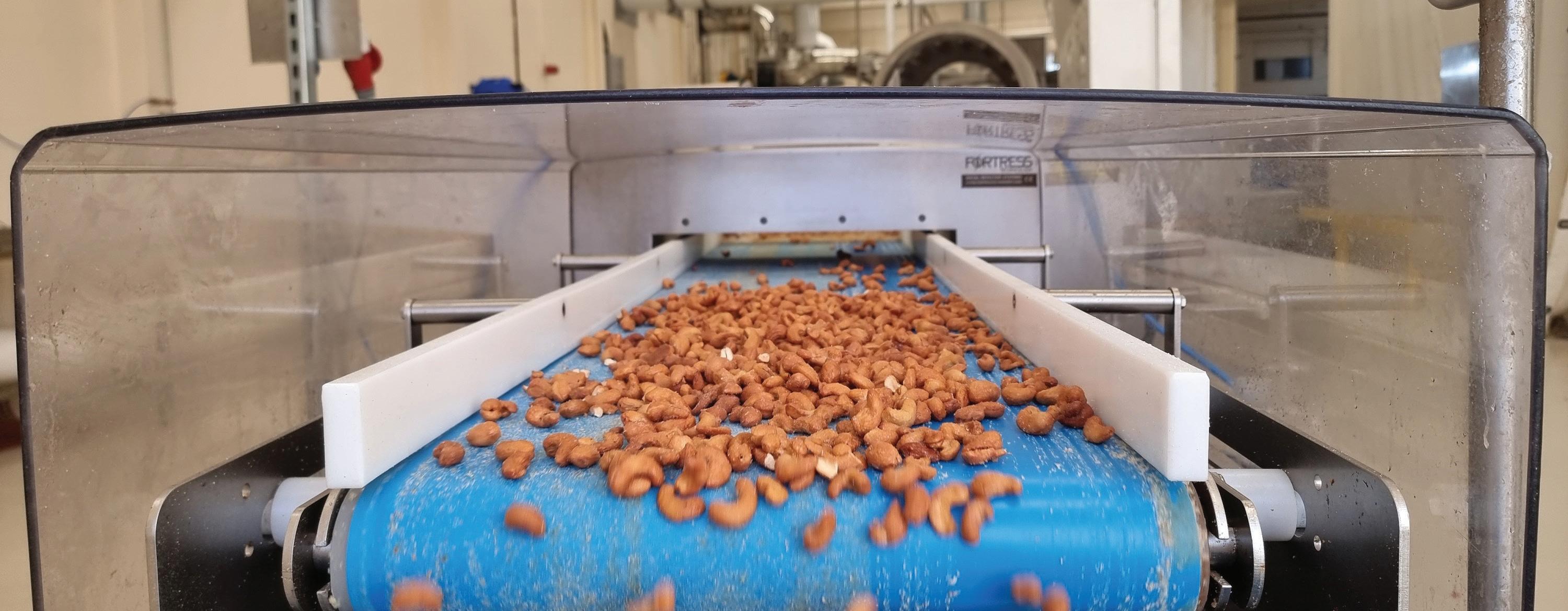
2 minute read
Metal detector integrated with conveyor ensures safer food
Fortress Technology’s supermarket-spec metal detector is sensitive enough to adapt to the fine oil and sugar tolerances on the honey roast nut line.
Most snack producers opt for gravity metal detectors. With 15 Fortress Vertex snack inspection systems integrated with multi-head weighers in its Liverpool factory, global nut supplier Trigon Snacks is no exception. Yet, for its latest coated honey roast nut production line, the sustainable nut specialist selected a custom linear Stealth metal detector with an innovative retractable conveyor reject system.
Processing 7,000 tons of nuts annually from its British Retail Consortium A-grade and RSPO certified facility, Trigon Snacks supplies a wide range of nuts and snacks to the licensed trade, retailers, and food service operators. Marketed under its own brands, and retailer own-labels, for its new honey roasted nuts line the company commissioned a highly sensitive conveyorstyle metal detection concept to ensure compliance with global retailer and regulatory standards.
Stringent retailer COPs specified that as “naked nuts” the new honeycoated range must be inspected for metal contaminants prior to own-label packaging. Additionally, Trigon required a supermarket spec metal detector that was sensitive enough to adapt to the fine oil and sugar tolerances and meet the regulatory requirements of every geographical market they are sold in.
For logistical reasons, a small-footprint, wide-head Fortress Stealth metal detector engineered to inspect the fried, dried, and seasoned nuts on a conveyor before entering the chute and falling into the one-ton sacks, was the most viable and accessible option.
