
14 minute read
Design Notes
Automated foodservice to disrupt restaurant industry
Edited by Mike Santora • Managing Editor
The Hyphen Makeline delivers a modular, industrial-hardened solution to help restaurants put kitchen operations on autopilot.
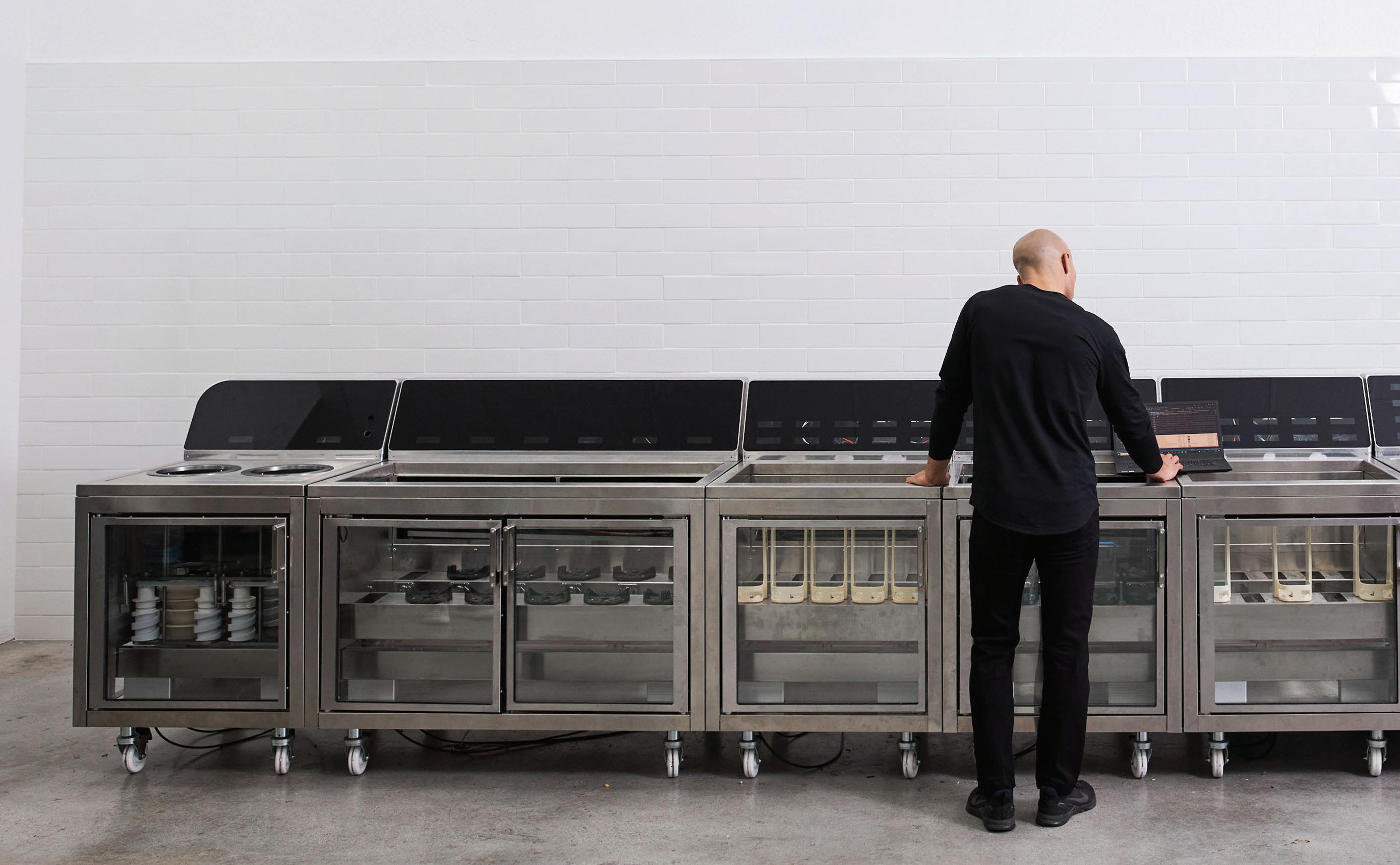
| Beckho Automation
Now an industrial-appliance-sized design called the
Makeline om food services company Hyphen is leveraging so ware, rugged automation, and networked controls to help labor-strapped restaurants meet modern business demands. “We founded the business in July 2018 to leverage automation technology in modern restaurants,” said Daniel Fukuba, Co-Founder and CTO of Hyphen. “Shortly therea er, we built the fi rst completely automated food truck. During the COVID-19 pandemic, we pivoted and designed our new Makeline system to give restaurants the in astructure to adapt toward digital-fi rst ordering.” The Hyphen Makeline assembles salads and other menu items served in a bowl — handling hundreds of ingredients at various temperatures. The system connects to Hyphen’s cloud services to route digital orders via MQTT. A er receiving an order, the Makeline activates dispensers to fi ll the bowls, conveying them through connected modules inside the enclosure. The machine also controls food safety and provides data insights about peak ordering times and customer habits. From the outside, it looks like a traditional makeline, and restaurant staff can still load ingredients and manually serve those who prefer to order in person.
Clean control architecture eliminates messy situations Hyphen wanted the Makeline to fi t into existing restaurant facilities; as Fukuba explained, “You can already buy mature industrial equipment off the shelf to process 300,000 pounds of salad per day. On the other end of the continuum, there are vending machines with
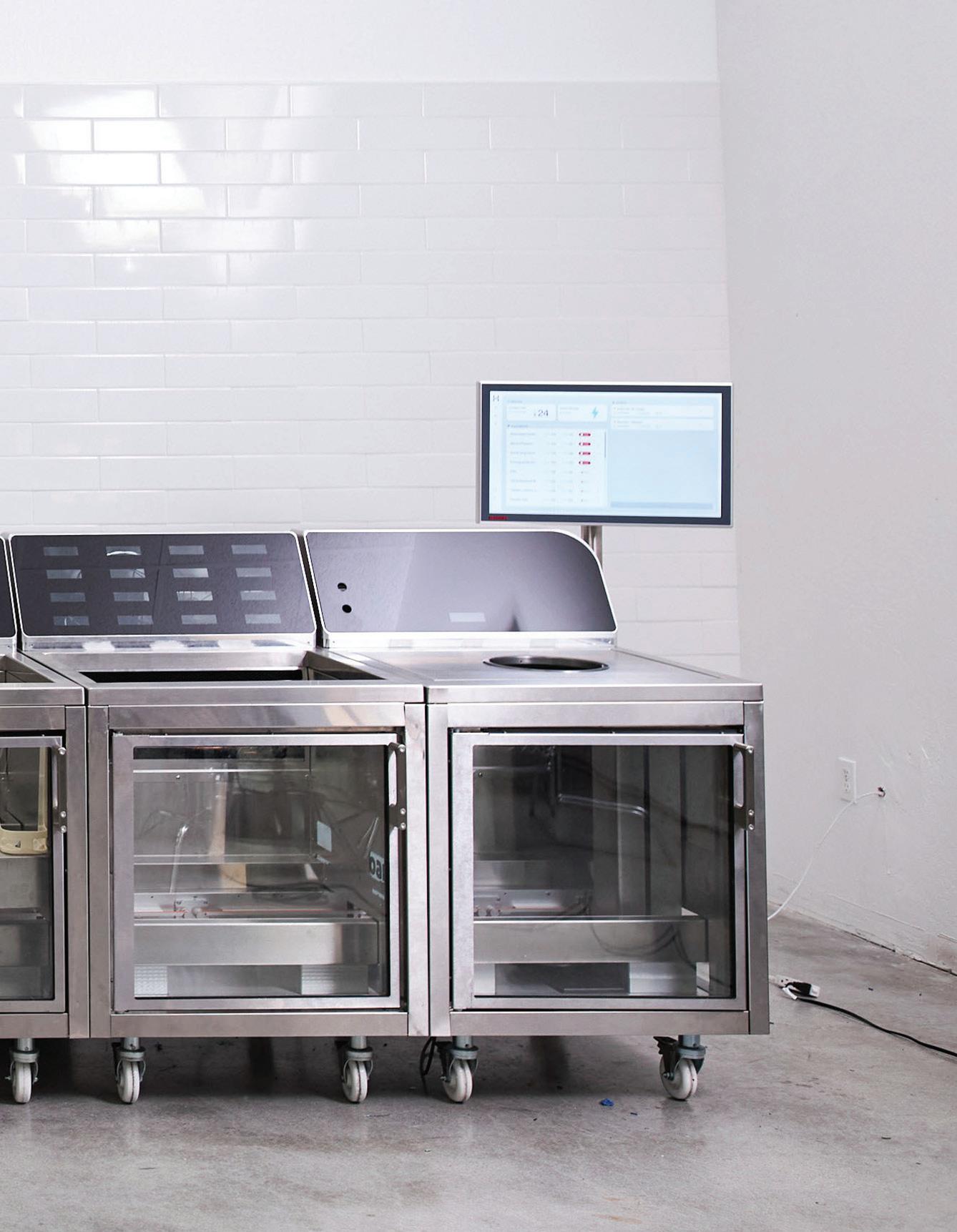

