
10 minute read
3DP-AM
Design for 3D printing and Additive Manufacturing
Accelerating assembly with 3D printed jigs and fixtures
orth American Lighting (NAL), a Koito Group Company, has been manufacturing automotive lighting systems for vehicle manufacturers since 1983. With eight facilities across the U.S., NAL provides advanced lighting technology, engineering design expertise, and state-of-the-art production capabilities. NAL works with some of the largest automotive OEMs in America like Ford and GMC, so speed and precision are critical. To that end, assembly production tools are essential to ensure that production continues smoothly. If a part breaks, that could N mean extended lead times and added costs. Joey Carpenter, production engineering technician, began using 3D printing to bring tooling production in-house and reduce potential disruptions. Carpenter was new to 3D printing when he was introduced to the MakerBot METHOD X series in early 2022. Since then, Carpenter, who handles robotic builds and cycles in new end of arm tools for production runs on new launches, has become the resident expert. Before 3D printing, Carpenter and his team relied on external vendors to design, produce, and send back parts that they would need. Receiving a new part could take several weeks. This was less than ideal since orders were equently late, forcing them to readjust their timelines.
North American Lighting manufactures automotive lighting systems for vehicle manufacturers. Assembly production tools are essential to ensure that production continues smoothly.

“Now with a METHOD X in-house, there is minimal wait time,” said Carpenter. “In 12 hours, we have what we need to build an end of arm tool. Not only does this drastically reduce our wait times, but we are also seeing a massive cost reduction. The cost to 3D print a part in nylon carbon fiber is one-third the price of what we were paying for outsourced aluminum parts.”
“In addition, since we started 3D printing, our overhead costs decreased by half because we don’t have to stock up on excess parts,” he continued. “We have reduced part inventory by 50%. Now all of our tool designs are digital so they’re easier and quicker for us to access, iterate, and print as we need. Instead of waiting weeks, we can turn parts around in five days, from design to assembly.”
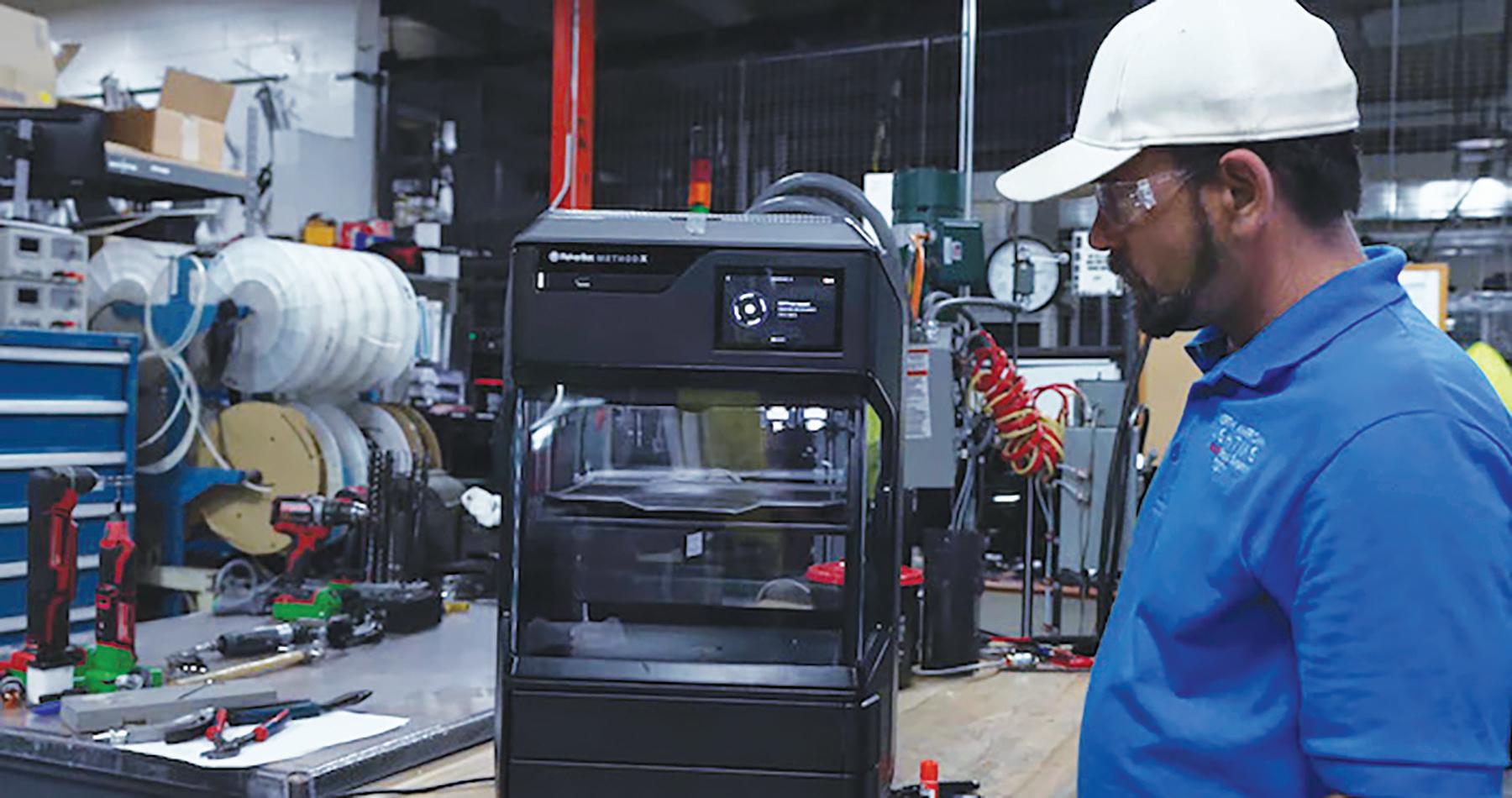
Leveraging Method X’s versatility In the Flora factory, the robots use around 200 end of arm tools a year, which are built in-house. Bringing tooling production in-house allows the team to significantly reduce costs while also saving them tremendous amounts of time.
