
3 minute read
14 experts on linear motion
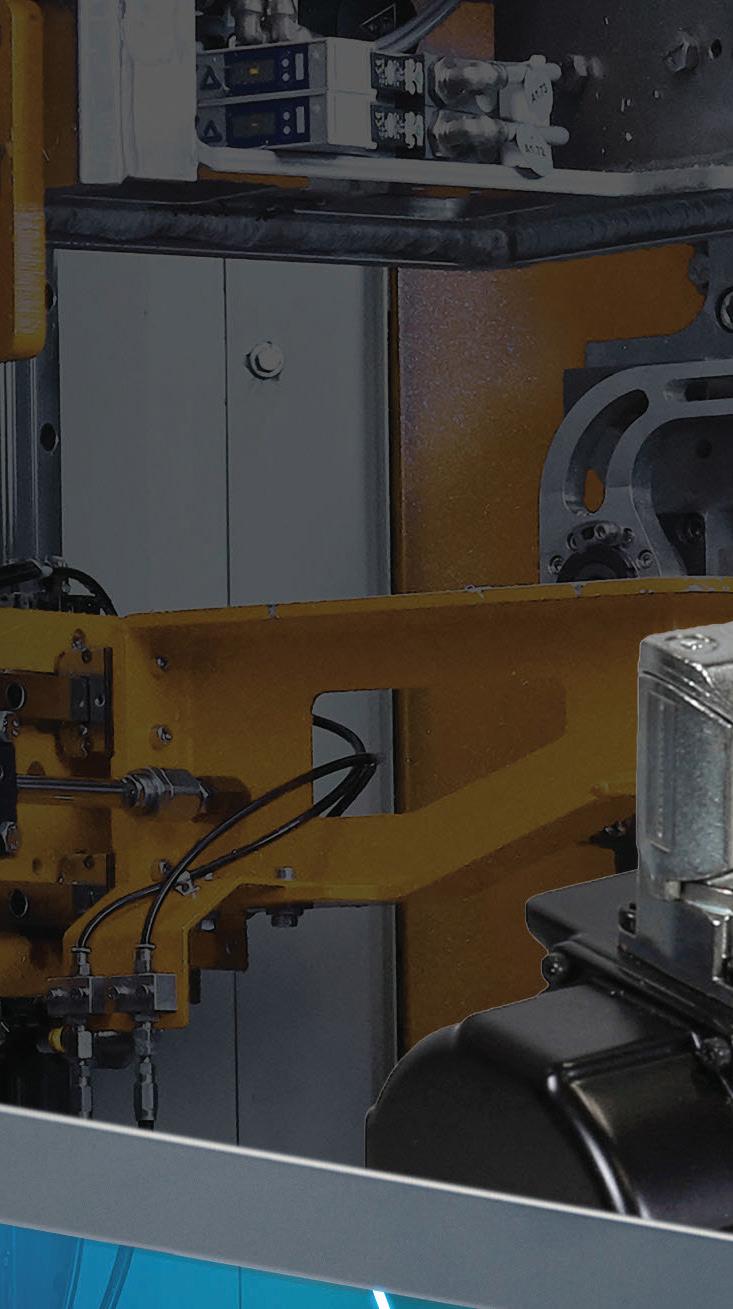

For the annual Design World Trends issue, we asked industry experts to share their insights into linear-motion trends. Here’s more of what they had to say on linear actuators, linear guides, and stages.



