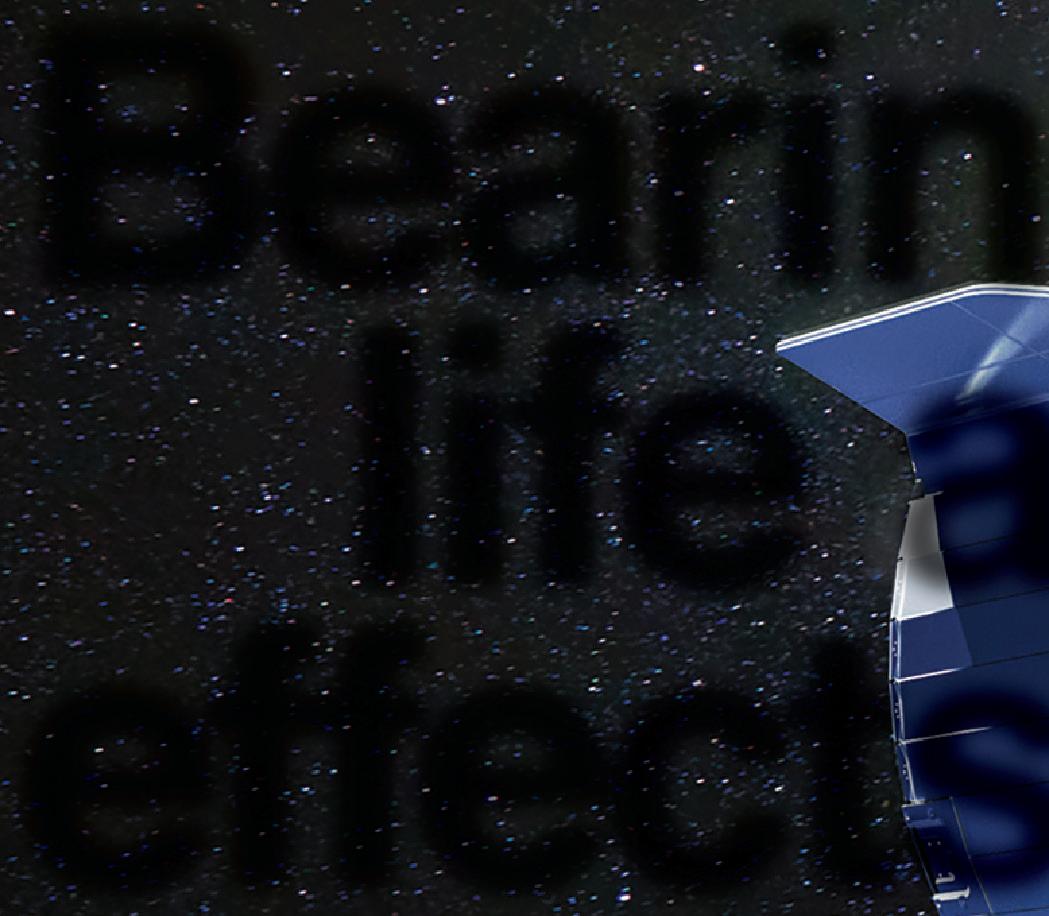
6 minute read
MECHANICAL
M e c h a n i c a l • • • • • • • • • • • • • • • • • • • • • • • • • • • • • • • • • • • • • • • • • • • • • • • • • • • • • • • • • • • • • • • • • • • • • • • • • • • • • • • • • • • • • • • • • • • • • • • • • • • • • • • • • • • • • • • • • • • • • • • • • • • • • • • • • • • • • • • • • • • • • • • • • • • • • • • • • • • • • • • • • • • • • • • • • • • • • • • • • • • • • • • • • • • • • • • • • • • • • • • • • • • • • • • • • • • • • • • • • • • • • • • • •
Bearing life and effects
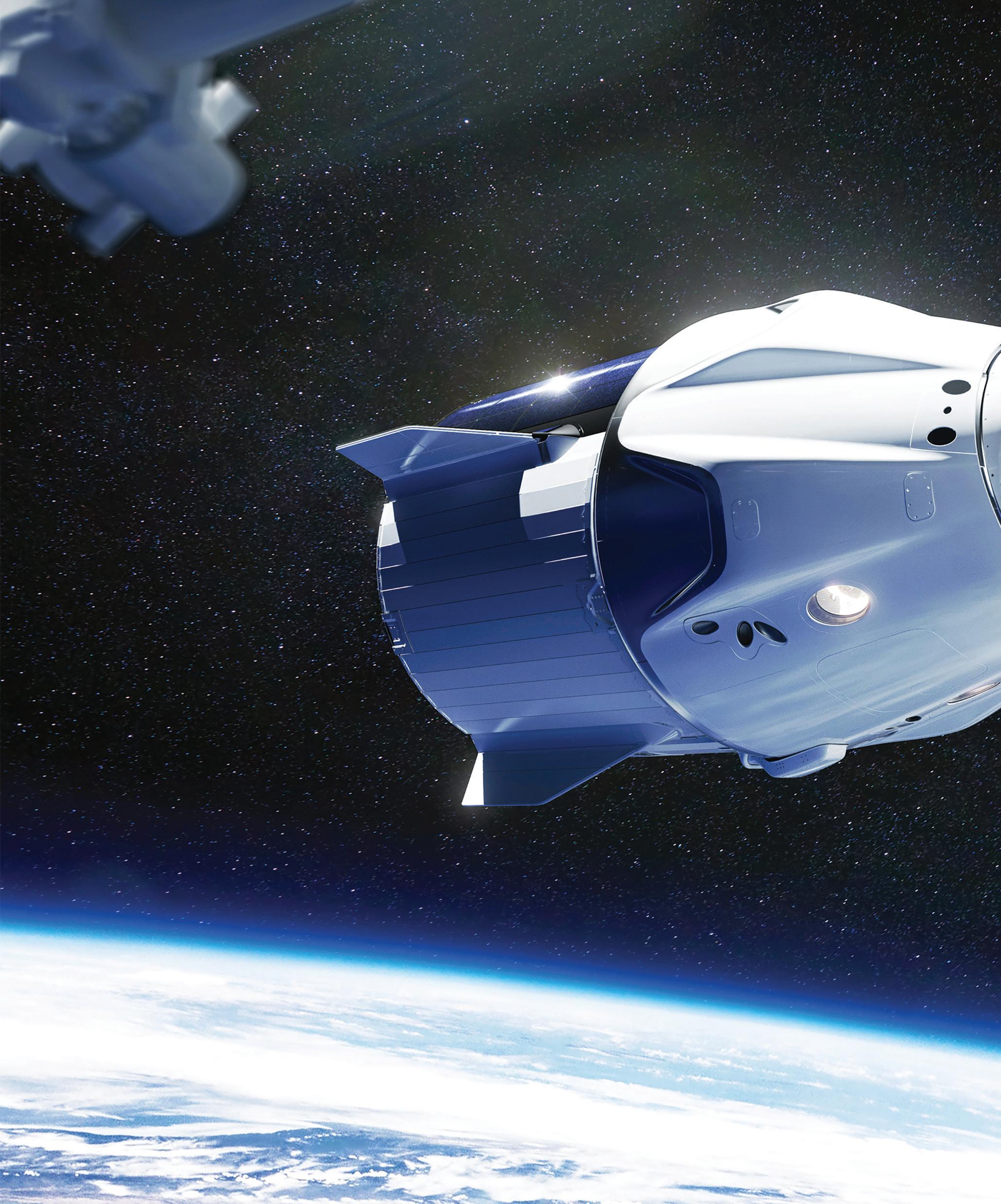
of harsh operational environments
Edited by Mike Santora
Manufacturers in nearly every industry are increasingly raising performance expectations for rollingelement bearings while at the same time exposing them to operating and environmental conditions that, when extreme, can reduce the rating life by as much as 90%.
SpaceX Crew Dragon spacecraft docking to the International Space Station.
Bearing life, explained
Under typical operating conditions, the inner and outer rings and rolling elements are constantly loaded and unloaded when bearings rotate. This produces material fatigue and eventually bearing failure. Statistically, the total number of revolutions reached or exceeded by 90% of a sufficiently large group of apparently identical bearings before the first evidence of material fatigue is called the basic rating life.
