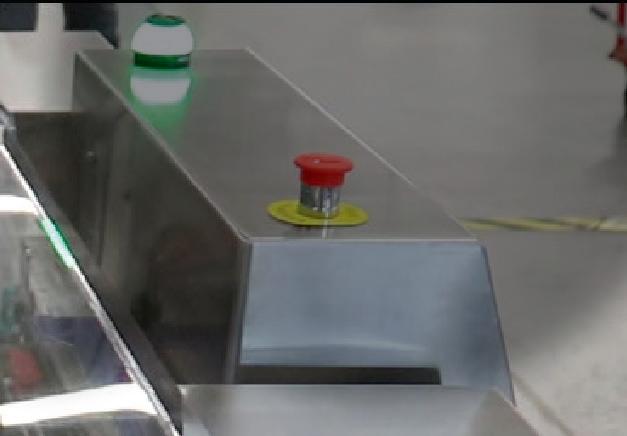
20 minute read
Design Notes
Upgrading a dairy company’s production safety
Edited by Mike Santora • Managing Editor
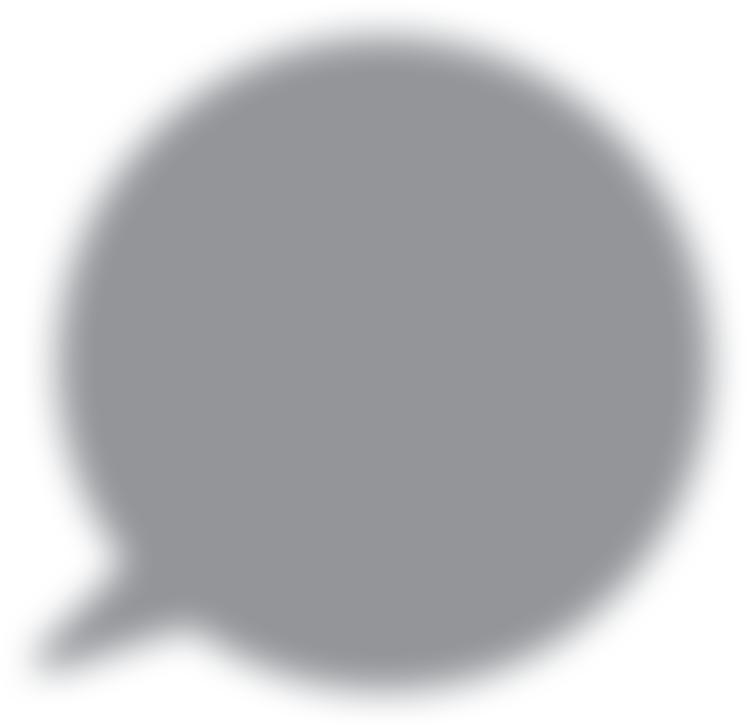
Fortress Technology installed this twin aperture Stealth metal detector and dual-lane Raptor 200 checkweigher to integrate with a dual-head VFFS bagging system for a leading dairy producer.
When a leading North American dairy plant needed signifi cant space and cost savings for packaging its shredded cheese, they worked with Fortress Technology to fi nd a solution. The Fortress Technology team custom-engineered the twin aperture Stealth metal detector and dual lane Raptor 200 checkweigher. The twin lane conveyor confi guration consolidates a single metal detector divided into two apertures and two independent, weightverifi cation Raptor checkweighers for optimized quality control. Each technology and lane have their own air-blast reject mechanism to isolate metal contaminants and weight rejects, helping to reduce product waste by over 50%. Measuring 10- in length, Fortress also integrated a radius conveyor into the metal detector infeed. For the producer of some of the world’s most iconic cheese brands, compromising on metal detection sensitivity was not an option. Explaining the benefi ts of the multi-aperture metal detector concept, Fortress Technology spokesperson Eric Garr explained, “Compared to the alternative multi-lane contaminant detection and combination systems on the market, the high-spec Fortress multi-aperture system was engineered specifi cally to ensure that that there was no trade-off in performance and metal detection sensitivity. One of the key benefi ts of a twin aperture system is the halving of waste caused by rejects.”
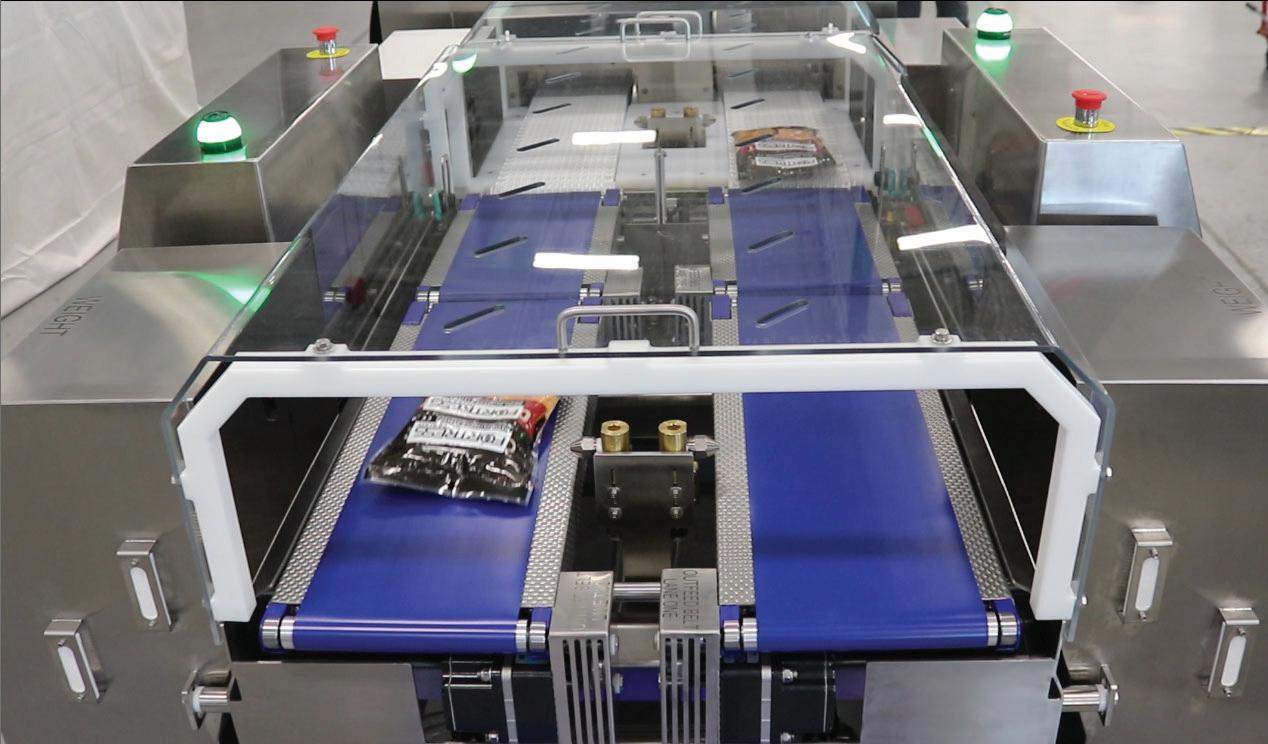
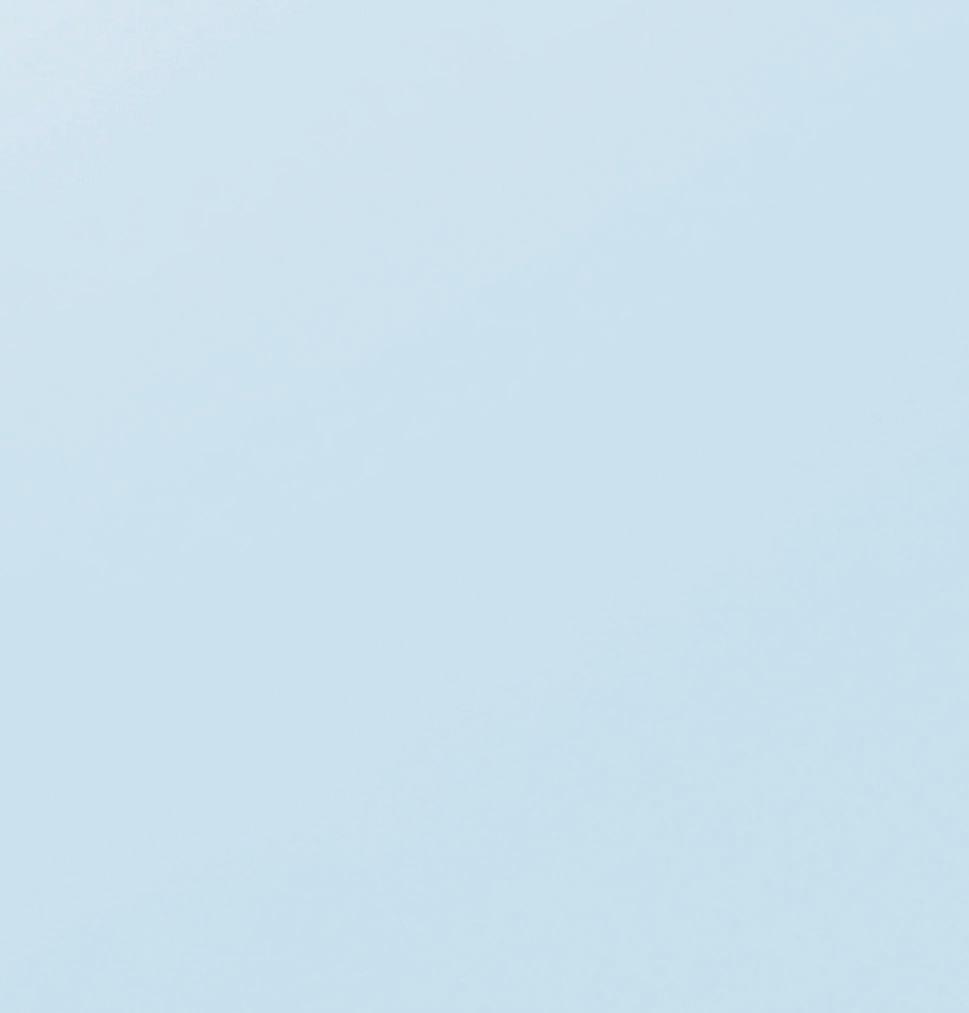
The special dual-lane version of Fortress Technology’s multi-aperture metal detector comprises a single unit split into two smaller dedicated apertures for each lane that act as independent metal detectors. Optimal metal detection sensitivity of the two compact apertures — measuring 4-in. by 10-in. — means that the packs pass individually through the center point of the metal detector. Fully integrated with the dairy plants’ upstream and downstream equipment and matching the 120-140 ppm output speed of the dual-head VFFS bagging system, the compact geometry of the customized radius conveyor facilitates the positioning and orientation of product packs as they round the corner towards the metal detector. Providing optimal spacing between product packs as they are presented to each metal detector aperture helps to avoid congestion, bottlenecks, and fl exible packaging formats overlapping — leading to distorted weight verifi cation checks. Each lane is programmed to run independently; the bespoke design helps minimize interruption to the packing process during product switchovers. Additionally, the design gives the plant increased inspection and weight verifi cation capacity, as two diff erent product lines, pack sizes, or SKUs can be run simultaneously adjacent to each other. Air blast nozzles between the two outfeed conveyors e ciently and independently remove contaminated product into lockable reject bins equipped with reject confi rmation and bin full sensors. “For lighter weight packaged applications like shredded cheese, an air blast reject is the most e cient and has fewer moving parts. Contaminated products are instantly removed off the conveyor belt without disrupting production,” stated Garr. Fortress would typically suggest using a pusher or retracting belt mechanism with heavier products. Delivering dynamic weight monitoring with minimal customizations to existing product feed and packing lines, the hygienic dual-lane design also targets operational ine ciencies, notably upstream product giveaway, nonconforming food packs, and packaging waste.