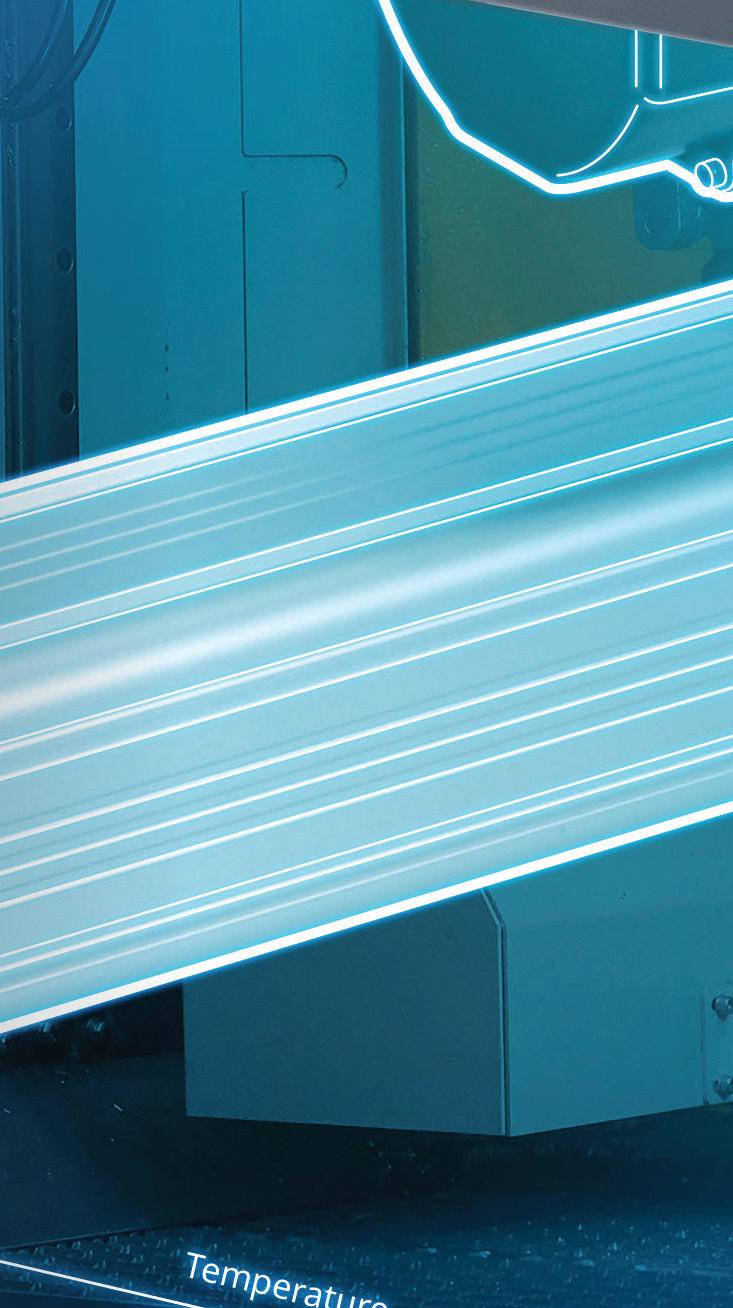

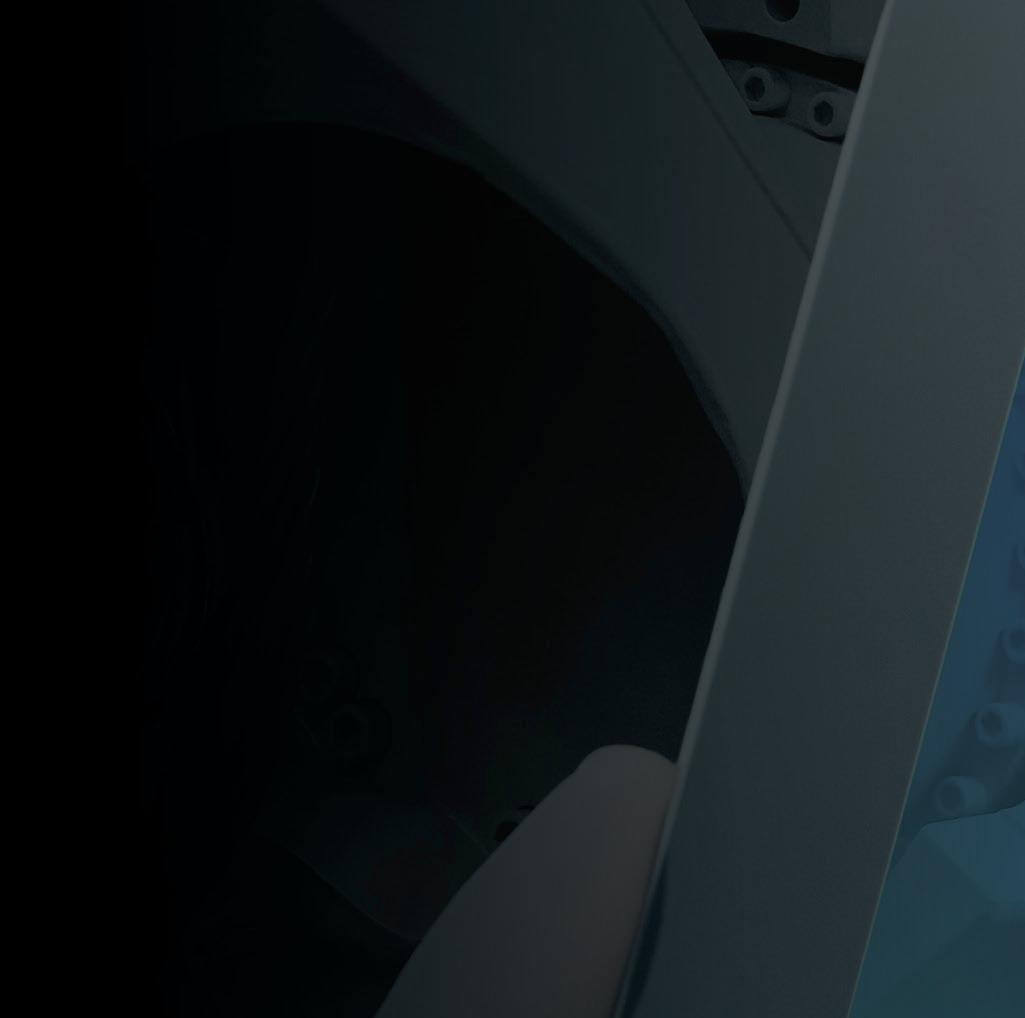
