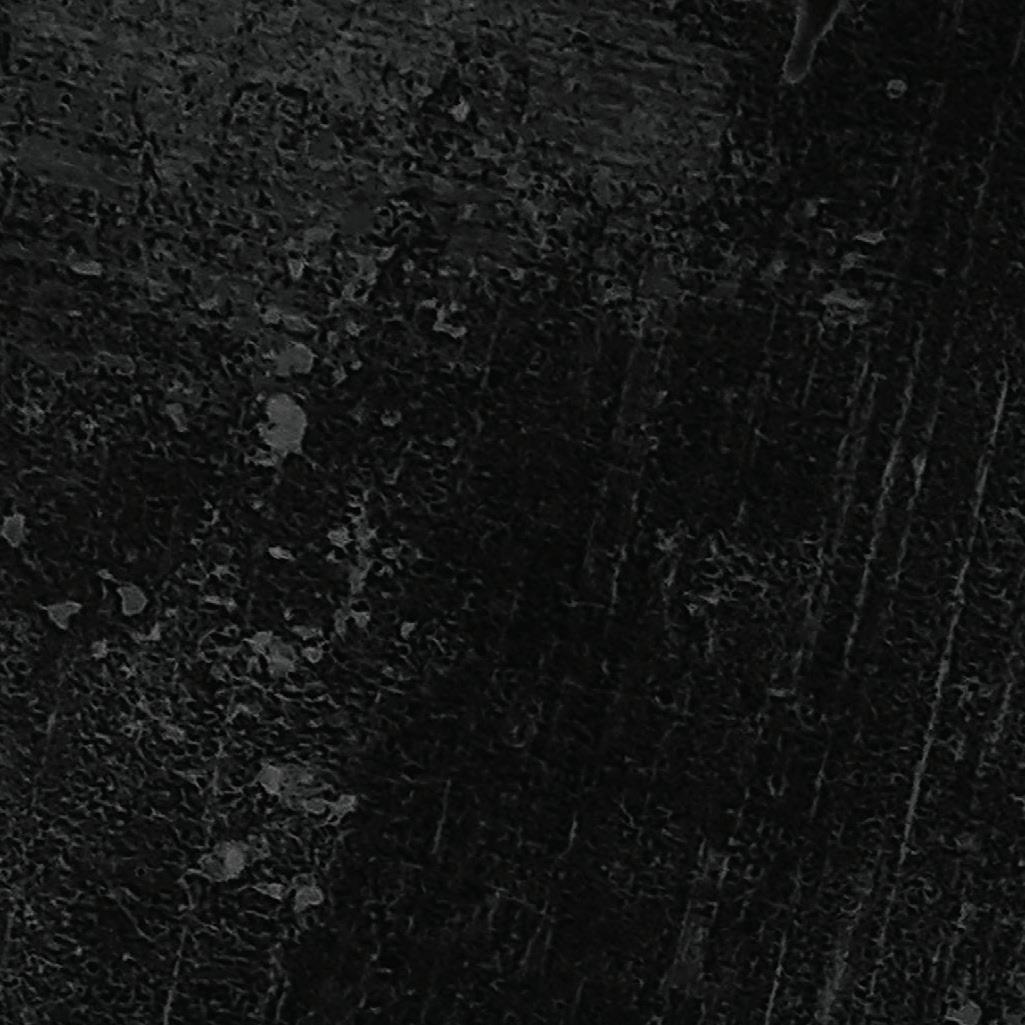
2 minute read
Jabil looks into the future of additive manufacturing
Jabil Inc. offers a forecast of five additive manufacturing trends that will continue to accelerate innovations this year.
According to a recent report from Grand View Research, the additive manufacturing market is projected to reach $76B by 2030, growing at a CAGR of 20.8% over the forecasted period. Aggressive market expansion is attributed in part to increased adoption of additive manufacturing in industrial applications and sustained momentum in incumbent industry segments, including automotive, healthcare, and aerospace and defense.
