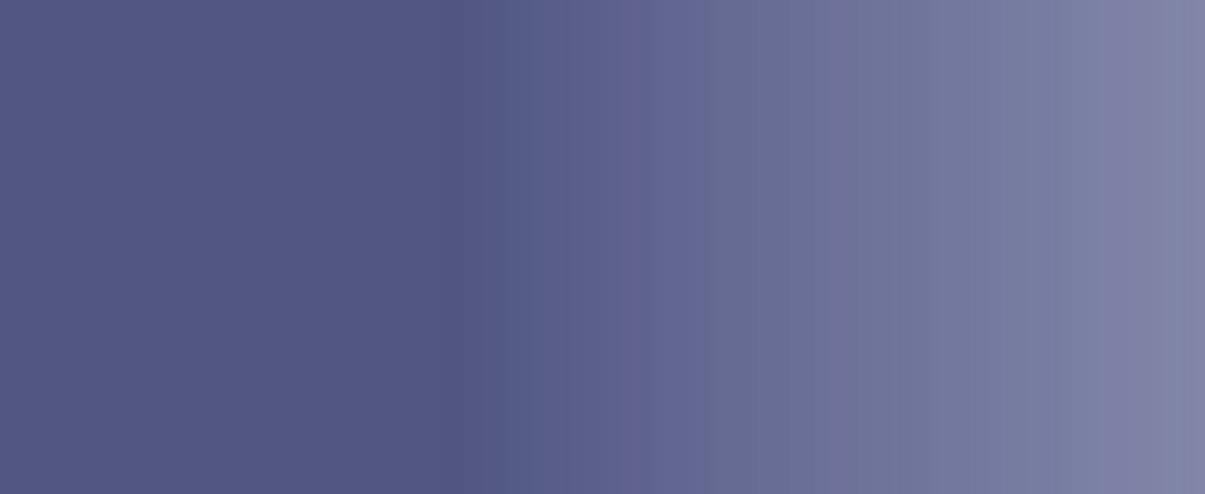
8 minute read
Sager Electronics - Lisa Auffrey
2021 Women in Engineering

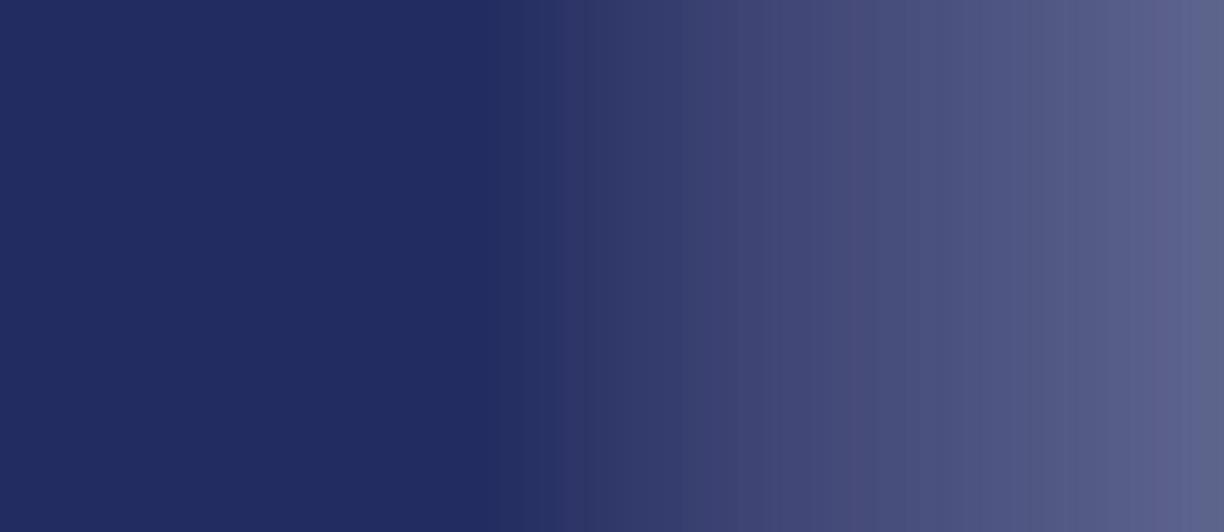


Lisa Auffrey
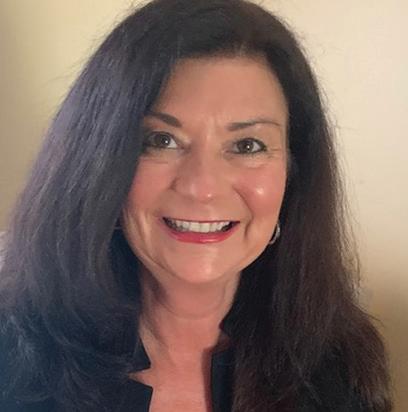
Power Systems Sales Engineer Sagar Electronics
Bachelor of Science Degree in Electrical Engineering/Management Engineering, Worcester Polytechnic Institute
Masters of Arts Degree, Business Management, Harvard University
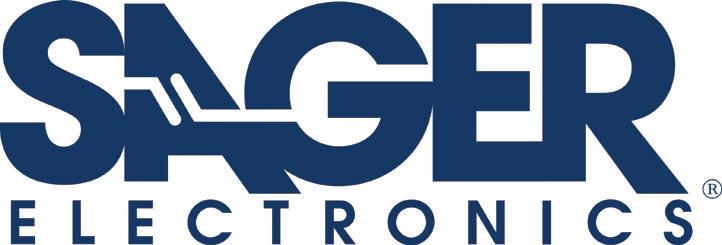
Lisa is an engineering professional with over 30 years of industry experience. After graduating from Worcester Polytechnic Institute, she started her career as a Quality Assurance Engineer with BAE Systems in Nashua, NH before moving to an applications role. She spent 20 years at Norris & Associates and later joined Warner Power, establishing a Manufacturers Rep network for the company. Lisa moved back into the electronics industry with a sales engineer position at Omron Electronic Components. In April of 2017, Lisa joined Sager Electronics as a Power Systems Engineer in the company’s specialized group, Sager Power Systems, where she focuses on solving power, thermal and battery issues at OEMs.