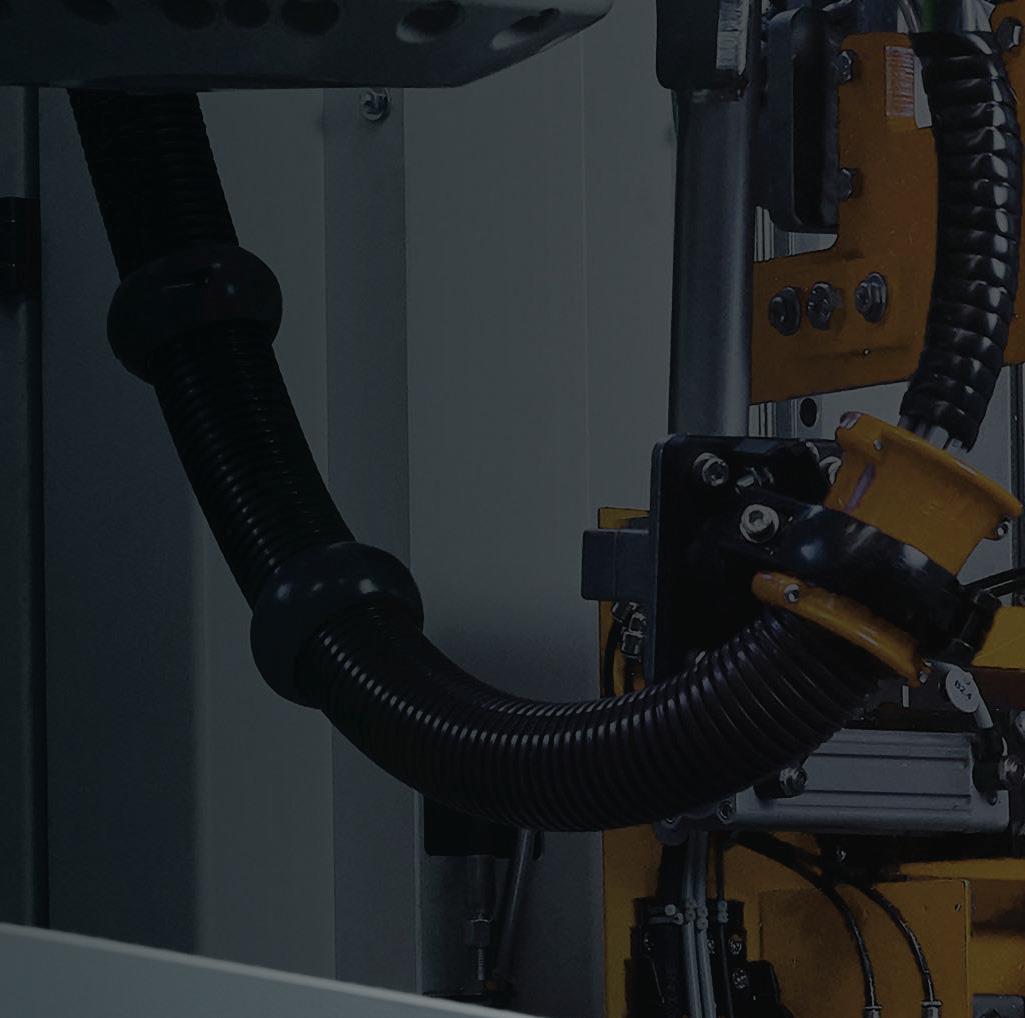
WWhat’s new in linear guide slides and ways?
