task, it would be more beneficial for the small robot to wait for the other small robot and then they do that big task together because that bigger robot’s resource is better suited to do a different large task,” Jose explained.
Zhang hopes this work will aid the progress of developing teams of heterogeneous robots, particularly as it relates to the scalability of large industry environments that require specialized tasks. AW
Scan the QR code to watch a demonstration of the LVWS method in a manufacturing assembly case study run in a Gazebo simulation or visit: www.youtube.com/watch?v=zslbOXQXtSI
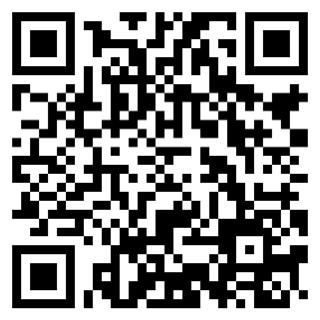
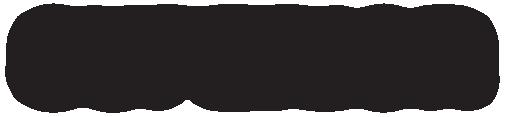
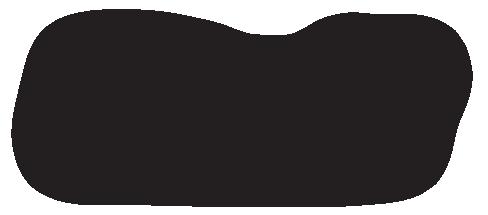
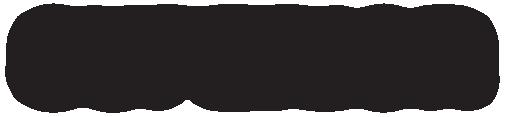
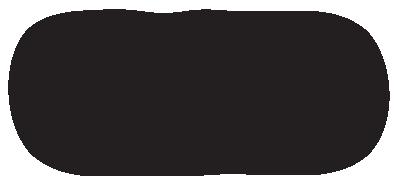
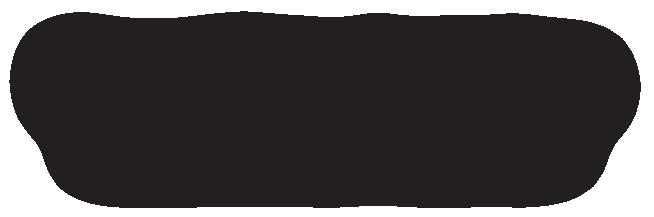
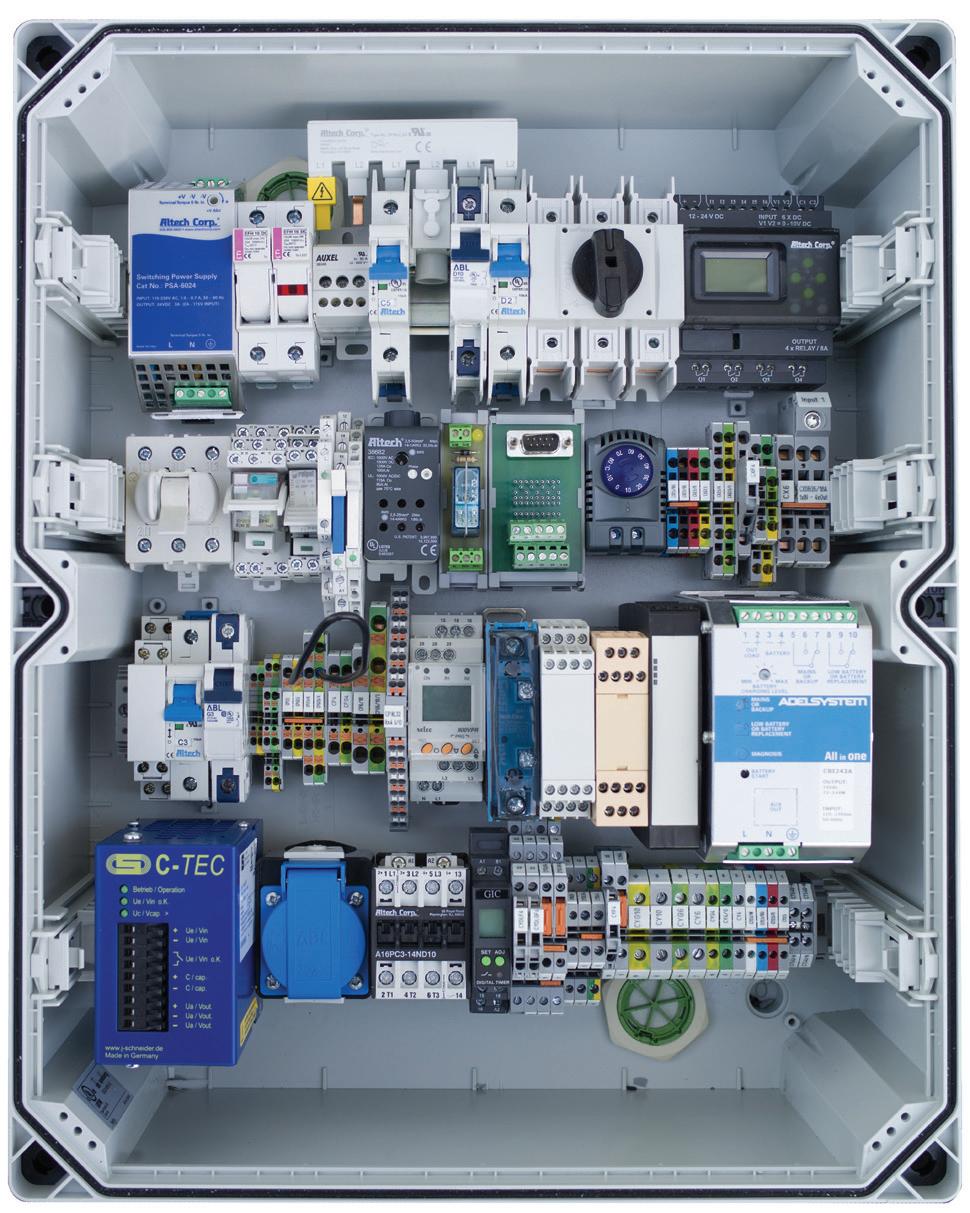