While Carpenter mainly prints end of arm tool parts, he has also found new applications where he can utilize the versatility of METHOD X. “We’ve also used in-house mockups and prototypes for water fittings and parts like that for future use. We prototyped with carbon fiber in house within a matter of three days, rather than outsourcing it which could take a month to get back,” he said.
“We’re finding that it’s very easy to replace aluminum with carbon fiber parts. With weight reduction and durability, carbon fiber is comparable to aluminum,” Carpenter noted. “With the LABS extruder, MakerBot and Jabil materials offered on the METHOD X, the tolerances and the consistency of your prints are far better than you can imagine.”
Carpenter’s team isn’t the only ones using METHOD X at the Flora facility. The Assembly and Lighting team at NAL also began using the printer to produce nest blocks for the assembly line. The nest blocks go into the tooling on the assembly line and are used to keep parts in place while the machine is working on them. Before METHOD X, the team would have to bring in one of their tool shop vendors to access their needs. They would have to then wait for the vendor to design the part and build it as well as wait for a quote for the part to be approved, before receiving the final product.
“There would be a four-to-six-week lead time before getting a part back,” said Dee Jay Griffith, manufacturing engineering technician. “And the cost would be pretty high— With METHOD X, we’re able to print a full nest for less than 10% of the cost and we’re able to do that faster.”
“The METHOD X and 3D printing helped my workflow by enabling faster lead times and cost savings that comes with being able to print my own things,” Griffith noted. “We’re now able to accomplish what we need to on these assembly lines faster and without having to rely on vendors’ timelines.”
Primarily printed in carbon fiber and PolyMax PC, the nest blocks are lightweight and durable. Since printing them months ago, Griffith has not yet seen any wear on them. He is also experimenting with different materials, constantly finding things they would like to print. For example, camera mounts, grease tips, leak test seals, and more.
While the teams at NAL are experiencing a significant savings in cost and time when using 3D printing, those are not the only factors for their use of METHOD X. Its ease of use and seamless ability to print carbon fiber as well as other industrial-grade materials with the MakerBot LABS Experimental Extruder have made METHOD X a must-have in their facility.
