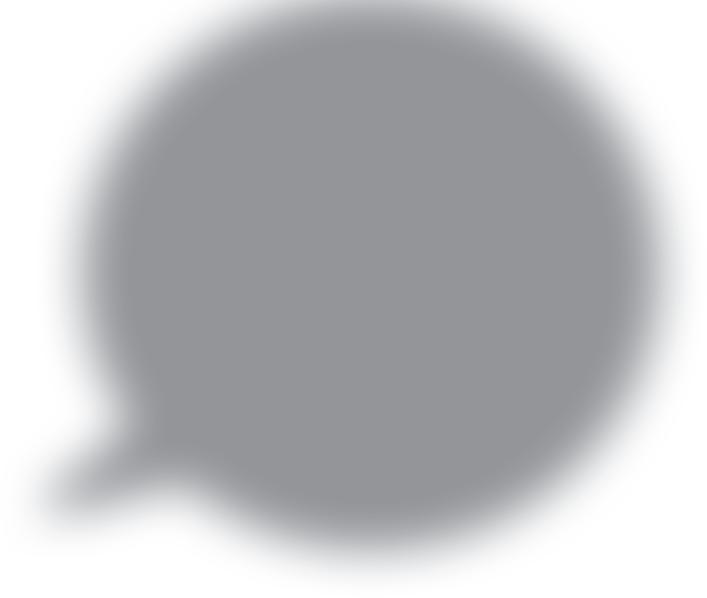
12 minute read
DfAM
Design for Additive Manufacturing
Blue industrial lasers make it easier to work with reflective metals in additive manufacturing
Jean-Michel Pelaprat, Founder & Chief Marketing and Scientific Officer Mark Zediker, Founder & Chairman • NUBURU, Inc.
The blue laser is a relatively new entrant into the additive manufacturing arena, and, as such, work has just begun to determine the optimum process parameters.
In 2017 the fi rst high-power industrial blue laser reached the market. It rapidly demonstrated unmatched speed and quality for welding copper, aluminum, and many other industrially important materials. The same fundamental physical characteristics needed for welding refl ective metals also suit additive manufacturing. Continuing technological advances allow the blue laser to quickly produce nearer net-to-shape parts at high material density in copper, steel, Inconel, and other industrially important metals. The blue laser’s advantage over incumbent in ared technology in both powder bed and laser metal deposition make additive manufacturing even more attractive for automotive, medical, aerospace, and other applications. Additive manufacturing for metals Additive manufacturing — 3D printing — started as a method to quickly produce prototype parts to check form, fi t, and function. Many early 3D printers used photo resins to create a desired part. The technology matured to off er a handful of diff erent fabrication styles for a wider range of materials. For additive manufacturing of metals, two approaches dominate: powder bed fusion (PBF), covering about 95% of applications, and laser metal deposition (LMD), generally for larger parts. Although alternative methods of energy deposition are available, lasers are the most fl exible and straightforward mechanism. In PBF a layer of metal powder is spread uniformly over a build plate prior to applying the laser power. A laser spot traverses the working area, causing the powder to melt and fuse in areas where the part is to be created. A er the targeted areas of powder have been fused on a given layer, another layer of powder is spread over the part and the process repeats as the laser fuses new raw material to the previously fused material. The maximum dimension of parts produced by PBF is generally limited to about 50 or 60 cm. Larger metal parts can be produced with LMD. In LMD a laser beam is directed to a metal substrate, where it creates a melt pool. Metal powder entrained in a gas jet or a short length of wire feedstock is sent into the melt pool, fusing into it and incrementally adding to the part. LMD part size is limited only by the range of the in astructure — the delivery system that directs the laser and feedstock. There’s a clear threefold logic driving growth in additive manufacturing. It
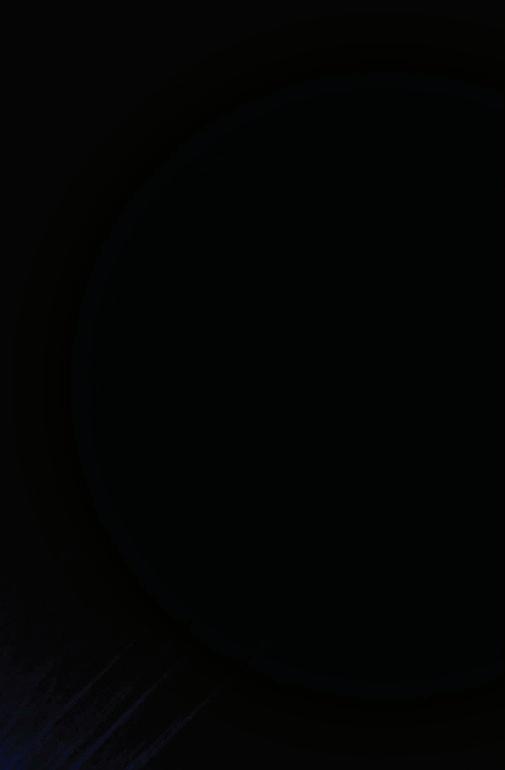
In less than fi ve years the blue industrial laser has brought qualitative and quantitative advantages to a variety of industries — and is now bringing those same benefi ts to additive manufacturing.