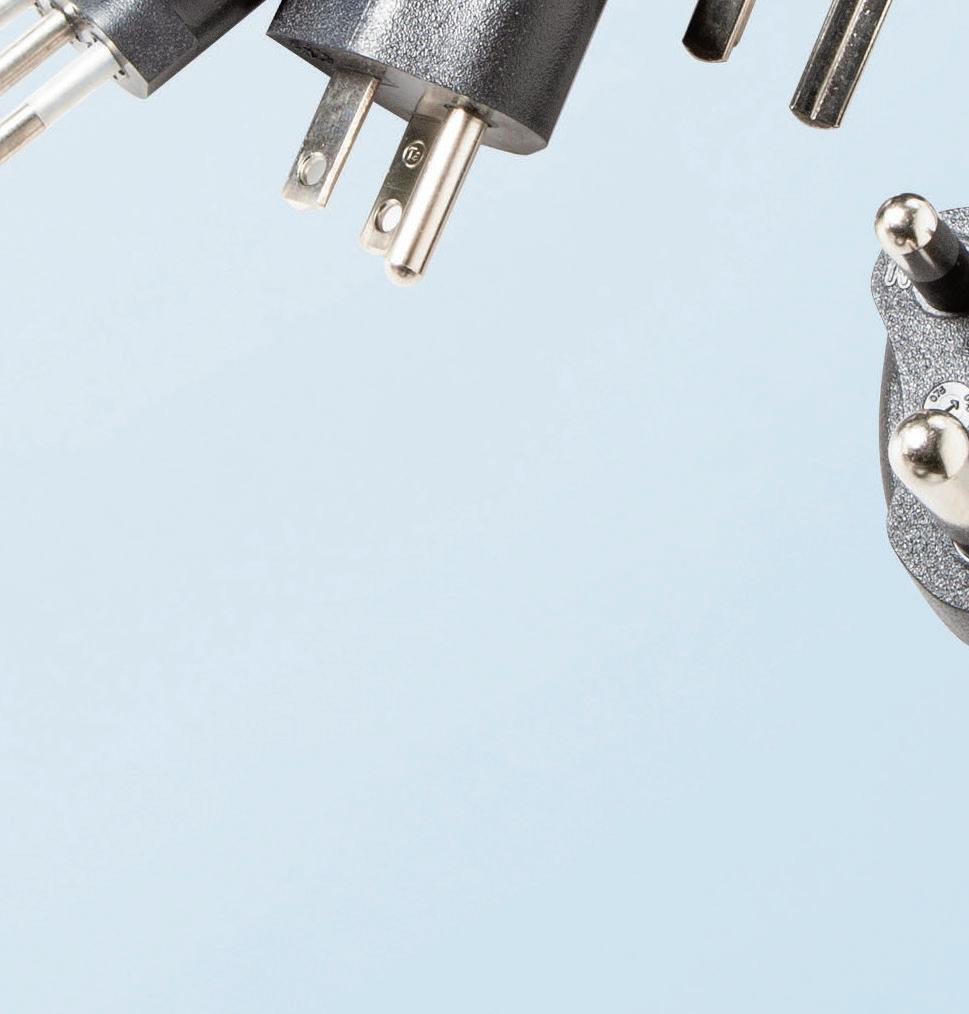

A single metal detector is split into two individual apertures for each lane to ensure metal detection sensitivity isn’t compromised.

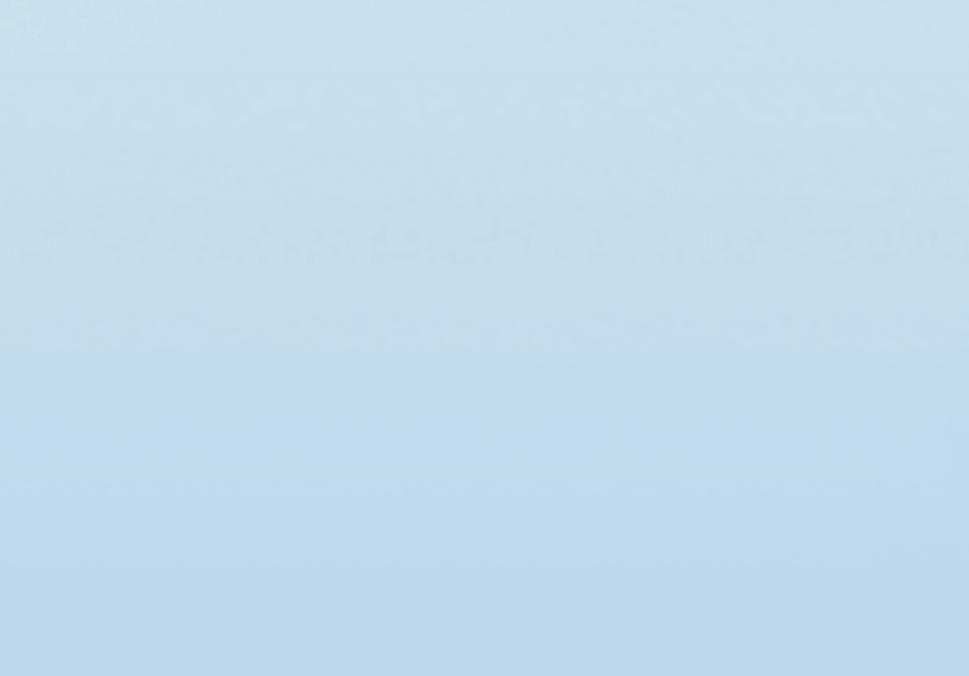
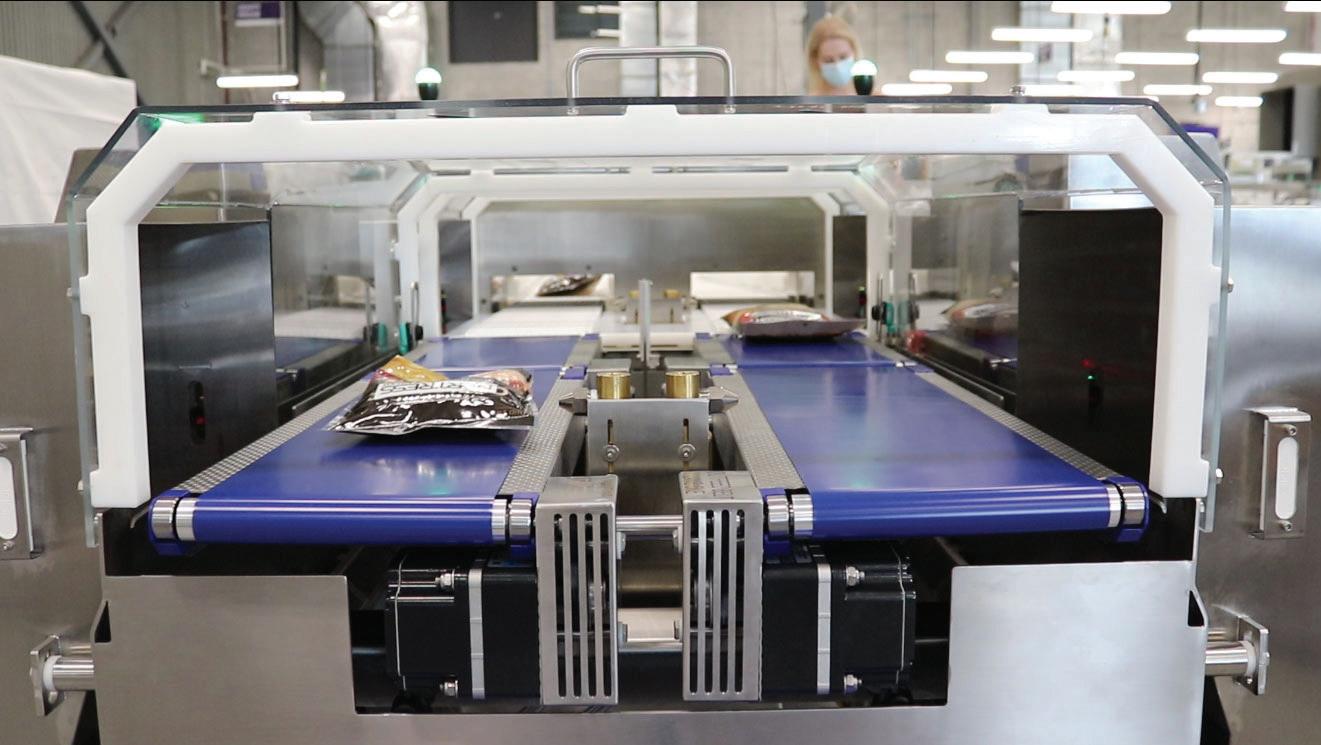
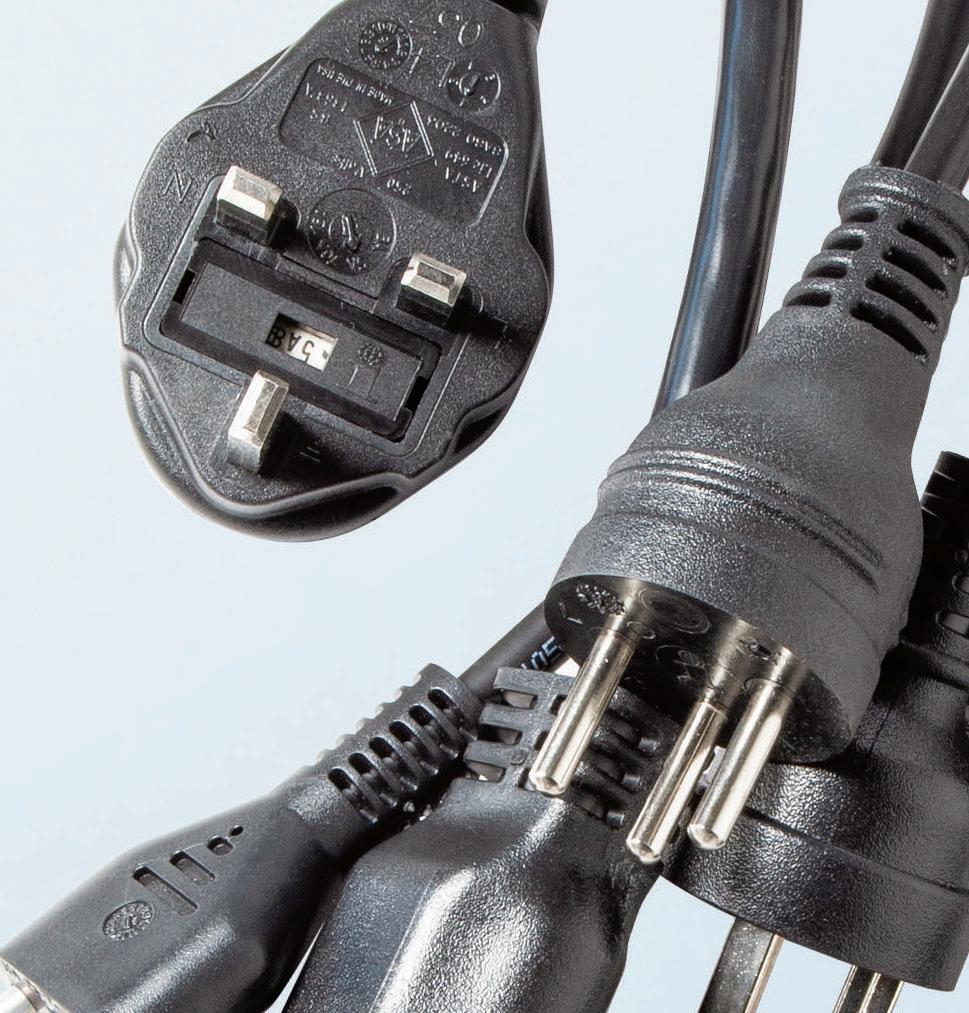
Interpower® North American & International Cords Made in America!
Interpower North American and international cords provide end users with the correct countryspecific amperages and voltages right out of the box. Interpower cords and components are manufactured in accordance with Interpower’s product quality plan: hipot testing, continuity testing, ground testing, and inspections after each process. Interpower also offers value-added options including customized cord lengths, colors, packaging and labeling with no minimum order requirements. Manufactured in Oskaloosa and Lamoni, Iowa!
Toll-Free Phone: (800) 662-2290 E-mail: info@interpower.com
Business Hours:
7 a.m.–6 p.m. CST
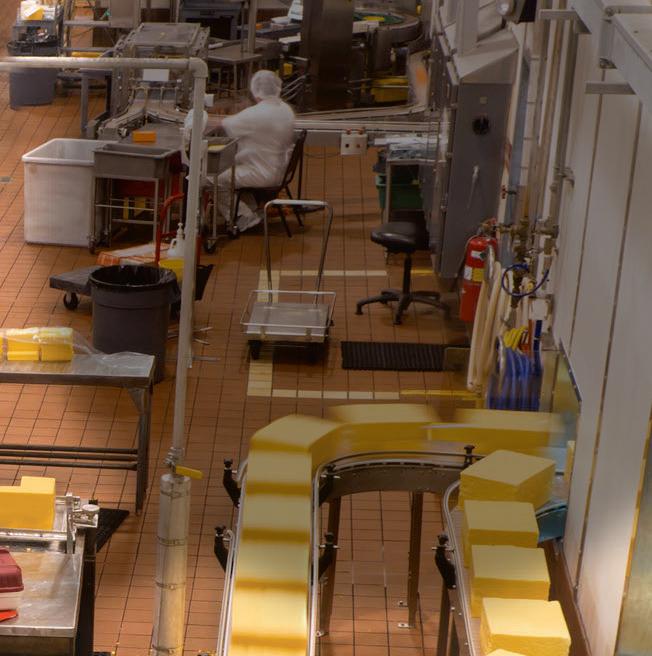
Design Notes
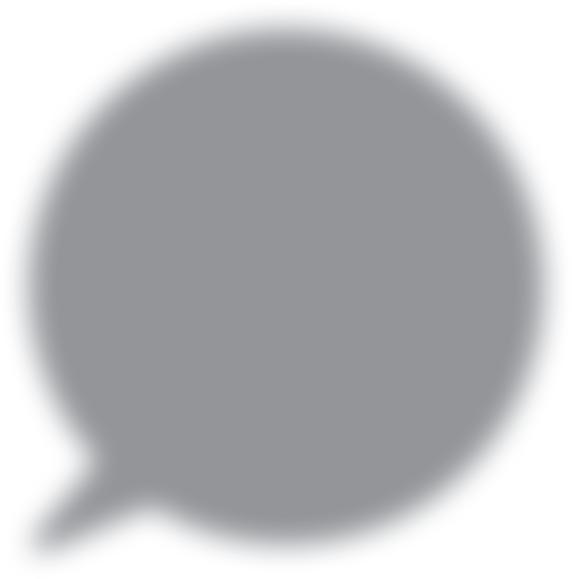
Two packs can pass over two Raptor load cells to weigh, analyze, capture, and report data in milliseconds. For ease of integration, air blast nozzles reject outof-weight specifi cation products with minimal operative intervention. To ensure absolute traceability and compliance with retailer Codes of Practice and QA protocols, both the metal detector and Raptor checkweigher capture live OEE data. “By gathering live production information om each lane independently, the dairy group can establish the operational parameters and extract statistics most valuable to their business, for instance, volume, weight, inspection speed, rejects, or downtime,” added Garr. Equipped with Contact Reporter so ware, the dairy plant can export and convert time-stamped production data om their dual-aperture metal detector and integrate into readable formats with their existing quality control reporting system. Also available is the option to connect the checkweigher to the Contact 4.0 connectivity so ware. Auditor- iendly data reports are exported as either PDF or Excel fi les covering a specifi c production line or time interval. “Rather than monitoring machine performance manually, this level of cohesive reporting on a multilane system provides valuable upstream trend feedback to boost operational e ciencies,” said Garr. Constructed to the highest food grade standards, the modular 200mm wide conveyor assembly, conveyor decks, and belts are all designed to be easily removed om the machine for deep sanitation and maintenance. In seconds, the conveyor belt can be removed and the belt tension and tracking are restored. With rent per square foot in North American industrial manufacturing plants
The rising cost of real estate in North American production facilities is pushing demand for spaceoptimized machinery.