prepackaged goods. In between, there’s no automation to handle the capacities and product variety for restaurant-based food service.” That’s partly because it’s technologically di cult to cram the necessary capabilities into a form factor small enough for standard kitchens. The Makeline must fi t more than 70 actuators plus the cloud-connected controls and I/O into what is essentially a restaurant-grade kitchen appliance. In addition to minimizing footprint, the system needed to meet hygienic standards, and Hyphen also required process controls, time and temperature holding information, and the ability to audit and log the food storage environment. The machines would need to accommodate 500 diff erent ingredients, which all interact diff erently depending on the menu item. In early 2020, the Hyphen controls engineering team started to explore EtherCAT and PC-based control technologies om Beckhoff Automation. “The Makeline’s requirements called for vendor agnostic, easy-to-interface systems,” said Bradley Hwang, Controls
Angled NEMA Cords— Multidirectional Power Made in America
Interpower® offers eight different cord angles with the NEMA 5-15 cord. When limited space makes connecting a cord to the mains power impossible, an angled cord allows just the right angle to reduce strain on both cord and plug. Eight different angles allow cords a path to connectivity. NEMA 5-15 angled cords are critical space-savers for any industry—medical, IT, food service or the office, anywhere tight boundaries push the bend radius of a cord. They work great in accessory power strips where strain reliefs and cable exits may interfere with neighboring outlets.
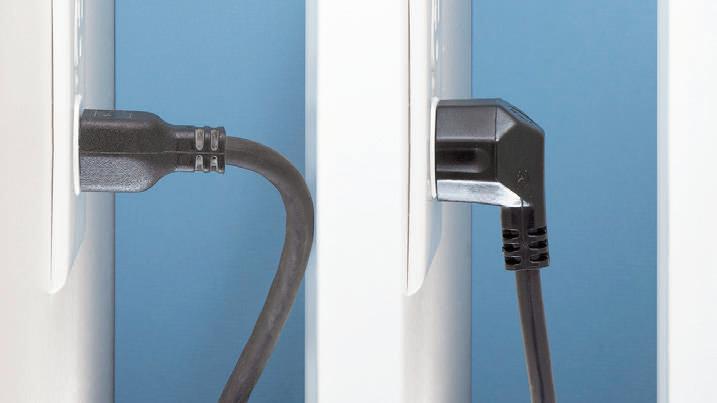
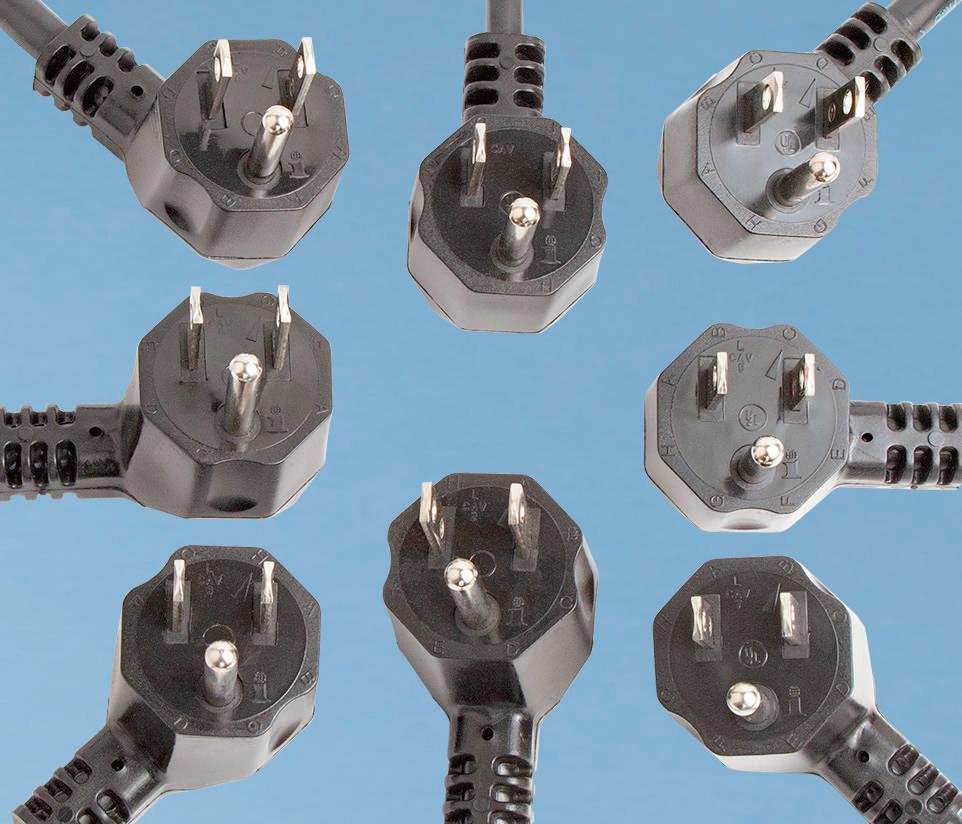
Toll-Free Phone: (800) 662-2290 E-mail: info@interpower.com
Business Hours:
7 a.m.–6 p.m. CST
Order Online!
Design Notes
A C6030 ultra-compact IPC serves as both machine controller and IoT gateway for the Makeline. PC-based automation and EtherCAT technologies from Beckho help the new system from Hyphen make 350 meals per hour with 99% order accuracy.