“We’ve already ROI’d this machine and we’ve only had it for a few months. Just in the savings of what we’ve already printed, not to mention the time we’ve saved doing it ourselves as opposed to waiting for a shop to come in to get it done,” said Griffith.
“I work for a multi-billion-dollar company and can afford any 3D printer out there but yet we have five MakerBots in house right now and there’s a reason for that,” Carpenter concluded. DW
In the Flora factory, robots use around 200 end of arm tools a year, which are built in-house using the METHOD X 3D printer.
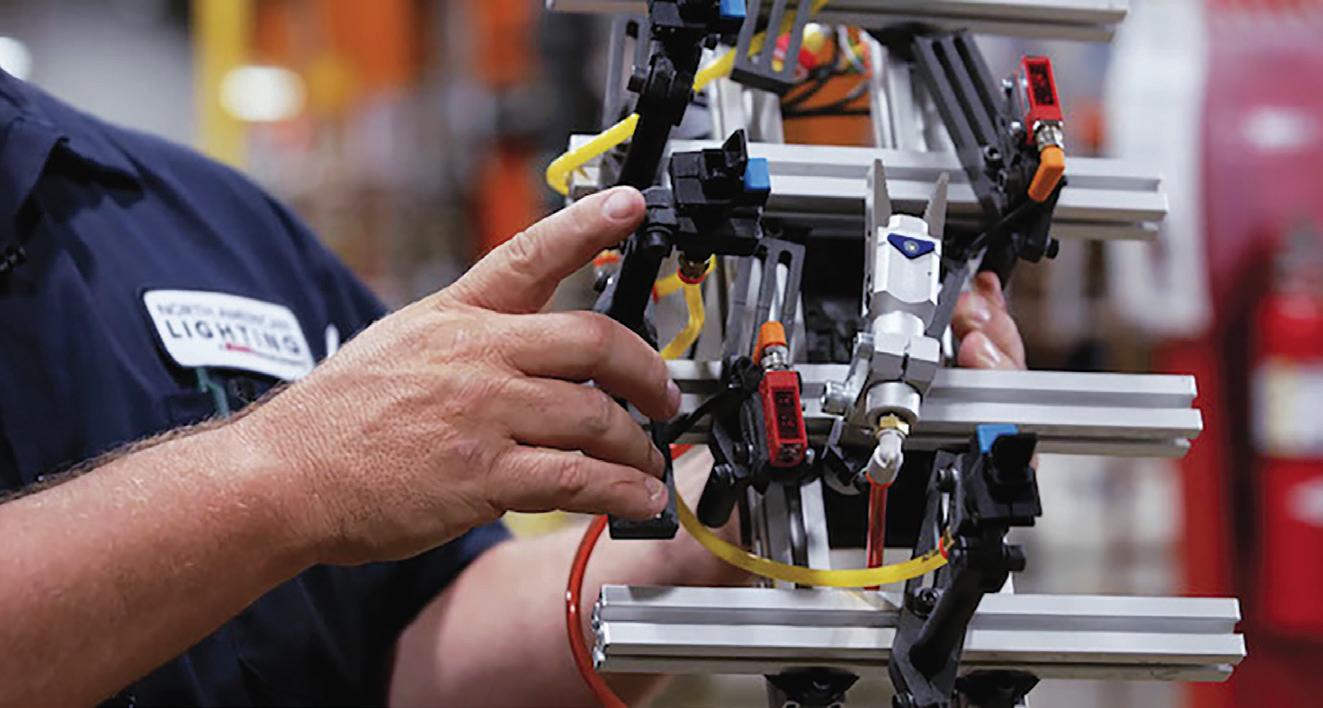
Design for 3D printing and Additive Manufacturing
