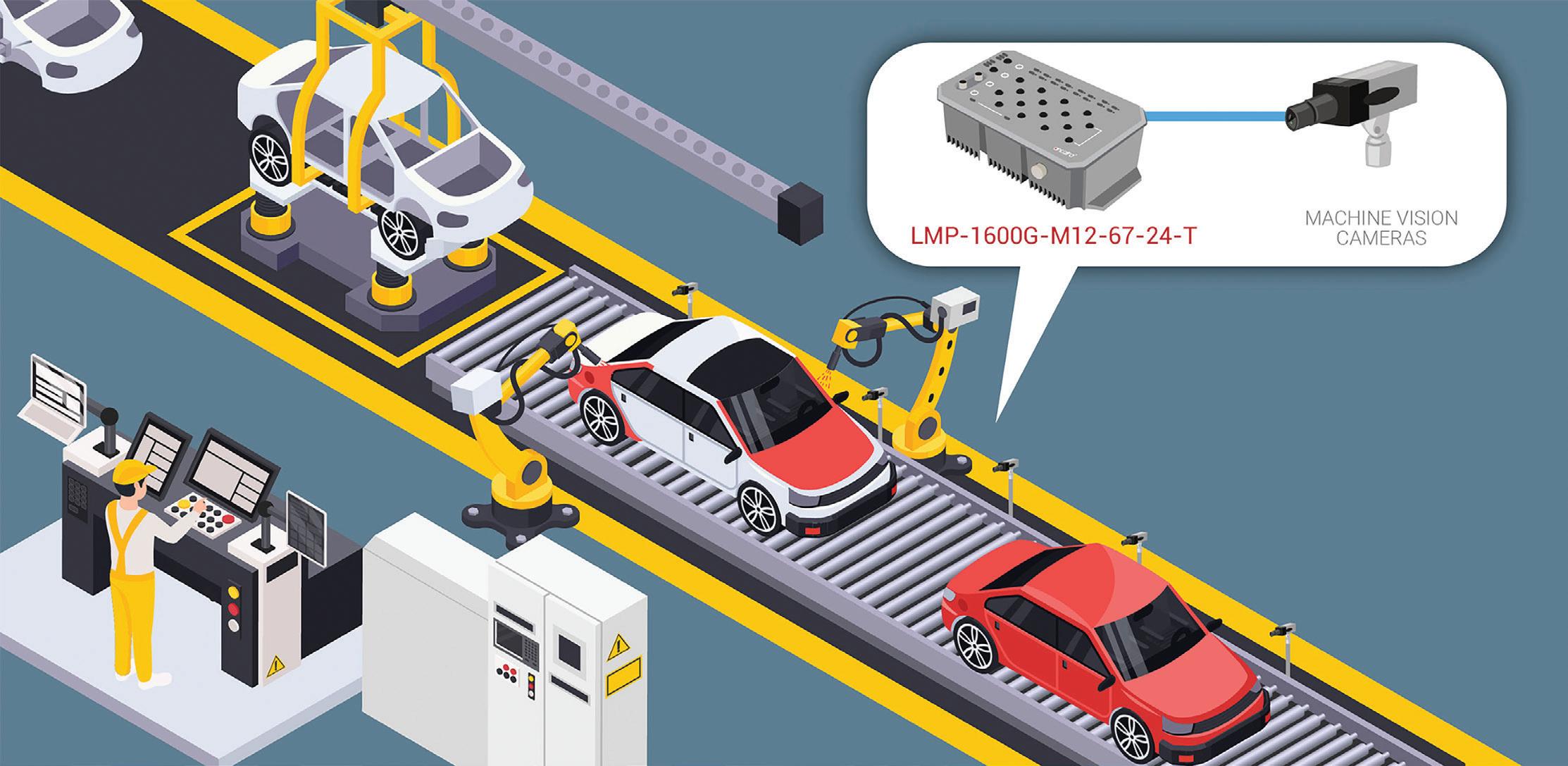
2 minute read
Design for Industry
Material handling
Machine Vision is becoming much more critical in automation applications, especially where robotics is involved. GigE Vision is a global standard communication protocol that has been adopted by machine vision camera manufacturers. Illustration courtesy of Antaira
Ethernet switches make it easier for vision robots to take on material handling tasks
As robots are increasingly used in various material handling processes, more users are finding that the addition of vision to these robots is enhancing and expanding their capabilities. Vision Guided Robot (VGR) technology has advanced beyond the early days of programmable transfer machines thanks to advances in 2D and 3D cameras, visual servo control, embedded Ethernet networks, and increasingly more sophisticated software including AI.
Advances in RGBD cameras — composed of a standard RGB camera and a depth sensor — have received considerable attention lately because of their ability to quickly acquire 3D models of the environment and to estimate the camera pose in a low-cost way.
Empowering a robot to “see” allows it to precisely and consistently differentiate, pick, sort, move, weld or assemble various parts no matter their complexity. For instance, a multiple-step manual welding task on an automobile assembly line might take ten “blind” robots to perform since each part must be mounted in place before every weld. However, this same multi-step welding process can be done with a single VGR, since its camera can precisely align the different parts in place without human assistance.
Flexibility is another huge benefit of VGRs. As with a machine vision system on an assembly line, a VGR uses intelligent processing to give it instructions. A slight alteration to the code allows the same robot to perform entirely different tasks, i.e., switching between products and batch runs, with no mechanical adjustments.
And then there is safety. With VGRs, factories can significantly reduce the risk of on-site accidents. A vision- guided forklift inside a warehouse, for example, will sense obstructions along its pre-programmed paths and avoid contact with people or objects while precisely selecting items o pallets to meet customer orders. At Amazon, for instance, robotic material handling “cobots” (collaborative robots) safely work directly alongside humans. The Amazon Sparrow robot uses vision and a robotic arm and is able to pick up a new item and deposit it on a metal chute every three seconds, handling more than 1,000 items per hour.
To add vision to a robot, one or more cameras are needed. One is mounted on the robotic arm, serving as the machine’s eye. Other cameras are installed in strategic locations in the working cell to capture more visual data. Adding these static cameras will compensate for the limitations of the arm-mounted camera. Careful attention must be given to ensure the camera and lens has the proper resolution, frame rate, and depth-of- field required for the application at an acceptable cost. Low-cost GigE Vision cameras are preferred since they use standardized, o -the-shelf Ethernet cables and components, while eliminating the need for frame grabbers.
A major trend today is to purchase VGRs already equipped with a vision system supplied by the robot manufacturer. This translates into faster adaptation into a production line, lower costs, and more responsive technical support from a single manufacturer.
Whether the vision system is installed by the end-user or the OEM, it will require an industrial Ethernet switch to create an embedded Ethernet network within the robot. Ethernet allows the individual robot parts to communicate with each other and is suitable for VGRs because Ethernet can handle image data. High port-count Industrial Gigabit Ethernet switches for robots can make the networking of Ethernet nodes uncomplicated.
Space inside a robot is always a limiting factor. A compact DIN-rail design