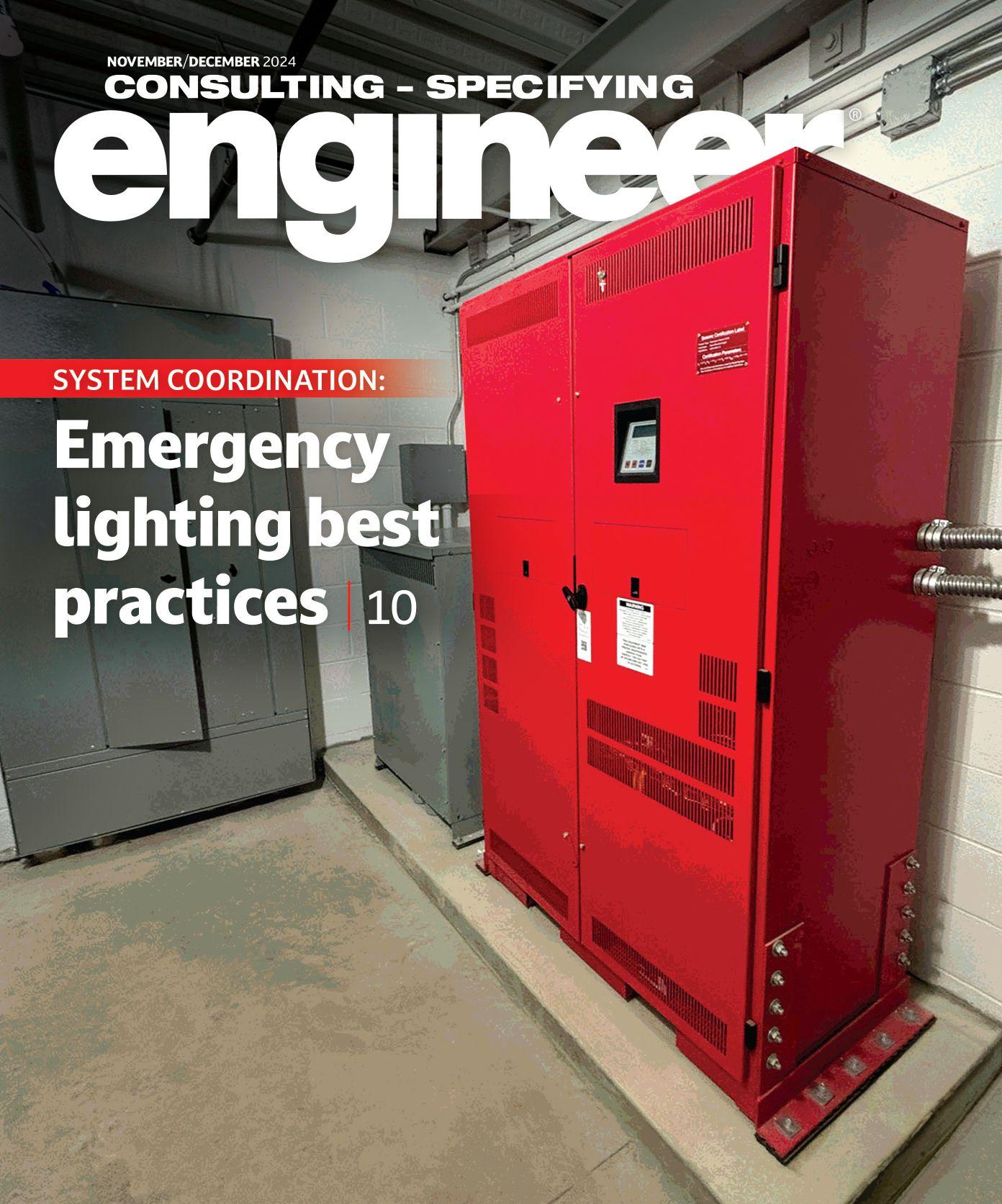
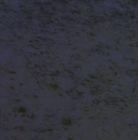
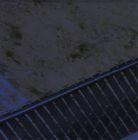
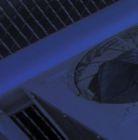
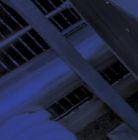
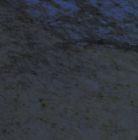
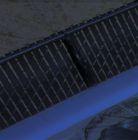
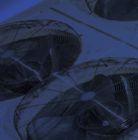
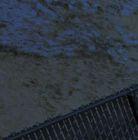
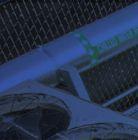

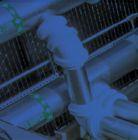
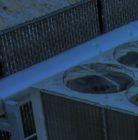
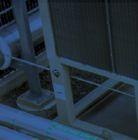
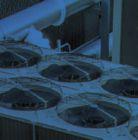
We’re growing our business to help yours.
SyMAX motors offer variable speed efficiency, precise airflow control, and effortless installation. By enabling customers to program multiple motors simultaneously, they set a new standard for excellence in HVAC performance. Contact your LEESON representative to learn more or visit us online at leeson.com today.
In an industry which is fast paced and volatile, you need to be as agile as your customers, we know what data centre and mission critical facility operators demand. Centum™ Force Series, our game-changing series of containerised solutions have you covered with Cummins renowned robust power in the most flexible package possible.
• Stackable design – maximise space and increase power
• Accelerated startup – faster commissioning and cost saving
• Integrated systems – for faster repositioning or redeployment
• Global support – wherever you need power, we’ve got your back
Leading the way in energy efficiency yet again, ABB Baldor-Reliance® SP4TM motors give you a shortcut in energy savings, lower operating costs and total cost of ownership. SP4TM motors achieve NEMA Super Premium® efficiency across-the-line, independently of a drive. Whether DOL or inverter duty, these motors run cooler, longer and quieter – now with a 48-month warranty. new.abb.com/motors-generators/sp4
16 | NEC How to use NFPA 70 for patient spaces in health care facilities
5 | Compensation pressures remain a challenge
The recent salary survey shows increasing compensation with hiring and workload challenges
7 | Three new firms enter the Commissioning Giants list this year
Consulting-Specifying Engineer 2024
Commissioning Giants gives a snapshot of the industry over the past year
10 | Design, coordinate and maintain emergency lighting systems
Know the different types of emergency lighting systems, and best practices for installation and maintenance
Return
When designing health care facilities, electrical engineers need to consult and comply with myriad different standards and regulations
24 | Understand how to size wire and cables in medium-voltage electrical systems
Medium-voltage cables need to be sized appropriately per the 2023 NEC to minimize the risk of fire
30 | Energy savings for HVAC systems in health care facilities
Health care facilities require sophisticated HVAC systems to maintain high levels of indoor air quality, thermal comfort and infection control
37 | How to choose the right HVAC System: Code and efficiency considerations
By completing system analyses and making appropriate decisions, an optimum HVAC system can be recommended for any building type
46 | Hospital design trends focus on patient experience and energy savings
Trends in hospital and health care facility design include a focus on decarbonization, patient experience and telehealth technologies
$120/yr; Canada/Mexico, $150/yr (includes 7% GST, GST#123397457); International air delivery $260/yr. Except for special issues where
CONSULTING-SPECIFYING ENGINEER, 1111 Superior Ave., Suite 2600, Cleveland, OH 44114. Printed in the USA. WTWH
contained herein, regardless of whether such errors result from negligence, accident or any other cause whatsoever. ON THE COVER: A 10 kilovolt-ampere central emergency lighting inverter with integral circuit breakers and maintenance bypass. Courtesy: Kohler Ronan Consulting Engineers LLC
The Cleaver-Brooks ClearFire®-CE (CFC-E) isn’t just another condensing hydronic boiler—it’s the powerhouse your medical campus needs for ef cient and reliable HVAC solutions. With up to 99% ef ciency, it’s designed to drastically reduce energy costs while offering unparalleled design exibility and long-term sustainability.
Boost ef ciency, lower operational costs, and embrace a sustainable future with the ClearFire-CE—the intelligent choice for HVAC systems on medical campuses. For Immediate Shipment In Stock
Why the CFC-E is the perfect solution for your medical campus HVAC systems:
» TurboFer® heat exchanger: Ensures industry-leading ef ciency and performance.
» Environmentally responsible design: <20 ppm NOx and options for sub-7 ppm NOx.
» Future-ready design: Supports dual-fuel capability (natural gas/propane) for backup fuel requirements.
» Advanced integrated controls: 10:1 turndown for precision.
» Scalable capacity: From 500 to 6,000 MBH, ideal for any size medical facility.
» Flexible system integration: Tailored to t diverse HVAC con gurations.
AMARA ROZGUS, Editor-in-Chief ARozgus@WTWHMedia.com
ANNA STEINGRUBER, Associate Editor ASteingruber@WTWHMedia.com
AMANDA PELLICCIONE, Marketing Research Manager APelliccione@WTWHMedia.com
MICHAEL SMITH, Art Director MSmith@WTWHMedia.com
DARREN BRUCE, PE, LEED AP BD+C, Director of Strategic Planning, Mid-Atlantic Region, NV5, Arlington, Va.
MICHAEL CHOW, PE, CEM, CXA, LEED AP BD+C, Principal, Metro CD Engineering LLC, Columbus, Ohio
TOM DIVINE, PE, Senior Electrical Engineer, Johnston, LLC, Houston
CORY DUGGIN, PE, LEED AP BD+C, BEMP, Energy Modeling Wizard, TLC Engineering Solutions, Brentwood, Tenn.
ROBERT J. GARRA JR., PE, CDT, Vice President, Electrical Engineer, CannonDesign, Grand Island, N.Y.
JASON GERKE, PE, LEED AP BD+C, CXA, Senior Design Phase Manager, JP Cullen, Milwaukee
JOSHUA D. GREENE, PE, Associate Principal, Simpson Gumpertz & Heger, Waltham, Mass.
RAYMOND GRILL, PE, FSFPE, LEED AP, Principal, Ray Grill Consulting, PLLC, Clifton, Va.
DANNA JENSEN, PE, LEED AP BD+C, Principal, Certus, Carrollton, Texas
WILLIAM KOFFEL, PE, FSFPE, President, Koffel Associates Inc., Columbia, Md.
WILLIAM KOSIK, PE, CEM, LEGACY LEED AP BD+C, Lead Senior Mechanical Engineer, kW Mission Critical Engineering, Milwaukee
KENNETH KUTSMEDA, PE, LEED AP, Engineering Manager, Jacobs, Philadelphia
DAVID LOWREY, Chief Fire Marshal, Boulder (Colo.) Fire Rescue
JASON MAJERUS, PE, CEM, LEED AP, Principal, DLR Group, Cleveland
JUSTIN MILNE, PE, PMP, Senior Engineer, Southcentral Region, Jensen Hughes, Allen, Texas
GREGORY QUINN, PE, NCEES, LEED AP, Principal, Health Care Market Leader, Affiliated Engineers Inc., Madison, Wis.
BRIAN A. RENER, PE, LEED AP, Principal, Electrical Discipline Leader, SmithGroup, Chicago
CRAIG ROBERTS, CEM, Account Executive, National Technical Services, McKinstry, Powell, Tenn.
SUNONDO ROY, PE, LEED AP, Director, Design Group, Romeoville, Ill.
JONATHAN SAJDAK, PE, Senior Associate/Fire Protection Engineer, Page, Houston
RANDY SCHRECENGOST, PE, CEM, Austin Operations Group Manager/Senior Mechanical Engineer, Stanley Consultants, Austin, Texas
MATT SHORT, PE, Project Manager/Mechanical Engineer, Smith Seckman Reid, Houston
MARIO VECCHIARELLO, PE, CEM, GBE, Senior Vice President, CDM Smith Inc., Boston
RICHARD VEDVIK, PE, Senior Electrical Engineer and Acoustics Engineer, IMEG Corp., Rock Island, Ill.
TOBY WHITE, PE, LEED AP, Associate, Boston Fire & Life Safety Leader, Arup, Boston
APRIL WOODS, PE, LEED AP BD+C, Vice President, WSP USA, Orlando, Fla.
JOHN YOON, PE, LEED AP ID+C, Lead Electrical Engineer, McGuire Engineers Inc., Chicago
The recent salary survey shows increasing compensation with hiring and workload challenges
The latest salary survey from Consulting-Specifying Engineer provides insight into the ever-changing compensation landscape, reflecting both positive trends and critical challenges.
With an average base salary of $118,310 in 2023 — a 3.4% increase from 2022 — engineering professionals are seeing consistent income growth, though it’s worth examining if this growth matches the demands and complexities engineers are tackling. Notably, 84% of respondents saw a rise in total compensation last year, with 77% receiving additional income from bonuses, profit sharing or stock shares.
Amara Rozgus, Editor-in-Chief
This trend highlights the increasing reliance on variable pay tied to profitability and individual performance. But how sustainable is this model with fluctuating project demands and evolving technology?
While base salaries have risen by nearly 20% since 2014, from $99,100 to today’s figure, nonsalary compensation has seen an even steeper climb — up by almost 90%. Is this shift toward performance and profit-based pay a double-edged sword?
Engineering roles are becoming increasingly intertwined with corporate performance, potentially incentivizing high productivity yet also placing added pressure on engineers to continually surpass previous project outcomes.
Beyond compensation, the survey’s findings reveal that the industry is grappling with big challenges, including shifting client expectations, shortened project timelines and cost-cutting pressures. One-quarter of survey participants cited communication issues with stakeholders as a core obstacle, underscoring the need for seamless collaboration across complex projects. At the same time, many report difficulty in recruiting junior staff, highlighting a broader issue: a gap in the talent pipeline that could impact industry sustainability. This raises an important question for firms: How can they attract and retain new talent in an industry increasingly dominated by technology-driven roles and rising expectations?
The path forward demands a delicate balance. To maintain a workforce of experienced, highly skilled professionals, firms must offer competitive salaries while addressing workload management and ensuring that younger engineers can see a clear and enticing career trajectory.
Looking to the future, can engineering firms foster an environment that not only keeps pace with changing demands but also secures a steady influx of emerging talent? Or will the dual pressures of compensation variability and evolving technologies limit the industry’s growth and sustainability? cse
By Anna Steingruber and Jack Morrissey, WTWH Media, Chicago
The Consulting-Specifying Engineer 2024 Commissioning Giants gives a snapshot of the commissioning industry over the past year
The Consulting-Specifying Engineer 2024 Commissioning Giants provides information on the top 25 firms based on self-reporting for this year’s rankings.
Total commissioning revenue for these firms was $913.4 million, an increase from $831.7 million last year. Three new firms entered the list this year: Bernhard, CMTA and Sindoni Consulting & Management Services.
Figure 1 shows a complete ranking for 2024, including the three new firms in the top 25.
On average, commissioning revenue represented 33% of a firm’s total gross revenue. This represents an average of $36.5 million, with the top three firms earning $80 million or more. While the percentage of commissioning revenue varied, 64% of firms reported it to be 20% or less of their total gross revenue for the last fiscal year.
The top building types for commissioning revenue included:
• Data centers (31%).
•
•
(15%).
(11%).
(8%).
• Industrial or manufacturing facilities/warehouses (7%).
• Office buildings (6%).
• K-12 schools (5%).
• Utilities, public works, transportation (5%).
• Research laboratories (5%).
• Engineered multi-dwelling buildings, retail complexes, restaurants (2%).
• Mission critical facilities, not including data centers or hospitals (2%).
Most projects (87%) were based in the United States. This data reflects commissioning at all levels: new buildings (48%), whole building (12%), existing building (8%), retro-commissioning (8%), emergency power systems (7%), monitoring based (6%), envelope (5%), fire protection systems (3%), recommissioning (2%) and communications systems (1%).
Commissioning Giants firms are predominantly consulting engineering firms (52%). New York has the most firms on the list with four, followed by California with three. Roughly two-thirds (76%) of firms acquired another company in the last fiscal year. On average, 50% of these firms’ staff were 40 years old or younger and 12% of the staff were female.
Firms reported that the top reasons for commissioning requests were sustainability, resiliency, savings and mandates. Anticipated future challenges with commissioning include not enough commissioning authorities or agents, lack of funding or buy-in, lack of knowledge about commissioning’s worth and changing codes and standards. Top corporate challenges included quality of younger staff, the economic impact on
the construction market and increasing costs in construction.
Firms reported an average of 37 certified commissioning authorities/agents or
Prominent
ASHRAE Standard 90.1 – 2019
Air Curtains allowed as Vestibule Exception
Henry C. Baker, PE, Kohler Ronan Consulting Engineers LLC, Danbury, Connecticut
Engineers should know the different types of emergency lighting systems, and best practices for their installation and maintenance
During a power outage, whether routine or hazardous, ensuring the safety of building occupants is paramount. Emergency illumination plays a crucial role in providing a safe exit route during power outages or other emergencies, such as fires.
Building codes and NFPA standards set the requirements for emergency illumination. The primary codes and standards for emergency lighting requirements are:
• International Building Code (IBC).
• NFPA 70: National Electrical Code (NEC).
• NFPA 101: Life Safety Code.
NEC Article 700, Emergency Systems, addresses the means for energizing, installing, controlling, testing and maintaining emergency lighting. Chapter 10, Section 1008, of the 2021 edition of IBC indicates the minimum locations where emergency lighting is required. NFPA 101 also indicates requirements for emergency lighting, many of which are duplicated in the building code, as well as detailed testing and maintenance requirements for emergency lighting.