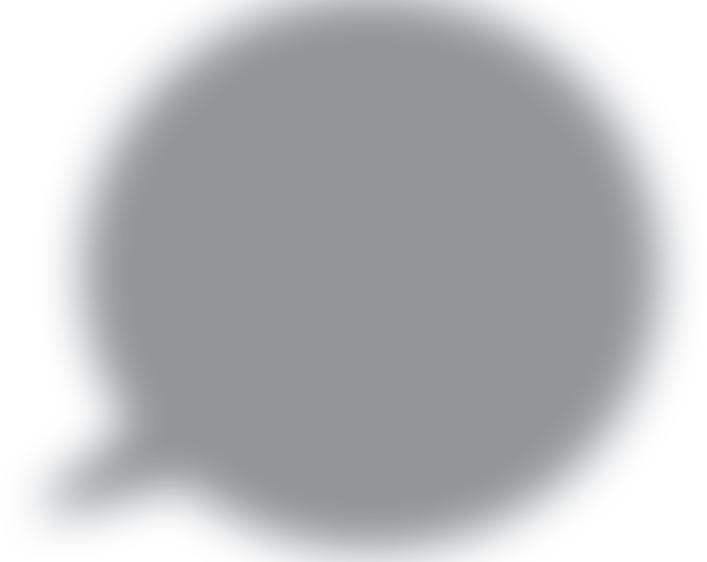

Desktop Metal expands lineup with Shop System+ and Shop System Pro
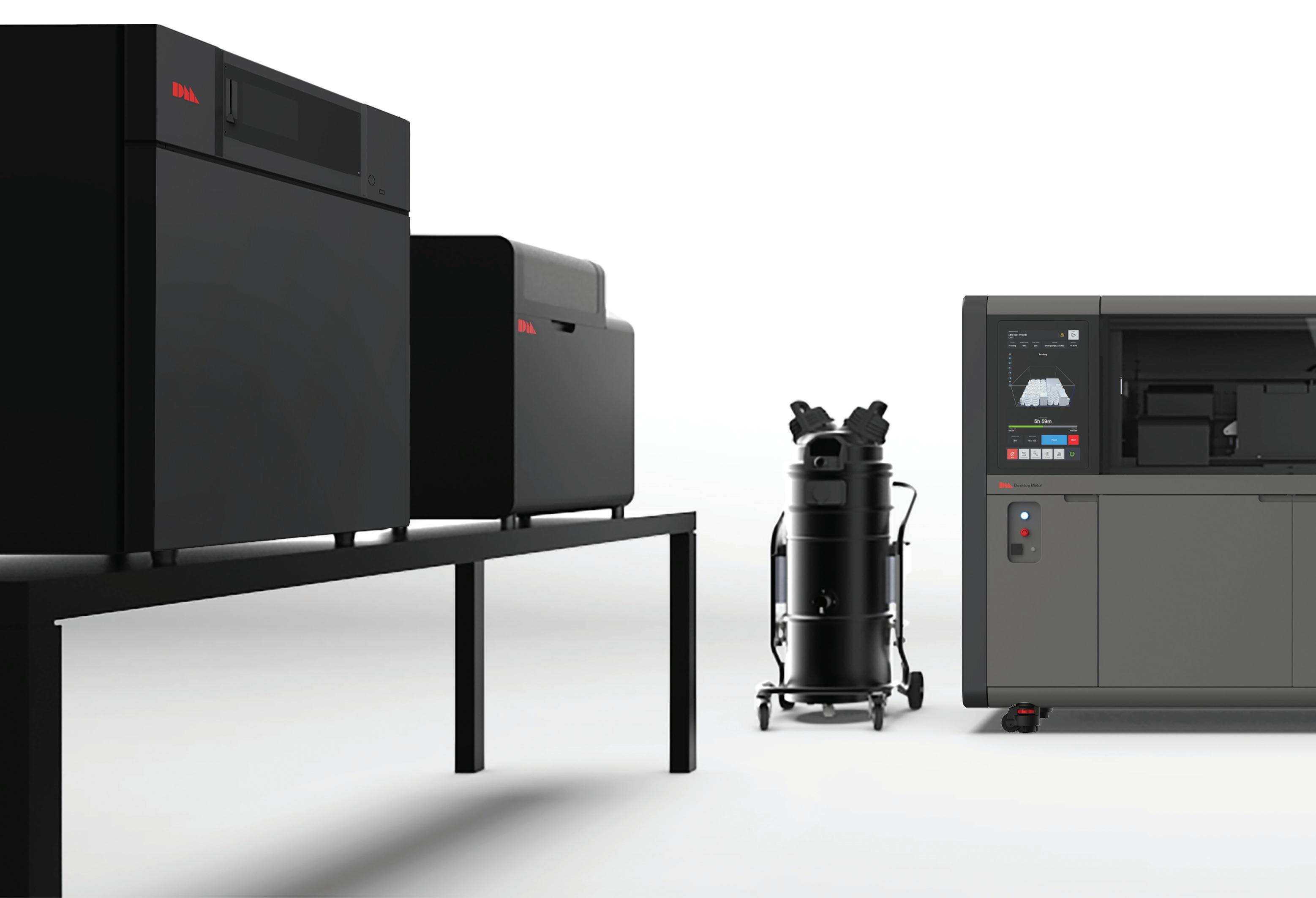
Desktop Metal announced two upgrade packages on its Shop System, off ering new fl exibility, functionality, and value for this metal binder jet system. The Shop System+ and Shop System Pro off er new options for materials and controls. The Shop System+ package enables users to access Desktop Metal-engineered powders and binders at a discount to MSRP, reducing the running costs of their additive manufacturing operations and improving their part costs to drive a faster return on investment. The Shop System Pro package