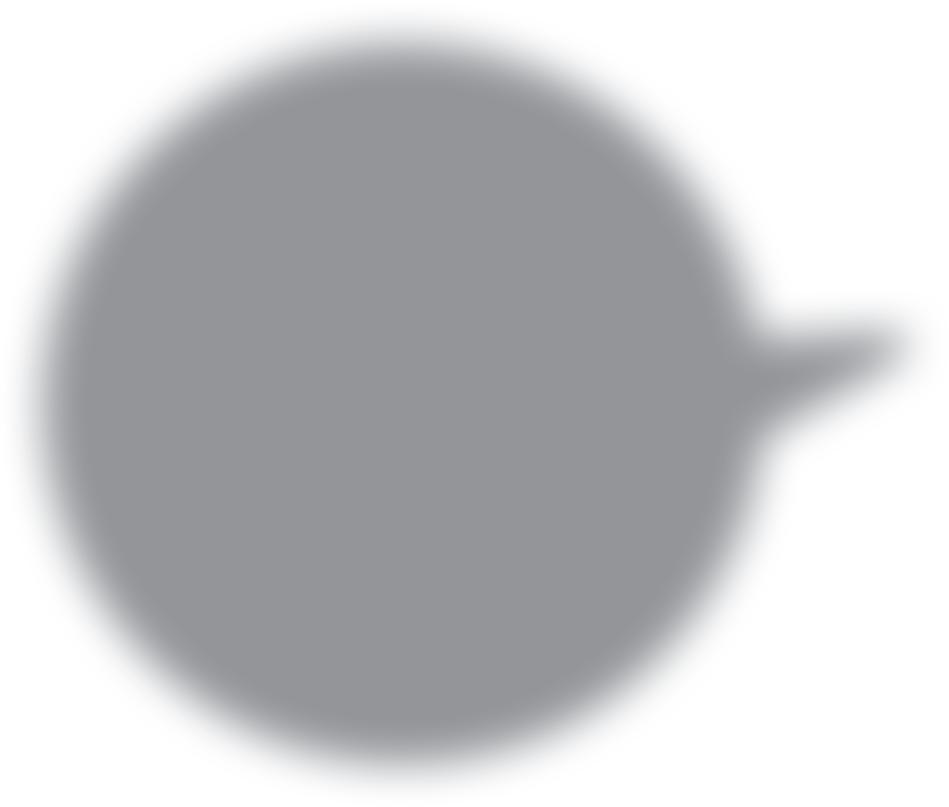
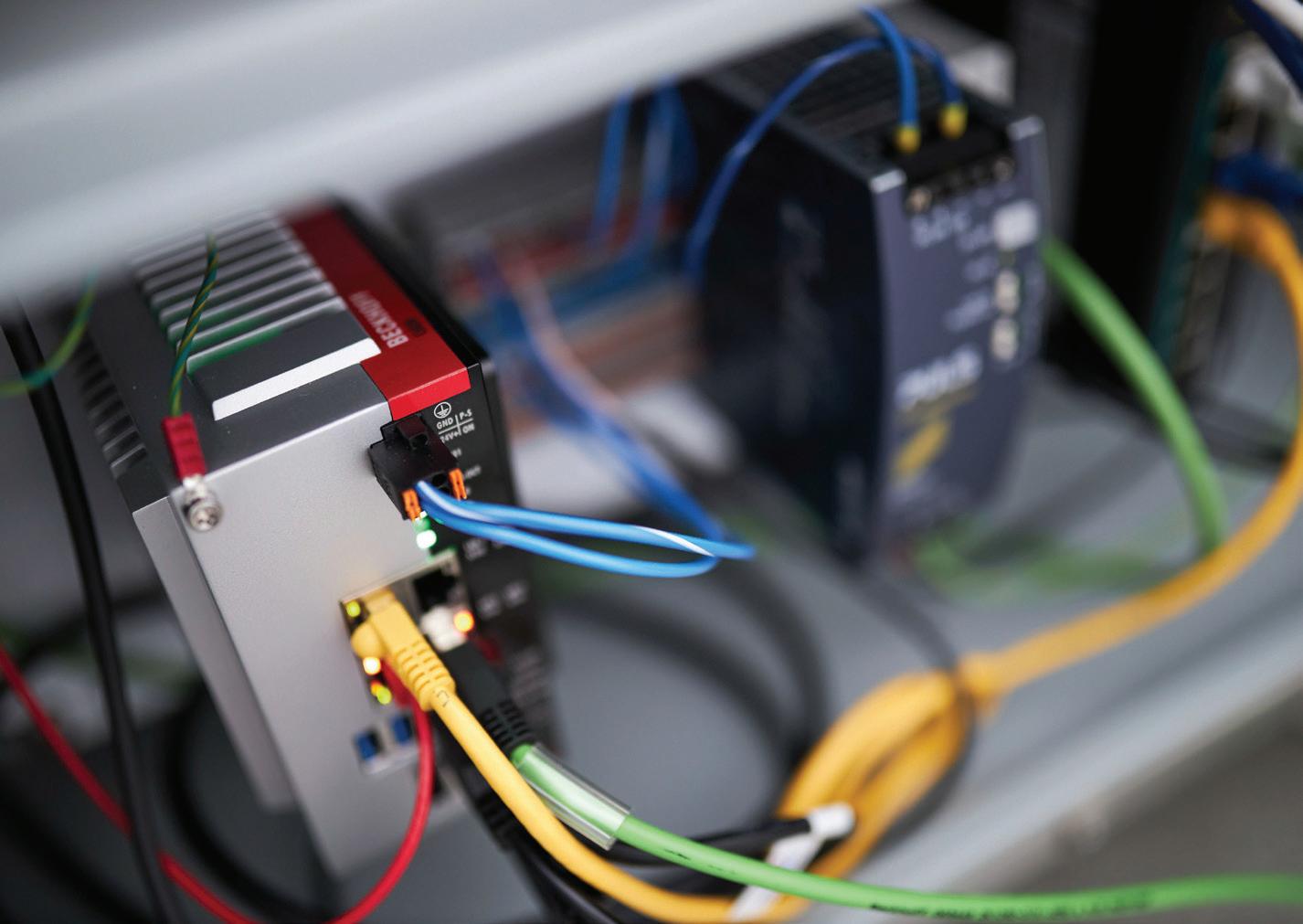
| Beckho Automation

The EJ series I/O Terminals allow Hyphen to implement TwinSAFE functional safety in a pluggable, space-saving form factor.
| Beckho Automation
Engineer at Hyphen. “Beckhoff simplifi ed seamless communication simplifi ed seamless communication om the PLC runtime up to the cloud om the PLC runtime up to the cloud so the so ware team could develop a completely new layer between that and third-party services.” Hyphen engineers and the Beckhoff sales and application engineering team at the nearby Silicon Valley Technical Center collaborated to create a solution.