NEC Article 700.16, Emergency Illumination, states that “emergency illumination shall include means of egress lighting, illuminated exit signs and all other luminaires specified as necessary to provide required illumination.”
The IBC generally requires automatic emergency lighting in “rooms and spaces that require two or more exits or access to exits” in aisles, corridors and exit access stairways and ramps. Within buildings, automatic emergency lighting is required in interior exit access stairways and ramps, interior and
exterior exit stairways and ramps, exit passageways, vestibules at the level of discharge used for exit discharge and exterior landings for exit doorways leading to the exit discharge, which terminates at the public way.
The engineer should coordinate with the authority having jurisdiction (AHJ) to determine what is considered the public way to confirm how far emergency lighting needs to extend outside the building. The building code also requires emergency lighting within specific rooms, including electrical rooms, fire pump rooms, generator rooms, public restrooms larger than 300 square feet and fire command centers.
NFPA 101 expands emergency lighting requirements, stating that it is needed at doors equipped with delayed-egress locks, sensor-release of electric locking systems in the means of egress, exit access escalators and specific stair shafts and vestibules of smokeproof enclosures.
Many of the rooms, spaces and egress components referenced in the building code requirements for emergency lighting are formally defined in the building code. The engineer should coordinate with the architect to determine which rooms in the building meet these definitions.
It is also recommended that the engineer request egress plans from the architect to review egress paths against the proposed emergency lighting and exit sign layouts. Furthermore, the engineer must coordinate with lighting designers and architects to appropriately select which fixtures should be used for emergency lighting for the desired aesthetic and light distribution.
If the project can accommodate it, it is recommended to be conservative with emergency lighting layouts, providing more than code minimum, not only because it will yield better visibility in an outage, but because interpretations of where emergency lighting and exit signs may be required can vary between AHJs.
It is therefore recommended that the design team include directives in the construction documents and bid forms for the contractor to provide unit pricing for additional emergency lighting, exit signs, UL 924 transfer devices and branch circuiting, in case the AHJ requests additional emergency lighting during construction. At the time of AHJ inspection, however, ceiling installation is likely complete or close to completion and post-in-
spection lighting and branch circuit installation can be more costly to the budget and schedule than if they were included in the base bid construction documents.
The IBC stipulates that emergency power systems are required to provide power to emergency illumination for at least 90 minutes via storage batteries, unit equipment (lighting fixtures with integral batteries and transfer devices), or an on-site generator.
FIGURE 2: Unit equipment “bugeye” style emergency lighting fixture. Courtesy: Kohler Ronan Consulting Engineers LLC
The NEC expands on what may be used as emergency power sources. Per NEC Article 700.12 (C) and (I), storage batteries (such as central lighting inverters) and unit equipment must be able to sustain the total load (power) for at least 90 minutes without the voltage falling below 87.5% of normal battery voltage. Unit equipment, specifically, is also required to maintain at least 60% of the initial emergency lighting output (lumens) for at least 90 minutes. Unit equipment fixture batteries and central lighting inverter batteries typically have 90 minutes of backup as standard offerings.
Increasing power storage capacity for inverters for even longer durations can yield significant increases in the physical size of the battery, the amount of space needed and the cost of the equipment, therefore it is uncommon to size an inverter for more than 90 minutes of battery backup. If an emergency power source is a standby generator, it likely has fuel storage for significantly longer runtime than 90 minutes and can sustain emergency lighting for hours.
The building code defines minimum illumination levels and uniformity during an emergency along the path of egress measured at the floor level. At initial loss of power, an average of 1 footcandle and a minimum of 0.1 footcandle are required. At the end of the 90-minute emergency lighting duration, lighting levels are permitted to be as low as 0.6 footcandle on average and 0.06 footcandles minimum.
In I-2 occupancies, such as hospitals, failure of a single lamp in a luminaire cannot reduce the illumination level to less than 0.2 footcandles in an emergency. To provide a relatively uniform illu-
• Become familiar with basic code requirements pertaining to emergency illumination, such as where emergency illumination is required and what lighting levels are required.
• Learn about different power sources and controls for emergency lighting, including unit equipment, central inverters and generators, as well as their respective advantages, installation requirements and maintenance considerations.
• Know some best practices for designing and installing emergency lighting systems, including coordination with architects and authorities having jurisdiction.
mination at the floor, the code specifies a maximum-to-minimum illumination uniformity ratio of 40:1, meaning the brightest spot measured at the floor cannot be more than 40 times brighter than the dimmest spot on the floor during emergency lighting operation.
Lighting calculation software, such as AGi32, can be used to simulate emergency lighting levels and verify the illumination parameters defined in the code are met. It is important for the designer running the simulation to check the .ies files used in the simulation against the emergency lighting source. If a central lighting inverter or standby generator is used to power emergency lighting, the normal lighting fixtures’ .ies files may be used.
If unit equipment batteries are used, the designer should check with the manufacturer if they have .ies files for the fixture with illumination data reflecting battery operation. If a conservative emergency layout cannot be achieved, it is recommended that a lighting designer or similar lighting specialist, such as a manufacturer’s representative, perform calculations with a realistic model of the space, including colors, geometries and reflectances proposed for use in the area of study (see Figure 1).
Emergency lighting must be illuminated within 10 seconds of loss of normal power per NEC Article 700.12, General Requirements. Power supply and transfer components in emergency lighting systems must be listed to UL 924.
Depending on the size of the project and occupancy classification, load profile of the building and the size and technical expertise of building staff, certain emergency lighting power sources are better suited than others for the application and project budget. In addition to the first cost, testing and maintenance costs are a significant factor when choosing the emergency lighting power source.
Emergency lighting fixtures, regardless of power source, are typically required to be operationally tested monthly for 30 seconds and annually for 90 minutes, per NFPA 101 7.9.3, Periodic Testing of Emergency Lighting Equipment.
Use of unit equipment is often favorable for smaller buildings with limited need for emergency lighting and limited technical staff. Unit equipment
are the simplest emergency lighting sources, with an integral light source, battery, charger, transfer device and testing function, which can be manual or automatic. Many emergency battery fixtures now have self-test features, which alleviate the owner’s need to have maintenance personnel climbing up and down ladders and pushing test buttons, monthly.
However, self-test features on unit equipment do not alleviate the need to walk the site, as personnel still must visually observe status indicator lights and document results unless results can be monitored and recorded by a computer-based system (see Figure 2).
An alternative to unit equipment for smaller projects that has a similar cost scale and maintenance impact is a microinverter or mini-inverter. These small inverters are typically sized ranging from less than 100 volt-amperes (VA) to a few thousand VA, depending on the manufacturer and are designed to energize small quantities of emergency lighting fixtures. Due to their size, they can often be wall-mounted. Smaller models even offer options to mount above ceilings or be laid into ceiling tiles.
While these inverters are more efficient in terms of the number of batteries required to energize emergency lighting compared to unit equipment, they often require the addition of UL 924 transfer devices to mimic control of normal lighting fixtures on the same zone of control and to monitor the normal lighting branch circuit serving the area (see Figure 3).
As projects become larger, it becomes less economical to use unit equipment or small inverters and project conditions tend to favor use of central emergency lighting inverters or generators for emergency lighting power. Deciding to use central lighting inverters or standby generators may ultimately come down to whether there are nonemergency loads that need to be, or are preferred to be, on a backup power source (i.e., legally required standby or optional standby loads).
If there are standby loads requiring backup power, a generator is typically specified to meet the larger power capacity and longer backup duration required, compared to emergency loads. If serving emergency loads from the generator, a dedicated emergency distribution (automatic transfer switch and downstream panelboards) is installed to serve
The Whittingham Discovery Center in Stamford, Connecticut, project was a new, ground-up construction, consisting of approximately 10,000 square feet of exhibit space, educational space, a cafe, an occupiable roof terrace and support spaces, such as offices and back of house areas, across two floors and a basement. The building was in a park, surrounded by existing walking paths and pedestrian spaces. A generator was not provided for this building.
While the building’s size did not prohibit using unit equipment or small, local inverters, the building’s geometry and the limited building technical staff would have made using such power sources challenging for maintenance. The center of the building was a double-high exhibit space through which most of the building’s occupants would egress. Not only was the ceiling height in this space tall, the ceiling was also sloped and had triangular ceiling tiles, with a carefully coordinated reflected ceiling plan.
To preserve the aesthetic of the space, standalone unit equipment, such as bugeye style emergency lighting fixtures, were not an option. Lighting in this space was generally recessed in the ceiling or cove-mounted and was well above a height that was easily accessible with a ladder. Had lighting fixtures been provided with integral battery packs, regular testing and maintenance would have been difficult. Lighting in many spaces was also decorative and was not available with standard battery backup options.
Furthermore, the limited number of maintenance staff warranted a simplification of emergency lighting testing. For these reasons, a central lighting inverter was ultimately specified to provide power to the emergency lighting throughout the building.
The lighting inverter was sized at 3 kilovolt-amperes (kVA) and was selected as a single-phase unit with a single 120-volt (V) input and 12 output circuit breakers at 120 V, 20 A. The inverter was in the center of the building in the basement, with the furthest emergency lighting fixture approximately 125 feet from the inverter.
emergency lighting and other emergency loads throughout the building, separate from transfer switches and distribution for standby loads.
If there are no nonemergency loads requiring backup, it may be advantageous to use a central emergency lighting inverter (or multiple, depending on building size) as first costs, maintenance costs and space needs are higher for generator systems than central emergency lighting inverter systems.
Emergency lighting was provided where required by code at the egress path, mechanical rooms, electrical room, elevator and public bathrooms. To provide an additional level of safety in an outage, emergency lighting was also provided in each dry lab classroom, the cafe kitchen and single-occupant bathrooms. Emergency lighting was also provided throughout the building exterior and landscape to ensure safe passage from the building to the surrounding park walkways during an outage or fire.
The lighting controls in the building were done via a combination of wireless standalone controls and a centralized networked system. For the areas with standalone control, such as offices, the kitchen and back-of-house spaces outside of the means of egress, UL 924 emergency lighting bypass relays were used to allow the emergency lighting to be controlled in tandem with the normal lighting and to monitor normal lighting power.
In the spaces where the centralized system was used, such as the exhibit space, dry labs and landscape, the lighting control system monitored normal power via a three-phase voltage sensing input connected to the panelboard serving the spaces and was UL 924 listed. The lighting control system was programmed such that, during normal operation, the emergency lighting zones were controlled to match the normal lighting, but upon sensing loss of power at the panelboard, emergency lighting was put to full brightness.
There was also a fire alarm contact provided to the central lighting control system to bring emergency lighting to full brightness upon an alarm. Because the central processor for the lighting control system was integral to the emergency lighting operation, the processor had to be circuited to the inverter as well. Bypass relays were not used for emergency lighting zones fed from the centralized lighting control system; rather they were fed via dedicated emergency lighting room controllers located in the basement main electrical room adjacent to the inverter.
The design team successfully coordinated and specified a functional and practical emergency lighting system for the building, satisfying the project budget, architectural aesthetics and owner’s operational needs.
A central lighting inverter is a battery cabinet that is listed as a power source for emergency loads. The physical size and cost of the inverter is largely dependent on the kilowatt rating of the unit, if it is three-phase or single-phase, if it is equipped with circuit breakers and if it has a maintenance bypass section.
Central lighting inverters can also be specified with communications inputs and outputs and can be monitored by building management s
ystems or other external software. Larger inverters are often floor-mounted in an electrical room and are recommended to be installed on a concrete housekeeping pad for resiliency. Central lighting inverters provide a single point of maintenance from a battery backup standpoint, with one point of testing and one set of batteries to maintain and replace, versus unit equipment at individual lighting fixtures or remote-mounted microinverters. Testing at a central lighting inverter in an electrical room is less disturbing to active spaces than testing at individual unit equipment battery packs (see Figure 4). For example, a maintenance person having to climb up and down a ladder in a busy corridor to test emergency lighting could be avoided by using a central lighting inverter. Like unit equipment batteries, batteries in central lighting inverters typically require replacement after approximately 10 years (more or less, depending on usage and environmental conditions around the batteries).
From a wiring and controls standpoint, using unit equipment battery packs is the simplest and least expensive emergency lighting source. Per NEC Article 700.12 (I) lighting fixtures with integral battery packs shall be energized from the
normal branch circuit that serves the area, with an additional connection made to an unswitched portion of that normal branch circuit to monitor normal power status. If normal power is lost, the unit equipment will sense the interruption via the unswitched branch leg and will illuminate its lamps via the battery pack. Another code-compliant option is to feed the unit equipment from a lockable-on branch circuit on the same panelboard as the surrounding normal lighting.
If a central lighting inverter or generator are used as the emergency lighting power source, additional components are introduced at the branch circuit level compared to unit equipment. UL 924 emergency lighting bypass relays and UL 1008 branch circuit emergency lighting transfer switches (ELTS) are used to monitor normal power and transfer to emergency power at the branch circuit level. One of these components is provided per lighting control zone with emergency lighting. For example, a room with two lighting control zones with emergency lighting will have two emergency lighting transfer devices or bypass relays.
UL 924 emergency lighting bypass relays are wired with a normal branch circuit input, an emergency branch circuit input, a normal branch circuit output and an emergency branch circuit output, as well as connections for monitoring normal and emergency power and for controlling the emergency lighting to match the normal lighting on that control zone.
During normal operation, the relay monitors the control (on/off/dimming) of the lighting on the normal branch circuit fed from that relay and controls the emergency fixtures fed via that relay in the same way. When power is lost to the normal branch circuit, the bypass relay detects this and forces the emergency lighting on that control zone to full brightness.
The UL 1008 ELTS is similar to the bypass relay in that it has one normal power branch circuit input and one emergency power branch circuit input, as well as inputs for normal power monitoring and controls, but, unlike the emergency lighting bypass relay, the ELTS only has one branch circuit output. The normal branch circuit acts as the source to the load until the ELTS senses loss of normal power, at which time it switches to the emergency source to maintain power to the lighting served.
Certain bypass relays and ELTSs can be specified with fire alarm dry contact inputs, which can be configured to bring emergency lighting to full brightness upon receiving a signal from the fire alarm system. Bypass relays and ELTSs can be wall mounted, ceiling mounted or mounted above ceilings, if accessible. Many are offered with plenum ratings for installation in plenum ceilings.
Both the bypass relay and the ELTS are required to be accessible for testing and include pilot lights indicating the availability and status of each source. For this reason, it is recommended that the devices be installed on or below ceilings and not above ceilings. Bypass relay and emergency lighting transfer switch models typically have options to support 0 to-10 volt (V) dimming, which is commonly used across commercial lighting systems (see Figure 5).
For more specialized applications, such as theatrical lighting, emergency lighting transfer devices are available for DALI and DMX protocols, which are digitally based and therefore have different wiring topologies than standard non-dimming or 0 to 10 V dimming applications.
In conclusion, emergency lighting is a critical component of building safety, mandated by building codes and adopted standards. Whether choosing unit equipment, central inverters or standby generators as the power source, the goal is to provide reliable illumination during emergencies in a manner that fits the project’s budget and owner’s maintenance capabilities.
Collaboration with architects, adherence to regulatory requirements and proactive maintenance are key to ensuring the safety of building occupants. By following best practices and exceeding minimum standards, designers can create robust emergency lighting systems that will be there to guide occupants to safety when needed most. cse
Henry C. Baker, PE, is an associate, senior electrical engineer at Kohler Ronan Consulting Engineers LLC specializing in power systems, lighting controls and fire alarm systems design.
Timothy Piehl, PE, Fitzemeyer & Tocci Associates Inc., Woburn, Massachusetts
When designing health care facilities, electrical engineers need to consult and comply with myriad different standards and regulations to ensure a safe and code-compliant design
The primary code book that an electrical engineer will reference on any given design project is NFPA 70: National Electrical Code (NEC). Health care facility design requires review and compliance with many codes, standards and regulations, however, compliance specifically with the NEC is a complex and important part of the design.
Article 517 within the NEC is dedicated to the design of health care facilities and references many of the other relevant codes and regulations, including both NFPA 99: Health Care Facilities Code and NFPA 101: Life Safety Code. Each of these code books have sections within them dedicated to electrical design, but also cover the more general requirements of health care facilities and life safety systems in greater detail.
While it is important to refer to these codes directly, the NEC is a great starting point that incorporates some of the most important electrical requirements within those codes into Article 517. Direct references to these code books can be found throughout Article 517 by the bracketed reference numbers following sections of text. Article 517 contains many subdivisions that indicate the requirements for specific types of health care facilities and equipment.
To determine which portions of Article 517 need to be followed, it is important to first understand the facility type being designed and what patient care services it will provide.
The NEC defines health care facilities as “buildings, portions of buildings or mobile enclosures in which human medical, dental, psychiatric, nurs-
Space in which failure of equipment or a system is likely to cause major injury or death of patients, staff or visitors.
1
Space in which failure of equipment or a system is likely to cause minor injury to patients, staff or visitors.
2
3
4
Space in which failure of equipment or a system is not likely to cause injury to patients, staff or visitors but can cause discomfort.
Space in which failure of equipment or a system is not likely to have a physical impact on patient care.
ing, obstetrical or surgical care is provided.” The type of facility, from hospitals to outpatient medical office buildings to nursing homes, will determine which requirements within the NEC need to be met. Areas such as business offices, corridors, waiting rooms and the like in outpatient facilities as well as immunization, psychiatry/psychotherapy offices and optometry centers do not fall under the umbrella of Article 517.
