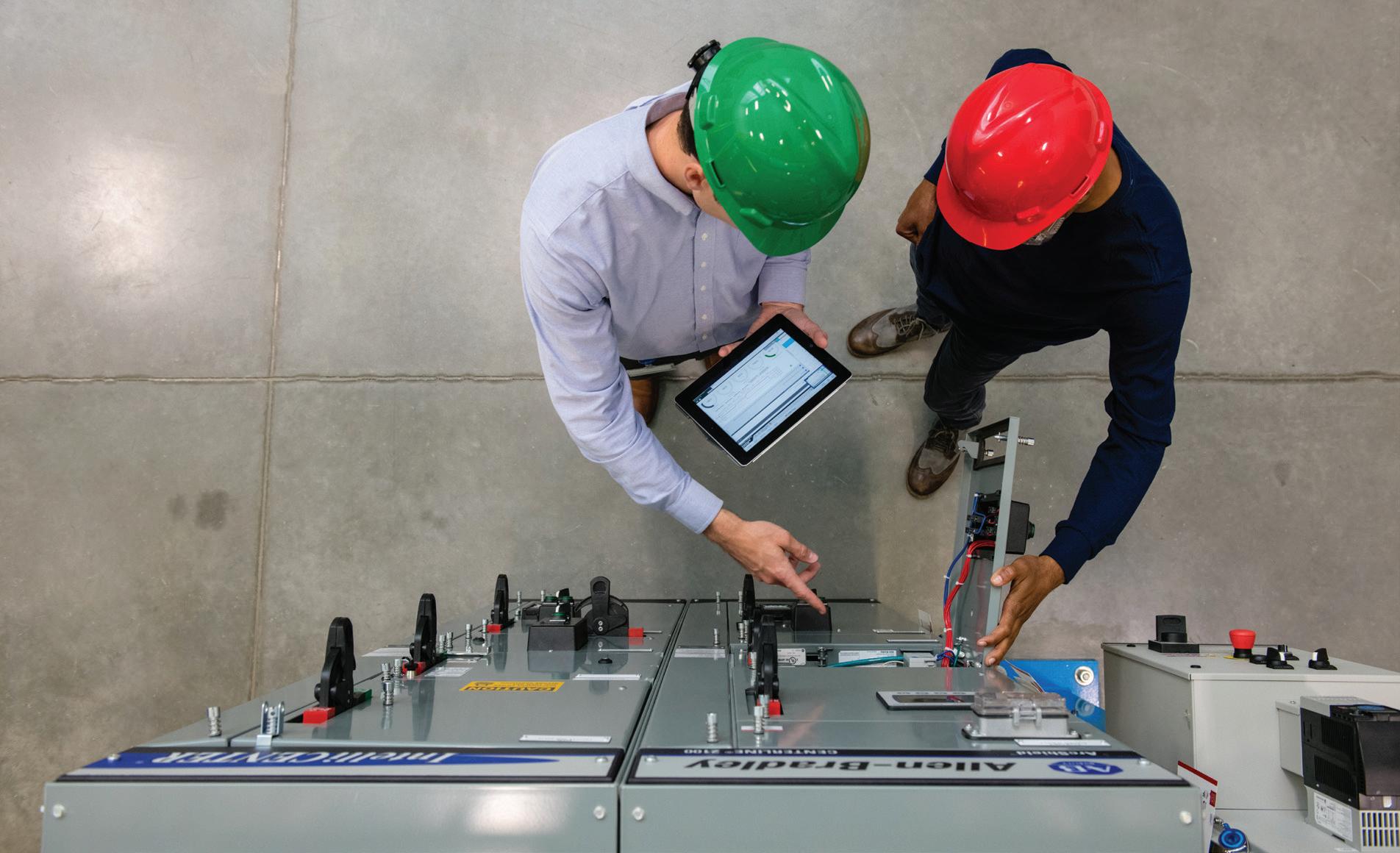
7 minute read
Internet of Things
An IoT lesson in IT/OT collaboration
Shubham Garg • Automotive Industry Manager • Rockwell Automation
Digital transformation in manufacturing, and the Industry 4.0 implementations that defi ne these transformations, are increasingly critical for post-COVID resilience and competitive advantage overall. Yet for many companies, the benefi ts lie on the other side of signifi cant implementation challenges. This is especially the case for established global manufacturers, who must transform at scale with minimum disruption and maximum alignment of information technology (IT) and operational technology (OT) teams – not unlike the proverbial changing the wheels on a vehicle while traveling at full speed. For National Engineering Industries, Ltd. (NEI) – a producer of ball bearings for the automotive, railway and industrial sectors – that was a particularly apt analogy in mounting a successful Industrial Internet of Things (IIoT) transformation to improve operations and performance. The NEI team sought their own IIoT transformation of replacing paper logs and non-real-time systems with a digital system connecting hundreds of Computer Numerical Control (CNC) machines and Programmable Logic Controllers (PLCs) to a single IIoT network, which became a lesson for mastering strategy and implementation at scale. Helping the team with this transformation was Rockwell Automation and other strategic partners.