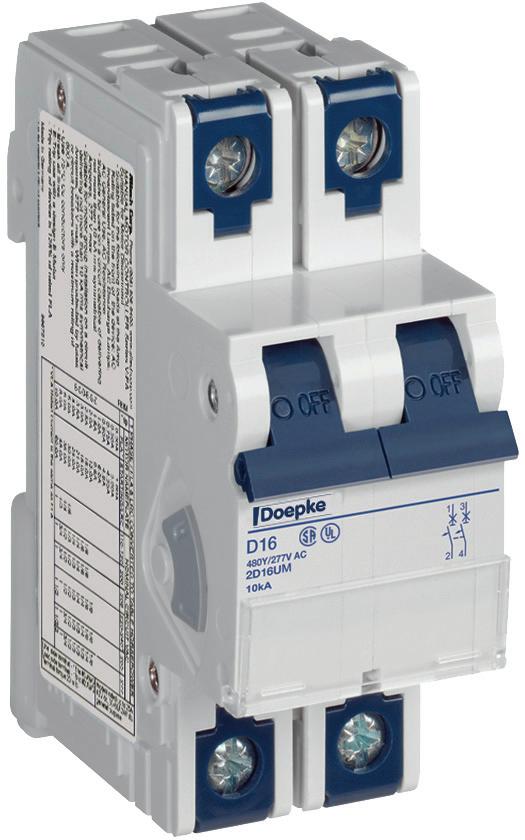

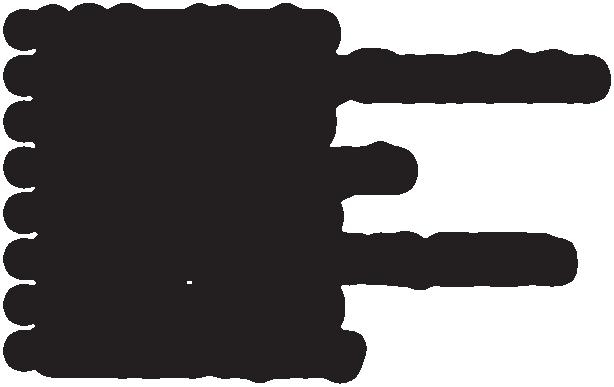
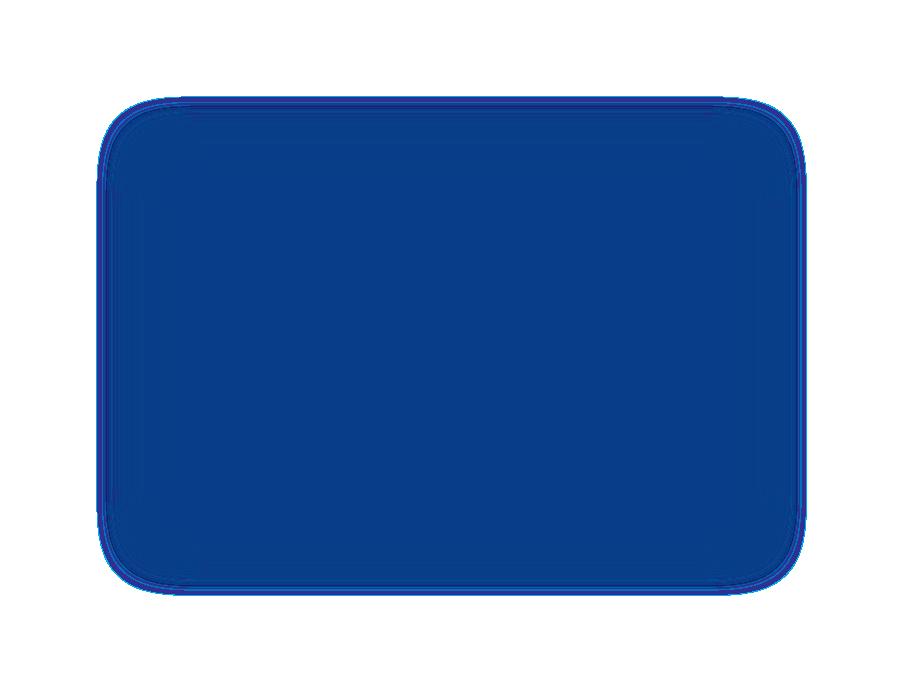


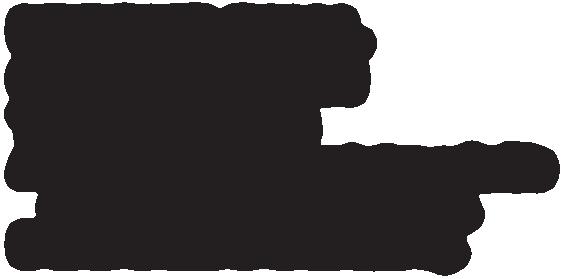
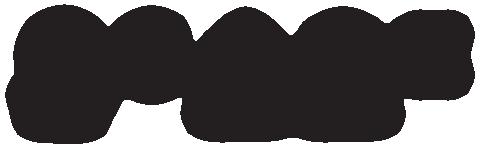
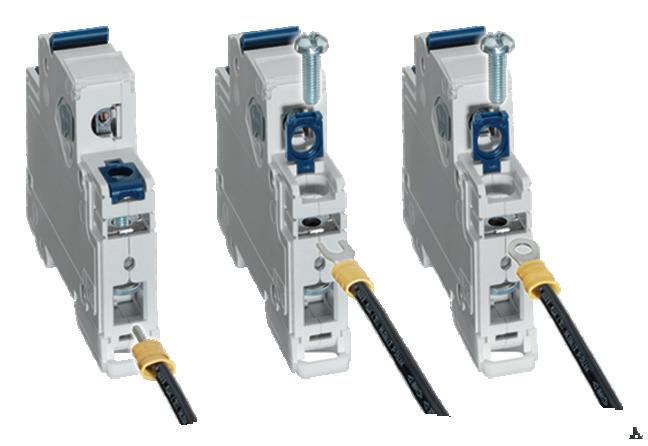



