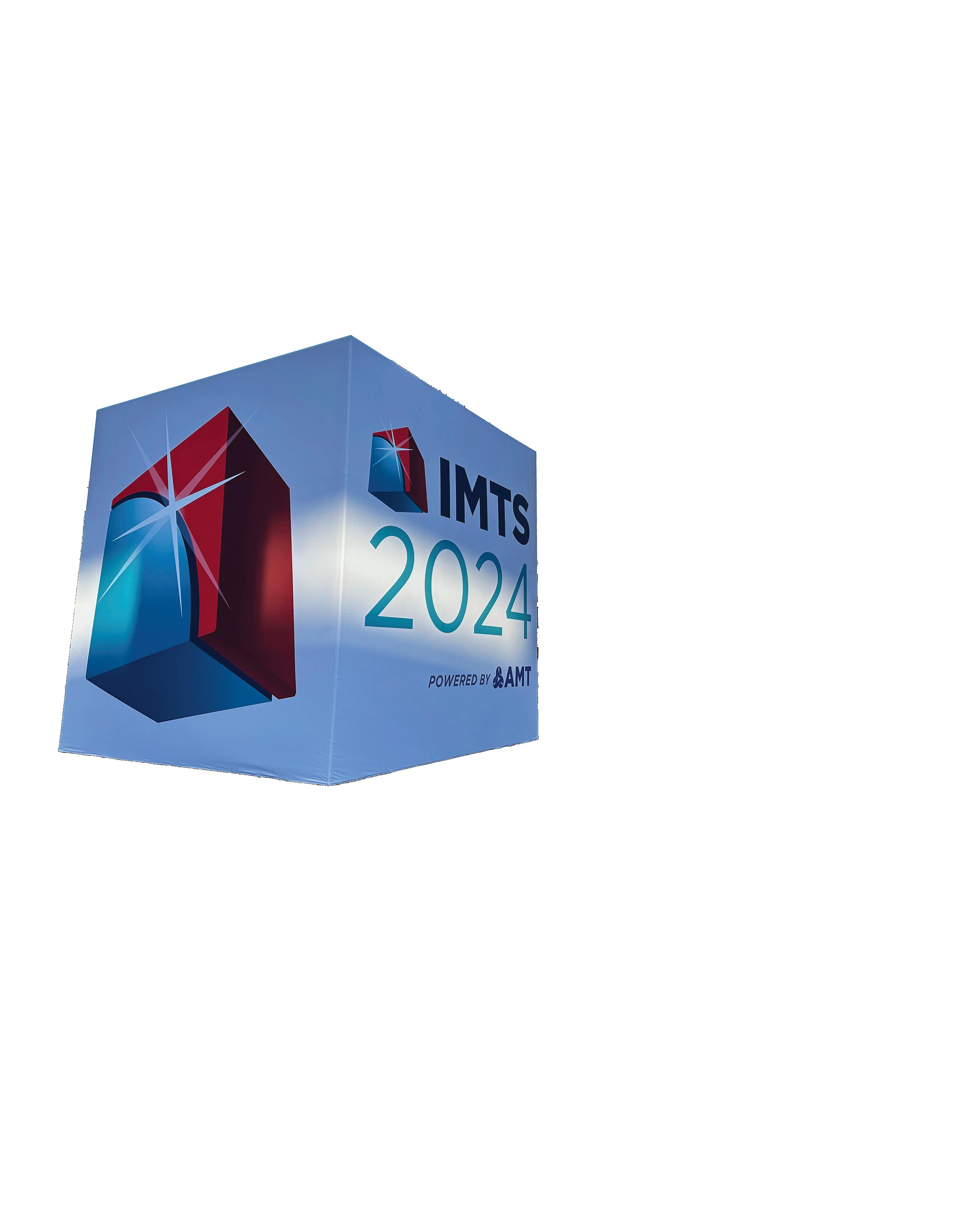
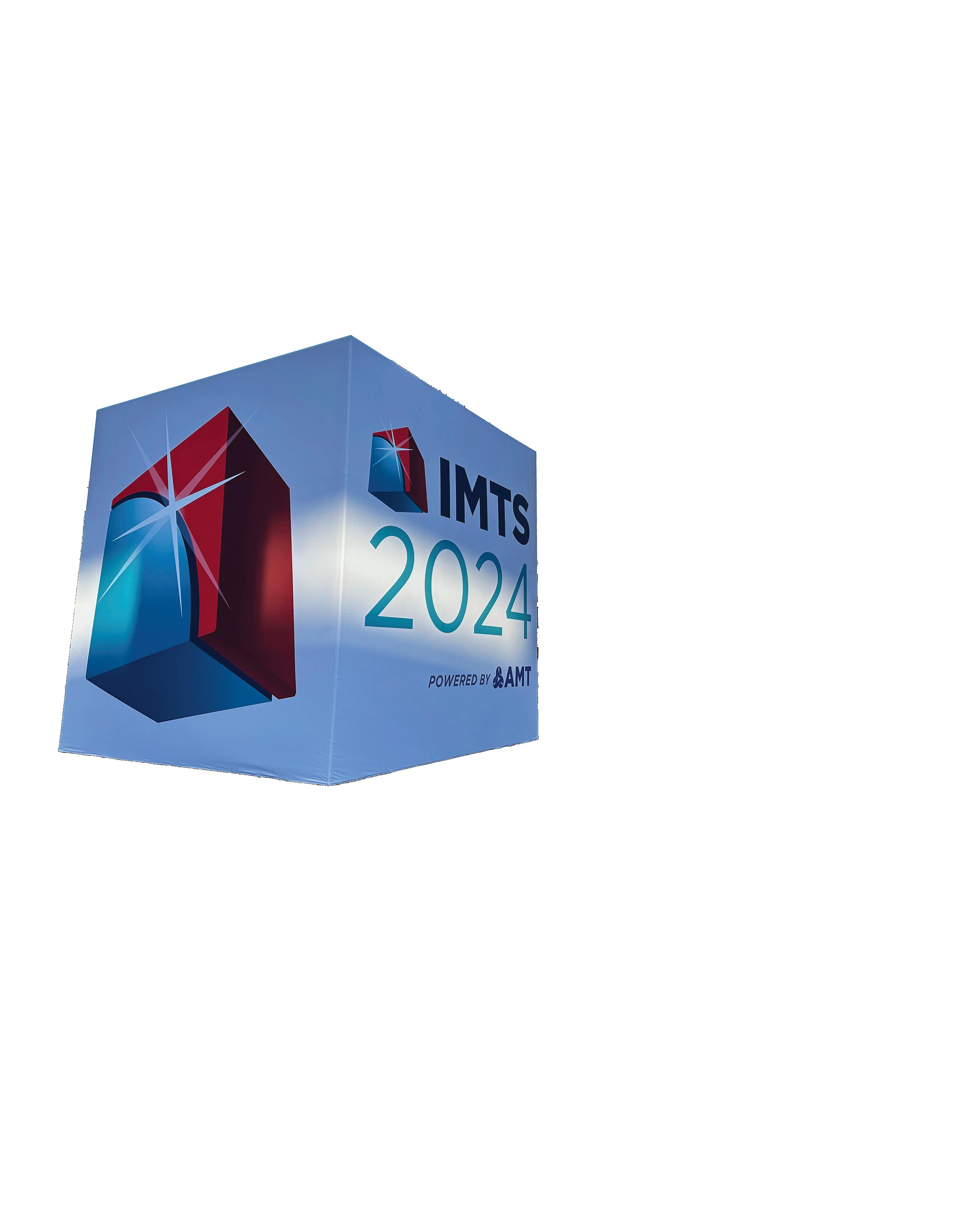
The democratization of automation takes center stage at IMTS
STEPHANIE NEIL • EXECUTIVE EDITOR
Artificial intelligence, together with the adaptive data cloud, has profoundly changed operations in the warehouse and on the factory floor.
The ability to analyze data across the entire value chain is improving productivity, aiding maintenance operations, and creating new serviceoriented business opportunities. That was the message Microsoft’s Kathleen Mitford delivered in her opening keynote at the International Manufacturing
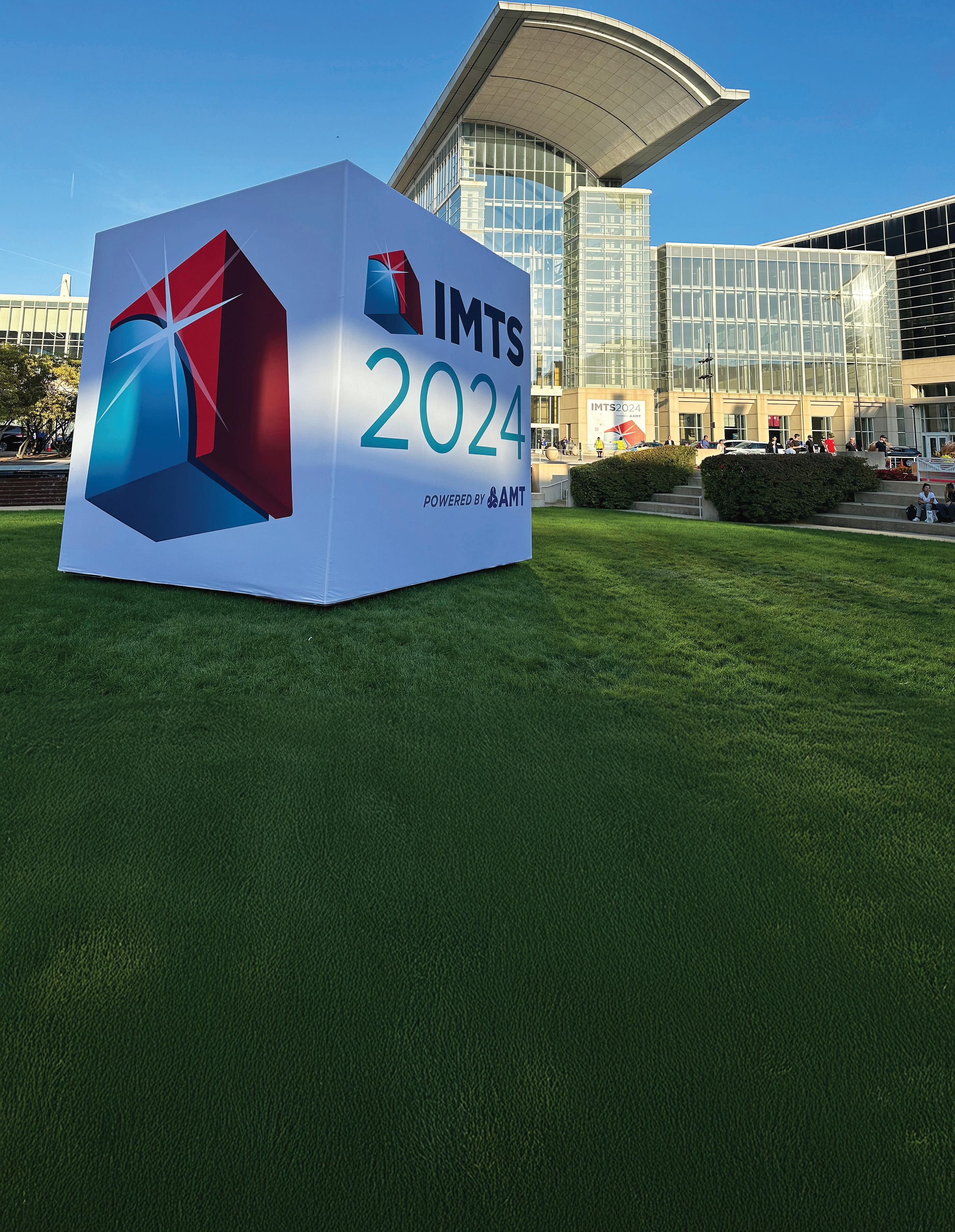
Technology Show (IMTS) 2024 in Chicago this past September.
From combing through CAD libraries to applying natural language models to maintenance records for delivering stepby-step instructions on how to fix a robot or even a jet engine, manufacturers have undergone an AI transformation. Everyone — from the CIO to the engineer to the operators — can access programs like Microsoft’s Copilot to act as a generative AI assistant.
The democratization of AI is an inevitable part of the factory floor going forward. “Basically, if [manufacturers] have not started on their AI journey, they’re late,” said Mitford, Microsoft’s corporate vice president of global industry marketing, in an interview with Automated Warehouse.
