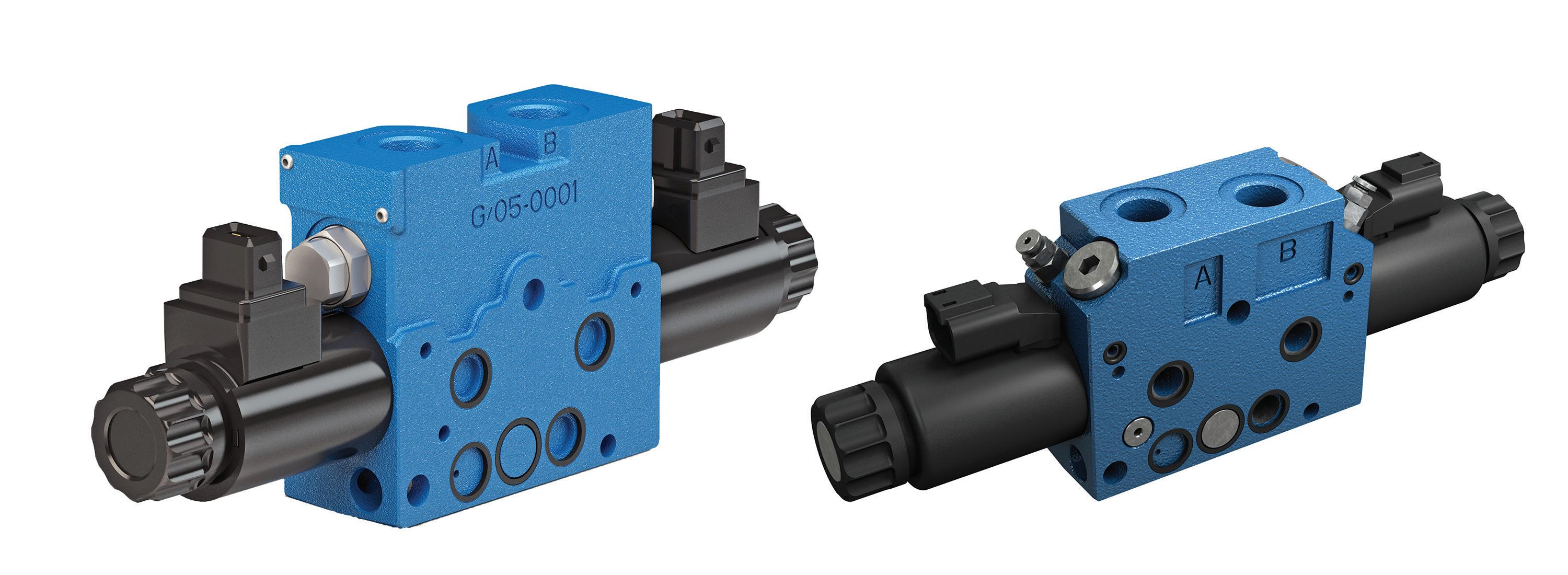
6 minute read
Hydraulic valves
Hydraulic valves, used in conjunction with actuators, are what helpmake hydraulics unique in its control of force, torque and motion. Valves govern direction, pressure and flow of hydraulic fluid, enabling smooth, safe control of actuators.
Valve use can be as simple as a relief valve to protect your pump and actuator. Conversely, the complexity of a hydraulic circuit can be extensive, using a dozen valves per function as can be seen in manifolds.