Tackling production challenges with real-time visibility and decision support NEI is part of the CK Birla Group, a growing $1.6 billion conglomerate with 20,000 employees at 24 manufacturing facilities and business operations on fi ve continents. The company has been in business more than 75 years and operates fi ve facilities to manufacture diff erent types of bearings – which are part of any rotating equipment or machinery. As India’s largest bearing manufacturer and a company
Internet of Things
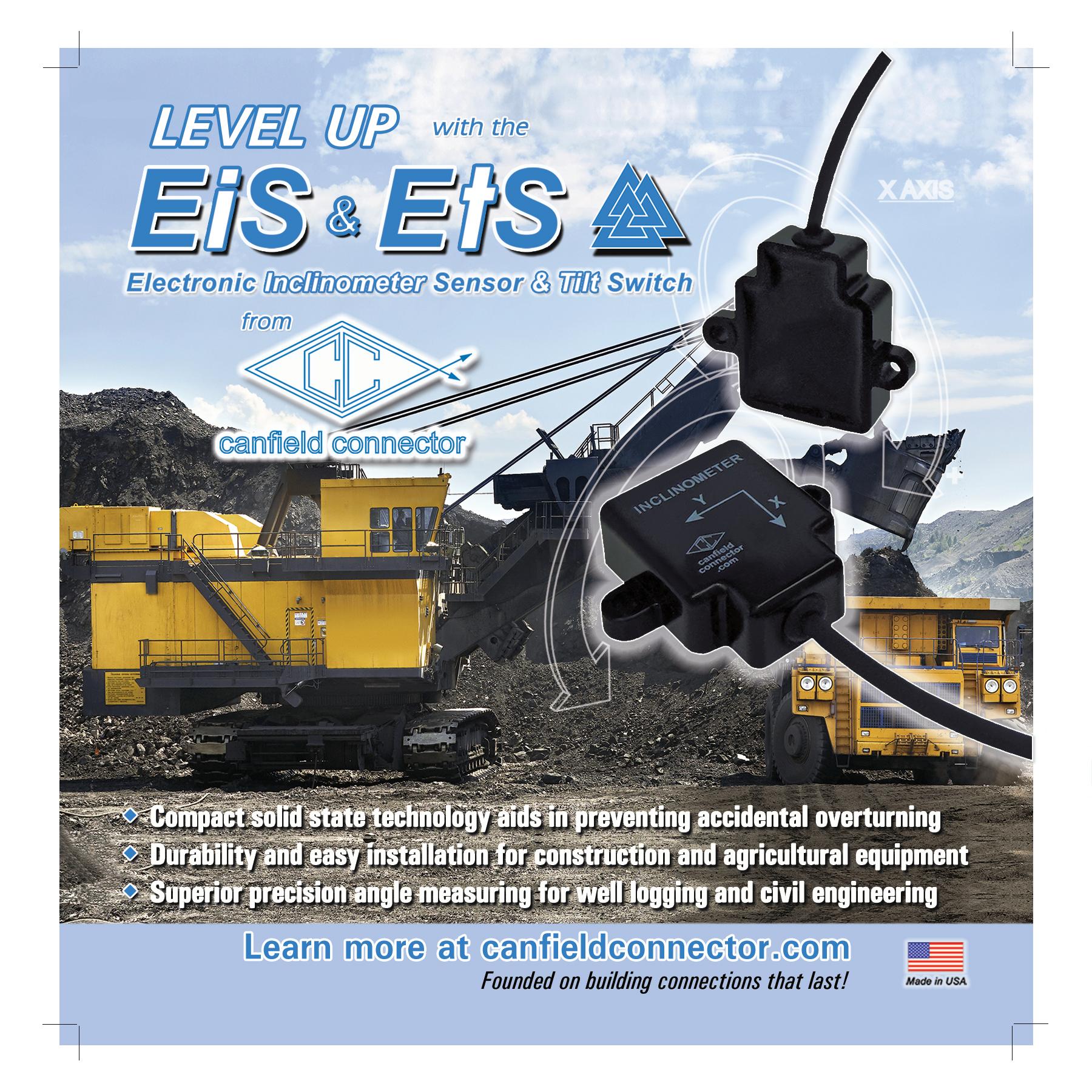
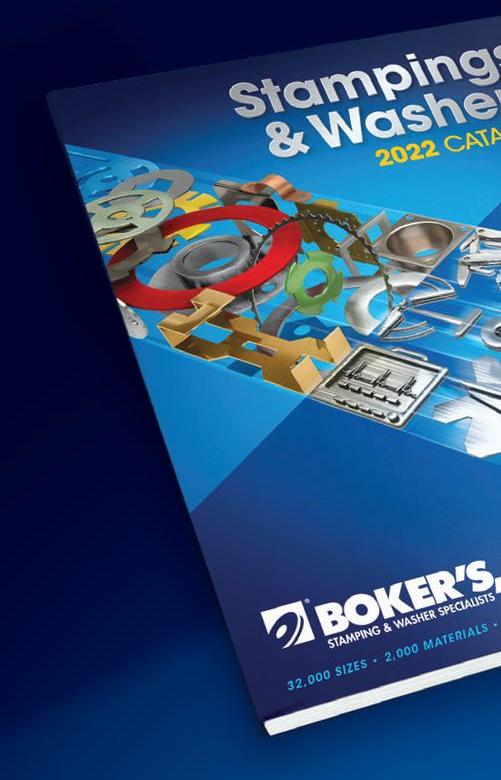
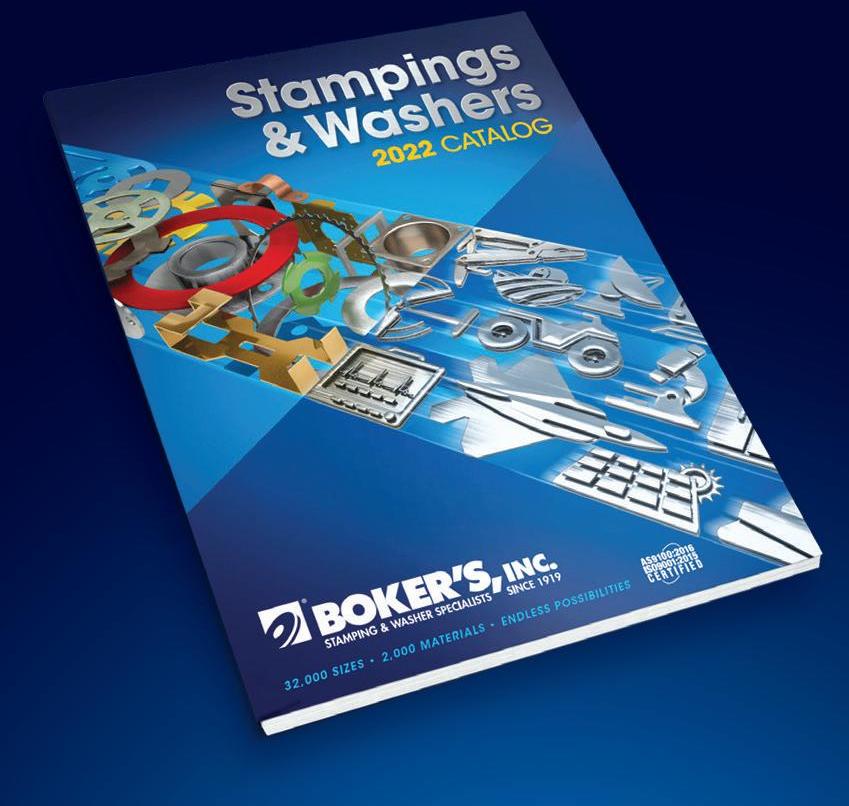
Serving a World of Industries!
Request your FREE
CATALOG & CALENDAR!
