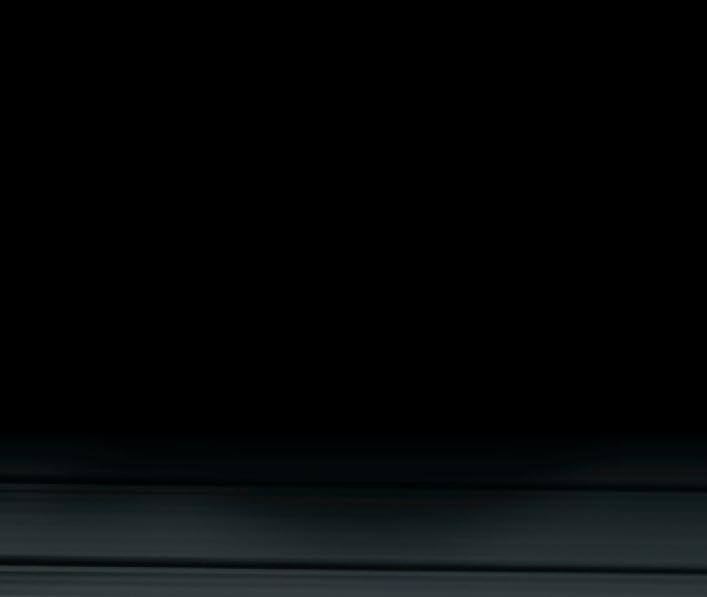
16 minute read
3DP AM
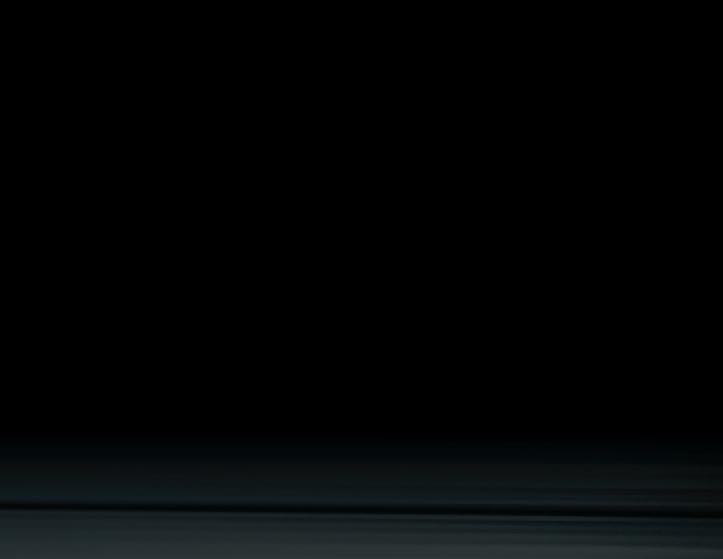
Design for 3D printing and Additive Manufacturing


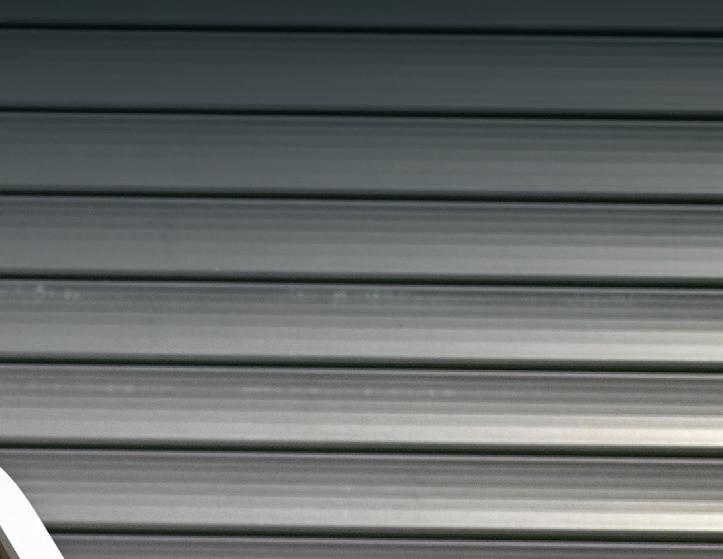

3D printing helps drive the future of sustainable mobility
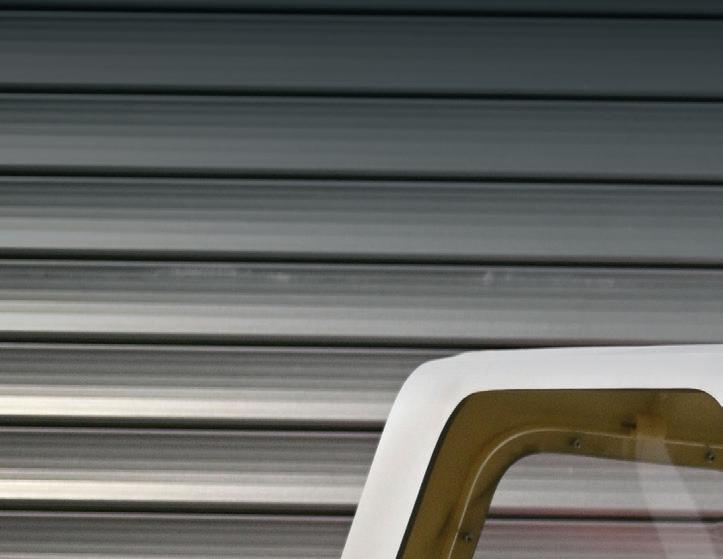
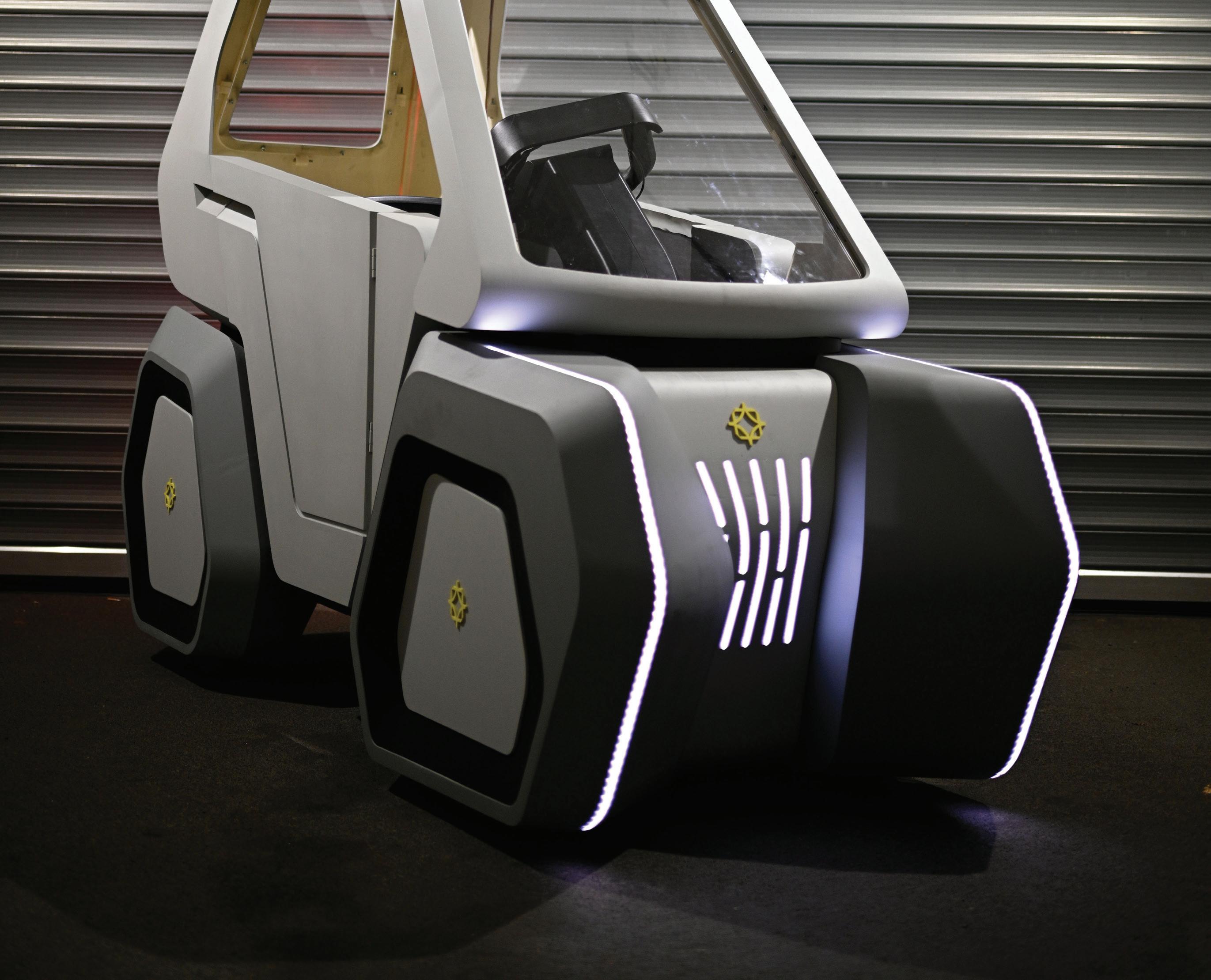
t the recent Formnext conference, nFrontier, the Berlin-based innovation studio and venture builder, unveiled UILA, a new vehicle and brand concept. As an industry fi rst, the fully functioning prototype is a hybrid between an electric cargo bike and a small Electrical Vehicle (EV). Extensively leveraging 3D printing, A
UILA was presented in cooperation with nFrontier industry partner Stratasys Ltd. and is a showcase for integrating disruptive technologies into a sustainable mobility solution. With a chainless electrical drive train, the vehicle e ortlessly accelerates to top speeds of 25 km/hr and has a range of 60-70 km. The four-wheeled two-seater also provides a cargo payload of up to 250 kg. With a length of 230 cm, the vehicle is only 170 cm high and 90 cm wide, weighing a total of 70 kg. With renowned engineering and manufacturing partners on board, nFrontier is preparing
UILA for serial production and tra c registration in
Germany some time in 2024. “UILA is our response to some of the most pressing challenges of our time such as climate change and the current energy crisis. UILA is not only radically changing the way we are commuting, but also provides a truly sustainable, game-changing mobility solution. At the same time, it delivers a feature set of digital functions and assets exceeding current bicycle industry standards,” said nFrontier CEO Daniel Buening. Current studies suggest that by 2040 there will be more than 750 million electric two- and three-wheelers on the road globally. Ultimately, the market for vehicles such as UILA is unlimited: Due to its dimensions and pedal-operated drive train it is technically a bike, so there is no need for a driver’s license, allowing users to drive it on bike lanes. Contrary to cargo bikes, UILA features additional comfort usually only o ered in small EVs: a modern infotainment system, including BYOD (smartphone) functionalities that will connect the internal display solutions. With the help of the UILA App, users will be able call the parked vehicle so it will drive autonomously towards you (‘Come to me Mode‘) or follow you without driver (‘Follow me Mode‘). “UILA is designed to be a digital device featuring many useful digital features that will make driving from A to B more enjoyable. We like to call it an ‘urban device’ because we believe that these features will unlock UILA’s full potential as a product with a potentially huge impact on urban transportation” added nFrontier CVO Dr. Stephan Beyer. UILA is an example of how 3D printing is transforming not only the product development process but also production. Using Stratasys FDM technology to 3D print large format body components signifi cantly reduced the cost of producing those same parts using traditional manufacturing, such as injection molding, while also saving