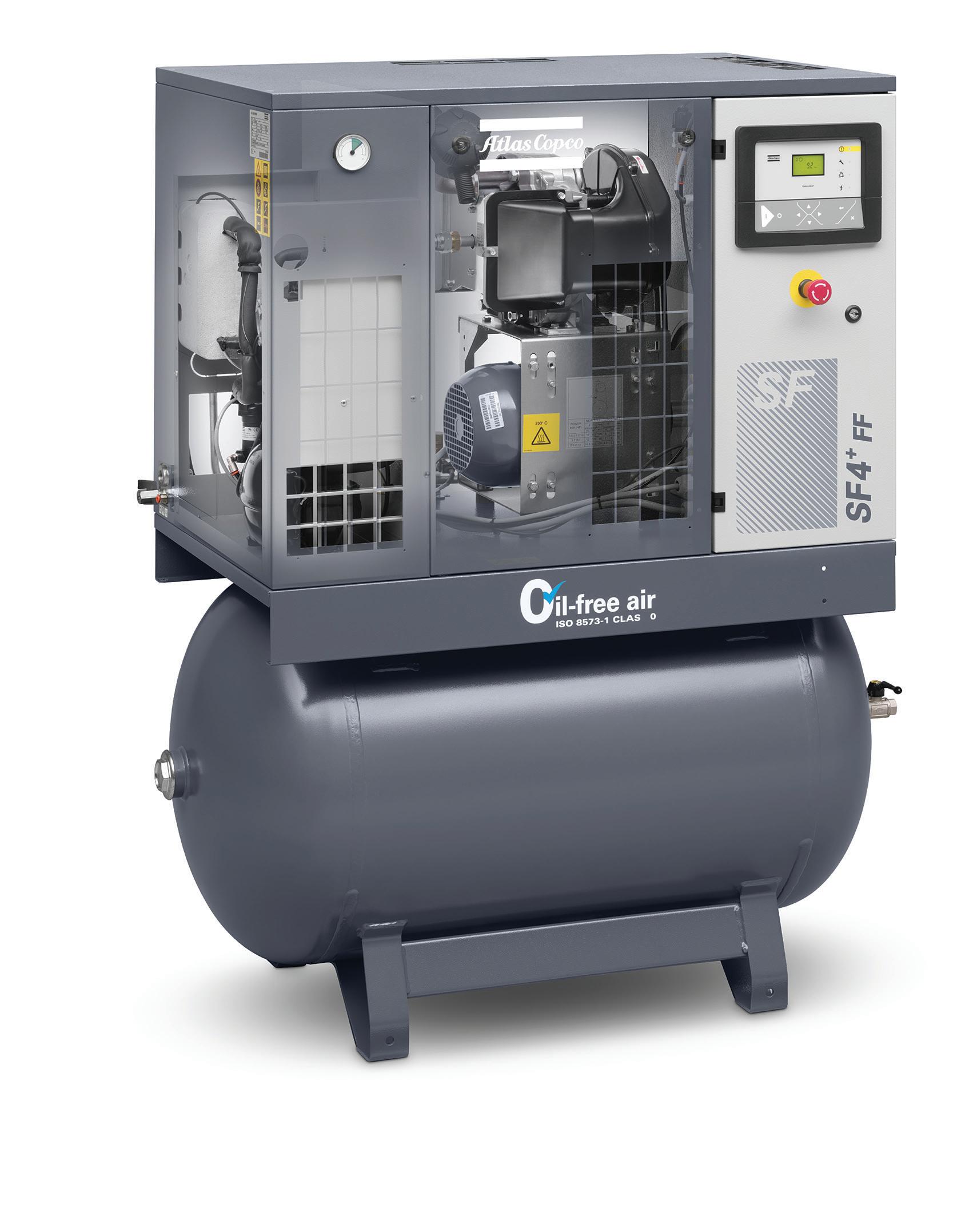
8 minute read
Air compressors
Air compressors supply the compressed air flow for all pneumatic equipment in a system. The compressor addsenergy to the air, which is cleaned and conditioned by filters and dryers,then transmitted in piping for use. Compressed air is an energy intensive source of process power, about 7 to 8 units of energy are consumed at the compressor for each unit of mechanical energy produced by a typical compressed-air powered device — and of this, typically 50% of the compressed air is wasted due to leakage and inappropriate use. Most of the energy released by an air compressor is in the form of heat of compression.