SINCE 1919 QUALITY STAMPINGS & WASHERS
bokers.com (888)-WASHERS
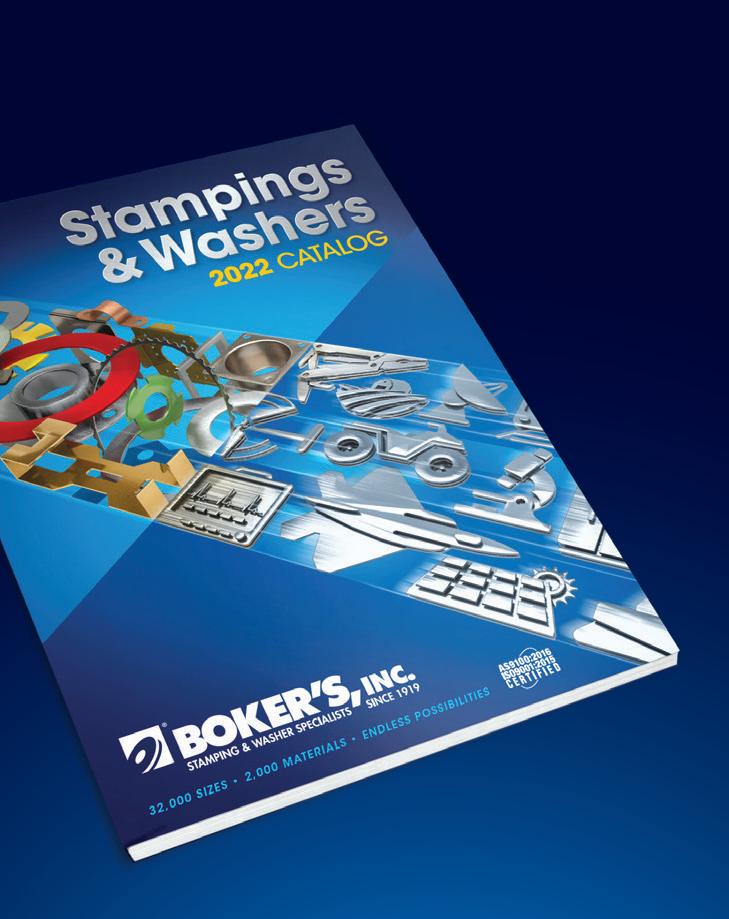

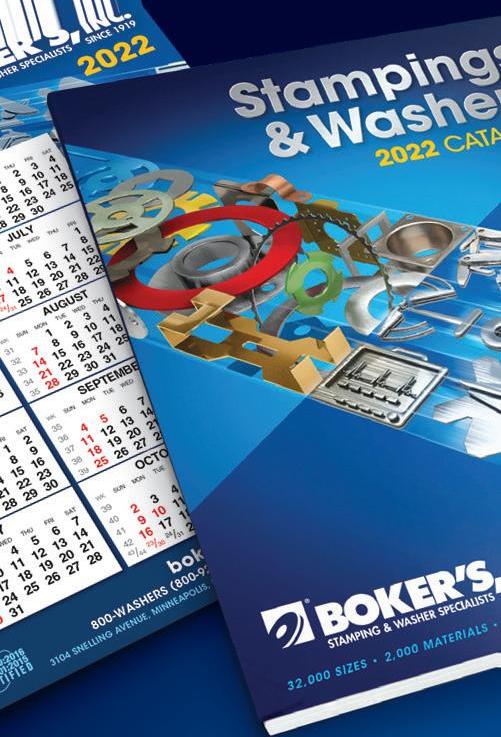
that has built trusted customer relationships over the years, NEI has embraced the Connected Smart Factory as a strategic priority for transformation to meet quality and production capacity demands. The specifi c focus of the transformation has been an Industry 4.0 implementation to render real-time data, reports and dashboards that are accessible by the shop fl oor and the top fl oor, with the goal of driving enhanced plant-fl oor decision making, improved predictive maintenance and increased overall equipment e ciency (OEE). Previously, data had been captured on paper and logged into a non-real time system – resulting in a 24-hour delay that, in eff ect, had manufacturing teams looking at yesterday’s data to make today’s decisions. At various stages of the production process, the data were captured in data sheets and collated at end of a shi . Management saw the need for an Industry 4.0 solution to enable real-time data analysis so breakdowns and maintenance could be better predicted before a potential failure. To replace the paper logs and non-real-time systems, the team developed a digital strategy to connect more than 300 CNC machines and PLCs to a single IIoT network. This would be done using a diverse set of controllers of various generations, makes and models – creating an OPC Unifi ed Architecture data layer and IoT Platform deployment. The result would enable various users in the organization, om shop fl oor to the top fl oor, to render real time data with sophisticated, accessible reports and dashboards for decision support.
Cross-disciplinary collaboration was critical for IT/OT alignment In building a strategy, the team placed importance on cross-disciplinary and inclusive teaming, particularly across IT and OT teams. This included a comprehensive change management program and engagement om all stakeholders in the organization. IT and OT collaboration was formalized as part of the digital transformation playbook, and standards were aligned for the data architecture design. The IT team focused on hardware, networking and connectivity; OT teams dealt with machine data and machine so ware. Review and governance at the highest level helped keep these team members aligned and collaborating to ensure the project remained on track. Team members also brought in domain experts and organizational stakeholders om the technical, functional and business perspectives. Digital team members acted
as translators and facilitators om business to technology realms, and IoT Platform experts were hired to roll up the data of machines into a visualization layer and provide decision making empowerment to ont line supervisors, plant heads and other personnel.