And if organizations are late with AI, they will miss out on the next evolution of AI, which is the democratization of automation
Photo courtesy of IMTS
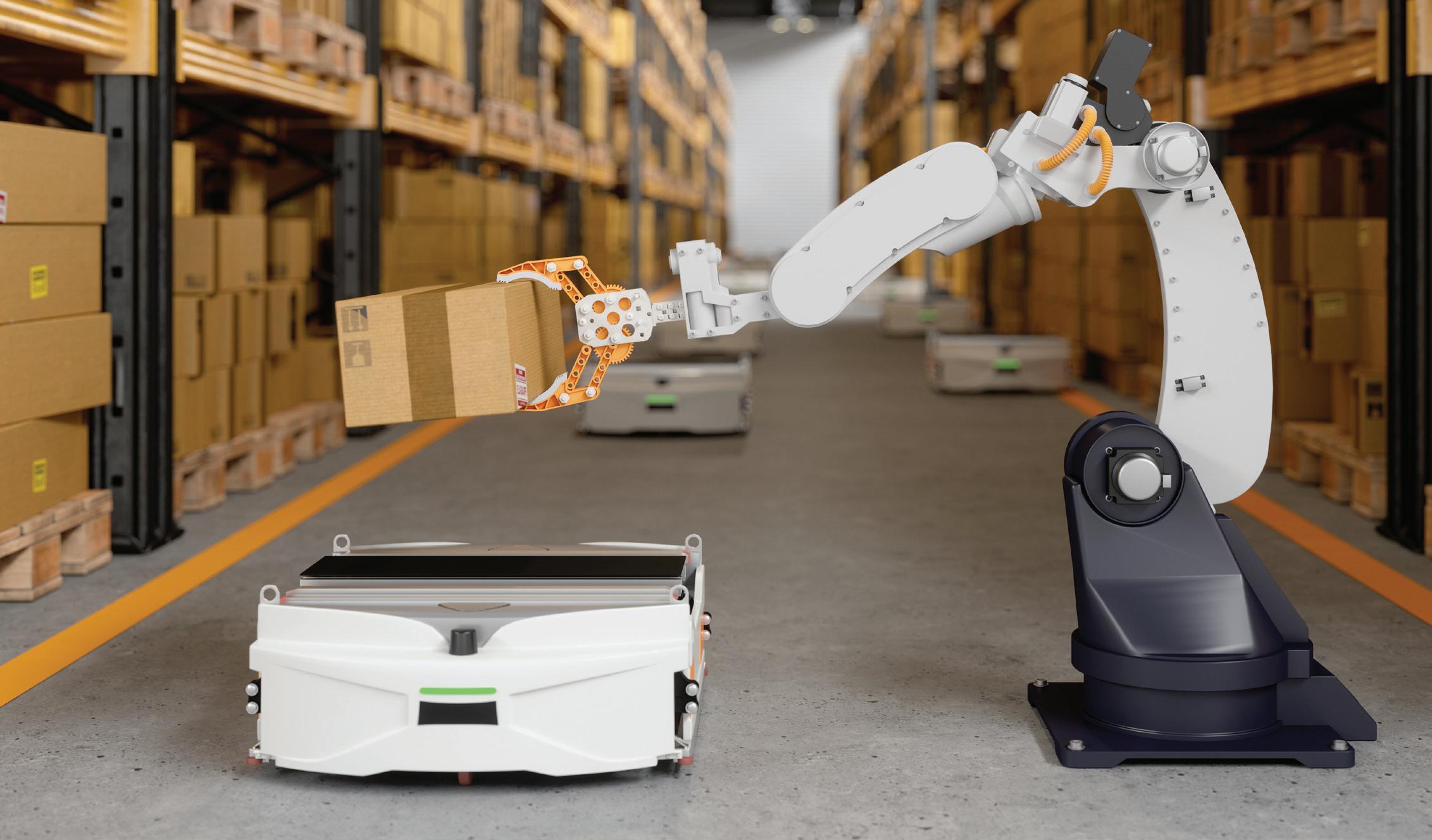
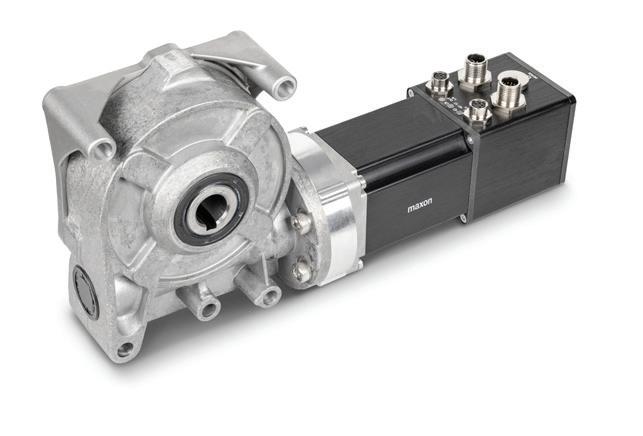
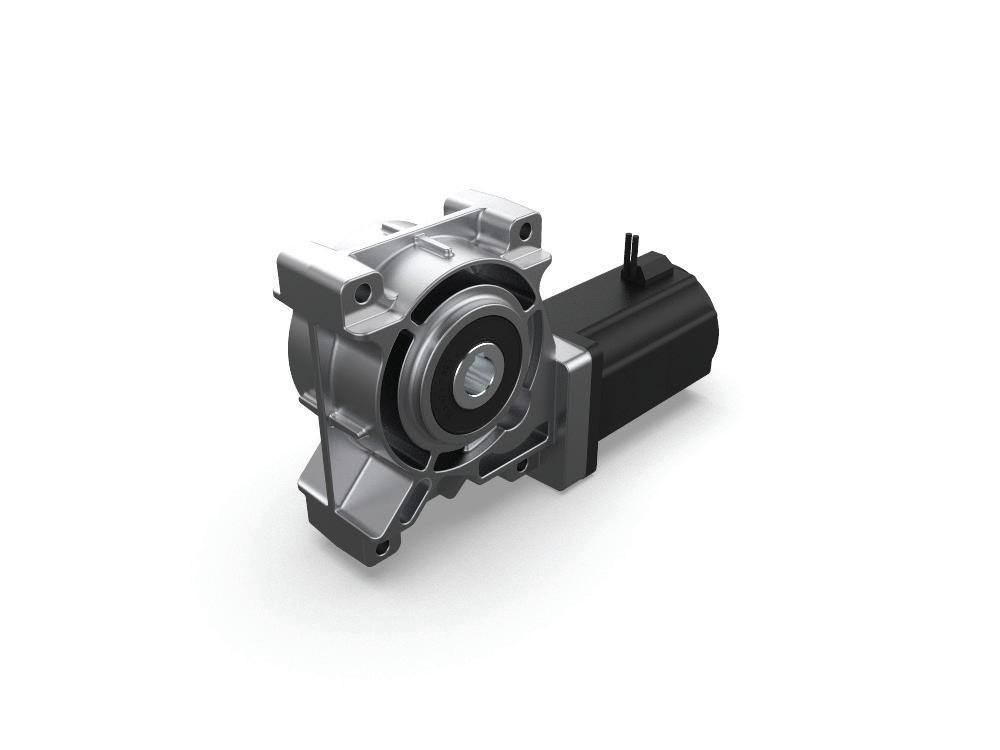



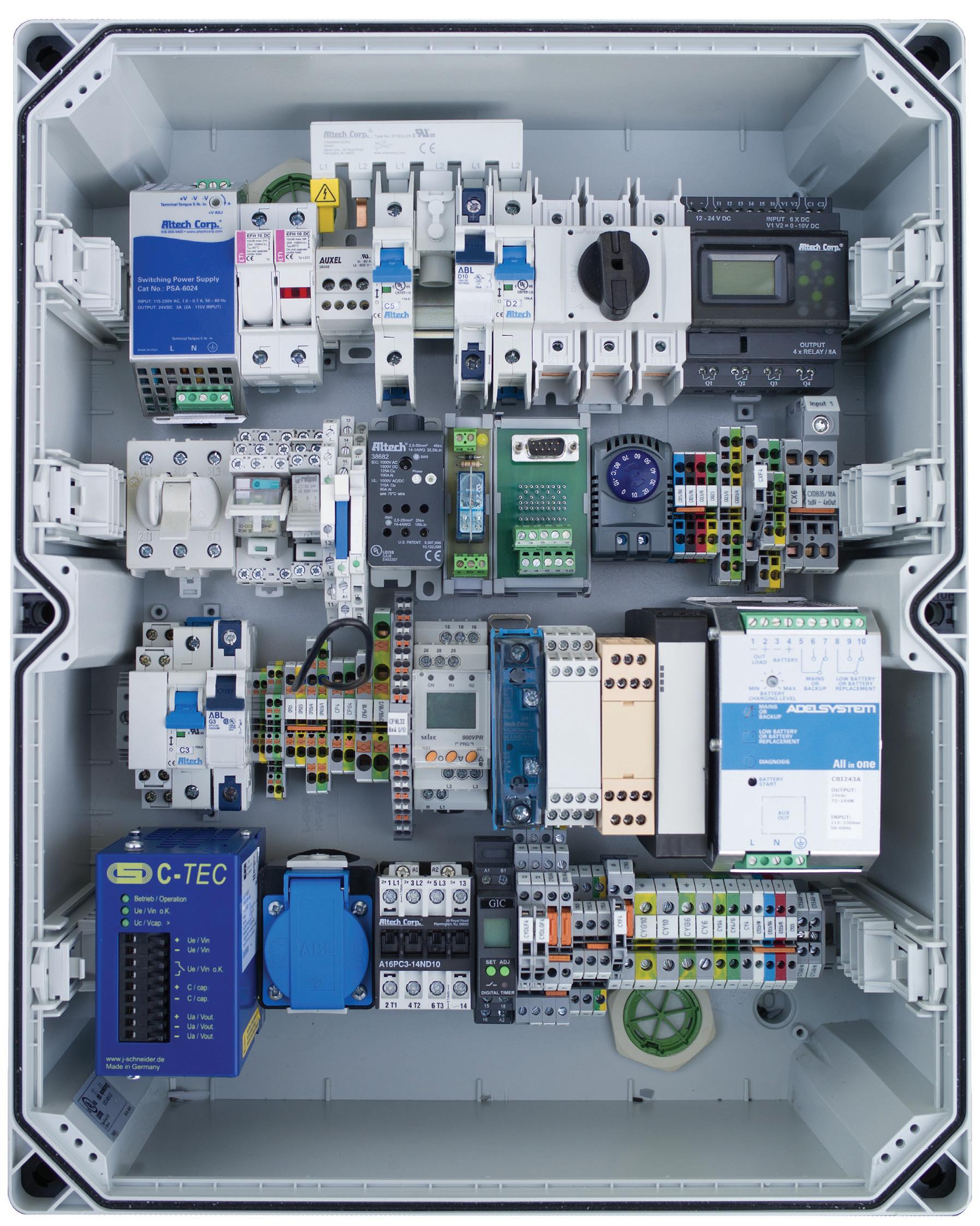
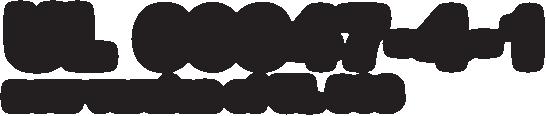
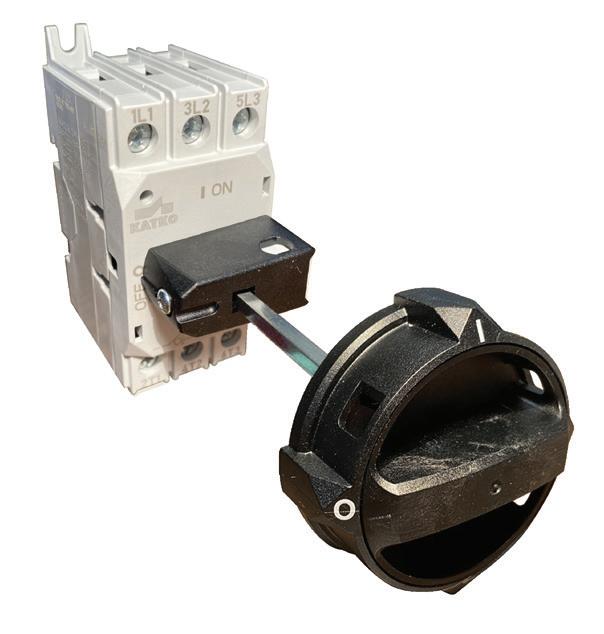

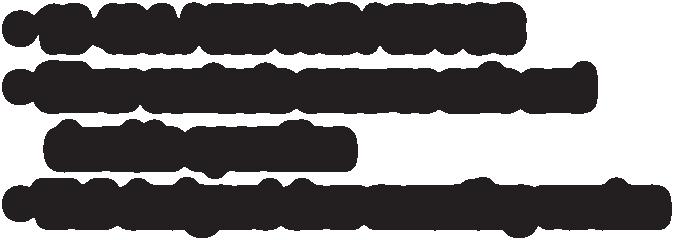

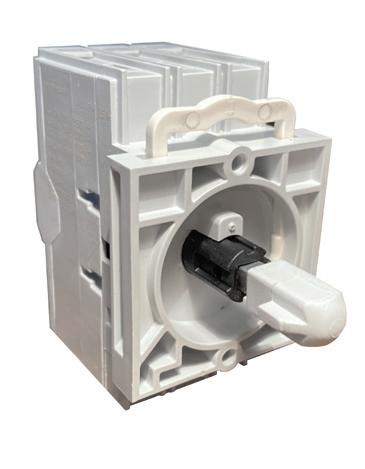
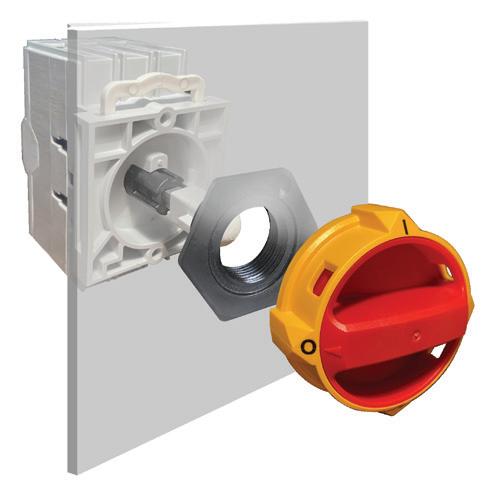
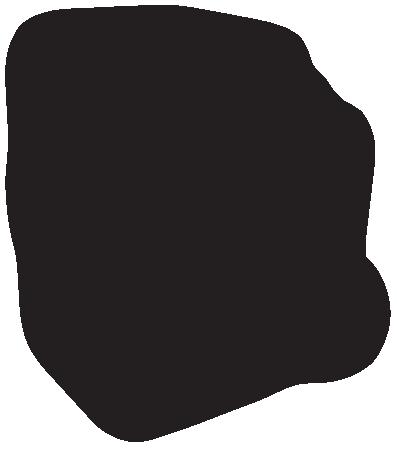
Automation democratization
During IMTS, there were examples of new products and services that unite AI and automation via programming, remote diagnostics, workcell workflows, and even self-service marketplaces to design and buy a machine online.
Here are just a few examples on display at IMTS that showcase these emerging areas of innovation:
Osaro: The Osaro Robotic Bagging System is an e-commerce robotic setup that can accurately scan and identify disparate items in a tote, effortlessly handle new SKUs, and quickly adapt to changing inventory. This allows the robot to pick and place multiple items into the auto-bagging machine and then to the conveyor to go out for delivery.
What’s different here is the company’s AutoModel. It allows AI to learn on the fly versus having to be trained, which is time-consuming, according to Brent Barcey, Osaro’s senior vice president of corporate development. Its rapid AI system allows for dynamic changes in the inbound and outbound flow of goods and the
integration of new peripherals, enabling the order-fulfillment line to adapt and evolve in real-time, ensuring continuous efficiency and productivity.
Olis Robotics: The company’s videobased remote diagnostic system watches a robot 24/7 on the packaging line or warehouse. Power over Ethernet cameras are set up around a cell, and when the visual system detects an issue, it saves the video files to allow an engineer to see what happened and even remotely take action.
Working with Universal Robots (UR), FANUC, and Kawasaki robots, the diagnostic system can connect to multiple robots through the robot controller. It also connects to the PLC that provides stats on what’s been going on for the past minute or past 24 hours.