time because parts could easily be produced inhouse at nFrontier. In addition, the nFrontier team has designed UILA to also use 3D-printed parts in the production process by leveraging higher volume additive manufacturing technologies such as powder-based SAF or photopolymer-based P3 systems. This reduces costs and improves sustainability by printing fewer components with less material and doing so locally — in the markets where the UILA vehicles are sold — reducing supply chain challenges and transportation emissions. UILA was designed by nFrontier lead designer Joschua Kranke and is a development by nFrontier’s EmTeCe (Emerging Technology Center), a leading facility of creatively applied Emerging Technologies in soft- and hardware in which Stratasys is a founding partner. (The EmTeCe converges the “Eight EmergingTechnologies” in one single facility: Additive Manufacturing, Augmented Reality/ Virtual Reality, Artifi cial Intelligence, Internet of Things, Robotics, Generative Design, Drones, and Advanced Visualization.) DW nFrontier | n ontier.de Stratasys | www.stratasys.com

Design for 3D printing and Additive Manufacturing
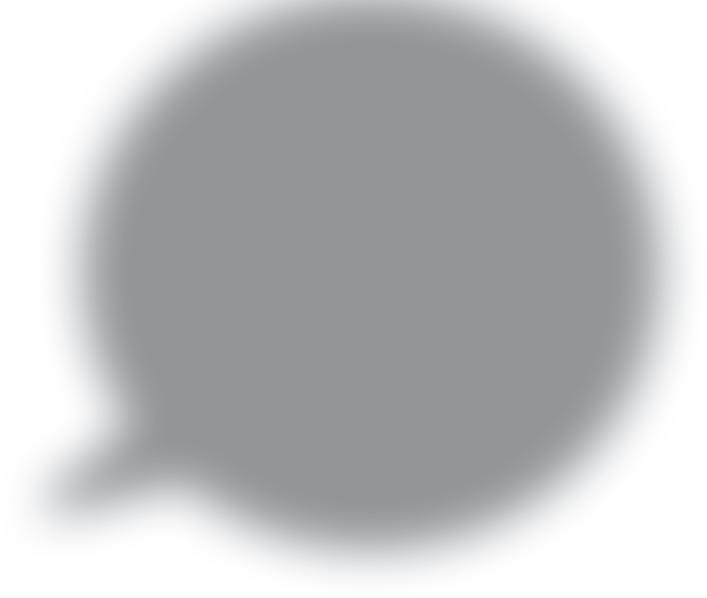
GE Additive and Shell use additive technology to create an oxygen hydrogen micromixer
This complex oxygen-hydrogen micromixer demonstration part was printed in nickel alloy 718 on a GE Additive Concept Laser M Line. This part needed to have multiple channels for hydrogen and compressed oxygen.
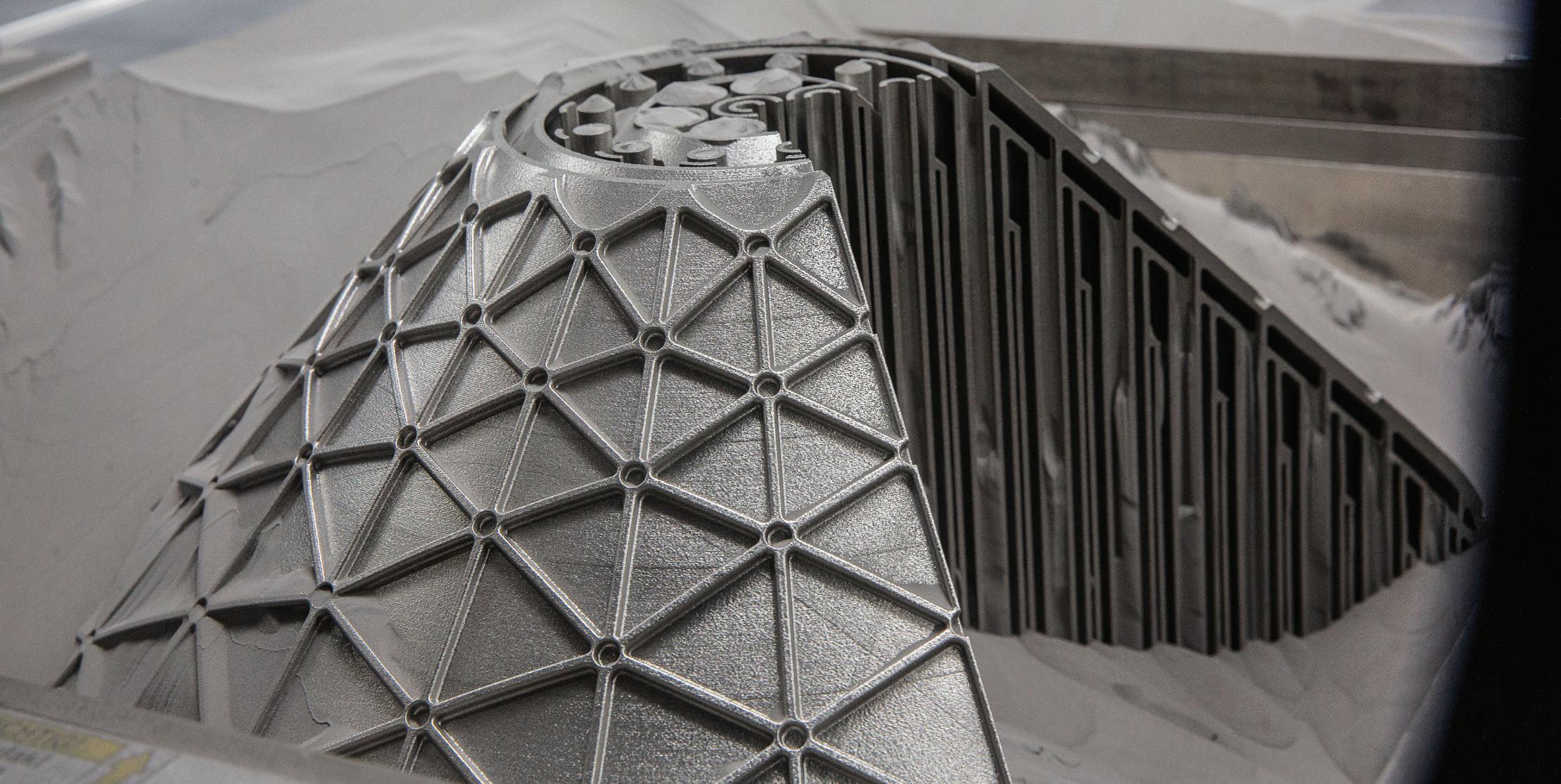
uring last year’s Formnext conference, Shell International B.V. and GE Additive unveiled the results of a joint design and engineering project — an additively manufactured oxygen hydrogen micromixer. This complex, non-functional, demonstration part, was printed in nickel alloy 718 on a GE Additive Concept Laser M Line system, and installed at Shell’s 3D Printing CoE and Workshop, part of the company’s Energy Transition Campus Amsterdam (ETCA) in the Netherlands.D Shell maintains a 3D printing facility at ETCA in proximity to its scientists and partner companies to leverage additive manufacturing to prototype, and print functional parts. Having its own printing capability grants Shell’s R&D department the freedom and speed to create novel parts not available in the market, and solve new technical challenges in support of the energy transition. Joost Kroon, an additive technology subject matter expert at Shell explained, “We really wanted to put the M Line through its paces and test it to its limits. Working with the GE Additive team we agreed to apply additive technology to reimagine a large, complex part, incorporating channels that would be di cult to manufacture conventionally. Working on an oxygen hydrogen micromixer aligns well with our companies’ strategies to play a positive role in the energy transition.”
Lead design engineer Sonali Sonawane Thakker at GE Additive’s AddWorks team based in Munich took inspiration from the ways pollen grains form in a flower head to arrange the more than 330 individual nozzles in a circular pattern. The curved wall and the conical shape also reflects the shape of a petal.