Here are five additive manufacturing predictions that Jesse Sumstad, senior product manager, Jabil Additive, sees as the additive manufacturing continues to mature.
1. Sustainable materials are having a moment. Increased demand for environmentally friendly materials is growing rapidly as companies seek more sustainable solutions to reduce raw materials, waste and carbon footprints. Moreover, regulatory pressures to recycle and repurpose plastic waste for 3D printing applications continues to gather momentum, especially in Europe where plastic waste pollution is being tackled on multiple levels. Equally important, the trend for bio-based and bio-compatible materials used in packaging and other traditional manufacturing applications is transitioning to the additive market. Examples include Jabil’s low-carbon PK 5000 and formaldehyde-free PA 0600.
2. Additive manufacturing processes need to be ecofriendly. While a lot of focus is on the development of sustainable, recyclable materials, expect to see this broaden to encompass demands for more eco-friendly processes and 3D printing platforms. Technical feasibility and research into more sustainable processes and machine platforms need to be addressed over the next 12-to-18 months as part of all-encompassing circular economy initiatives.
3. The industrialization of AM continues. Over the past year, additive manufacturing has seen an uptick in volume serial production of final parts. While prototyping and tooling still rank high on the list of AM applications, it’s clear that the production of end-use parts is growing, along with the availability of rigorous manufacturing processes and Quality Management Systems
(QMS) to ensure the highest levels of part reliability, resiliency and robustness. Future expansion is forecasted, especially for applications where Design for Additive Manufacturing (DfAM) is being used to design parts. Additionally, as the costs of additive manufacturing continue to come down, the ability to compete with injection molding increases, resulting in more viable uses for AM to manufacture end-use parts.
4. Applications are propelling pellet printers forward. Interest in pellet printers is growing alongside the availability of pellet-based materials for making large parts based on the favorable economics of this type of 3D