
4 minute read
Internet of Things
as quickly as possible. Delays must be minimized or, ideally, eliminated completely.
The digital replica of the physical entity allows engineers to design, test, and virtually validate their work. This requires considerably less manual e ort and, in turn, less time. Organizations have also seen benefits such as increased safety, enhanced agility, and lower cost of design changes compared to legacy physical commissioning.
By using digital twins, engineering teams are able to test any number of system elements, including Programable Logic Controller (PLC) logic and code, software integration, and user interfaces.
Digital Twin creation
Creating digital twins requires that aspects of the engineering system be accurately and virtually replicated. Typically, this involves the modeling of mechatronics systems, including elements such as motors, actuators, and conveyors, all connected to a controller (usually a PLC). The digital twin for system engineering replication includes two aspects:
• System modeling using CAD
• Controller code
During program testing, the virtual system is integrated with either a physical or simulated controller. It’s at this stage that the benefits of virtual commissioning are realized. The ability to test the integration of controller code with the physical system in a virtual environment enables an organization to test various code configurations, create and analyze various failure modes, and conduct comprehensive throughput analysis. ‘What if’ scenarios can be run, and potential program issues or bugs can be identified and triaged before expensive equipment fabrication and physical testing is started. Engineers can also make improvements to the products at this stage, based on the simulated interaction between the product and the equipment. This kind of virtual testing leads to a valuable reduction in physical testing time, risk, and uncertainty by converting a sizable portion of that physical testing to be finished virtually, prior to the fabrication of equipment. It is traditionally executed on the shop floor. At this point however, making design changes is significantly restricted and significantly more expensive.
With the increase in model fidelity, more processes and critical elements can be factored in within virtual testing. Typically, an organization will move towards a convergence of five di erent types of digital twins to accelerate the commissioning of new equipment and processes.
1. Geometric Design: Digital representation of physical assets (3D model of a product cell or line)
2. Physical Dynamics: Digital representation of physical processes and dynamics (details around how equipment physically moves, where the constraints are, and the interaction of di erent mechanical components)
3. Programmed Behavior: Digital emulations of logic and animations of physical processes (incorporating physical kinematics of the equipment with software control)
4. Human Interface: Digital representation of the interface between human and equipment (virtual version of an equipment HMI or enhanced methods of interacting with the equipment such as using VR)
5. Analytical Insights: Digital characterization of data, measurements, sensor readings, and telematics of assets or processes (utilizing sensor data to monitor equipment condition and to predict failures)
A three-phased approach
The development of industrial engineering systems goes through three generalized phases:
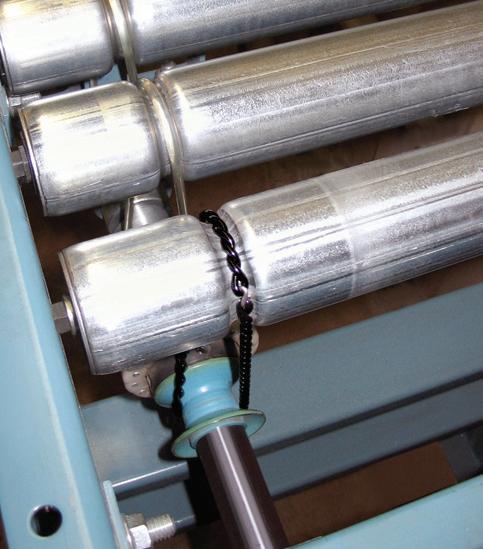
1. Planning and Concept: In this initial phase, the work, functions, business requirements, and selection criteria are defined. Front-end engineering studies are conducted, options are narrowed down, and the first conceptual designs generated.
2. Engineering and Construction: Moving from conceptual to tangible, all the functional and technical requirements are laid out. This phase includes elements such as safety, mechanical, electrical, software, and instrumentation specification, as well as the selection and fabrication of systems and equipment based on the previously defined specifications.
3. Installing and Commissioning: The final stage is the installation and testing of systems against design specifications and pre-defined acceptance criteria to identify any gaps. This phase also includes work done to resolve any issues. This step leads to the performance of site acceptance and final equipment commissioning.
All three phases require the engagement of multiple stakeholders, such as general contractors, subcontractors, and equipment suppliers. Any undiscovered design or development issues in phases one or two can cause substantial problems downstream during the installation and commissioning phases of engineering systems.
After the first two phases, the cost of resolving issues grows exponentially and can be between 200 and 800 times more costly compared to issues addressed in early phases. Running scenarios to troubleshoot software and hardware in the early phases also allows engineers to generate feedback and plan accordingly to avoid these costs later down the road.
Crucially, digital twins can shorten physical testing time during the Installation and Commissioning phase.
By creating a virtual commissioning phase prior to physical testing, teams can perform actual acceptance tests and resolve issues encountered within the specified equipment in short order and with minimal disruption.
When it all shakes out…
We’ve seen first-hand that enterprises that deployed virtual commissioning were able to reduce time to steady-state operations by up to 40% compared to using conventional methods.
By using digital twins to capture the design, engineering, construction, and commissioning elements of a facility expansion, organizations can reduce risk and enable faster ramp up.
Digital twins are one of the technologies at the heart of digital transformation, powered by the digital thread that unifies data across an organization, removing legacy silos and creating a truly connected enterprise. It enables the integration of the internet of things (IoT), artificial intelligence and software analytics to enhance outputs, evolve, and scale with organizational needs. Over time, the digital twin can be leveraged to help realize significant breakthroughs, including generating PLC code or even removing the PLC programming step of the commissioning process entirely.
Virtual commissioning can be leveraged alongside other capabilities of this technology, such as facility layout planning, capacity planning, and operator training. It can even be combined with AI and other forms of advanced technology to perform dynamic system optimization, AI-enabled control, and intelligent model training. As merely one application of digital twin technology, virtual commissioning’s benefits include decreased commissioning times, reduced risk, increased reliability, and lowered costs throughout the manufacturing operations commissioning process. As the technology continues to evolve and incorporate more capabilities, organizations will have to adapt their strategies or risk missing out. DW