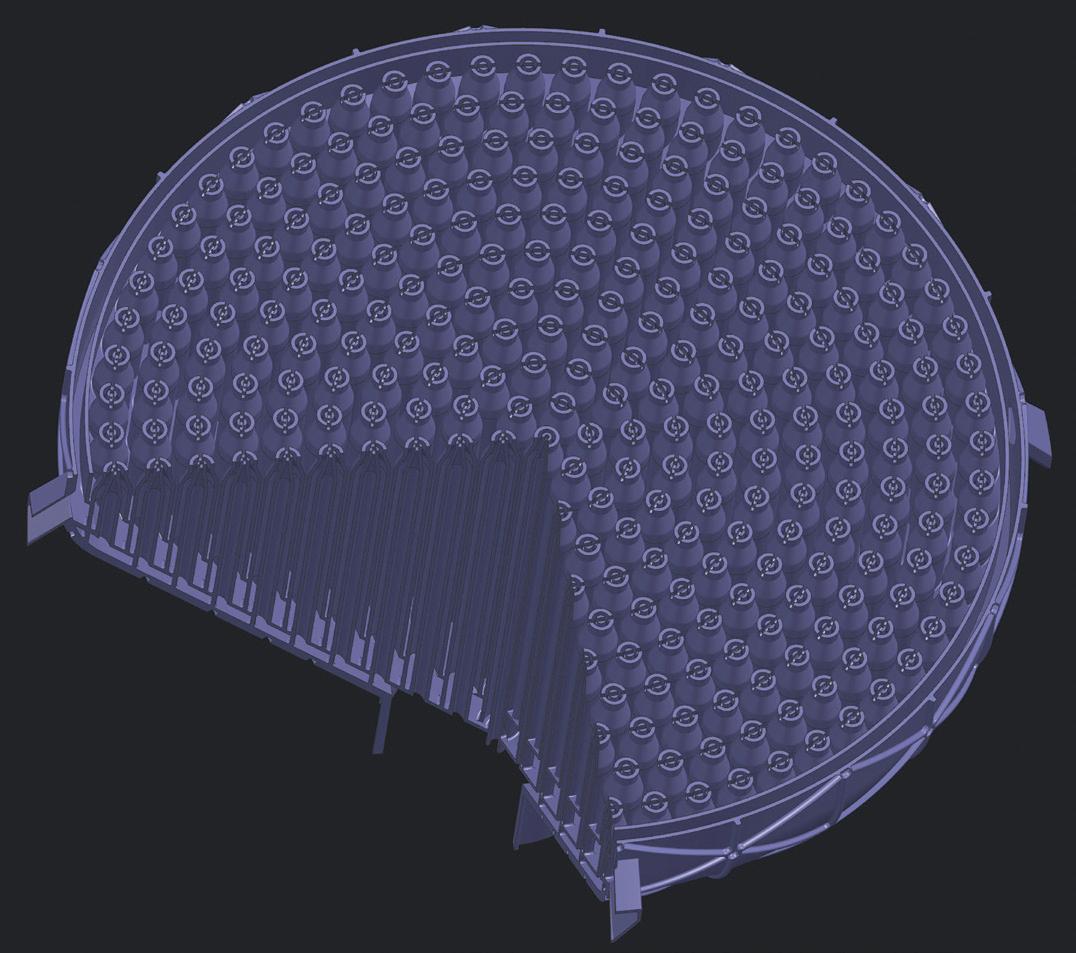
Existing micromixers – also known as hydrogen-oxygen burners – are typically cylindrical when conventionally manufactured to accommodate the complex layout of tanks, pipes and nozzles. Sonawane Thakker and her team chose a large conical design and also moved from a flat to a curved structure with an ISO grid to increase the overall strength, rather than a customary flat grid.
Taking inspiration from geometry in nature
Sonali Sonawane Thakker, a lead design engineer at GE Additive’s AddWorks team based in Munich handled researching, designing, and iterating the final design. Her brief was to design a part that was large, complex and incorporated channels for hydrogen and compressed oxygen. Sonawane Thakker was able to deploy the design freedoms that additive technology affords to rethink the structure and the shape of the part.
“Once we had settled on a part, our preliminary research showed that existing micromixers — also known as hydrogen-oxygen burners — are typically cylindrical, when conventionally manufactured, to accommodate the complex layout of tanks, pipes, and nozzles. For additional complexity we chose a large conical design and also moved from a flat to a curved structure with an ISO grid to increase the overall strength, rather than a customary flat one.”
Sonawane Thakker sought inspiration from geometries and symmetry in the natural world, in particular the Fibonnaci sequence replicated in flowers and petals.
“With over 330 individual nozzles to incorporate in a circular pattern, I took inspiration from the ways pollen grains form in a flower head. The curved wall and the conical shape also reflects the shape of a petal,” she added.
Build and post-processing
Following feasibility reviews and iterations by Shell and GE Additive teams, the design and dimensions of the reimagined part were finalized and nickel alloy 718 was chosen as the material for the build. Dimension of the part: Height: ~296 mm Diameter: 484 mm Other: X ~ 429 mm Y ~490 mm
The build preparation and printing of the part on the M Line was overseen by Lisa Kieft-Lenders, team lead and Dennis Boon, a technician at the Shell 3D Printing Center of Excellence and Workshop.

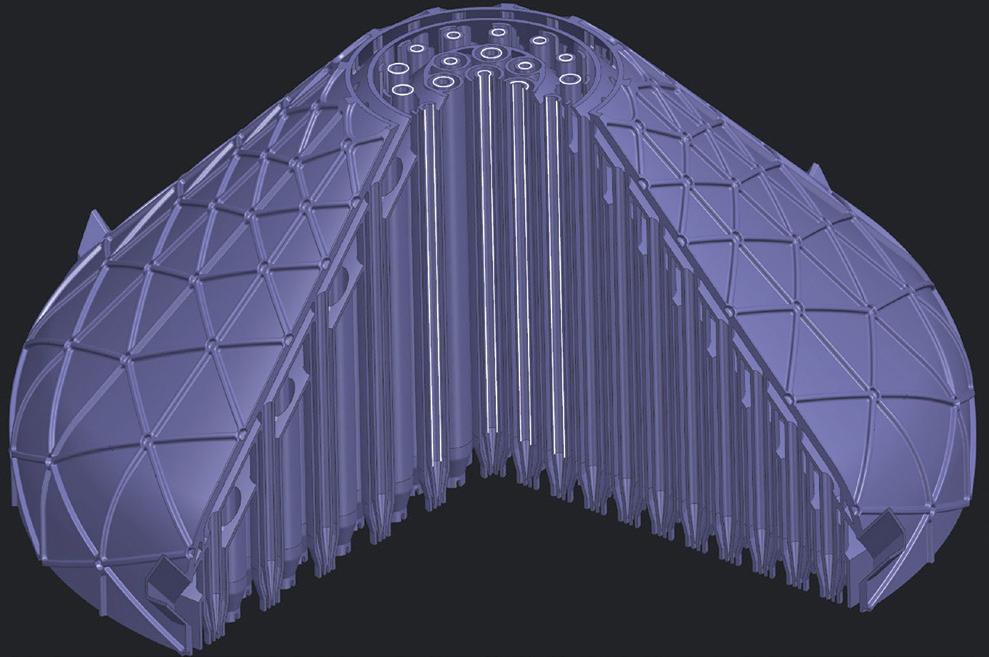
Design for 3D printing
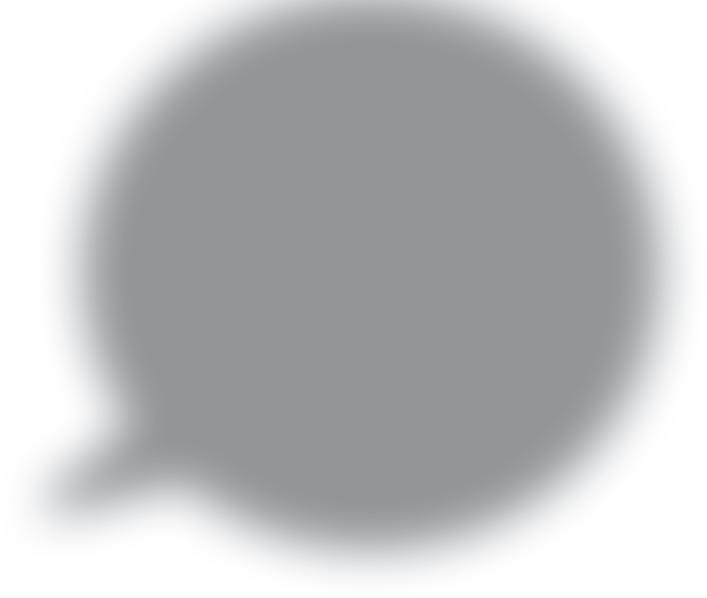
Optimizing Next-Gen Medical Device Manufacturing. Precisely.

PRECISION MOTION CONTROL TRANSFORMING CRITICAL MANUFACTURING PROCESSES.