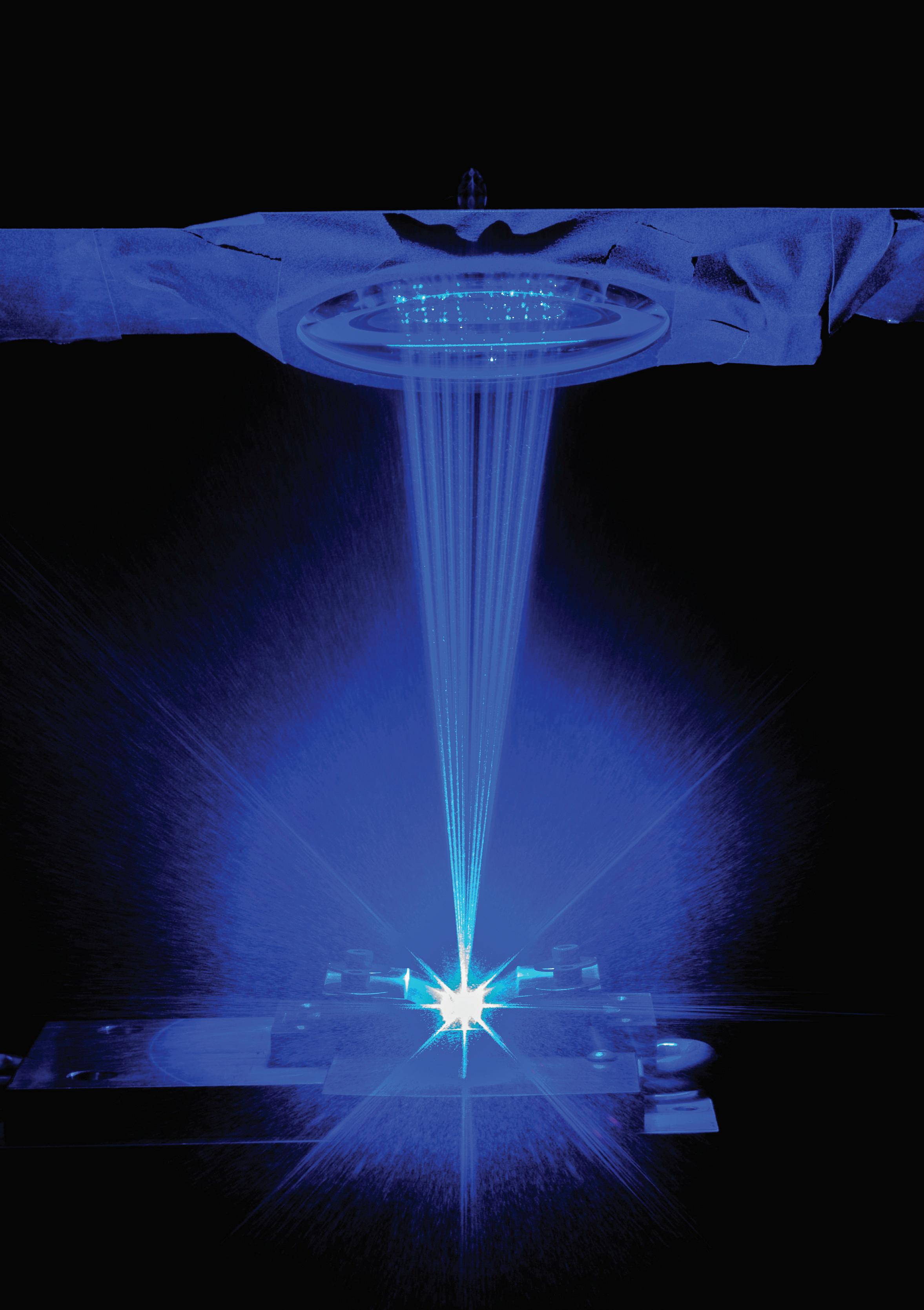
Design for Additive Manufacturing
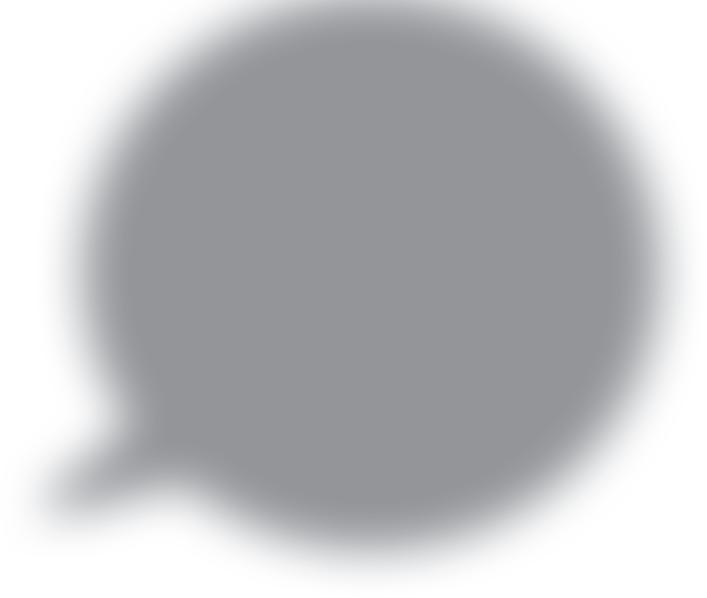
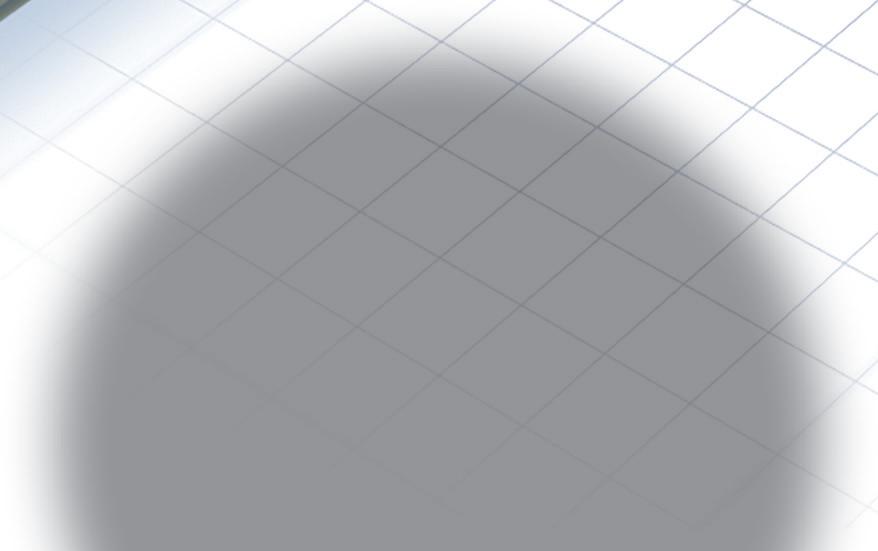
Figure 1. Additive manufacturing can produce complex parts where needed, simplifying logistics and reducing costs.