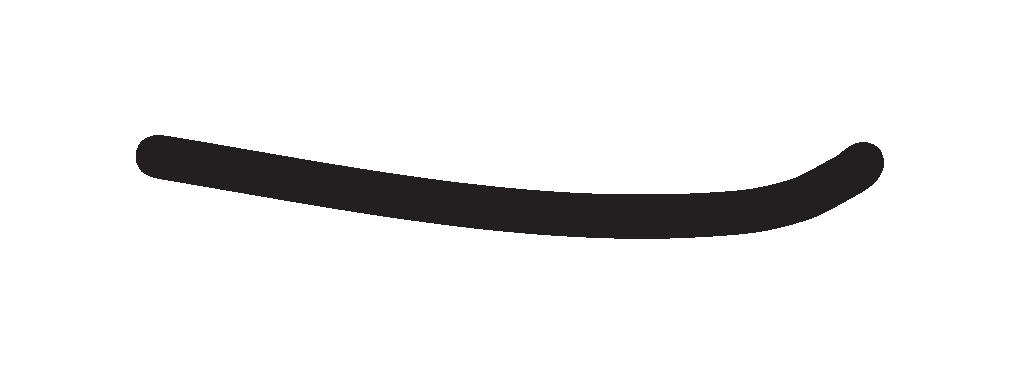
Hao Zhang
Williard Jose
in the automated warehouse cybersecurity Mitigate risk
How to recognize threats, track critical data, and train employees.
BY STEPHANIE NEIL • EXECUTIVE EDITOR
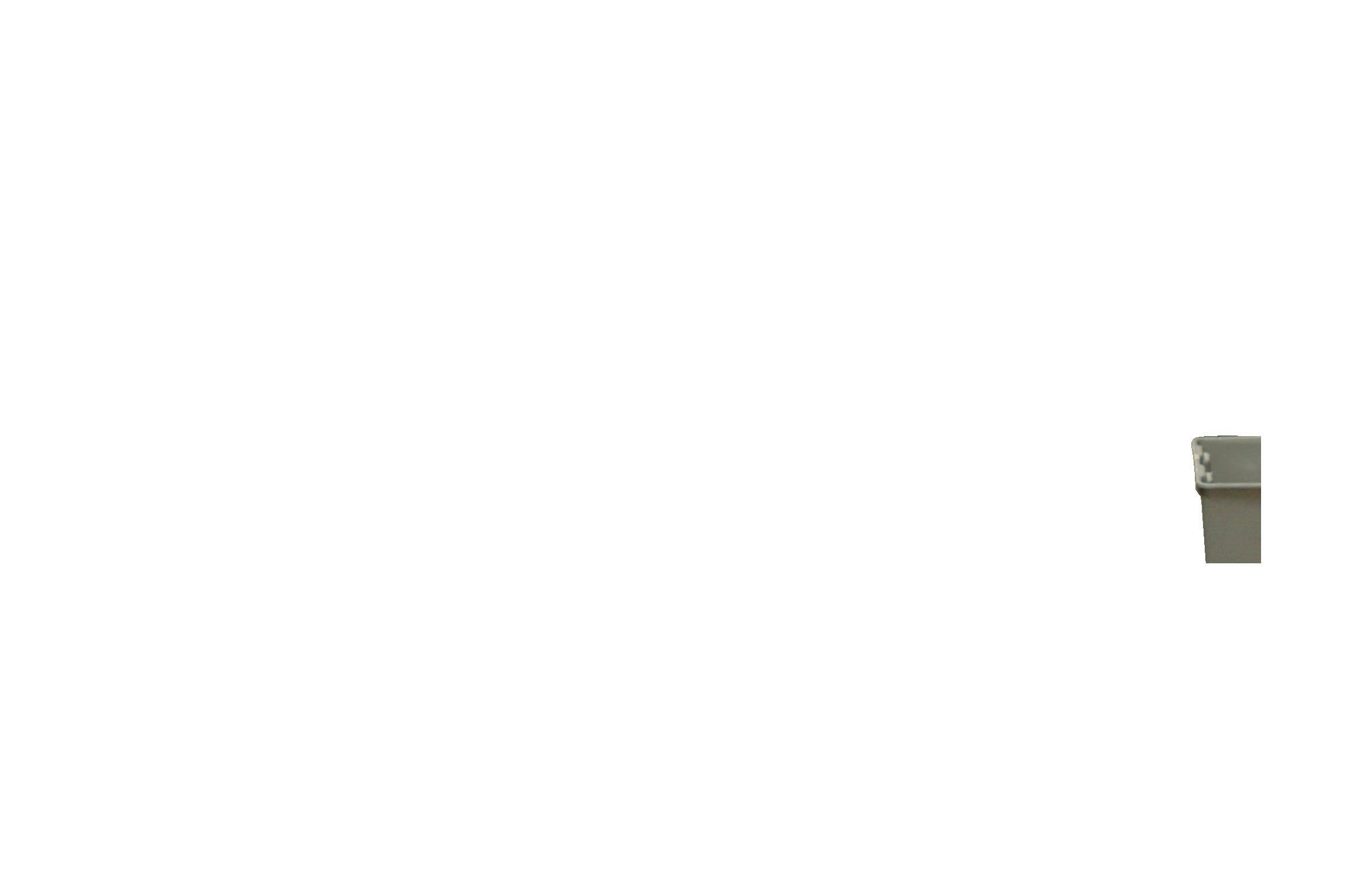
Thewarehouse is integral to the manufacturing supply chain.
As such, with cybersecurity threats on the rise, there’s an urgent need to adopt best practices that will ensure that the warehouse doesn’t become the weakest link in the supply chain.
As more automation makes its way into warehouses and more assets are integrated, there is a pressing need to safeguard the digital and physical infrastructure. This is especially urgent since cybercriminals are crafty and could use an opening in a warehouse as a backdoor into a partner’s network.
For example, in February 2023, Applied Materials, a semiconductor technology supplier, was reportedly the victim of a cybersecurity incident that originated from a ransomware attack on one of its suppliers. That incident cost Applied Materials $250 million in its second quarter that year.
No warehouse or fulfillment center wants to be a catalyst for cyber catastrophe. Yet, staying safe is not easy, as malicious actors are finding new ways to infiltrate organizations.
McKinsey has identified three cybersecurity trends that represent the biggest threat now and in the future:
• On-demand access to ubiquitous data and information platforms. Recent shifts toward mobile platforms and remote work require high-speed access to ubiquitous, large data sets. This dependency exacerbates the threat of a breach. And since organizations collect more data about their customers, such a breach could be costly.
• Hackers are increasingly using artificial intelligence to launch sophisticated attacks. Attackers using advanced tools such as AI, automation, and machine learning could cut the end-toend life cycle of an attack from weeks to days or even hours.
• The growing regulatory landscape and continued gaps in resources, knowledge, and talent. Many organizations don’t have enough cybersecurity expertise. The shortfall is growing as regulators increase their monitoring of cybersecurity in corporations.
With these trends in mind, it’s important to understand how to mitigate risks.
To get a better understanding of the actions needed to protect the automated warehouse, Locus Robotics outlined some best practices. The company makes autonomous mobile robots (AMR) for fulfillment. In June, it received the 2024 Fortress Cybersecurity Award in the Compliance category from the Business Intelligence Group.
Locus specified three areas of importance: understanding the threats, capturing the data, and training the workforce.
Bad actors vs. bad decisions
Cybercrime is growing and is descending upon unsuspecting businesses from all directions. There are nation-state adversaries that pose a national security risk in the form of advanced persistent threat activity (APT) aimed at targeted and prolonged network intrusion. There is malware, phishing, and ransomware, which are
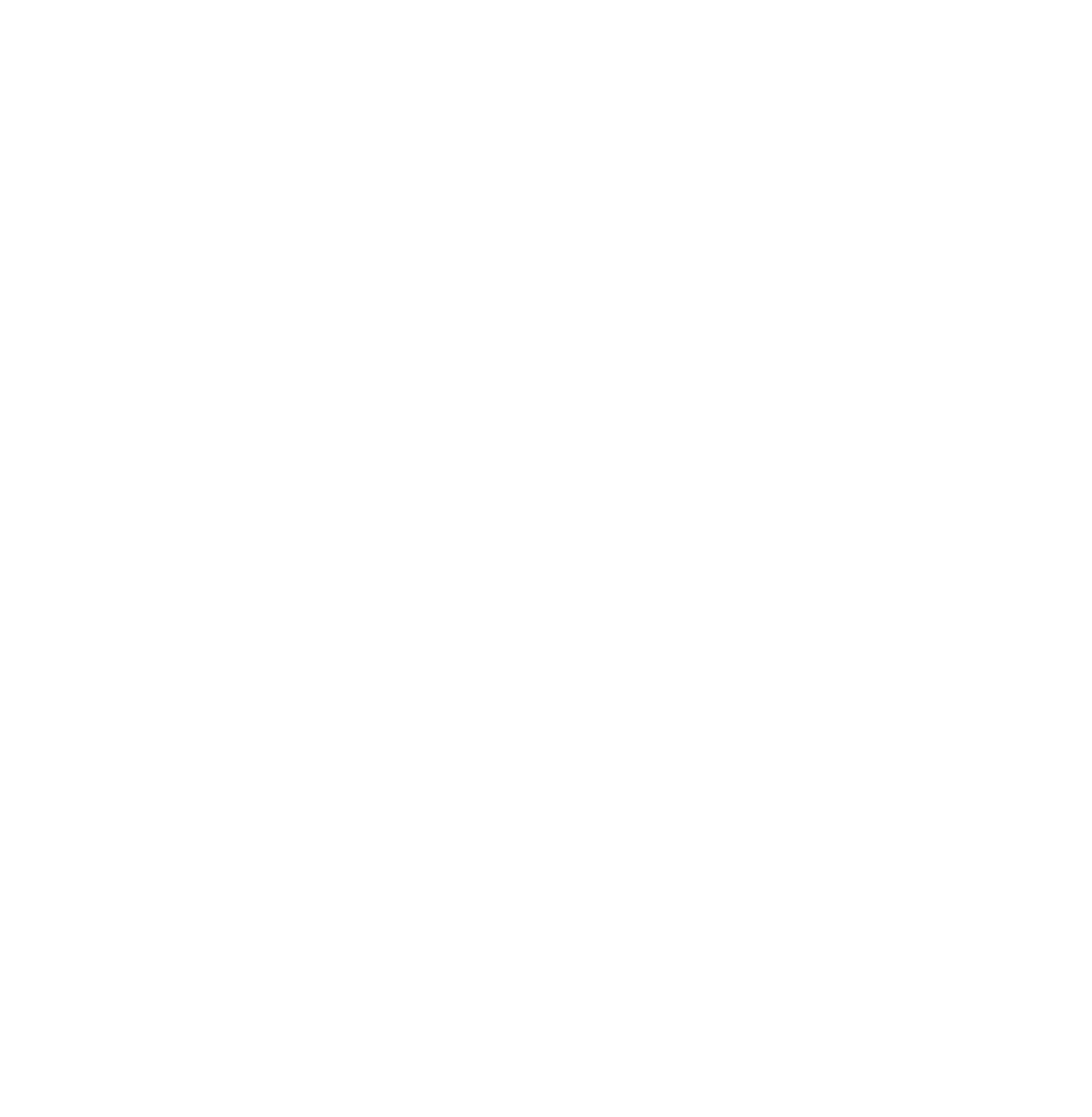
the most common forms of attacks on business, and, as seen in the Applied Materials example, can be costly.
And then there are the employees who make mistakes – such as plugging a virus-infected USB drive into a system. Or simply taking a call from the wrong person. The data breach at MGM Resorts in September 2023 that shut down electronic payments and casino machines was initiated by a hacker group impersonating the IT staff, gaining access to systems via a call to an employee.
Fouad Khalil, senior director for enterprise security, risk, and compliance at Locus Robotics, is a member of a group called InfraGard, a national nonprofit organization that has formed a partnership between the Federal Bureau of Investigation and the private sector to educate and share information on security threats and risks. As an InfraGard member, he has access to timely insight on threats to critical infrastructure, providing the knowledge and resources to not only protect Locus Robotics, but also its customers.
However, other threats are already penetrating the plant and warehouse. “Artificial intelligence, I think, is a big security risk,” Khalil said.
The cybersecurity risks associated with generative artificial intelligence (GenAI) in warehouses can be broadly categorized into data breaches, system vulnerabilities, and compliance challenges.
While GenAI may boost productivity and enhance decisionmaking, its integration into robotics and other systems exposes new potential attack vectors for cybercriminals.
“The data that powers GenAI — often sensitive and proprietary — can become a target,” said Khalil. “Moreover, the interconnected nature of modern warehouses means a breach in one area can have cascading effects throughout the entire operation.”
To that end, the cybersecurity risks associated with this technology should be considered and steps taken to mitigate risk. (see sidebar).
Solutions for Automation and Robotics
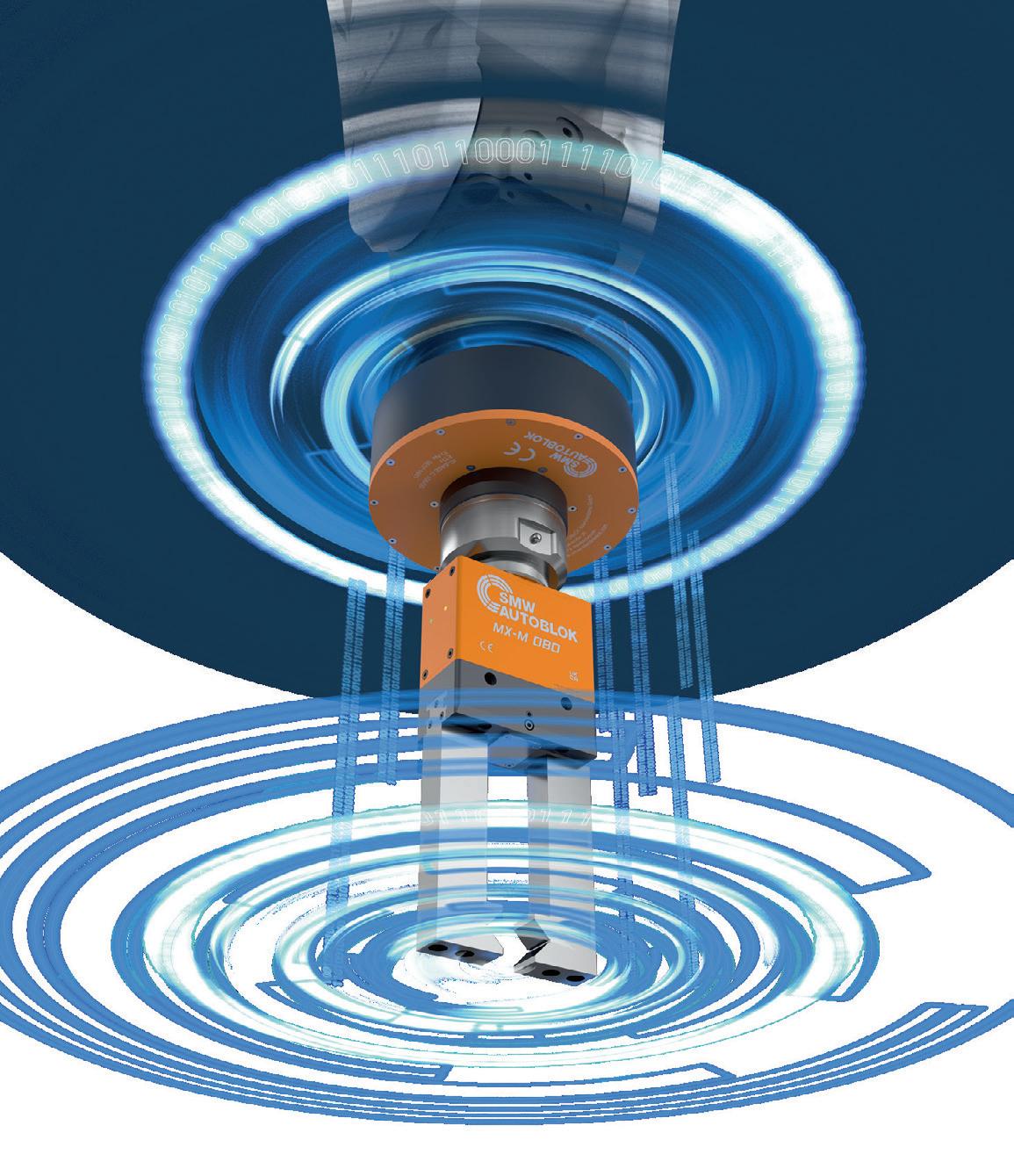
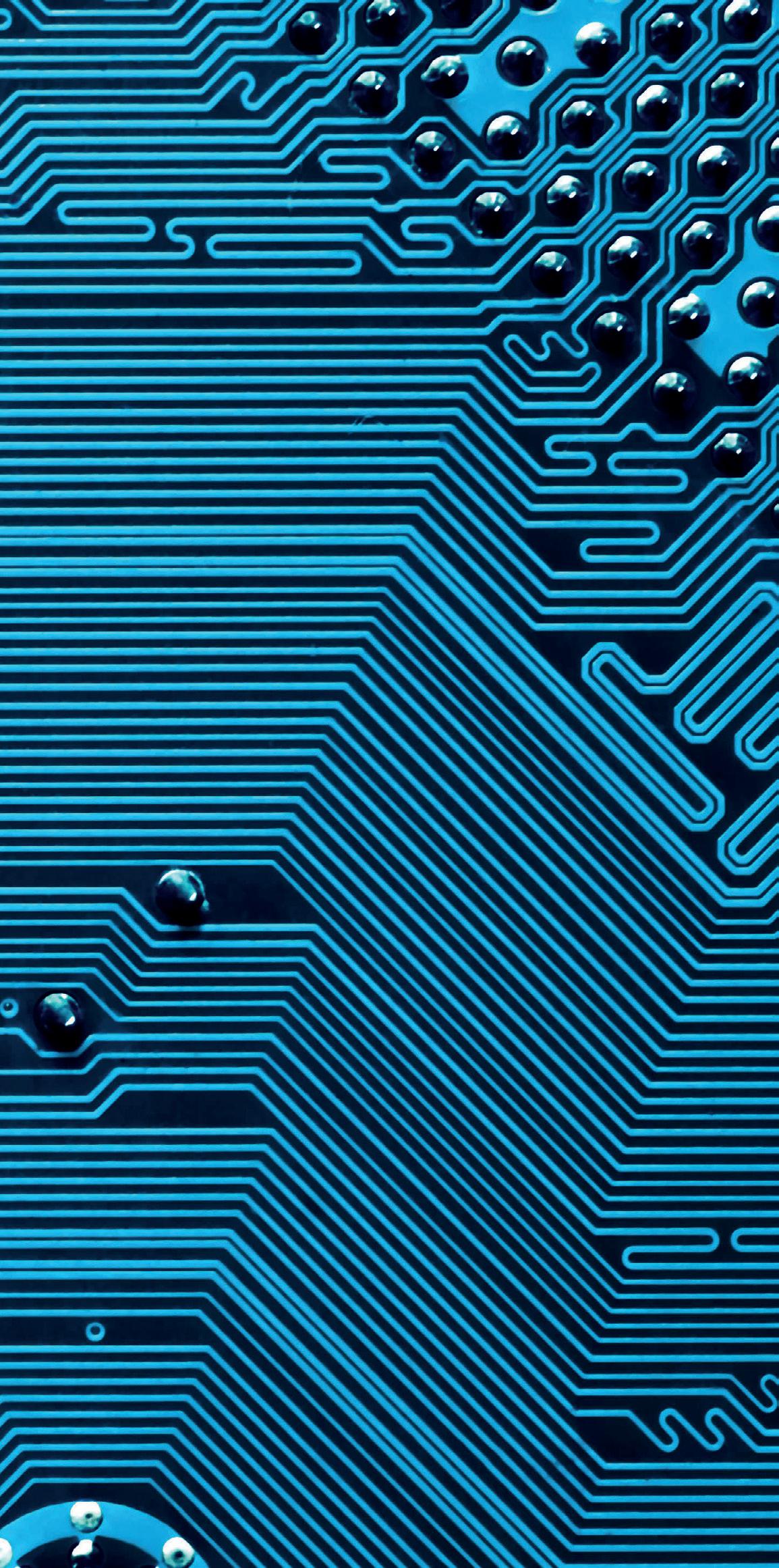
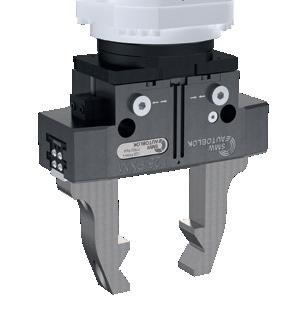
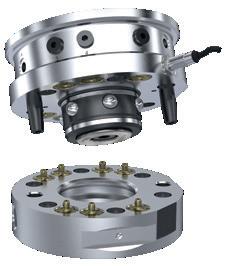