Screening 32 tons of honey roasted nuts daily, space limitations were a key driver to the design, said the company’s lead engineer Mark Grieve. “Being located on a mezzanine floor, we commissioned a wide head yet highly sensitive metal detector with a specially adapted linear conveyor system measuring just 40 cm wide.”
Factoring in the conveying and reject system was critical to guarantee reliable operation and avoid false readings. Given the tight footprint, a custom solution was the best way to ensure that metal detector performance was not compromised.
The low-profile nuts combined with the inspection speed meant that a kicker would be incompatible. It is also virtually impossible to isolate and divert contaminated products with naked products. With insufficient space to accommodate a flap style reject, Fortress instead engineered a clever and efficient retracting band conveyor and reject mechanism.
The metal detector which sits at the front of the conveyor calculates precisely how long any contaminated nuts will take to reach the end of the conveyor band, communicating via the metal detector control system. The belt then smoothly retracts back on a sliding rail rolling the rejected nuts into the dedicated bin located beneath the conveyor, resuming its inspection position in just seconds.
To-date, Trigon reports zero false rejects on its new honey roasted nut line, upholding the company’s longstanding sustainable, ethical, and traceable principles. Despite admitting he was slightly apprehensive by the compact dimensions of the entire system, Mark corroborates that it has already proved itself to be a reliable and easy to use machine.
Hourly manual tests are the only reported source of daily waste. The lead engineer estimates this to be less than 0.05% of the total production, well below the food manufacturing average which on some lines can reach double figures.
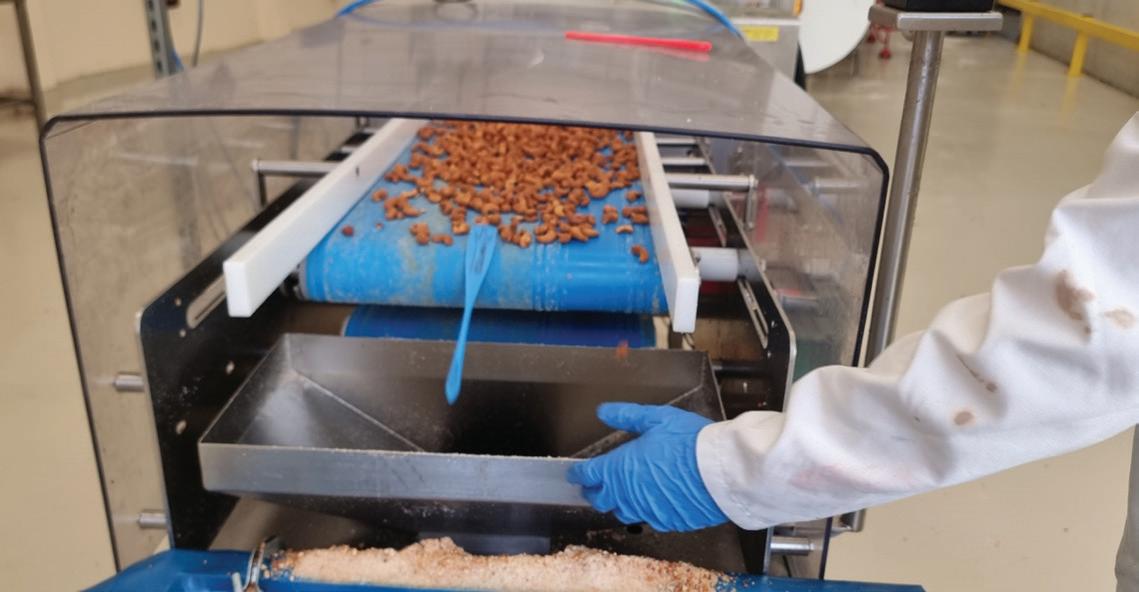
From a sensitivity perspective, the metal detector is exceeding expectations identifying ferrous and non-ferrous particles smaller than 1.0 mm and stainless-steel particles under 1.5 mm. This level of sensitivity can be attributed to the low-profile metal detector head.
Affirming the importance of customizing the aperture, Eric Garr, North America Regional Sales Manager commented: “Aperture size is critical to optimal operation. Customizing the aperture around the product being inspected is one way to ensure the metal detector will perform to optimal levels. Additionally, integrating a conveyor system, fully assembled and checked, is another failsafe way of making sure a producers’ stringent sensitivity requirements are not compromised.” DW
Fortress Technology | www.fortresstechnology.com