Code requirements ranging from basic wiring device locations and quantities to essential electrical system functions will be dictated by the type of facility and which patient care spaces are provided. It is essential to coordinate with both the architect and owner to understand what types of patient care will be performed, ensuring the correct set of requirements within the NEC are followed, to prevent the over or under, designing of the facility.
Inpatient facilities — hospitals: When thinking about what types of buildings are classified as health care facilities, hospitals are typically the first to come to mind. The NEC defines hospitals as “buildings or portions thereof used on a 24-hour basis for the medical, psychiatric, obstetrical or surgical care of four or more inpatients.” Hospitals will typically include several inpatient rooms, operating rooms, intensive care units and the like, requiring a more robust electrical system in comparison to other health care facilities.
Outpatient facilities — medical office buildings/ambulatory surgical centers: Outpatient facilities can have a wide range of different requirements depending on what types of services are
Critical or intensive care units
Delivery rooms
Operating rooms
Class 3 imaging room
Inpatient bedrooms
Dialysis rooms
IVF rooms
Procedure rooms
Class 2 imaging room
Exam or treatment rooms
Medical and dental offices
Nursing homes
Class 1 imaging room
Anesthesia work rooms
Labs
Morgues
Waiting rooms
Utility rooms
Hospital
Hospital
Medical office buildings
Hospital
Medical office buildings
Nursing homes
Hospital
Medical office buildings
Nursing homes
being provided. Facilities such as clinics and dental offices have different requirements from hospitals due to the lower risk associated with power failures. The NEC defines medical offices as “buildings or part thereof in which examinations and minor treatments/procedures are performed under the continuous supervision of a medical professional.” The expectation within these facilities is that any sedation would be minimal and patients are not required to stay overnight.
Ambulatory surgical centers fall in the area between hospitals and medical clinics. These facilities are typically equipped with operating rooms or procedure rooms that require anesthetizing patients, but on an outpatient basis. These facilities are not equipped with inpatient rooms typical to hospitals.
Nursing homes: Nursing homes, which provide long-term care for residents, have specific electrical requirements to ensure the safety and comfort of their occupants. Nursing homes can range from independent living facilities to assisted living facilities, each requiring a unique set of requirements. Independent living facilities tend to have similar electrical requirements to medical office buildings but facilities that require more assistance become more involved if certain patient care spaces, such as dialysis rooms or memory care areas, are included in their design.
• Understand the difference in NFPA 70: National Electrical Code (NEC) requirements for hospital, outpatient and nursing home facilities.
• Define the NEC requirements for various patient care spaces within health care facilities.
• Learn the difference between Type 1 and Type 2 essential electrical systems and where each is required.
FIGURE 2: Branches of a Type 1 essential electrical system (EES), the most stringent EES required in environments where a power failure could result in loss of life or serious injury. Courtesy: Fitzemeyer & Tocci Associates Inc.
Patient care space requirements: Determining the type of facility will provide a foundation for what codes requirements will be involved in the design. The next step is to make sure the design meets the requirements for each individual type of patient care space included within the facility. The NFPA defines a patient care space as “any space of a health care facility wherein patients are intended to be examined or treated.” These spaces can be further broken down into categories, defined by the type of patient care provided within each space (see Table 1).
Determining which patient care spaces will be included in the design requires coordination with both the architect and owner of the facility to ensure the correct electrical system is provided. It is important to note that the distinction of each space type should be provided by the health care facility’s governing body. While the NEC provides examples of each category, it is up to the health care facility to review and designate each space with a category based on the type of patient care anticipated.
This is particularly important to confirm in the design of imaging rooms as these spaces can span from Category 1, such as image-guided open surgical procedures, to Category 3, such as diagnostic imaging like mammography and ultrasounds.
Once the type of health care facility and patient care spaces being designed are confirmed, it is possible to determine the requirements of the essential electrical system (EES) for the facility as well as the more granular requirements of each patient
care space. Part III of Article 517 is dedicated to the requirements of each type of EES and what they can serve within the health care facility. Part II covers wiring and protection requirements, along with specific patient care space requirements, such as receptacle quantities and branch circuits. When starting out a design, it can be helpful to refer to Part III first to ensure the overall electrical system requirements are being met.
Essential power selection: Type 1 versus Type 2: The NEC defines an essential power system as “a system comprised of alternate power sources and all connected distribution systems and ancillary equipment, designed to ensure continuity of electrical power to designated areas and functions of a health care facility during disruption of normal power sources and also to minimize disruption within the internal wiring system.”
These systems are designed to provide a reliable power source to maintain patient care and safety by ensuring vital equipment and systems remain operational during normal utility power outages. The two major portions of an EES are the emergency power supply (EPS) and its associated emergency power supply system (EPSS). As defined by the NEC, the EPS is the source(s) of electric power for the EPSS, while the EPSS consists of all conductors, disconnecting means, overcurrent protection devices, transfer switches and associated controls/ support devices up to and including the load terminals of the transfer equipment. These, along with the panelboards, branch circuits and devices downstream, make up the facility’s EES.
Type 1 essential electrical systems are the most stringent and are required in environments where
a power failure could result in loss of life or serious injury. Articles 517.29 through 517.35 of the NEC are dedicated to the requirements for Type 1 EES. These systems are required in all facilities with Category 1 patient care spaces, typically hospitals and ambulatory surgical centers, but may also be used to serve Category 2, 3 and 4 spaces.
Every Type 1 EES is required to have at least two independent sources of power, a normal source that generally supplies the entire electrical system and one or more alternate sources of power, such as an emergency generator, fuel cell or battery system. The components should be in such a way to minimize any interruptions caused by natural forces and all feeders are required to be physically separated from the normal power feeders to prevent possible simultaneous interruption.
Type 1 EES are separated into three power branches (see Figure 3):
1. Life safety branch: This branch supplies power to systems that are essential for life safety, such as exit signs, egress lighting, alarm and alerting systems such as fire alarm and medical gas alarm, communication systems required for issuing instructions during emergency conditions, generator set accessories, elevator lighting, control and communication systems and electrically powered egress doors. These systems must remain operational to ensure safe evacuation and emergency response. This branch is required to automatically connect to the EPS within 10 seconds upon loss of normal power.
2. Critical branch: This branch powers equipment and systems that are critical to patient care. This includes task lighting, selected receptacles and fixed equipment in critical care areas as well as nurse call and information technology systems. The critical branch ensures that essential medical equipment remains functional during a power outage. In addition to the equipment listed in Article 517.34, the governing body of the facility can determine if any additional equipment is required to be backed up on the critical branch to ensure effective facility operation. While this branch can be flexible based on the facility needs, there are some limitations to motor circuits, allowing only single-phase, fractional horsepower motors to be connected to the system. This branch is required to automatically
its electrical system, including
As part of a renovation project for a Boston-based health center, it was requested that its existing essential power system be upgraded due to the age and condition of the two generators located on the roof of the building. One of the generators served two automatic transfer switches (ATSs), one that fed an emergency panelboard originally designed for egress lighting and one that fed a standby power panelboard designed for receptacle and heating, ventilation and air conditioning (HVAC) loads. The second generator was dedicated to a separate standby power ATS to serve additional HVAC loads.
Over time, the loads served by each of these panels became mixed to the point where it was difficult to determine which panels were supposed to be dedicated to emergency loads.
To ensure the correct essential power system design was provided for the facility, several meetings were held between the owner and design team to determine the types of patient care that would be provided within the building and what flexibility would be needed in the future. Through these conversations and follow-up emails, it was determined that the facility would have no Category 1 spaces but would have Category 2, 3 and 4 spaces. However, there was a desire to keep the facility flexible should any Category 1 spaces be needed in the future.
Based on these criteria from the owner, along with the budget constraints of the project, it was determined that a Type 2 essential power system was the correct solution for the project. Both generators on the roof were to be replaced and upsized based on the new load requirements of the renovation but instead of serving specific ATSs they were to be paralleled and connected to a new essential power switchboard. The decision to parallel the generators allowed engineers to bypass the requirement to add a temporary generator connection (NFPA 70: National Electrical Code (NEC) Article 700.3(F)) as each generator was sized appropriately to carry the life safety loads of the building should one of the generators need to be serviced.
The new essential power switchboard was designed with five sections:
• Two incoming generator breaker sections.
• One life safety branch section.
• One equipment branch section.
• One spare section.
Each section was designed to be vertically isolated from the other sections allowing the spare section to be used to feed a new critical branch if required by the facility if they add any Category 1 spaces in the future. This provided the flexibility desired by the owner while minimizing unnecessary costs for the project.
The existing emergency power ATS was replaced and tied into the new life safety section of the essential power switchboard. The existing standby transfer switches were replaced with one larger equipment branch ATS and a distribution panelboard to back feed each of the standby panelboards throughout the building from the new equipment branch section.
The branch circuit discrepancies were not addressed as part of this project but will be corrected in future renovation projects at the facility to ensure essential power loads are served from the correct branch based on the NEC requirements of Article 517.
connect to the EPS within 10 seconds upon loss of normal power.
Courtesy:
3. Equipment branch: This branch supplies power to systems that are necessary for the overall operation of the facility, such as heating, ventilation and air conditioning systems, elevators and other building systems. While not directly related to patient care, these systems are crucial for maintaining a safe and functional environment. This branch is required to be automatically connected to the EPS at an appropriate time-lag interval following the energizing of both the life safety and critical branches, typically within 60 seconds upon loss of normal power. Depending on the types of equipment served by this branch, manual transfer to the EPS can be an option, as described in Article 517.35(B).
Any equipment that is not served by these three branches can be served by a fourth optional branch of the EES. This branch requires a dedicated transfer switch that should not transfer if doing so would overload the EPS. This branch is also required to be automatically shed upon overloading of the EPS if it had already transferred.
Type 2 essential electrical systems are required in facilities where a critical power branch is not required. These systems are typically found in outpatient clinics, nursing homes and other health care facilities where the risk associated with power failure is lower, as no Category 1 patient care spaces
are present. Articles 517.40 through 517.44 of the NEC describe the requirements for Type 2 essential power systems with the main differences from Type 1 systems:
• Facilities that have Category 2 but no Category 1 spaces are required to have a Type 2 EES backing up their utility power. Though they are not required, Type 1 systems can still be used if preferred by the owner of the facility.
• Simplified branches: Unlike Type 1 systems, Type 2 systems are only required to have two separate branches: life safety and equipment power. The life safety branch of both Type 1 and Type 2 EES needs to comply with the requirements of Article 700 as described and amended in Article 517.26. One requirement worth noting is the temporary source of power for maintenance or repair of the alternate source of power, indicated in Article 700.3(F). To meet this requirement, a permanent connection for a portable generator, sized to serve the life safety branch, must be installed to provide temporary power during periods of maintenance on the permanent EPS.
It is possible to bypass the requirement of a temporary power connection point if a second, permanent alternate energy source is installed that can support the life safety branch. One solution commonly employed at larger health care facilities is to provide paralleled generators in lieu of a single gen-
Flood control protects the vibrant New Orleans community from rising waters. At the world’s largest drainage pumping station along the Gulf Intracoastal Waterway (GIWW), 11 Pentair® pumps help NOLA play on.
csemag.com
NEC insights
u NFPA 70: National Electrical Code (NEC) outlines rigorous standards for electrical installations in health care facilities and hospitals, ensuring the reliability and safety of critical systems like life support and emergency power.
u Compliance with NEC in these environments is crucial, as it directly impacts patient safety and the continuous operation of essential medical equipment.
u In this article, we will explore the various challenges within health care project design and how to navigate the NEC to ensure electrical safety and reliability within your designs.
erator when designing the EPS, with one remaining operational while the other is serviced.
For both EES types, separation of each system branch occurs at the transfer switches, per Articles 517.31 and 517.42. In addition to the standard essential power branches, branches may be provided for a fire pump if included in the design and elevator systems if they are not connected to the equipment branch. If the transfer switches are located ahead of an essential power switchboard, each vertical section within the switchboard is required to be separated by a barrier to maintain isolated branches. If the essential power switchboard is located ahead of the transfer switches, it is not required to have separate, barriered vertical sections for each branch. In instances where the power source is limited to 150 kilovolt amperes (kVA), the separation of the branches can occur after a single automatic transfer switch (ATS), per Articles 517.31(B) and 517.42(B).
Facilities that only have Category 3 and Category 4 spaces are not required to have an EES as part of their design. They are still required to meet emergency egress lighting and fire alarm requirements though, so many owners will opt to install a Type 2 system to accommodate any future needs the facility may have.
Patient care vicinity panelboard requirements: Panelboards that serve patient care vicinities have additional bonding requirements as noted in Article 517.14. The NEC defines a patient care vicinity as “a space, within a location intended for the examination and treatment of patients, extending 1.8 meter (6 feet) beyond the normal location of the bed, chair, table, treadmill or other device that supports the patient during examination and treatment and extending vertically to 2.3 meter (7 feet 6 inches) above the floor.”
Any panelboards serving the same patient care vicinity are required to have their equipment grounding terminal buses connected or connected to the same copper busbar installed in an accessible location by an insulated continuous copper conductor 10 AWG or larger.
Hospital-grade wiring: The term “hospital-grade wiring” is a generalization referring to all wiring that falls under Article 517.13 of the NEC. This article requires all wiring within patient care spaces to be provided with a redundant grounding path. Article 517.13(A) requires the raceway,
cable armor or sheath to act as effective groundfault current path in addition to the green-insulated copper grounding conductor required by Article 517.13(B). The following common wiring methods will typically meet both requirements.
• Cable within electrical metallic tubing (EMT).
• Type AC cable – AC-HCF.
• Type MC cable – MC-HCF.
Standard MC cable and wiring within polyvinyl chloride conduit do not meet the requirements of Article 517.13. The acceptable wiring methods noted above must be used in all patient care spaces within a health care facility. One exception to this rule is the wiring to any light fixtures mounted above 7 feet 6 inches and their associated light switches, should those be located outside the patient care vicinity, as indicated in the “exception” text to Article 517.13.
In that case, it is acceptable to meet the requirements of either 517.13(A) or 517.13(B). Any life safety or critical branch circuits intended to be served by flexible metal sheathed cable must also meet the requirements of Article 517.31(C)(3)(3). If these requirements cannot be met, these circuits should be served by cable within EMT.
Some owners have standards requiring that these wiring methods be used throughout their facilities, even in areas where patient care is not provided. This helps to “future proof” an installation, allowing any existing wiring to be maintained and reused should a nonhealth care space (such as offices, breakrooms, corridors) be reworked into a patient care space.
Hospital-grade receptacles: Hospital-grade receptacles are required to ensure a proper grounding connection when equipment is plugged in within a patient care space. They also require additional pull-force to remove the plugs, helping prevent accidental removal. Unlike hospital-grade wiring, hospital grade receptacles are only required in specific patient care spaces; Category 1 and Category 2. This is noted in Articles 517.18 and 517.19 of the NEC. While these receptacles are not required in every type of patient care space, many health care facilities will require they be installed in all areas of their buildings to help ensure their spaces are code compliant, should the space type change in the future.
Receptacle quantity/branch circuit power requirements: Some patient care spaces have receptacle quantity requirements described in Article 517 of the NEC. The NEC defines a single receptacle as “a single contact device with no other contact device on the same yoke or strap.” The receptacle requirements within Article 517 can be achieved using any combination of single or multireceptacle devices, such as duplex receptacles. Both Category 2 and Category 1 spaces have receptacle quantity and branch circuit requirements indicated in Article 517.18 and 517.19, respectively. Operating rooms are also provided with their own set of requirements as well as wet procedure locations:
• Category 2 Spaces: Per Article 517.18, Category 2 patient care bed locations are required to have a minimum of eight receptacles and two branch circuits; one normal branch and one critical branch. If there are two critical branches served by separate automatic transfer switches, it is permitted to use one branch circuit from each in lieu of a normal branch circuit.
• Category 1 Spaces: Per Article 517.19, Category 1 patient care bed locations are required to have a minimum of 14 receptacles and two branch circuits; one normal branch and one critical branch. If there are two critical branches served by separate automatic transfer switches, it is permitted to use one branch circuit from each in lieu of a normal branch circuit. In addition, one of the critical branches must be dedicated to receptacles at the patient bed location.
• Operating rooms: Per Article 517.19(C), operating rooms are required to have a minimum of 36 receptacles and two (branch circuits; one normal branch and one critical branch. If there are two critical branches served by separate ATS, it is permitted to use one branch circuit from each in lieu of a normal branch circuit. At least 12 but no more than 24 receptacles shall be connected to each of the branch circuits within the room.
• Wet procedure locations: Branch circuits serving wet procedure locations must be provided with ground fault protection to interrupt the power supply or be fed by an isolated power system to mitigate the possible ground fault current to a low value without interrupting the power. Operating rooms will typically fall under this category, but coordination should be done with
the facilities governing body to determine if any other patient care space is required to meet these criteria. Selection of either ground fault protected receptacles or isolated power should also be coordinated with the owner, as the loss of power associated with the ground fault protected receptacles can pose a hazard for some critical procedures.
In addition to the NEC, FGI Guidelines should be referenced to determine recommended receptacle quantities in the spaces not covered by the NEC. While the FGI Guidelines may not be formally adopted in all states, they are seen as an industry standard for proper health care planning, design and construction and provide recommendations for spaces not formally covered by the NEC.