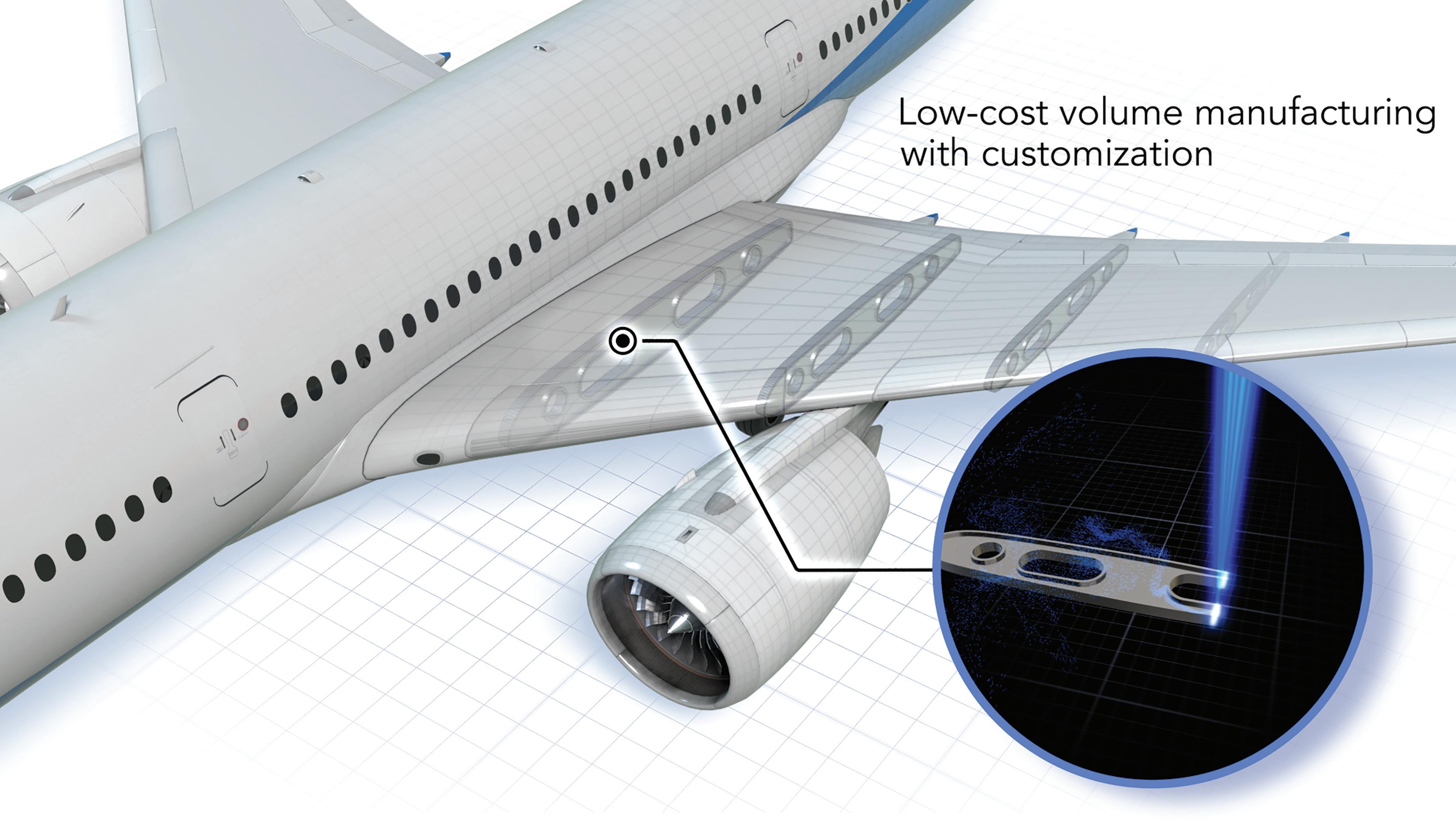
reduces raw material waste; it replaces several (typically costly) assembly operations with a single fabrication step; and it simplifi es logistics for complex operational support, bringing the “supply chain to the edge,” as illustrated in Figure 1. The logic of additive manufacturing only prevails, however, where performance of manufactured parts matches or exceeds that of parts or assemblies produced by traditional methods — and at a competitive cost. For many refl ective metals, the in ared laser cannot reach that goal. The blue laser has proven it is better than IR lasers for welding copper and other industrially critical metals, producing defect- ee copper welds at speed. That ability is founded on fundamental physics: copper, aluminum, nickel, and other refl ective metals absorb blue light better than they absorb other wavelengths.
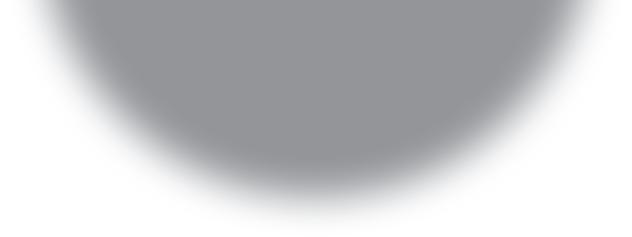
Making “good” parts The fundamental measure of part quality is simply how closely the dimensions match design targets. Equally fundamental: the part’s mechanical strength must meet design requirements. These are both inherent challenges for additive manufacturing. For fabricating to design dimensions, additive manufacturing o en requires support elements that must be machined away, and the incremental addition of material leads to surfaces that usually require at least some degree of grinding and polishing. The goal is to reduce those post-fabrication operations to a minimum, that is, to achieve a near net-to-shape part. Providing mechanical strength is also a challenge for IR-based additive manufacturing, fi rst because the layer addition process itself is inherently prone to introduce voids in the fi nished part, and second because poor fusion of feedstock metals can diminish the fi delity of internal bonding. Compared to traditional IR additive manufacturing, blue provides a “quiet” fusion process. Blue lasers can operate in a conduction mode regime, versus keyhole mode
Design for Additive Manufacturing
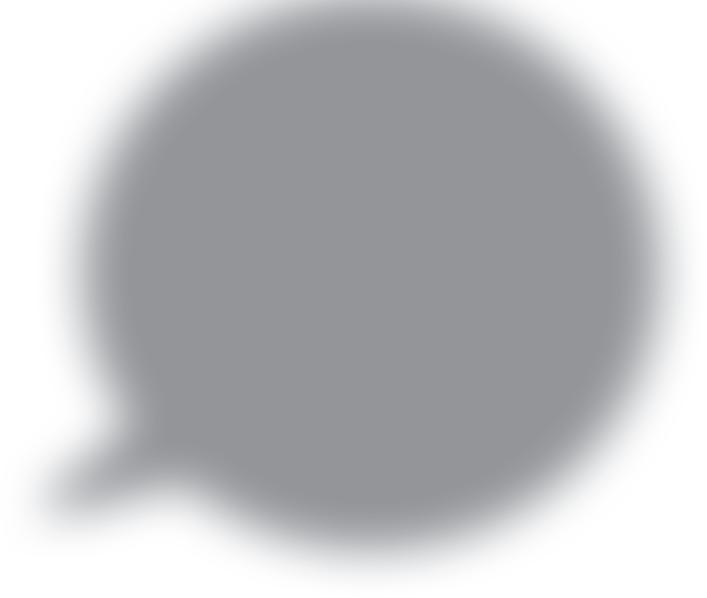