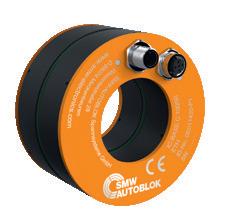
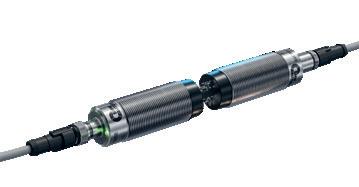
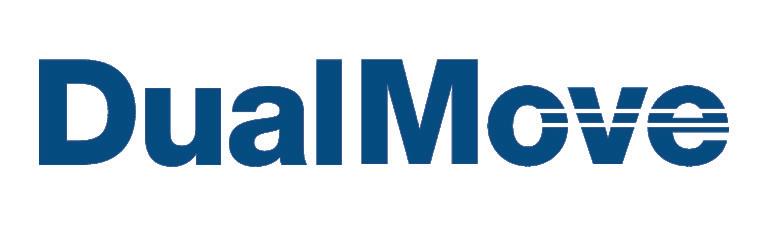
Intelligent Pallet Systems
Built For Capacity, Speed, & Accuracy
Follow the data
While GenAI uses data, robots generate it. To secure that data throughout the warehouse, it has to be tracked.
“When you follow the data, you understand where it is stored, how it is transmitted, how it is processed, and you have sufficient controls over those data elements to make sure that it’s protected,” Khalil said. “And if it’s not protected, then [you have to figure out] what action you can take to mitigate the risk.”