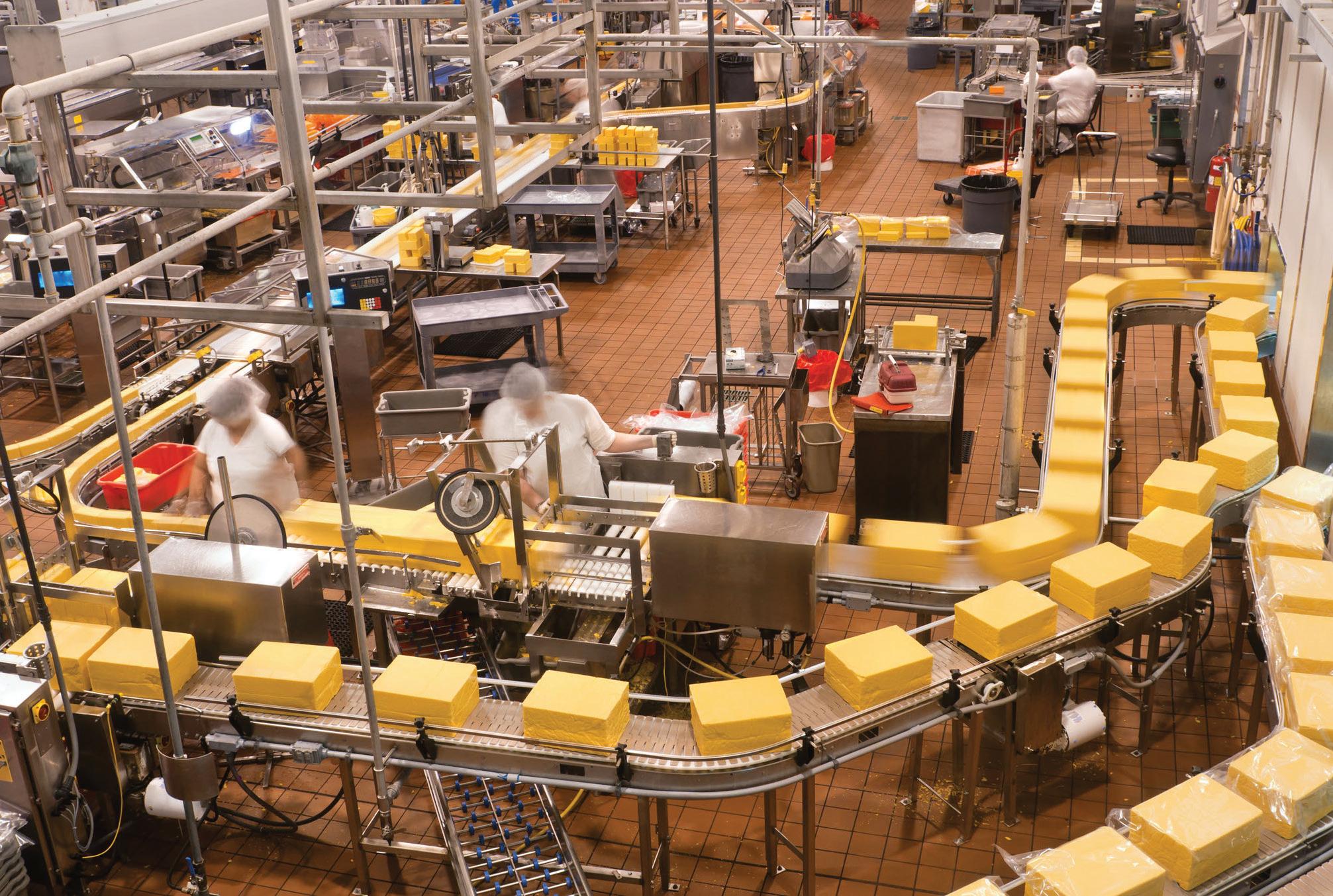
currently averaging $6.36, this latest multi-lane combination metal detection and checkweighing solution shows the space-saving possibilities. DW
Fortress Technology www.fortresstechnology.com
WHAT DO YOU THINK?
Connect and discuss this and other engineering design issues with thousands of professionals online
MAGNETIC ENCODERS FOR POSITION FEEDBACK
Contactless, no wear and maintenance-free High positioning accuracy and resolution Economical, small, compact designs and custom solutions Flexible ring diameters and measuring lengths
Design Notes
Pictured (L to R): Matt Sagaser, director of Innovation for Doosan Bobcat; Joe Alfi eri; Nicole WodkaCook, business director for Moog Construction; Joel Honeyman, VP of Innovation for Doosan Bobcat; and Dave Grabau, business development manager for Moog Construction.
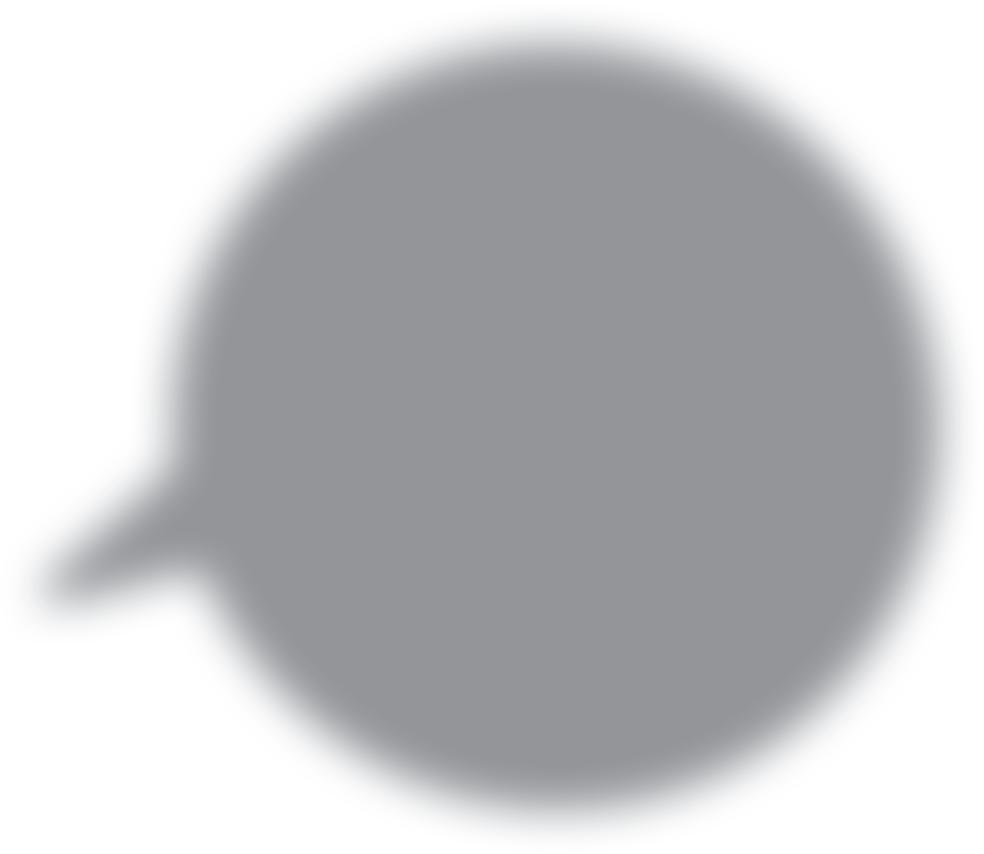
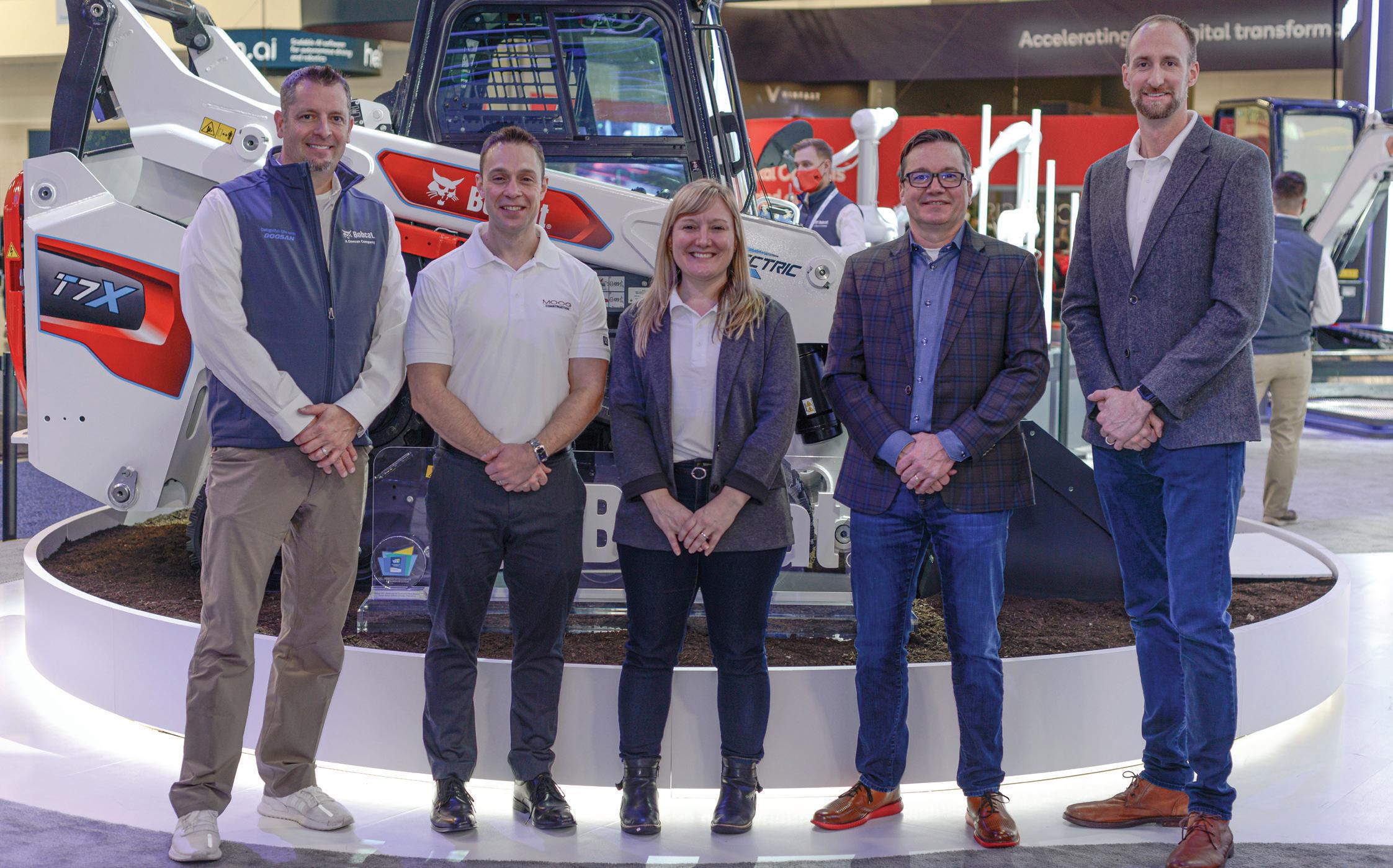
Engineering the fi rst all-electric compact track loader
Edited by Mike Santora Managing Editor
Doosan Bobcat had a vision for designing and building an all-electric machine. Its team was looking for an allelectric actuator for its compact track loaders. The search led them to Moog, which has a history of converting hydraulic systems to electric ones. The result was the awardwinning Bobcat T7X, which does not use hydraulic parts or oil. The T7X is a zeroemissions and all-electric machine with the power and performance of a diesel-hydraulic machine but without the noise, emissions, and hydraulic leaks. Here’s how they did it. The intelligent machine electrifi cation system consists of an integrated so ware amework, a sophisticated electric machine controller, li and tilt electric cylinders, electric traction motors, and power electronics. With the help of this new system, the T7X is a major step forward for the productivity, safety, and sustainability of construction machinery. “Bobcat had a vision for an all-electric machine,” said Joe Baldi, director of strategy & partnerships for Moog. “Our conversation began with Moog’s all-electric actuators, but ultimately our talks led to the intelligent machine electrifi cation system. Working together with Bobcat, we were able to bring that all-electric vision to life in six months.” The new intelligent machine electrifi cation system helped the T7X control
the motion of the tracks and li and tilt functions with e ciency, enabling a powerful zero-emission machine with increased run time and reduced maintenance costs. “To describe our contribution to the T7X in anatomical terms,” added Baldi, “we supplied the brain’s ontal lobe (the part that controls motion); the nervous system helping to intelligently coordinate actions, power, and sensor information to and om diff erent parts of the machine; and the muscles, which are the allelectric actuators and motors.” On January 4, 2022, in Las Vegas at CES 2022, Doosan Bobcat announced that Sunbelt Rentals would invest in a fl eet of the all-electric T7X compact track loaders. The all-electric machines will be co-branded by Bobcat and Sunbelt and made available this year. So, what makes Moog’s solution an “automation-ready integrated system” versus a set of components for motion control and energy management? The digital so ware amework makes this solution automation-ready, enabling Bobcat to build digital and so ware-confi gurable machines for users. Each axis on the machine can be independently and precisely controlled, but they’re tied together with other sub-systems, making it easy for Bobcat to develop valuable functionality for their customers. Think of how Tesla and Apple introduce new features through so ware updates; Moog enables this with its system. What’s unique (or fi rst of its kind) about the off ering for the Bobcat T7X is that it’s all-electric — no hydraulic parts, no oil, and fewer parts than a diesel-electric machine; it produces zero-emissions and is quiet enough that construction crews can communicate without shouting or hand signals. The