“This is a pretty comprehensive diagnostic suite for automation,” said Olis CEO Fredrik Rydén, noting that the data allows for predictive maintenance as well. “When you have facilities that have a lot of volume of products going out the door, you want to keep them

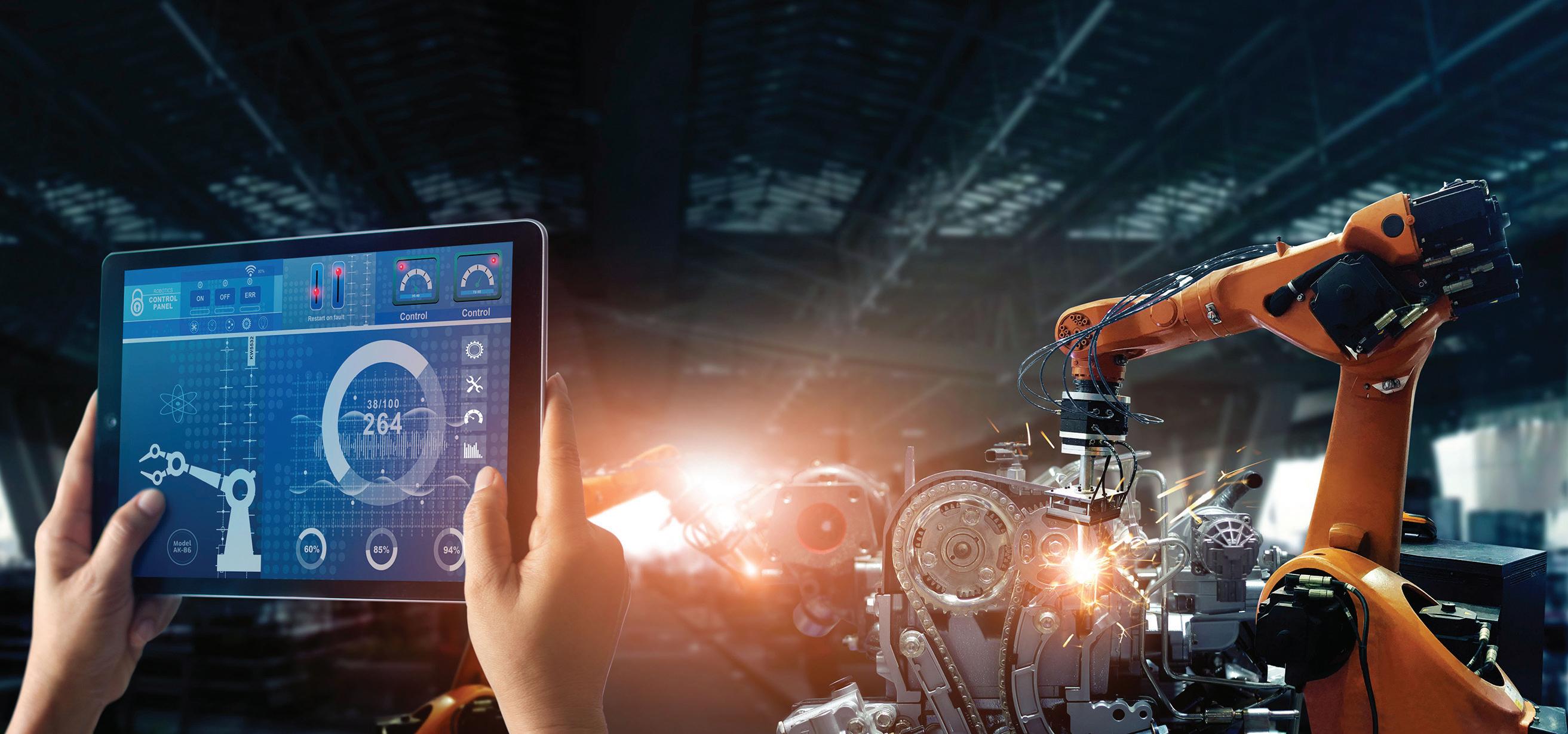
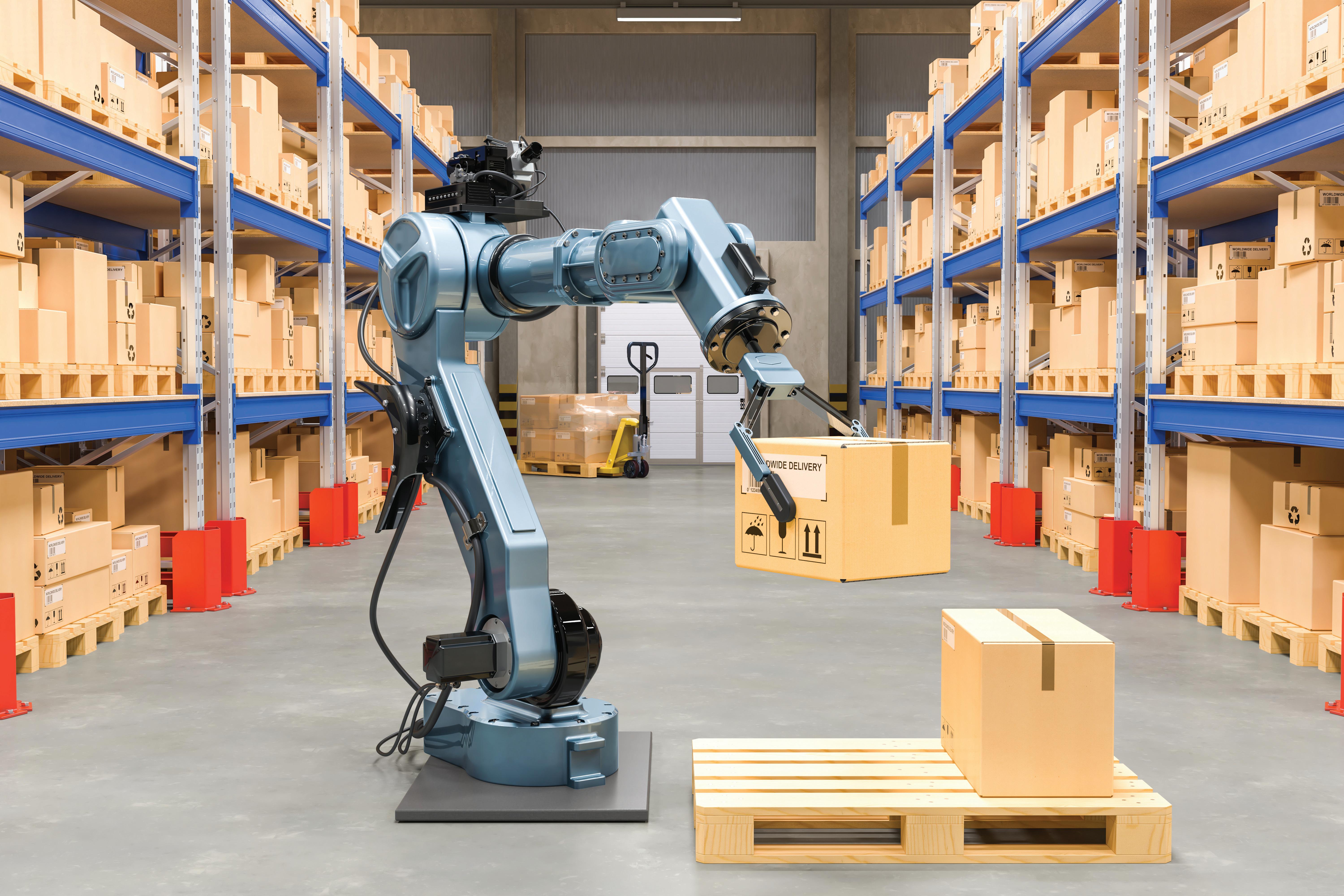
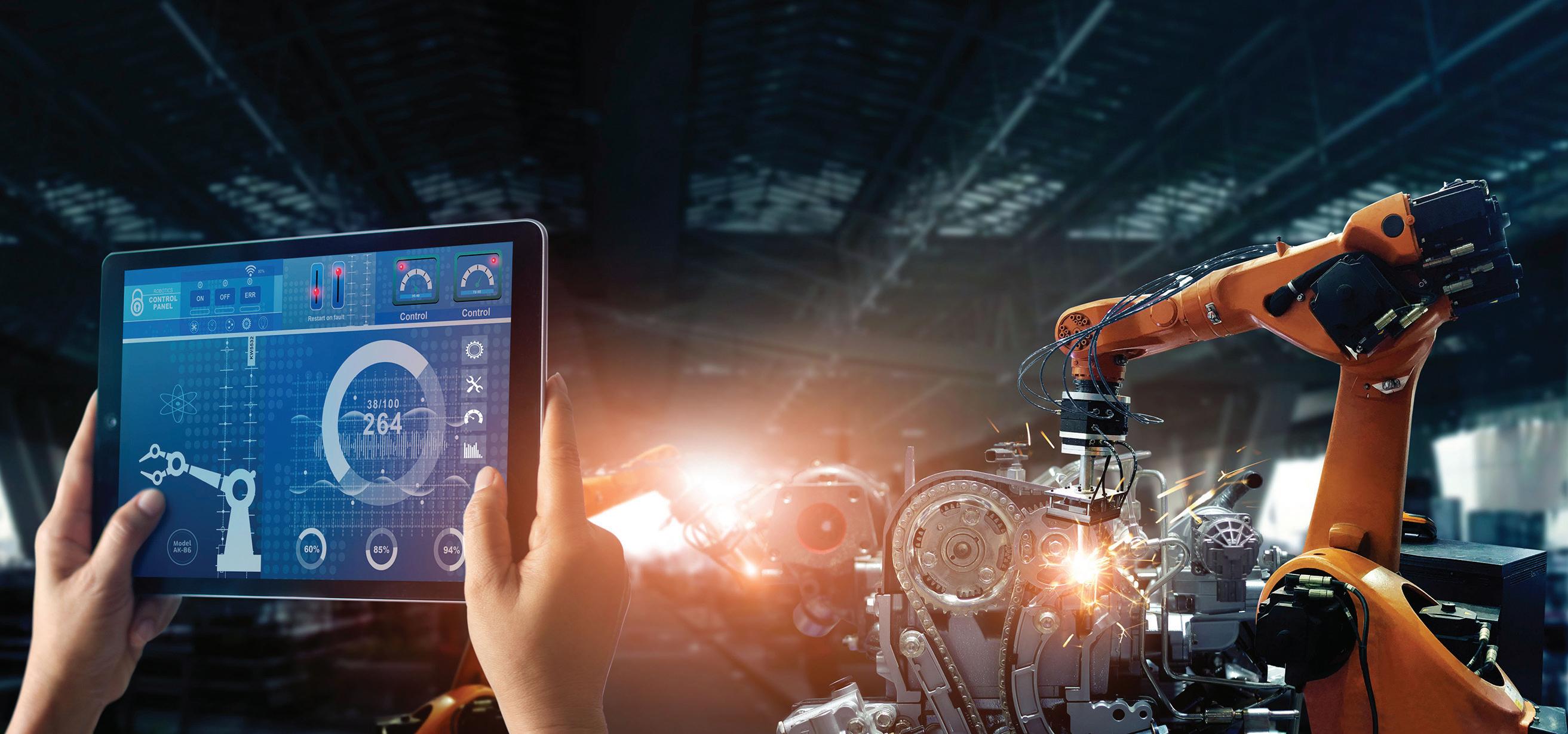
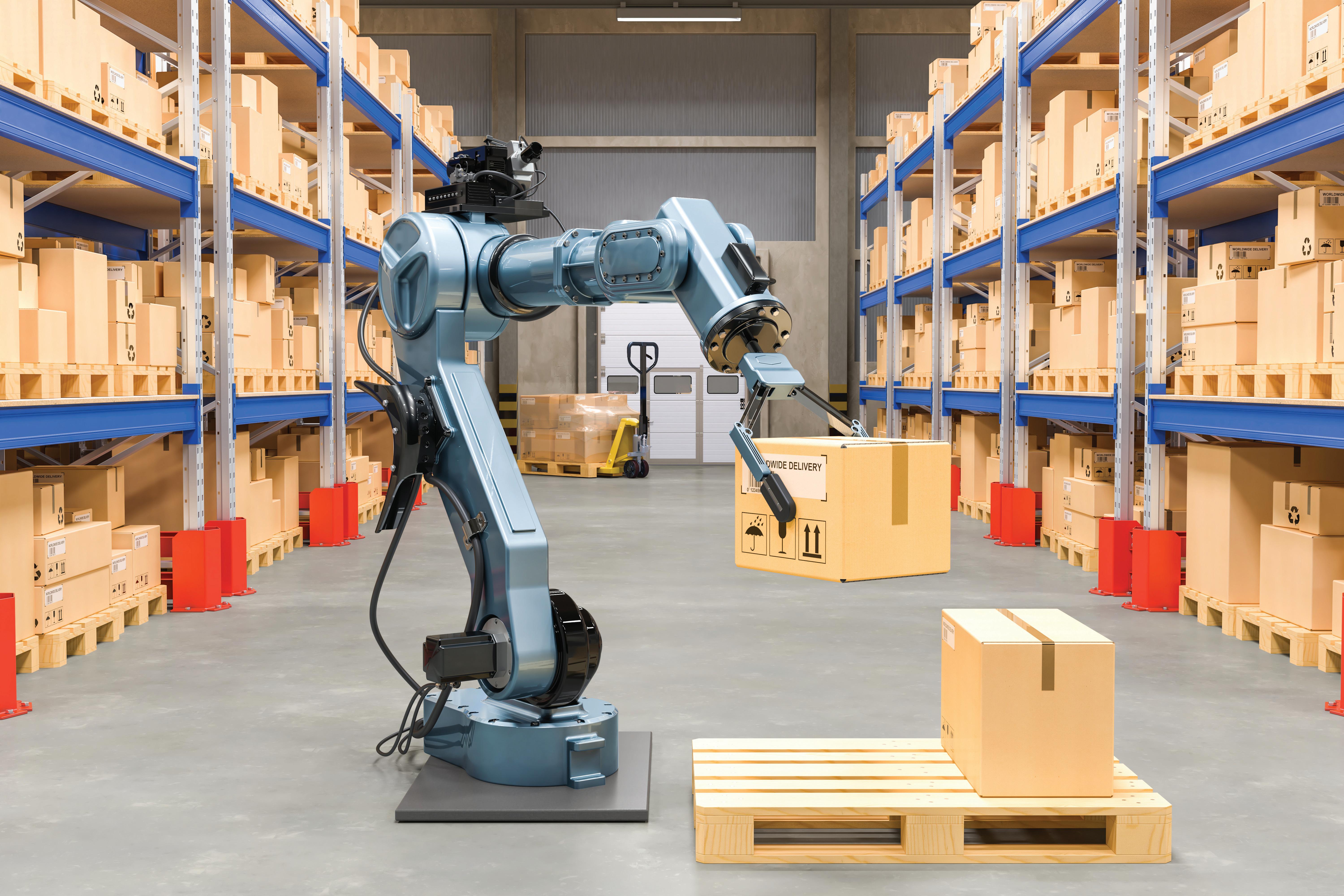
Osaro’s Robotic Bagging System uses AI to learn on the fly. Stephanie Neil
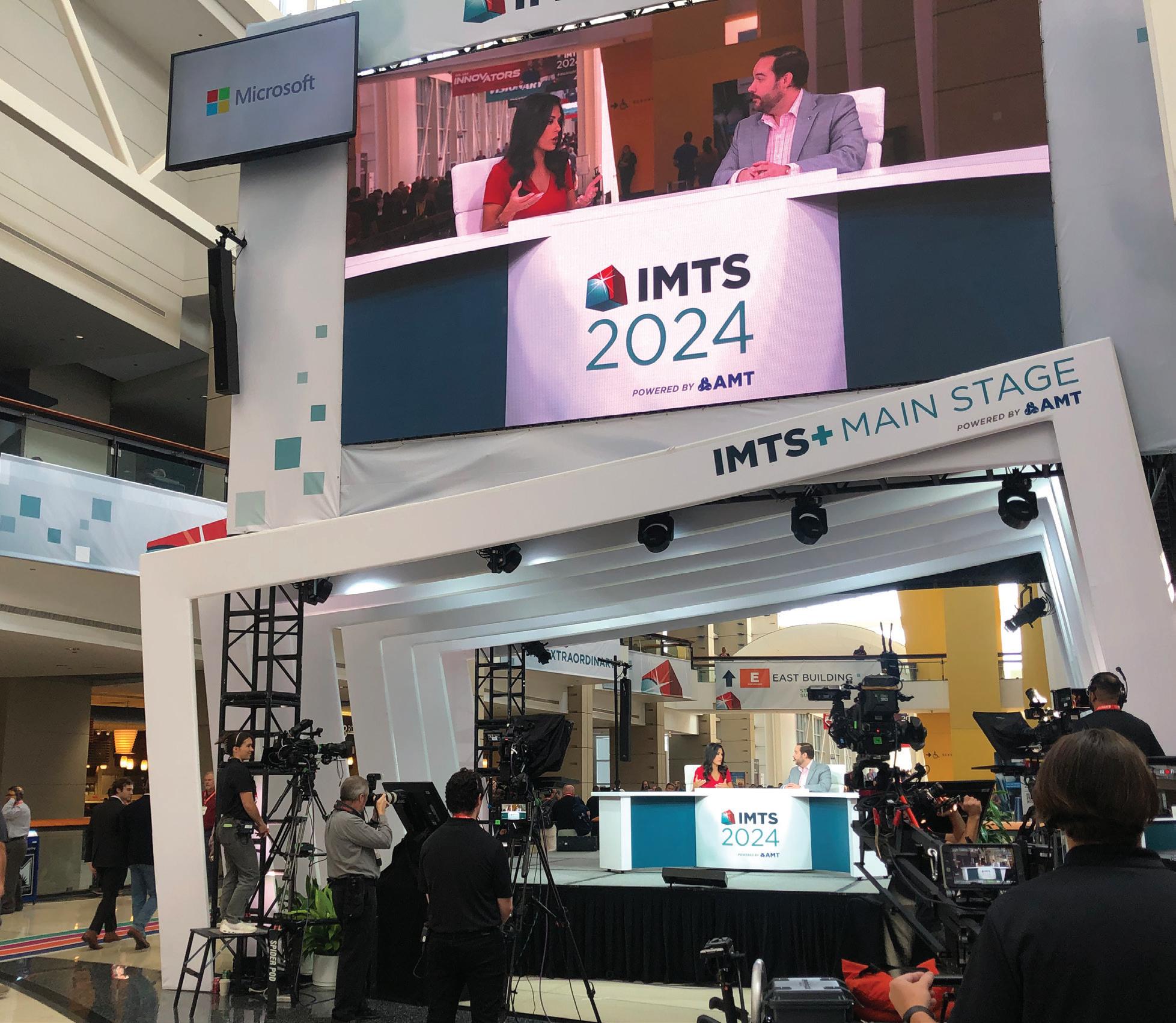
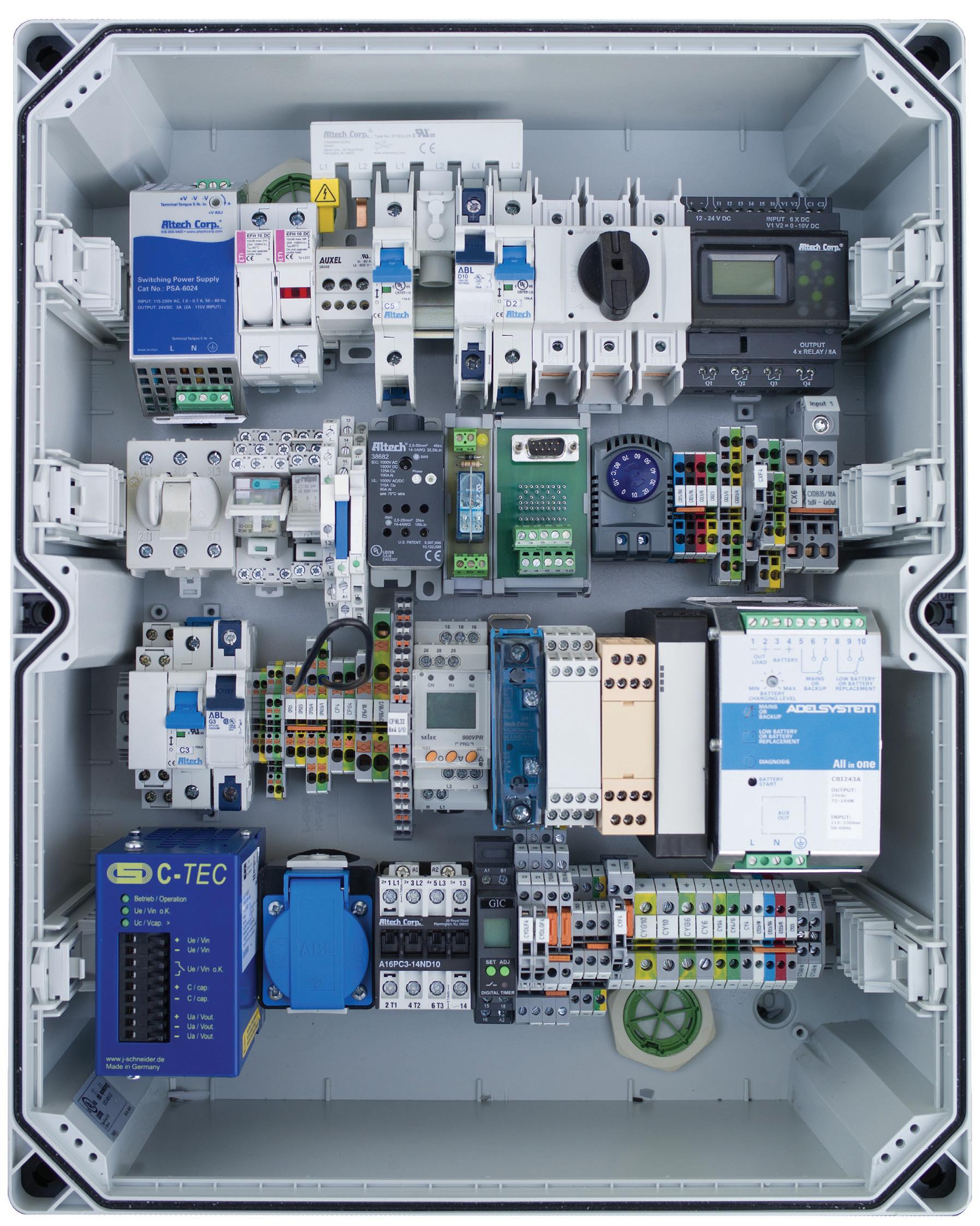

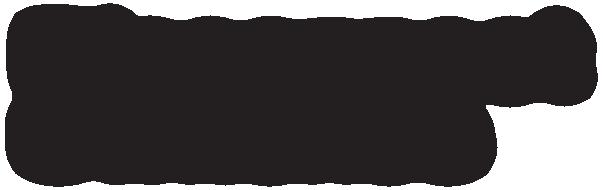
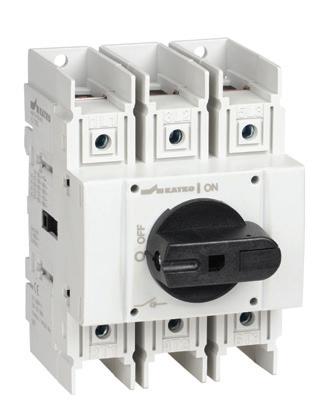
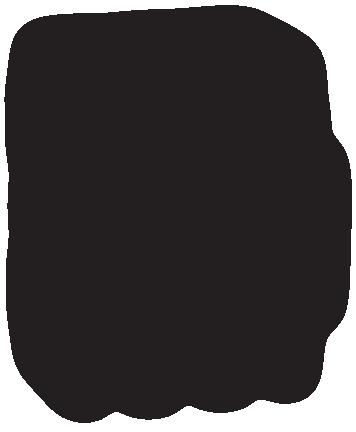
running. This is a tool to ensure you can do that.”
In addition, by partnering with collaborative robot providers like UR, the goal is to make the robot experts more efficient, especially in the face of a labor shortage.
“What UR has been spearheading is the ability for anyone to adopt automation by making it easy to program the robots. Now it is easy to keep them running as well,” Rydén said.
Tulip Interfaces: This no-code system offers an almost effortless way to build applications, which could be workflows, traceability, dashboards, or machine monitoring, for example. The common data model includes templates for different applications that are available for download and includes application program interfaces (APIs) to connect other applications.
As part of the system, the operator is provided instructions, as well as
continuous feedback to show errors that may have occurred during a repeatable process. In addition, the Tulip starter kit provides pre-built applications that can be implemented in multiple ways. This allows small and large manufacturers alike to adapt the system to their processes.