One way to mitigate the risk is to create a barrier, which is what Locus Robotics does with its secure tunnel of encrypted data used to share information. But constant infrastructure changes in a warehouse can affect the environment. Adding a network node or allowing an OEM access into the network, for example, could open the door to unauthorized network access.
“It sounds simple, but it's a lot of complexity that comes into play,”
While Locus Robotics builds AMRs, they are just one piece of the solution. According to the Wilmington, Mass.-based company, it has designed its navigation software with measures to protect customers’ proprietary data.
“It's a one-stop shop/blackbox secure solution that gets deployed to a warehouse that offers the cloud reporting, the onpremises reporting, the robotics, services, operational efficiencies, connectivity for the network, and everything else that comes into play to make it effective and more productive,” Khalil explained. “That black-box approach is what we deliver, and security comes through that entire lifecycle, from start
Awareness must be raised for security
Khalil emphasized that security is everyone’s responsibility – from the robot provider to the management team to the engineers and the operators in the warehouse. With all these different people in the mix, education is imperative.
“The first challenge that you find in our industry is awareness and acceptance that there is a risk,” he said, noting the shared responsibility model is important to understand. “Every time we deploy our solution to a warehouse, we are accepting the risks that they're experiencing.”
Shared responsibility should be reflected throughout the ranks of an organization, as well. Security
awareness training is a critical part of keeping the warehouse safe from cyber threats. “Especially given the fact that employees are your front line of defense, they must be always kept up to date on all things security,” Khalil said.
And it's not just about training your employees to be cybersecurityaware, but also training everyone in the partner ecosystem. To ensure a safe environment in the warehouse and beyond, the entire supply chain needs to embrace cybersecurity best practices. AW
Locus Robotics locusrobotics.com
Mitigate Your Cybersecurity Risks
According to Locus Robotics’ Fouad Khalil, the cybersecurity challenges of integrating GenAI into warehouse operations are significant, but not insurmountable. Here are some ways to safeguard warehouse operations:
• Conduct a comprehensive risk assessment: Begin with a thorough assessment of the cybersecurity risks associated with implementing generative AI. Understand where vulnerabilities may exist and how they can be exploited.
• Use robust data-protection measures: Implement state-of-the-art encryption, access controls, and data anonymization techniques to protect sensitive information from unauthorized access.
• Regularly update systems and manage patches: Keep all systems, including AI algorithms and connected devices, updated with the latest security patches to close any vulnerabilities that could be exploited by attackers.
• Train employees: Educate your workforce about the potential cybersecurity risks and best practices for preventing breaches. A wellinformed team is your first line of defense against cyber threats.
• Have an incident-response plan: Develop a comprehensive incident response plan that outlines steps to be taken in the event of a cybersecurity breach. This should include procedures for containing the breach, assessing the damage, and communicating with stakeholders.
• Collaborate with AI vendors: Work closely with your GenAI vendors to ensure they adhere to rigorous cybersecurity standards. Understand their data handling and storage practices, and ensure they align with your security requirements.

– Process automation
– Mechatronic drives
– Reduced CO2 footprint
– Reduced energy consumption
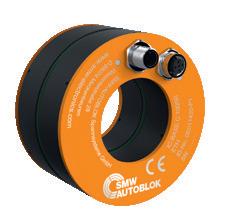
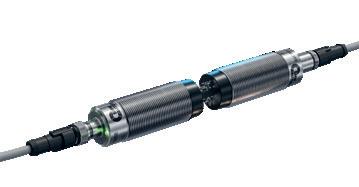
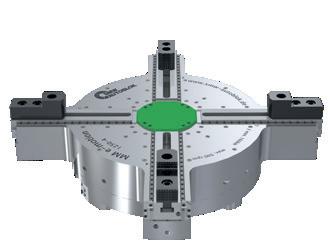
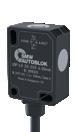
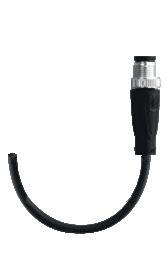


AUTOMATED WAREHOUSE
Preparing the plan warehouse automation
BY CHRIS VAVRA • SENIOR EDITOR
Consider this five-step strategy for a successful move away from manual processes.
The warehouse industry has transformed from its dire state 20 years ago, to an exciting era driven by Industry 4.0. Automation, fueled by efficiency, drives global growth, especially in the United States. However, newcomers to robotics need a solid warehouse automation plan, according to Movu Robotics, a maker of shuttle systems and autonomous mobile robots (AMRs).
Five current trends, including e-commerce growth and workforce challenges, are driving warehouse adoption of automation. Upcoming trends like actionable data and robotics-as-a-service (RaaS) also
promise significant benefits, reflecting continuous industry evolution.
Christoph Buchmann, sales director at Movu Robotics, outlined a five-step process for successful automation adoption. The steps include change management, a robust process review, software design emphasizing IT integration, hardware considerations, and meticulous implementation with worker training for long-term success.
The warehouse industry was in a terrible state 20 years ago, according to Buchmann. Today, he said, it’s a very exciting time, thanks to the rise of Industry 4.0 and other concepts,
which are fueling the growing trend toward automation and data exchange in technology and processes.
Automation offers great potential for manufacturers, Buchmann said during his presentation, “Mastering the Path to Automation: A Roadmap for Successful Implementation” at Modex in Atlanta earlier this year. “If you’re not thinking about automation now, you should start,” he said.
Five trends to consider in a warehouse automation plan Buchmann said five things are driving the acceleration of warehouse automation:
THE 5 PHASES OF TRANSITION

Movu Robotics presented steps to a successful warehouse automation plan. | Chris Vavra, WTWH Media
“The one thing you can expect is the unexpected”
1. Greater efficiency and profitability. It’s more costeffective than ever to implement automation.
2. Workforce development changes. The worker shortage remains a major challenge for employers.
3. Rising cost of real estate. Rather than build new facilities, companies are trying to make more of what they have.
4. E-commerce growth. The COVID-19 pandemic was among the factors forcing changes in consumer behavior and expectations for faster order fulfillment.
5. Food supply. The food and beverage industry has been using automation even more to match consumer demand and keep costs down.
While these trends are fueling automation’s growth now, Buchmann said five more trends are coming that will have just as big an impact:
1. Actionable data. There is more data than ever, and the technology has evolved to where companies can take advantage.
2. Accelerating technology. Advances in machinery, software, and now artificial intelligence are continuing.
3. Entry-level automation.
Buchmann said automation was big and complex 20 years ago. That has changed. Now, robots are more scalable, more affordable, and less complicated.
4. RaaS. Robotic fleets have grown in manufacturing facilities and small-to-midsize enterprises (SMEs) are turning to the service
model to use robotics for their short-term needs rather than making the long-term investment right now.
5. Safety and sustainability. Keeping workers and facilities safer has always been a priority, but now companies are trying to reduce energy costs.
Five steps to moving from a manual to an automated process
Buchmann said there are many benefits automation can bring, such as better efficiency and throughput, higher profitability, better safety, and improved accuracy. However, he acknowledged that it isn’t as easy as pushing a button.
Buchmann described a fivestep process to transition from a manual process to an automated one. The entire transition requires a culture change, he said, and taking ownership and trusting in your partners and employees is key.
Management might approve, but the workers are the ones who will make a deployment happen, Buchmann added. It’s critical that the plan be flexible throughout the entire process.
“The one thing you can expect is the unexpected,” he said.
1. Change management
Putting people, particularly those who will be most affected, in a leadership role is critical. Buchmann said people are naturally reluctant to change, and they need to be persuaded. He said doing this with a heavy hand and making people feel bad about what they’re doing wrong right off the bat will shut down the conversation before it even begins.