energy management so ware also gives the machine increased battery life because the machine supplies energy only to the parts of the machine when needed. This extends battery life and makes zero-emission construction machines possible because they can do more work for longer before needing a charge. Moog has experts in motion control, automation, simulation, and modeling for whole systems and across markets ranging om aerospace to renewable energy. Today, most centralized systems on a construction vehicle have one motor and pump distributing hydraulic fl uid; the pump is always running. With a traditional loader, the machine would waste energy on every axis for li ing, tilting, moving — even when the machine is stationary. Moog designed a more e cient system using distributed control to send power only when and where the T7X needs it, such as li ing dirt or moving side to side. The T7X wastes little to no energy.
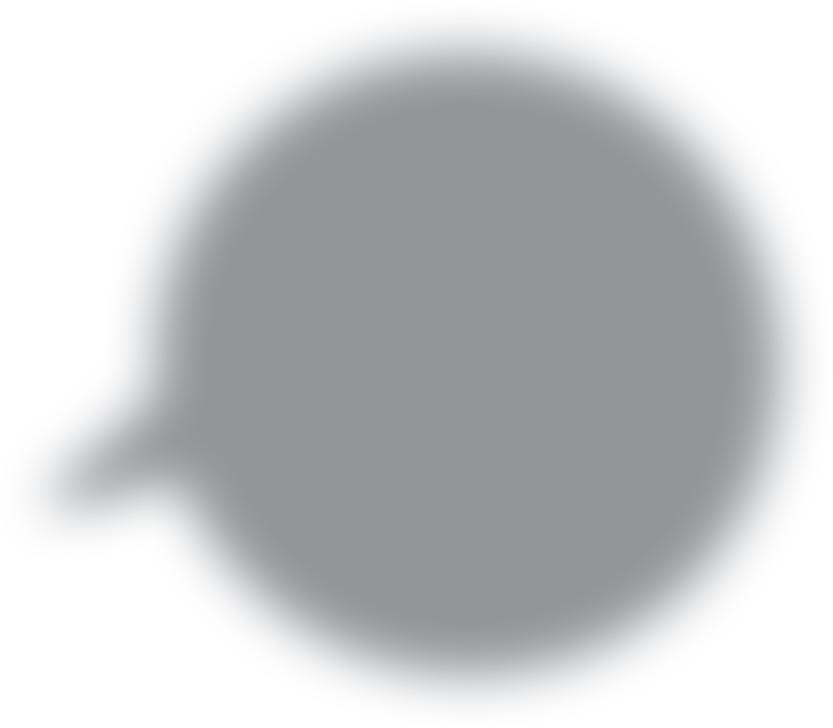
T7X on display at CES 2022 in Las Vegas features Moog electric cylinders and the Moog traction motor located at the uppermost point under the triangle forming the vehicle’s tracks.
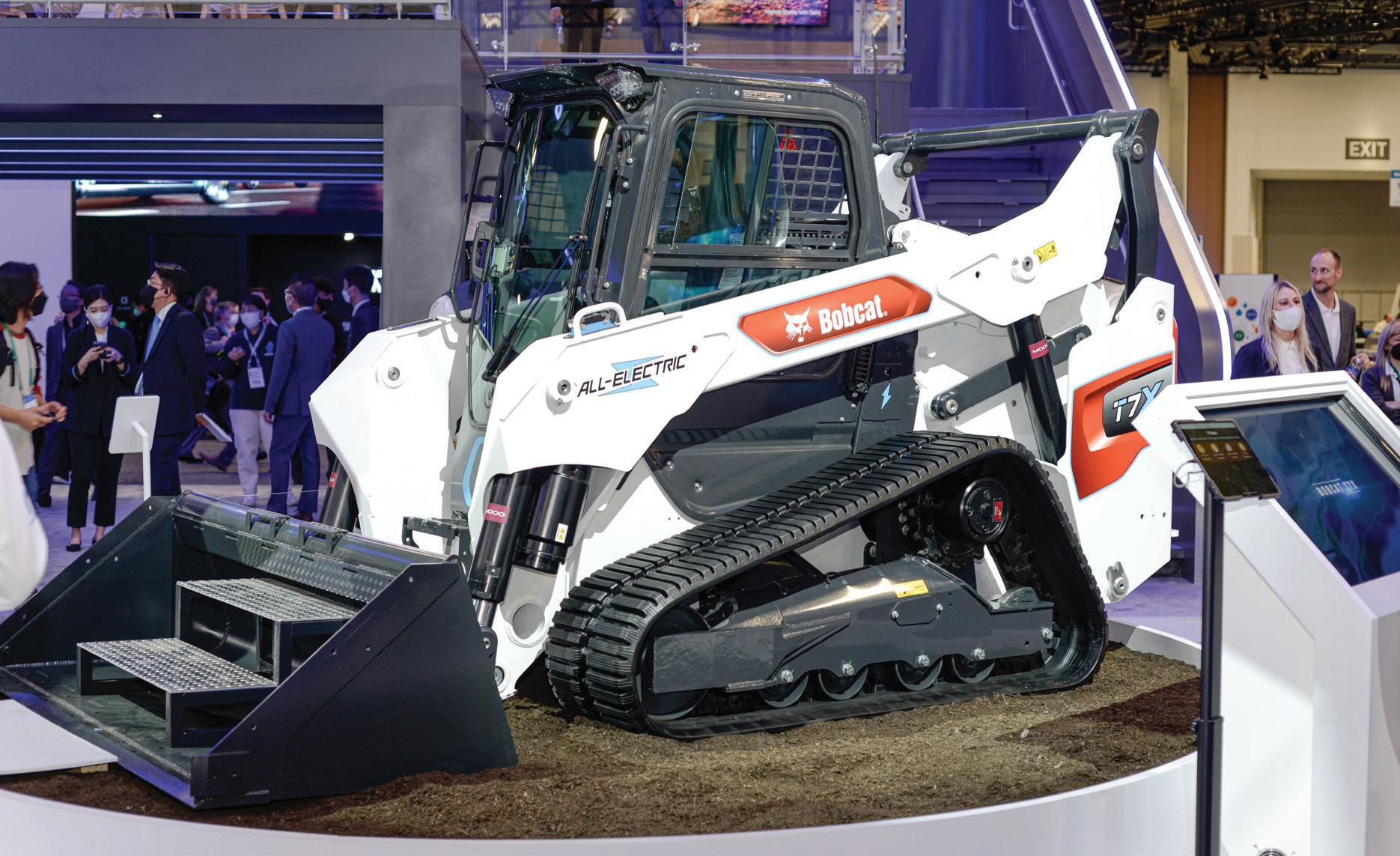
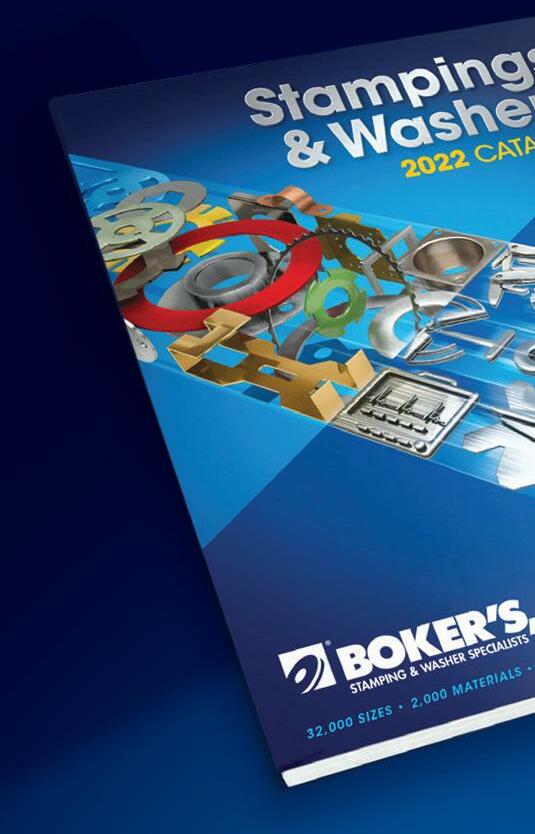

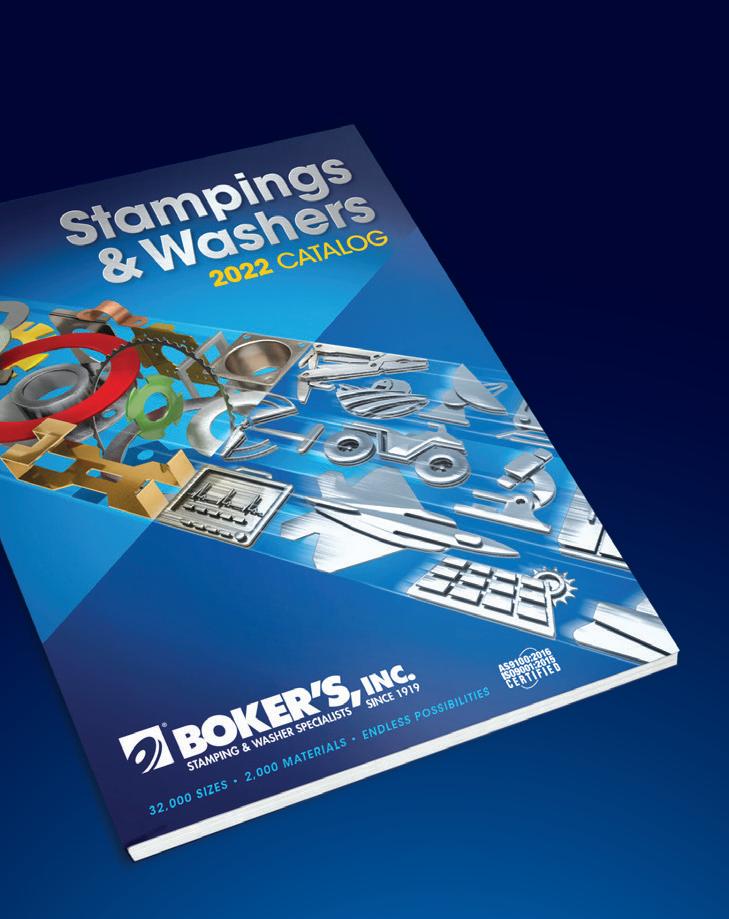
Serving a World of Industries!
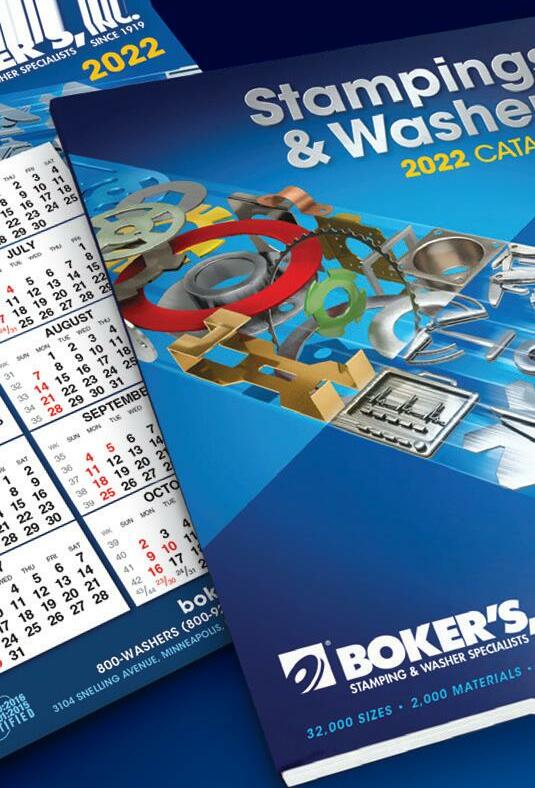
Request your FREE
CATALOG & CALENDAR!
SINCE 1919 QUALITY STAMPINGS & WASHERS
bokers.com (888)-WASHERS
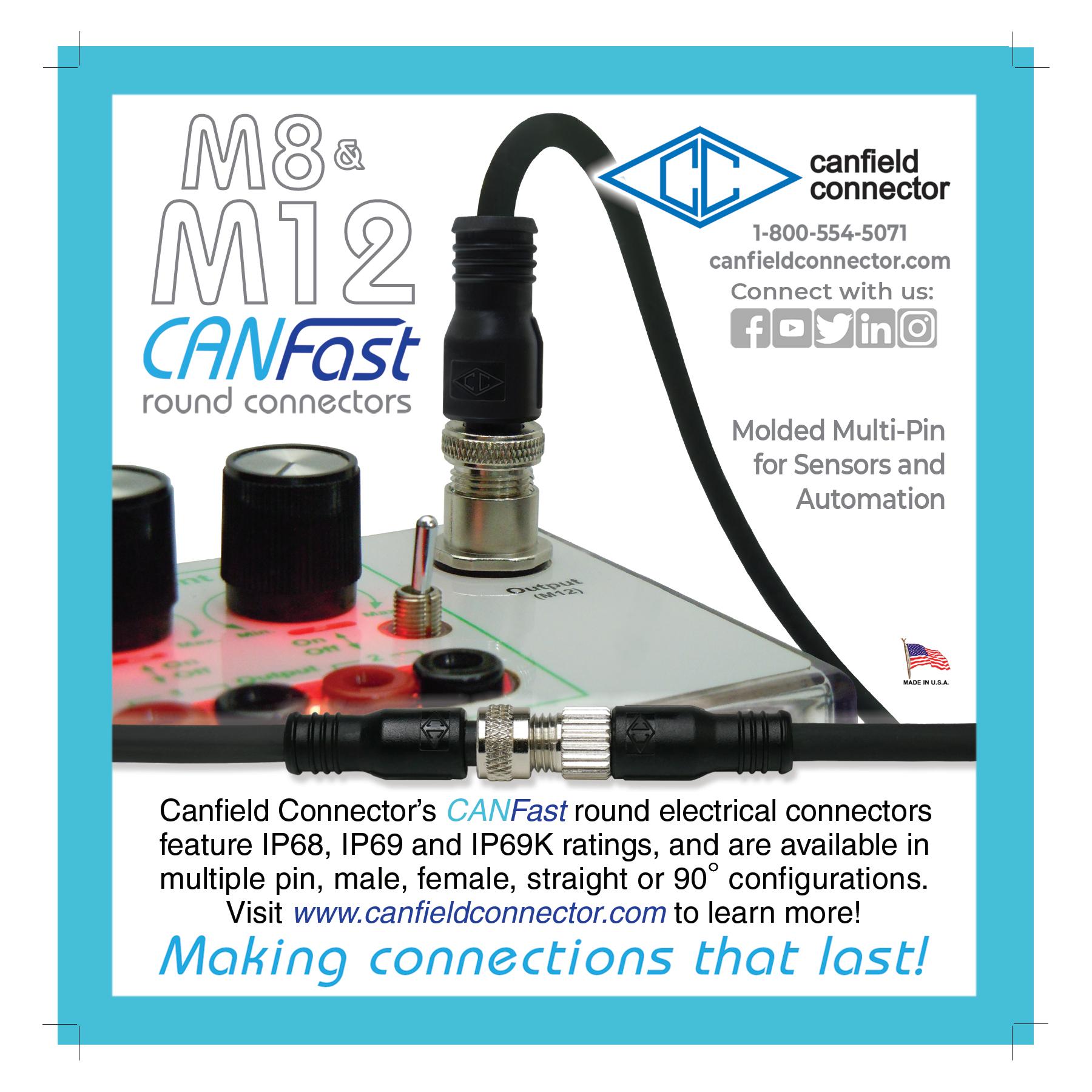
Design Notes
Additionally, the Moog team e ciently manages motion and thermodynamics for the T7X’s system, which keeps each component operating at the proper temperature range, reduces energy use, and extends run time. Lastly, the new intelligent so ware optimizes the T7X’s motion as it carries out tasks by learning to smooth out the machine’s movements and operation, which boosts run time by more than 25%. The machine gets the same output and work done with less energy by smoothing out the peak moments of energy usage.