“The goal is to democratize this so you don’t need to be an engineer to do it,” said Natalia Gutierrez, product marketing manager at Tulip.
Vention: When it comes to designing a machine, Vention is incorporating AI into the process to make suggestions on the next component – which is added automatically to expedite the design process.
On the automation side, Vention released a machine motion AI controller with NVIDIA Jetson. The low-power system is designed for accelerating machine learning applications and enables robots to learn in the cloud.
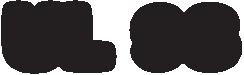
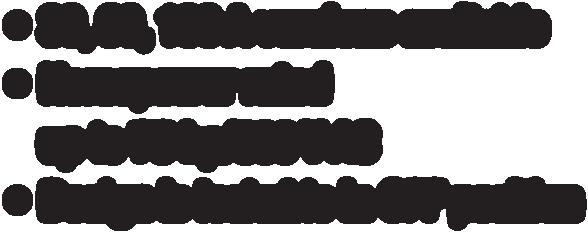
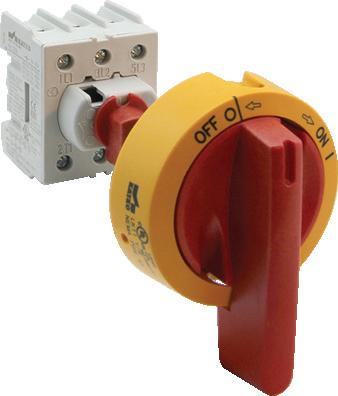
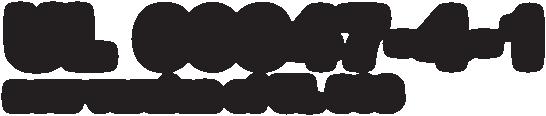

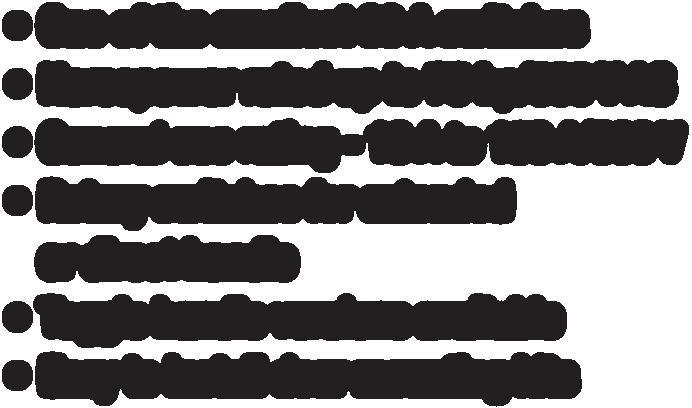
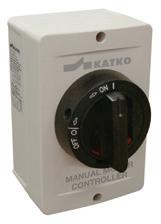
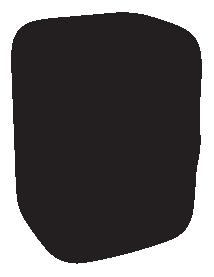
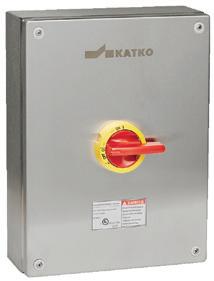
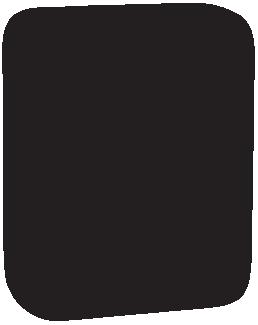
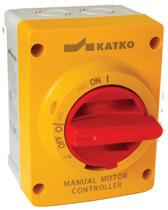
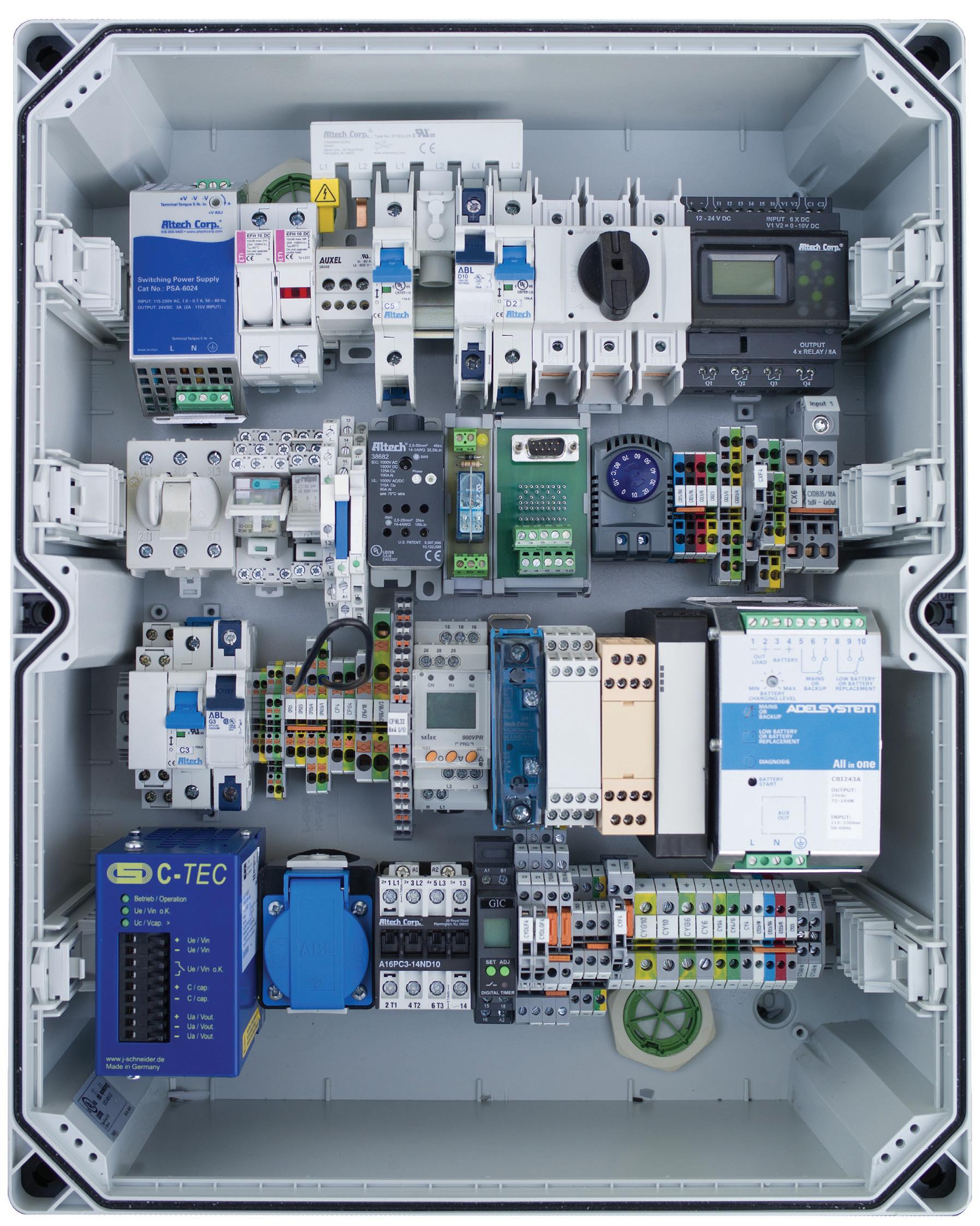

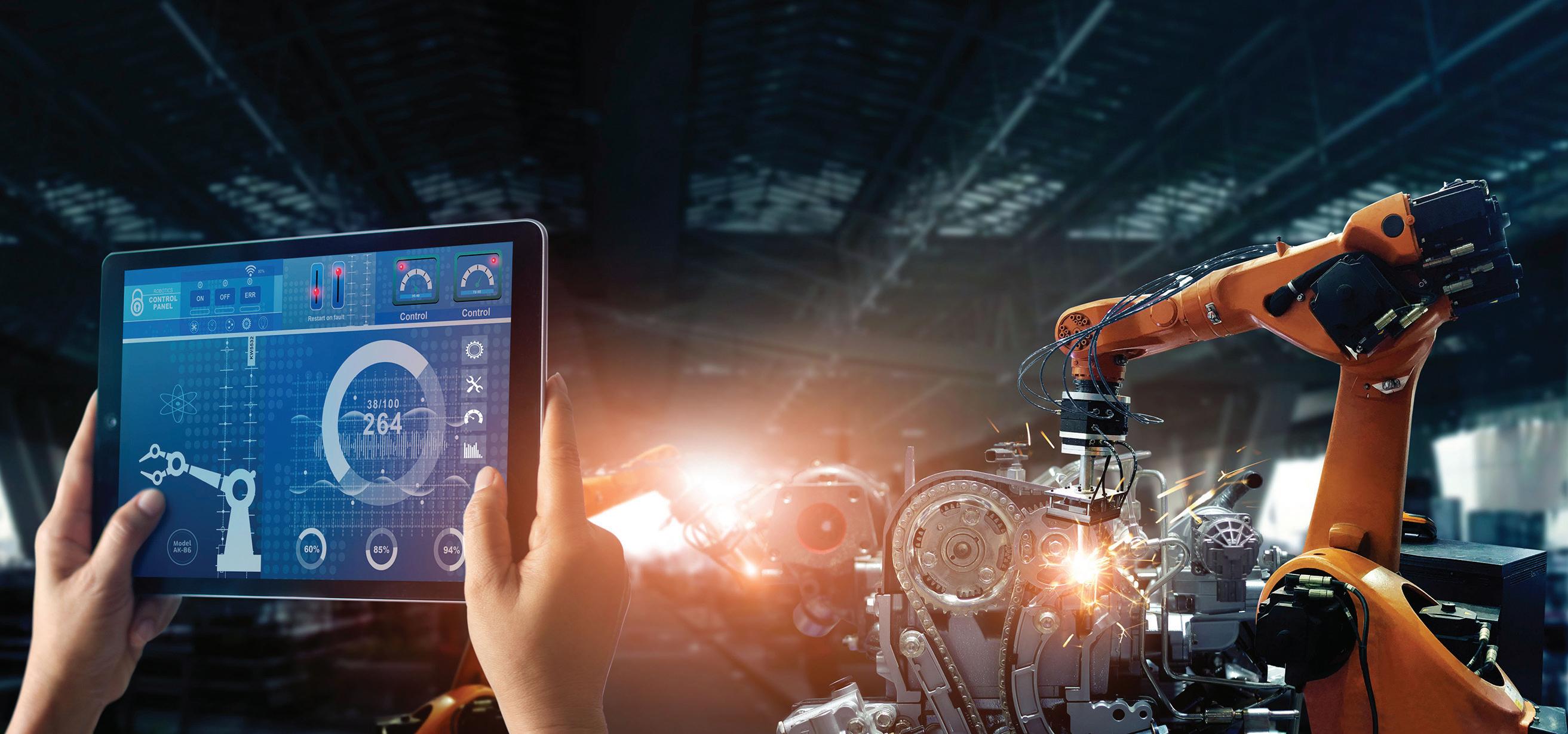
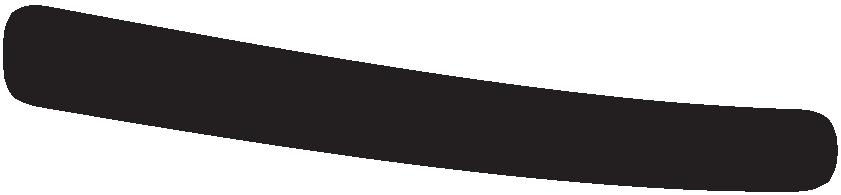
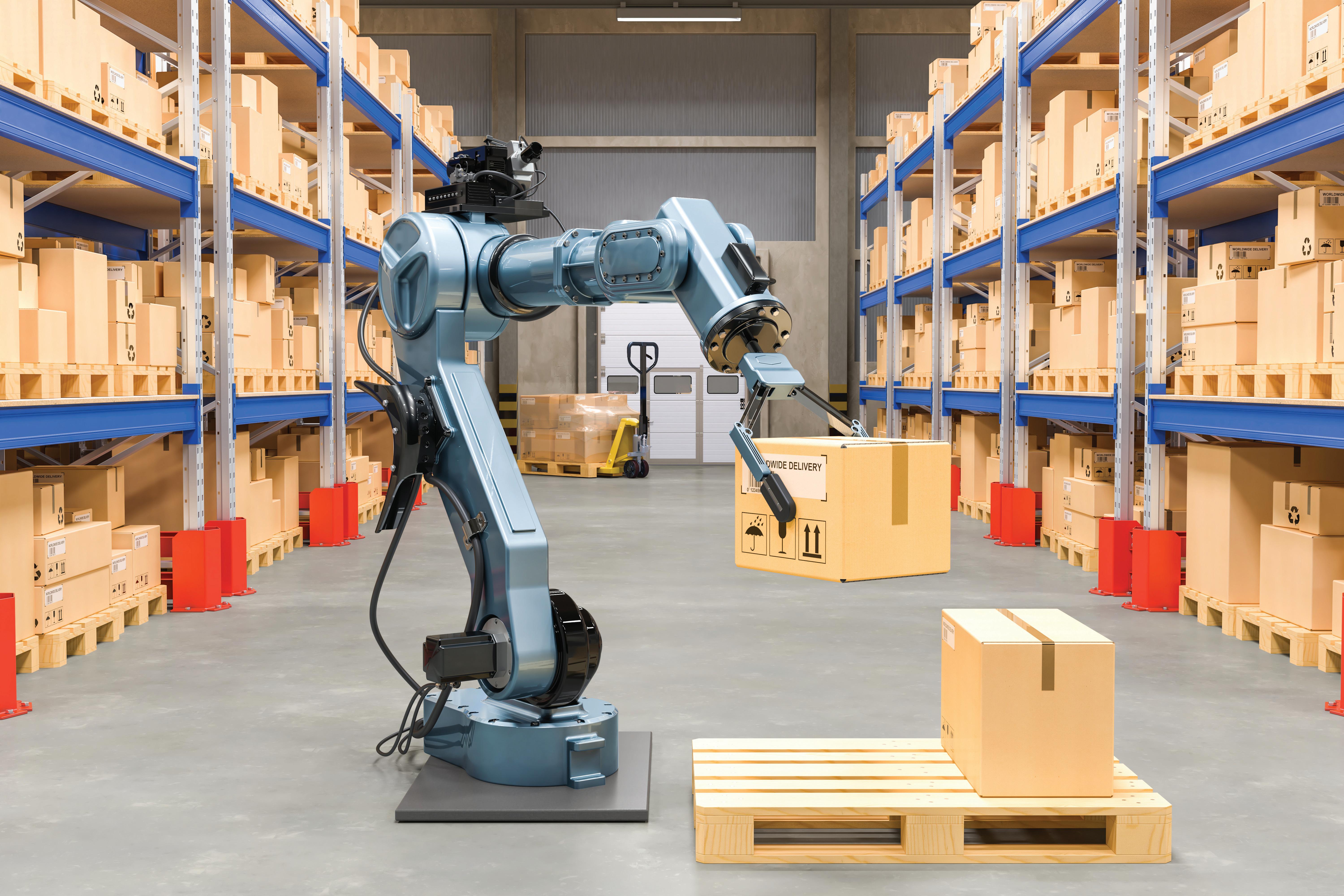
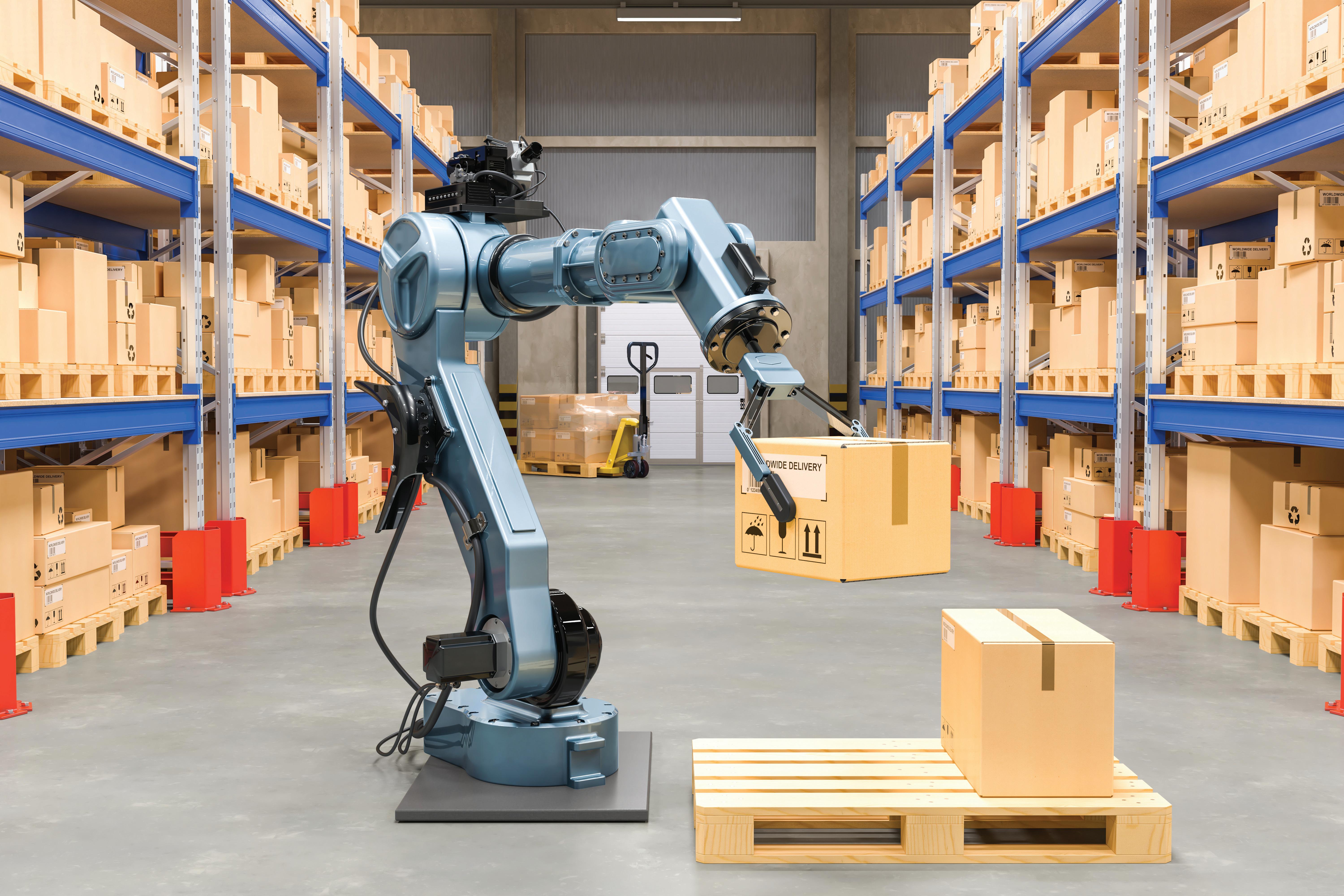
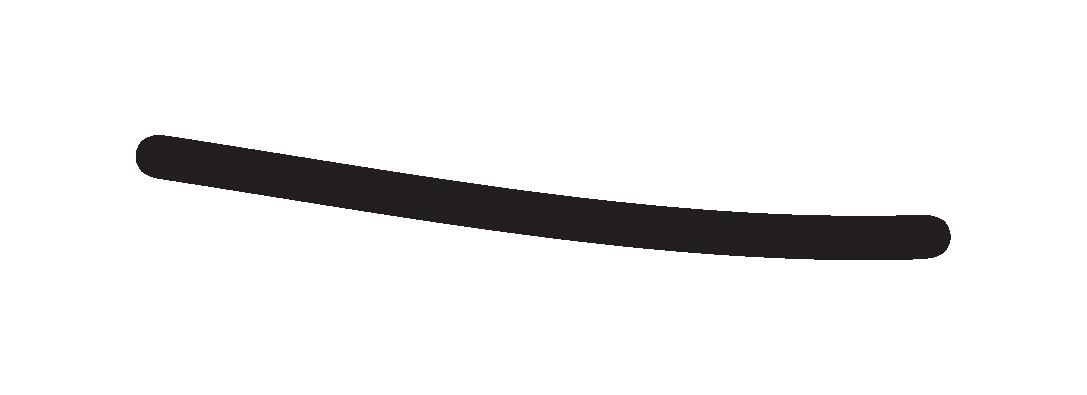
Stephanie Neil
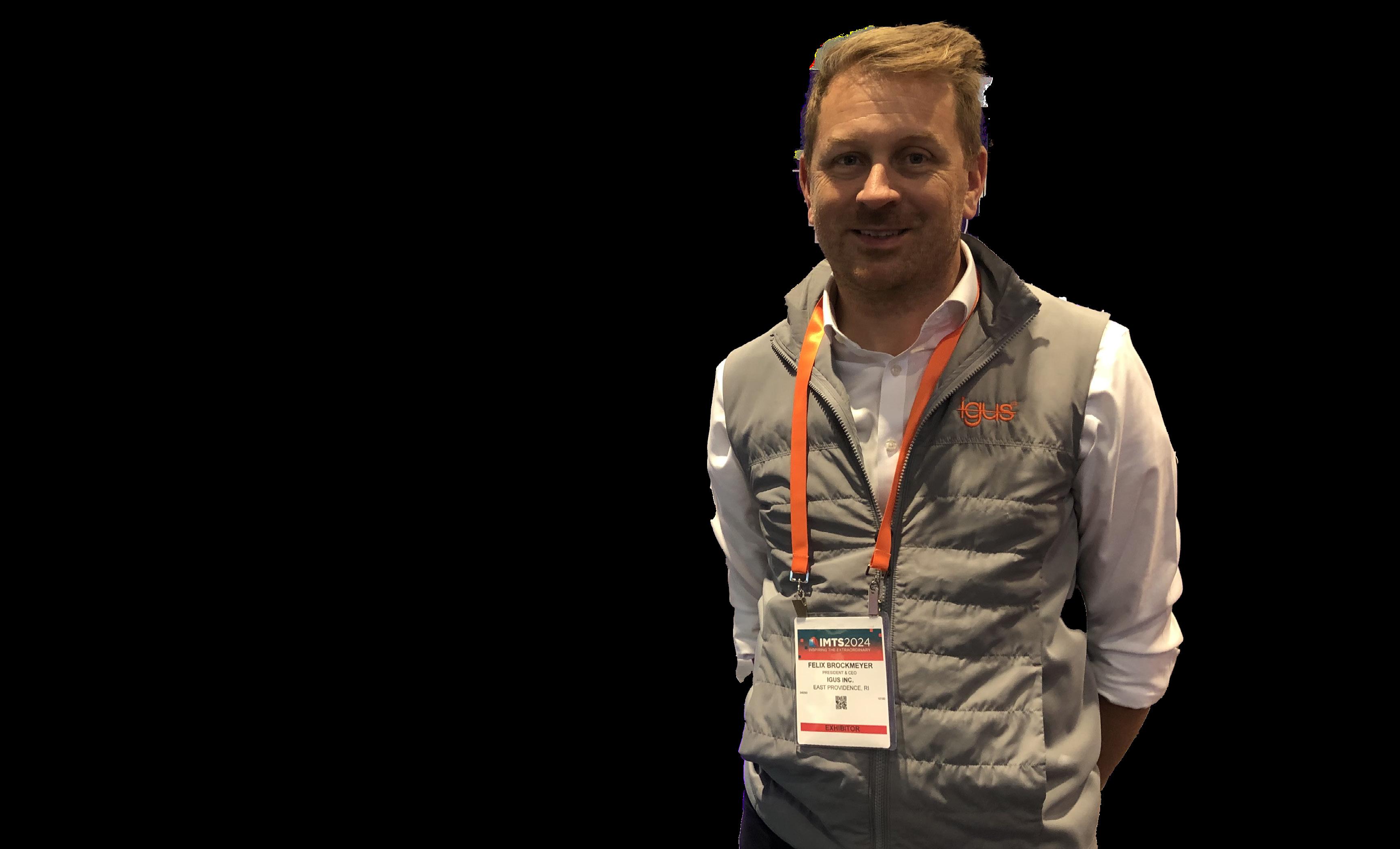
“We’ll have a robotics model in the cloud that will learn from the operation that is running to give you a better program for your robot for more efficient operation.” said Carl Hajal, Vention’s senior software and robotics segment manager.
He noted that Vention differentiated its AI offering by applying it both on the controller and in the cloud. When programming a robot, Vention has also added a co-pilot that can write a program for the engineer and push it into an existing script to update it.