Walden: This past year, we’ve seen linear guidance used for aerial vehicle (drone) hangers to service and protect the vehicles when not in use.
Rice: There are new ways of integrating the linear guide and linear bearing into the actuator body. Instead of being constrained by manufacturers’ available dimensions, the OEM uses one of these new guides where it makes the most sense for linear motion. For example, the guide can be wider for higher moment loads or mounted closer to the actuator base to strengthen the carrying system foundation. Festo has developed a guide that is part of the actuator body, which makes more e cient use of materials and reduces weight. Assembly is easier, and performance is higher.
What’s behind the growth of leadscrew, ballscrew, and roller screw applications?
Orozco: Leadscrews are known for high static force applications, withstanding excessive vibration, and operating quietly. They’re cost-e ective options and have been traditionally used in machine slides and heavy-lifting applications, such as vises, presses, and jacks. However, miniature as well as precise leadscrews are attracting industries such as photonics and autofocusing optics.
Ballscrews are the most commonly used screws that provide high-performance solutions for a range of applications where high loads, high speeds, precision driving, durability, and value are prerequisites. Roller screws are more expensive than but outperform the capabilities of ballscrews. Roller screws are well suited for heavy loads, high duty, high rotational speed, high acceleration, and rigidity, and for operation in harsh environments. Roller screws are good for high-precision applications with high positioning accuracy and repeatability.
Enhanced feedback technologies help linear-motion endusers verify position and speed and monitor actuator performance.