What is the “modular, scalable, platform approach?” This means solutions like this one used for the Bobcat application are scalable across multiple types of machines with few modifi cations — it saves Bobcat time and money in developing its next all-electric product. Because the solution was built om modular hardware and so ware building blocks, the engineers on this project collaborated quickly to apply the blocks to diff erent machines. The result? Zero-emission machines getting to market faster and at a reduced cost.
How much time passed om the initial discussion to producing a working, all-electric loader? Approximately six months.
How does Moog’s approach ensure electric vehicles have comparable force and torque to hydraulic systems? The initial, all-electric solution for the T7X was thought to be too robust versus its hydraulic predecessor, but the intelligence of the machine systems allowed for diff erent work modes to control the output when needed. There’s a misconception across many industries, not just construction, that hydraulic systems are stronger than electric ones. It takes the right experience to best apply the advantages of these diff erent technologies to a machine. DW
Moog www.moog.com/construction
Design Notes
Getting the drop on precision fl uid dispensing in auto assembly
Edited by Mike Santora • Managing Editor
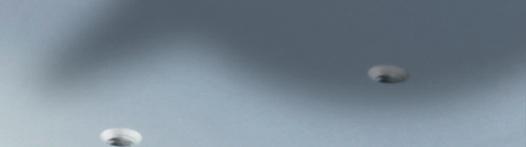
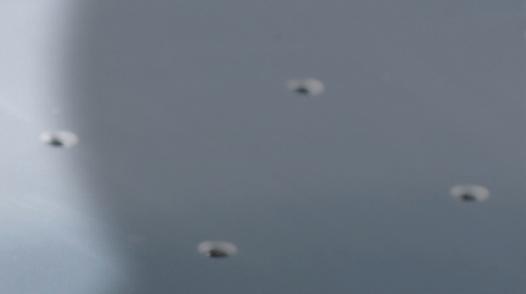
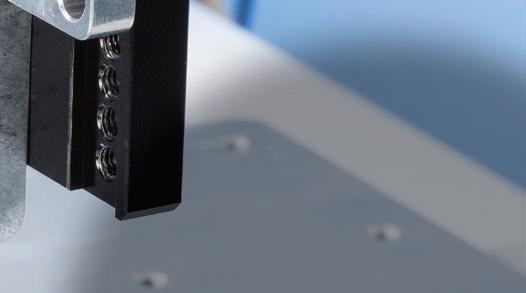
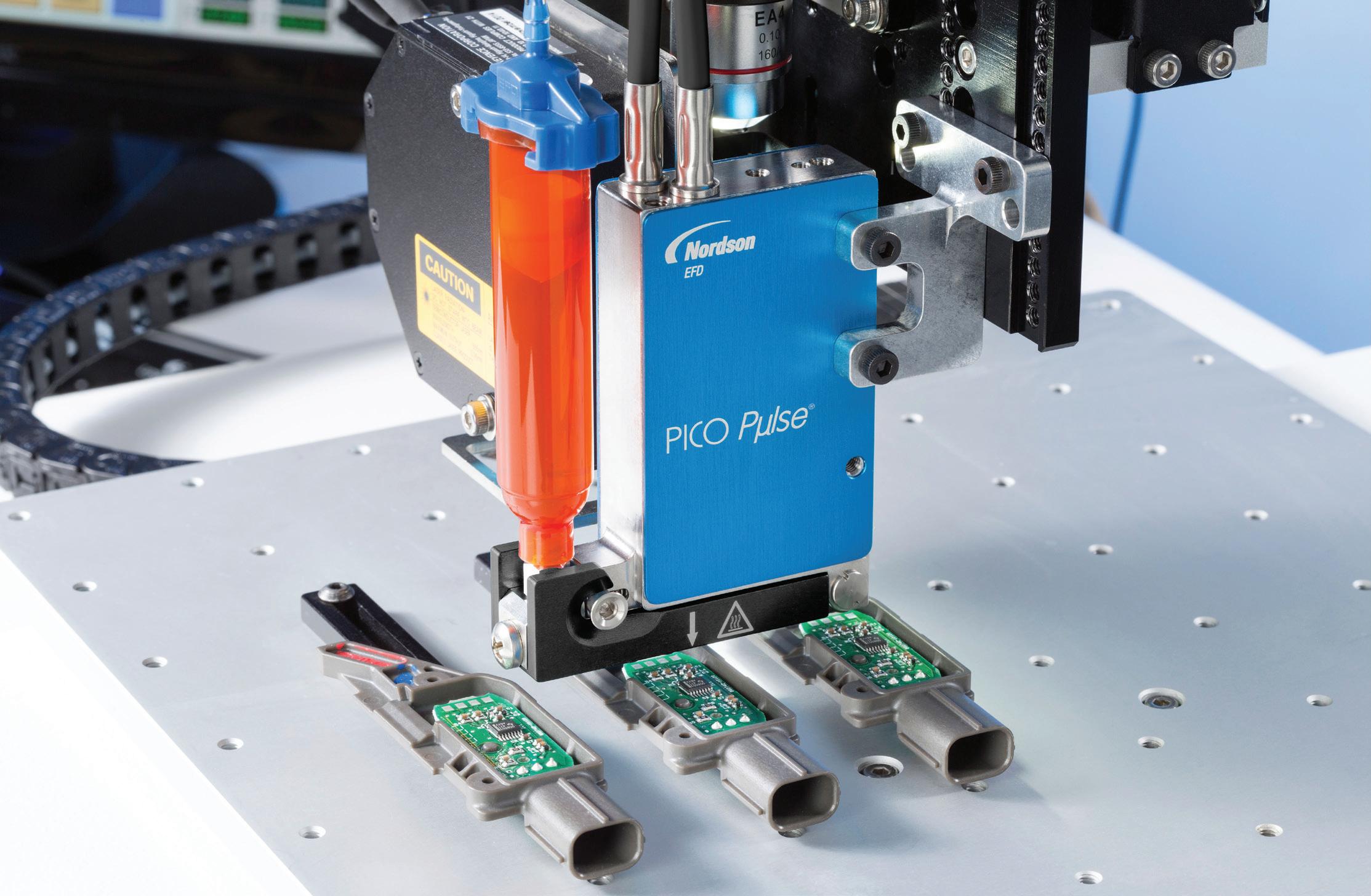
Automotive component manufacturers face several
production challenges. The most vital is maintaining product quality supported by consistent production throughput with systems that ensure profi tability. A key function in this process is assembly; the need to manufacture more complex assemblies poses challenges for process engineers in their manufacturing and assembly functions.
Fluid dispensing Critical to meeting strict requirements is the need to deposit small and precise amounts of fl uid — such as adhesives, greases, silicones, and lubricants — to parts during the assembly process. The minimal amounts of adhesive, silicone, and other fl uids must be dispensed reliably and accurately. The precise positioning and quantity of these fl uids deposited on the parts are critical to these products’ viability. This technique of depositing tiny volumes of liquid media dosages spans several assembly applications in automotive component manufacturing that require the precision dispensing of oils, grease, lacquers, and other media. Depositing small and precise amounts of fl uid is an ever-increasing challenge for automotive manufacturers of tiny micro-electronics and other minuscule parts. Substrates are becoming more
Design Notes
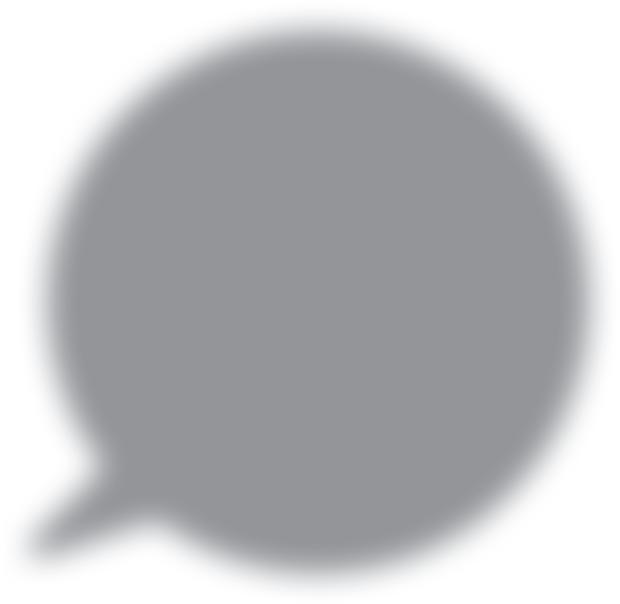
This jetting system prevents short-cuts in EV battery cells by applying precise, consistent amounts of UV-cure adhesives.