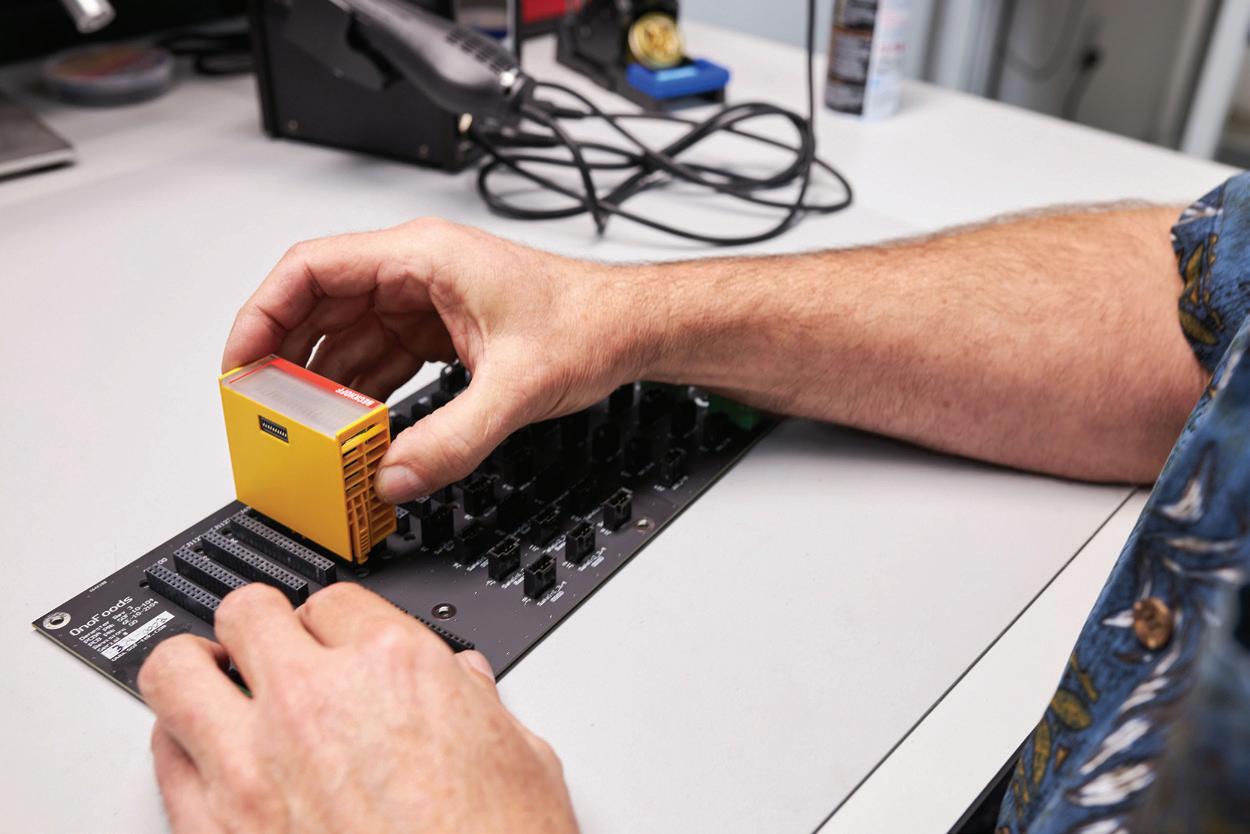
EtherCAT and I/O: more than a slice The EtherCAT industrial Ethernet system proved indispensable for Hyphen. The speed and modularity of EtherCAT helped optimize system communication, and the network doesn’t need switches, which reduced cost and space requirements. Each Makeline module features pluggable EJ series EtherCAT I/O technology for functional safety, which mount to a custom-design PCB board. These pluggable TwinSAFE terminals are roughly 50% smaller than traditionally wired I/O slices and reduce potential wiring errors. “Most industrial electrical cabinets with this amount of I/O are massive, but that wasn’t an option for this product. With the EJ safety modules, we could connectorize communication, power supply, and more on a spacesaving circuit board, allowing easy and repeatable assembly,” Hwang explained. Using TwinSAFE technology om Beckhoff lets engineers apply safety devices for doors and potential hazards in a simple programmable way sans hardwiring needed by traditional safety systems. TwinSAFE uses the Safety over EtherCAT (FSoE) protocol to communicate via a black-channel approach.
Control so ware and hardware serve up performance TwinCAT three automation so ware provided a comprehensive engineering and runtime platform for the Makeline. TwinCAT supports many programming methods. This made it easier for Hyphen to bridge the gap between its controls and app-development technologies. “We want to be able to scale the Makeline om 10 units to 10,000 without having to scale the workforce proportionally,” Hwang said. “TwinCAT allows us to use Structured Text, collaborate with version control, and leverage so ware-oriented processes like GitHub.” The Makeline relies on one C6030 Industrial PC (IPC) for all operations. TwinCAT off ers core-isolation
capabilities to enhance system performance by designating individual processes in the quad-core CPU, such as PLC or IoT, to one specifi c core in the IPC. The C6030 is suitable as an IoT gateway and machine controller. The C6030 resides in a base cell with a CP3924 multi-touch Control Panel. The 24-in. pole-mounted display provides a user interface for the environment, according to Fukuba: “We develop the HMI screens like modern web apps, so the multi-touch capabilities and display fi delity give us the responsiveness that we want in the UI. This user- iendliness means any restaurant employee can operate the Makeline.”