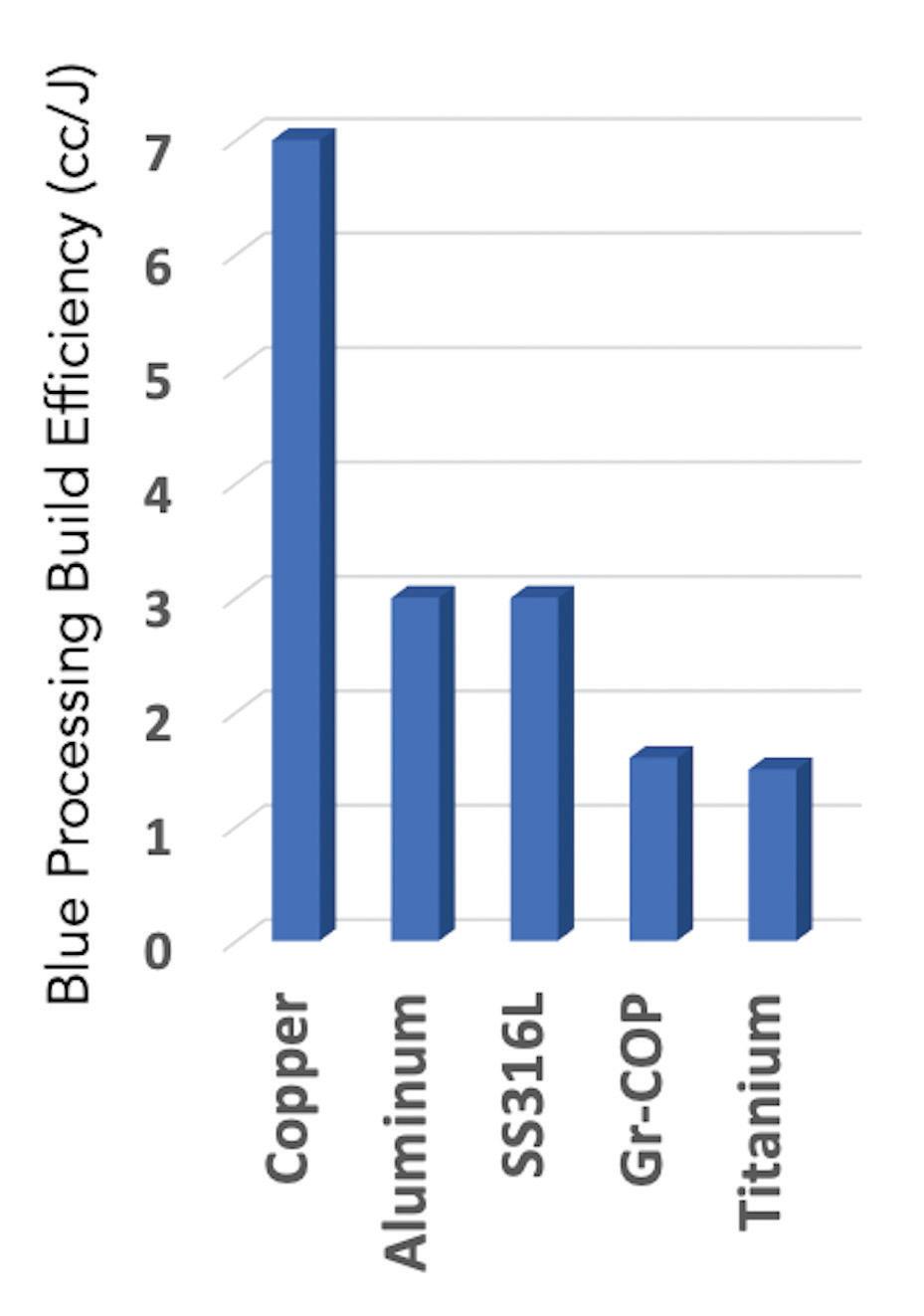
Figure 2. The build e ciency of
the blue industrial laser already exceeds that of IR for most.
operation — the only option for IR processing of refl ective materials. The keyhole IR process vaporizes the metal, creating defects, and consequently reduces fi nished part density. IR processing also ejects metal particulates, requiring expensive gas handling to get rid of them. Blue quiet mode means high metal densities close to that of the base metal can be achieved with a much simpler and lower-cost gas handling system. Part density is a primary measurement of the e ciency of the bonding process. Once a process has demonstrated the ability to achieve a certain maximum density, it can be adjusted to create mesh structures that provide a high strength-to-weight ratio. The voids in a mesh structure must, of course, be intentionally introduced by design, and not as a side eff ect of a poorly controlled process. The blue laser is a relatively new entrant into the additive manufacturing arena, and, as such, work has just begun to determine the optimum process parameters. Even at this early stage, the blue laser matches the high expectations set by its performance in welding. As seen in Table 1, the blue laser produces parts at rates comparable to or signifi cantly faster than the incumbent IR technology, with improved quality. But quality is only part of the story. Any new technology must not only demonstrate its capability, but also show its readiness to step into a manufacturing environment, where stability and reliability are essential.
Stability and reliability Although the blue laser is relatively new to the additive manufacturing world, it benefi ts om its previous deployments in factory environments. The blue laser is being used for welding in battery fabrication, consumer electronics production, and electric vehicle manufacturing. From its inception, the blue industrial laser was designed specifi cally with the inherent robustness necessary to provide reliable, stable operation in challenging production environments.