Image courtesy of Bosch Rexroth
DIRECTIONAL CONTROL VALVES
The directional control valve is available in myriad configurations and is named as such if its primary function is to somehow control the path of fluid flow. Directional control valves manage fluid by blocking, diverting, directing, or dumping. Their complexity varies immensely (just like their cost), as does the method of integration. Valve construction runs the gamut from cartridge valves to monoblock valves, or subplate mounted valves to inline valves. Their usage depends on the industry in which they are typically applied.
The most basic directional valve is the check valve; it allows flow into one work port and blocks flow from coming back through the opposite work port. Alternatively, directional valves can be complex, such as with the pilot-operated valve. A standard spool valve has one directly operated component that controls fluid through the valve. However, as flow increases, the force upon the spool also increases, and these forces can prevent a spool from actuating, as is most often with electric coils. By using a small pilot valve to control the movement of the larger, mainstage spool, the size (and flow) of the valve is nearly limitless.
Directional valves are often described by the number of “ways” fluid can travel through them, and also by the positions available to be shifted into. The ways are equal to the number of work ports, so a 4-way valve will have Pressure, Tank and A and B work ports. Positions are equal to the number of positional envelopes. For example, one would describe a double-acting single monoblock valve as “4-way, 3-position,” or simply a “4/3 valve.”
Directional valves are available in monoblock or sectional valves, common to the mobile-hydraulic industry, as well as subplate mounted industrial type valves such as ISO style D03, D05 and so on. Also common to both mobile and industrial markets are cartridge valves installed into manifold blocks. Cartridge valve manufacturers offer many unique products and allow high levels of creativity with limitless available valve combinations.
PRESSURE CONTROLS
A pressure valve is any component designed to limit pressure. Most pressure valves are based on a poppet being pushed against a seat with an adjustable spring, although pressure valves can be a simple ball and spring configuration or use spools for high flow circuits. Their operation is simple: a spring pushes the poppet against a seat, and when pressure from the system is strong enough to counteract the force of the spring, the valve will open, bleeding off fluid to limit pressure.
A relief valve controls maximum pressure for either the entire system or a sub-circuit of it, the lowest spring pressure of a system being the one to open up first. Most other pressure valves are based on the relief valve’s simple spring-loaded ball or poppet. Sequence, counterbalance and brake valves are all forms of relief valves with added utility or functionality, such as reverse flow checks or pilot operation built in. The pressure-reducing valve differs from the other pressure valves because it limits pressure downstream of itself rather than upstream. It is used in applications where sub-circuit pressures need to be lower, without sacrificing any performance in the rest of the system.

Image courtesy of Doering
FLOW CONTROL VALVES
Flow control valves control or limit flow in one way or another. They are often just a needle valve, which is just a variable restriction, adjusted by a screw or knob much like pressure valves, to limit the energy potential to create flow. When installed with reverse flow check valves, we change the name to flow control. Flow control valves can sometimes have multiple ports, such as with a priority flow control. They provide controlled, fixed flow to one part of the circuit (sometimes at the sacrifice of another part) and only if input flow is high enough for its priority demand.
Flow controls are (ideally) pressure compensated, which allows the valve to maintain its set flow regardless of load-induced pressure variances. Pressure compensators are a type of flow control valve available as a single component, often added to other valves in a circuit to provide flow rate accuracy independent of load, such as with an electronic proportional valve.
Proportional valves are considered both flow and directional valves, and not only meter flow, but also control the direction flow is metered in. Proportional valves use pulse-width modulation to maintain voltage while controlling current. Varying the current modifies the force of the magnetic field and subsequently how far the spool or poppet moves within its body, changing the size of the opening available for fluid to take, which of course limits flow. A simple variable resistor can be used to limit current, but it is inefficient and cannot provide the benefits a PWM controller can.
An electronic valve controller can provide adjustable minimum and maximum settings. A minimum current value is needed to move the spool past its “dead zone” overlap where it “starts” to flow. Also, a maximum current value prevents too much electric juice from fatiguing the valve and coil when only a couple amps are required to achieve full flow anyway. Additionally, a proper controller and driver provide a dither signal to the valve, which vibrates the spool so that static friction doesn’t stick the spool within the body. The spool movement is unnoticeable but is enough so that when a change in current is required, the spool responds rapidly without overshooting the desired new position.
WHAT IS A RELIEF VALVE?
A relief valve is a device used to limit pressure in one or more locations in a hydraulic circuit. A relief valve uses a spool or poppet engaged to the closed position by a spring. A spool is a cylindrical piece of machined steel that slides within a machined body. A poppet is a flat piece of machined steel attached to a stem, and the face of the poppet rests against a seat to provide superior sealing. A spool often provides better metering characteristics, but has significantly more leakage than a poppet design.
When pressure rises in the portion of the circuit where the relief valve is installed, force acts upon the spool end or poppet face; the force applied by the spring opposes the force on the spool end or poppet face to keep the valve closed. Valve spring compression force is often variable — compression height can be reduced by an adjustable screw — although effective range is limited (for example, a spring might be effective between 1,000 and 5,000 psi or 100 and 1,200 psi, b ut rarely between 100 and 5,000 psi).
As hydraulic pressure continues to rise in the circuit where the valve is installed, force against the spool or poppet starts to overcome the opposing force of the spring, opening a flow path to the tank. As pressurized fluid exits the relief valve, energy is diverted (in the form of heat) until downstream pressure equals the spring value force, which could be drops of flow or all of pump flow, depending on the application and state of the circuit.
In short, a relief valve is a hydraulic component designed to limit pressure in an entire system or subcircuit by diverting pressurized flow to the reservoir. They are most often installed directly downstream of the pump to control system pressure, but can be used in other parts of the circuit to protect isolated components.

Image courtesy of HYDAC