The implementation of NFPA 70 in health care facilities varies based on the type of facility and the associated patient care services provided. While there are other health care specific codes that must be followed, the NEC provides a framework for many of the patient care spaces that are typical to all health care projects. Understanding the different requirements for each type of facility and patient care space is essential for ensuring the safety and reliability of the electrical systems throughout every health care facility. cse
Timothy Piehl, PE, is Electrical Engineering Manager at Fitzemeyer & Tocci Associates Inc.
4: Hospital-grade receptacles in patient room headwall, which are required to ensure a proper grounding connection when equipment is plugged in within a patient care space. Courtesy: Fitzemeyer & Tocci Associates Inc.
Lilly Vang, PE, and Joshua Hunter, PE, CDM Smith, Maitland, Florida
Medium-voltage cables need to be sized appropriately per the 2023 NEC to minimize the risk of fire
Medium-voltage (MV) electrical systems, which are considered to be around 1 kilovolt (kV) to 35 kV, are not typically seen at the consumer level. ANSI and IEEE standards define voltage classifications as follows:
• Low-voltage (LV): up to 600 volts (V).
• MV: between 600 V and 69 kV.
• High-voltage: between 69 and 230 kV.
• Understand the makeup of Type MV cables.
• Know the NFPA 70: National Electrical Code (NEC) requirements for medium-voltage conductor sizing.
• Learn basics of sizing medium-voltage conductors for an industrial application.
MV systems are not typically seen at the consumer level. It is often used for larger buildings with significant power demand such as health care, manufacturing or data centers. It is also commonly seen on commercial and institutional campuses with multiple buildings where the owner wishes to own and maintain the power system. transmission or for bigger motors/loads.
This is because systems that have a higher power demand will have a lower current draw in a MV system than a LV system. This results in much smaller voltage drops and reduced sizes of cables, which reduces cost and distribution space needs. However, the MV cable delivering the power to the load must be rated for its voltage level and demand. For applications requiring or benefitting from the use of MV, it is important to ensure proper MV wire
sizing and compliance with codes and standards. Although the 2023 edition of NFPA 70: National Electrical Code (NEC) is not a design book, it contains minimum requirements to prevent overheating and fire. The minimum requirements for conductors rated from 2,001 V to 35,000 volts alternating current (Vac), per NEC Article 315, covers the use, installation and ampacities for MV conductors, cable, cable joints and cable terminations.
There are two types of Type MV cables: Type MV-90 and Type MV-105. The numbers following MV indicate the maximum operating temperature of the cable. Type MV-90 cables are rated for a maximum 90°C and Type MV-105 cables are rated for a maximum of 105°C. Type MV-105 cables have a higher current carrying capacity but tend to cost more than type MV-90 cables. These two types must have a thermoplastic or thermosetting insulation and an outer covering consist of jacket, sheath and/or armor.
Type MV cables can be made up of the conductor, insulation, shield, armor and jacket as seen in Figure 1.
Conductor: The conductor carries the current. The conductor material is allowed to be aluminum, copper-clad aluminum or copper per NEC Article 315.12(B). Unlike LV systems, MV conductors are almost always required to be stranded.
Insulation: The insulation prevents the flow of current to any adjacent ground. The insulation must be thermoplastic or thermosetting per NEC Article 315.10(A), such as ethylene propylene rubber (EPR) or cross-linked polyethylene (XLPE). EPR is a copolymer of ethylene and propylene. It is typically used in the industry due to its flexibility and lower thermal expansion. XLPE is a thermo-
set insulation material. Compared to EPR, XLPE is slightly cheaper and has lower dielectric losses but is not as easy to install.
The thickness of the insulation is dependent on the protective device upstream of the cable and the materials of the MV cable.
For shielded insulated MV cables, there are three levels of insulation requirements: 100%, 133% and 173% insulation level. The application of each level of insulation are depenedent on the upstream relay protection. Cables with 100% insulation level, per NEC Article 315.10(C)(1), can only be used in situations where the system is provided with relay protection that can clear ground faults and de-energize the faulted section within a minute or less.
Cables with 133% insulation level can be used where the faulted section can be de-energized within one hour even if it cannot meet the clearing time for the 100% insulation level requirements.
Cables with 173% insulation level can be used only if:
• Qualified personnel maintan and surpervise the condition of the cables in industrial facilities.
• The fault clearing time required for the 133% insulation level requirements cannot be met.
• The facility requires an orderly shutdown to protect equipment and personnel.
• The faulted section can be de-energized in an orderly shutdown.
The thickness, measured in millimeters and/or in mils (one-thousandth of an inch), of the insulation for shielded insulated MV cables can be found in NEC Table 315.10(C).
‘ The MV cable delivering the power to the load must be rated for its voltage level and demand. ’
Shield: The shield confines the electrical field, symmetrically distributes the electrical stress, reduces electromagnetic interference (EMI) noise and protects the power system by conducting fault current to ground. The following lists the different types of shields. Often, these various shields are applied in combination to provide the facility with the best protection suited for the application.
• A metallic shield, i.e., foil shield, is typically a thin, light layer of either copper or aluminum wrapped around the cable core. The foil shield provides 100% cable core coverage. Due to its thinness, it can be harder to work with. In most cases, to ground the entire foil shield, a drain wire is used.
• A metallic tape shield involves wrapping the cable core with overlapping layers of aluminum or copper tape. The tape provides an effective shield against external EMI and can offer physical protection to the cable core. Often, metallic tape shield is used with another shield type to provide better overall cable protection.
• A wire braid shield is typically made of aluminum, tinned copper or bare copper wires braided into a mesh around the cable core. The braided shield does not provide 100% cable core coverage
due to the gaps, but it does allow for better cable flexibility while offering high levels of shielding against EMI. However, it is made of small wires, meaning a cable with a braid shield tends to be bulkier and more costly.
• Extruded insulation shielding is a methodology for providing a shield by adding semiconductive materials to the cable insulation to provide the inherent shielding properties. This typically eliminates the need for additional shielding layers, which simplifies the cable construction process.
• A semiconductive shield is made of a layer of semiconductive material, typically in the form of tapes or screens, which is applied over the insulation. This type of shielding helps distribute the electric field evenly across the cable’s surface and reduces the risk of electrical stress concentration.
Not all MV cables are shielded. For nonshielded insulated MV cables, the conductors are limited to voltages rated 2,001 V to 5,000 V and can only be used in industrial establishments where main-
tenance and supervision is done only by qualified persons per NEC Article 315.44. These type of cables are much cheaper as there are less materials and typically smaller in size compared to shielded insultated MV cables.
Since it is nonshielded, the MV cable does not limit voltage stress on the insulation, which can quickly degrade the life span of the insulation making it dangerous to anyone who comes into contact with the energized cable if the insulation is damaged. The requirements for the thickness of the insulation and jacket of a nonshielded insulated MV cable can be found on NEC Table 315.10(B). Nonshielded insulated MV cables are not typically recommended to be used in water treatment plants.
Armor: The armor is a layer of metal, such as steel, wrapped around the outside of the cable. The armor physically protects the cable and is often used in applications where the MV cable is potentially exposed to physical damages. It is not to be confused with the jacket or shield. Typically the armor is not necessary, especially if the MV cable will be protected by a metal conduit.
Jacket: The jacket is the outermost layer that provides environmental protection to the cable. The jacket is often made of semiconductive material that can be flame retardant, oil- and sunlight-resistant.
Like LV conductors, all Type MV cables are required to have markings. Per NEC Article 315.16, all Type MV cables must have the following markings:
• The maximum rated voltage.
• Letter(s) indicating the type of wire or cable.
• The manufacturer’s name, trademark or identifiable marking by the organization responsible for the product.
• The conductor AWG size or circular mil area. Figure 2 shows an example of markings on a MV cable in a pad mounted switch. Type MV cables can be marked with optional additional information such as the cable materials or whether the cable is oil- or sunlight-resistant.
Belimo’s gas monitors are factory calibrated and measure single or dual gas combinations to help maintain adequate ventilation. The monitors can be used as a standalone system or integrated into a building automation system using BACnet MS/TP.
If the MV conductor is intended to be used as ungrounded conductors, the cable needs to be clearly distinguishable from grounded or grounding conductors per Article 315.14. The distinguishable markings shall not conflict with any of the four required markings as listed previously.
There are four different allowable methods to mark Type MV cables. They can be used alone or in combination. These are:
FIGURE 4: A one-line diagram shows the electrical system at a water treatment plant. The switchgear feeds power into two utility switches with a radial loop connection, providing power to several utility transformers powering various buildings and well sites. Courtesy: CDM Smith
• Surface markings: Where the cable is durably marked on the surface. The conductor size needs to be repeated in intervals of 24 inches. All other required markings can be repeated in 40-inch intervals.
• Marker tape: Where tape containing the required markings is located within and along the complete length of the cable.
• Tag marking: Where a printed tag with the required markings is attached to the cable reel.
• Optional marking of wire size: Applicable only for multiconductor type metal clad cables (i.e., MV cables with armor). The wire size of the conductor can be marked on the surface of the individual insulated conductors in the multiconductor.
The minimum size of the MV cable is limited by the voltage level per NEC Article 315.12(A). Refer to Table 1 for the minimum size requirement for MV cables per typical voltage levels seen in a water treatment plant. For a complete list of minimum sizes, refer to NEC Table 315.12(A).
This is a case where the NEC must not be used as a design guide. Even though the NEC has a minimum size requirement, some manufacturers do not make MV cables as small as the size listed in the table. For a complete design, availability of cable sizes must be checked and confirmed with MV cable manufacturers to ensure availability of the MV cable.
Per NEC Article 315.32, Type MV cables, with different requirements and exceptions, can be installed in wet/dry locations, raceways, cable trays (per NEC Article 392), exposed runs (per NEC Article 305.3), corrosive conditions, direct buried (per NEC Article 315.36) or paralleled (per NEC Article 310.10[G]).
How and where the MV cable is to be installed influences the ampacity of the cable. In situations where there is more than one calculated or tabulated ampacity
for the given length of the circuit, the lowest value shall be used. The ampacity for a conductor rated 2,001 to 35,000 V can be found in the NEC Table 315.60(C)(1) to Table 315.60(C)(20) or calculated under engineering supervisions per NEC Article 315.60(B).
The ampacity in the NEC Table 315.60(C)(1) to Table 315.60(C)(20) are provided with the following considerations. Any changes to these considerations will require adjustment.
• Grounded shields: The ampacities detailed in NEC Tables 315.60(C)(3), 315.60(C)(4), 315.60(C) (15) and 315.60(C)(16) only apply for cables with shields grounded at one point. If the shield is grounded at multiple locations for these cables, the ampacity needs to be adjusted with consideration to the temperature increase caused by the shield currents.
• Ampacity in air: The following is mainly applicable for NEC Table 315.60(C)(1) to Table 315.60(C)(10). The ampacities in those tables are based on the ambient air temperature being 40°C. In the cases where the ambient temperature is rated anything other than 40°C, the ampacity needs to be adjusted based on ambient temperature.
• Ampacity in underground (ducts or direct buried): The following is applicable for Table 315.60(C)(11) to Table 315.60(C)(20). The ampacities in those tables are based on ambient earth temperature as 20°C, load factor as 100%, soil thermal resistance (i.e., rho) as 90, the minimum burial depth to the top of the electrical ducts or cable is in accordance with NEC Article 305.15 and the maximum burial depth to the top of the electrical ducts is 30 inches and for direct buried cable, 36 inches.
Temperature greatly affects the ampacity of the conductors. Ambient temperatures different from the considerations listed previously will need to consider ampacity adjustment factors as listed in NEC Table 315.60(D)(4). Temperature increase caused by parallelling conductors per NEC Article 310.10(G) will also require adjustment factors. With multiple current carrying conductor(s) in a raceway, the temperature in the raceway will increase, which will decrease the ampacity level of
‘ Although NEC Annex B is not a part of the NEC requirements, it provides more details on ampacity calculation and considerations for varying values of rho and load factor should a more specific engineering calculation be required.’
the conductor. This means that the conductor will need to be increased to the next conductor size.
The burial depths of all direct-buried cables rated 2,001 to 35,000 V shall be in accordance with NEC Article 305.15, which states that direct buried cables shall be a minimum of 30 inches deep for circuit voltages over 1,000 to 22,000 V and 36 inches deep for circuit voltages over 22,000 to 40,000 V.
Depending on the conduits and location of the raceway, the minimum burial depth may vary per NEC Table 305.15(A). If the burial depths of the raceway are increased in part(s) of the total run, given that the part(s) is only 25% of the total run, then an adjustment in ampacity is not required.
However, if the part(s) of the total run is more than 25% and the burial depths are deeper than 30 inches for electrical ducts or 36 inches for direct buried cables, then an ampacity derating factor of 6% per 1 foot increase in depth needs to be considered for all values of rho. Although NEC Annex B is not a part of the NEC requirements, it provides more details on ampacity calculation and considerations for varying values of rho and load factor should a more specific engineering calculation be required. In most cases, the tables provided in the NEC will cover all areas in the United States, as the rho for the average soil is 90. cse
Lilly Vang, PE, is an electrical engineer at CDM Smith, focusing on the design of electrical power systems.
Joshua Hunter, PE, is an electrical engineer at CDM Smith, experienced in the design and analysis of electrical power systems.
Terence Boland, PE, LEED AP, Principal, Director of Engineering, Fitzemeyer & Tocci Associates, Inc., Woburn, Mass.
HVAC systems to maintain high levels of indoor air quality, thermal comfort and infection control while navigating stringent regulations and rising energy costs
Health care facilities are among the most complex and demanding environments for heating, ventilation and air conditioning (HVAC) design. They require high levels of indoor air quality, thermal comfort, infection control and reliability while facing challenges such as limited space, stringent regulations and rising energy costs. To achieve optimal performance
and sustainability, health care HVAC designers must apply energy-efficient strategies that balance patient, staff, visitor and equipment needs.
HVAC designs must follow the requirements established by various entities, such as ASHRAE, NFPA, the Facility Guidelines Institute (FGI) and the Centers for Disease Control and Prevention. Some relevant codes and standards for industry-standard health care HVAC design are highlighted in Figure 2.
Adherence to state and municipal codes is also necessary and, in many cases, such documents reference the above guidelines in their requirements. Meeting guidelines, such as FGI or ASHRAE, is also often a prerequisite for other health care busi-
ness operations, including insurance coverage or public health department certification.
Health care as a building use is among the more regulated segments of design and construction. This often hinders the ability to design a more energy-efficient system through common solutions like reductions in capacity, diversities or setbacks. These guidelines tend to focus on exhaust increases and associated makeup airflows, filtration performance and air change rates, as well as tighter humidification ranges, which inherently add to energy usage.
Energy efficiency is likely to come with an additional first cost to cover things like more advanced technology or additional controls development. If designing for energy efficiency is made that much more difficult when navigating complex rules and guidelines, why would it remain a project goal? Several motivations should be considered.
Health care facilities consume a large amount of energy, especially within their HVAC systems, which account for about 45-55% of the total energy use in hospitals and 50-60% in outpatient facilities. By implementing energy-efficient measures, health care facilities can lower their utility bills, improve their financial performance and allocate more resources to patient care and quality improvement. According to a study by the American Society for Healthcare Engineering, a 10% reduction in energy use can boost the net operating income of a typical hospital by 1.5%.
More and more federal, state and local regulations and standards that aim to promote energy conservation are appearing. These serve to establish minimum standards and also offer assistance to achieve them. There might also be an incentive to improve on the minimum. In either case, the positive business case is likely inherent and there’s a business benefit to compliance. Additionally, for equipment that’s expected to be in service for a generation, there’s a benefit to future-proofing the facilities for standards we expect to continually develop.
In New England, Mass Save, EnergizeCT and Efficiency Vermont are all state-backed programs that offer financial and technical assistance for energy efficiency projects that may be relevant to various health care applications. Federally, IRS Section 179D provides for available tax deductions on
FGI Guidelines for Design and Construction of Hospitals, Residential Health, Care and Support Facilities, and Outpatient Facilities.
Description
These three separate guidelines provide best practices and recommendations for health care facility design, including HVAC systems. They cover aspects such as space planning, infection prevention, sustainability, and resilience.
ASHRAE Standard 170Ventilation of Health Care Facilities. A standalone document that is also embedded in the FGI Guidelines, this standard provides minimum requirements for ventilation systems in health care facilities, such as air change rates, filtration levels, humidity control, and pressure relationships.
ASHRAE Standard 90.1Energy Standard for Buildings Except Low-Rise Residential Buildings. This standard provides minimum requirements for energy-efficient design of buildings, including health care facilities. It covers aspects such as building envelope, lighting, HVAC, and service water heating.
NFPA 99: Health Care Facilities Code
CDC Guidelines for Environmental Infection Control in Health-Care Facilities
This code provides minimum requirements for fire and life safety in health care facilities, including HVAC systems. It covers aspects such as fire protection, emergency power, medical gas, and electrical systems.
These guidelines provide evidence-based recommendations for preventing the transmission of infectious agents in health care facilities, including HVAC systems. They cover aspects such as ventilation, filtration, air cleaning, and maintenance.
FIGURE 2: Table outlining the relevant codes and standards for industrystandard health care HVAC design. Courtesy: Fitzemeyer & Tocci Associates, Inc.
energy efficiency improvements, and further, the recent Inflation Reduction Act allows for nonprofits, including health care systems, to collect incentives or tax credits.