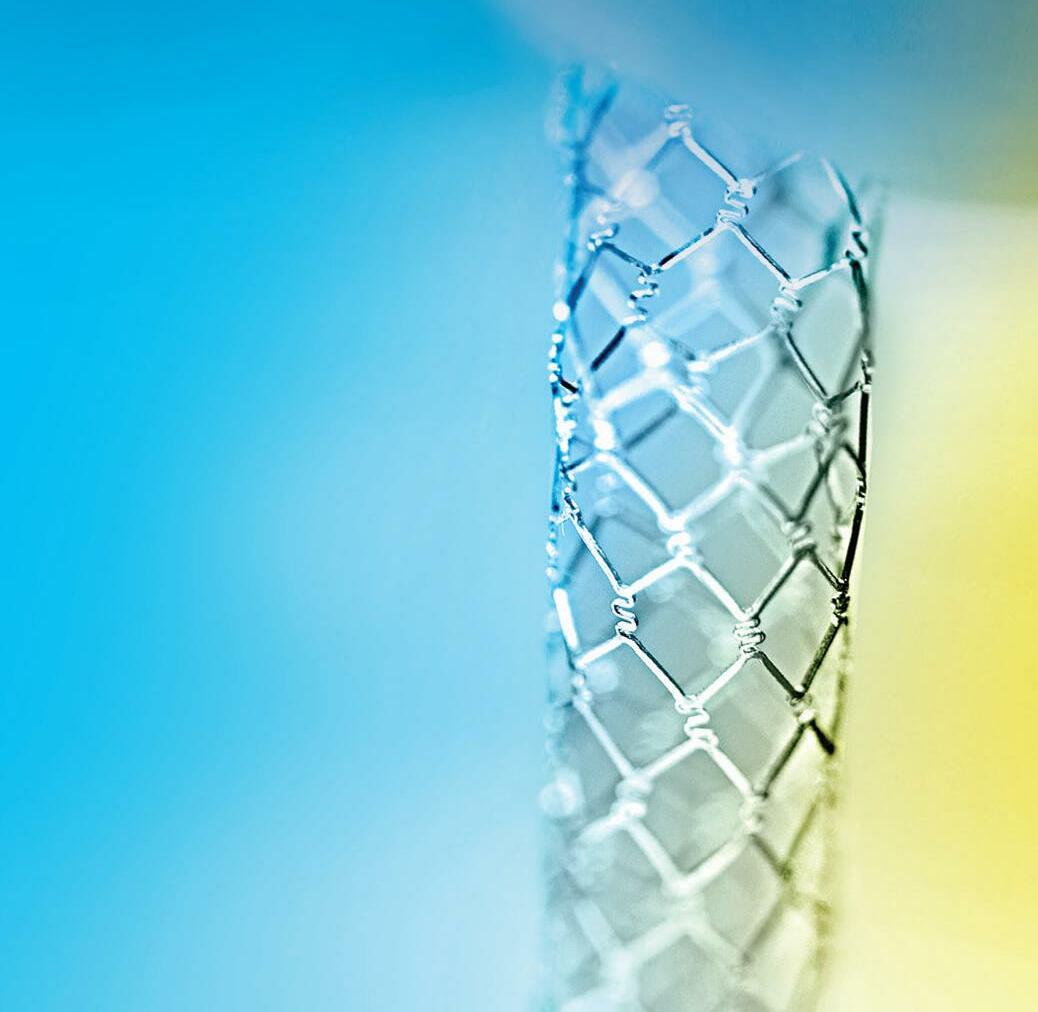

“We have been involved in the project from the outset and have therefore been particularly close to this build and invested in its success. Given this is one of, if not the largest and most complex parts built on an M Line so far, we’ve remained in close contact with the GE Additive team in Munich and were supported, on the ground here in Amsterdam, by their local fi eld service engineers. After some adaptions at the start, the build ran smoothly over nine days,” said Kieft-Leenders. Post-processing was also completed at the Shell facility, and this was made easier through inclusion of powder removal holes, incorporated by Sonawane Thakker during the design phase. The part was completed in early November. The micromixer will be put on display at Shell’s ECTA. “We are confi dent in the M Line’s ability to perform. Indeed, we grasp every opportunity to test it to its limits with both hands. I cannot underestimate the power of collaboration and problem-solving during this project. It has brought together some great additive minds and the end result is not only visually stunning, but it is also substantial in size, complexity, and equally strong,” said Rob Dean, GE Additive’s AddWorks leader in EMEA. DW
GE Additive www.geadditive.com
Design for 3D printing and Additive Manufacturing

Unlocking PEKK’s lightweighting potential for aerospace
H
exagon’s Manufacturing Intelligence division and
Stratasys have applied Hexagon’s simulation technology to capture the behavior of Stratasys’ ultra-lightweight Antero reinforced polyetherketoneketone (PEKK) materials and its additive manufacturing processes. These rigorously validated simulations help engineers develop lighter weight components for use in new sustainable aircraft and spacecraft. 3D printed plastic parts enable the ability to take excess weight out of parts for aerospace applications, reducing the energy use and potentially increasing the range of new aircraft. When the material and processes are fully exploited by product designers, it may also reduce the cost caused by over engineering and the waste and lead times of traditional manufacturing. However, the adoption of plastics and additive methods for structural components has remained slow due to the industry’s safety-critical nature and regulations. Providing engineering teams with simulation tools to validate these materials is the “missing link,” enabling designers to apply these breakthroughs today. Rigorously validated multi-scale models of these new high-performance aerospace-approved materials — Stratasys Antero 840CN03 and Antero 800NA — have been added to Hexagon’s Digimat materials exchange ecosystem, with associated print process parameters from Stratasys’ aerospace-ready 3D printers. Using these detailed proprietary models, engineers can create digital twins that accurately predict how parts printed with the chosen material and approved aerospace-ready Stratasys printer will perform in a digital reality with real-world use cases and certifi cation tests before any physical prototypes are manufactured. Developed to be open, Digimat software gives manufacturers the ability to design lighter parts that can match metals in performance and avoid costly over engineering using their preferred fi nite element analysis (FEA) and computeraided engineering (CAE) tools. Moreover, companies that use Digimat in conjunction with Hexagon’s MSC Nastran and MSC Apex will accelerate the This pie-shaped component is part of the hatch cover assembly for NASA’s Orion spacecraft. It was 3D printed using Stratasys Antero 840CN03, a PEKKbased thermoplastic with low outgassing and consistent electrostatic dissipative (ESD) properties. Antero 840CN03 gives manufacturers a high-performance, ESDcompliant 3D printing material that meets demanding applications such as space fl ight. Image courtesy of Stratasys Inc.
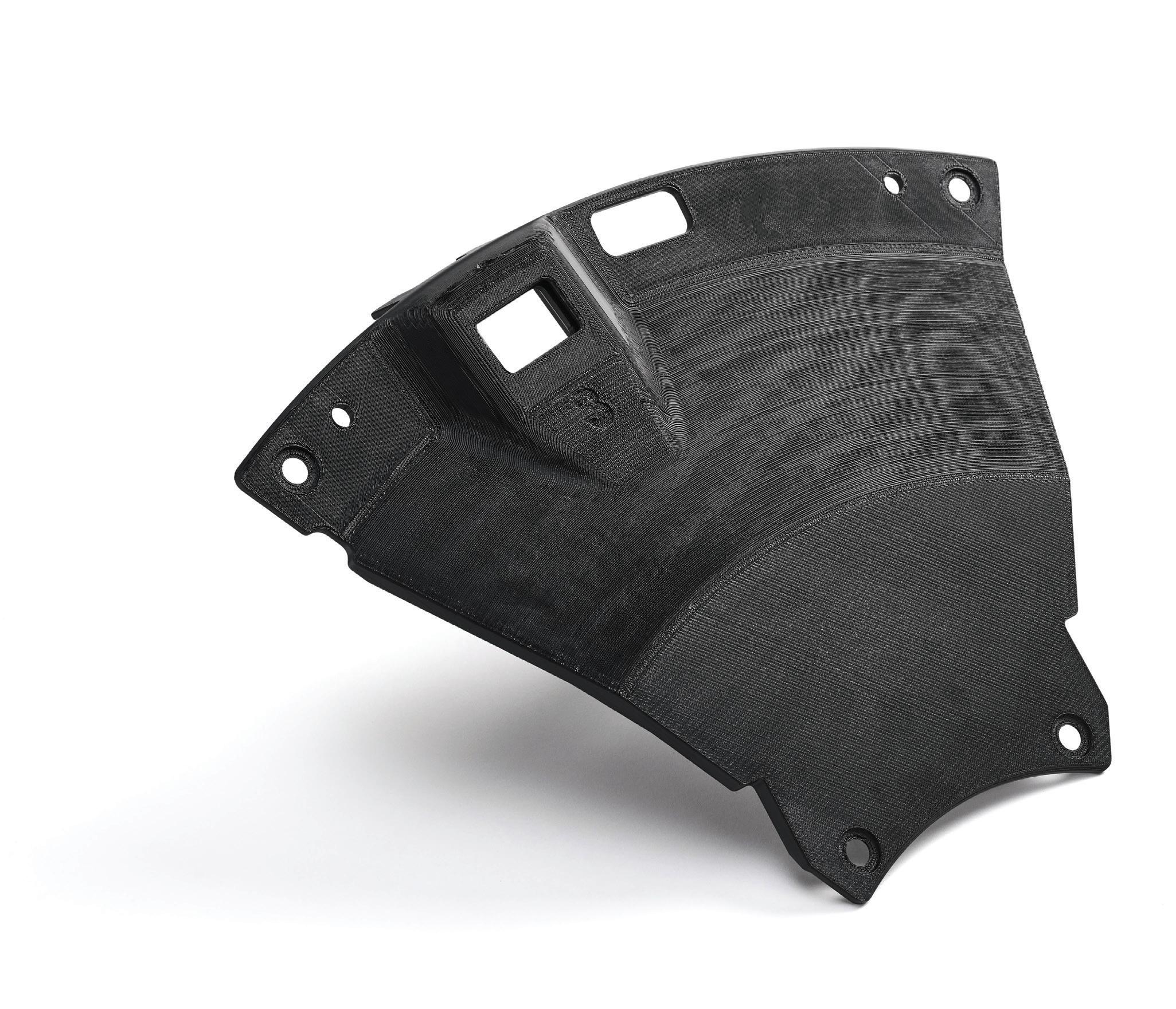
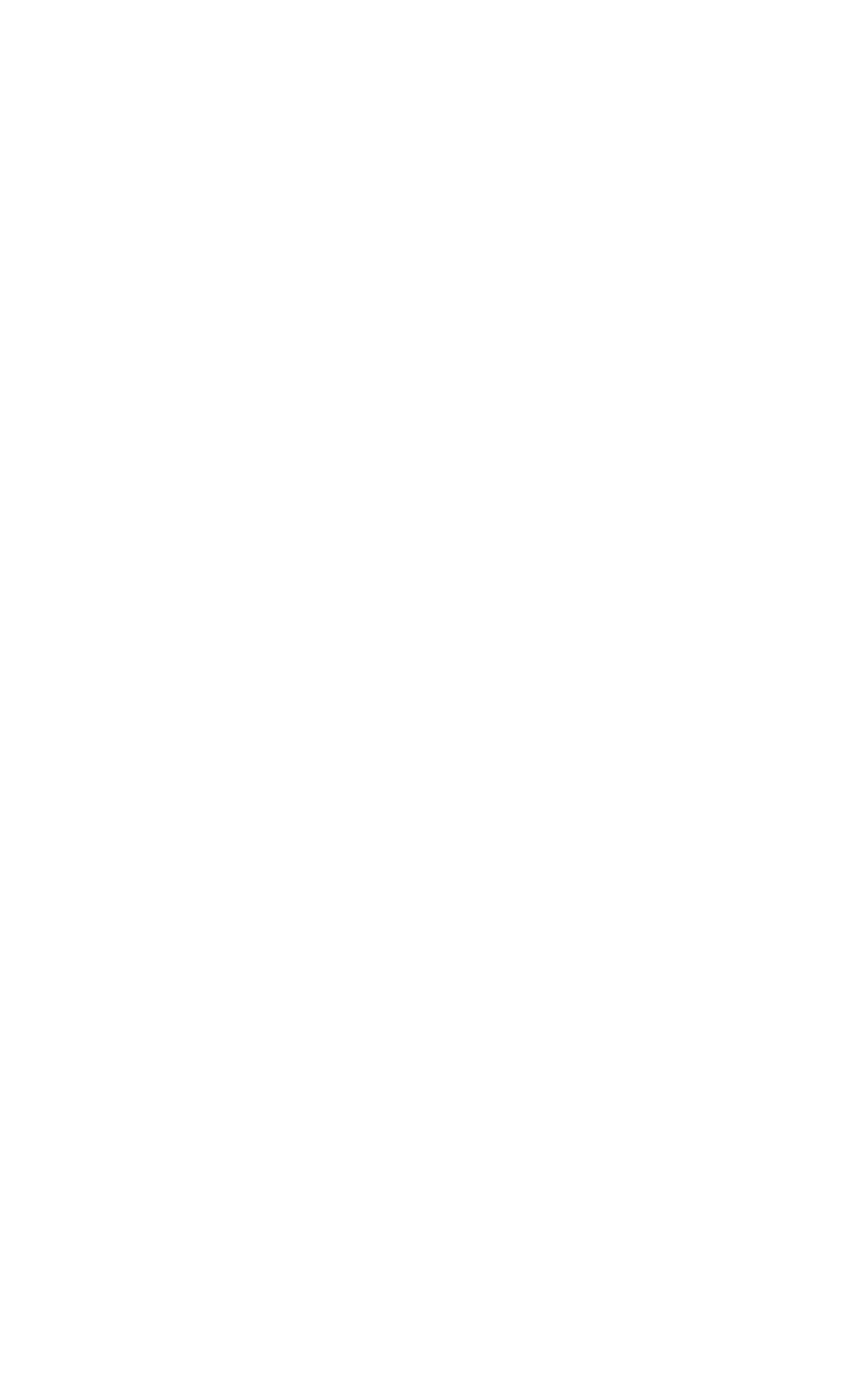


Design for 3D printing and Additive Manufacturing
certifi cation and documentation of their work.