Manufacturers of ball bearings typically publish Load Ratings for each bearing they produce. The methods used to calculate ratings can vary from manufacturer to manufacturer. However, both ABMA and ISO have published standards related to load ratings.
• ABMA Std. 9 – Load Ratings and Fatigue Life for Ball Bearings • ABMA Std. 12.1 and 12.2 – Instrument Ball Bearings • ISO 76 – Static Load Ratings • ISO 281 – Dynamic Load Ratings and Rating Life
Dynamic load ratings are determined by bearing geometry, number and size of balls, bearing pitch diameter, and ring and ball material. This load rating is used in conjunction with the actual applied radial load to calculate bearing fatigue life.
The static load rating relates to limiting loads applied to non-rotating bearings. The static load rating depends on the maximum contact stress between the balls and either of the two raceways. It is affected by material, number and size of balls, raceway curvatures, raceway depths, and contact angles. It is also based on using clean, high-quality bearing steel with typical hardness levels of 58-64 Hardness Rockwell C (HRC) for rings and 60-65 HRC for balls.
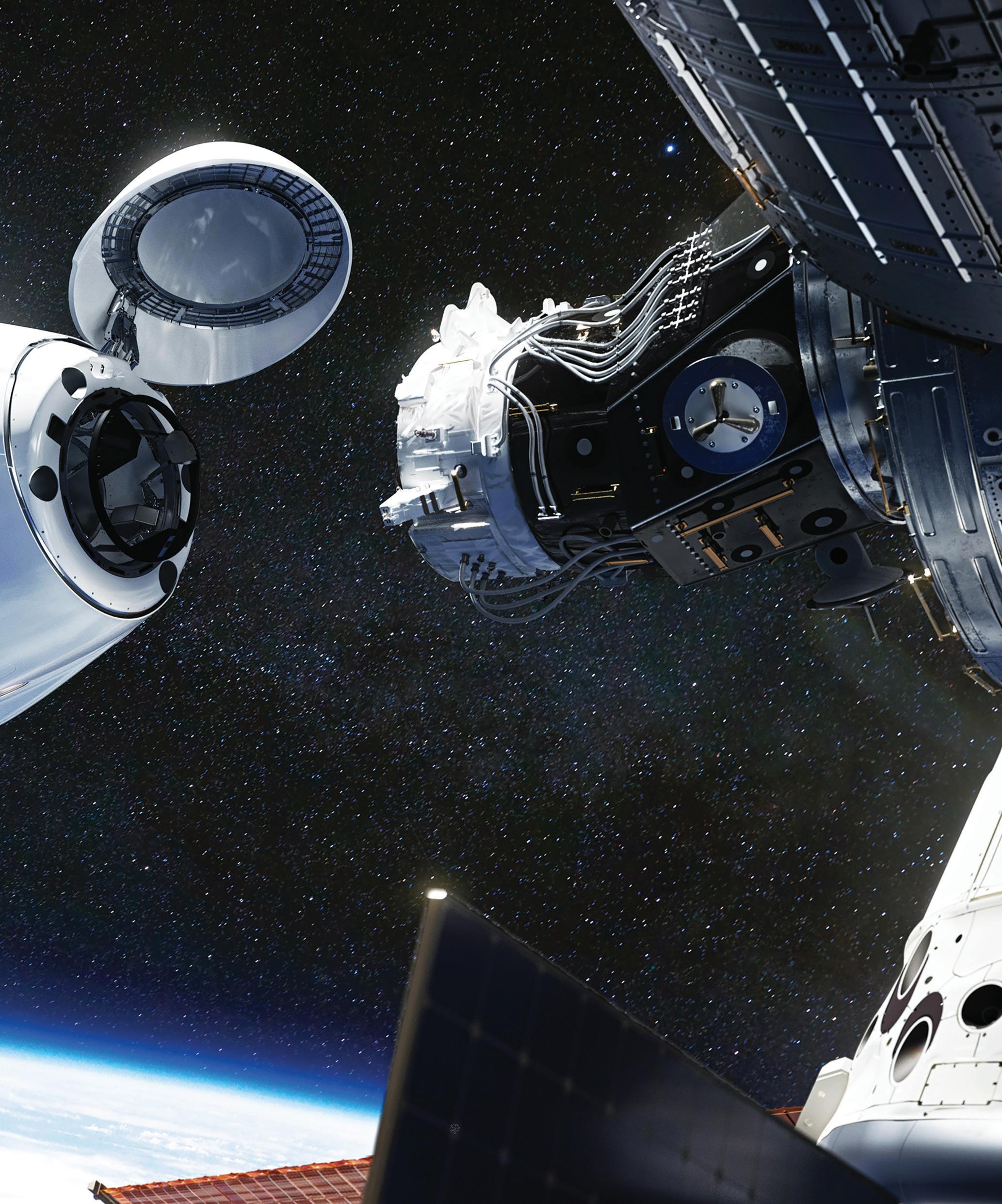
M e c h a n i c a l

Glasswork: glass
melting on the side of an electric furnace.