Energy-efficient HVAC systems help health care facilities reduce their greenhouse gas emissions and environmental footprint, which can contribute to mitigating climate change and its adverse effects on public health. Such alignment with the mission is a clear message to patients regarding the integrity of the facility. Lowering costs while also maintaining high levels of indoor environmental quality for patients, staff and visitors will increase patient satisfaction and care.
Health care facilities serve a unique role not only as businesses but also as civic institutions. The design can offer some opportunities from that perspective. Energy-efficient HVAC systems can demonstrate the commitment of health care facilities to environmental stewardship and social responsibility, which can foster a positive organizational culture and attract and retain talented staff.
Pursuing energy-efficient design and operations strategies in the health care sector is an import-
• Learn about the importance of energyefficient design in health care facilities.
• Identify key codes and standards that govern HVAC design in health care.
• Understand what ways standard health care design can be adjusted and how nontraditional systems can be incorporated to improve efficiency.
FIGURE 3: MEP rendering of surgical suite, which requires high levels of filtration and low dewpoints. Courtesy: Fitzemeyer & Tocci Associates, Inc.
ant component in improving the economic, environmental and social performance of health care facilities. In a competitive market, it’s imperative not to dismiss energy-efficient solutions based on first cost. Instead, focus on the potential benefits to the health and well-being of their patients, staff and communities.
There are numerous health care HVAC applications, from inpatient hospitals to outpatient specialists to residential care. Each project must always be evaluated on its own merits. There isn’t just one design strategy that’s always going to be the best, most energy-efficient choice. However, it’s important to remember the throughlines of ventilation and exhaust, air changes and filtration, which are the consistent drivers for health care HVAC. There’s no avoiding these potential energy hogs, but there are ways to reduce their impact.
An important concept that should be considered in almost any design is that systems should be designed for the space they serve and, conversely, systems shouldn’t serve spaces they aren’t designed for. On the surface, this seems obvious. The implication is that a system shouldn’t be under designed for its space. It goes both ways though. It can be
incredibly wasteful to run an entire medical office building, for instance, through a unit designed to accommodate a space with the most stringent requirements.
Spaces where this is particularly important include operating suites, compounding pharmacies and other areas where high levels of filtration and low dewpoints are required. Consider how the design can reduce the amount of airflow required through a HEPA filter, across an eight-row chilled water coil or the mass of air that needs to be cooled to 48-49 F only to be re-heated back to a tolerable level. In terms of maintaining this type of unit, cleanliness is costly, both operationally and with respect to the first cost of a stainless-steel equipment upgrade to be kept sanitary more effectively.
This is also applicable to a space like an emergency department that has heavy exhaust requirements. Energy recovery is most attractive at 100% outside air, and effectiveness drops as more mixed air is introduced. Running additional air across an enthalpy wheel doesn’t provide worthwhile benefit. It makes sense to provide the energy recovery ventilator (ERV) only for the emergency department, where it’s needed, and address adjacent spaces with a lower feature unit and economizer.
On the other hand, non-clinical administrative and office spaces can be divorced from any clinical system. There is often an opportunity to provide a small, flexible, self-contained system, such as a variable refrigerant with energy recovery that uses basic filtration and lower air change and ventilation rates to reduce the equipment load.
One of the most straightforward ways to realize energy savings in any application is through controls, which can be retrofitted to an existing building management system (BMS). Smart sensors and controls can optimize the operation and performance of the HVAC system by reducing the energy waste. Through a fully integrated BMS, controls should also be set up to monitor as many key indicators as possible and adjust as needed. Not only should the building be looking to lower airflow and initiate setbacks based on timing and occupancy, but also at outdoor temperatures for hydronic temperature reset, solar conditions for automatic shades and historical trending to identify energy waste from a broken valve or actuator.
“ It’s good to be proactive rather than reactive. You have to go find out what’s out there, get outside of your role and your company and see what other people out there are doing.”
Level up at the event for HVACR.
FEBRUARY 10-12, 2025
FIGURE 4: Air Handling Unit (AHU) fans, which are an essential component of an HVAC system that help maintain temperature and humidity levels, and distribute air properly throughout a building. Courtesy: Fitzemeyer & Tocci Associates, Inc.
Finally, it’s important to remember that the controls design intent shouldn’t be neglected during operation. Resets and overrides are the enemy. To ensure they are operating as designed consider periodic re-commissioning and retro-commissioning, especially if the system has been in operation for 10 years or longer. As time goes by and operations “fixes” this, replaces that and adjusts the other thing, all without documentation, the properly designed system gets lost. Personnel changes in facilities departments can be a huge driver of inefficiency for this reason.
The basic standard for health care design is a system of variable air volume (VAV) terminals with re-heat connected to a heating and cooling air handling unit with economizer ventilation. This system provides a straightforward way to accurately deliver a lot of air at a robust minimum outside air percentage to a lot of spaces. It also provides a means to control high humidity through sub-cooling and re-heat. If the AHU contains a humidifier, then low-limit control is also available. With all this in place, the
basic needs of a standard health care design are met. While there are other design concepts that have been used extensively, such as constant volume and fancoils, VAV is the most common default.
All VAV systems should be designed with appropriate setbacks. When not in use, conference rooms and shared spaces should be subject to CO2 occupancy sensing. Guidelines are inconsistent, but 1000 parts per million (ppm) is a reasonable maximum and it can be assumed that ventilation is not needed in that space at 200-400 ppm. Spaces that aren’t used 24 hours should be on a time scheduled setback, and overrides should have a timer on them as well. Consider using fan-powered terminals to facilitate actual unit shutdown overnight. Setbacks setpoints should be specified for airflow and for temperature.
Spaces that require pressurization monitoring typically provide an opportunity for setback management as well. For instance, a compounding pharmacy likely has a negative buffer room, positive buffer room and ante room, depending on the specific program. Consider including both supply and return VAV terminals in the design, so that the system can respond to both pressurization and minimum air changes. A dedicated pharmacy suite air handling system is important to realize this efficiency.
Another legacy concept is that of terminal cooling, often exemplified by zoned fan-coils. This type of system intends to reduce the amount of air that the system has to move in large quantities throughout the building, thereby gaining some energy savings. Drawbacks of these types of systems are often due to the inability to maintain tight conditions ranges, along with the maintenance of additional fans, motors or coils. Specific to health care, these systems often are unable to provide the filtration requirements.
Active chilled beams are an energy-saving terminal cooling technology that can reduce the fan power and cooling load of the system. These systems can apply to health care HVAC design under certain circumstances. An active chilled beam is a device that consists of a coil and air nozzle array. Room air passes through the coil and provides sensible cooling or heating to the space. The primary air supplied by the nozzle array is typically conditioned by a dedicated outdoor air system (DOAS), ERV or desiccant system that provides the required ventilation and humidity control.
THE PROJECT FOCUSED on designing an energy-efficient HVAC system for a 33,500 sq ft healthcare facility.
The project involved the design of a new 33,500 square foot health care facility with three floors and a basement, along with provisions for future vertical expansion. The facility would provide primary care, behavioral health services, pharmacy, lab and community amenities to the local population.
The main design challenge was to provide a high-performance HVAC system that would meet the diverse and stringent requirements of different program elements, achieve energy efficiency, indoor air quality and occupant comfort goals while meeting the client’s overarching corporate goal to phase out the use of fossil fuels. The HVAC system had to accommodate the varying heating and cooling loads, ventilation rates and exhaust needs of the different spaces, as well as plan for potential future expansion. Additionally, the available budget for the work was on the leaner end of the typical spectrum.
The VRF system consisted of multiple outdoor units connected to multiple indoor units via refrigerant piping. The indoor units were mostly ceiling concealed ducted units, with some wall-mounted units, based on space requirements and aesthetics. The indoor units were controlled by individual thermostats and could modulate their capacity to match the zone load. The outdoor units were controlled by a central controller and could operate in heating mode, cooling mode or both, depending on the demand. The outdoor units were also equipped with variable speed compressors and fans, improving the part-load efficiency and reducing the noise.
‘
The main design challenge was to provide a high-performance HVAC system that would meet the diverse and stringent requirements of different program elements.’
As part of the process, a third party conducted a preliminary energy modeling exercise to analyze potential solutions. Three basic variable air volume (VAV) systems with hot water re-heat and varied types of cooling were compared against the variable refrigerant flow (VRF) with energy recovery ventilators (ERV) scenario. The VRF was found to be by far the most energy efficient.
Of the four energy uses reviewed, three were significantly reduced, while one came with a minor penalty. Fan power was reduced through the use of multiple small, lower-static variable speed fans. Humidification energy was reduced by virtue of only humidifying needed ventilation, rather than also during economizer periods. Heating was vastly reduced due both to heat recovery from using heat rejected from one space to warm exterior spaces and the lack of a re-heat requirement.
Only cooling used more energy, as the inability to go to economizer mode for a dedicated outside air system required full-time cooling work by the VRF compressors.
The design solution was to use a VRF system with ERVs for the HVAC system, specified with the capability for simultaneous heating and cooling of different zones.
Active chilled beams can be used in health care facilities that have medium to high sensible heat ratios, such as patient rooms, offices or corridors. This kind of system reduces fan energy by lowering the required primary airflow rate when compared to a VAV system, and eliminates the zone fans through the use of a high-pressure differen-
This project included a central roof-mounted ERV with enthalpy wheel technology for ventilation and general exhaust. The pre-conditioned air was ducted throughout all floors of the building to connections at each interior unit. The ERV system was designed for constant volume operation, with the only airflow management being off-hours unoccupied (off) mode.
The VRF and ERV system provided a very energy efficient system, utilizing both ventilation and space heat recovery to lower the requirements on the fans and compressors. Aside from efficiency, the VRF system lends itself to excellent indoor air quality and thermal comfort performance through individual zone control, once-through ventilation and consistent system discharge conditions. There was also a space utilization benefit in terms of much smaller ventilation ductwork to coordinate with a fairly low structural floor-to-floor.
Without specifying the system for heat recovery, the argument for VRF is not as compelling. While its likely to remain more efficient than VAV with large air-cooled systems, it may not be enough to justify the change from a tried-and-true method. If lowering or eliminating fossil fuel for heating is not a goal, a familiar hydronic system may still work. But when considering the benefits of heat recovery, VRF becomes a fairly easy decision, if it can be made appropriate for the building program.
tial induction system. It also operates with a higher chilled water temperature (to stay above space dewpoint), reducing chiller energy consumption. For specific project needs, active chilled beams can be a good option that could yield 30% energy savings over all-air systems and 20% over VRF. They have excellent temperature distribution and
very low noise levels, but they are more costly to install and require a sophisticated hydronic temperature control system. This system is worth an evaluation where recirculation is allowed by ASHRAE Standard 170: Ventilation of Health Care Facilities.
Terminal cooling may be a legacy concept, but a relatively new and certainly still evolving, technology is VRF with dedicated ERV. VRF is a type of heat pump that can modulate the refrigerant flow according to the cooling or heating demand of each zone, thus reducing the energy consumption and improving the comfort level. VRF systems have become fairly common in recent years and are becoming more well known to building owners and users.
ty, piping leaks will sap performance and efficiency. If maintenance is not upkept properly, system wear will also sap performance and efficiency.
Terminal cooling systems all share one major energy efficiency: each utilizes some form of energy recovery in its ventilation system when they get to be a certain size. This has been standard practice for years, as it is generally inexpensive to install and maintain. More recently, it’s been mandated by most relevant codes and guidelines.
While not always ideal for the central system of an inpatient hospital, terminal cooling offers many benefits for a satellite system or for an outpatient application.
csemag.com
Energy efficiency insights
u Energy-efficient strategies like variable refrigerant flow, active chilled beams and smart controls can significantly reduce energy consumption in health care facilities.
u Designing HVAC systems tailored to specific spaces within health care facilities is crucial for optimizing energy use and achieving compliance with stringent industry standards.
However, it may be that the biggest energy saving benefit is too often being value-engineered out or ignored altogether. VRF can be specified to be capable of simultaneous heating and cooling, meaning that, for instance, the heat rejected from the solar gain on the southern exposure on a cool, sunny day can be used to heat the spaces on the northern exposure. This is a massive benefit as any heat reuse directly reduces the energy requirement of the outdoor condensing unit and heat pump. Health care facilities often have diverse and dynamic thermal loads. Even with its high-cost, simultaneous VRF design should be evaluated in these cases.
It should be noted that VRF, like any terminal system, includes more equipment spread throughout the building, creating more opportunities for failure. If initial installation is not of a high quali-
Health care HVAC design is a complex and challenging task that requires compliance with various codes and standards, often at the expense of energy efficiency. By providing the amount of ventilation air, filtration and cleanliness levels and the specific temperature and humidity conditions required, design engineers are continually introducing loads to the system. By utilizing some of the recommendations and practices outlined in this document, health care facilities can achieve HVAC systems that provide safe, comfortable and healthy indoor environments, while reducing energy consumption and costs. cse
Terence Boland, Director of Engineering and Principal at Fitzemeyer & Tocci Associates, Inc., is a registered mechanical engineer and LEED Accredited Professional with 20+ years of experience in the AEC industry.
Randy Schrecengost, PE, CEM, CxA, Member ASHRAE, Stanley Consultants, Austin, Texas
System analyses and appropriate selections are necessary when choosing an optimal HVAC system.
The process of selecting and sizing heating, ventilation and air conditioning (HVAC) systems includes several steps that a designer needs to complete for any given installation or application. The final selection of an appropriate system option is based on the designer’s experience, the owner’s requirements and the overall project constraints.
While providing comfortable HVAC systems has always been important for design engineers, energy efficiency has become a particular focus in recent years. The owner’s project budget and many other factors will impact a building’s overall energy use. As building codes and standards have become more stringent, owners, property managers and/or those in charge of budgetary responsibilities for projects should fully understand how design decisions will impact energy use.
ly include safety, structural stability and energy efficiency requirements. To ensure compliance throughout the design, construction and operation phases of a project, the entire team of professionals must familiarize themselves with the relevant codes and standards.
Local, state and federal codes, standards and/or regulations dictate requirements that can affect an HVAC system’s design, installation and operation. Location, building type and occupancy dictate the specific sections of the codes and standards that will ensure safety, efficiency and compliance with regulatory requirements. As the design of a system includes multiple components related to its specific application, a thorough review of the codes, standards and/or regulations necessary to finish a design must be completed to avoid conflicts.
Codes vary from state to state but typical-
ASHRAE is one of the most useful organizations that coordinates and develops consensus standards to establish minimum values for acceptable performance levels. ASHRAE publishes standards and guidelines specifically related to HVAC systems, indoor air quality (IAQ), energy efficiency and thermal comfort. These include ASHRAE Standard 90.1: Energy Standard for Buildings Except Low-Rise Residential Buildings. This is the reference standard for Energy Efficiency with the purpose, “to establish the minimum energy efficiency requirements of buildings, other than low rise residential buildings, for 1) design, construction and a plan for operations and maintenance and 2) utilization of on-site, renewable energy resources.”
Of the International Code Council codes, the International Building Code systems, in residential and commercial buildings. The IECC mandates energy efficiency requirements for HVAC systems and the IMC provides requirements for the design, installation, operation and maintenance of various mechanical systems. It covers ventilation, duct systems, heating and cooling equipment and energy efficiency.
Finally, the Unified Facilities Criteria (UFC)
• Identify codes and standards that guide design and specification considerations of HVAC systems.
• Understand basic information for selecting HVAC Systems to meet Owner and project requirements.
• Identify the roles and components of air handling units (AHUs) in HVAC systems, including configurations and applications for various building types.
FIGURE 1: This illustrates a plan view of a hydronic supply and return water boiler plant system using multiple boilers and pumps in a primary / secondary pumping arrangement with N+1 redundancy. Courtesy: Stanley Consultants
covers all types of systems and components for the different military branches and some federal buildings. One example is UFC 3-410-01 for HVAC Systems which provides design requirements for system sizing and selection and types of HVAC systems based on building occupancy, usage and climatic conditions.
It may sound simplistic, but system selection is greatly dependent upon the project being developed. A new building being designed can have almost limitless options, depending on the owner’s
budget for both upfront costs and long-term operating costs. The options might be considerably reduced for a building upgrade or retrofit project due to space constraints or budget, often dictating a similar system selection with some conversions to more advanced components.
The owner and designers must work together to define and prioritize project goals and criteria to meet the design. Designers should present the advantages and disadvantages of various system types, while the owner should relate how the systems will fit within the project's financial and operational goals. Project criteria to consider include local climate and comfort, building load calculation and energy model, proposed and future equipment capacities, system reliabilities and redundancies, serviceability and sustainability.
Once the project criteria and goals are identified, any system constraints must be evaluated with the different possible system selections. Constraints may include the building architecture and functionality (occupied tenants, process and ventilation requirements, etc.), available space for equipment, limitations on capacities and performance (temperature, humidity, efficiencies), applicable local codes and available utility sources.
The primary goal for HVAC designers is to provide a system that can meet the building's comfort requirements at a reasonable cost while minimizing maintenance costs and energy use. IAQ, energy use and occupant thermal comfort are a few of the concerns faced by building operations and maintenance staff. Due to project constraints, and specifically the owner’s budget, potential HVAC system choices are typically narrowed down to one or two options. These selections will typically also consider a primary system that creates a medium for the heating/cooling requirements and one or more secondary systems that deliver the conditioned medium to the individual spaces for environmental control.