A recipe for disruption Hyphen began conceptualizing the Makeline in mid-2020, and its fi rst units will arrive at design engineers by the end of 2021. The machines can produce 350 meals per hour with 99% accuracy, and it improves portioning precision om the industry average of +/-15% down to +/-2%. The control hardware, IoT, and networking technologies om Beckhoff helped Hyphen deliver the technical capabilities while meeting footprint requirements. The engineering team plans to continue working with Beckhoff sales and support to add more automation technologies in the future and is already testing TwinCAT Vision as a solution for greater quality control and inspection. DW
Beckhoff www.beckhoff .com
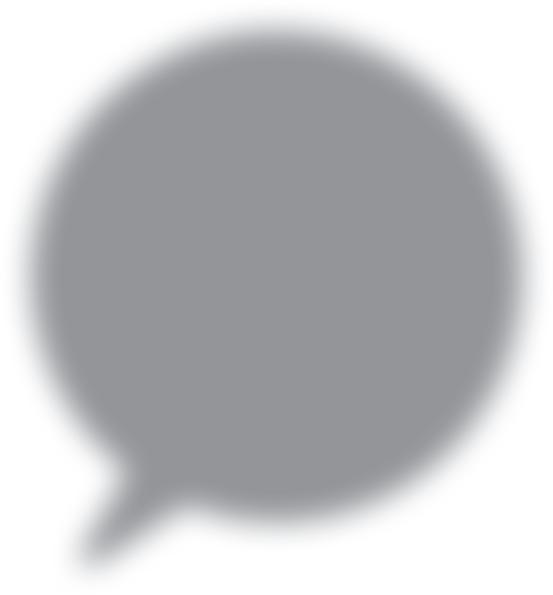
EtherCAT networking and hardware deliver fast cycle times with minimal footprints.
| Beckho Automation

Design Notes
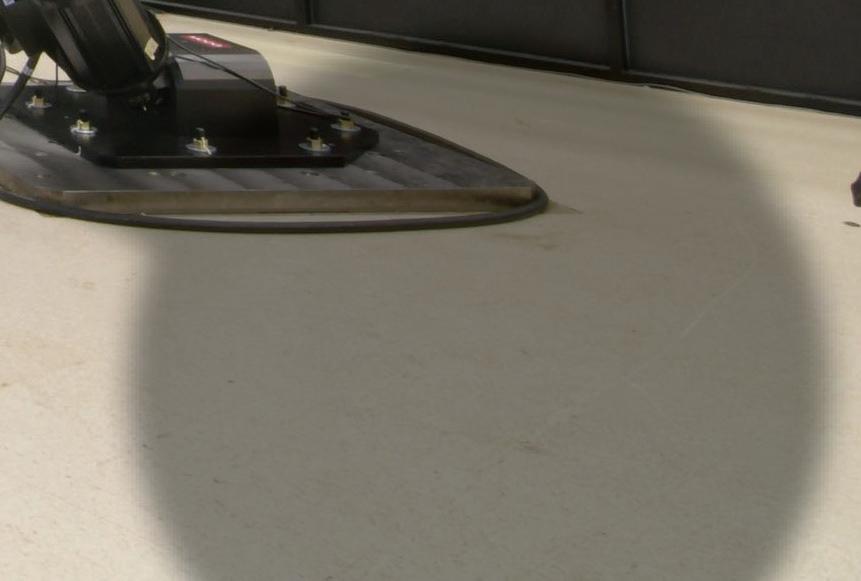
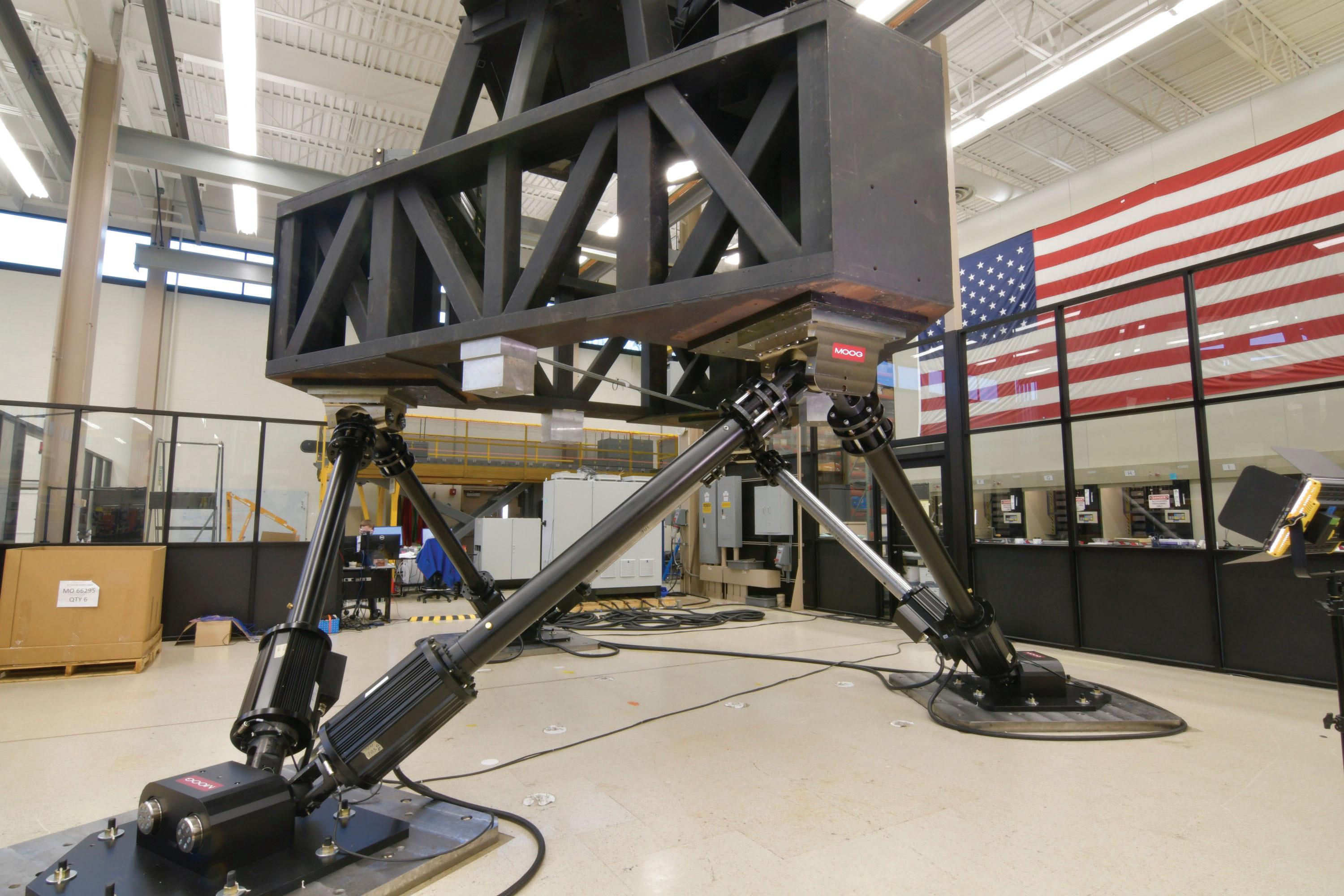
How to build a smart energy management system
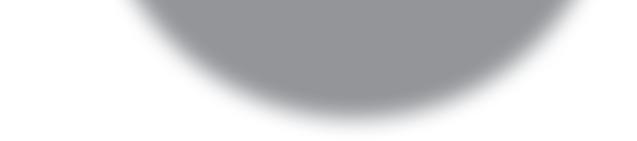
Edited by Mike Santora • Managing Editor
The Moog DE2020 smart energy management system has helped Moog’s Gen3 motion system (designed for certi ing commercial and military fl ight crews and developing motor vehicle designs) reduce surge power by 65% without sacrifi cing performance. With more than 1,000 motion systems installed worldwide, Moog’s team drew on this experience to develop not only the new Gen3 motion base but also the DE2020 technology. With the DE2020 system, engineers used proprietary Moog technology in Formula 1 race cars to design an energy recovery system for the Gen3 motion system. The system absorbs the short-term energy bursts that occur with fl ight simulation and vehicle design for later use. The DE2020 eliminates the need to size electrical power to handle peak loads, even if the peaks rarely occur during a work cycle. The result saves energy, reduces costs, and streamlines cable design and power connections for Gen3 motion system users. “During normal operations, a motor or motion system generates a regular load. But during acceleration, a system requires more short-term energy, while the release of energy om mechanical inertia or braking mostly converts to heat without being used,”
said Tim Herget, a staff systems engineer for Moog. The DE2020 system meets peak loads by drawing power om the Gen3 motion base’s capacitor banks while using energy gains om braking and mechanical inertia to recharge the capacitors. By doing this, the DE2020 prepares the capacitors for the next peak. This system can also compensate for fl uctuations in the mains by using a prefi lter in