Hajal claimed that this should accelerate programming by about 50% for engineers.
Welcome to the automation marketplace
Vention is known for its self-serve platform, which allows OEMs to design automated equipment, robot cells, and tooling online, while providing real-time bill of materials and pricing information before the equipment is shipped out for assembly on site.
Now, with the proliferation of tools and cloud-based services that make automation accessible and easy to use,
self-serve marketplaces are popping up from different technology providers. igus: The motion plastics company makes flexible cables, chains, linear bearings, slides, actuators, motors, and more. The differentiator for igus products is its self-lubricating material, a proprietary blend, said Felix Brockmeyer, igus CEO.
Over the years, customers have asked igus to assemble its parts into entire systems. Now, the company has an internal startup, called RBTX by igus, which is an online marketplace that connects users with suppliers of compatible, cost-effective robotic components using simple tools.
“It started with small and midsized manufacturers and OEMs in mind, but now everybody is our customer base,” Brockmeyer told Automated Warehouse. “There is a need in the market to offer simple automation instead of what normally is overkill.”
To that end, pricing for specialized robot applications such as pick and place, material handling, machine loading and unloading can be offered at lower price than a traditional feature-rich system.
“There wasn’t an offering in the market to address people that just want to do simple automation tasks,” said Brockmeyer. The igus robot control includes the company’s own open-source software, which can be downloaded for free to start writing programs before buying a robot. There are also application-specific overviews including videos showing how it works.