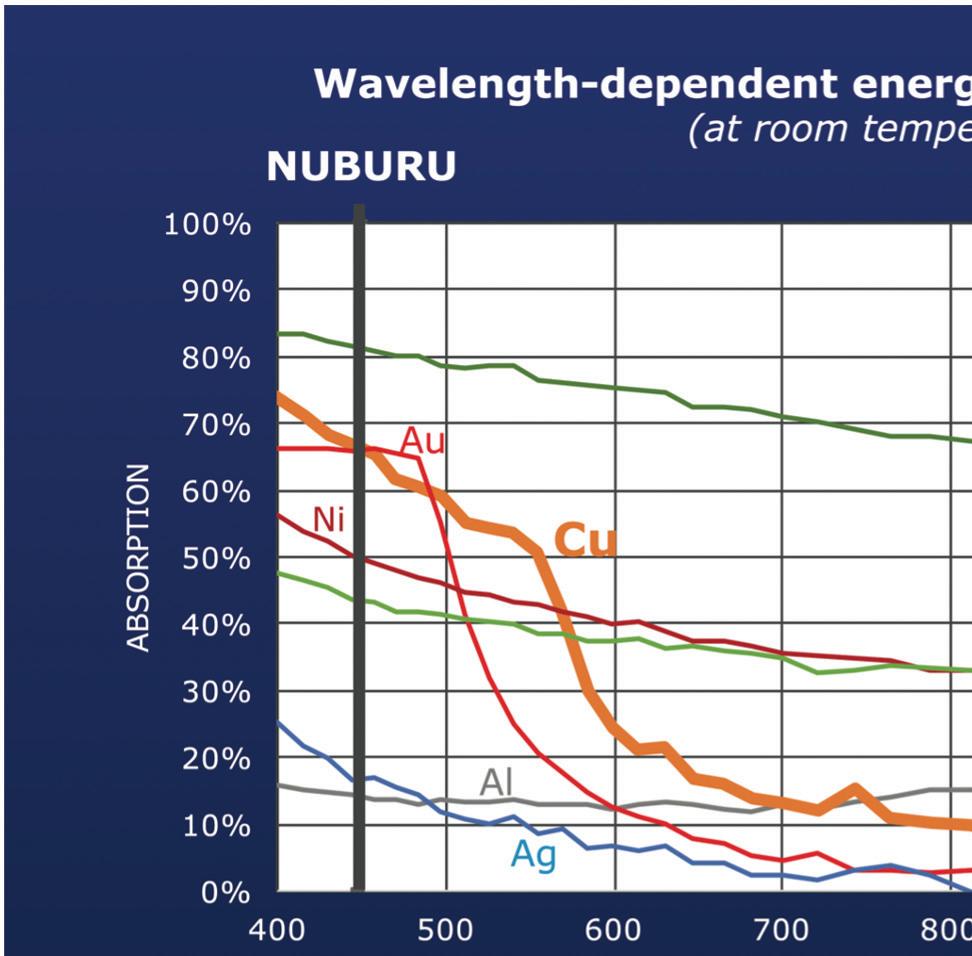
Figure 3. The blue laser is absorbed far better than IR in a wide range of refl ective metals.
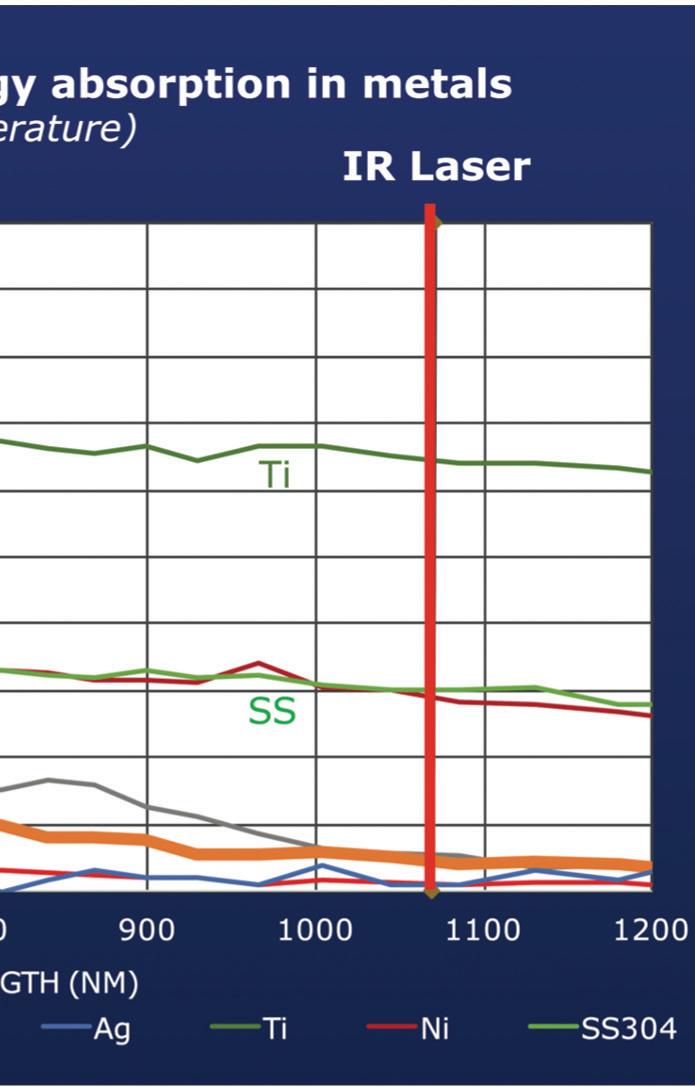

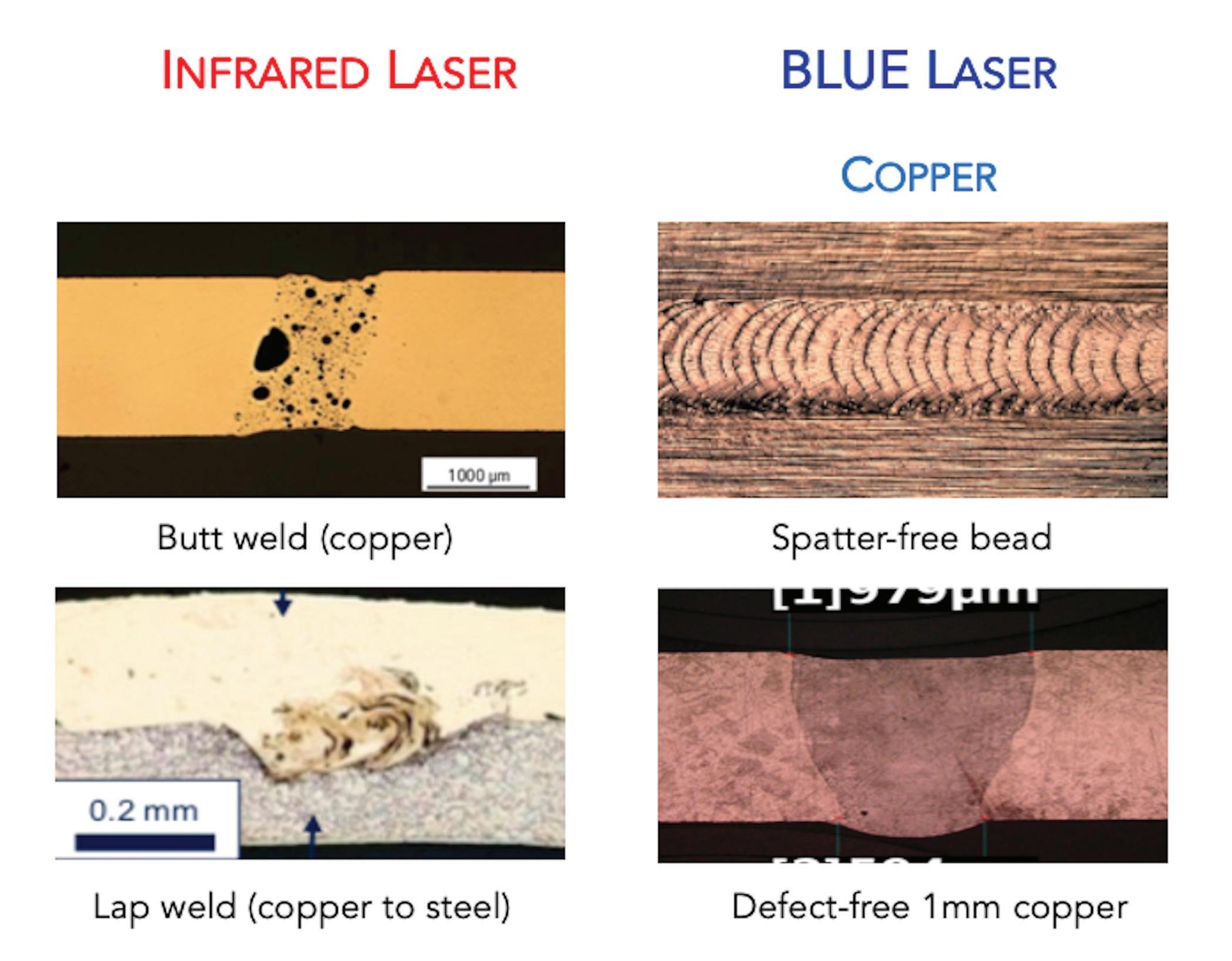
Figure 4. Poor IR absorption leads to poor weld quality, while high absorption of blue wavelengths
is the foundation of high-quality, high-speed reflective metal welding.
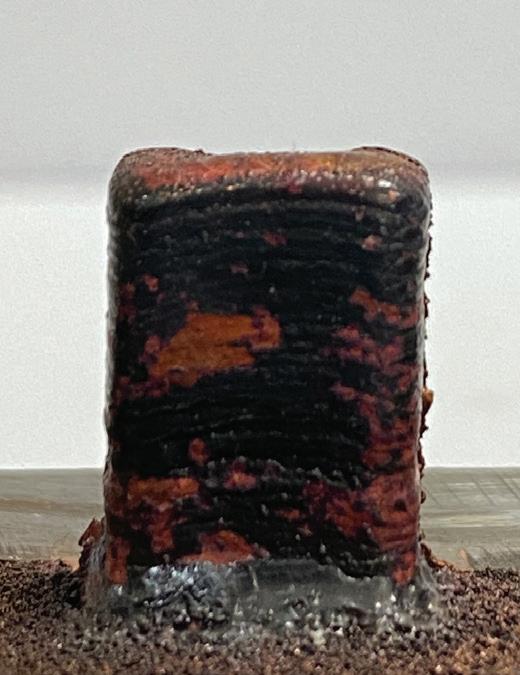
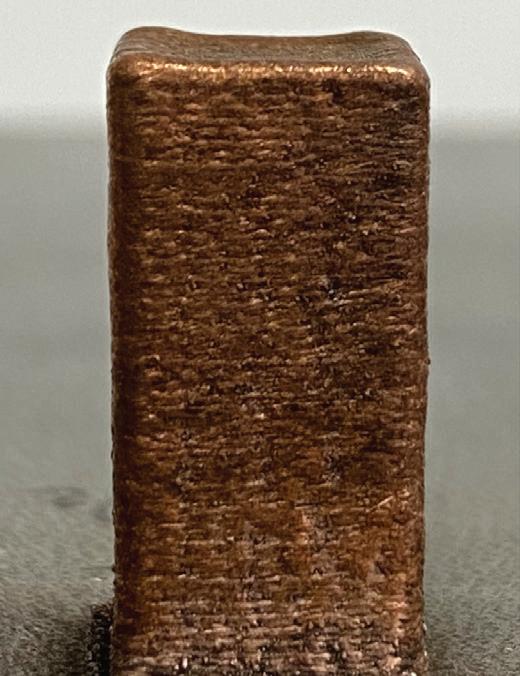
In general, lasers require precise internal optical alignment, and the NUBURU high-brightness blue laser, in particular, requires extremely accurate alignment, but proprietary design and fabrication techniques maintain that alignment even in uncontrolled environments. For example, the measured power degradation is less than 0.4% per thousand hours of operation. In addition, the modular design is tailored to minimize downtime should a module need replacement, with plug and play operation that rapidly returns the laser to the required output power.