combination with the capacitor bank. Or, in the event of a sudden power failure, the DE2020 can supply the Gen3 system with enough energy to reach the safe return to home position. The Gen3 control cabinet, half the size of prior designs, houses Moog’s DM2020 multi-axis servo drive, which controls the motion system’s actuators. Moog engineers achieved the compact design using a common DC bus managed by the DE2020 system. The DM2020 ensures high speeds and faster cycle times through a control board and so ware that handles various motor and actuator types. The DM2020 synchronizes the axes through an EtherCAT connection between the modules; with a standard DC bus confi guration, the DM2020 enables an energy exchange between the axes, reducing energy consumption. The Gen3 motion system also uses Moog’s fastest, most-recent planetary roller screws, which carry high loads while precisely accelerating or braking. Depending on the type of payload the Gen3 system underpins, its actuators can move approximately 15 tons om 2.2 meters (7.22- ) to 4 meters (13- ) and tilt the payload +/- 27° at a rate of 70 cm (28-in.) per second. Moog engineers expect the Gen3 system to reduce unplanned maintenance by approximately 22% and provide users with more than 99.5% uptime. “In redesigning the Gen3 system, we evaluated every component, especially the actuators, to ensure that the motion system contains fewer parts and customers can easily swap out or repair worn components,” added Herget. “Customers can replace the dampening elements during operation without removing or recalibrating the actuator. The power connection and encoder assemblies are replaceable too.” Moog engineers see the DE2020 and DM2020 technology improving other applications for industrial automation, test benches, handling, robotics, or replacing hydraulic and pneumatic systems at an industrial facility. DW
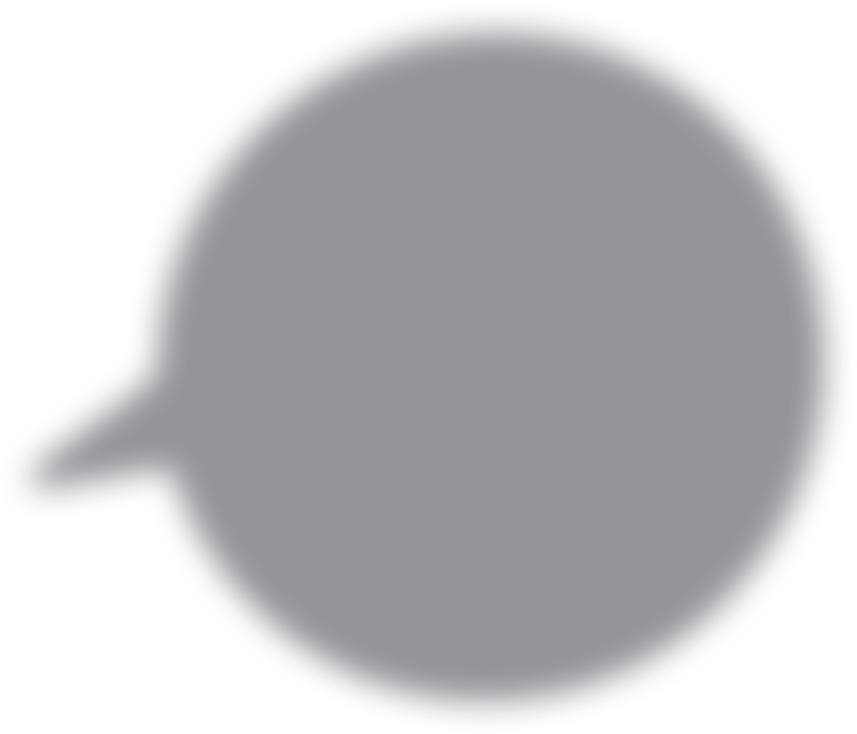

Moog engineers expect the Gen3
Moog | www.moog.com
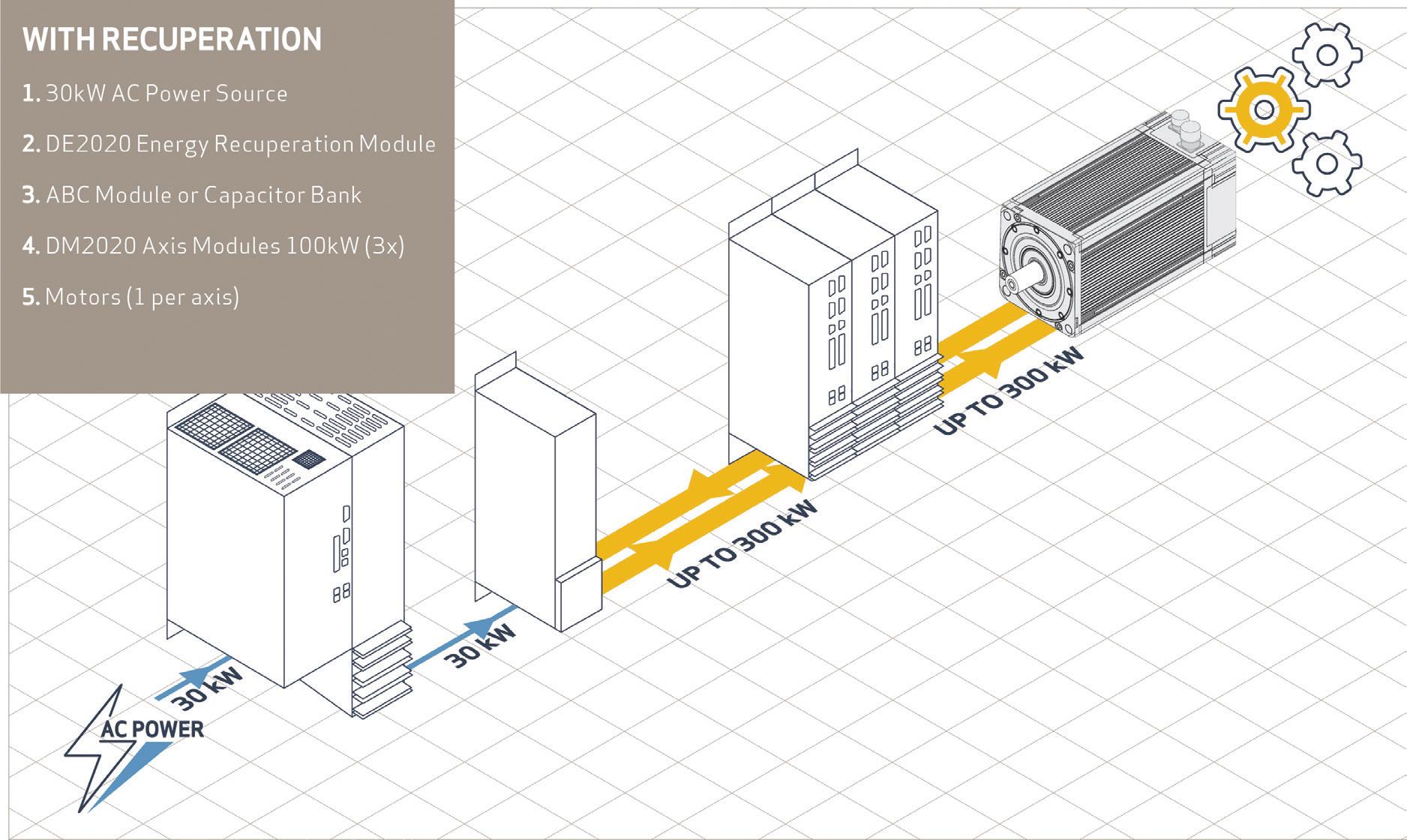
Design Notes
Tokyo Denki University.
Magnetic encoders help two-wheeled robotic vehicle stay balanced
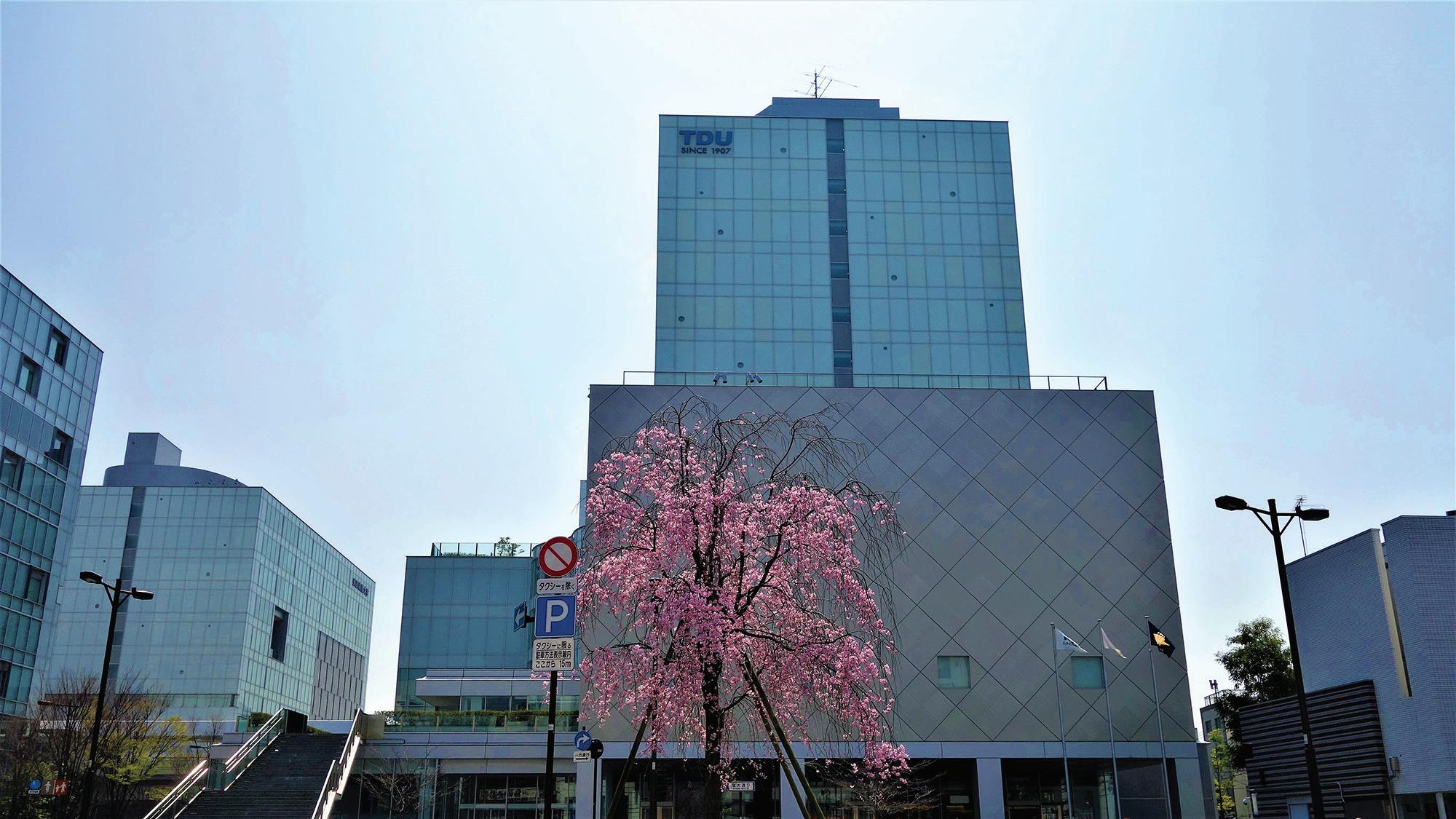
Edited by Mike Santora • Managing Editor
In the design of a self-balancing two-wheeled robotic vehicle, accurate highspeed measurement of angular rotation is a key requirement. Furthermore, minimizing component weight and size is an equally vital consideration. Engineering students at Tokyo Denki University found the answer in the RM08 rotary magnetic encoder om Renishaw’s associate company, RLS.