The Antero materials are already being used in aerospace engineering. Lockheed Martin, for example, used Antero 840CN03 to create NASA’s Orion spacecraft docking hatch cover. By making rigorous digital engineering and virtual manufacturing possible with these new simulation tools, more product development teams can apply and de-risk Stratasys’ aerospace additive manufacturing solutions. Through the partnership between Stratasys and Hexagon, which has spanned more than a decade, several high-performance thermoplastic materials — including Ultem 9085, Ultem 9085 CG, Ultem 1010, and Nylon12CF — have been characterized and added to Hexagon’s Digimat material modeling software.
Antero materials · The Antero 840CN03 material is a PEKKbased thermoplastic for Fused Deposition Modelling (FDM) additive manufacturing that combines the physical and mechanical qualities of PEKK with carbon nanotubes for consistent electrostatic dissipative (ESD) properties. The high-performance polymer exhibits exceptional chemical and wear resistance, ultra-low outgassing properties.
·The Antero 800NA material is a PEKKbased FDM thermoplastic with mechanical properties that include high strength, high heat resistance, toughness, and wear-resistance. These qualities make it a lighter alternative to aluminum and steel in certain use cases. Chemical resistance and minimal outgassing provide suitability for aerospace applications where prototypes and parts are exposed to jet fuel, oil, and hydraulic fl uid. Other uses include industrial applications where high strength and chemical resistance are needed. DW