Centralized, or decentralized primary HVAC systems will produce the medium air, water or refrigerant for the cooling/heating requirements for a specific application and deliver it in a constant or variable volume format. Afterward, one or more secondary systems will ultimately deliver the medium to building spaces (e.g., pumps, air handling
units) for the control of each individual environmental requirement. Designers have multiple options to employ in HVAC systems but, in general, there is always a heat absorption or removal component and a transfer of that heat within the medium (water, refrigerant) to a heat rejection component (a condenser, heat exchanger) where the waste heat is “dumped or wasted,” and the medium is recycled back to the original component.
Cooling systems may consist of various technologies such as chillers, direct expansion systems or evaporative cooling that provide equipment for selecting and designing these systems to meet specific cooling loads and conditions. Most primary cooling systems employ refrigerants in a vapor-compression or absorption cycle. They can also include chillers (air- or water-cooled), heat pumps (air, ground or water source) and other refrigeration-based systems that may be centralized, remote, split or portable. Some systems are evaporative, using water evaporation and swamp coolers to cool air in either smaller or larger applications, including cooling towers. Other systems use chemical-based substances like desiccants to control temperature and humidity by absorbing moisture from an air stream. No matter what
HVAC insights
uProject-specific criteria influence HVAC system selection and design.
u Air handling units (AHUs) and associated components are critical in maintaining indoor air quality.
4: An HVAC layout within a dorm room utilizing 4 pipe FCUs along with pretreated OA (DOAS supply air) being provided directly to the room. Courtesy: Stanley Consultants
kind of system is employed, there will be additional components and possible devices such as pumps, compressors, expansion tanks, air separators or eliminators, control valves and more.
Primary heating system types may include boilers and furnaces that provide heat by circulating hot water or steam through a network of pipes or heated air that is distributed throughout the building via ductwork. The distributed medium temperatures are controlled either by utilizing various types of fuels or with heat pumps and refrigeration-based systems. Just like in the cooling systems, there should be an emphasis on selecting the most efficient and appropriate system while keeping in mind that there may be similar additional components and devices. Designers should select the equipment at high part load efficiencies to maximize energy savings while considering any mission-critical functions that might require redundancy provisions incorporated in the design.
A pump is required in any hydronic system composed of piping, fittings, heat exchangers or other equipment through which a fluid needs to be delivered or transferred. The process of selecting and
sizing pumps includes several steps for any given installation.
Items to consider in selecting a pump include overall system layout, building floor space and headroom, requirements of the pumping scheme, code issues, intended life of the system, up-front costs of the pump versus maintenance costs and overall energy use. The piping distribution system may have more than one pump and may operate in series or parallel.
Air handling units (AHUs) are comprised of several components that must be integrated to efficiently condition a mixed air stream of both outside air (OA) and return air (RA) within the building. In terms of functional definitions, most HVAC air systems fall into two major types. A constant-volume, variable air temperature system provides constant airflow and varies the temperature of the air delivered. Conversely, a variable-volume, constant air temperature system will vary the amount of air delivered to the space and keep the temperature the same. With new technology and increased sophistication of building automation systems (BAS), modern HVAC systems can be a hybrid.
AHUs typically contain added equipment or components for control, isolation, safety and static pressure gain to perform a combination of the four basic psychrometric processes of cooling, heating, dehumidification and humidification. Common components are fans or blowers, cooling and heating coils, filters to remove particulates and contaminants, energy recovery devices, dampers, controls to regulate and circulate the various airstreams and inlet and discharge plenums. AHUs can come in any number of sizes and capacities ranging from airflows of a few hundred cubic feet per minute (cfm) to tens of thousands cfm.
AHUs are used to condition and/or circulate air within an overall HVAC system. They can be small terminal types used in local environmental spaces that include minimal components such as fan coil units or blower coil units. Slightly larger AHUs selected for outdoor use, located on grade outside or the roof, are usually referred to as packaged units or rooftop units. Other units of similar sizes can be located in buildings, typically inside a mechanical room, or maybe in an elevated mezzanine area. In addition to the components noted
Greenheck’s air source heat pump dedicated outdoor air system delivers optimal comfort and efficiency while minimizing your environmental impact. Our advanced technology provides reliable heating and cooling for commercial buildings, even in challenging climates. Experience the future of commercial HVAC solutions while reducing your carbon footprint with Greenheck's air source heat pump.
Specify with Confidence. Specify Greenheck.
above, these units will typically have control dampers and serve larger areas or multiple zones within a building. They are much more defined in terms of total heating and/or cooling capacities.
The next level of AHU is considered semi-custom, highly flexible and cataloged. They can be selected to meet almost any commercial, institutional or industrial applications. Many manufacturers have a line of these types of AHUs that can be modified to meet a designer’s specific job requirements for new or existing building projects. These units use building-block or modular construction methodology for a wide range of standard and custom-engineered modules or splits. There are standardized components available such as fans, coils, filters and control packages with optional components.
Lastly, designers can specify custom AHUs for special applications or capacity requirements of a project that goes beyond standard manufactured equipment, often due to physical size constraints. These units are engineered and designed so their
size, material type, wall thickness, insulation and internal components can be altered to meet specified performances. For example, a large semi-conductor manufacturing plant might need several AHUs sized at 150,000 cfm with a 200 horsepower fan motor and a preheat coil, a primary and secondary chilled water coil, a glycol coil, a reheat coil and a humidifier section to precondition and treat outside airstreams.
One other subset of AHUs is a dedicated outdoor air system (DOAS). As the name implies, a DOAS conditions 100% of the outdoor air brought into a building for the use of ventilation. This outside air can be delivered to all the occupied spaces directly or in coordination with local/zoned AHUs or terminal equipment to serve the building’s HVAC requirements. A DOAS unit will use familiar equipment to treat the building’s outdoor air stream independently and completely before it enters the building’s systems and mixes with other supply and/or return airstreams. A DOAS unit can be successfully applied across a wide geographical range within several different climate zones.
An AHU is a metal box that comes in different sizes depending on the components or appurtenances necessary for the applications. They are typically constructed around a framing system with insulated roofing, flooring and side panels, either single or double skin. They are sometimes built in modules, sections or splits as required for the overall configuration.
AHU control damper assemblies should be corrosion-resistant and automatic for mixing and controlling the outside and return airstreams. Both parallel or opposed blade dampers can be used, but pressure relationships and sizing for wide-open and/or modulating pressure drops need to be considered. Dampers should be specified to meet the leakage requirements of ASHRAE Standard 90.1: Energy Standard for Buildings Except Low-Rise Residential Buildings and the International Code Council.
Filters should be placed in the mixing plenum or filter section of an AHU ahead of other components, such as fans and coils. Their primary function is to filter out dirt and other contaminants and protect the AHU’s other components. Filters can be arranged in one or more layers or sets within a
THE RENOVATION of a 1990 dormitory aimed to correct mechanical, electrical and plumbing deficiencies, upgrade code compliance and improve air quality.
A dormitory building was constructed in 1990 and consisted of 100 rooms. Over the years, the building was operated with sustainment-level repairs and maintenance, resulting in multiple mechanical, electrical and plumbing deficiencies that required code compliance upgrades, as well as environmental remediation and deteriorated interior finishes. The basis for the renovation and improvement design was to correct deficiencies and reconfigure the dorm room restroom areas to provide additional lavatories, toilets and showers as well as abate asbestos, mold and mildew. The goal was to extend the life of the dormitory and ensure students' quarters met or exceeded minimum standards by converting to a newer, more appropriate HVAC system and by re-ducting air distribution to improve exhaust and outside air ventilation of all areas as required to meet fresh air/health requirements and to prevent IAQ issues.
exhaust airstreams included new outside air and exhaust risers ducted to each room vertically from the attic space above.
• The installation of a new crawlspace exhaust fan to dry out the building’s crawlspace.
• A new building automation control system panel to incorporate all new and existing building components and allow for monitoring and control from the campus energy management control system.
• Advanced metering of applicable utilities to meet mandatory requirements of the applicable codes.
The existing HVAC system consisted of a hydronic distribution supply and return piping system that could either provide chilled water (CHW) or heating water (HW) with their associated pumps served from two separate CHW / HW central plants located nearby. Depending upon the cooling/heating seasons, the required CHW / HW was distributed to the building’s twopipe fan coil units serving each living unit. Other components of the HVAC system provided exhaust to all toilet rooms and provided exhaust and freeze protection to mechanical spaces.
The goal was to extend the life of the dormitory and ensure students' quarters met or exceeded minimum standards
All the work was designed, specified, fabricated and constructed per the latest standards and codes, other ordinances and industry standards when not in conflict with the above. These included reference to High Performance and Sustainable Building Requirements, Cybersecurity of Facility-Related Control Systems, ASHRAE Standard 62.1: Ventilation for Acceptable Indoor Air Quality, ASHRAE Standard 90.1: Energy Standard for Buildings Except Low-Rise Residential Buildings, International Building Code and NFPA 90A: Standard for the Installation of Air-Conditioning and Ventilating Systems.
The scope of work was to install a new HVAC system, including controls as needed; to reduce energy use; provide year-round comfort and improve ventilation of the living units; improve exhaust of toilet/shower rooms; and provide crawlspace ventilation to address mold issues under the building.
The new system included:
• The installation of four-pipe fan coil units, along with associated controls in each dorm room, and a new four-pipe hydronic system per the latest accepted codes. The new system included all new piping and insulation, pumps with N+1 redundancy and associated accessories, appurtenances and controls required to continue utilizing the existing chilled water and hot water distribution systems.
• The installation of two new dedicated outside air systems (DOAS), one each for both the east and west half of the dorm complex, to deliver conditioned outside air to each unit and assist in providing humidity control. The DOAS units were direct expansion types. Refer to Figure 5.
• The installation of two new energy recovery units (ERU) to pretreat the outside air streams before being ducted to each new DOAS unit. An air-to-air fixed plate heat exchanger was used for the energy exchange within the ERUs to provide lower energy costs associated with preheating and precooling the outdoor air streams.
• The replacement of all supply air and exhaust ductwork with associated insulation and room air devices. Both the supply and
The ASHRAE 62.1 exhaust ventilation excerpt demonstrates the minimum exhaust rate required for each room per the prescriptive compliance path. The renovated dorm building design included dedicated exhaust vents from each restroom to a central system with a continuous operation fan for the applicable occupancy categories for the rooms. Once the minimum total exhaust rate was determined a safety factor of 10% was used to ensure room pressurization and allow for the Test and Balance contractor to be within plus/minus 10% of the design requirements (per recommendations of the Associated Air Balance Council for operational practicality, flexibility, and system variability and uncertainty).
The ASHRAE 62.1 Outdoor Air Calculation demonstrates the minimum outside airflow quantity required for each room per the ventilation rate procedure. This is required to be calculated and tabulated in design documentation per Section 6.2 of ASHRAE 62.1. Increasing outdoor airflow compared to ASHRAE 62.1 minimums provides benefits such as increased health and productivity of space occupants as well as reduced sensible/latent loads for the terminal fan coil units. In addition, the ASHRAE DOAS Design Guide recommends a positive ratio of outdoor air to the exhaust air to create a slightly positive pressurization to the building (to combat infiltration) whether in a cold or hot and humid outdoor climate, to prevent air and moisture from leaking into the building envelope and/or occupied spaces and causing comfort and IAQ issues.
There were 10 combinations of unit size and fan speed selected to fit the desired operating parameters for the fan coil units. The selections covered the range of loads (Btu/hour) and supply airflows (CFMs) that corresponded to the building load outputs.
Although the ERUs’ loads were not equal between the East and West wings, they were provided as the same model/size to comply with ASHRAE 90.1 effectiveness values.
holding frame assembly or racking system configured in flat or angular bank arrangements. Filters can be a variety of types and sizes, from throwaway 2-inchthick type to reusable 36-inch-deep type, based on the application. Filters are rated
by ASHRAE Standard 52.2 test methods and classified by the minimum efficiency reporting value ratings.
Another important component of AHUs is the supply air fan. Depending upon the size and application, this supply
fan can be composed of a centrifugal fan, one or more plenum or plug fans or a vane axial fan. The AHU can also have a return air fan to assist in overcoming static pressures to get the return air back to the AHU.
The ASHRAE Handbook - HVAC Systems and Equipment, Chapter 21, covers fans and provides information on selection criteria, such as the desired design operation point for the airflow required and the static pressure of the system.
Coils are used in AHUs to provide sensible heating or cooling and/or in conjunction with humidification and dehumidification for various psychrometric applications or processes. Coils are primarily constructed of copper tubes with copper or aluminum fins pressed or extruded on the external surface for several heat transfer processes. Chilled water and refrigerants for are often used for cooling and hot water, steam and refrigerants are typically used for heating.
BAS are typically involved in all HVAC systems as well. Using direct digital control system components, the BAS will provide enhanced control and monitoring of HVAC operations using equipment and component control sequences to achieve energy management and savings goals. These sequences improve system efficiency and provide real-time data for maintenance and troubleshooting efforts. An overall control sequence can manually enable the system’s components or automate the process through a BAS. Control schemes for a HVAC system will usually vary with the size and complexity of the system. cse
Randy Schrecengost is a Senior project manager / principal mechanical engineer with Stanley Consultants. He has extensive experience in design and in project and program management at all levels of engineering, energy consulting, facilities engineering and Commissioning. He is a former ASHRAE Director Regional Chair for Region VIII and is a member of the Consulting-Specifying Engineer editorial advisory board.
The biggest trends in hospital and health care facility design include a focus on decarbonization, patient experience and integrating telehealth technologies.
CSE: What are the biggest trends in hospitals, health care facilities and medical campus projects?
Cory Duggin: Health systems are looking for us to help guide them toward their emissions reduction goals as part of new projects, expansions and longterm infrastructure planning. There isn't a one-size-fits-all solution to health care decarbonization. We have to look at the location, electricity grid conditions, climate and existing infrastructure to create a bespoke plan for each client.
Benjamin Medich: Emphasis on the patient experience is central to the design and delivery of 21st-century health care. Telehealth and virtual care are becoming key components of patient care offerings, especially since COVID19. This drives additional technology integration and requires additional informational technology (IT) bandwidth to support the caregivers who are practicing both in-hospital and remotely.
Kevin Jayne: The complex nature of hospital operations demands design considerations far beyond those of less critical building types. A strict regulatory environment dictates programmatic elements such as departmental adjacencies and space types. At the same time, the engineering systems must carefully balance requirements for temperature, humidity, pressure relationships, device quantity and type. Health care design requires extensive coordination in support of patient experience, navigating a complex puzzle that addresses diverse stakeholder priorities.
CSE: What types of challenges do you encounter for these types of projects that you might not face on other types of structures?
ered with as little interruption as possible. A design must allow for renovation work to continue without disrupting critical spaces that could adversely affect the delivery of care. An example of this would be to run under-slab plumbing in non-critical areas (i.e., not above an operating room).
Benjamin Medich: Hospitals have an extensive requirement for generator-backed equipment, which is far greater than in most other building types. Ensuring reliable power to critical functions involves planning beyond first-level failure scenarios and often necessitates more sophisticated solutions than simple generator backups.
• Understand major trends influencing health care facility design.
• Identify ways hospitals and health care facilities are working to meet more stringent energy and efficiency standards.
Cory Duggin: The largest challenge and most important requirement for any health care project is to provide high-quality, continuous care to patients while implementing any upgrades and/or expansions. This can involve temporary backup equipment to feed existing loads while new equipment is installed and brought online. Careful planning and phasing for the construction to ensure no loss of facility operation is paramount.
Daniel Noto: In a renovation project, it's critical that health care can be deliv-
Additionally, hospital staff must be capable of manually operating systems during extended outages. This necessitates designing systems with flexibility for both automatic and manual load-shedding options. Furthermore, curtailment to save fuel must be implemented to maintain operability and reliability, which is a complexity not commonly seen in other less complex buildings.
CSE: What are engineers doing to ensure such projects (both new and existing structures) meet challenges associated with emerging technologies?
Kevin Jayne: Navigating a complex regulatory environment and an industry known for its escalated level of caution regarding any substantive change makes introducing and implementing emerging technologies a significant challenge for health care designers. As energy codes continue to raise the bar, they effectively mandate progressive technology adoption. The design engineer must present these innovations to the owner and diligently review and refine the design to ensure a successful initial implementation.
Daniel Noto: For me, the key to incorporating emerging technologies into a successful health care project is understanding the technology’s benefits and weaknesses. Blindly specifying the newest technology can lead to problems in performance and can cause long-term problems, including expensive replacements in the future. Meeting with product experts, taking factory tours and visiting other facilities with the technologies already incorporated are techniques that can aid in that understanding. Additionally, talking with the people who already have the technology installed is a great way to find out if the benefits are as advertised or exaggerated.
CSE: Are there any changes from the Covid-19 pandemic that are still impacting these kinds of facilities?
Cory Duggin: We are providing additional capacity for pandemic mode in the wings of new facilities to allow higher volumes of exhaust and outside air. All our health care clients want to be prepared for whatever the next challenge is. One way to do that is by allowing for greater flexibility and capacity in how hospital wings operate. This may include going to 100% outside air or making sure designated wings are able to operate at negative pressure compared to the rest of the facility.
