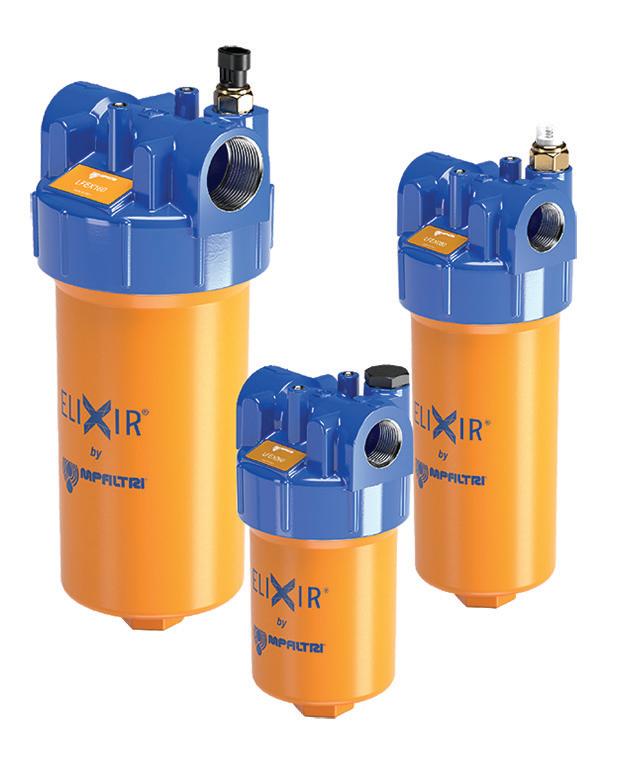
2 minute read
Designing with lters on mobile machinery
A reliable and efficient hydraulic system starts with the fluid. Keeping hydraulic oil conditioned and free of contaminants, air, water and heat is critical to ensuring that all system components run as they are meant to. To ensure this dependability, proper fluid filtration is required and should be taken with great care.
Contamination often enters a machine during startup, when particles from machine operations — be they metal shavings or sawdust or plastic bits — enter hoses, actuators, reservoirs and manifold ports. These particles can also flood a system during maintenance, if proper preventions aren’t taken, or during a complete machine failure.
To prevent them from entering a system, use one of three main types of filters. The first, the suction filter, is mounted in the reservoir and attached to the suction line to protect downstream components, such as the pump. They are meant to catch coarse, large particles, so are not effective in trapping the major culprits of wear — fine particles. These mesh steel filters are often not included in a system’s filtration design, as they can cause clogging and pump cavitation.
Next up is the pressure filter, which is installed in the pressure line, downstream of pumps and system circuits when fine filtration is required. This traps particles in fluid as it flows from the pump, so protects components downstream of the pump. You must select a pressure filter that matches the system pressure you’ll be operating in, but they are generally available in wide ranges up to and higher than 10,000 psi.
The most common type of filter is the return line filter, which traps very fine particles before the fluid reenters the reservoir. Spin-on filter and in-tank drop-in assemblies are the most popular. Spin-on filters are used heavily on mobile equipment. They are rated for most fluid types and a range of pressures and temperatures. They are available in glass, cellulose fibers and paper media. Water-absorbing medias also remove freestanding water from oil.
Growing in use in the mobile market are in-tank return filters. They use stronger filter media, such as synthetic and natural fibers and stainless steel wire mesh. Constructed of steel, aluminum or plastic, they are suitable for heavy-duty applications. And because they are located in the filter stream, they can remove most fine particles throughout the rest of the system, ensuring clean fluid enters the reservoir.
When selecting a filter you need to know what size particles it is rated to remove in one pass through. You must also know its efficiency or Beta ratio (the ratio of particles upstream of the filter to downstream of the filter during standardized testing). For example, we know how efficient a filter was at removing 10-micron particles in a single pass, such as 99%. In this case, “10 micron at Beta 200,” means the filter is 99.5% efficient at removing 10-micron particles in one pass. The lower the micron rating and higher the efficiency rating the better.
Other considerations include pressure drop, flow rate and size, and obviously, price. If sized improperly, filters can break, releasing all the collected contaminants back into the system.

Image courtesy of MP Filtri