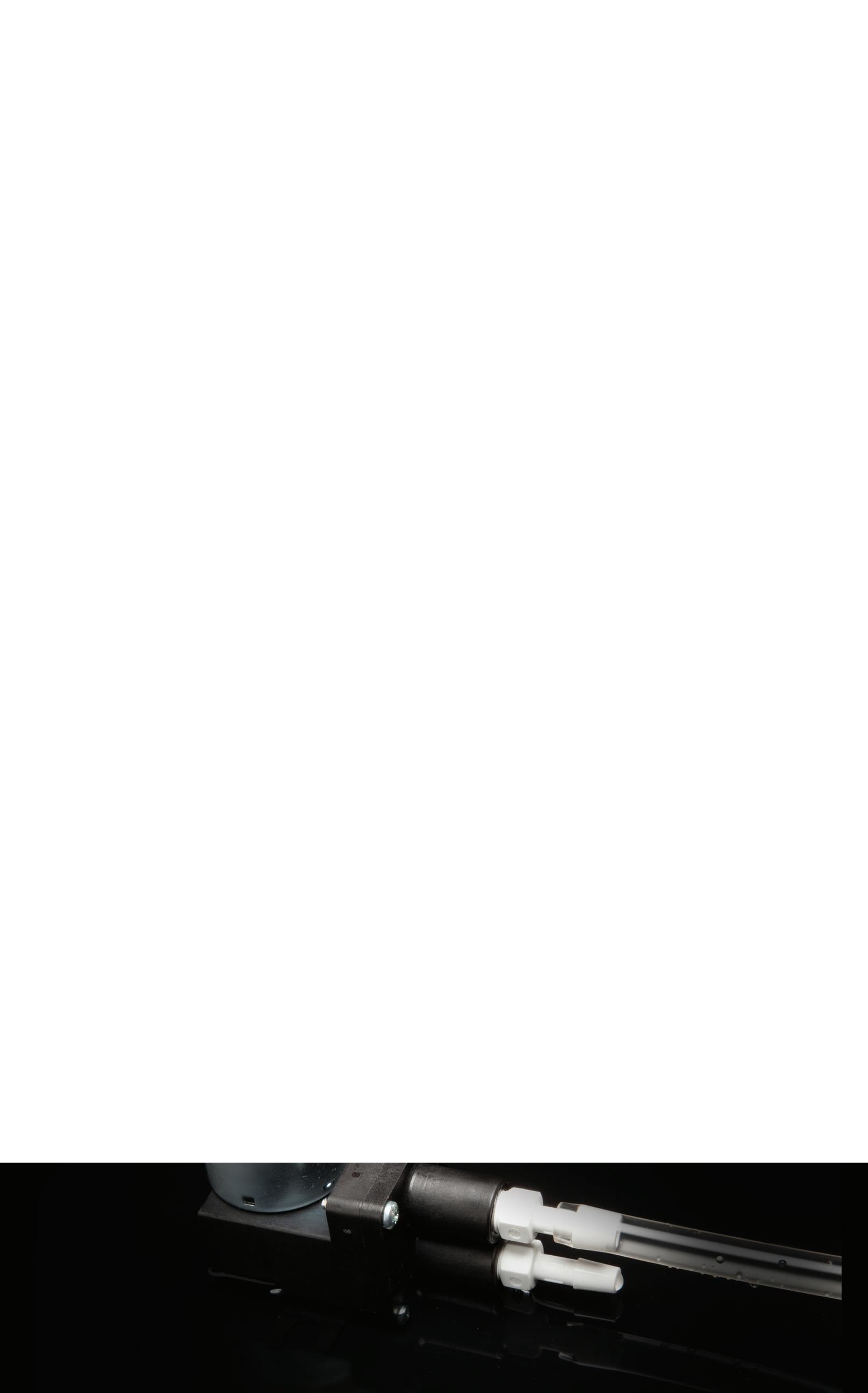

DISCOVER
OUR CUSTOMIZABLE CHECK VALVES & PUMPS
Hexagon | hexagon.com/mi. Stratasys | www.stratasys.com
Design for 3D printing and Additive Manufacturing

Parts-made-with-nonexplosible-powder-scaled
Equispheres Inc. has developed a non-explosible aluminum alloy feedstock for additive manufacturing (AM) that reduces the hazards associated with day-to-day handling of materials for 3D printing. Identifi ed as NExP-1, this material is specifi cally designed for production printing of aluminum parts. It can produce high-quality prints at high throughput rates, but unlike other metal powders for AM, it is dust-free and characterized as non-explosible per ASTM E1226, Standard Test Method for Explosibility of Dust Clouds. The material is also non-combustible, per the UN Manual of Tests and Criteria, Part 3, Subsection 33.2.1. for fl ammable solids. “We have achieved these key safety properties without altering the quality of our material nor the chemical composition. In printing, this material performs just as well as our other aluminum powders, but it has the added benefi t of being non-explosible and non-combustible,” said Evan Butler-Jones, Vice-President — Product & Strategy for Equispheres. “It would almost be inaccurate to even call this a powder,” he continued. “It is almost totally free of dust; it fl ows like water and it is easy to clean o of equipment surfaces. It is a completely unique printing media for production additive manufacturing.” The material is currently available in AlSi10Mg. Equispheres has developed recommended parameters for printing the new material, targeting several enduse applications. DW