Talk about the culture at your company. What makes it inclusive or supportive of women in engineering and automation?
When I entered the industry there were few women in roles like mine. Thanks to efforts encouraging young women to enter STEM over the last decade or so, there are now many more of us. Sager and the TTI Family of Specialists (FOS) promote women advancement evident by the numbers of women in key management, director-level and senior executive roles. In my role as a Power Systems Sales Engineer (PSE), I work closely with customers in the design and selection of either a standard or custom solution, while also exercising my organizational, project management and negotiation skills. As a female in my chosen profession, I also have the opportunity to infl uence not only my colleagues at Sager, but those outside of the organization. I’d like to think I am doing my small part to advance women in engineering roles.
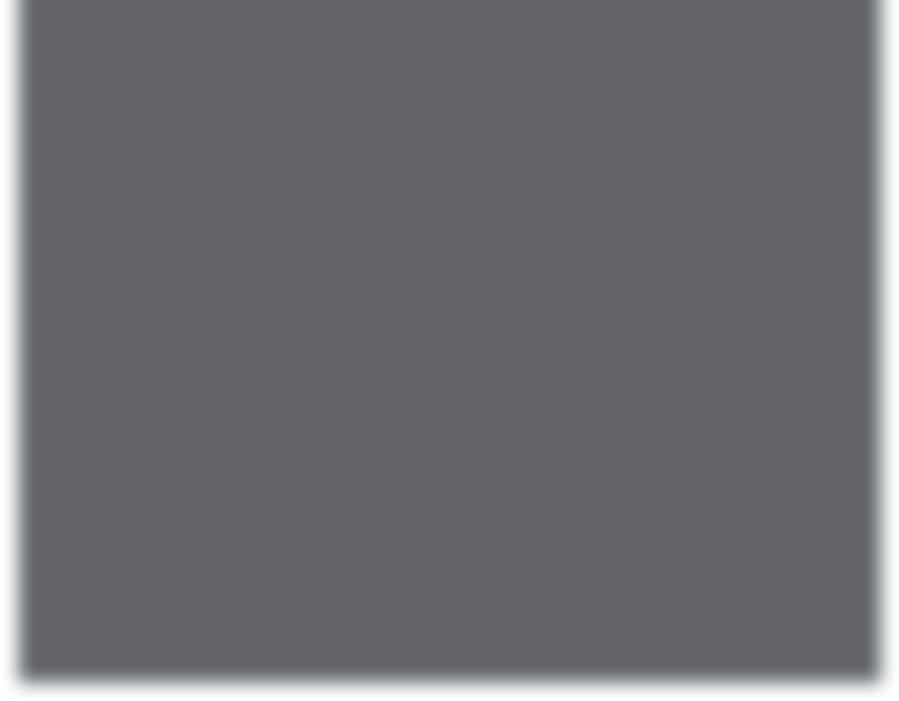
Describe a recent company project (in which you were involved) that went particularly well.