transmission of
– Safe and fast data communication via Ethernet Signals (Profinet, Ethernet IP, etc.)
– High energy transmission (up to 400 Watts)
– Totally wear and maintenance free
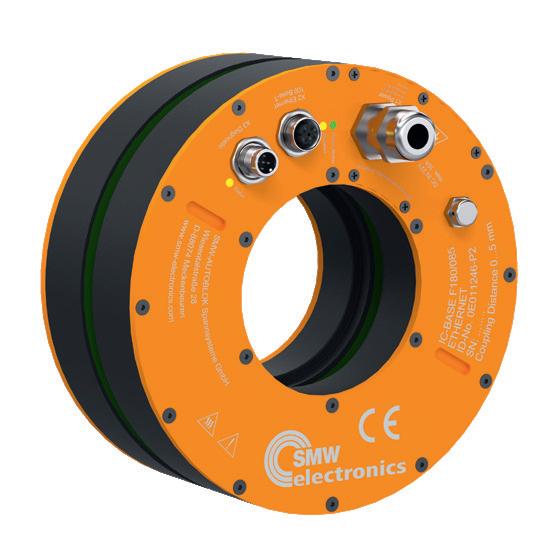
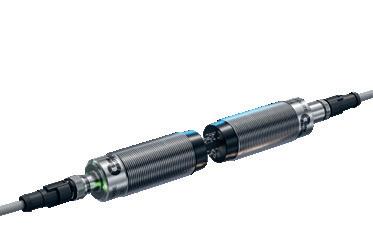
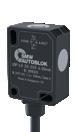
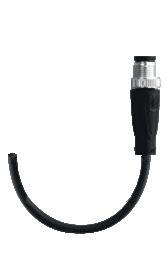
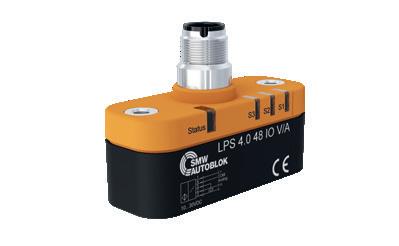

WHAT’S DRIVING THIS ACCELERATION?
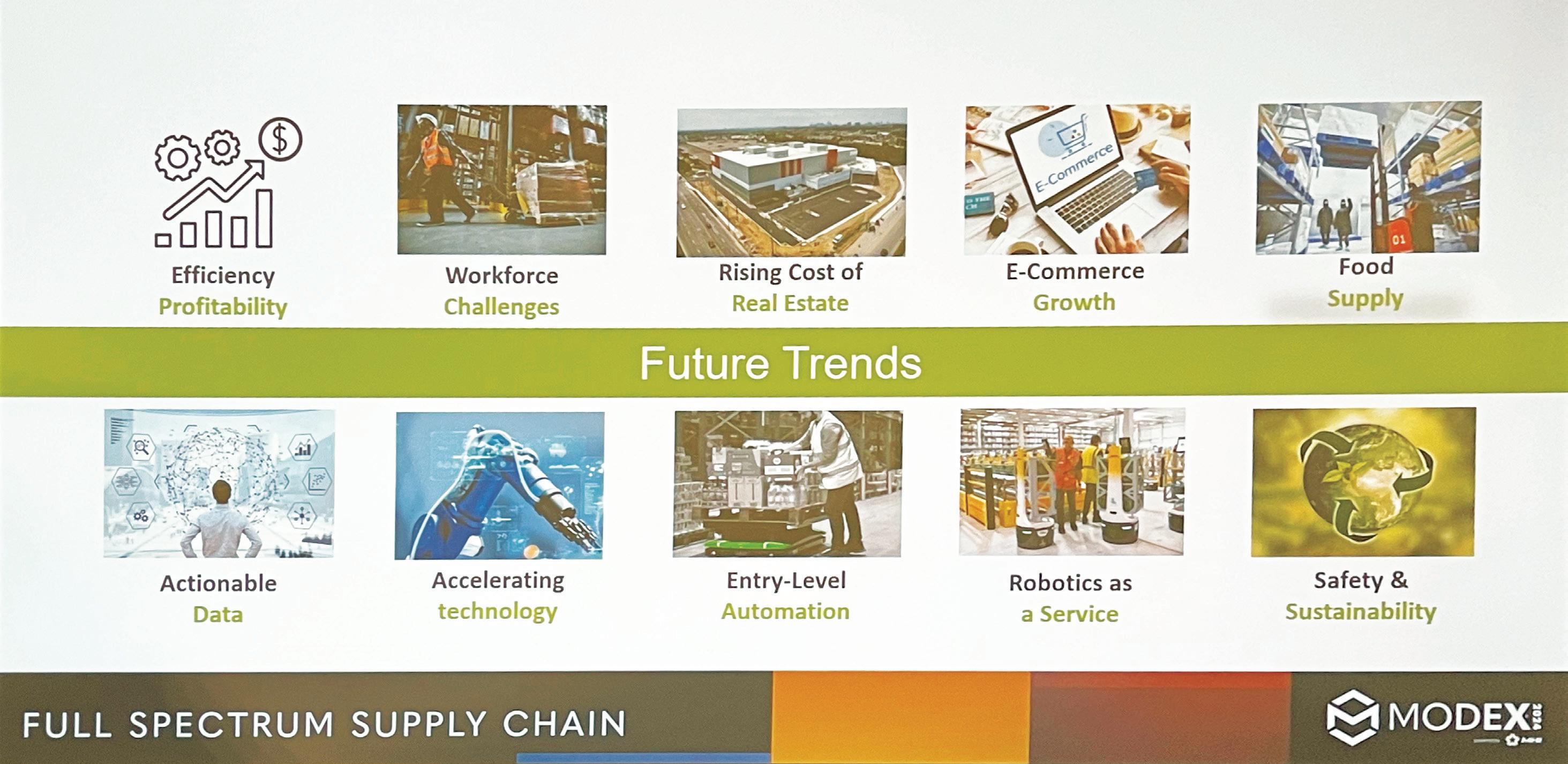
Five current and future trends are driving automation growth in warehouse facilities.
| Chris Vavra, WTWH Media
He said the trick is to encourage them by highlighting what they’re doing well and lowering their emotional barriers to new ideas.
“You’ll be surprised how quickly they’ll buy in,” Buchmann said. “Workers want to shine.”
By building on those small wins and having them own the new processes and technology, it’ll be easy to get buy-in on the ground floor, which is where change management starts.
2. Process review and design
Buchmann said developing a strong plan is critical because it needs to improve upon what is already being implemented. Having the right data is critical to success, and any potential solution is only as good as the data that goes into the design. Developing an automation plan on bad data or a bad process is only going to lead to a bad automated process, he said.
Gathering the right data requires an in-depth data analysis of the information most important to the operation and creating models that illustrate a full view of the four walls within an operation. It can also help uncover the nuances that make each corporation unique and provide a foundation to build success, said Buchmann.
He recommended that companies follow these three steps during the process review and design:
Assess current operations. Conduct a thorough analysis of warehouse processes, workflows, and technologies and consider future needs.
Set clear objectives. Define specific goals for warehouse automation and establish key performance indicators (KPIs) and targets to measure the implementation’s success.
Educate yourself. Buchmann said people involved in the project should engage with vendors and technology experts as well as evaluate the latest automation technologies to find successful examples.
It’s important to answer key questions such as “What is the automation
transition designed to achieve?” he said. It’s also worth looking at an alternative analysis and determining what is the cost or risk of not automating.
From there, the plan can move forward with a business case that provides a thorough and detailed roadmap for success.
3. Software design
Buchmann said companies should not underestimate the importance of IT integration because the most common reason for failed automation implementations is lack of it.
It’s a little more complicated because warehouse software can have overlapping functions and no fixed function divisions. That means each IT landscape of a warehouse is different. Companies need to find the right set of functions to successfully fulfill operational needs.
Getting the automated interface right and using a digital twin, which is an emulation and virtual replica of a real-life system, also can help as a tool to drive improvements in warehouse productivity and efficiency.
4. Hardware design
There are many types of automation equipment used in warehouse facilities. The four most common are:
1. Mobile robots
2. Automated storage and retrieval systems (ASRS)
3. Conveyor and sortation systems
4. Stationary and collaborative robots.
Buchmann explained that there are many operational needs and priorities to consider, such as whether the facility should be semiautomated or fully “lights out.” It’s also worth asking about operational redundancy, adaptability, and scalability during the process.
Whatever the case, a thorough analysis is a must because mismatched technologies lead to inefficiencies.
5. Implementation and support
Now the real physical work starts, said Buchmann. The good news is everything is all set because KPIs were already established.
The commissioning and implementation process should cover the fundamentals, such as testing everything at all levels and doing performance tests beforehand. Worker training is also critical for a warehouse automation plan to be successfully executed.
It won’t be a perfect process and it shouldn’t be, but the issues will be minor, Buchmann said, as long as people know how to react. “Minor problems can cause downtime if you’re not trained for them,” he said.
People are at the heart of the process, and companies that realize and value their workers’ potential and take the time to develop a strong process will come out ahead in the automation race. It’s one they can’t afford to lose as it becomes more than a “nice to have,” like it was 20 years ago. Now, a warehouse automation plan is a necessity. AW
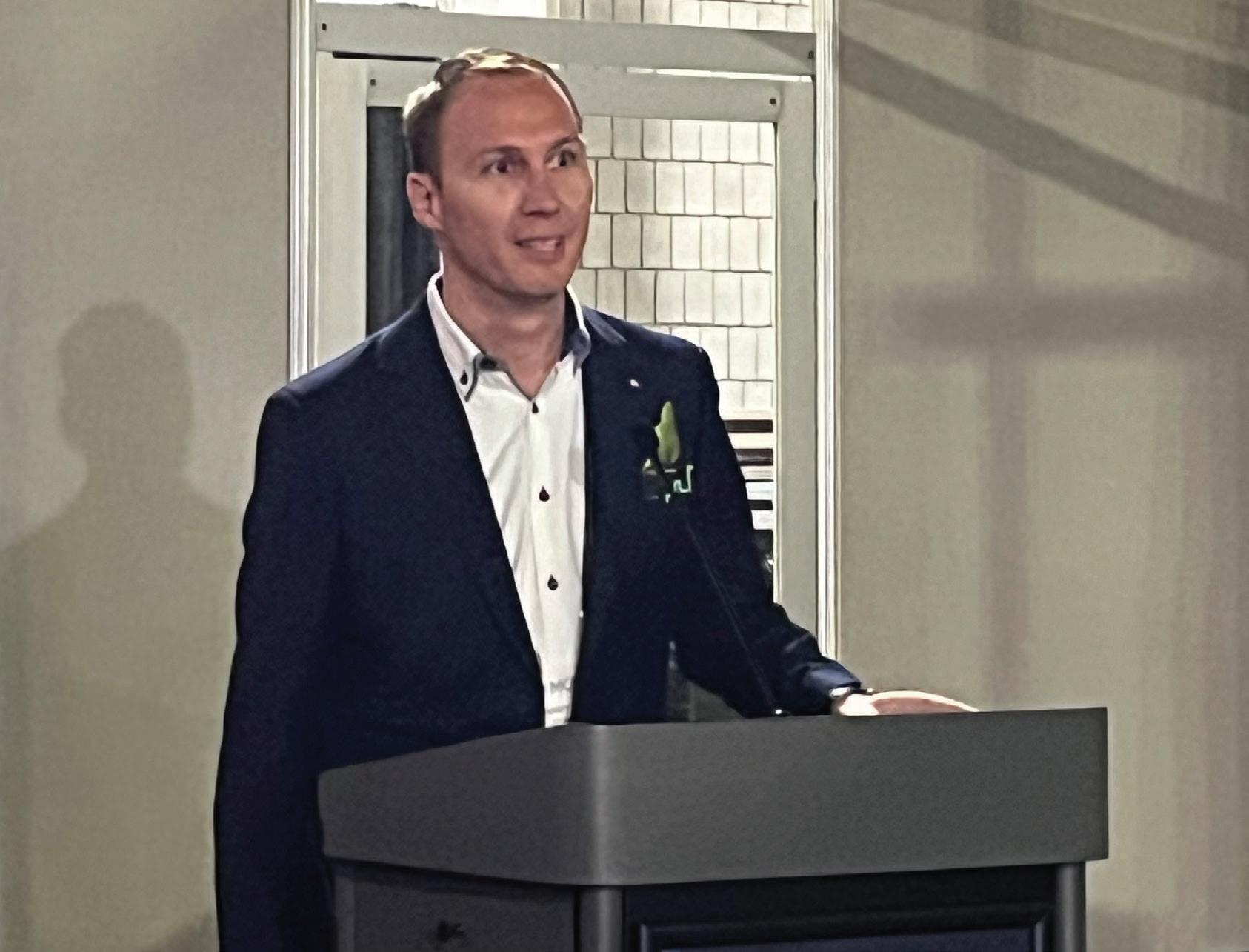
Christoph Buchmann, sales director at Movu Robotics, discussed how to adopt warehouse automation in Atlanta. |
Chris Vavra, WTWH Media