Initial results indicate the blue laser’s performance advantages in welding translate effectively to additive manufacturing. Even without full process optimization, blue laser additive manufacturing generally matches or exceeds IR laser performance in both quantitative and qualitative metrics. And the blue laser has the advantage of a history of reliable service in fabrication environments, so even though it’s relatively new to additive manufacturing, the foundational technology has maturity borne from practical applications in a number of industries. Those characteristics combine to create
5A
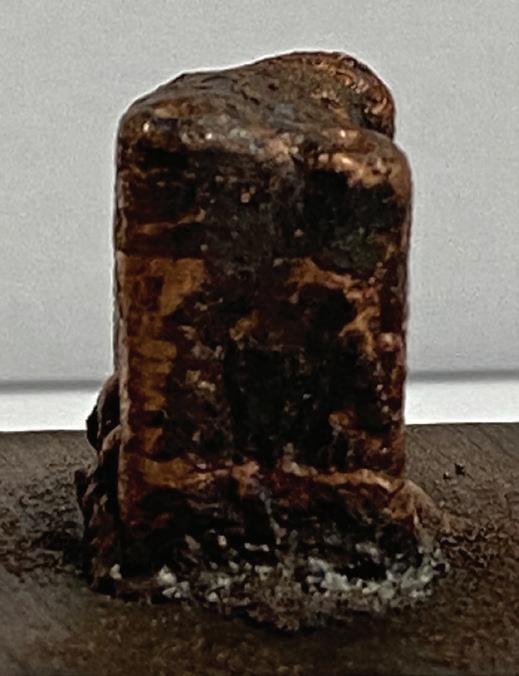
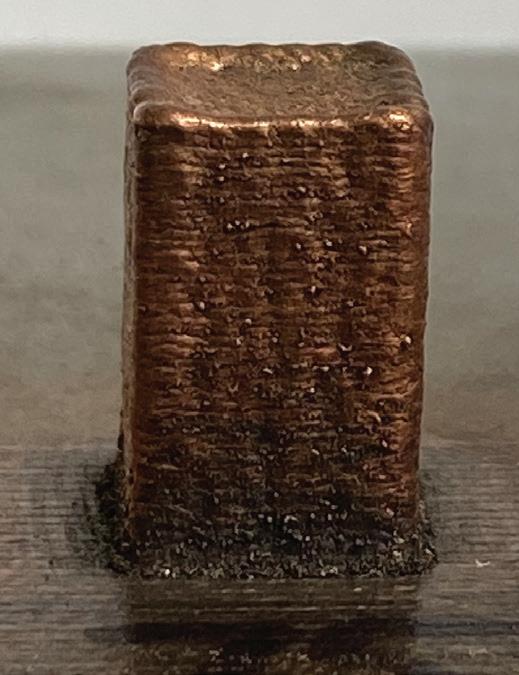
5C 5B
5D Figure 5. Additive manufacturing with the blue industrial laser is faster and more efficient than IR lasers, and the quality is quite evidently superior.
The images on the left show test blocks produced with the blue laser, while those on the right were made with IR. The top test blocks are of the GrCop alloy, and the bottom of pure copper.
Design for Additive Manufacturing
Building blocks of blue performance
Table I. Blue Laser LMD Performance Comparison with IR Metal Parameter Blue IR Blue/IR Change
Ti-64
Pure Cu Build Rate (cm3/hr) 11.76 9.3 26% Build Rate E ciency (cm3/hr/W) 0.0653 0.0423 54% Density (3rd Party) 97.8% 95.6% 2% Hardness (36 for Titanium) 35 34 3%
Build Rate (cm3/hr) 5.35 2.6 106% Build Rate E ciency (cm3/hr/W) 0.0089 0.0013 576% Density (3rd Party) 94.4% 92.75% 2% Hardness (3rd Party) (68 for annealed Cu) 59.0 49.1 20%
The blue advantage
a set of circumstances ripe for rapid advancement in blue laser additive manufacturing. The fundamental physical advantages of the blue laser and the similarity between welding and PBF and LMD processes made it reasonable to expect that the blue laser would excel in metal additive manufacturing. But theoretical advantages do not always translate into real world performance, so it was essential to evaluate the blue laser’s capabilities in commercial equipment. NUBURU partnered with an additive manufacturing company to perform tests in both the IR and blue using LMD with a variety of metals commonly used in additive manufacturing. Titanium alloys are light, strong, and corrosion resistant, so they’re commonly
Materials processing applications are all about transferring energy om some external source into a target material. When the external source is a laser, the e ciency of energy transfer depends upon how closely the energy of the laser light matches the energy levels of the target material. The energy carried by a photon is a function of the wavelength of light, while absorption of the target material is based on its energy levels, which depend on its constituent atoms, their chemical arrangement, and the material’s physical state. For example, as seen in Figure 3, copper absorbs only about 5% of incident light at wavelengths around 1 µm — a common in ared laser wavelength. Thus, the IR laser welding process is inherently ine cient when compared to blue light lasers. When the IR laser delivers enough energy to melt the copper and start the weld, the melted copper now absorbs incident IR laser energy at a much greater rate. The result is a runaway process where the “extra” energy — the 95% that was refl ected — is now absorbed. That extra absorption leads to rapid vaporization of the metal causing miniature explosions, sending particles of copper fl ying and leaving holes behind.
The blue laser stands in stark contrast. Copper absorbs blue light more than 13 times better than it absorbs IR — and the absorption is almost the same when the copper melts. That allows for a wide process window — a large range of laser power settings and weld speeds capable of joining copper with none of the particle ejection or consequent voids om IR laser processing — leading to 3D printed part density that can exceed 95% as printed compared to the 80% achieved with an IR laser. As seen in Figure 4, the comparison between IR and blue laser performance for copper welding illustrates the advantage of the blue laser, but it’s not the only one. The same description can be applied to nickel, aluminum, and alloys such as Inconel. And blue holds that advantage not only over IR, but over other visible wavelength lasers as well. For example, copper absorbs blue 20% more e ciently than it absorbs green. The fundamental physical advantage has already brought benefi ts to a variety of industries, including energy storage, consumer electronics, and e-mobility, where the process improvements have led to production e ciencies and higher product quality. Now, that proven advantage is being turned to applications in additive manufacturing.