The Sager marketing, sales and Power Systems teams work in tandem to ensure we are supporting our customers. The recent extension of lead times for electronic components has added complexity to providing newly designed products to our customers. We were working with a customer on a design opportunity that involved a product newly introduced to the market. This was a customized solution requiring design creativity and resourcefulness in order to meet the customer’s prototype schedule. The team worked together, concentrating in their areas of expertise to secure raw materials for the build, and successfully deliver the prototype on schedule and to specifi cation. It is quite satisfying to come together as a team, meet a customer’s requirement and develop a solution that helps bring a new application to the marketplace.
What fi rst drew you to engineering and this industry?
My father was a structural engineer, exposing me to engineering from a young age. My strengths were in math and science, therefore, an engineering degree seemed logical. Originally, I started out as a Civil Engineering major, but realized I could not see in the third dimension; so designing bridges was probably not a good idea and I refocused my education on electrical and management engineering.
2021 Women in Engineering

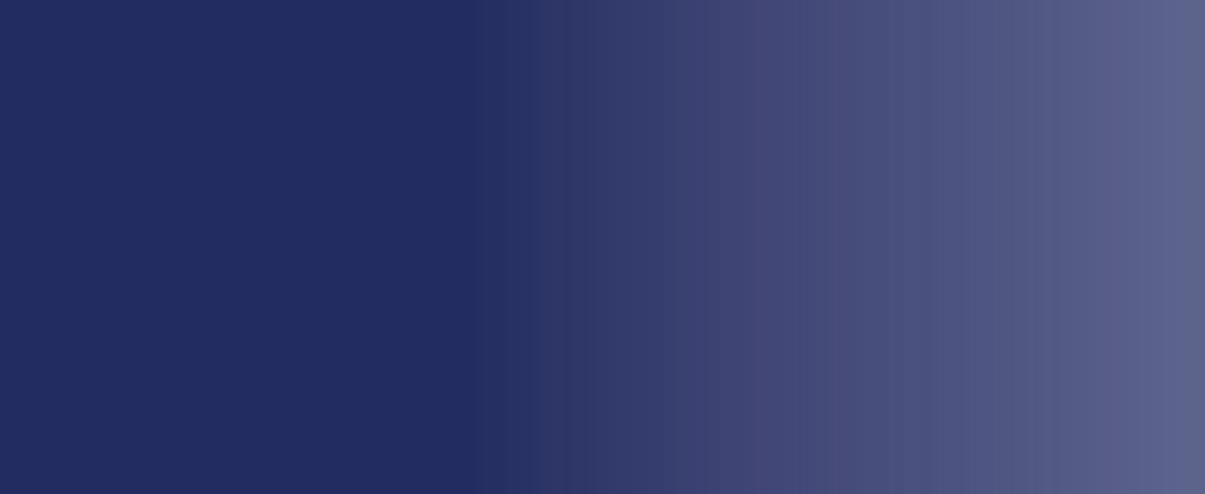
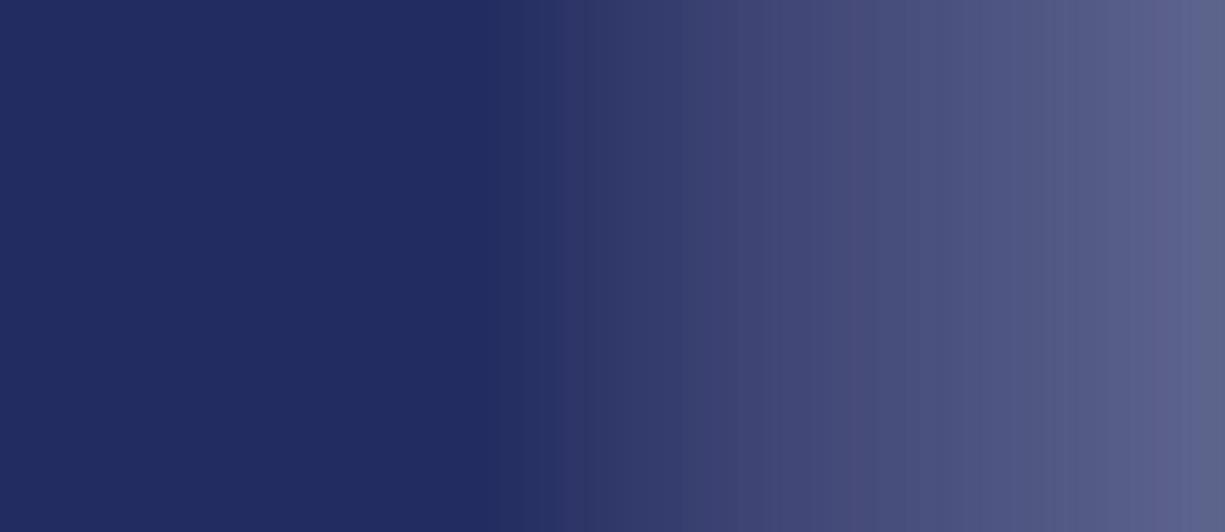
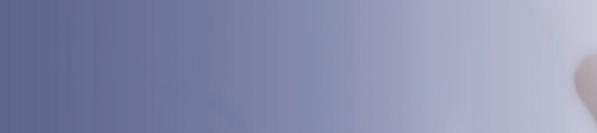

Laura Allison
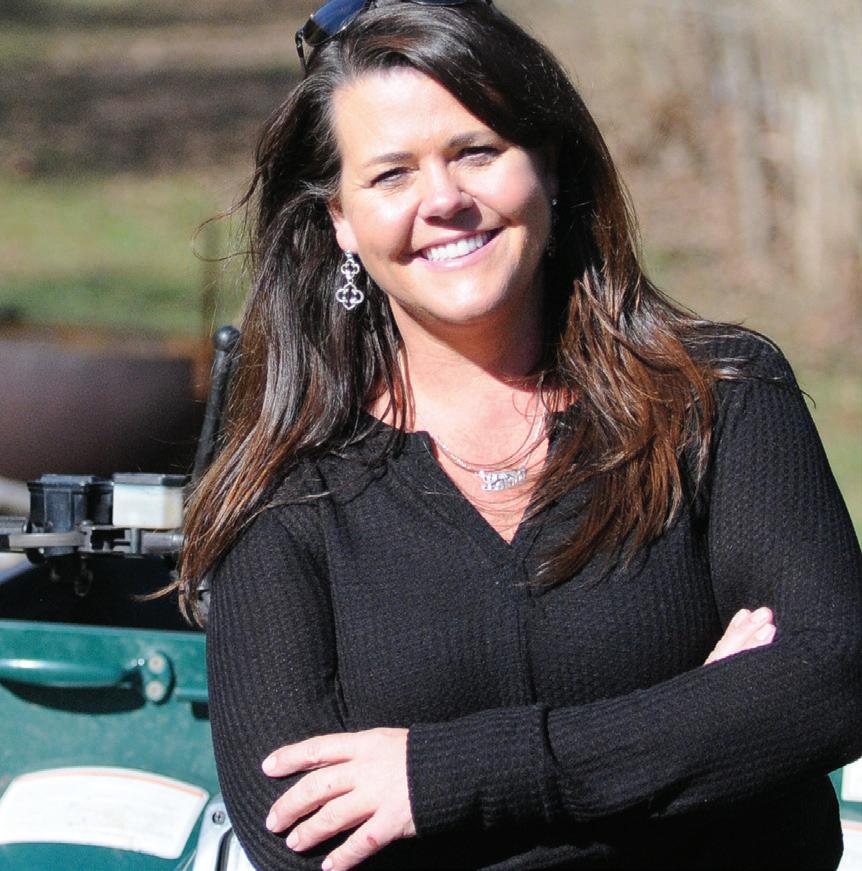
Mathematics, Jacksonville State University

Laura Allison is the Director of Technical Operations for Siemens Mainstream Engineering, a business unit of Siemens Digital Industries Software. She has worked for Siemens for over 30 years. She is the release manager for Solid Edge and the Xcelerator Share web client.