is for high-production users with powder metallurgy expertise who seek not only to optimize their running costs, but also to enable specifi c applications or cost structures by leveraging proprietary or third-party powders. This Shop System Pro package includes all the benefi ts of the Shop System+ package as well as additional process fl exibility through new features, such as custom printing and spreading parameters and bi-directional printing for the Shop System Printer and custom sintering profi les for the Desktop Metal Furnace.
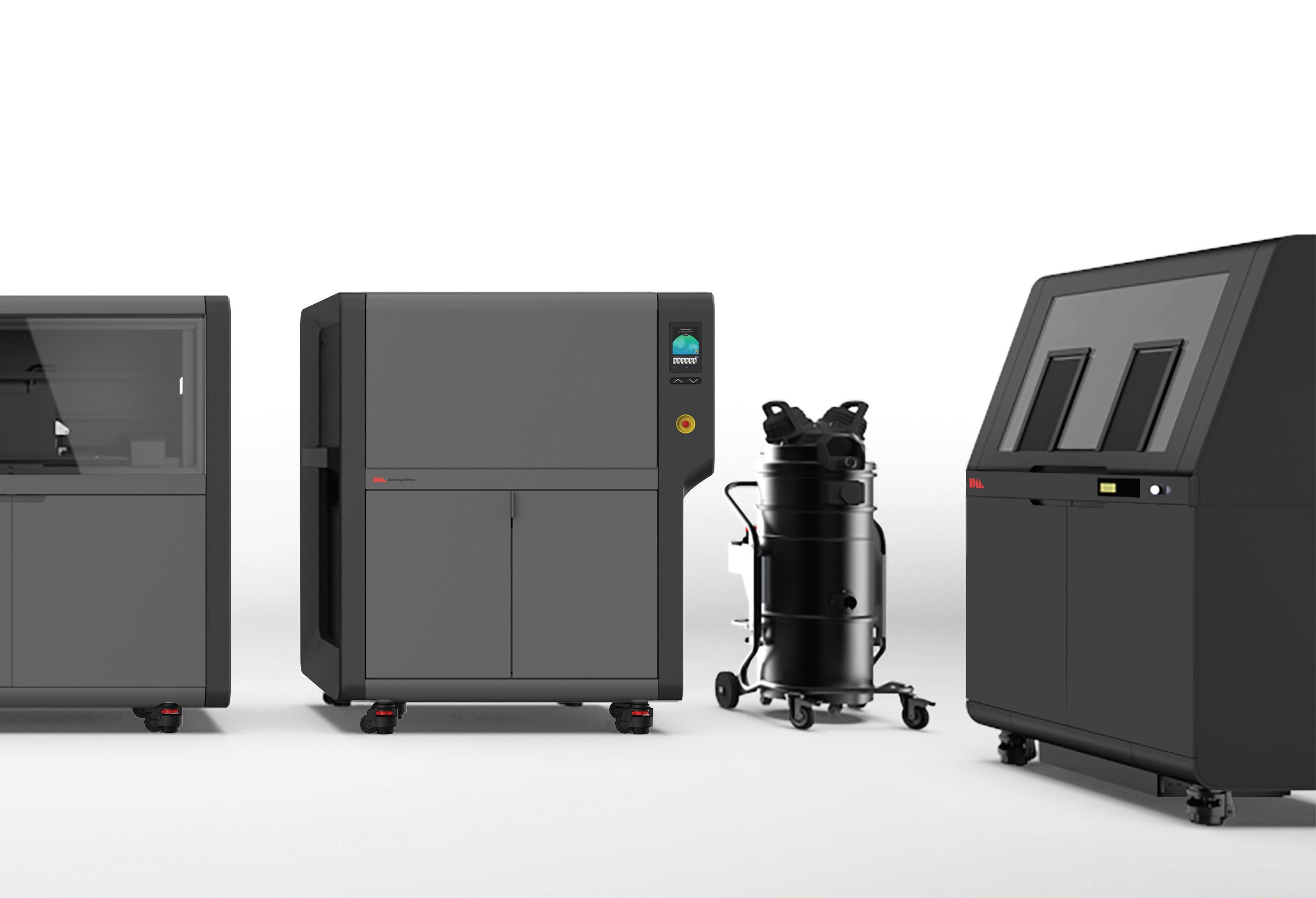
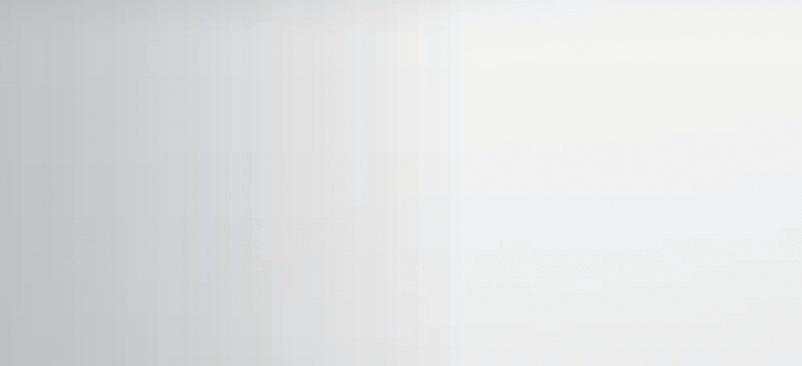
Shop System details Featuring the highest resolution and most advanced single pass print engine in the binder jetting market, the Shop System is a complete end-to-end solution for producing complex, end-use metal parts that includes: • a binder jetting printer with 1600 native dpi resolution and 5x nozzle redundancy, • a drying oven for hardening green parts prior to depowdering, • a powder station for depowdering parts with built-in powder recycling, • a furnace designed for accessible, industrial-strength sintering, • integrated powder handling accessories and workfl ow, • Desktop Metal-engineered binders and powders, and • Desktop Metal so ware for build preparation and sintering simulation.