“It’s automation for anybody,” Brockmeyer said.
Universal Robots: The UR Marketplace was also a talking point at IMTS. It is a one-stop shop to choose and purchase cobots, components, and services. The platform offers a range of equipment from the UR ecosystem and a quoting and ordering management process and 24/7 call support. AW
For more news on AI and digital transformation in the warehouse, visit Design World’s sibling site Automated Warehouse at: automatedwarehouseonline.com
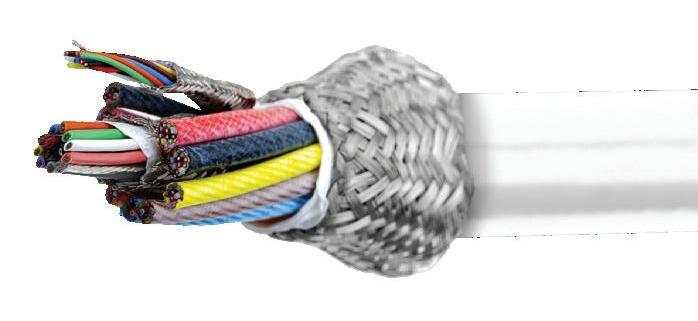
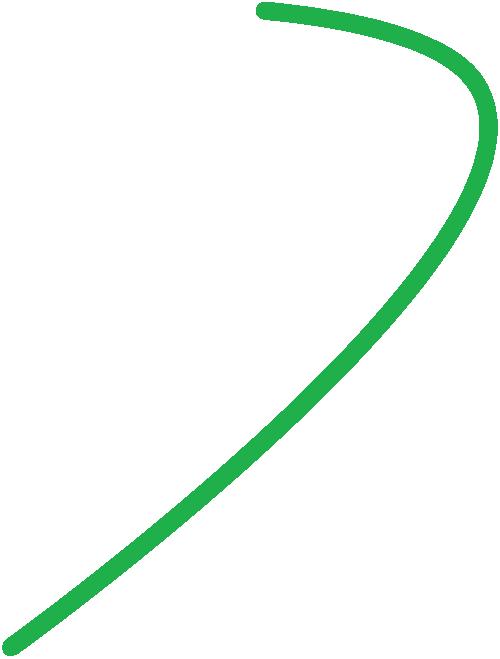

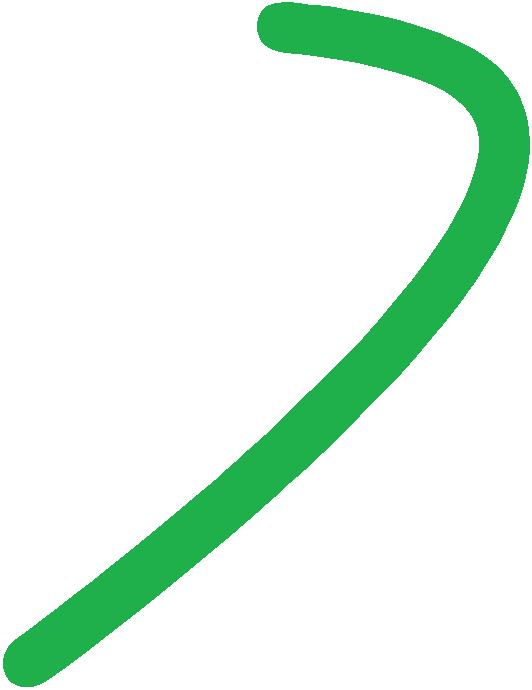
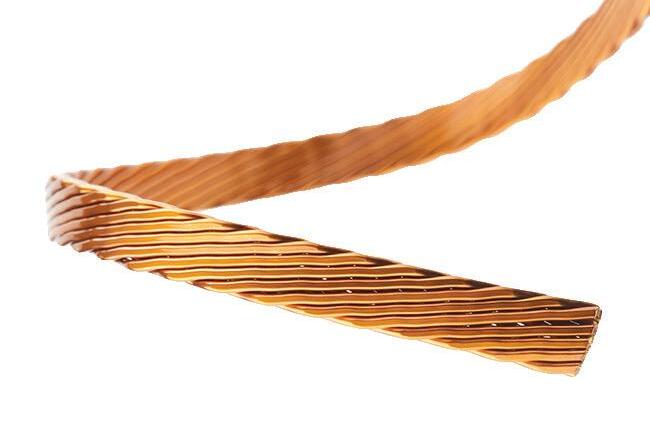
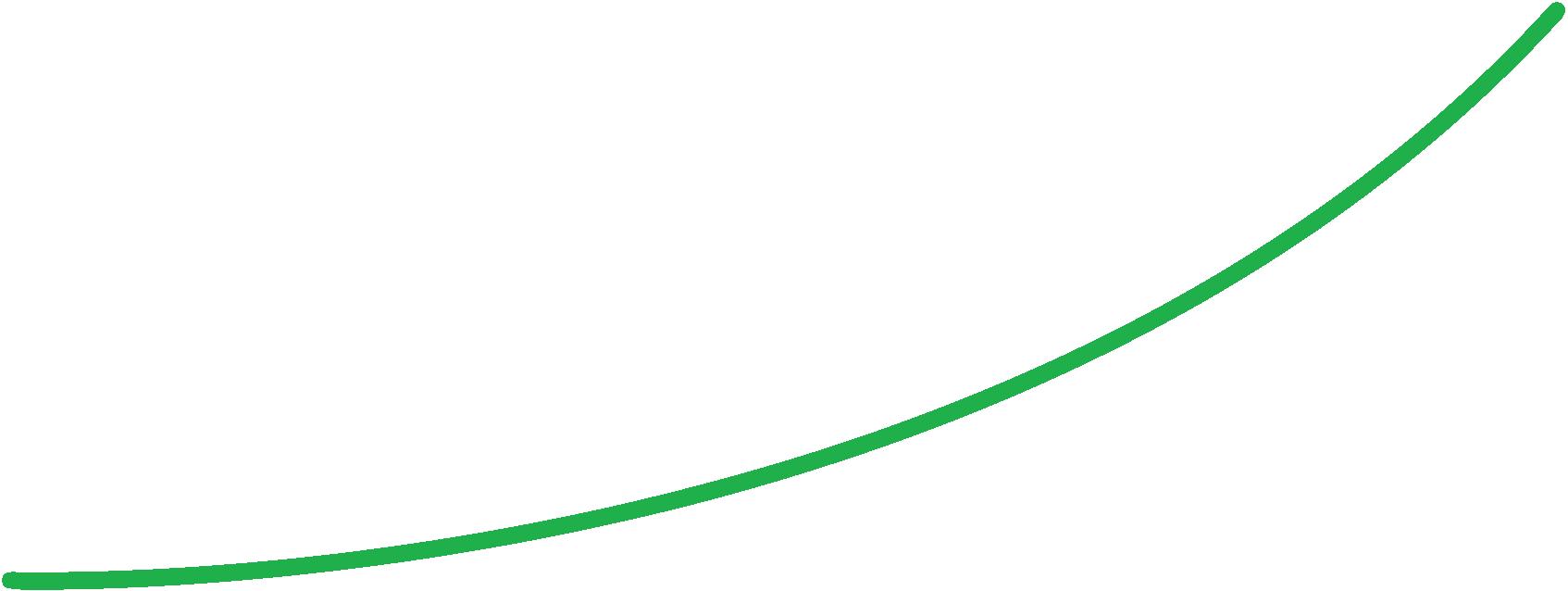





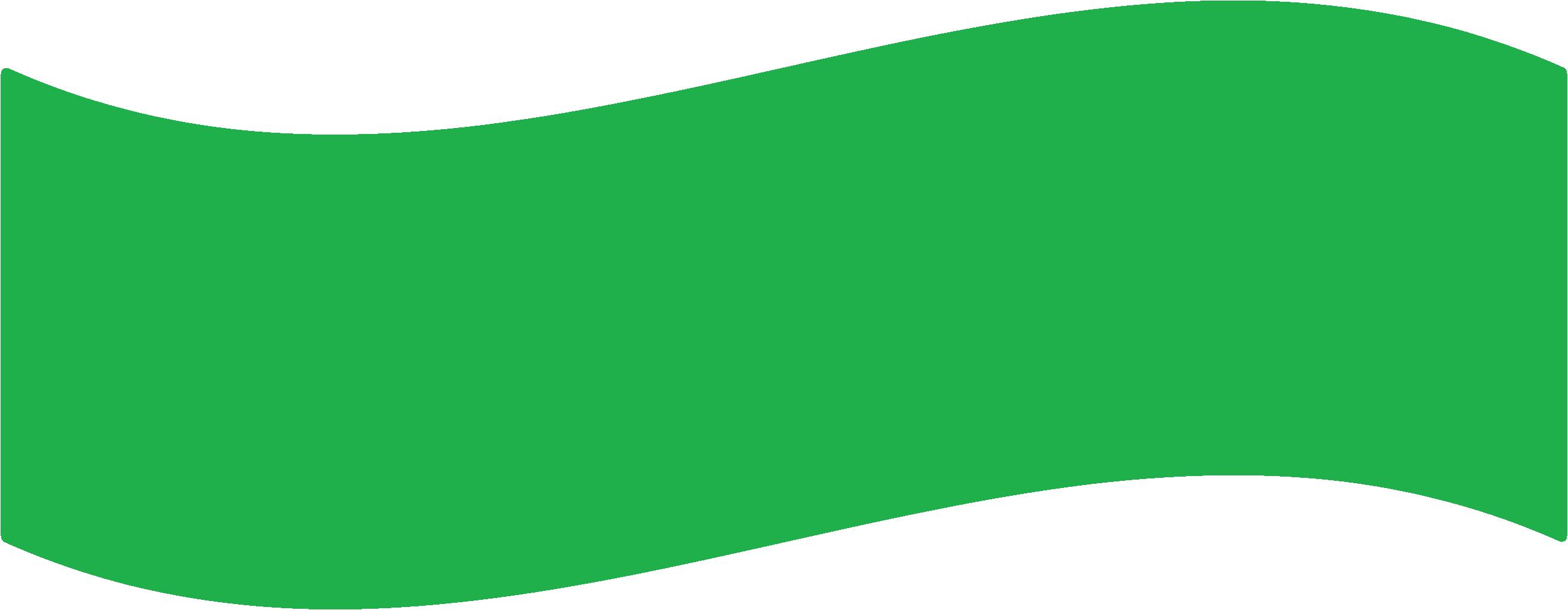
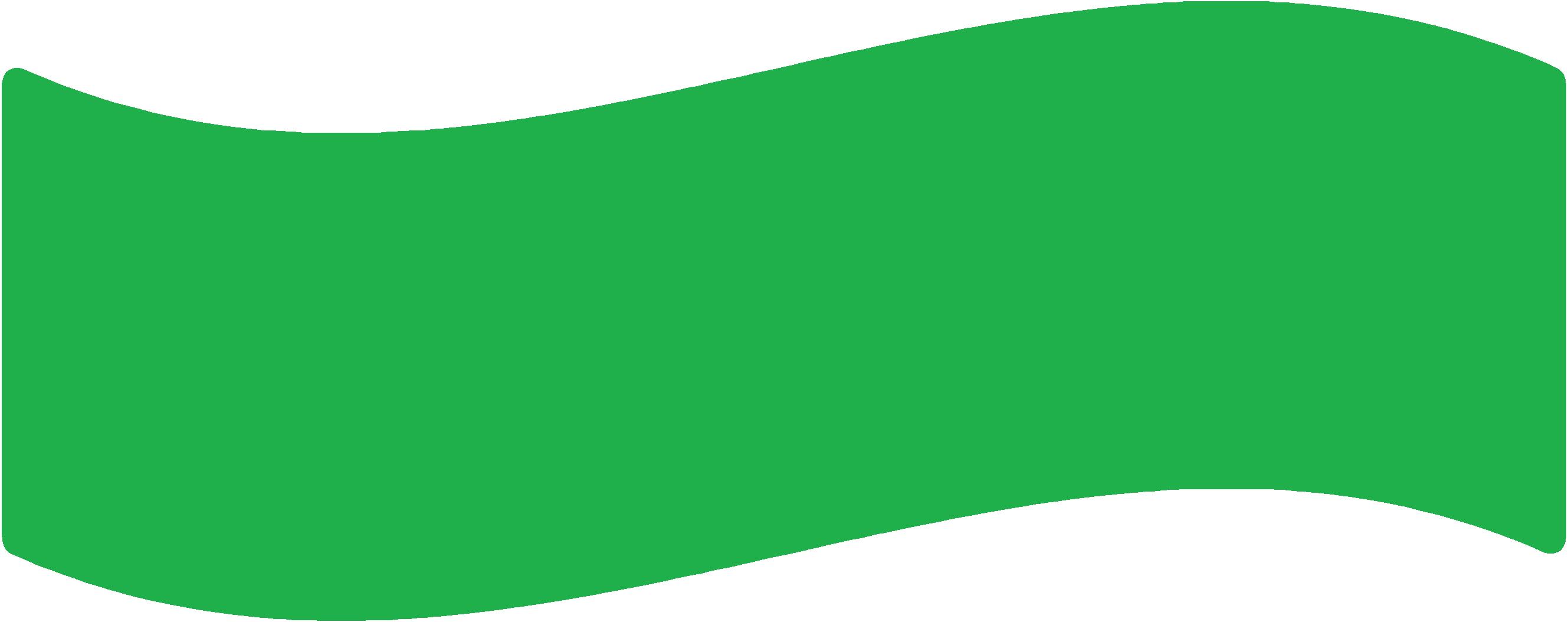
The digital transformation of ABB’s instrumentation warehouse
STEPHANIE NEIL • EXECUTIVE EDITOR
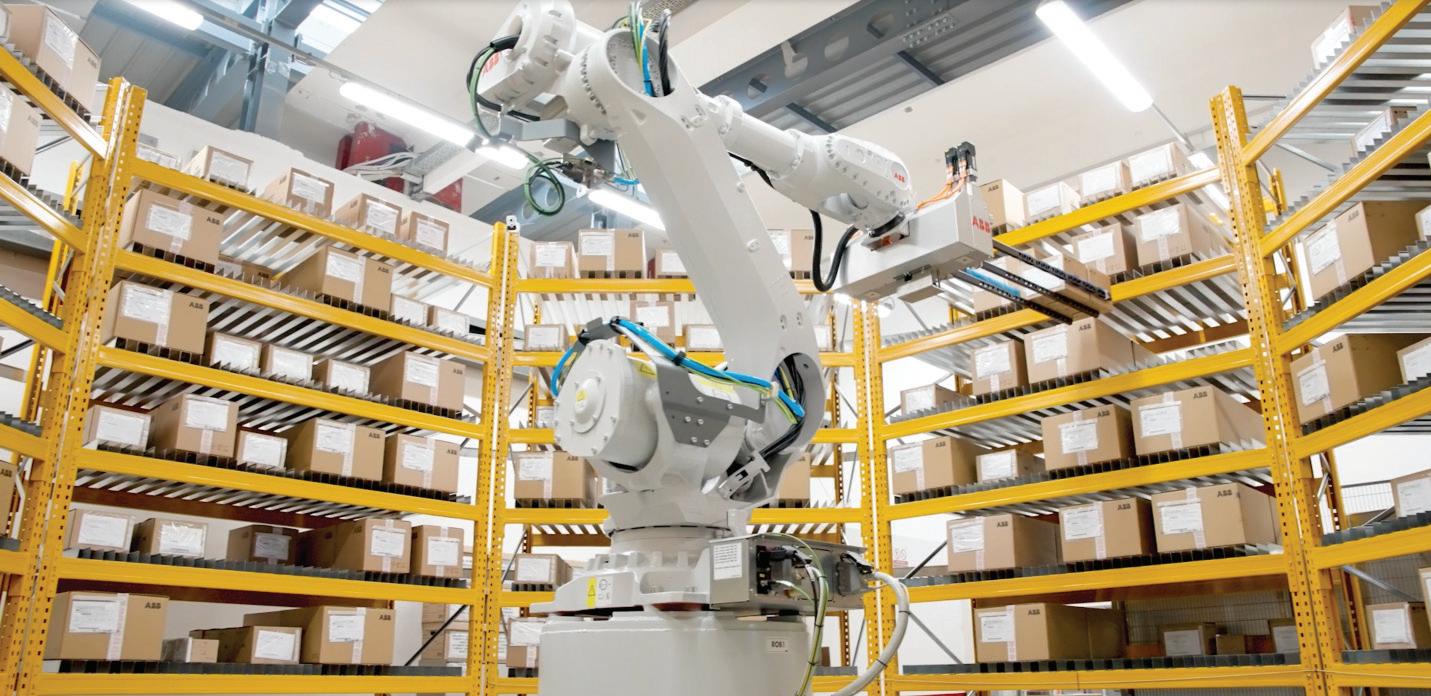
AThe addition of robots, motion control, and digital twin tools leads to a 90% improvement in overall logistics efficiency.
BB’s Measurements & Analytics factory in the Italian village of Ossuccio — situated on the shores of Lake Como — produces pressure transmitters that enable industrial companies around the world to measure, monitor, and control applied force. This technology is key for both safety and efficiency and is a fundamental component in industrial digital transformation.
Today, the Ossuccio factory exports the majority of its components to other ABB factories around the world through its logistics center. It’s a midsize operation that has relied on warehouse workers to prepare products for shipment.
