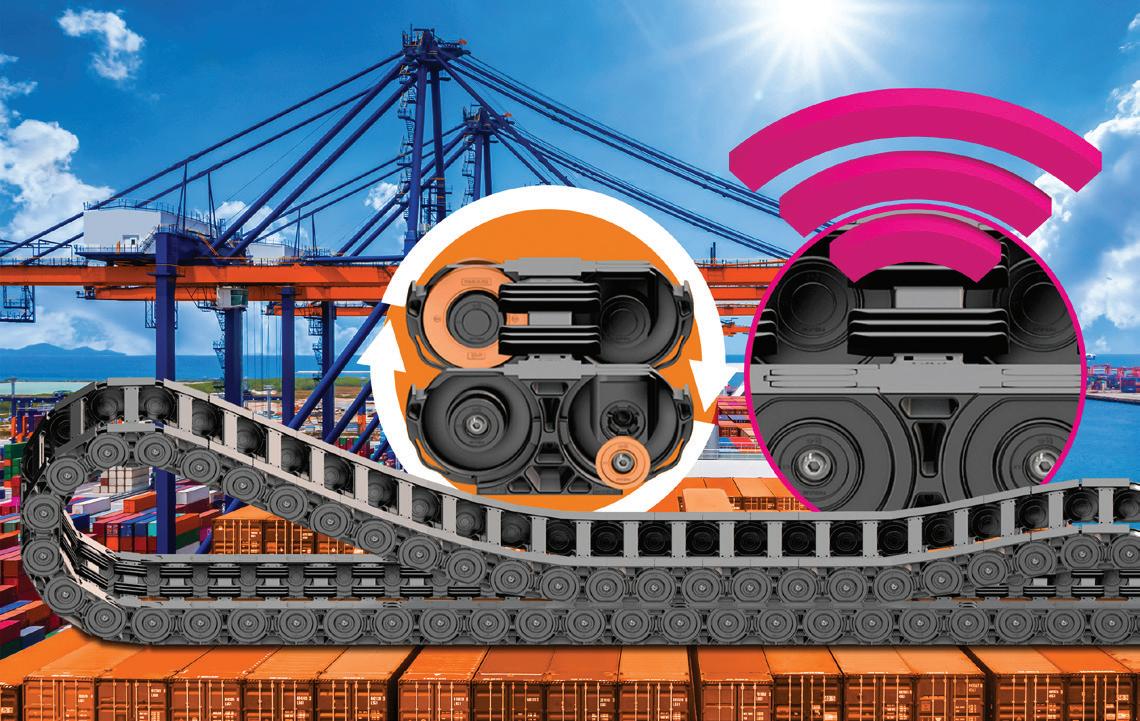
2 minute read
Product World
Chain cable carrier
igus igus.com
The P4HD.56.R is a heavy-duty energy chain cable carrier for long travels, high speeds, heavy cable loads, and Industry 4.0. The recent development of ultra-large container vessels (ULCV) is changing the industry and putting new pressure on terminals to provide deeper drafts and taller ship-to-shore (STS) cranes to service these mammoth containers e ciently. This enlargement also a ects the cable carriers that guide the energy and data cables for the crane trolley. They must withstand unprecedented loads: travels of over 130 m, cable weights of up to 10 kg/m (over 20 kg/m for motor-driven trolleys), and accelerations of more than 1 m/sec2 are standard for Triple E-class STS cranes. In other applications, travel distances of several hundred meters, cable loads of up to 50 kg/m, and accelerations of 8 m/sec2 and more are possible. The heavy-duty e-chain can run trouble-free for up to 15 years. The engineers have developed special design features to achieve a long service life in STS cranes under high loads. A special fork-tab principle ensures greater stability at higher additional loads, while a pin/bore connection made of tribologically optimized plastic minimizes wear. Furthermore, rollers are mounted in the inner radius of the chain links. As
Brakes for robotic arm applications
Miki Pulley mikipulley-us.com
BXR Brakes apply holding torque after the motor joint stops and provides dynamic braking in the event of an emergency such as a power interruption. The brake opens and allows for free rotation during robot arm movements and snaps closed when power is disengaged — halting position of the arm. When the robot arm is in position for long periods of time, the brake consumes no voltage. The brake’s internal compression springs mechanically hold the armature plate against the rotor disc, ensuring no movement. When voltage is re-applied, the brake opens and allows for free movement. These Miki Pulley brakes are a cost-e ective safety device for all robot holding arms and joints including cobot systems. They are a positive “halt and hold” device to mitigate potential mechanical damage to an automated system. An important operating feature: when compared to most other electric brakes, the unique Miki Pulley brake design is one-half the overall size thickness.
Specifi cations are: • Maximum RPM: 6000 • Static friction torque range: 0.044 to 2.36 ft-lb. (0.06 to 3.20 Nm) • Ambient operating temperature 14° – 104° F (-10° to 40° C) the e-chain travels, the upper run rolls on the lower run instead of sliding. Thanks to the low coe cient of friction, payload, and acceleration can be increased without changing the push/ pull force. Long-term tests in igus’s in-house laboratory prove that P4HD.56.R, the heavy-duty design, achieves a 50% longer service life than the standard P41.56R variant.