A change in the pitch circle can impact the dynamic load rating, and a change in the ball diameter or ball quantity can impact both load ratings. Changing all these variables at the same time can result in the dynamic capacity moving in one direction and the static capacity moving in the opposite direction. Both standards, ABMA Std.9 and ISO 281, use the same method to determine the basic rating life of a ball bearing. However, while based on similar concepts, they use di erent modifi ers to determine the adjusted rating life. These include adjustments for reliability, unique bearing properties, operating temperature, lubrication conditions, and certain environmental factors. For example, the life adjustment factor, a2, relates to special bearing properties, such as material. AST standard bearings are made from vacuum degassed steel, leading to an extended life for the bearings. The basic load ratings have been established by taking this longer life into consideration. This increases the operating life in hours by a factor of 2.2 and an increase in the load-carrying capacity by a factor of 1.3. When subjected to harsh operational environments, bearing life can be greatly reduced. Design modifi cations are typically required to maintain life expectancy (i.e., changes may include materials for rings and rollers, coatings, seals, retainer materials, and lubricants). Before making any modifi cations, designers must consider all the environmental factors in determining appropriate changes. Three common and challenging operating environments that impact bearing life are high temperature, exposure to corrosive chemicals, and vacuum environments. To meet production goals, manufacturers must account for these variables.
M e c h a n i c a l
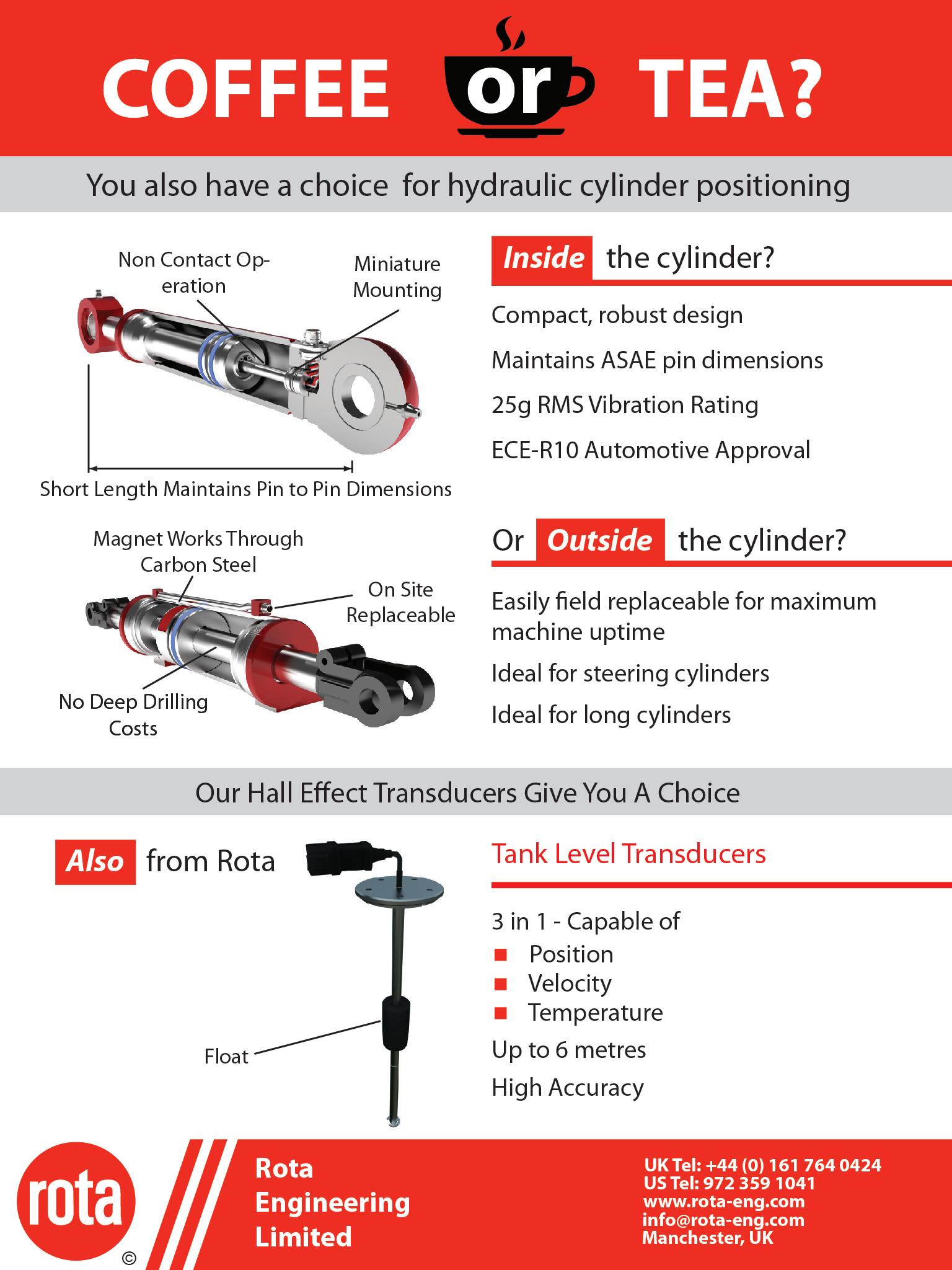
High-temperature environments
Custom bearings can accommodate temperatures exceeding 350°C. To design a custom bearing used in such environments, manufacturers must consider both the bearing material and lubrication. 52100 chrome steel is a common ball and roller bearing material, and it can withstand temperatures to 125°C. Heatstabilized materials must be considered for temperatures above 350°C. Also, high-temperature grease or oil that can operate up to 285°C should be added to the design.
Corrosive environments
Water and chemicals can have a signifi cant impact on the longevity of bearings. While rings and components are commonly made of stainless steel, in corrosive environments, consider nitrogen-enhanced