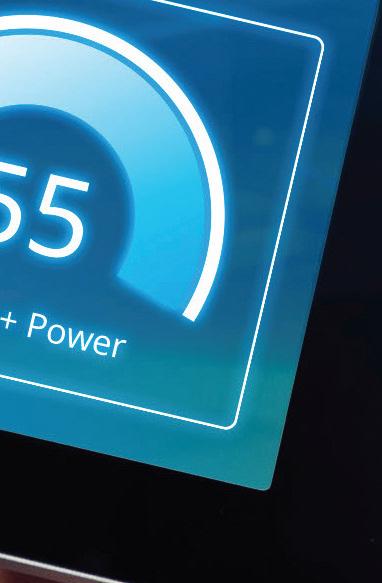

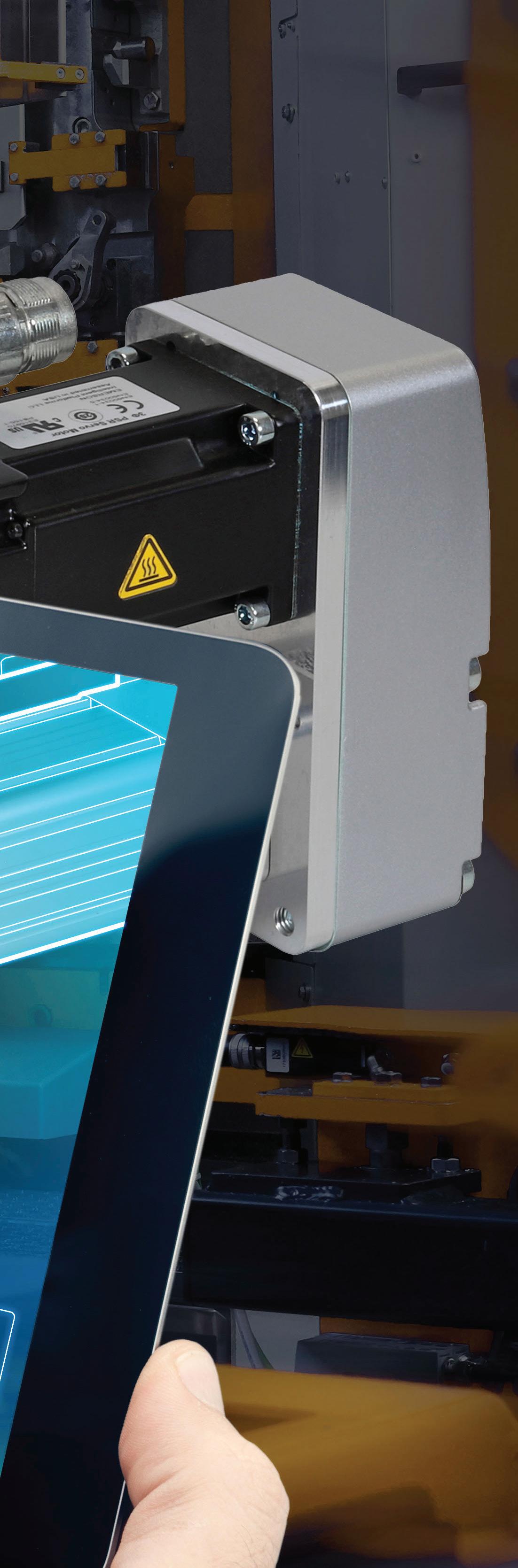
| courtesy of Emerson
Falasco: Adoption of ballscrews and especially roller screws is due to more companies switching from hydraulic to electromechanical technologies for cleanliness and economic reasons. Roller screws o er high load capacity in a small footprint, and ballscrews o er high load and (with recirculating ball bearing technology) moderately high speed capacity. Will ballscrews and roller screws replace all hydraulics applications? No, but change is happening in the linear-motion world, and customers see the benefi ts of electromechanical solutions that similar hydraulics can’t o er.
Rice: Ballscrews are a primary mechanical drive system in our linear actuators. They provide high-precision motion and positional repeatability along with high forces. Engineers can easily optimize ballscrews to the application by simply changing the lead or pitch of the screw. Roller screws extend these benefi ts by increasing the force capabilities and are now used frequently in high-force applications. Roller screws are encroaching into the high-force areas traditionally dominated by fluid-power actuators.
Multi-axis gantry attachment kits extend the working envelope of linear actuators and enable the fast and simple connection of several actuators into a more complex motion system.
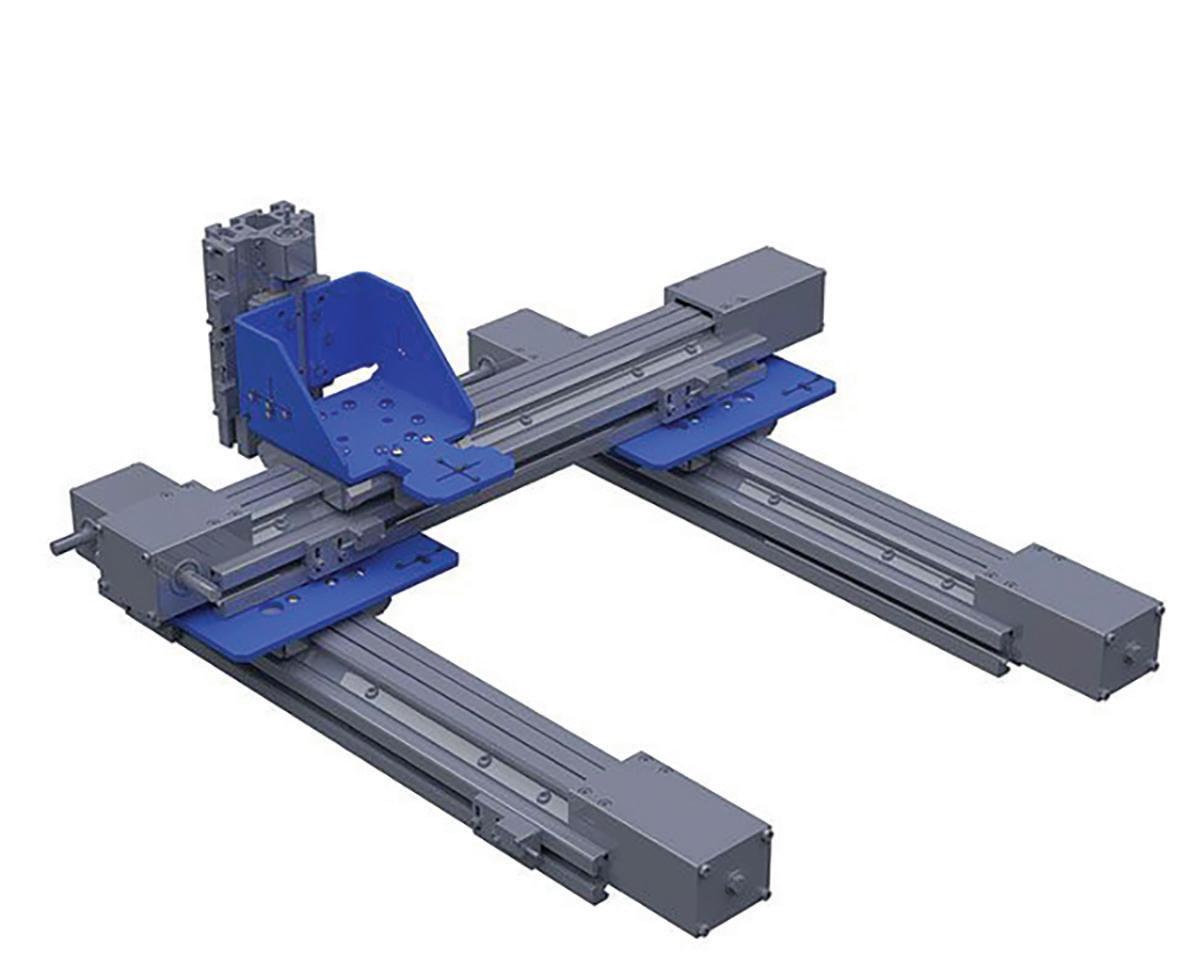
| courtesy of Bishop Wisecarver
Zaske: We’ve been a primary manufacturer of planetary roller screws for over a decade and see an increasing interest in and application of roller screws due to their dense power capability and long life. Customers consider them a key component as they explore ways to eliminate or reduce hydraulics in production applications. This doesn’t mean that roller screws are a panacea, but with a proper understanding of their benefi ts and limitations, we see planetary roller screw applications continuing to grow for a long time.