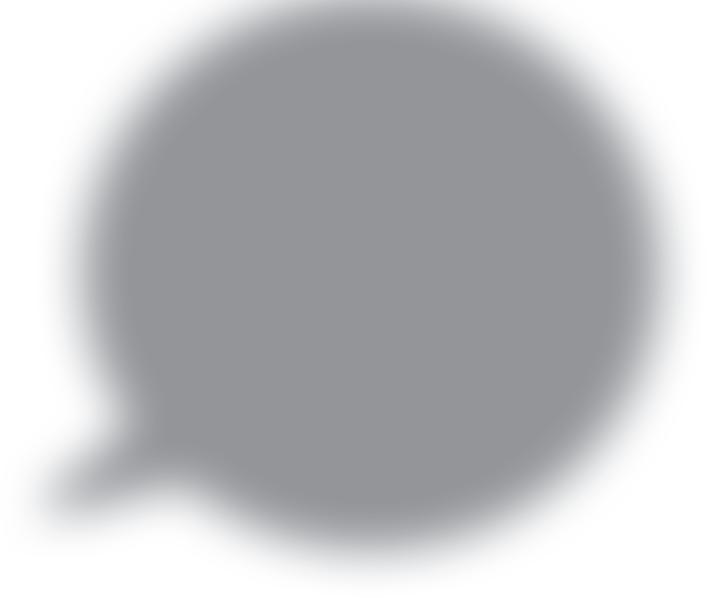
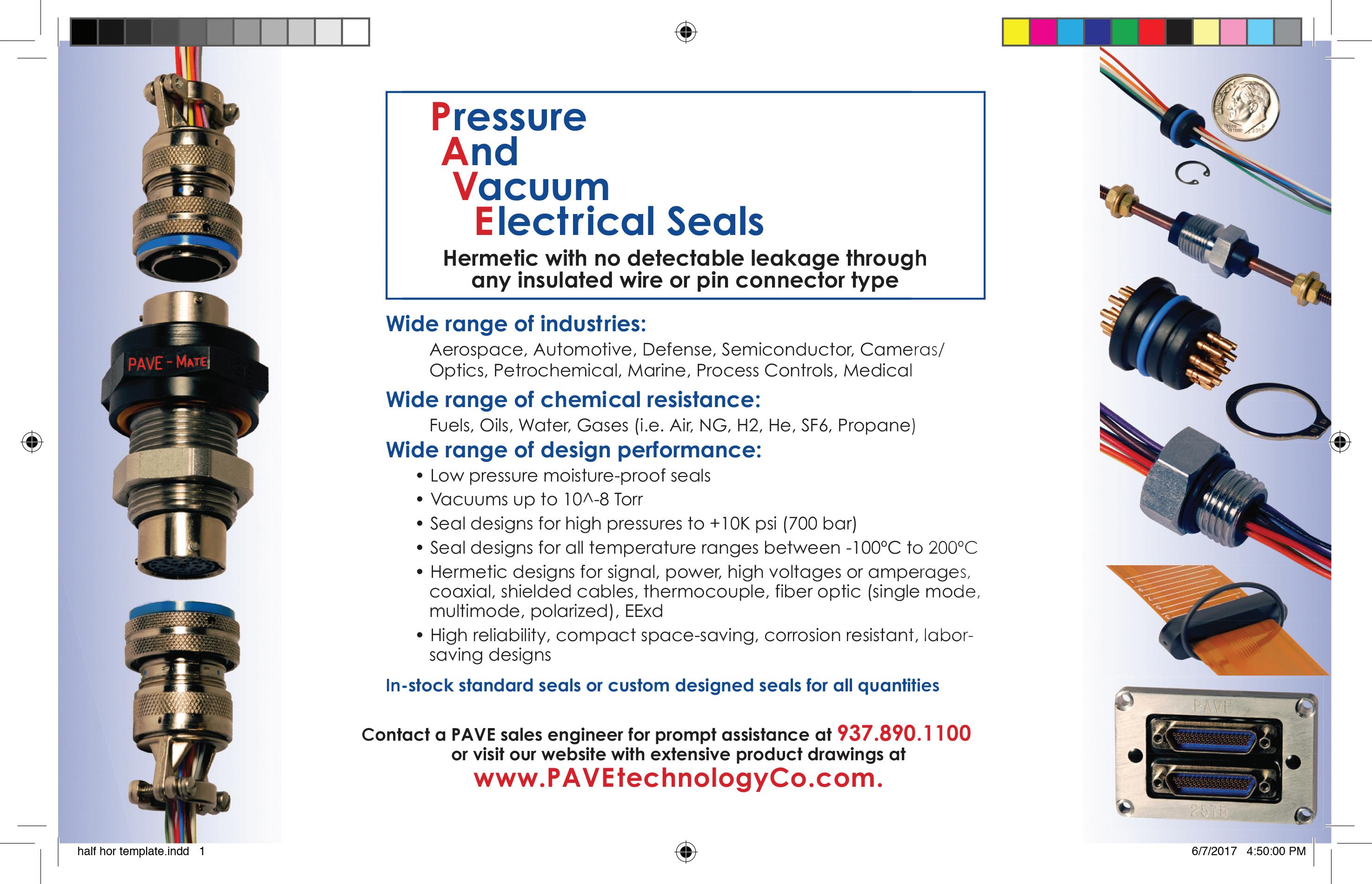
used for high value parts. Ti-64, for example, is a non-magnetic titanium/ aluminum/vanadium alloy with excellent corrosion resistance, a high strength-toweight ratio, and good fatigue resistance. Those qualities, along with an eff ective temperature range om cryogenic temperatures up to more than 800°F, make it a useful material in applications ranging om aircra structural members to prosthetic joints. A comparison of the production of one-inch Ti-64 blocks using both IR and blue lasers showed that the build rate for blue was more than 25% faster than the IR build rate, with better net-to-shape performance for blue. In addition, third-party testing showed the blocks produced with blue had both higher density and greater hardness. Tests on pure copper — a material that has proven to be recalcitrant to incumbent additive manufacturing processes — demonstrated the blue laser produced one-inch test blocks at more than twice the rate of IR. As illustrated in Figure 5, blue also provides signifi cant qualitative improvements in net shape, surface quality, and the same third-party verifi ed improvements in density and hardness. These initial tests veri the expected blue advantage in speed and quality, but there’s an additional parameter of equivalent importance: e ciency. For additive manufacturing this is conveniently expressed by the metric of build rate e ciency, here measured in cc/ hr/W or cc/J, as in Figure 2 — essentially, how much part volume you get for the power you put in. DW
NUBURU, Inc. www.nuburu.net
WHAT DO YOU THINK?
Connect and discuss this and other engineering design issues with thousands of professionals online