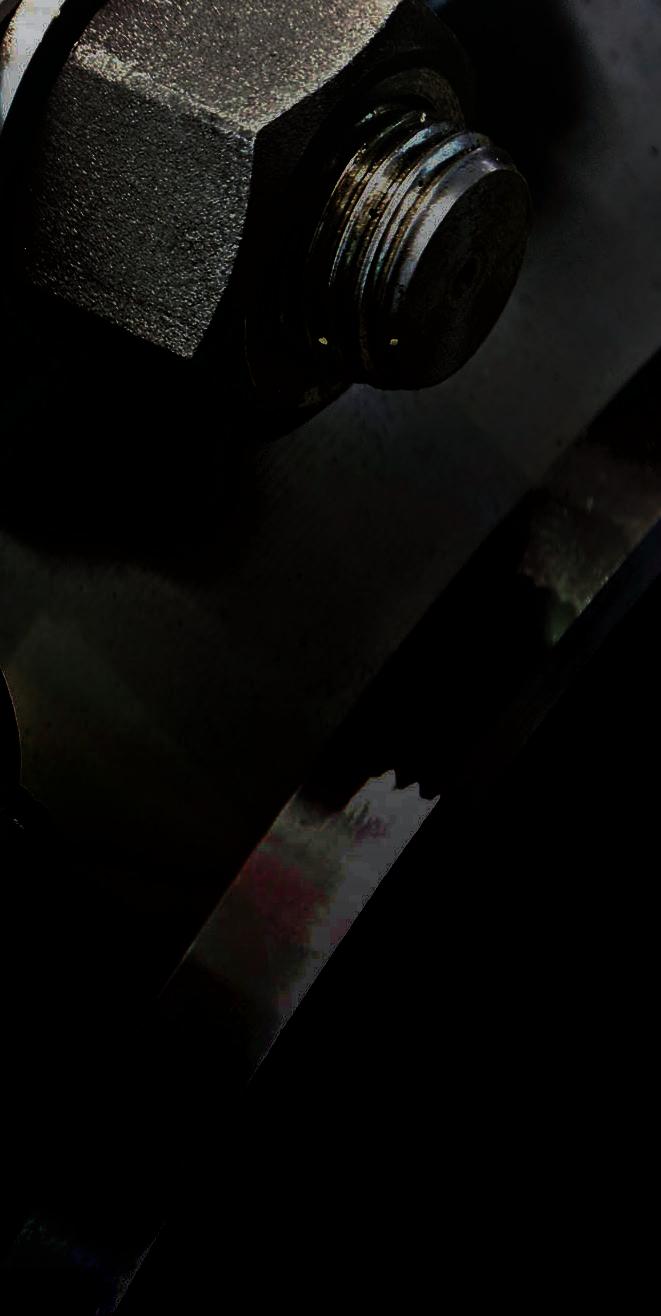
2 minute read
Fastener Engineering
This area has long been one of the most read and sought after by our engineering audience! From screws to bolts and adhesives to springs, these critical but often overlooked components are the key to every successful design.

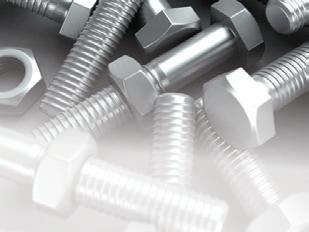
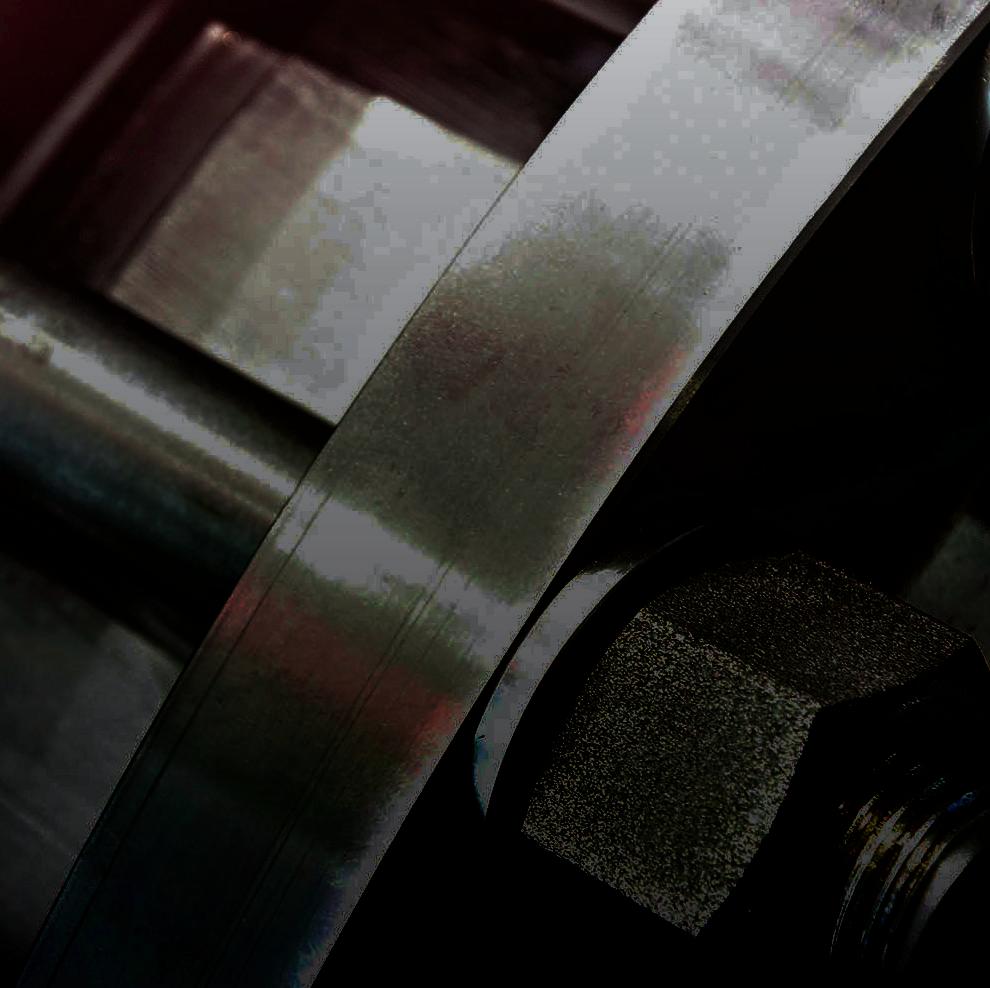
FastenerEngineering.com will serve readers in the mechanical design engineering space, providing news, product developments, application stories, technical how-to articles, and analysis of engineering trends. This site will focus on key issues facing the engineering markets around fastener technology, along with technical background on selected components.
ADDITIONAL RESOURCES:
• Special print section in select issues of Design World
• Fastener Engineering monthly newsletter
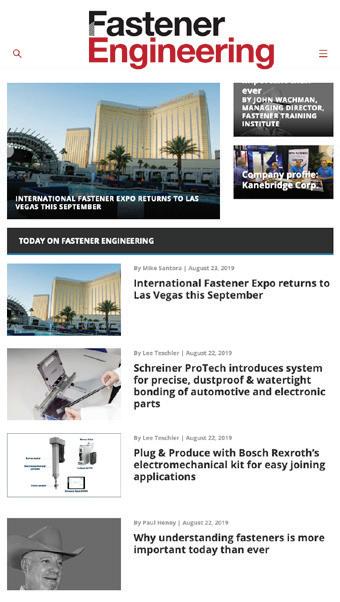
Motion Control
Power density plays an important role in applications with limited available space and a high power requirement, such as drones and quadcopters.