Project implementation and outcomes All fi ve NEI factories are currently executing the Industry 4.0 DX initiative, with contingency planning in place to ensure upgrades pose minimal disruption to the implementation of the new systems. The Jaipur factory is already at scale implementation – having been chosen as the fi rst location for full scale deployment based on its existing emphasis on automated operations. The remaining four plants are now targeted to be brought onto the real-time data and application mode in the next eight months. Rockwell’s focus for NEI has been on developing an agnostic solution to bring all machines on the same IIoT platform, which was made more challenging by having a mix of earlier generation controllers and equipment. Rockwell handled application development services, with management and IT consulting handled internally by NEI team members, as well as the machine connectivity to the OPC layer. Already, the project is achieving success toward specifi c goals that included driving the overall equipment eff ectiveness (OEE) of the factory 2-3% above baselines of 78-80%. As such, the 2-3% goal is a signifi cant stretch in OEE, and it’s being made possible by a more paperless factory; real time shop fl oor data; decision making empowerment at all levels; and a new workforce culture focused on a proactive, versus reactive, mindset for work and problem-solving.
Continuous learning and improvement As this digital transformation continues, the company is researching and developing new use cases around advanced analytics; augmented and mixed reality for shop fl oor training; collaborative workfl ows for streamlining information fl ow and process integration; machine vision for inspection and other Industry 4.0 innovations. Continuous learning is a priority throughout, with feedback loops for team optimization, technology data architecture adjustments and insights on failure points leveraged for process optimization. Given that any shop fl oor deployment will have many unknowns, these insights form the learning for future deployments and a ready checkpoint for resolution. As they prioritize use cases for digital transformation, the NEI team constantly assesses factors such as business impact, ease of implementation, organization-wide coverage, number of users impacted, cost of implementation, returns and benefi ts. And to ensure everyone stays aligned on the roadmap and goals for the transformation, the team maintains a dynamic and a comprehensive execution plan; with the project represented as part of team members’ Key Responsibility Areas (KRAs) and Objectives for the year. DW
Rockwell Automation www.rockwellautomation.com
MAGNETIC ENCODERS FOR POSITION FEEDBACK
Contactless, no wear and maintenance-free High positioning accuracy and resolution Economical, small, compact designs and custom solutions Flexible ring diameters and measuring lengths
Internet of Things
Wi-Fi antennas for 2.4GHz and 5GHz applications

The X9001748 Series external,
dual-band Wi-Fi antennas have a standard, ready-to-use, RoHS-compliant design with IP67 sealing for reliable outdoor operation and provide highgain, high-e ciency, and high-reliability performance in low- and high-band applications with a variety of device confi gurations and equencies spanning 2,400–2,485MHz and 5,150–5,850MHz. The series’ ready-to-use, and RoHS-compliant design results in fewer design changes, enables quick and easy implementation using standard or reverse-polarity (RP) SMA connectors, and hastens product development and time-to-market. Its range of equency options, high-gain, -e ciency, and -reliability performance, and IP67rated protection against both dust and immersion (1 m for 30 minutes) make it suitable for use in 2.4GHz and 5GHz indoor and outdoor Wi-Fi, Bluetooth, ISM, and Zigbee applications including routers, gateways, access points, IoT gateways and devices, smart meters, home automation equipment, smart city in astructure, smart agriculture, machine-to-machine (M2M) communication, telematics, structural health monitoring, and predictive maintenance. The external, dual-band Wi-Fi antennas are currently available as four part numbers, all of which have linear polarization and thermoplastic polyester elastomer (TPEE) radomes, measure 180 mm ±2 mm in height and 12.98 mm ±0.20 mm in diameter, and weigh 24 grams. They are also available in black and white and with SMA or RP-SMA male connectors for additional design fl exibility. In terms of performance, these Wi-Fi antennas exhibit 50Ω feed-point impedance, less than -9.00 dB return loss, 3.2 dBi peak gain, and 71% average e ciency in low-band (2.4GHz) applications and less than -7.33 dB return loss, 3.6 dBi peak gain, and 68% average e ciency in high-band (5GHz) applications, and are rated for operating temperatures spanning -40°C to +120°C. Leadtime for the series is currently nine weeks. DW