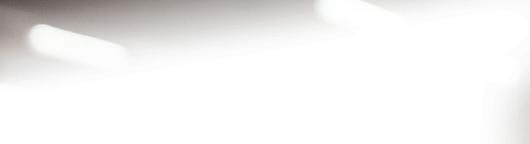










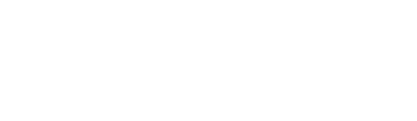










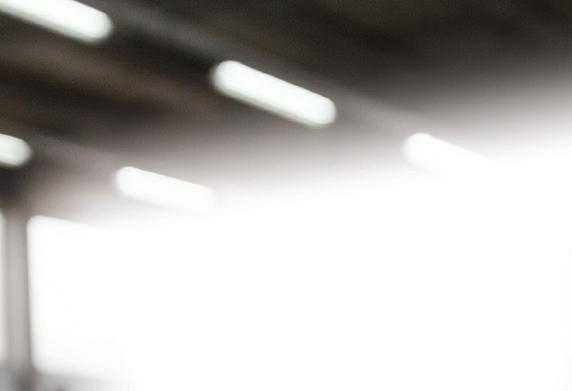
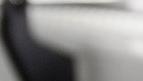
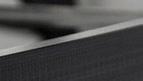
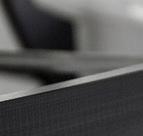







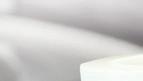

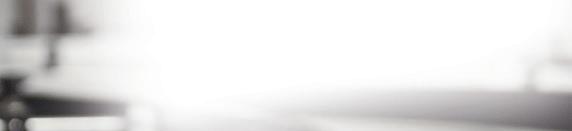
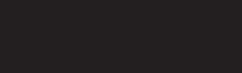
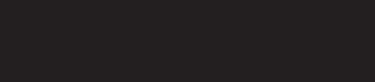

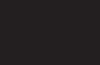
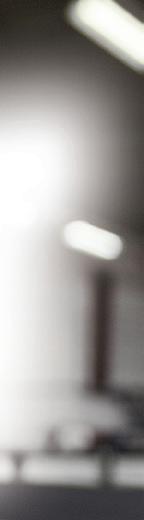
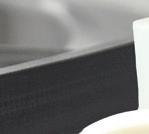
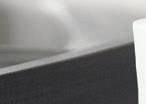
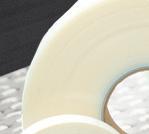
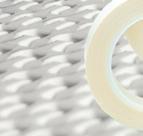
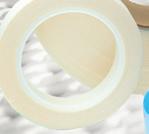
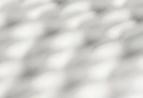
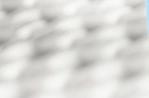
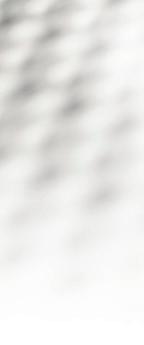
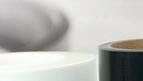
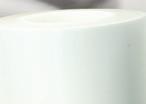

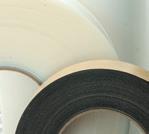
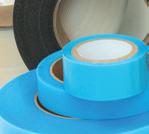
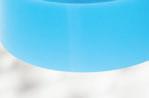
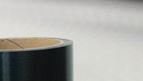
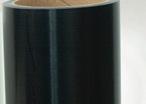
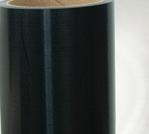


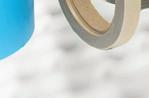
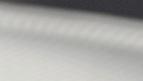
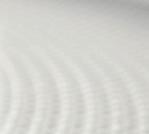
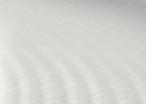



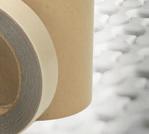
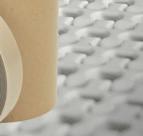
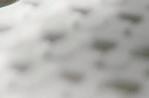
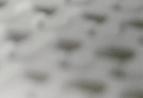

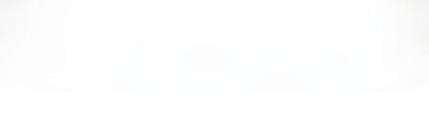

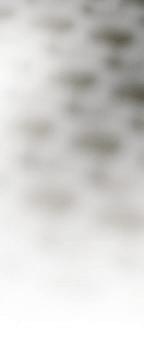
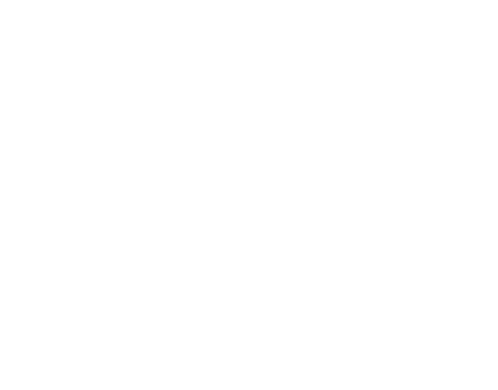