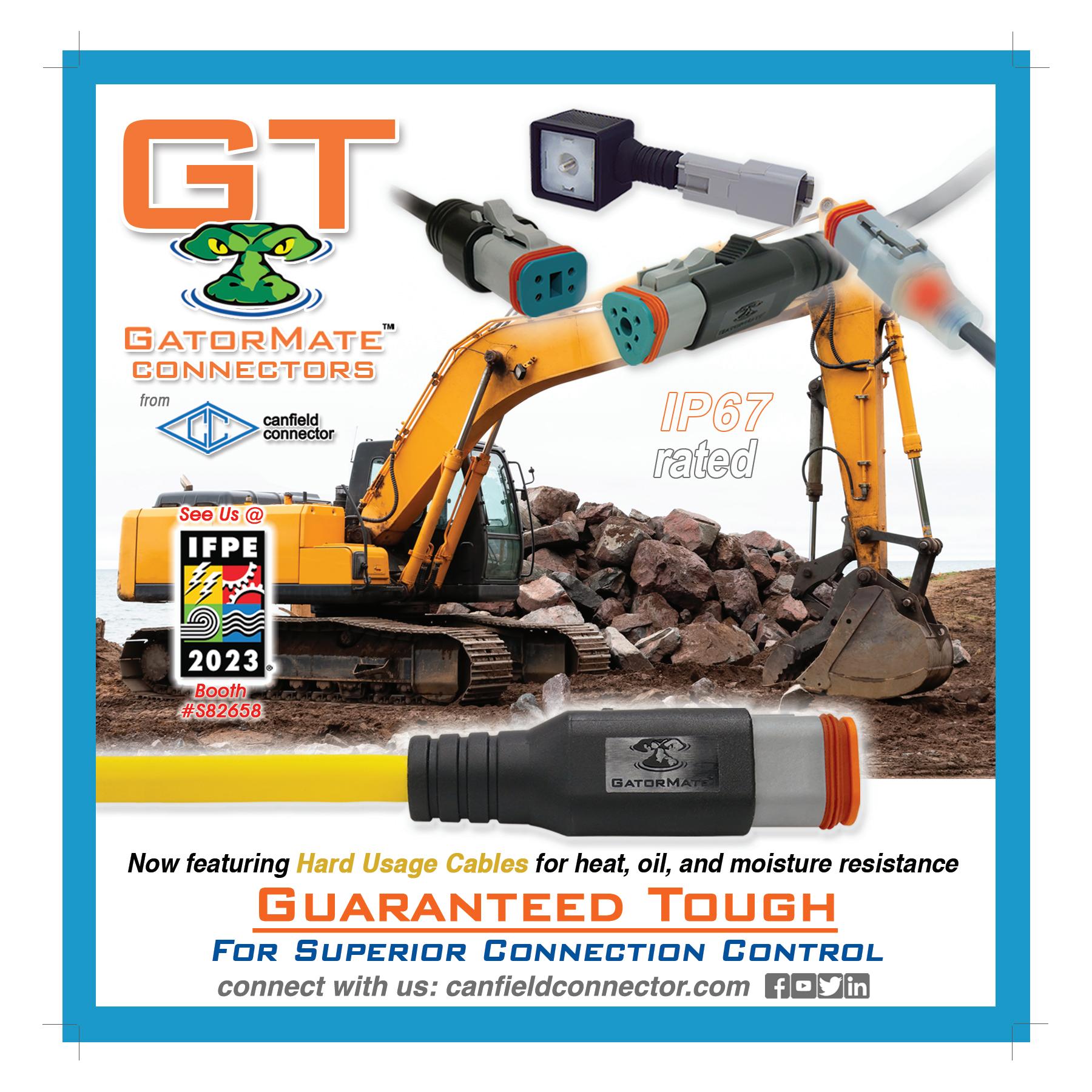
Temperature rise comparison
As mentioned previously, constant current operation for the stepper motor leads to major energy losses in the windings, mainly in the form of heat. During the experiment, the motors’ body temperature was measured in an ambient temperature of 22°C.
The stepper motor’s temperature rises steadily regardless of the load on the shaft. In comparison, the brushless dc motor’s ability to not draw excessive current means the body temperature only increases minimally. Unlike stepper motors, BLDCs convert a high percentage of input power into mechanical power instead of heat.
Acceleration and noise comparison
The high pole count of steppers is directly responsible for their superior positional accuracy over BLDCs. However, the high pole count also results in limited acceleration and more audible noise during operation. Accelerating a stepper motor can be difficult because it requires a gradual ramping of motor speed to sustain the shaft’s angular positional accuracy. If a stepper accelerates quickly, then it faces the risk of missing steps, which can cause issues in many applications. In addition, if there is low input current combined with high acceleration demand, then the stepper may stall.
In terms of noise, brushless dc and stepper motors can detect a particular torque, otherwise known as cogging torque, which causes vibrations and ringing at every step of the stepper motor rotation. Because the BLDC current draw is proportional to the load on the shaft, BLDCs can draw the additional current required to accelerate the load within the motor’s rated speed range. BLDCs are much quieter during normal operation than steppers. Therefore, BLDC motors are reliable and efficient solutions that offer high speed, high acceleration, and less audible noise.
Conclusion
While the positional accuracy of BLDC motors is proportional to the angle sensor accuracy, integrated BLDC motors with a high-resolution angle sensor can offer exceptional positional accuracy. With microstepping, stepper motors offer superior positional accuracy over brushless dc motors. This comes with the disadvantage of offering less torque beginning from mid-range speeds, which lead to missing steps or stalling. Steppers lack the ability to quickly accelerate, and they produce more noise than BLDCs. Overall, stepper motors are a less expensive solution, but they are limited to lowspeed applications. BLDC motors are dependable, quieter solutions that offer higher efficiency and accuracy across a wide speed range. DW