martensitic stainless steel, which o ers fi ve times the corrosion resistance. Similarly, ceramic can be used for rolling elements, which deliver exceptional performance in corrosive environments.
Vacuum environments
Finally, vacuum environments, including those encountered in space, impact retainers and lubricants, with outgassing materials condensing on optical elements (lenses, solar cells, navigation sensors). The rate of outgassing increases at higher temperatures, requiring solid lubricants, including gold, silver, molybdenum disulfi de, and polytetrafl uoroethylene. Additionally, austenitic stainless steel AISI
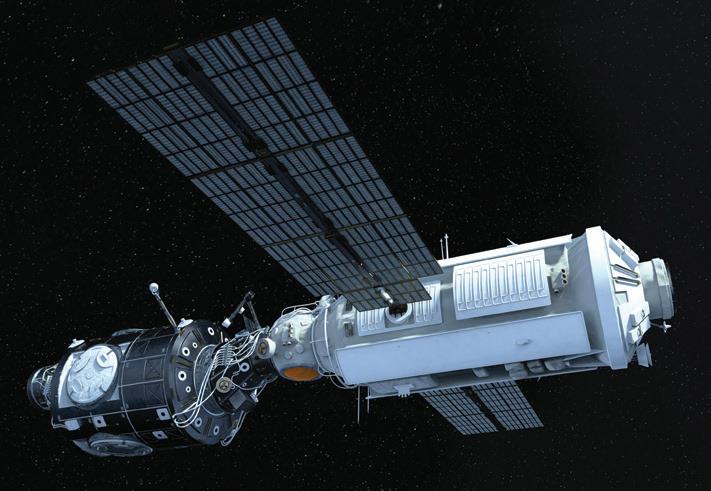
M e c h a n i c a l
304 cages are preferred in retainer materials, reducing the torque between the rolling element and the cage. Achieving success in meeting design life requirements is essential to your bottom line. To achieve the desired results for your bearing in these extreme environments, you must ensure that an experienced and knowledgeable bearing engineer performs a comprehensive analysis. DW
AST Bearings | www.astbearings.com
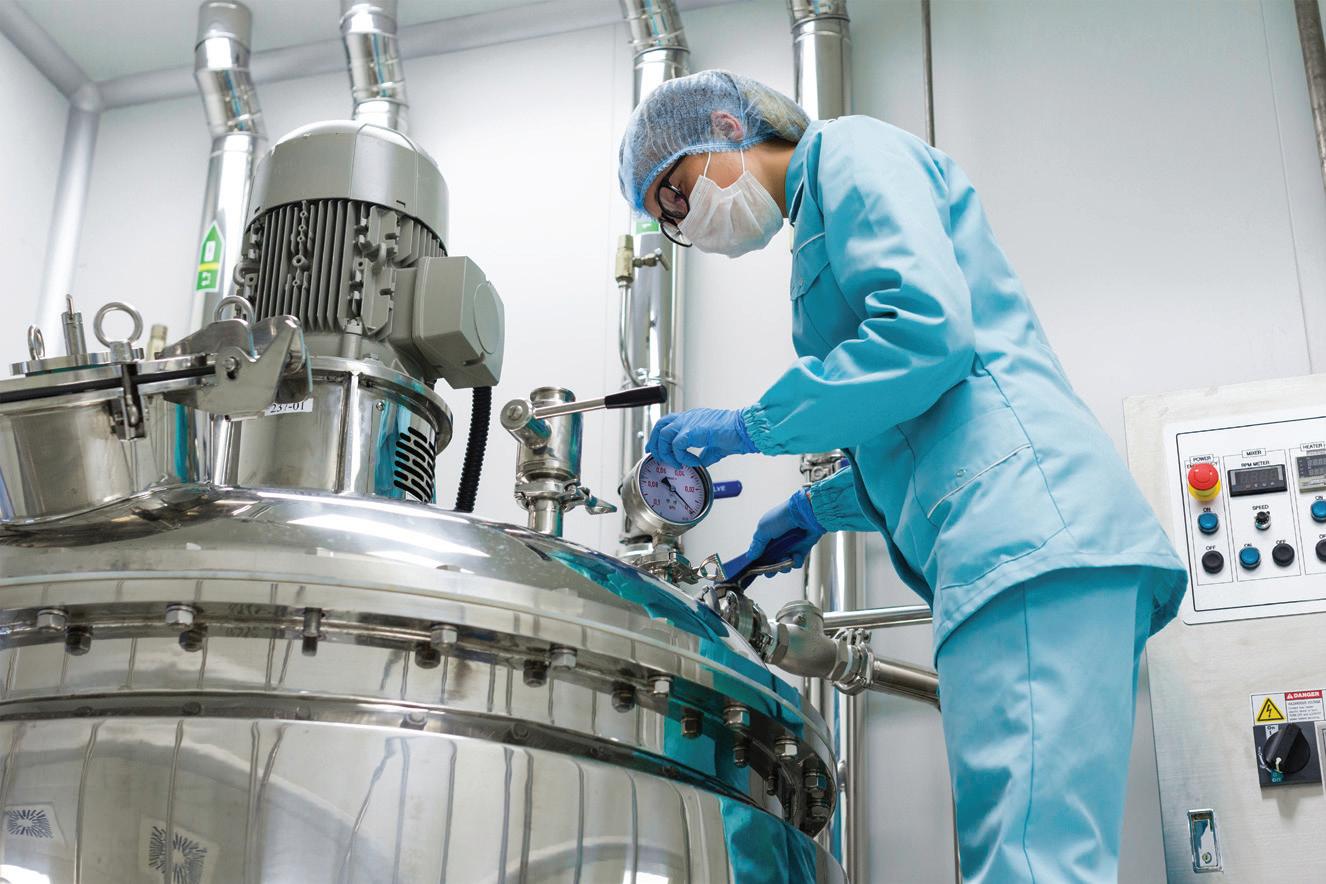
Aluminum tanks for the storage of raw materials in the chemical
industry, sterile conditions in the enterprise.