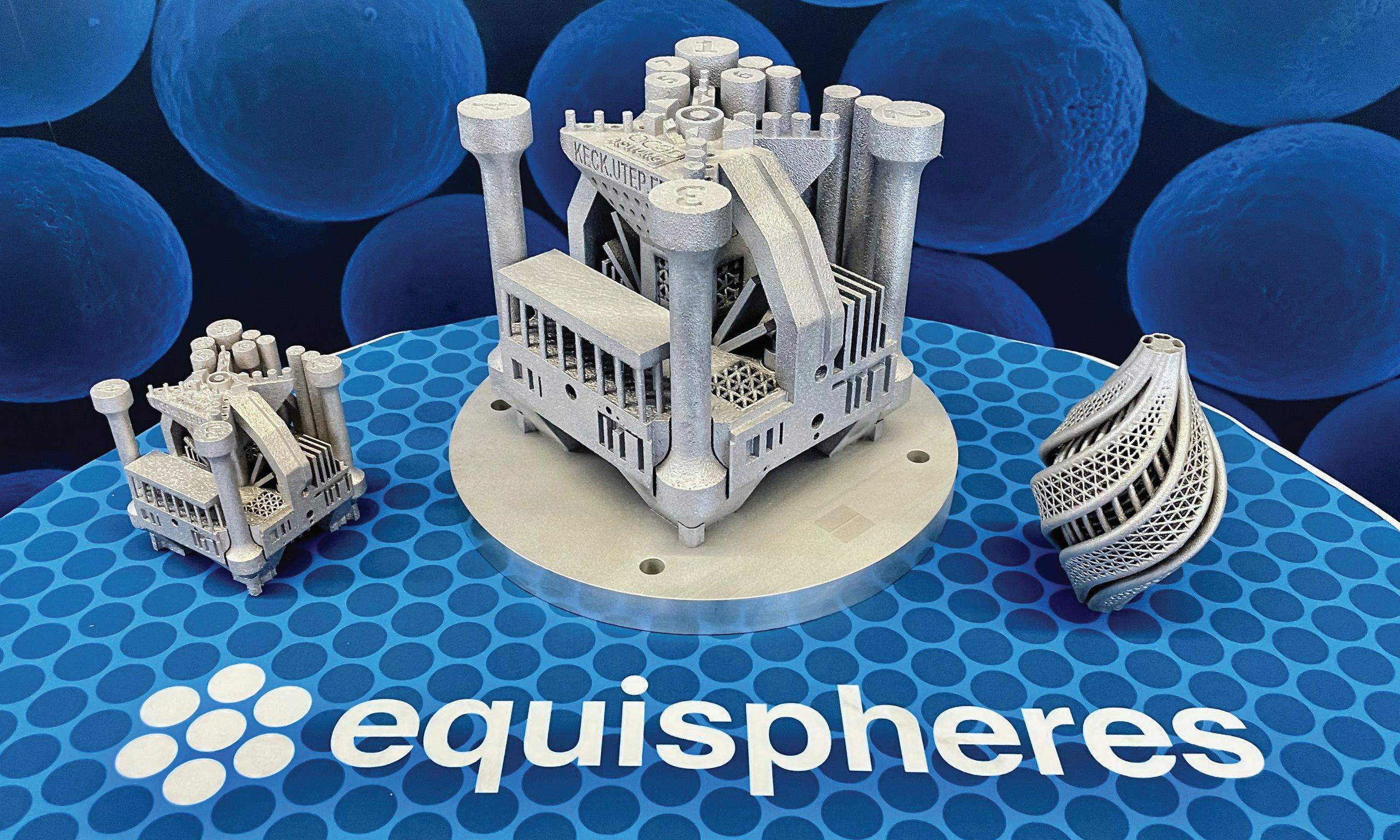
Equispheres www.equispheres.com
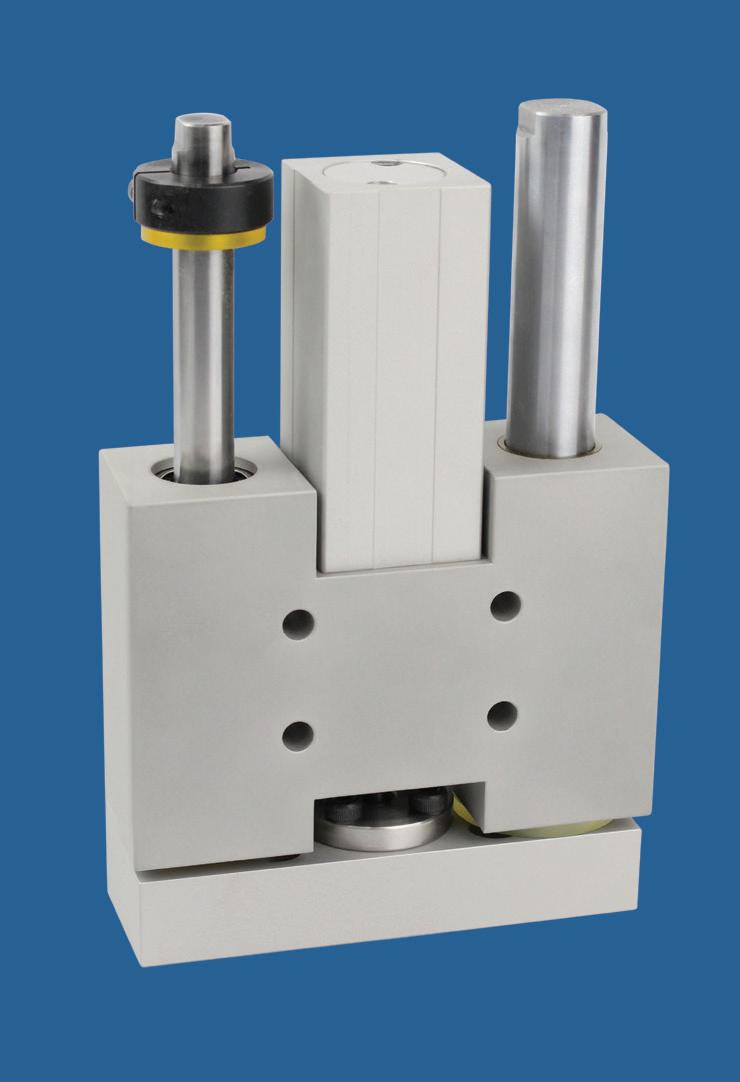
800.229.4955 • nasonptc.com
Design for 3D printing and Additive Manufacturing
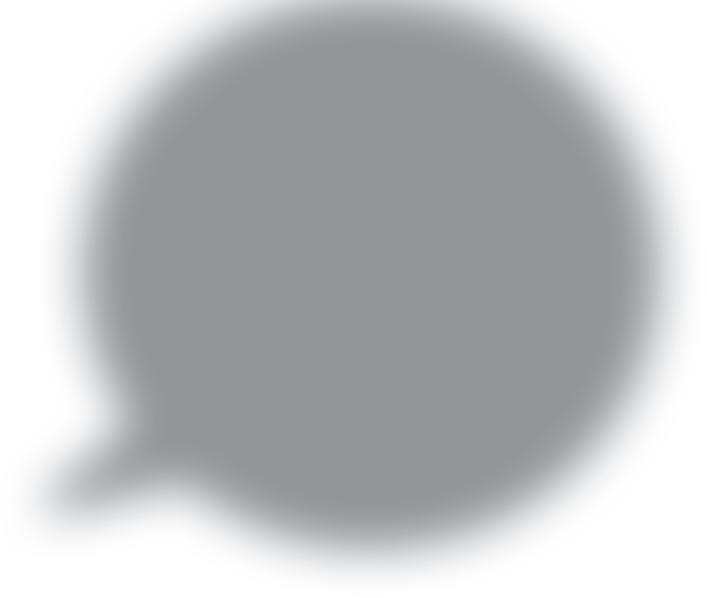
Damping elastomers for additive manufacturing
he EPU 43 and EPU 45 are two damping elastomers recently introduced by Carbon. These materials o er new opportunities for breakthrough products in impact protection such as padding, gloves, and helmets. EPU 43 is an energy-damping elastomer that is soft while o ering promising durability under high-cycle fl exing, making it suitable for applications like comfort padding for helmet liners and safety gloves. EPU 45 achieves the highest level of damping performance and printability within the Carbon portfolio, making it the choice for many high-performance applications including sports padding and seating. The dual-cure, damping elastomers o er opportunities and solutions for a number of impact protection needs, including: • Damping performance: EPU 45 is a strain-rate-sensitive material that sti ens to absorb energy at higher impact rates, enabling the design of highly breathable lattice geometries tuned for comfort at low-impact speeds and energy absorption at high-impact speeds. EPU 43 o ers moderate sti ness, good damping, and excellent durability through fl exing cycles in various temperature and humidity