Kevin Jayne: Given its unprecedented nature, the industry’s COVID-19 response was decidedly reactive. However, lessons learned have shaped consistent themes in preparation for the next disruptive event. Spaces must be flexible, adaptable and capable of shifting to alternative functions during emergencies or evolving patient needs. For example, standard patient rooms that can flex into double occupancy or accommodate higher-acuity patients. Acknowledging COVID-19’s airborne transmission, design engineers have begun incorporating surge mode capabilities that allow portions or entire patient floors to con-
Cory Duggin, PE, LEED AP BD+C, BEMP
Principal / Senior Energy Wizard
TLC Engineering Solutions Brentwood, TN.
Benjamin Medich, PE Vice president
HDR
Pennington, N.J.
Daniel Noto, PE, LEED AP
Southeast market leader Fitzemeyer and Tocci Associates
Alpharetta, GA.
Kevin Jayne, PE, LEED AP
Principal
Affiliated Engineers, Inc. Denver, CO.
vert into negative pressure environments using exhaust systems to isolate hospital sections.
Benjamin Medich: Facilities are giving more consideration to the design of their isolation rooms, and the flexibility to implement rooms that are convertible to isolation rooms in the event of an outbreak. Furthermore, additional bandwidth is being incorporated into more robust IT systems to provide additional remote telemetry and telehealth capabilities, extending the reach of hospital-based clinicians.
CSE: What types of smart buildings or campuses are you designing for hospital clients? Outline the automation and controls, integration and any cutting-edge technology.
Benjamin Medich: Advancements in metering and control allow for much
more precise operation and understanding of emergency power systems. With the latest metering and control packages, we can see where power is available and look at individual and composite metering to understand how adding loads will affect the local and overall systems operation.
Furthermore, smart systems, such as telemetry and real-time monitoring, allow for faster response to changes in patient data and environmental conditions.
Kevin Jayne: The modern hospital facility must balance competing energy use demands. Natural light enhances patient outcomes, but glazing also increases solar heat gain. Medical technology and equipment advancements require more electricity, often introducing additional heat to a space. Regulatory requirements for minimum air changes further amplify electrical demand by increasing fan power consumption. Addressing these rising demands while adhering to energy codes requires an opportunistic system approach, such as through heat recovery. Equipment such as heat recovery chillers capitalize on a building’s consistent year-round heating and cooling loads, utilizing the available heat to generate chilled water. Maximiz-
ing the run time of such systems optimizes efficiency.
CSE: How are hospitals, health care facilities and medical campus buildings being designed to be more energy efficient?
Cory Duggin: The biggest challenge in health care facility design is efficiently handling the heating, ventilation and air conditioning load created by the requirements of ASHRAE Standard 170: Ventilation of Health Care Facilities. ASHRAE 170-2021 added a column to Table 7-1 for which spaces are allowed to setback when unoccupied. Incorporating unoccupied setbacks to reduce the required air changes per hour when spaces are not in use will significantly reduce the cooling, heating and fan energy for those spaces. One space type we have been implementing this in already is operating rooms. Surgeries are largely scheduled, except for emergencies, so we have been able to show 15-20% energy savings in the surgery tower by reducing the minimum total air changes per hour from 20 to six during unoccupied periods, while still keeping a minimal number of operating rooms at full flow for emergency cases. Recovering all useful heat in the building is another simple strategy to
Introducing the VFD Check Valve, the first Center
Guided Silent Check Valve developed for VFDs. Metraflex re-engineered a classic hydronic component to improve e ciency and cut costs.
increase building energy efficiency and lower emissions. Typically, we do this by adding a heat recovery chiller to remove heat from the chilled water loop and add to the hot water loop for reheat. In 2022, a requirement for heat recovery chillers was added to Section 6.5.6.3 of ASHRAE Standard 90.1: Energy Standard for Buildings Except Low-Rise Residential Buildings for inpatient health care.
Daniel Noto: Specifically, health care facilities are consistently having electrical reheat being removed and replaced with hot water reheat for variable air volume boxes. Having a central plant that produces either hot water or steam and using that for reheat takes much less energy and reduces costs, particularly in high-energy cost states. Additionally, selecting LED lighting in operating rooms and other high-demand spaces is a trend that we see continuing throughout the health care market.
Benjamin Medich: Designing hospitals, health care facilities and medical campus buildings to be more energy efficient involves navigating competing demands. On one hand, significant investments are being made in energy-saving measures such as LED lighting, advanced lighting controls and more efficient mechanical systems. On the
• Hydrodynamic disc design increases flow.
• Provides superior functionality in low-flow conditions, common with VFD drives. The VFD Check Valve
• Same face-to-face dimension as common globe-style center-guided check valves.
other hand, the introduction of power-intensive medical equipment, like higher-resolution CT scanners and nuclear medicine rooms, has increased overall power demands. Despite these opposing trends, the total power consumption of health care facilities has remained relatively stable over the past 25 years. This stability, however, masks the underlying progress. We are achieving far greater capabilities and efficiencies with the same amount of power. Thus, while the net savings in power consumption may appear marginal, the advancements in medical technology and facility operations represent a substantial improvement in energy efficiency.
CSE: What future design challenges do you anticipate related to hospitals or health care facilities?
Benjamin Medich: The future of green energy will have a notable impact on health care facilities. Electrification is driving up power density, while on-site green energies, such as fuel cells and photovoltaics, are reducing the effect on the overall power grid. Ensuring a safe installation and maximum emission reduction requires more integration and increased coordination within the electrical system and with the serving utility. The ability to be flexible and adapt to new technologies as these become viable without disrupting the facility's daily operation is a key factor in the overall economic viability of future facilities.
CSE: Please explain some of the codes, standards and guidelines you commonly use during the project’s design process. Which codes/standards should engineers be most aware of?
Kevin Jayne: In addition to the suite of International Building Codes that govern various aspects of commercial buildings, health care design must adhere to other sets of codes and guidelines that require careful review and understanding for proper application. The Facility Guidelines Institute (FGI) encompasses ASHRAE Standard 170: Ventilation of Health Care Facilities, which dictates numerous engineering requirements, including quantity and type specifications for electrical, medical gas and low voltage devices, along with mechanical system requirements related to temperature, air changes and pressure relationships. A health care designer must be familiar with FGI to effectively apply relevant design concepts across a range of programmatic applications.
Benjamin Medich: The cornerstone of design is NFPA 99: Health Care Facilities Code, NFPA 70: National Electrical Code (NEC) and FGI. While NFPA 70 and 99 carry the force of code through adoption, FGI's authority currently stems from its use by the Joint Commission in evaluating facilities. NFPA 70 and
FIGURE 1: This structural plastics manufacturing facility and office demonstrates some of the unique considerations engineers face when designing industrial buildings. Courtesy: Page
NFPA 99 are not always aligned, and it is important to know where they diverge, including selective coordination requirements. It’s also necessary to know how your local authority having jurisdiction (AHJ) is interpreting these requirements. For example, many jurisdictions default to the NFPA 99 requirement for selective coordination in hospitals, while some others use the more stringent NFPA 70 requirements.
Kevin Jayne: Proper code application begins with familiarity, as any early design oversight can lead to significant ramifications later in the project. On large-scale projects, the code cycle may shift to the next iteration mid-design, requiring the design engineer to stay current with industry trends. For instance, the
proofing projects to the greatest extent possible by considering how buildings will be adaptable, agile and responsive to emerging technologies. Retrofit and adaptation is a key trend that we are currently experiencing. Network architecture needs to be scalable. Cloud-based solutions should be considered, and control platforms should be as modular as possible to allow the acceptance of technology advancements with minimal change to existing infrastructure.
CSE: from prepared Jarron ogies cess discussion, mentations from holders plan upgrades ability Justin ty issue Because it is possible base facilities base consequences Jonathan owners sion technologies owners ing processes fire alarm request provide ing of mitting Michael easily required, The is growing ity should mation and part tain
‘ Designing above standards and codes is key to a truly successful project and a health care facility that operates with a higher standard of performance.’
FGI 2022 introduced additional resiliency standards through a mandated Disaster, Emergency and Vulnerability Assessment, placing greater emphasis on disaster preparedness than what had been covered historically through the Safety Risk Assessment. A thorough understanding of this process enables health care designers to guide the owner through the assessment and deliver system designs that align with the owner’s goals.
Daniel Noto: For me, the first step is understanding the standards and codes. This comes from referring to them during design, but also staying involved in professional organizations that write the standards (i.e., ASHRAE). From there, one needs to understand that standards and codes are the absolute least you can do on a project. Designing above those standards and codes is key to a truly successful project and a health care facility that operates with a higher standard of performance.
Benjamin Medich: First and foremost, it is essential to read and understand the codes. This involves understanding the content that is written, and also how your AHJ and hospital administration interpret these codes. Depending on your location, interpretation can vary. For example, do you need isolation panels in the operating room (OR)? This depends on whether the OR is designated as a "Wet Procedure Location" according to NFPA 99. However, NFPA does not directly define a "Wet Procedure Location," this designation is made by the hospital.
Understanding these types of code variations and interpretations will
streamline your approach to designing the facility.
Conducting code reviews throughout the design process also keeps the design team updated on emerging regulations that may need to be applied to the project, or which may be beneficial to incorporate.
CSE: From your experience, what systems within hospitals, health care facilities and medical campus projects are benefiting from automation that previously might not have been?
Kevin Jayne: Rapid advancements in technology and computing power continually equip modern hospital facilities and caregivers with greater access to information. There’s been an industry movement toward telemedicine for many years, which was accelerated by the pandemic. These systems now offer enhanced capabilities, providing patients with more immediate access to quality care. Infrastructure to support patient monitoring services has become essential in modern patient rooms. New engineering systems typically integrate with building automation system networks, enabling continuous data logging, supporting improved analysis and offering predictive insights for facility staff.
CSE: What types of system integration and/or interoperability issues have you overcome for these projects and how did you do so?
Kevin Jayne: Smart technology enables clinical, IT and facilities staff to streamline operations in modern health care settings. Given the growing number of stakeholders and subject matter experts involved, integrating these advanced systems necessitates a strategic and collaborative approach. Comprehensive system analysis, including infrastructure planning for future upgrades, is essential to fully leverage smart technology’s potential.
Cybersecurity and vulnerability are increasing concerns. Are you encountering worry/resistance around wireless technology and IoT as the prevalence of such features increases? How are you responding to these concerns?
Benjamin Medich: As cybersecurity and vulnerability concerns grow, we typically restrict the use of wireless technology and prioritize strong cybersecurity measures in our equipment specifications. Our team of dedicated cybersecurity engineers design comprehensive protection schemes to safeguard systems. However, wireless systems inherently present additional entry points for potential cyber threats. While network segmentation can help maintain network integrity and limit the risk of bad actors compromising Internet of Things (IoT) devices, the inability to maintain current security protocols in many IoT devices is challenging and, in many instances, the potential risk outweighs the benefit. cse
csemag.com
u Engineers face unique challenges in healthcare projects, such as ensuring continuous patient care during upgrades and designing systems for reliable power and flexibility during emergencies.
u Post-COVID, healthcare facilities are being designed for greater adaptability and energy efficiency, with an emphasis on flexible spaces.
Case studies provide valuable discovery of challenge situations, recommended solutions, and implementation actions to solve specific real-life issues.
CSE magazine invites you to explore the pages to follow while you learn and benefit from the case study success stories and project details shared by the following companies:
Belimo
Berner Air Curtains
Champion Fiberglass
Cleaver-Brooks
Cummins
Greenheck
Inaba Denko
LS Electric America, Inc.
Miura
Noritz
Regal Rexnord
An online digital content hub for design engineers.
• Classrooms
• Design World Handbooks and Special Editions
• Technical Design Guides
• Industry Trends
Challenge: Outdated software and obsolete hardware were causing headaches for a major beverage manufacturer in South Africa. They wanted to enhance system capacity and increase reliability.
Solution: Cummins collaborated with an electro-mechanical contractor specialized in handling the high voltage installations. A partnership that saw the legacy DMC200/300 decommissioned and a new DMC8000 installed.
ReSult: The DMC8000 not only improved operational efficiency and reliability but also empowered operators with enhanced control and monitoring capabilities, facilitating smoother and more efficient management of operations.
SummaRy: A smoother, more efficient power plant is the goal of any operator, but obsolete hardware, outdated software, and slow communication protocols get in the way. This was the issue a major beverage manufacturer in South Africa was experiencing. It was clear their legacy DMC300 required an upgrade, but they also wanted to add more generators and required changes in the control sequence to enable integration with a PV renewable system.
CliCk or scan QR to read the full Case Study online.
This involved decommissioning the existing panel, disconnecting all control cables, removing the DMC200/300, and installing a new Digital Master Controller 8000 (DMC8000). The DMC8000 represents a leap forward in power plant control technology – Cummins’ capability to empower operators with enhanced control and monitoring capabilities is second to none
Cummins had a two-week window to complete the installation and were required to coordinate the project with other contractors at the plant, including electromechanical engineers specialized in handling high-voltage installations. This project synergy resulted in limited operational downtime, saving the client both time and money. With their DMC8000 fully installed and operational, the client was able to manage their power plant more efficiently and effectively – enjoying improved user interface, ease of data access, and enhanced connectivity.
www.cummins.com
Challenge: Operations demanded varying levels of steam, creating a need for a system that can quickly adapt to fluctuating loads while minimizing downtime and energy consumption.
Solution: Miura’s modular boiler system—unlike conventional boilers—allows for rapid steam generation and precise control, enabling the company to achieve high-pressure steam within minutes.
ReSult: Daily operational efficiency has significantly improved. With the ability to deliver high-pressure steam quickly, the boilers support smooth and uninterrupted production, even during periods of varying demand.
SummaRy: Nu-Tek Biosciences, a leading manufacturer of plant-based peptones used in biological vaccines, faced the challenge of maintaining efficiency in their steam generation process. Miura’s innovative technology has transformed Nu-Tek’s daily operations, improving efficiency, scalability, and overall cost-effectiveness. With the ability to deliver high-pressure steam quickly, the boilers support smooth and uninterrupted production, even during periods of varying demand.
The modular design of Miura boilers offers scalability that traditional systems cannot match. Nu-Tek has already prepared for future expansion by leaving room for additional Miura units as needed. This flexibility ensures that the company can grow without the need for extensive infrastructure changes. Additionally, the efficiency of the Miura system translates into significant cost savings over time. By consuming less energy and operating more efficiently, the company can allocate resources to other critical areas of their business.
Nu-Tek Biosciences has seen substantial long-term benefits from using Miura’s modular boilers. The energy savings achieved through efficient operation are expected to accumulate significantly over the years, enhancing the company’s bottom line. The reliability and cost-effectiveness of Miura’s system have proven instrumental to the success and sustainability of their operations. Click here to read the case study online. 678-685-0929 www.miuraboiler.com
Challenge: The County Home Lift Station in Danville, Indiana sits downstream from a hospital, county jail, and landfill. Objects introduced to the system by these facilities, such as clothing, needles, toothbrushes and more, were causing the station’s three pumps to clog repeatedly.
Solution: The lead pump in the triplex pump station was replaced with a Pentair Hydromatic Next Gen Submersible Pump for a 90-day trial.
ReSult: Throughout the trial, staff noted a considerably cleaner wet well and less debris. The trial was completed without a single clog, increasing productivity and improving quality of life for staff and town residents.
SummaRy: The Danville Wastewater Department was facing rising service costs and decreased productivity due to frequent emergency unclogging with vacuum trucks and manual clearance of debris.
A Hydromatic Next-Gen Pump trial was recommended by local distributor BBC Pump and Equipment, Inc. The Next-Gen pumps utilize an innovative combination of a semi-open stainless steel impeller and self-cleaning cutter plate to eliminate tough clogs. The oil-filled, premium efficient motor reduces energy use and lengthens pump life.
At the first 30-day inspection personnel noticed the significant decrease in solids present. “It does so much work for the other two pumps,” said wastewater operator Wayne Herring. “There’s less trash at our facility. We’re not clogging up.”
During the 90-day trial, the Next-Gen pumped over 17 million gallons of wastewater at an average flow rate of 754 gallons per minute, experiencing zero clogs1. The Danville team was so impressed with the pump’s performance and reliability, they opted to purchase the trial pump and replace the other two pumps at the station with Next-Gen models.
1 Participants were not compensated for their testimonials regarding Pentair products. Statements and values based on a 90-day trial period. Individual Pentair product experiences may vary depending on use case and application.
Challenge: New York City’s Local Law 97 mandates improved energy efficiency and reduced carbon emissions, targeting a 40% reduction by 2030 and becoming progressively stricter through 2050.
Solution: In response to this law, property owner Paramount Group undertook a significant retrofit of three key properties in New York City utilizing the Belimo Energy Valve, a pioneering, IoT-enabled device that optimizes energy usage and maintains Delta T.
ReSult: The reductions in energy translated to over $1 million in utility savings in 2023 and the buildings are now aligned with the 2030 requirements of Local Law 97.
SummaRy: Paramount Group faced challenges with outdated HVAC systems that caused inconsistent tenant comfort in their New York City buildings. The old pressure-dependent, two-way pneumatic valves contributed to overheating or overcooling, and there was no real way to control tenant comfort. To address this, Paramount installed Belimo Energy Valves, creating a pressure-independent system that improved energy efficiency and Delta T performance.
Today they are seeing the true design 18-degree delta at those coils, and in some cases above 20-degree Delta T, demonstrating the effectiveness of the Energy Valve in optimizing coil performance and energy consumption. The valve’s cloud capabilities allowed for remote system monitoring, helping maintain optimal conditions and reducing occupant complaints. The valve even detected legacy problems, like reversed flow in a fan coil unit.