But ABB, like its industrial customers, continues to strive for efficiency through innovation — regardless of the size of the operation. So, the company used its own in-house automation, robotics technology and simulation capabilities to modernize the historic facility, which has been on Lake Como since World War II.
The modernization effort included the addition of ABB’s OmniVance FlexBuffer robot system, an advanced automated storage and retrieval system (ASRS) that manages all of the warehouse loading and offloading activities. According to the company, the robot not only transformed the warehouse into a fully
ABB’s OmniVance FlexBuffer automated storage and retrieval system can handle a variety of box sizes with the same robot gripper.

Autonomously transport materials up to 4,200 lb with the industry’s most comprehensive autonomous mobile robots and fleet management software.
$1.5M
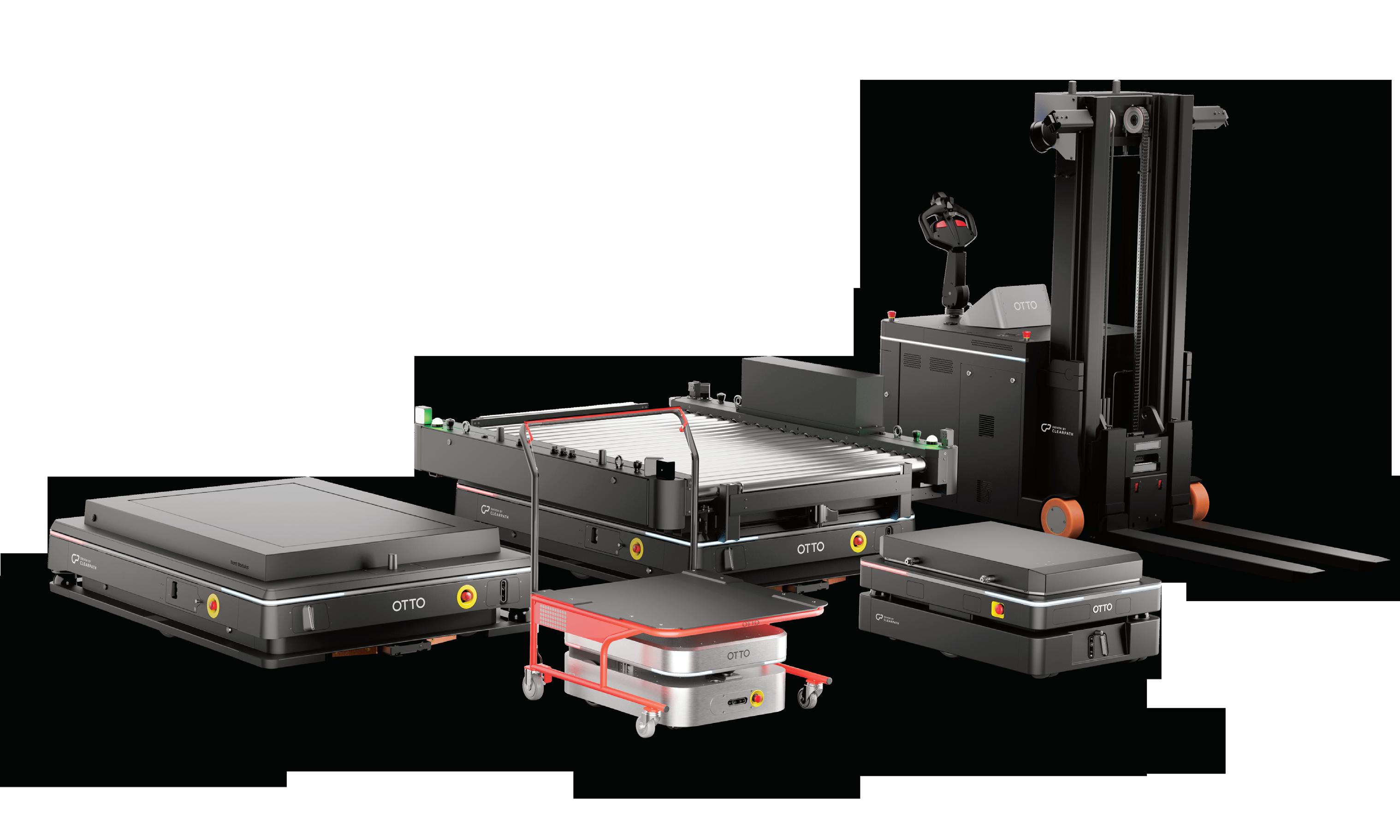
Adoption of the AS/RS has alleviated the physical strain associated with manually handling heavy boxes.

automated operation, but it has also led to 90% improvement in overall logistics efficiency.
“We wanted to improve logistics at the Ossuccio site while also enhancing the entire manufacturing process,” said Mariafrancesca Madrigrano, general manager of the ABB Measurement & Analytics factory. “Upgrading the existing warehouse was an important project that we did together with our colleagues in robotics in order to align with the current state-of-the-art automation.”
ABB configures its own robots
The solution consists of two FlexBuffer systems connected by a conveyor, each one equipped with ABB robots. The control architecture includes ABB Group’s B&R Industrial Automation PLCs and HMIs to drive the conveyor system and robot control from ABB’s OmniCore control platform.
