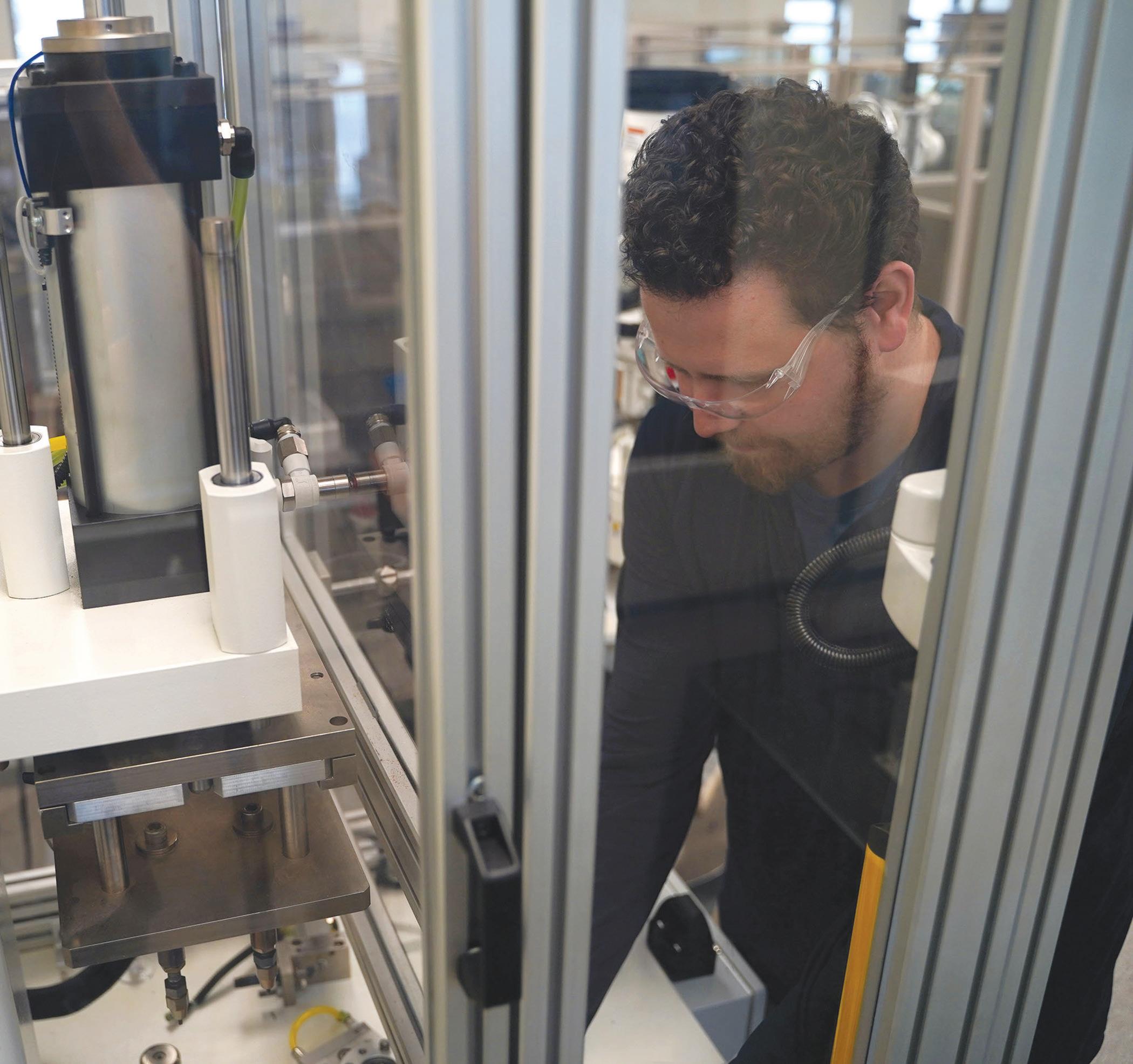
2 minute read
How to choose the proper fastener when automating
Christie Jones Director of Marketing, Vice President SPIROL International Corporation
Fasteners are as important in automation as the equipment itself. Choosing the ideal fastener can prevent exorbitant machine and fixture costs, decrease set-up and cycle times, and reduce the manufacturing cost of the components.
Of course, not all fasteners are easy to orient, feed, or install, and the more tooling necessary for these tasks, the pricier the equipment. It’s important to select a fastener that meets the application requirements and is conducive to automation to maximize productivity and minimize costs.
The design stage of the assembly is where decisions are made that will make or break the success and ease of automation. A common mistake is letting the cost of the fastener take precedence over the cost of fastening. Money saved on the fastener can quickly be lost on intricate automation equipment — decreasing productivity via increased assembly cycle times and equipment downtime.
Ideally, companies should focus on parts with the lowest installed cost. Typically, these are permanently installed fasteners pressed into (rather than threaded into) a hole, requiring no secondary operations for retention.
There are a few additional factors to consider when automating fastener installation.
• The length-to-diameter ratio of the fastener is critical. Any part with a length-to-diameter ratio of less than 1:1 can be problematic because the parts in the feed tube can tumble and jam.
• Fasteners should be clean and sorted. Dirty fasteners cause some parts to stick in the feeder bowl and the feed tube. Improperly sorted fasteners can jam the insertion equipment. Time is money, and both are wasted if the machine must be disassembled to clear the jam.
To ensure successful automation, design engineers and assemblers should become familiar with the features of fasteners.
Consider the symmetry
Non-symmetrical fasteners are often challenging to automate, requiring end-to-end orientation. This means more costly tooling than for symmetrical fasteners.
If using conventional automating methods, headed parts should hang by the head. A good rule of thumb is to ensure a minimum 20% differential between the head and body diameter to provide enough distinction for orienting and hanging the parts. If the diameter differential can be held between 20 to 30%, it’s possible to avoid additional tooling costs.
By considering the fasteners early during the design stage of an assembly, companies can implement automatic fastener installation at the lowest installed cost.
Headed parts with no consistent head diameter or inconsistent beneath the head tend to get jammed on the feed rail. Flat heads are better than round heads for automatic installation. This is because pressing a flat insertion quill onto a flat (instead of round) surface is easier while keeping the fastener straight.
The additional cost to feed, orient, and install headed fasteners make it fundamental to ensure the application requires a headed fastener before specifying one.
Non-headed, non-symmetrical fasteners must also have differential to use the typical feeding method of hanging on a set of rails. This differential can be a 20% difference between the body and feature diameter or a significant weight imbalance of at least 10% between the ends of the fastener. When put in a set of rails,