What fi rst drew you to engineering? / When did you fi rst know you wanted to be an engineer?
Math was always easy to me; the solution to a math problem was something I could prove to be true – not just accept. When I started college, I planned to be a high school or college math teacher. But I quickly realized I wanted the additional challenges and fi nancially security that the fi eld of engineering could bring. I have always enjoyed identifying the root cause of problems, developing a plan or technical solution, and then executing the plan to resolve the problem. Software engineering offers daily opportunities to grow that skill. I am also personally rewarded by helping people. In software engineering, the solutions we provide enable us to help our customers be more productive and develop better solutions for their customers too.

Describe your biggest engineering challenge. How did you conquer it or resolve it, or what was the outcome?
Solid Edge is a complete suite of product development software, which is part of the Xcelerator portfolio, the comprehensive and integrated portfolio of software and services from Siemens Digital Industries Software. We started developing Solid Edge more than 25 years ago using the traditional waterfall software development lifecycle. About 5 years ago we recognized the benefi ts of switching to Scaled Agile. This required us to replace existing processes and tools and introduce Agile Sprints, Program Increments, and Scrum teams. This transition was one of the biggest challenges I faced in my career. The change empowered teams to self-organize and make decisions at the team level, but cross-team communication was the key to implementing high-quality solutions across our broad product offerings. The biggest benefi t I have seen from this change has been the ability to deliver many more quality features for our customers each release. By allowing teams to self-manage, we found huge gains in innovation. With the help of my teammates and good processes, we just released our fourth major Solid Edge release using all Agile processes.
2021 Women in Engineering
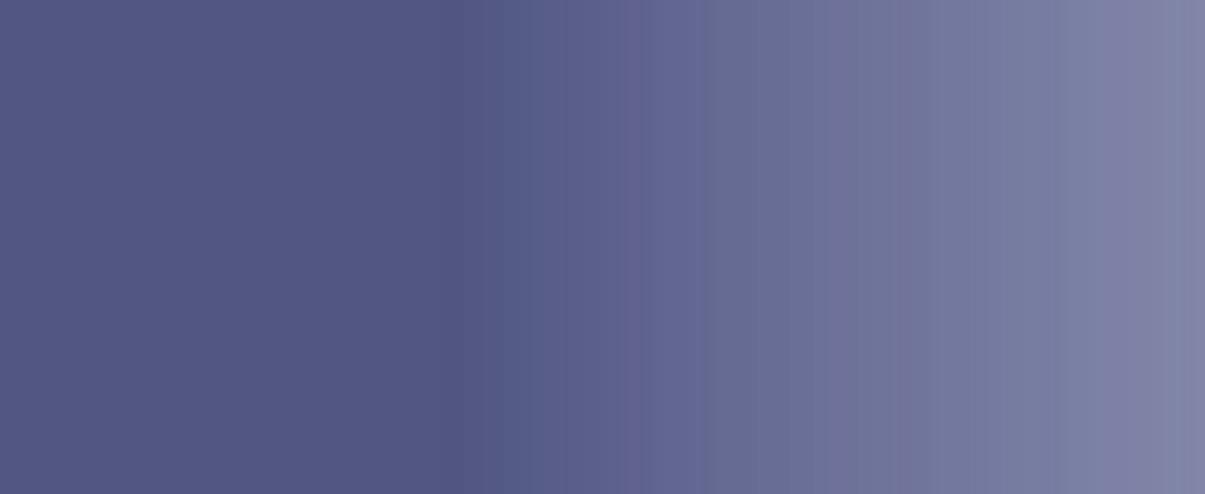

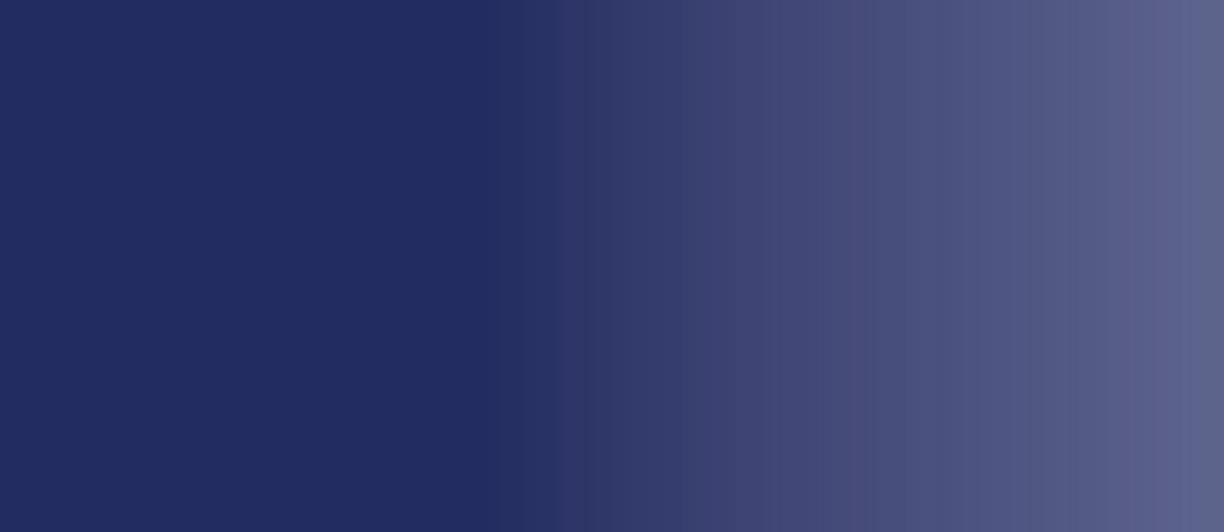
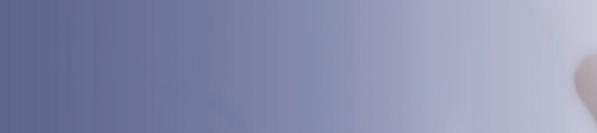
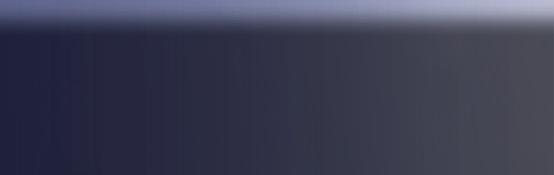
Amanda Beaton

Bachelor of Industrial and Systems Engineering, Georgia Tech
MBA, Georgia State University
Talk about the culture at your company. What makes it inclusive or supportive of women in engineering and automation?
Over the past 18 years, I have noticed a tangible change in the Siemens culture. While we are still a global powerhouse in engineering, there are so many more women in leadership roles. Early on, the culture was obviously very masculine and technically focused. Today, we have so many opportunities to participate in groups focused on diversity and inclusion, and it isn’t just for show. These groups, our projects, and our roles make a real impact on the company and how we work. I can feel the shift in promoting better work-life balance and a much more diverse work force across all the roles and levels and it makes me very proud to work here.