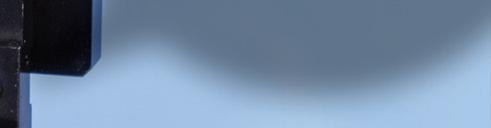
crowded and uneven in nature. Such is the case with printed circuit board (PCB) assembly and other applications. Dispensing fl uids onto hard-to-access areas or on delicate substrates are vital factors that must be assessed. These directly aff ect the Z-axis movement of a dispensing system, infl uencing its ability to move over uneven surfaces and dispense the correct volume of fl uids. Cycle times for fl uid dot deposition and throughput rates are regulated to some extent by the substrate surface topography. The variety of fl uids and fl uid viscosities that can be dispensed in automotive assembly can be substantial — encompassing epoxies, adhesives, silicones, greases, oils, fl ux, lacquers, solder paste, and solvents. The fl uid to be dispensed must readily fl ow through the dispensing heads. In some instances, once the fl uid reaches the part, it must restructure and recover to keep it om spreading and contaminating other components. Other properties of the fl uid that must be considered include its density and weight, the presence of abrasive fi llers, and whether it’s safe to dispense or if it’s combustible. The fl uid properties can also be modifi ed by the dispensing process being used. Temperature variation within the dispensing system can change the viscosity of the fl uid, aff ecting the fl uid pressure and line speed. Whether applying UV cure glue to a sensor PCB, grease, or lubricant into automotive switches, anaerobic glues into connectors, or high-viscosity grease into multiple surfaces of an automotive part, characterizing diff erent fl uids and determining the best dispensing parameters are important factors for creating a successful dispensing process.

Parameters for precision fl uid dispensing in automotive parts assembly Fluid dispensing in the assembly of automotive components encompasses a range of methods that can accommodate specifi c fl uid application processes. The latest benchtop and robotic dispensers provide a high degree of process control, capable of dispensing adhesives, solder pastes, lubricants, and other assembly fl uids with high consistency. Handling fl uid dispensing of dots, beads, and fi lls under a broad range of conditions, these units are equipped with multiple capabilities to refi ne the dispensing process. From precision benchtop fl uid dispensers, pneumatic valve systems, piezoelectric jetting valve systems, and in-line robotic dispensing systems, many factors would support adopting a more e cient and controlled dispensing method in the assembly of automotive components:
•Shot-to-shot repeatability and accuracy are improved as a more automated and controlled dispensing approach is employed.
•Increased productivity comes with increased automation.
•Part quality improves when switching om manual squeeze bottle dispensing to air-powered dispensing and further along to in-line automated dispensing, because operator-to-operator variance is reduced. The ability to set the time, pressure, and other dispensing parameters for an application improves process control and ensures the right amount of fl uid is placed on each part.
•Rework and reject rates lessen when upgrading to more automated dispensing solutions, thus improving the yield of the manufacturing lines and greater profi tability to the manufacturer.
•The amount of assembly fl uid used decreases signifi cantly when using a more controlled method of dispensing.
It is important to consider each of these fi ve points, as they represent the actual cost-to-benefi t factors infl uencing fl uid dispensing processes in automotive parts assembly.
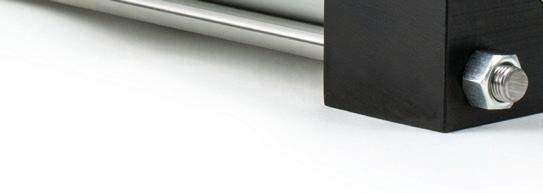
Shot-to-Shot Repeatability & Accuracy Shot-to-shot repeatability and accuracy are critical in fl uid dispensing. Depositing the right amount of fl uid has a compounding eff ect of not only maintaining product integrity but also keeping downstream production moving. For example, in a bonding application, if too much fl uid is applied, it can take longer to cure, which will delay production downstream. Conversely, if too little fl uid is applied, the part will not properly bond, interrupting downstream assembly or causing product failure. Precision dispensing systems apply shot-by-shot repeatable amounts of virtually any manufacturing fl uid by using digital timers and precision air regulators to determine the amount of material applied. The latest generation of fl uid dispensers can distribute practically all assembly fl uids — om thin solvents to thick silicones and brazing pastes — with greater accuracy. They deliver exceptional throughput and process control, with consistent deposits om the beginning to the end of the fl uid reservoir. For the precise application of adhesives, lubricants, paints, solder pastes, two-part epoxies, UV-cure adhesives, and other assembly fl uids, precision dispensing systems enable optimal results. The consistency and repeatability performance of precision dispensing systems goes beyond the actual dispensing equipment itself and also depends on the quality and proper usage of the system components. These consumable plastic components — syringe barrels, adapter assemblies,
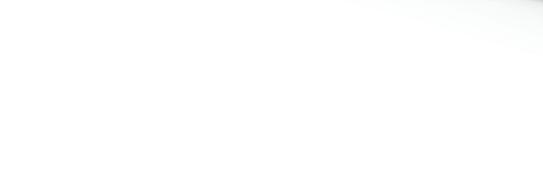
Fabco-Made NFPA
Versatile, rugged cylinders—when you need them
FABCO-AIR
A member of Festo Group



Our NFPA interchangeable pneumatic cylinders take the guesswork out of cylinder selection.
We design and manufacture our NFPA cylinders in Gainesville, Florida—so expect fast delivery, supply chain resilience and local support no matter your application. Built tough, our NFPA actuators feature anodized aluminum heads and barrels and stainless steel hardware for corrosion resistance. They also incorporate high-strength composite rod bearings and PTFE piston wear bands for superior load handling and long service life. Choose from 19 standard mounting options and hundreds of standard confi gurable options to meet the requirements of almost any application. Standard catalog not enough? Tell us about your application and let us design a custom solution optimized for your environment. • Standard bore sizes: 1.5–6 inches • Standard strokes to 99 inches • Pressure rating: 250 PSI • Temperature range: -10° to +165°F • Conforms to NFPA dimensional specifi cations • Lead time for standard confi gurations: 7–10 days
Design Notes
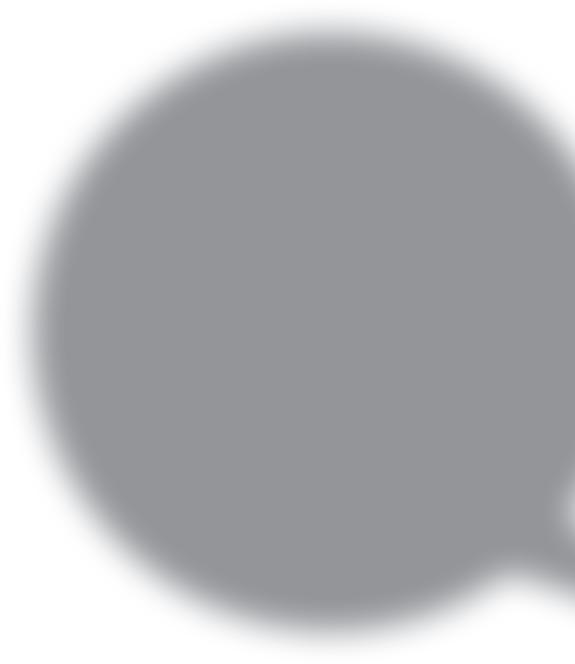

pistons, caps, and dispense tips — are designed to meet the requirements of diff erent types of fl uids and applications and to dispense the most precise fl uid deposit possible. Consumable plastic components working together as part of an integrated system are designed to reduce fl uid waste and air entrapment.
For the highest level of performance om these dispensing systems, several requirements necessary:
•Each of the consumable plastic components should be designed as part of a complete, integrated system. This will improve yields and reduce costs by producing the most accurate, repeatable fl uid deposits possible. Mixing and matching components om diff erent systems or suppliers is a recipe for diminishing performance.
•Maintaining precision shot-to-shot repeatability in dispensing starts with quality manufacturing of the components. For best performance, all components should be certifi ed that no silicone mold-release agents are used in the precision molding process or at any other time during the production of the dispensing components.
•The dispensing components should always be used as singleuse consumables. In high-precision dispensing systems, barrel internal diameters (IDs), piston diameters, and dispensing tips, are manufactured with tolerances that make any residue om prior dispensing residing in the barrel, piston, or tip degrade dispensing repeatability performance. Once the piston reaches the bottom of the barrel; the barrel, piston, and tip should be discarded.
Process Control The ability to set the time, pressure, and other dispensing parameters for an application improves process control and ensures the right amount of fl uid is placed on each part. The latest generation of fl uid dispensers provides a high degree of process control for dispensing applications in the assembly of automotive components, are capable of dispensing adhesives, solder pastes, lubricants, and all other assembly fl uids with high consistency. Fluid dispensing of dots, beads, and fi lls can be achieved with dispensing equipment features such as a 1-100 psi air pressure regulator, timed-shots, vacuum control to keep thin fl uids om dripping, digital time/pressure displays, and electric foot pedals. Time adjustments can be as fi ne as 0.0001 seconds, and constantbleed air pressure regulation will provide reliable control when dispensing any type of fl uid. Some of the latest fl uid dispensers allow programmable sequencing to automatically adjust dispensing parameters, making them suitable for applications that involve two-part epoxies and other fl uids that thicken over time or get thinner as ambient temperatures rise. Another feature supporting precision dispensing, particularly applicable for automotive component manufacturers, is Automated Optical Inspection (AOI). When coupled with CCD cameras and confocal lasers, Nordson EFD vision-guided automation platforms provide optical assurance of fl uid deposit volume and placement accuracy, ensuring a conforming deposit. With robotics, using a robot’s existing vision systems, the AOI so ware verifi es fl uid deposit widths and diameters. With the AOI confocal laser, the system measures the height of a fl uid deposit in addition to the width and diameter, providing 3D deposit verifi cation and determining if dispense requirements have been met. The confocal laser detects deposit height measurements regardless of the transparency of the fl uid, which can sometimes distort quality data. Constant closed-loop feedback delivers automated quality control data, saving automotive component manufacturers time and costs.
DW
Nordson EFD www.nordsonefd.com