Background Tokyo Denki University was established in 1907 by two young engineers, Seiichi Hirota and Shinkichi Ogimoto. Their founding principle was to promote engineering education as a basis for national economic development. Working in the University’s Robotics and Mechatronics Department, Jun Ishikawa is a researcher in several technological fi elds, including robot control system development. He challenged his engineering students to create a two-wheeled, self-balancing robotic vehicle. For this project, his students chose the RM08 rotary magnetic position feedback encoder om RLS.


Background Ishikawa asked the university students to solve a classic control theory problem — the inverted pendulum. The basis for the wellknown Segway personal transporter, the inverted pendulum, has its center of mass located above the pivot point. Unlike a suspended pendulum, which will naturally return to a stable equilibrium position a er being displaced, the inverted pendulum is inherently unstable. Imagine holding a pool cue or a broom handle upright on the palm of your hand — it would tend to fall over without continuous adjustments to the position of your hand. A shorter inverted pendulum accelerates away om the vertical position faster than a longer one, requiring more equent position adjustments and presenting a more challenging control problem — balancing a pen on your hand is trickier than balancing a pool cue. One solution to the problem, as implemented by Segway, is to mount the pivot point on a wheeled platform. This type of vehicle takes inertial inputs om an IMU (inertial measurement unit) which comprises two sensors: an accelerometer and a gyroscope. In this case, both vertical-axis and horizontal-axis accelerometers are used to determine the angular acceleration due to gravity. By constantly monitoring the pendulum’s tilt angle and angular velocity,
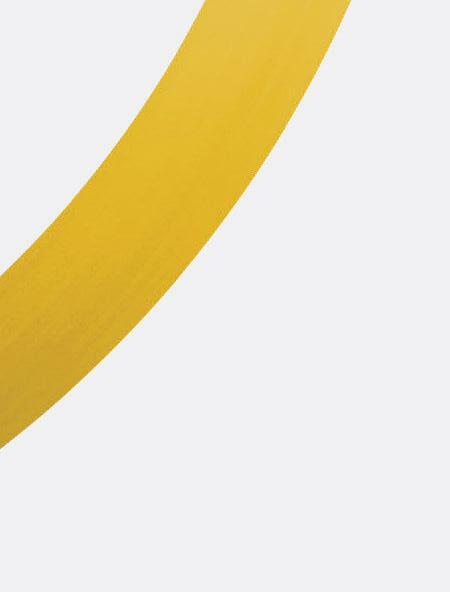
OPTIMIZE YOUR DESIGN
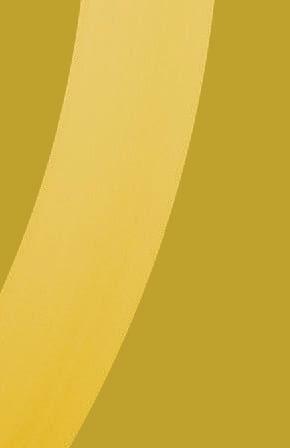
We make it easy to take your design further with a custom ring or spring.
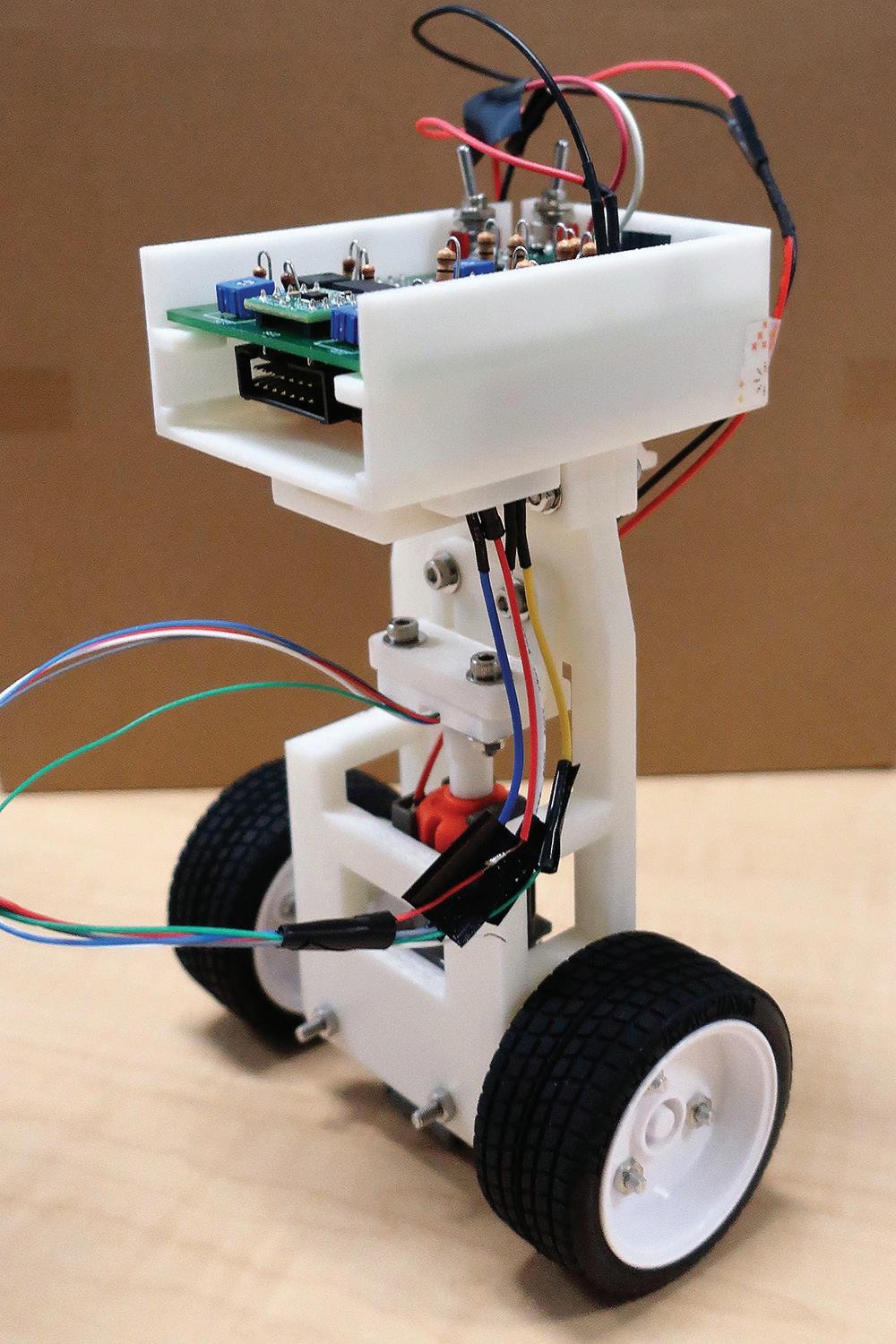

The two-wheeled, self-balancing robotic vehicle designed by the engineering students at Tokyo Denki University.