“These are palletizing/depalletizing robots handling a combination of either boxes or totes within a combined
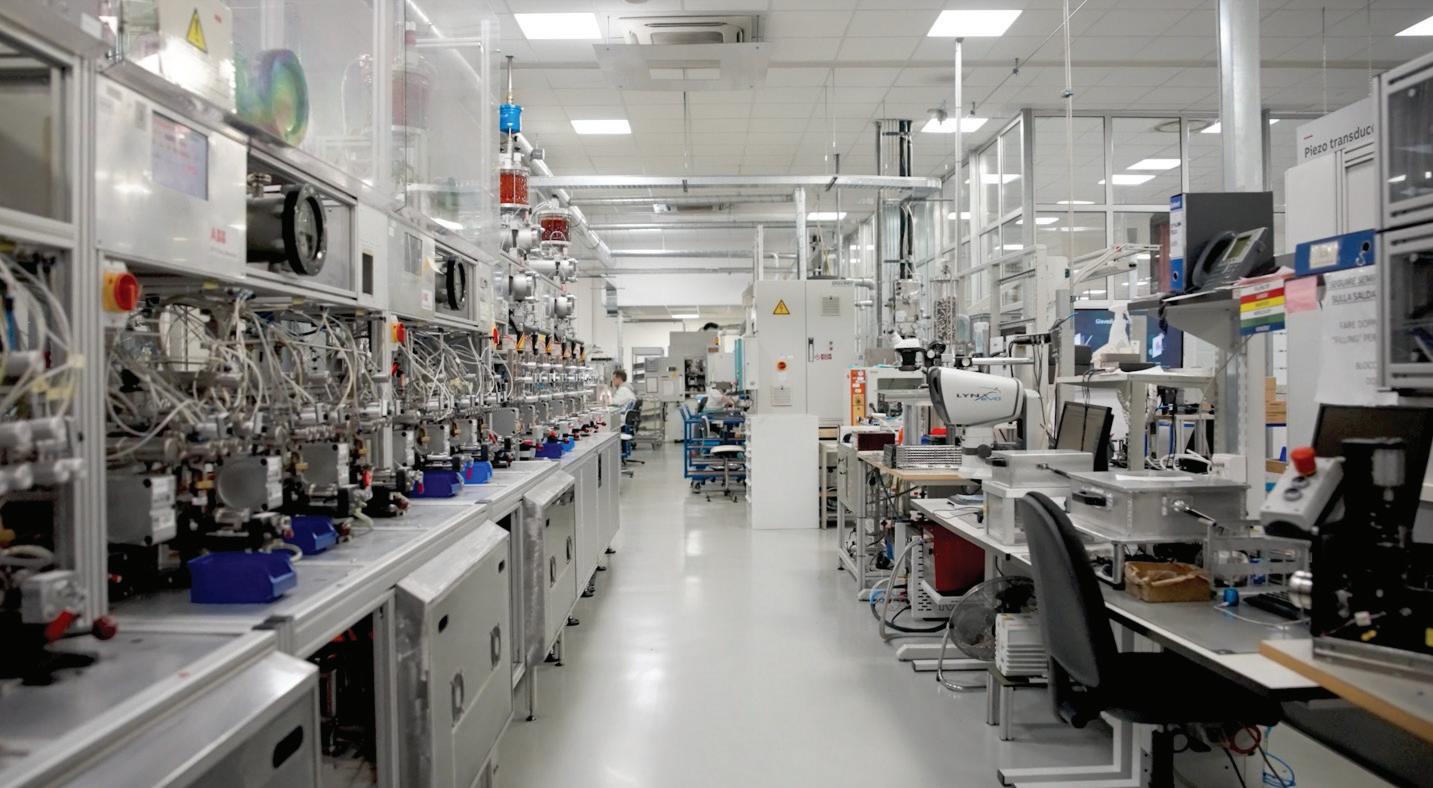
application,” said Craig McDonnell, business-line managing director of ABB Robotics. “In this application, the FlexBuffer system is managing the inbound or outbound location of the totes, balancing of the tote or boxes between two separate buffering systems, and the complete software architecture to manage that.”
To that end, FlexBuffer allows for easy transitions between buffering,
storing, and sequencing tasks. It combines temporary storage and sequencing functions to provide additional functionality over traditional ASRS.
The mixed-item variant of the FlexBuffer enables the user to store a wide variety of box sizes, all being handled with the same robot gripper. And the dynamic racking positions all boxes with minimal loss of space.
The ABB Ossuccio factory specializes in the production of pressure transmitters.
The application at the ABB warehouse is an example of the scalability of the system, as ABB robotics are typically found in larger e-commerce sites, McDonnell said.
“Over recent years, we've found there's a big need for manufacturing processes to drive greater efficiency,” he explained. “Like in this plant, they were using a lot of robots in the end processes, be it welding or whatever it might be that you need for that specific process.”
“But the intralogistics feeding typically was the last part to be automated in many of these smaller factories. And the trouble was, it just ends up being too custom,” added McDonnell. “So, we've spent quite a bit of time coming up with a standardized modular system that you can use in small to medium-size facilities.”
Digital twins and digital transformation
The system was designed in ABB’s RobotStudio, a simulation tool for robot applications, which created a complete digital twin architecture. This reduces commissioning time as well as enables remote access after the installation.
“In the digital twin, we build a complete duplicate all the way down to the deep robot motion in the actual runtime engines. Then you have much quicker commissioning times and troubleshooting assistance,” McDonnell explained.
While the decision to deploy the ASRS in the warehouse was driven by customer needs, the digital transformation aspect was an extra benefit.
“The reason digital transformation is important is because the goal of ABB
New England Wire Technologies Advancing innovation
for over 100 years
Why accept a standard product for your custom application?
NEWT is committed to being the premier manufacturer of choice for customers requiring specialty wire, cable and extruded tubing to meet existing and emerging worldwide markets. Our custom products and solutions are not only engineered to the exacting specifications of our customers, but designed to perform under the harsh conditions of today’s advanced manufacturing processes. Cables we specialize in are LITZ, multi-conductor cables, hybrid configurations, coaxial, twin axial, miniature and micro-miniature coaxial cables, ultra flexible, high flex life, low/high temperature cables, braids, and a variety of proprietary cable designs. Contact us today and let us help you dream beyond today’s technology and achieve the impossible.
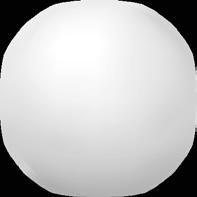
is to serve the customer better,” said Madrigrano. “The big advantages have been that we’ve reduced the possibility of human error, and we’ve reduced throughput time.”
And the entire workforce benefits. Adoption of the system has enhanced working conditions for operators, alleviating the physical strain associated with manually handling heavy boxes.
In addition, many people were reallocated to other manufacturing areas that required additional manpower, giving the factory a greater flexibility during peak production times. AW

Scan the QR code to see ABB’s newly automated Ossuccio site
www.youtube.com/watch?v=gxc8-o8-WAA
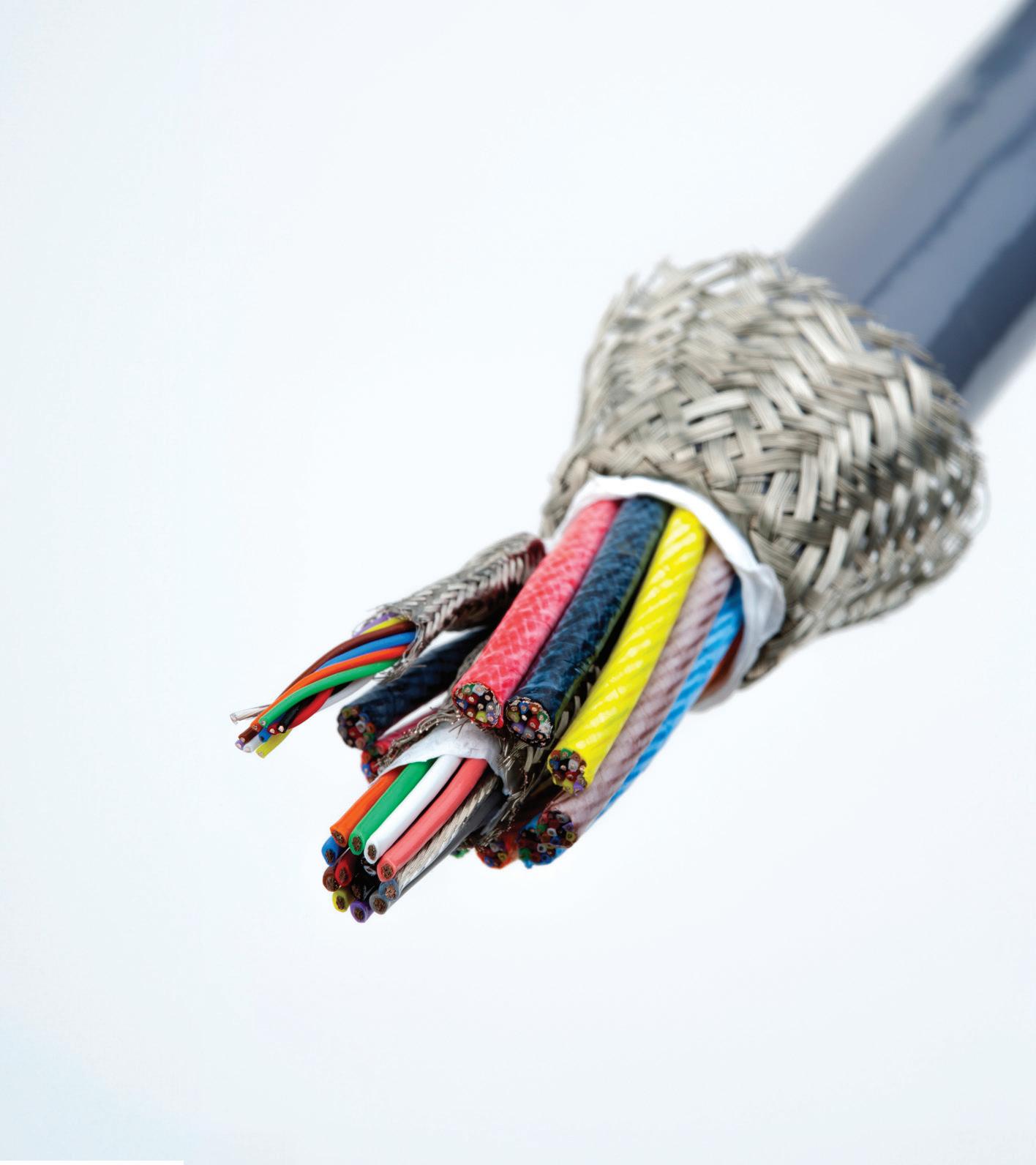
The Data Driven Warehouse
How real-time data collected at every touch point smooths out operations
Emerging technologies are revolutionizing supply planning, enhancing supply chain efficiency, agility, and resiliency. Real-time data and advanced analytics driven by connected assets and systems help identify potential disruptions, mitigate risks and make informed decisions. We will discuss key insights into today's supply chain challenges.
What are today’s supply chain challenges?
The constantly evolving global supply chain landscape poses a range of challenges for businesses today that can impact their operational efficiency and effectiveness. Here are the biggest challenges:
• Business disruptions and market volatility: Over the past five years, supply chain operations in various industries faced unexpected events, which resulted in reactive responses. This can impede the ability to meet demand, leading to lost revenue, increased costs, and a decline in overall profit margins.
• Demand predictability: Social media, COVID driven direct-to-consumer (DTC) models, market volatility, and now inflation have made traditional demand forecasting insufficient. Operations are leaning on outdated forecast approaches that also lag and fail to respond adequately to current market dynamics.
• Holistic inventory visibility and optimization: Inventory management is complex and dynamic. The end of 2022-2023 saw excess inventory across many organizations due to COVIDrelated supply chain constraints. This led to higher costs, lower margins, and waste. The long term impact will lead to lost sales, and loss of differentiation, loyalty, and market positioning. Adopting an integrated approach and leveraging advanced technology and best practices, businesses can overcome these challenges - improving supply chain efficiency and resilience.
What is lacking in today’s supply chain strategies?
Supply planning today involves technology, data analysis and stakeholder collaboration. While technical and data analytic advancements have been made, there are still several areas that need improvements in the industry:
• Accurate transparency of data
• Dynamic supply planning and execution based on integrated intelligence and automated decision-making
• Convergence of network modeling, scenario and traditional planning and planning
Businesses want to improve supply chain visibility, predict, and mitigate risks, and optimize performance. Incorporating advanced concepts can enhance agility and resilience, meet customers’ evolving needs, and optimize performance. Below are a few advanced technologies and characteristics that must be included in an organization’s growth plans for supply chain optimization.
• Artificial intelligence and machine learning: Artificial Intelligence (AI) and Machine Learning (ML) can help businesses analyze data, find patterns, and make proactive decisions to mitigate risk. Many planning solutions have already integrated AI/ML into their core plans, but further integration of this can enhance algorithms. This could include detecting shifts and anomalies -- optimizing execution, automating operations such as key planning processes and real time decisions, and more.
• Digital twins and advanced simulation: Digital twins and simulation create virtual versions of physical assets, processes, and systems. These outputs can be used to evaluate scenarios and risk, identify key constraints, optimize, and evaluate alternative configurations.
With data and AI/ML, digital twins can continuously evaluate supply chains and networks, informing businesses in an unprecedented way.
• Automation and autonomous systems: The targeted deployment of automated storage retrieval systems (ASRS), autonomous mobile robots (AMR) and other assets with IoT connectivity, RFID asset tracking and machine vision can mitigate risks ranging from labor shortages to inventory loss. Working in tandem with digital twin and AI/ML, these assets comprise self-optimizing systems that drive higher output and efficiency by learning from both physical and simulated scenarios in the connected warehouse.
The future of supply chain planning requires digitization, automation, connectivity, and data-driven decision-making. Organizations that embrace these technologies create agile, transparent and efficient supply chains that are resilient to market changes and disruptions. AW

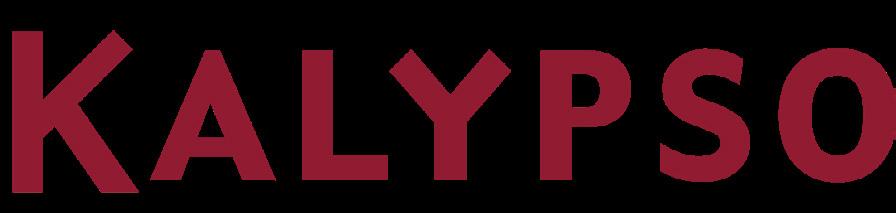
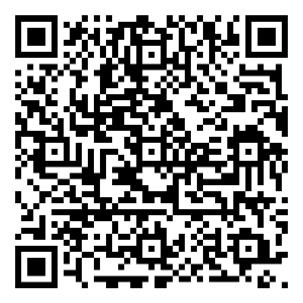
You can read more in our recent whitepaper, Synchronizing Supply & Demand in 2023 and Beyond.