From 2022 to 2023, the retrofit cut energy consumption by 4 million kilowatthours and yielded over $1 million in utility savings across three properties. Also, the Energy Valve’s data reporting helped Paramount secure an additional $2.1 million rebate from utility provider Con Edison. The retrofit has positioned the buildings for compliance with Local Law 97 and demonstrated the Belimo Energy Valve’s role in improving efficiency, tenant comfort, and sustainability in New York’s commercial real estate sector.
Challenge: The Internet of Things (IoT) has transformed industries by connecting devices to the internet, enabling innovations like remote control of home appliances and adaptive traffic systems. The rapid growth in cloud-connected devices has opened new possibilities across sectors.
Solution: Advancements in electric motors now allow for precise control and feedback, offering tailored speed and torque solutions. Modern motors can be electronically controlled, providing real-time operational data to control systems.
ReSult: For over 50 years, LEESON® motors, including SyMAX® EC motors, have delivered reliable, smart, and efficient solutions, excelling in commercial kitchen environments.
SummaRy: The SyMAX-SRi motor offers high efficiency and remote monitoring for commercial ventilation and pump applications, allowing operators to track speed, voltage, and temperature. It features multiple speed control options, including 0-10V DC, 4-20mA, and digital inputs.
• Power density enables compact designs, saving space.
• A flat efficiency curve ensures watt savings across speeds.
• 60°C operating ambient temperature rating provides reliability in commercial kitchens.
• Energy savings of over 30%* compared to induction motors are typical.
The SyMAX-SRt motor is ideal for compact convection ovens with its smaller frame, less than half the length of an induction motor. It helps reduce the equipment footprint, making it easier to move through standard doorways and rearrange in tight kitchen spaces.
• Smart monitoring provides alerts on motor health, voltage, and current to keep the kitchen up and running.
• Tethered control offers flexible mounting options.
• Variable speed capabilities allow for custom cooking cycles.
• Operating ambient temperatures up to 65°C.
• The motor is ~47%* more efficient than standard induction motors, supporting energy requirements.
support@leeson.com • 262-377-8810 regalrexnord.com/leeson
Challenge: Texas A&M University needed conduit installed to replace aging electrical infrastructure at Kyle Field. The project deadline was tight, and heavy rigid steel conduit suppliers presented logistical challenges. The project manager needed an electrical conduit to properly safeguard circuits that could be procured and installed on time.
Solution: The project manager introduced Champion Fiberglass® electrical conduit, which offered quick production and lightweight design. The engineer initially doubted fiberglass conduit’s suitability, but was quickly convinced after learning more about its benefits which also included speedier installation.
ReSult: Champion Fiberglass conduit was delivered within two weeks. The lightweight conduit reduced costs, required fewer workers, and accelerated installation. The field was ready on time.
SummaRy: Texas A&M University, a major educational institution with over 50,000 students, faced a critical deadline to upgrade the electrical infrastructure for their football stadium, Kyle Field. The aging, damaged, and unreliable existing power supply posed a significant safety risk.
EAS Contracting was tasked with installing underground electrical conduit across the campus in a tight timeframe. The engineers specified rigid steel conduit, but logistical challenges and the heavy nature of the material threatened to delay the project.
Champion Fiberglass offered a solution with lightweight fiberglass conduit, which could be procured quickly and installed more efficiently. Despite initial skepticism from engineers, Champion Fiberglass successfully demonstrated the conduit’s ability to meet both protection and regulatory demands.
EAS ordered the conduit and completed the installation within two weeks. The lightweight material reduced costs, required fewer workers, and accelerated the project, ensuring Kyle Field was ready for the upcoming football season.
This case study highlights the successful implementation of a time-sensitive project through innovative material selection and efficient project management. Champion Fiberglass’s solution not only met the urgent deadline, but also provided a more cost-effective and efficient solution for the university.
CliCK or scan the QR to read the full Case Study online.
Communications@championfiberglass.com 281.655.8900 • https://championfiberglass.com/
Oahu Correctional Center safeguards hot water supplies by replacing aging boilers with Noritz tankless water heaters.
challenge: Replace two failing 23-year-old 1,000,000 BTU boilers with a multi-tankless commercial heater system at Hawaii’s Oahu Community Correctional Center to safeguard reliable hot water supplies for its 1,200 inmates.
solution: Installed six NCC199CDV gas-fired commercial condensing tankless heaters to improve the resiliency and reliability of the correctional facility’s hot water supply system.
Result: Besides providing an uninterrupted flow of hot water, the multiple-tankless option offers the ability to service any of the six units without shutting down the entire system. Furthermore, load balancing ensures that operation is equalized across all units, so one doesn’t suffer undue wear and tear.
summaRy: Officials at the Oahu Community Correctional Center (OCCC) in Honolulu were faced with a hot water crisis when their aging boilers and storage tanks failed, posing a risk to staff and inmate hygiene. To address this essential need for hot water, a solution was urgently devised in partnership with Hawaii Gas. They decided to replace the failing boilers with a system of commercial condensing tankless water heaters to ensure a continuous and reliable hot water supply.
The project was executed in three phases to accommodate the facility’s 24/7 operations. The first phase involved installing six gas-fired commercial condensing tankless heaters to serve a portion of the inmate housing modules. The second phase added two prefabricated water heater banks to provide hot water to the remaining inmates. The final phase introduced 12 more tankless units to support the center’s laundry and kitchen operations, ensuring redundancy and uninterrupted hot water supply.
The choice of tankless water heaters, specifically the Noritz NCC199CDV models, offered higher energy efficiency, greater flexibility in meeting demand, and significant cost savings compared to traditional boilers. With a focus on operational redundancy, this approach ensures a continuous supply of hot water even if one or two units are temporarily offline.
The installation of tankless water heaters eliminated the need for bulky storage tanks, simplified maintenance, and significantly reduced operating costs, offering a reliable and efficient hot water solution for OCCC.
ClICk or scan QR to download the study.
commercial@noritz.com www.noritz.com/commercial
Challenge: The necessity to protect and organize the HVAC refrigerant lines at a rooftop installation was heightened by the plans to install solar panel on the same area.
Solution: Slimduct RD enclosures are made of high-quality metal, is hot dip galvanized to increase durability and prevent corrosion. The RD comes pre-assembled for streamlined installation and future maintenance.
ReSult: Slimduct RD provided the durability and reliability needed for the rooftop installation. Protected the HVAC piping from environmental damage and wear, while also streamlining pipe management. “I definitely recommend the RD enclosure, the project looked very neat and clean.”, said James Bencivengo.
SummaRy: Diana Place, Nyack’s new boutique apartments, set a high standard for sustainable living, combining energy efficiency with comfort. Each unit features state-of-the-art, individually controlled HVAC systems. Valley Mechanical Services installed 27 ductless units for the 26 apartments, with piping routed on the rooftop due to space constraints. Protecting the rooftop piping became essential, especially with plans to install solar panel James Bencivengo, managing partner at Valley Mechanical Services, state that “placing the pipes on the rooftop exposes them to the elements, posing a significant challenge”. Despite attempting various solutions such as fiberglass, plastic, and insulation, none proved effective. The persistent issue of crows pecking on the insulation compounded with the risk of damage from people stepping on the piping, leading to cracks and compromises in the system’s integrity.
Facing challenges of insulation degradation, due to environmental factors, Mechanical Services turned to Slimduct RD for a comprehensive solution. The Slimduct RD covers emerged as the optimal solution to protect the HVAC piping while facilitating efficient pipe management. Designed to withstand environmental elements and prevent damage from external factors such as bird activity and foot traffic, Slimduct RD covers provided the durability and reliability needed for the rooftop installation.
Learn more: https://inabadenko-america.com/brands/slimduct-rd/
info@inabadenko-america.com 310-943-7520
www.inabadenko-america.com
Challenge: Chagrin Tavern wanted to maintain an open-air feel with wide-open doors facing the scenic Chagrin River, while keeping the indoor areas comfortable and free from insects. However, allowing so much conditioned air to escape would put the restaurant at risk of high heating and cooling costs.
Solution: Contractor Bruce Botchick recommended installation of Berner’s Architectural Elite air curtains to cover the large door openings. They prevent conditioned air from escaping and keep insects out, all while being quiet and visually discreet.
ReSult: By preventing energy loss while the doors are open, Chagrin Tavern keeps its doors open without worrying about skyrocketing energy bills. Patrons and staff are able to enjoy an inviting, comfortable indoor/ outdoor atmosphere without disturbance from insects.
SummaRy: Chagrin Tavern in Eastlake, Ohio, offers a perfect blend of great food, scenic views, and a welcoming atmosphere. Situated along the Chagrin River, the restaurant and bar invite patrons to sit indoors or outdoors, with large doors wide open to the view. To maintain indoor thermal comfort and block insects without sacrificing the open-air feel, contractor Bruce Botchick of 72 Degrees Heating, recommended Berner’s Architectural Elite air curtains. Intentionally designed for customer-facing applications, these quiet and effective air curtains span the large doorways, ensuring conditioned air stays inside, insects stay out, and energy bills stay down.
The energy savings from the air curtains have been a gamechanger for Chagrin Tavern, allowing the restaurant to maintain its open, inviting atmosphere without a spike in energy costs. Guests enjoy the comfort of a climatecontrolled space, while the restaurant saves on energy bills—proving that an open-door policy doesn’t have to come with an expensive price tag.
The Berner Architectural Elite Air Curtains
Quiet, technologically advanced & beautifully designed for entrances where aesthetics matter AMCA Certified, meets the Vestibule Exception in ASHRAE 90.1. Made in USA
Challenge: In 2022, LS Electric received two large projects for Switchgear Systems with very short lead times.
Solution: LS went into overdrive in both of its U.S. and Korean divisions to meet the challenge—hiring additional engineers and expanding its subcontractor workforce.
ReSult: LS met the challenge head-on, and both large projects were completed on time.
SummaRy: In 2022, LS Electric achieved a major milestone by winning two significant project bids: a semiconductor fabrication plant in Texas and an EV battery manufacturing facility spanning Kentucky and Tennessee. These projects were valued at over $150 million and $100 million, respectively. LS Electric was tasked with delivering over 450 unit substations, including medium voltage (MV) switchgears, UL1558 and UL891 switchboards, MV cast resin transformers, and high voltage (HV) transformers, all within a tight delivery schedule. The scope of these projects exceeded the total amount of electrical equipment LS Electric had previously supplied to the U.S. market.
To meet this demand, LS Electric took several strategic actions. The company hired experienced engineers, diversified its subcontractor base, and maximized production capacity at its manufacturing facilities. These efforts were critical in meeting high client expectations and marked a turning point for the company.
Thanks to these efforts, LS Electric delivered all required switchgear and transformers on time. This accomplishment not only met customers’ needs but also established LS Electric’s reputation as a premier supplier of electrical equipment in the North American market, paving the way for future growth.
Challenge: Replacing a boiler in a wastewater treatment plant is difficult. If the thermal input to the city’s wastewater digesters falls below 85°F, the system can become septic.
Solution: Install a ClearFire® -CE condensing boiler for its exceptional operational efficiency, engineering flexibility, and reliable performance.
ReSult: The entire project, including demolition, was finished in just seven days, largely due to the retrofit-friendly design of the CFC-E. The hydronic systems were quickly restored, and the staff began raising the digester temperatures to the optimal 99°F. The system has operated safely, efficiently, and reliably.
SummaRy: At one wastewater treatment plant, a firebox-style boiler installed in 1999 began to fail due to a tube leak. City administrators decided it was time to replace the aging boiler with a more reliable and efficient solution.
Cole Industrial, Inc., based in Lynnwood, Washington, recommended the Cleaver-Brooks ClearFire® -CE (CFC-E) condensing hydronic boiler, which offers up to 99% efficiency and less than 20 ppm NOx emissions. The CFC-E’s design includes dual-temperature returns, maximizing operating efficiency across various system applications. With no flow limitations and fewer boiler design constraints, the system offers significant engineering flexibility.
The quick delivery of the CFC-E boiler and its engineering flexibility allowed the team to rapidly demolish the old system and deliver, install, and commission the new boiler. This swift action ensured that the wastewater digesters maintained thermal input before temperatures dropped below 85°F – a critical threshold where sewage-eating microbes begin to die, causing the system to become anoxic and septic.
Following startup, digester temperatures gradually increased to the optimal 99°F, and the system has been running efficiently and reliably ever since. The CFC-E’s hinged top assembly and simplified gas train make inspections and maintenance straightforward, while its duplex stainless-steel construction ensures durability and long-term performance.
Challenge: Improve ventilation in an airport concourse to increase thermal comfort while adding a distinctive look that accentuates the facility.
Solution: Two Greenheck DC-5 high volume low speed (HVLS) fans were installed to provide the necessary air movement to reduce air stratification and help regulate temperature in a large, open space.
ReSult: Airport management was pleased with the project results. In particular, the HVLS fan controls were very intuitive and easy to use, and the ability to use different colors for the fans allowed them to blend nicely with the concourse’s color scheme.
SummaRy: Central Wisconsin Airport (CWA) in Mosinee, Wisconsin is a busy regional airport offering travelers access to destinations worldwide. As more travelers use the airport, the need to provide for their comfort grows, prompting the airport to address increasing complaints about thermal comfort in the concourse.
The CWA concourse is a very large, open space with high ceilings and significant use of glass window walls. However, the large space is susceptible to uneven temperatures affecting thermal comfort. Adequate circulation also was a challenge, adding to the discomfort for travelers waiting to board flights.
CWA updated the 20-year-old HVAC system in the concourse area but uneven temperatures still caused thermal discomfort. Greenheck’s DC-5 HVLS fans addressed this issue. The two DC-5 fans with eight-foot airfoils reduced air stratification, providing thermal comfort by gently moving air in the space with a maximum of 29,000 cfm. The DC-5 is licensed to bear the AMCA seal for Circulating Fan Performance and weighs less than 100 pounds allowing for easy installation. Aesthetics were another important consideration. With finish options for every portion of the fan (winglet, airfoil, downtube, hub plate, and universal ceiling mount), the DC-5 fans complemented the remodeled interior.
CLICk or scan QR to read the full case study.
www.greenheck.com
Cummins
Cummins
Greenheck Corporation
Greenheck Corporation
Hammond Power Solutions
Inaba Denko America
International Exposition Co
Lennox Industries
LS Electric America, Inc
LS Electric America, Inc
Metraflex
Miura North America, Inc
Noritz .
Pentair Flow Technologies
Pentair Flow Technologies
Pritchard Brown .
Regal Rexnord
Regal Rexnord
Tjernlund Products, Inc
Uline .
Yaskawa America Inc .
.53
.49
.C-2
.15
.C-4
.cleaverbrooks .com
.greenheck .com
.hammondpowersolutions .com
.inabadenko-america .com
.www .lennox .com
www .lselectricamerica .com
.www .lselectricamerica .com
.metraflex .com/VFD
.www .miuraboiler .com
.www .noritz .com/commercial
.www .pentair .com
.www .pentair .com
.www .pritchardbrown .com
.www .regalrexnord .com
.www .regalrexnord .com
.www .tjernlund .com
.www .uline .com
.www .yaskawa .com
VP, Sales
Matt Waddell
Sales Account Manager
MWaddell@WTWHMedia.com 312-961-6840
Brian Gross BGross@WTWHMedia.com 847-946-3668
Sales Account Manager
Richard Groth RGroth@WTWHMedia.com 774-277-7266
Sales Account Manager
Robert Levinger RLevinger@WTWHMedia.com 516-209-8587
Sales Account Manager
Judy Pinsel 847-624-8418 JPinsel@WTWHMedia.com
Patrick Lynch, Senior Vice President, Sales & Strategy 847-452-1191, PLynch@WTWHMedia.com
McKenzie Burns, Marketing Manager MBurns@WTWHmedia.com
Courtney New, Program Manager, Content Studio CNew@WTWHMedia.com
Paul Brouch, Operations Manager 708-743-5278, PBrouch@WTWHMedia.com
Rick Ellis, Director, Audience Growth 303-246-1250, REllis@WTWHMedia.com
Custom reprints, print/electronic: Paul Brouch, PBrouch@WTWHMedia.com
Information: For a Media Kit or Editorial Calendar, go to https://www.csemag.com/advertise-with-us.
Letters to the editor: Please email us your opinions to ARozgus@WTWHMedia.com. Letters should include name, company and contact details, and may be edited.
Whether you operate a large health system, stand-alone clinic or anything in between, Carrier is your single partner for a full suite of solutions designed to create healthy, safe, sustainable and intelligent healthcare environments.
Connect with a Carrier Strategic Account Manager or visit carrier.com/healthcare for experience and solutions that benefit your staff, patients and planet.
External events influencing power quality can interrupt equipment and cause failure of electrical components. A lack of redundancy potentially puts patient care at risk. For example, a lightning strike or even a planned generator test could interrupt delivery of critical air to an operating room.
Our HV600 Redundant VFD Solutions help to insure that these external events are one less thing to worry about. They provide seamless automatic switchover during the primary failure of any fan, pump, chiller, or cooling tower application.
Yaskawa has over 35 years experience in delivering quality HVAC VFD solutions and our products are built in U.S.A.
Want to learn how Yaskawa benefits healthcare? Call us today.