environments. • Durability and comfort: EPU 45 has the toughness and recovery needed to survive repeated, high-energy impacts in a variety of environments. EPU 43 has moderate sti ness that enables softer and more conforming lattice structures.
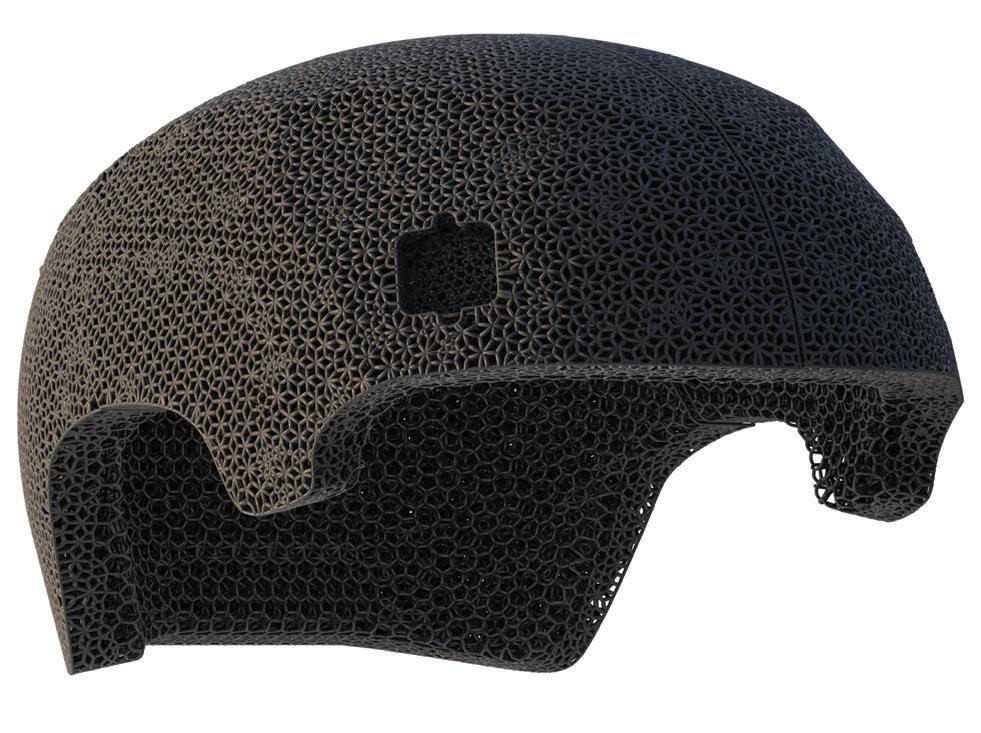
T• Production throughput: EPU 45 has the highest green strength of Carbon’s elastomers, allowing the widest range of part shapes and lattice geometries to be printed with a high yield. EPU 43 prints with moderate green strength, allowing for a broad set of production shapes with high yield. • Proven-in-production: Products utilizing EPU 45 will be on the market soon and EPU 43 has been proven with well-known products like Hard Head Veterans and the CCM Hockey helmet. Both elastomers are available now in North America, Europe, and China. Starting in 19L package sizes with high-volume production workfl ows, EPU 45 will also be available in 5L samples to support mid-volume production workfl ows. DW
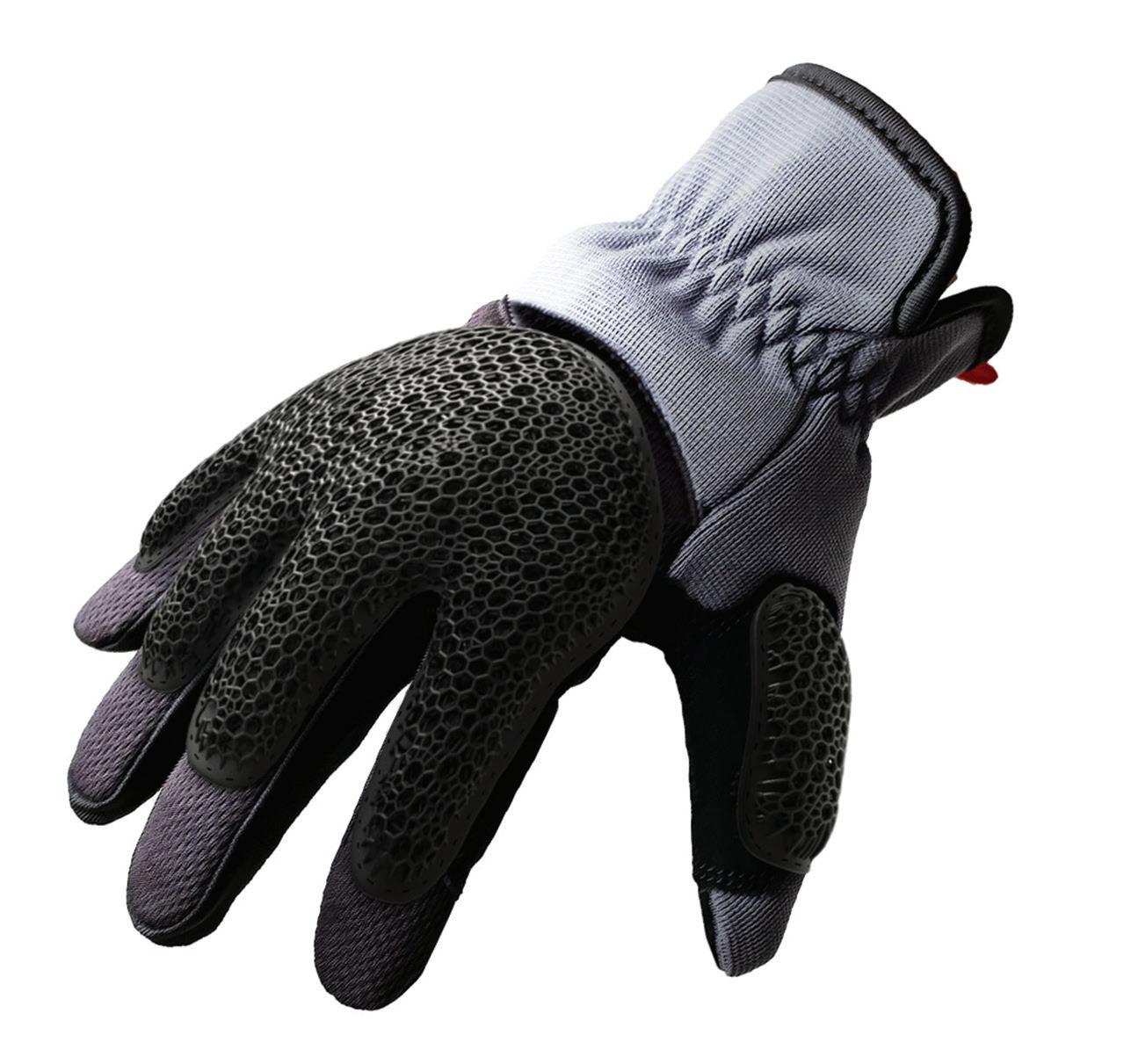
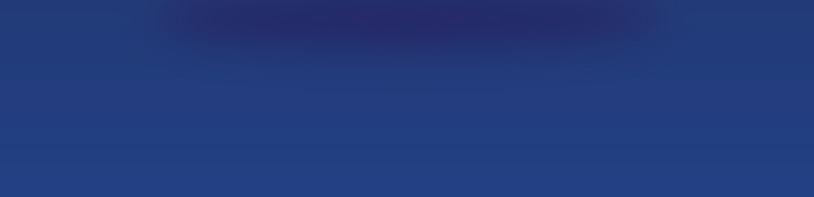
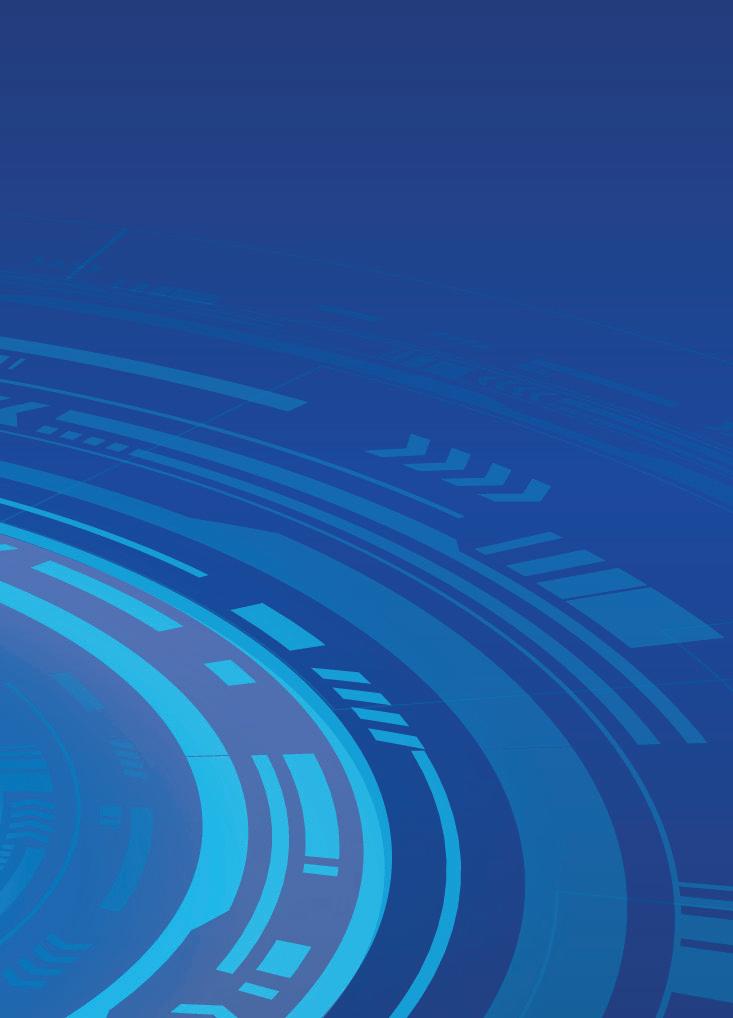
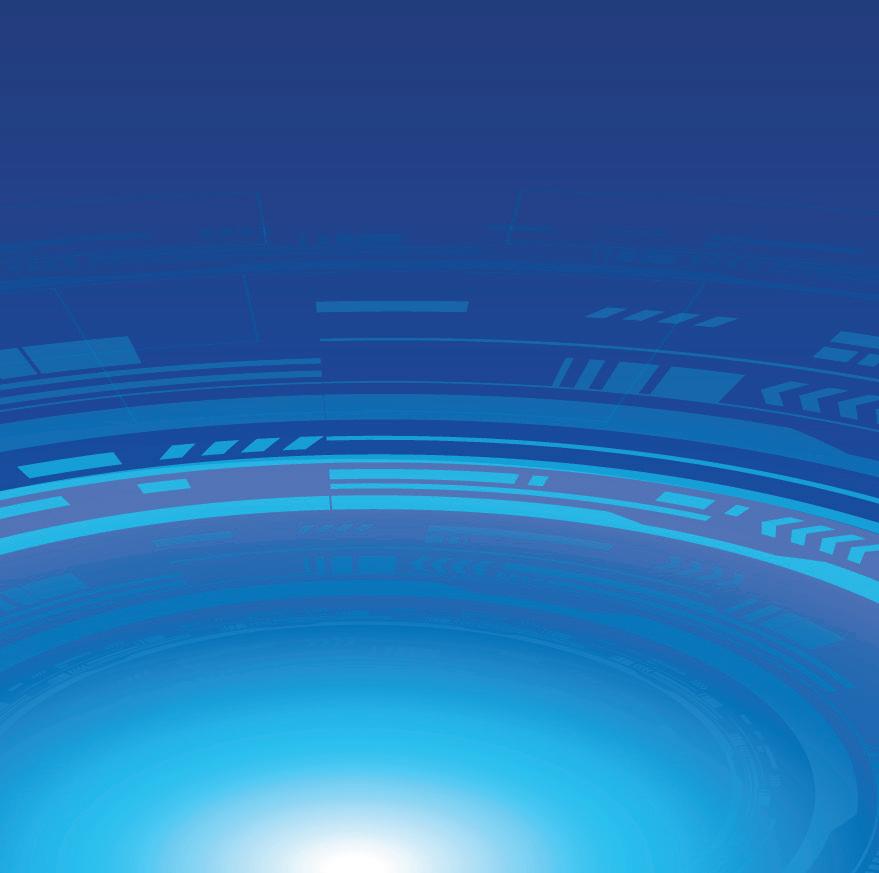
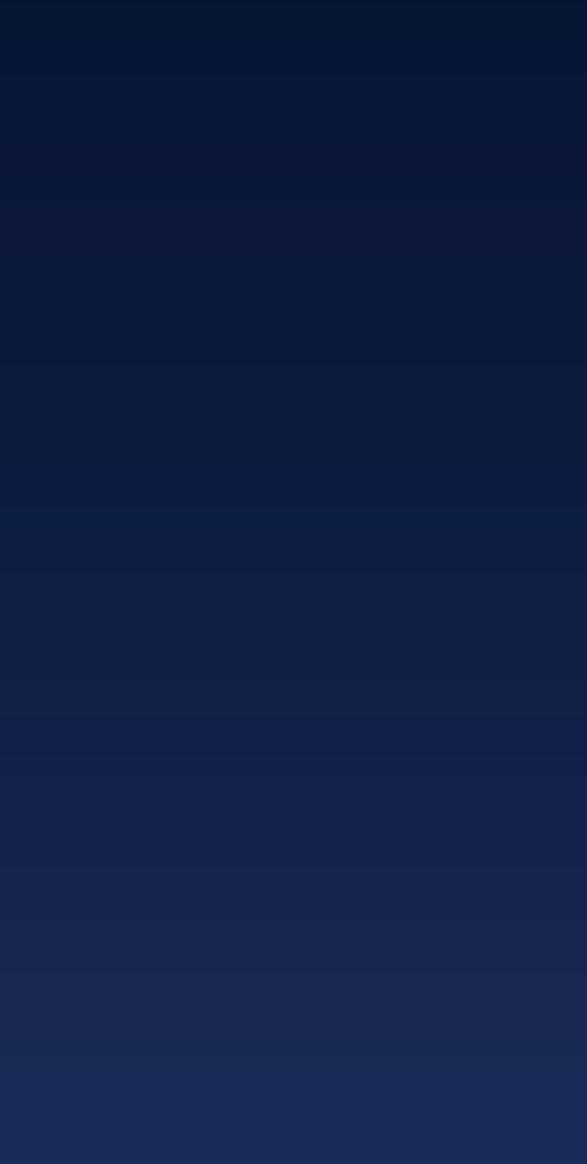
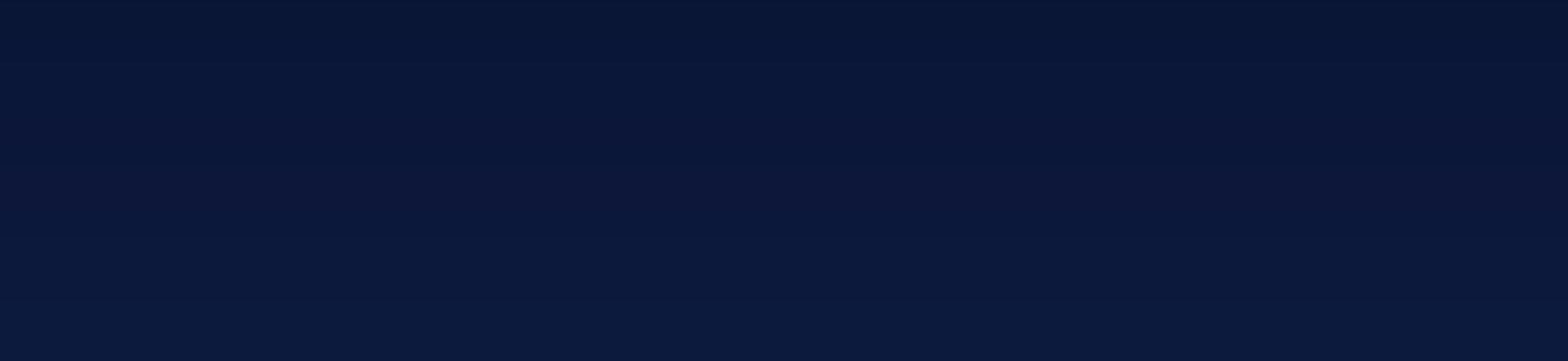
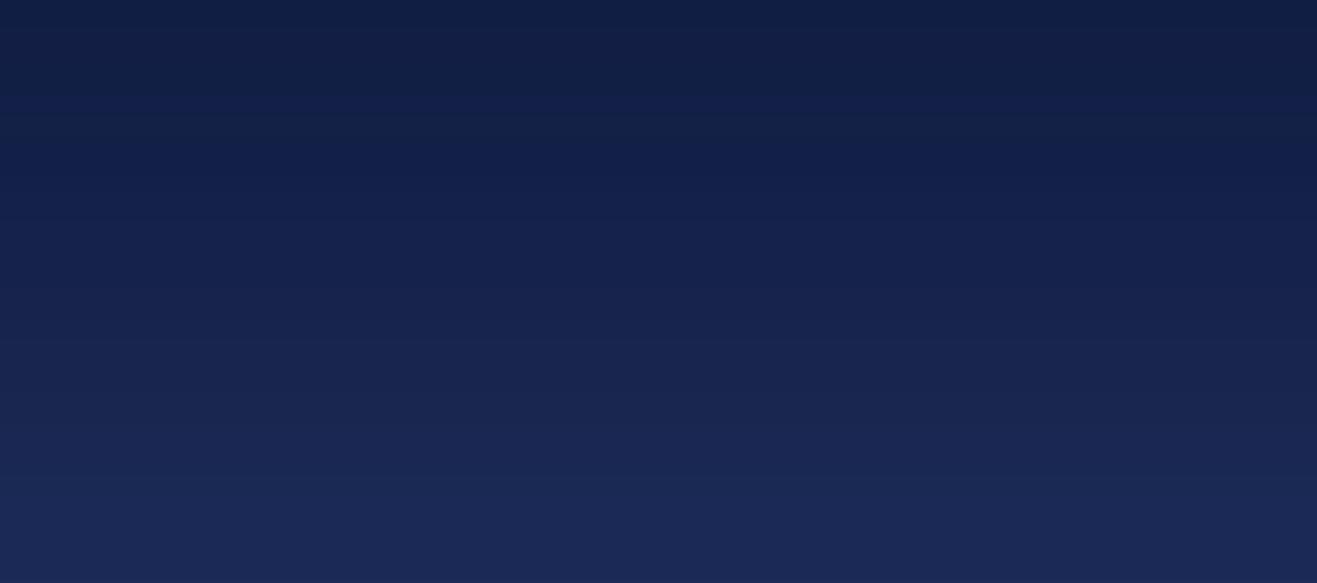

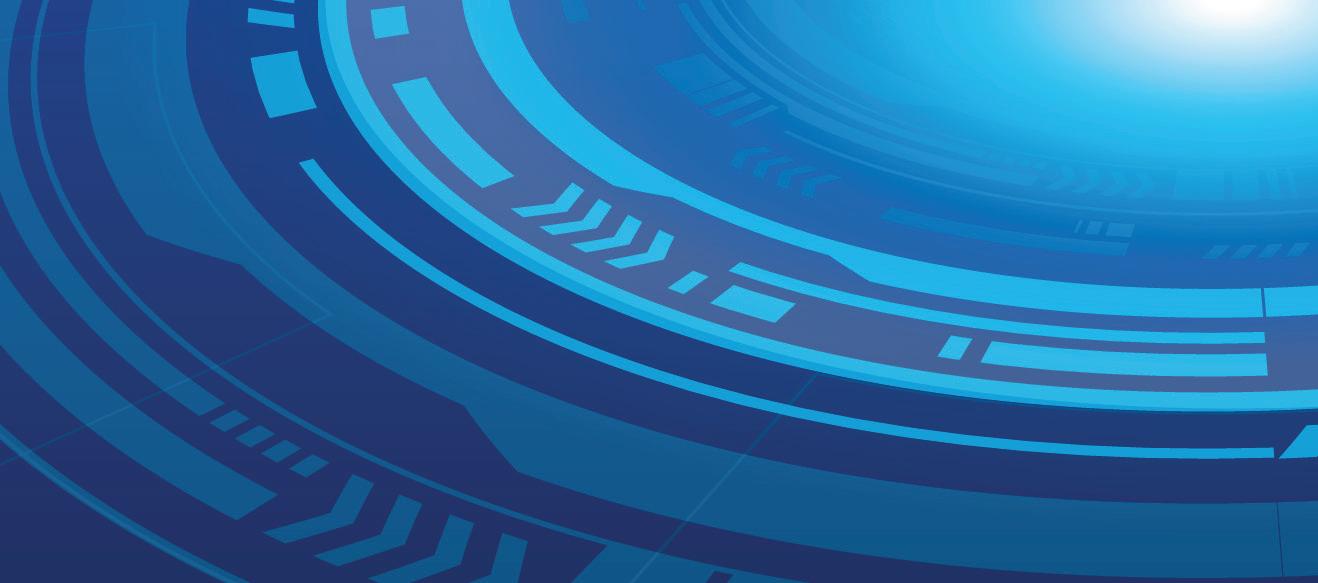
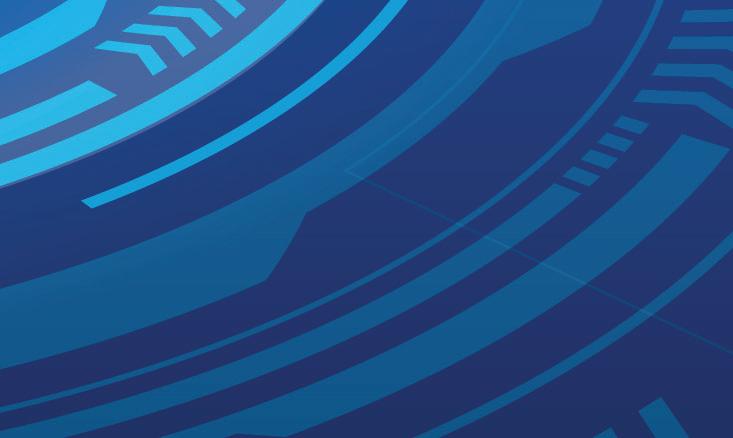
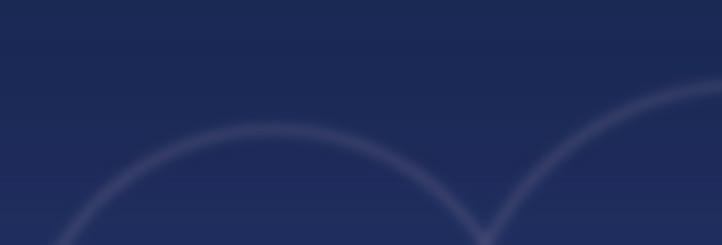





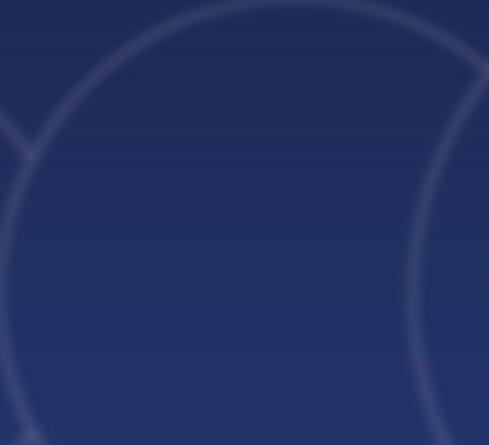
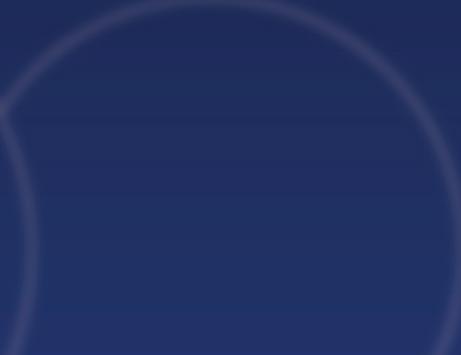
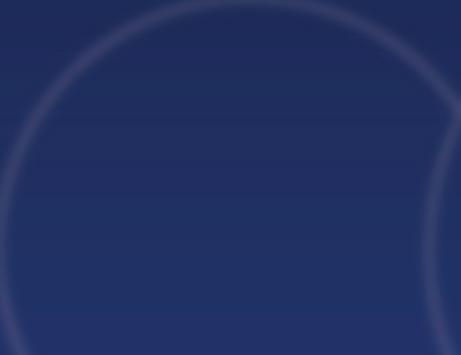
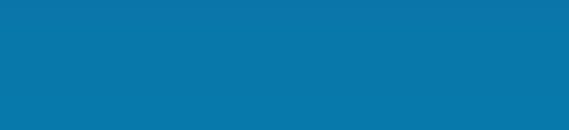