printing. Continued expansion in this area is on the horizon, particularly for applications involving large-scale castings and patterns.
5. Custom materials nearing a heyday:
The push is on for custom materials as companies recognize opportunities to achieve extra ductility, flexibility, and agility with materials tailored for specific applications. In particular, growing interest in polyketone-based materials is being driven by the need for high degrees of impact strength while being resistant to most fuels and fuel additives. As a result, this type of engineered material is ideally suited for fuel-tank applications.
An additive manufacturing pioneer and manufacturing powerhouse, Jabil has supported market growth through its materials, processes and machines.
“As serial production becomes more viable and mainstream, we need to take a holistic view of the end-to-end part production ecosystem,” said Sumstad. “All the factors that impact success — from design for additive and the use of engineered materials to post-processing methods and cost of labor — must be part of the overall decision-making process.” DW
Jabil | www.jabil.com
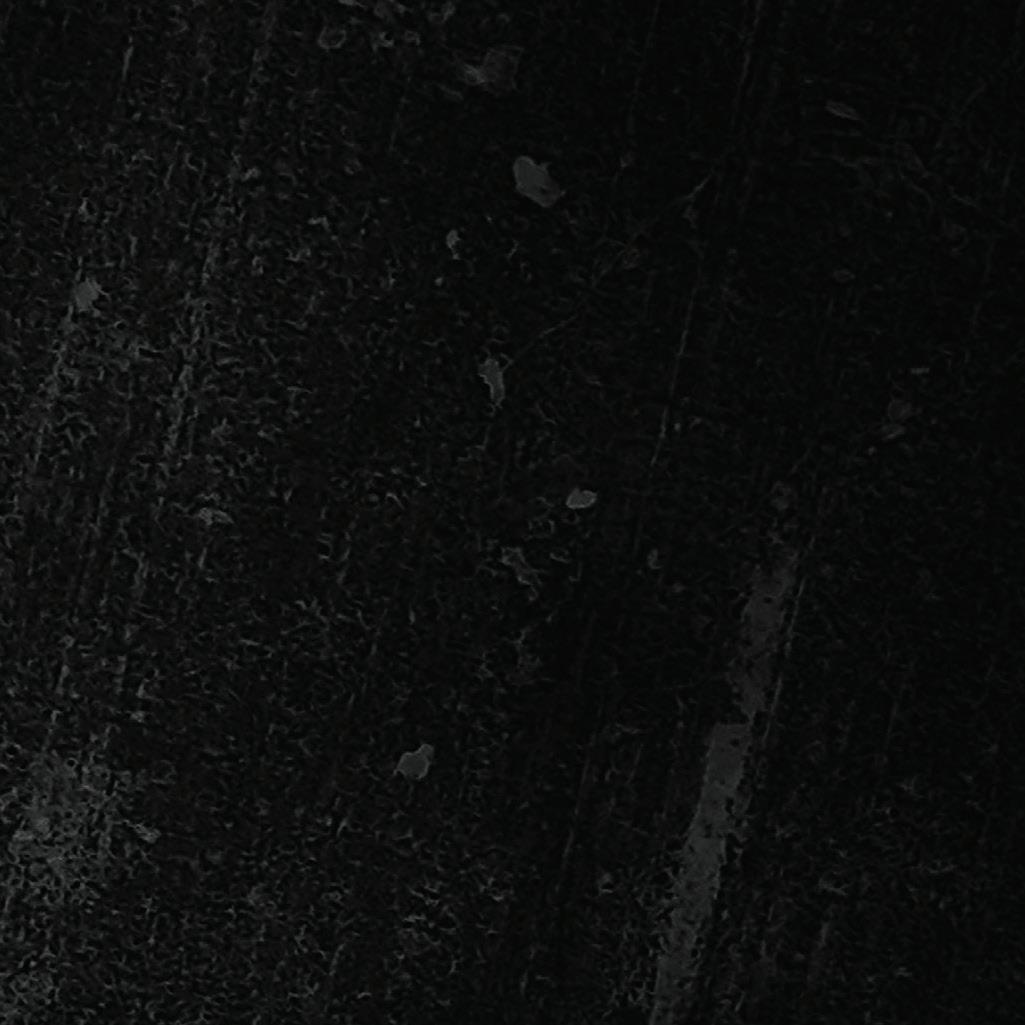

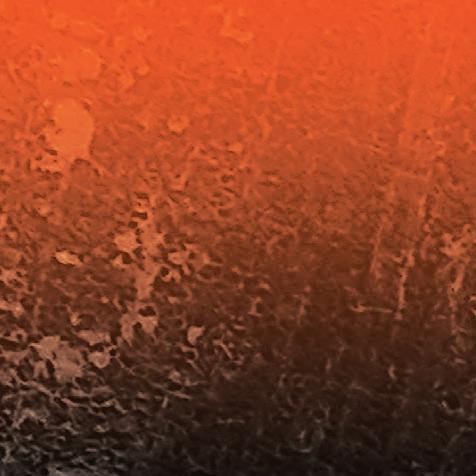
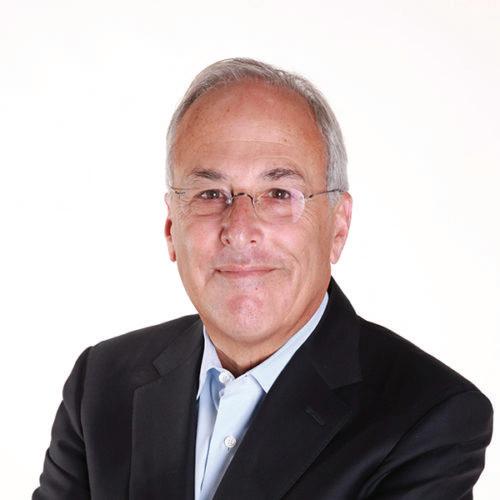
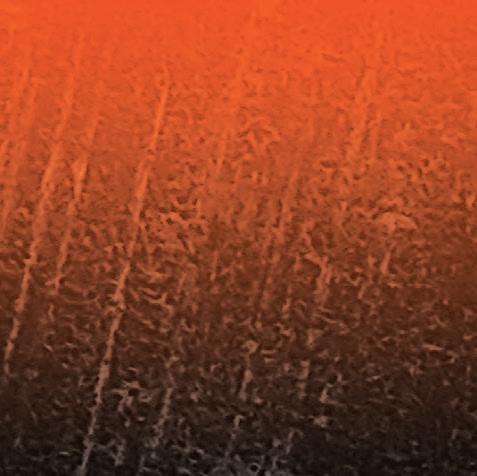
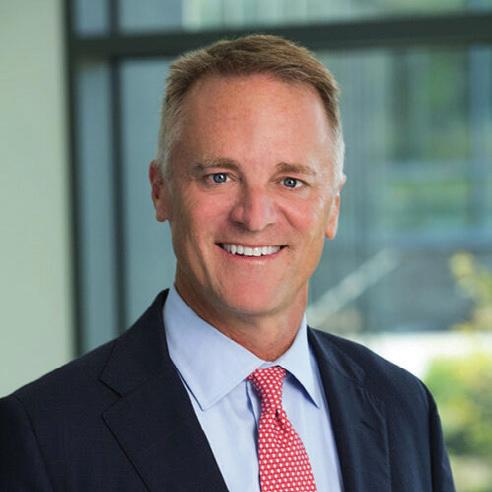

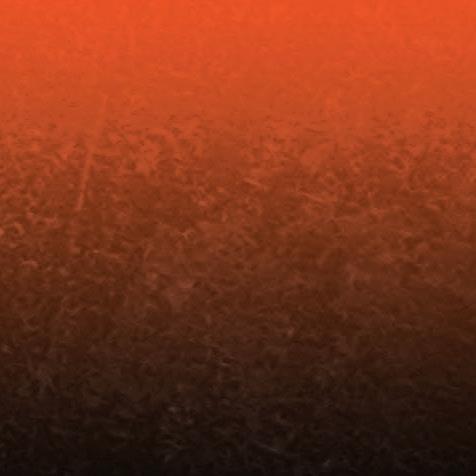

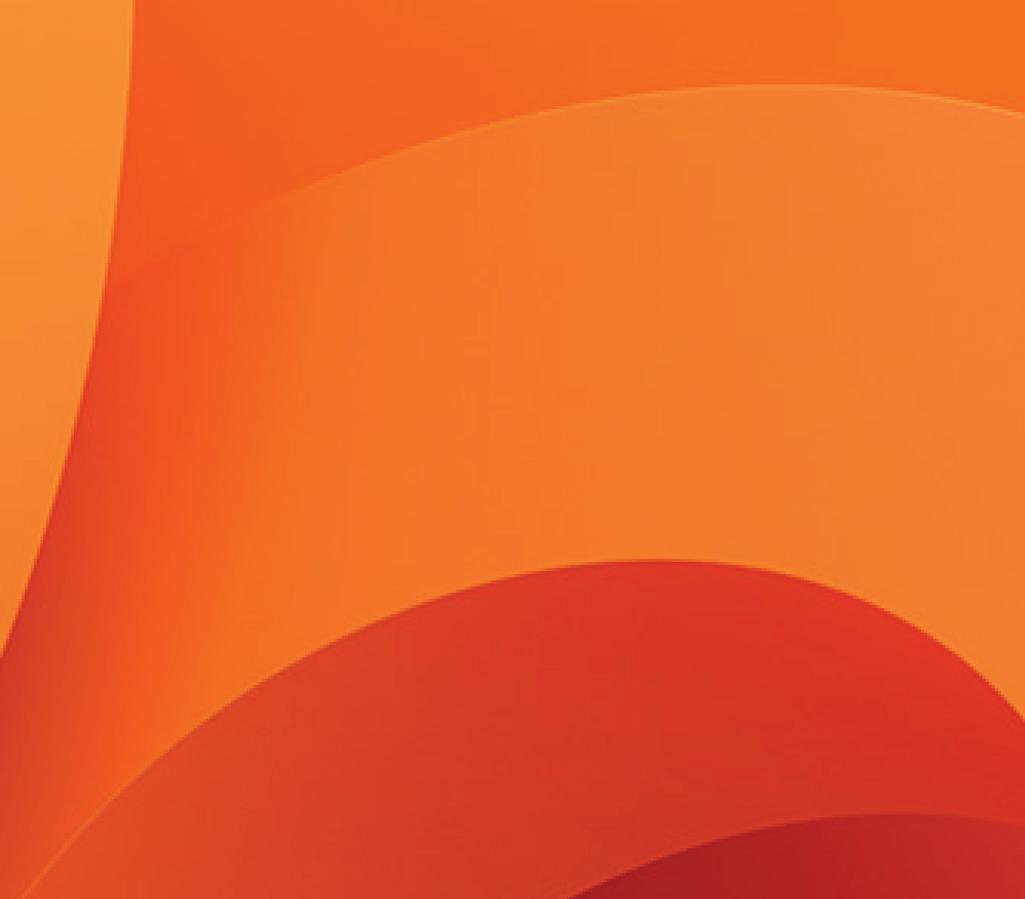
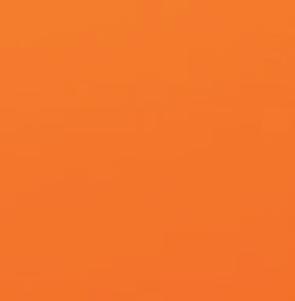
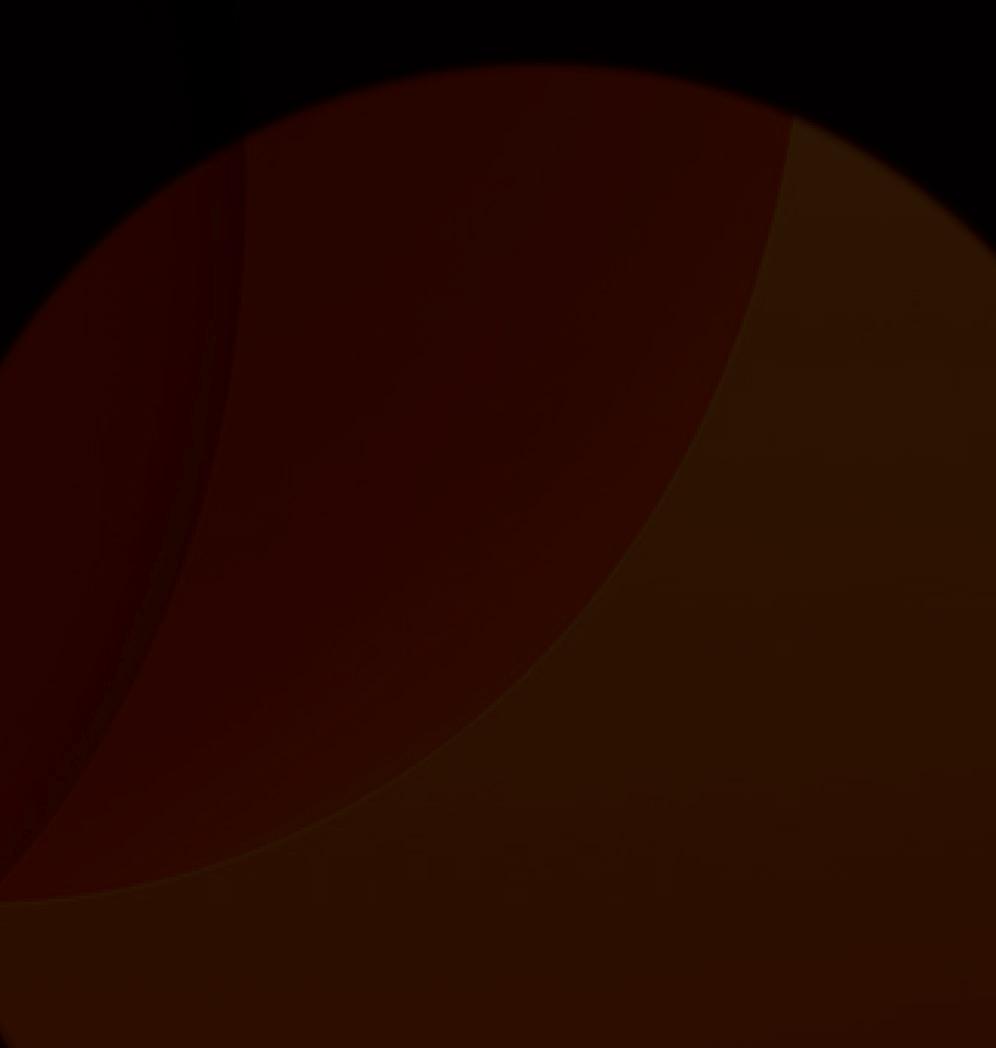
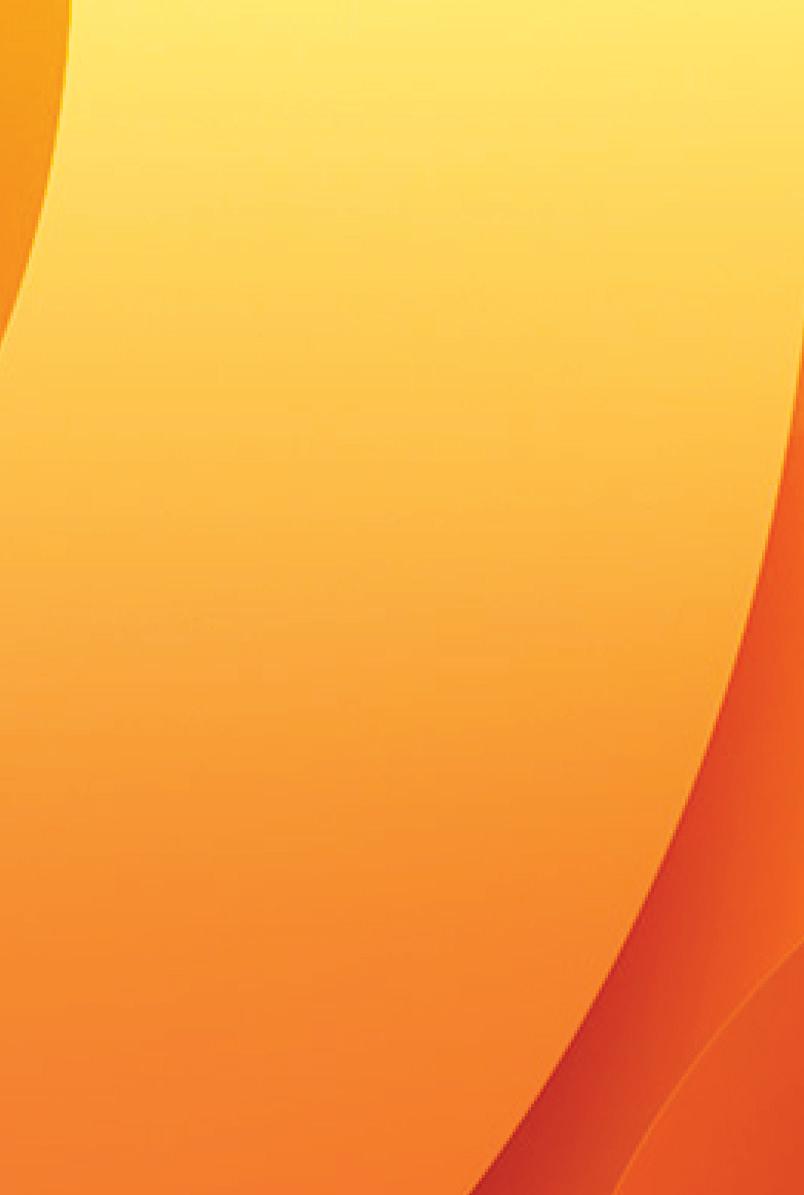