This turnkey solution, designed with the modern machine shop in mind, seamlessly integrates with existing shop operations and makes it easy for businesses to get up and running with binder jetting in days instead of weeks or months. DW
Desktop Metal www.desktopmetal.com
Design for 3D printing and Additive Manufacturing
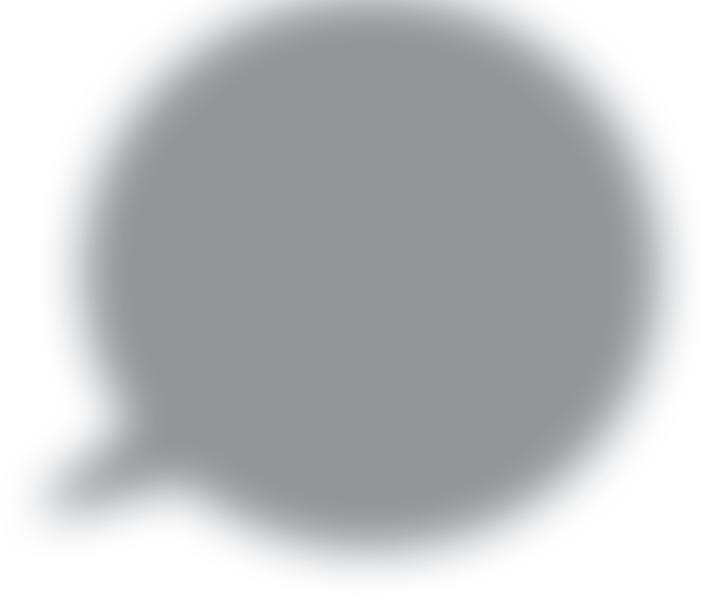
Materialise secures its CO-AM platform with the acquisition of Identify3D M
aterialise has acquired Identi 3D, a
company that develops so ware to encrypt, distribute and trace the fl ow of digital parts across complex supply chains. Data security and integrity have become top of mind for companies that want to retain control over their design and production data, as they transition om a centralized production model to multiple digital production sites, closer to their customers. The acquisition of Identi 3D makes Materialise’s CO-AM platform the most secure platform for distributed manufacturing. The Identi 3D product suite encrypts, distributes and traces the fl ow of digital parts, preventing counterfeits and ensuring that maliciously or inadvertently modifi ed, substandard or uncertifi ed parts cannot enter the physical supply chain. It also allows designers and manufacturing engineers to couple designs with specifi c production criteria, such as a designated user, a type of machine or material to control the production process and to meet the original manufacturing specifi cations. The Materialise CO-AM so ware platform gives manufacturers cloud-based access to a full range of so ware tools that allow them to plan, manage and optimize every step of the 3D printing process. At the heart of the CO-AM platform is a data lake that connects to all production tools and keeps track of what is happening on the production fl oor. Moving forward, CO-AM will off er the most robust and secure so ware platform to manufacturers that are concerned about protecting their design data, such as prototypes, and their unique production expertise. The acquisition of Identi 3D allows Materialise to add an additional security layer to CO-AM, making it the most robust and secure so ware platform for manufacturers that are looking to scale up their 3D printing operations as part of a digital and distributed production environment.
Shi to distributed manufacturing “We believe that the factory of the future will not be a single, central location”, says Fried Vancraen, CEO of Materialise. “Instead, future manufacturing, enabled by smart technologies like 3D printing, will take place at multiple digital production sites, distributed around the world, closer to customers. But this will only be possible when companies are sure that their design and production data remains secure. This acquisition allows manufacturers to secure the fl ow of digital parts and maintain a competitive advantage.” DW
Materialise www.materialise.com
WHAT DO YOU THINK?
Connect and discuss this and other engineering design issues with thousands of professionals online
Carbon acquires ParaMatters to expand design software for additive manufacturing C
arbon announced the acquisition of
ParaMatters, a software provider for additive manufacturing. This acquisition expands Carbon’s current software capabilities to include topology optimization. Carbon’s technology platform now broadens to enable product design and development teams to create better products in less time using a wide variety of materials and production systems.
The lack of modern design software that can quickly iterate and take advantage of the benefits of additive manufacturing continues to constrain the product development lifecycle. This acquisition addresses this gap and expands Carbon’s generative design software capabilities to enable increased automation and the creation of more complex, higher performance part designs. These benefits build on Carbon’s introduction of Design Engine™ earlier this year which is used by global brands to automate the process of developing latticed parts for production.
“We recognize the critical role software design tools play in our customers’ digital transformation. For far too long, designers have settled for software design tools that adhere to the limitations of traditional manufacturing,” said Phil DeSimone, co-founder and member of the Office of the CEO. “Many design tools of yesterday are not optimized to take advantage of industry innovations, including advanced 3D printing materials and manufacturing processes. Both Carbon and ParaMatters have shared the same vision to provide modern tools to ensure product development teams can create better products in less time.” DW
Carbon www.carbon3d.com