
1 minute read
WAREHOUSE AUTOMATION
analysis difficult, an open architecture solution can converge the data from the various systems to produce a much clearer view in the digital dashboard. When analytics highlight a problem, data sources can be analyzed to detect which system generates the issue, from micro-stops to AGVs receiving incorrect instructions.
In the end, a process analysis can be overlaid on top of the productivity metrics to get a picture of the overall health of the operation and a clear understanding of where the process can improve or where the next bottleneck or failure will occur.
A critical component of this datadriven, preventive maintenance solution is to share all the data sources from the smart sensors and machines to constantly evaluate the health and condition of the process. This is typically managed in the background of the operation in a non-time-sensitive fashion. The advantage is that rather than having the maintenance team periodically or regularly check the systems, the software-driven solution queries the smart sensors for their IOLink-provided health diagnostics. This data can be shared to help operations, engineering, and management understand the warehouse’s long-term health. This requires the previously mentioned methods of converging systems and the technology connectivity that provides the data to be analyzed.
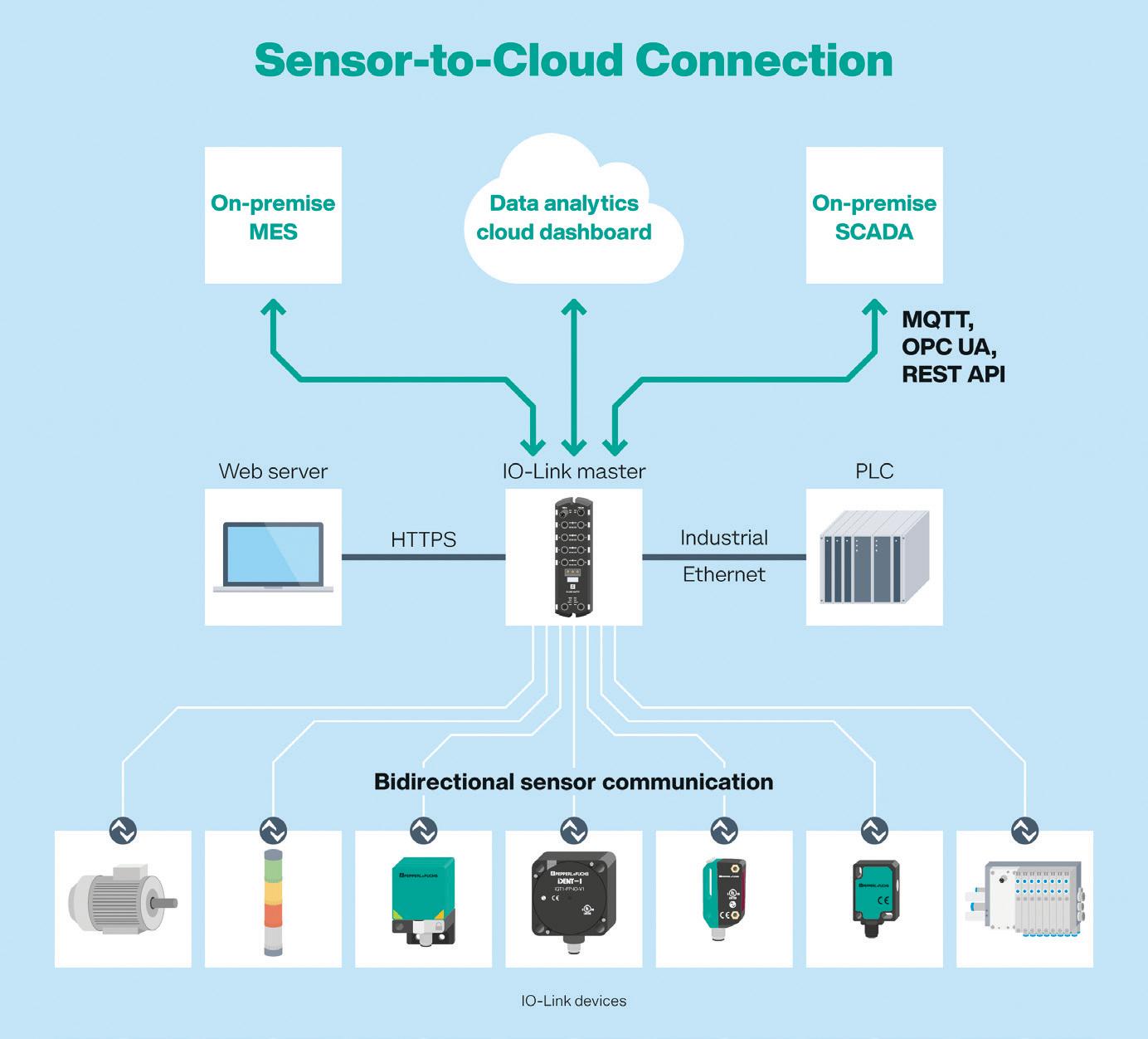
As we continue to debate which diagnostic approach is right for each specific warehouse organization, there are two aspects most may agree on today: having the ability and resources to prevent downtime and failure is strongly desired, and it’s a very interesting problem to solve. l WH
Pepperl+Fuchs pepperl-fuchs.com
| Courtesy of Pepperl+Fuchs
For an effective preventive maintenance program, all data sources from smart sensors and machines should be shared to constantly evaluate the process and equipment’s health and condition.
| Courtesy of Pepperl+Fuchs