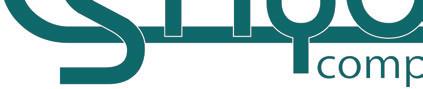
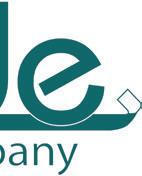
Unleashing Efficiency: The Dynamic Duo of Conveyors and Robotics in Modern Warehousing
In the dynamic landscape of modern warehousing, the integration of conveyors and robotics has emerged as a game-changer, revolutionizing how facilities meet goals of throughput and accuracy. This combination enhances operational efficiency and catapults warehouses into a new era of productivity.
Elevating Throughput with Robotic Precision:
Robotics, equipped with advanced vision systems and machine learning, are transforming the movement of goods within warehouses. Automated guided vehicles (AGVs) and robotic arms seamlessly collaborate, ensuring a continuous flow of items from receiving to shipping. Conveyors act as the arteries, efficiently transporting products between robotic workstations and amplifying throughput rates. Dorner conveyors specifically act as the Autonomous mobile robots (AMRs) and robotic arms have redefined order picking. Conveyors play a pivotal role in integrating these robotic picking systems, allowing for a smooth transition of items from storage to packing stations. This dynamic interaction ensures that orders are fulfilled rapidly, meeting the demands of today’s fast-paced supply chains.
Dorner’s 2700 Medium Duty series conveyors are designed for AGV/ AMR compatibility, allowing for quick and easy integration of the technology
into existing conveyor systems. With a robust design, increased weight rating, extended widths, and a low-profile aluminum frame, the 2700 series is ideal for applications that require both speed and precision.
Precision at Scale: Conveyors and Robotics Driving Accuracy:
Automated Quality Control: Robotics with computer vision capabilities ensure unparalleled quality control process accuracy. Conveyors serve as a conduit for products to undergo automated inspections by robotic systems, guaranteeing that only defectfree items proceed through the supply chain. This not only reduces errors but also maintains high product quality.
Error-Free Order Fulfillment:
Integrated with robotic order fulfillment systems, Conveyors contribute to flawless picking and packing processes. Robots navigate the warehouse, guided by conveyors, ensuring the correct items are selected and efficiently transported to packing stations. This collaborative approach significantly reduces order errors and enhances overall accuracy.
Real-time Inventory Accuracy: In conjunction with conveyors, robots are transforming inventory management. Drones and robotic platforms equipped with RFID technology conduct real-
time inventory checks. Conveyors efficiently transport these robotic platforms, enabling swift and accurate updates to inventory levels. This synergy ensures that warehouses maintain optimal stock levels, reducing the risk of stockouts or excess inventory.
Looking Forward: The Future of Warehousing Efficiency:
As modern warehousing continues to evolve, the integration of conveyors and robotics is a testament to technological innovation. This dynamic duo not only meets the demands of today’s throughput and accuracy goals but also positions warehouses for a future of continuous improvement and adaptability. By embracing this integrated approach, warehouses are not merely keeping pace with the times but defining the future of efficient, accurate, and responsive supply chain management.
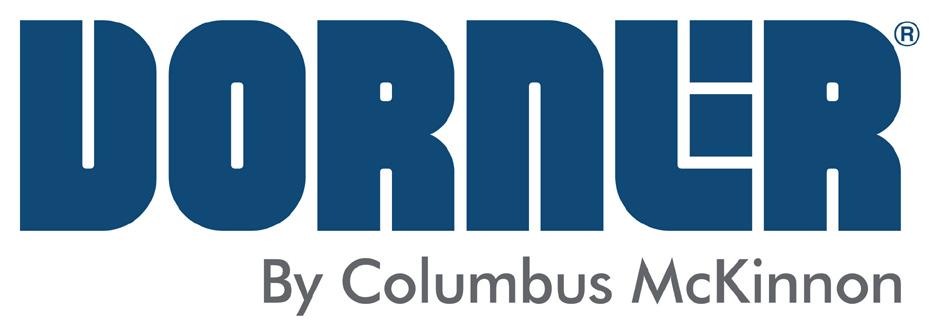
The Data Driven Warehouse
How real-time data collected at every touch point smooths out operations
Emerging technologies are revolutionizing supply planning, enhancing supply chain efficiency, agility, and resiliency. Real-time data and advanced analytics driven by connected assets and systems help identify potential disruptions, mitigate risks and make informed decisions. We will discuss key insights into today's supply chain challenges.
What are today’s supply chain challenges?
The constantly evolving global supply chain landscape poses a range of challenges for businesses today that can impact their operational efficiency and effectiveness. Here are the biggest challenges:
• Business disruptions and market volatility: Over the past five years, supply chain operations in various industries faced unexpected events, which resulted in reactive responses. This can impede the ability to meet demand, leading to lost revenue, increased costs, and a decline in overall profit margins.
• Demand predictability: Social media, COVID driven direct-to-consumer (DTC) models, market volatility, and now inflation have made traditional demand forecasting insufficient. Operations are leaning on outdated forecast approaches that also lag and fail to respond adequately to current market dynamics.
• Holistic inventory visibility and optimization: Inventory management is complex and dynamic. The end of 2022-2023 saw excess inventory across many organizations due to COVIDrelated supply chain constraints. This led to higher costs, lower margins, and waste. The long term impact will lead to lost sales, and loss of differentiation, loyalty, and market positioning. Adopting an integrated approach and leveraging advanced technology and best practices, businesses can overcome these challenges - improving supply chain efficiency and resilience.
What is lacking in today’s supply chain strategies?
Supply planning today involves technology, data analysis and stakeholder collaboration. While technical and data analytic advancements have been made, there are still several areas that need improvements in the industry:
• Accurate transparency of data
• Dynamic supply planning and execution based on integrated intelligence and automated decision-making
• Convergence of network modeling, scenario and traditional planning and planning
Businesses want to improve supply chain visibility, predict, and mitigate risks, and optimize performance. Incorporating advanced concepts can enhance agility and resilience, meet customers’ evolving needs, and optimize performance. Below are a few advanced technologies and characteristics that must be included in an organization’s growth plans for supply chain optimization.
• Artificial intelligence and machine learning: Artificial Intelligence (AI) and Machine Learning (ML) can help businesses analyze data, find patterns, and make proactive decisions to mitigate risk. Many planning solutions have already integrated AI/ML into their core plans, but further integration of this can enhance algorithms. This could include detecting shifts and anomalies -- optimizing execution, automating operations such as key planning processes and real time decisions, and more.
• Digital twins and advanced simulation: Digital twins and simulation create virtual versions of physical assets, processes, and systems. These outputs can be used to evaluate scenarios and risk, identify key constraints, optimize, and evaluate alternative configurations.
With data and AI/ML, digital twins can continuously evaluate supply chains and networks, informing businesses in an unprecedented way.
• Automation and autonomous systems: The targeted deployment of automated storage retrieval systems (ASRS), autonomous mobile robots (AMR) and other assets with IoT connectivity, RFID asset tracking and machine vision can mitigate risks ranging from labor shortages to inventory loss. Working in tandem with digital twin and AI/ML, these assets comprise self-optimizing systems that drive higher output and efficiency by learning from both physical and simulated scenarios in the connected warehouse.
The future of supply chain planning requires digitization, automation, connectivity, and data-driven decision-making. Organizations that embrace these technologies create agile, transparent and efficient supply chains that are resilient to market changes and disruptions.
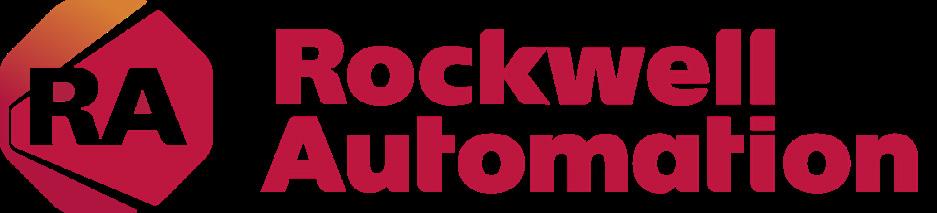

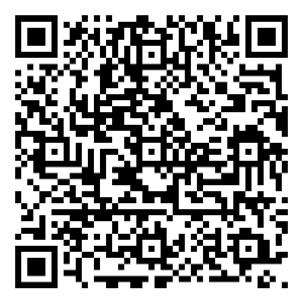
You can read more in our recent whitepaper, Synchronizing Supply & Demand in 2023 and Beyond.