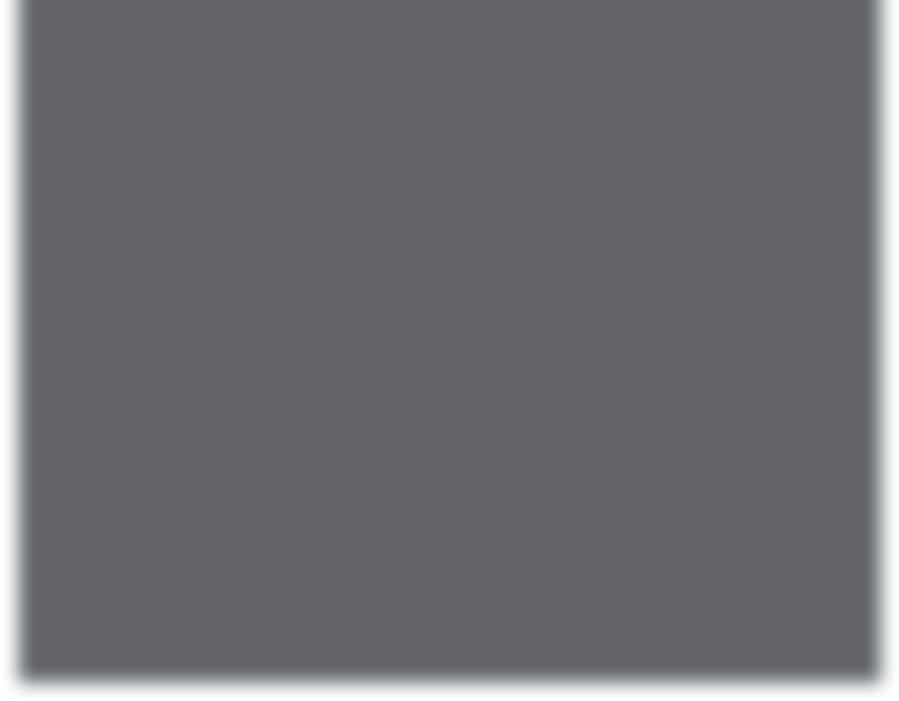

Amanda Beaton has been with Siemens since 2003. As the U.S. Program Manager for Siemens Cooperates with Education (SCE), she is responsible for connecting academia to industry by facilitating the use of Siemens Factory Automation products in schools. Amanda started her career with Siemens in the Operations Leadership Development program and worked in manufacturing in Mexico and the U.S. Amanda holds a Bachelor of Industrial and Systems Engineering from Georgia Tech and an MBA from Georgia State University. Amanda sits on several industry advisory boards at colleges and universities across the US. She is also a frequent STEM volunteer at her daughters’ elementary and middle schools.
Describe a recent company project (in which you were involved) that went particularly well. How did you and your team go about ensuring success?
I helped a team of students from a large university complete a year-long project during covid to build a digital twin of a mechatronics line. The students not only became profi cient in our software, but also did the wiring and physical construction to create the digital and physical models of a manufacturing line. Several delays and the inability to travel made things more diffi cult, but the end result was a successful working digital twin and a wonderful presentation from the students on their accomplishments.
What fi rst drew you to engineering and this industry?
I knew when I was young that I really enjoyed math, science, and technical subjects. I like making things and understanding how things work. I only applied to one college and knew that engineering was for me from an early age. Once I got the opportunity to intern in a manufacturing plant, I was drawn to the life and energy in the facility and sought out manufacturing. I didn’t know exactly what part of manufacturing or engineering I wanted to settle into, so a rotational program focused on operations was perfect for spending time across several manufacturing plants and functional areas to get a feel for the entire supply chain. With Siemens, I was able to transition into product marketing and management roles across different business units and product areas and experience several parts of the business and functional areas. As the child of two teachers, this has been my favorite role yet because I get to hear from so many educators and students and see the positive impact of placing technology into the classroom.