• Economical Prototyping (No-Tooling-Charges™) • Quick Lead Time • Diameters from .118” to 120” in 40+ Materials • Industry-Specialized Design Support Industry-Specialized Design Support
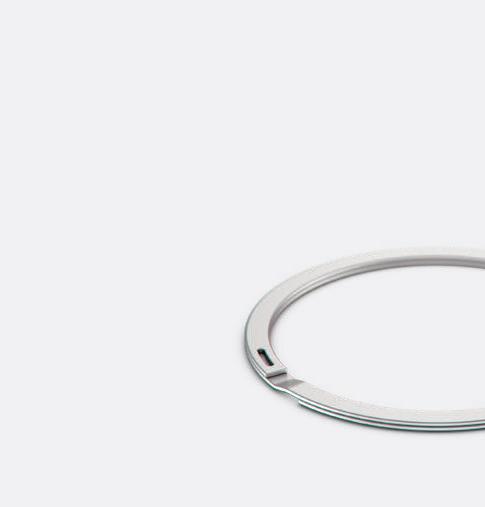
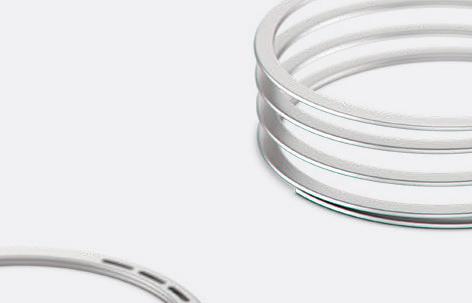
Custom Retaining Rings and Wave Springs

Design Notes
The encoder coupled to the motor shaft.
a PD (proportionalderivative) control system can be used to drive the wheels forwards or backward to maintain balance. Adopting a similar approach in their own control system, Ishikawa’s students needed to design and integrate what was eff ectively a three-part solution, comprising tilt-angle sensing, control logic, and motor drive circuitry. When designing PCBs for this control application, small size and low weight are crucial for integration within the handlebars. PCB architectures have been optimized to ensure that all the required functionality is delivered in the smallest package size.
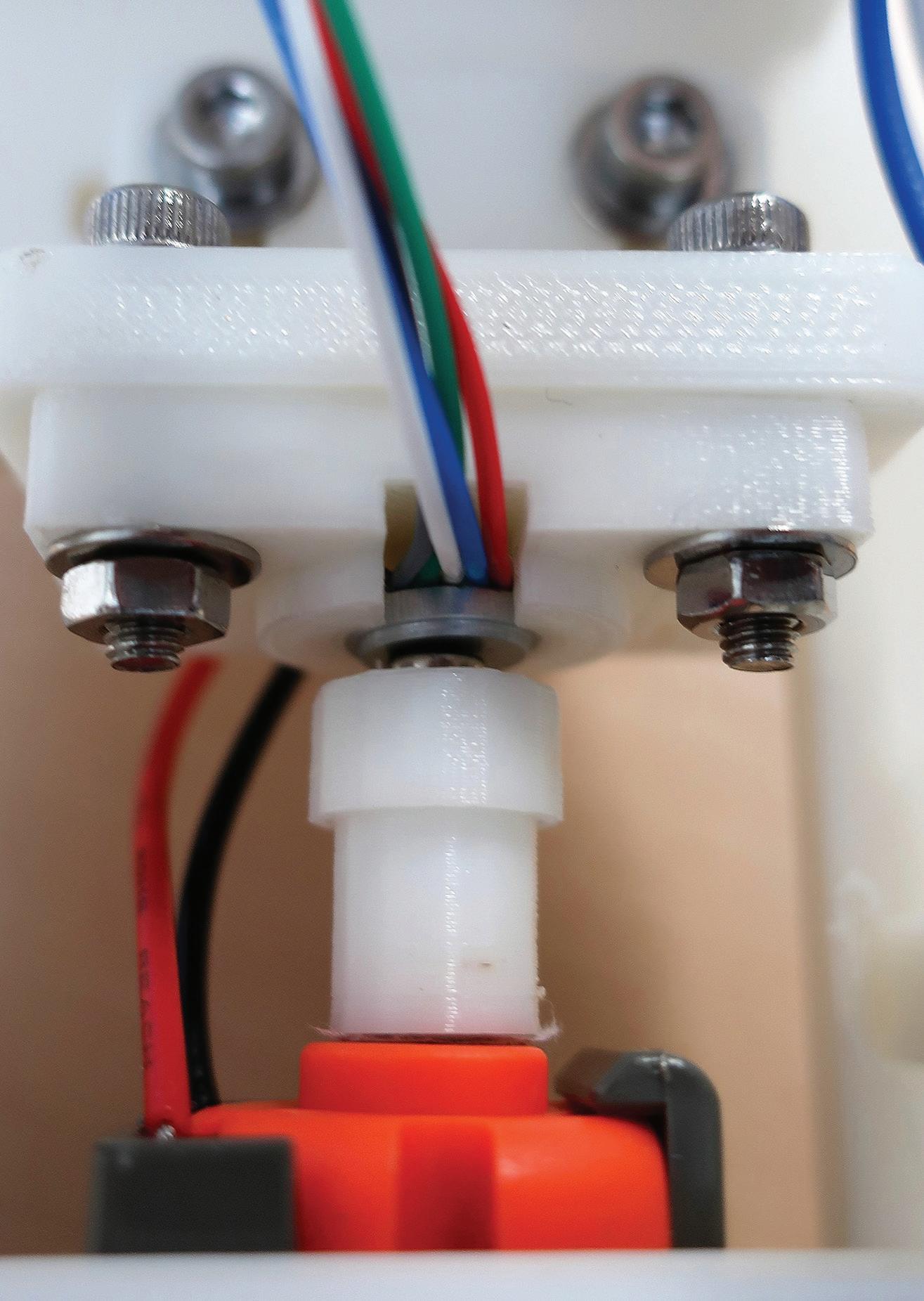
Solution The PCB control board sits at the top of the pendulum, inside the handlebars, and carries all the electronic circuitry required, including a solid-state gyroscope, microcontroller, DC motor drive, and power management components. In the wheeled platform, at the bottom, there are two axles: a horizontal axle linking the wheels and a vertical axle driven by a compact DC motor. Simple bevel gearing at the intersection between the axles enables the motor to drive the wheels in either direction. For eff ective control, the system must maintain orientation within a small range of angles that are nearly vertical. If the vehicle tilts by more than 30° in either direction, stability might be lost. To maintain the vehicles balance, the wheels must be driven continuously with carefully calculated acceleration and speed. To achieve the required level of motion control performance, the students needed a high-resolution position encoder to enable monitoring and regulation of the motor output. It also had to be small and light enough to accomodate the vehicle’s slim vertical structure. A er much consideration, the solution came in the shape of the RM08 rotary magnetic encoder om RLS. This noncontact, ictionless rotary magnetic encoder weighs just 2 g, including cabling, and has an aluminum sensor housing measuring 8 mm in diameter with a thickness of only 3 mm. The students designed a narrow nylon collar to act as a mechanical linkage between the motor sha and the magnetic actuator of the RM08 encoder, which added less than 0.5 g to the assembly. The RM08 encoder produces a 12-bit resolution output (4,096 steps per revolution), is suitable for high-speed operation up to 30,000 rpm, and delivers an accuracy of ±0.3 º. Results Using the RM08 high-speed rotary magnetic encoder to measure angular rotation at 12-bit resolution, the students could design a motion control scheme for a two-wheeled robotic vehicle capable of self-balancing and staying upright. The RM08 encoder is IP68-rated and designed for integration into a wide range of high-reliability, high-volume OEM applications. Importantly, the rotary magnetic encoder also addressed the vehicle’s demanding physical design constraints. Being a highly compact and lightweight component, it helped the students overcome space and load-carrying limitations. DW
Renishaw www.renishaw.com