Describe how motion-subassembly design work is increasingly outsourced.
Rice: OEMs that outsource subassemblies gain competitive advantages. These turnkey solutions decrease engineering time and procurement costs. Outsourcing shortens design cycles and speeds up new machine development and production. Areas of acute interest for outsourcing today include XY tables and Cartesian gantries. These systems o er maximum work envelopes in a compact footprint; do not require safety guarding; are fast, flexible, and precise across the entire envelope; and are more coste ective than an articulated arm and SCARA robots in many applications.
Lackey: It all began with the semiconductor industry — partnering with customers to provide completely engineered-to-specification subassemblies for wafer lifts that fall outside of the standard catalog product o ering. While Rexroth currently supplies thousands of engineeredto-specification subassemblies in the semiconductor market per year, we see increased demand for custom-engineered or engineered-tospecification subassemblies in other industry segments.
Meet the experts
Dave Walden | Applications engineer • PBC Linear
Eric Rice | Product market manager — electric automation • Festo
Samuel Orozco | Product marketing manager — Electric actuators • Emerson
Eric Falasco | Product manager — Screws, bushing/shafting, small handling modules • Bosch Rexroth
Andy Zaske | V.P. of sales and marketing • Tolomatic
Justin Lackey | Product manager — Systems • Bosch Rexroth
Andrew Jung | Director of engineering • Bishop-Wisecarver
Tim Sharkey | Director of market management for electric automation • Festo
Saurabh Khetan | Product line manager — Leadscrews • Thomson Industries Inc.