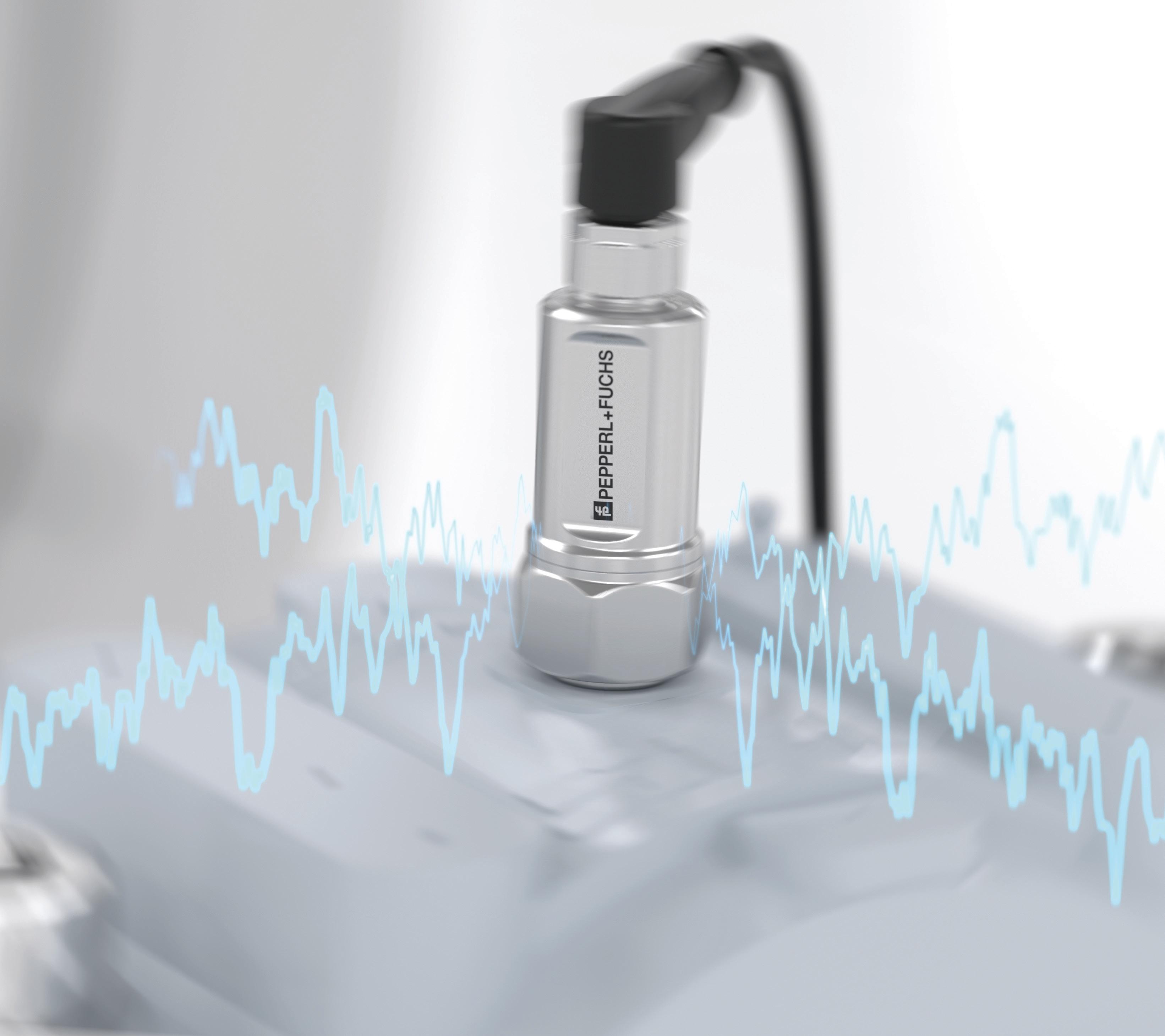
2 minute read
How real-time can increase uptime data
Today in automation, predictive and preventive maintenance are constantly in the conversation. While the ideas may be clear, the implementation and advantages are not. Is this a fad that will fizzle out soon?
By Gerry Paci, Marketing Manager — Material Handling, Pepperl+Fuchs
FFor many years in the material handling industry, warehouse operators have strived to achieve minimal downtime and optimal operation. There are countless ideas and aspects for attaining this milestone within the warehouse.
In this era of intralogistics, the requisite for automation has become apparent. While some automate more than others, the necessity has proven clear. Managing automated equipment and potential downtime is crucial to production and intralogistics.
When a machine is down, the alarm will sound, reminding those on the floor that time and money are paramount. It is one thing to fix the issue quickly so that the process can continue, but understanding when this type of issue or downtime could occur again is the real prize. Moving from reactive to proactive maintenance in the warehouse can be the di erence between a streamlined process and a chaotic event within intralogistics.
The industry has learned over the years that regularly scheduling maintenance helps minimize problems with automation. A planned approach involving inspecting and repairing equipment to prevent failures has proved successful. Based on history, the warehouse maintenance team may understand that a motor controlling the conveyor needs to be inspected once per quarter for potential loosening due to vibration. This tactic helps extend the equipment’s lifespan and identify and address problems before they cause downtime. Nonetheless, if the maintenance team had access to the motor’s vibration velocity and temperature over time, they could predict when a failure could occur, streamlining their maintenance process.
This information and data have become widely available from the software and sensor technology intertwined with the automation process. From a simple photoelectric sensor that detects whether an AS/RS shuttle has entered the proper level of the rack to a 2D LiDAR system looking down over a conveyor to understand the flow of parcels over time, real-time data is constantly surging into a PLC, IPC, or data collection tool within the warehouse. How this real-time data is used is one of the most interesting portions of the process.
As with any newer process or idea in a long-standing industry, challenges and speculation will arise. The transition from preventive to predictive maintenance is not free of these challenges. Where the data comes from, how to process it, and how much upfront implementation time it takes are all common questions during development.
In many cases, some of these questions can be answered using the data from the sensors already living in the warehouse. For example, it is becoming more difficult to walk into a warehouse without seeing the major use of automation, which requires sensors. To implement preventive maintenance, the data from an IO-Link capable sensor can be used as an analytical tool to understand when the machine could fail.
Vibration sensor data extends automation equipment’s lifespan and helps maintenance teams identify and address problems before they cause downtime.