When discussing compressed air flows, there are various definitions that relate to compressor capacity:
ACFM — actual cubic feet per minute (also called free air delivered, FAD, or inlet cubic feet per minute, ICFM). This is the flow of air taken in by the compressor at site conditions (local atmospheric pressure, temperature and humidity). In general, higher altitudes, temperatures and levels of humidity reduce the capacity of the compressor to produce a given mass of compressed air; therefore, if these conditions exist, a larger compressor must be purchased.
CFM — cubic feet per minute. This is the flow of air at a certain point at a certain condition, which must be specified. With regard to sizing air compressors, it is important to understand the wide range of conditions at which the CFM can be stated.
SCFM — standard cubic feet per minute. This is the flow of free air measured and converted to a set of standard conditions. The definition of SCFM for air compressor rating purposes (Compressed Air and Gas Institute based on ISO Standard 1217) is the flow of air at 14.5 psig atmospheric pressure, at 68° F and 0% relative humidity. ACFM and SCFM are both measured at atmospheric pressure, not at the pressure the air compressor produces. There are two types of compressors: positive displacement and dynamic (also called centrifugal or axial).

Image courtesy of Atlas Copco
POSITIVE DISPLACEMENT AIR COMPRESSORS
Positive displacement compressors take in air and mechanically reduce the space occupied by the air to increase pressure. They can further be divided into rotary and reciprocating types. Rotary compressors are available in sizes from 5 to 600 hp. In rotary screw compressors, filtered air enters the inlet of the air end where male and female rotors unmesh. The air is trapped between the rotors and the air end housing. This space is reduced as the rotors remesh on the opposite side of the air end. Thus, the air is compressed and moved to the discharge port. For lubricated compressors, cooling fluid is injected into the housing, which mixes with the air to seal, lubricate and remove the heat generated by compression. This fluid forms a thin film between the rotors that virtually eliminates metal-tometal contact and wear. The fluid is separated from the compressed air, cooled, filtered and returned to the injection point. The compressed air passes through an after-cooler and water separator to reduce its temperature and water content so it is ready for the air treatment equipment.
Cooling takes place inside the compressor package, so the rotary compressor is a continuous duty, air-cooled or water-cooled compressor package. These compact designs provide smooth, pulse-free air output and high output volume. They are also easy to maintain and operate.
Oil-free rotary screw air compressors use specially designed air ends to compress air without oil in the compression chamber, yielding true oil-free air. Oil-free compressors are typically two-stage units and are more costly than lubricated types. Oil-free rotary screw air compressors are available as aircooled and water-cooled, with both load/ unload and variable speed control options. They also offer the same flexibility as oil-flooded rotaries when oil-free air is required.
Reciprocating air compressors use a piston within a cylinder as the compressing and displacing element. Single-stage and two-stage reciprocating styles are commercially available. Single-stage compressors are generally used for pressures in the range of 70 to 100 psig and twostage compressors are generally used for higher pressures in the range of 100 to 250 psig. These types of units are most often used for smaller systems. Typically, these compressors are not rated for continuous duty due to limited cooling methods and should be operated at duty cycles of 60% of full capacity or lower, or equipment damage may result.
The reciprocating air compressor is singleacting when the compressing is accomplished using only one side of the piston. A compressor using both sides of the piston is considered double-acting.
Reciprocating air compressors are available either as air-cooled or water-cooled in lubricated and non-lubricated configurations and provide a wide range of pressure and capacity selections.

Image courtesy of Vert Rotors
DYNAMIC AIR COMPRESSORS
Dynamic compressors use the mechanical action of rotating impellers to transfer pressure to the air. The centrifugal air compressor is a dynamic compressor, which depends on transfer of energy from a rotating impeller to the air. Centrifugal compressors produce compressed air by converting angular momentum imparted by the rotating impeller (dynamic displacement). To do this efficiently, they rotate at higher speeds than the other types of compressors.
Adjusting the flow by straight modulation or with the use of inlet guide vanes is the most common method to control capacity of a centrifugal compressor. By closing the guide vanes, volumetric flows and capacity are reduced with good turn-down efficiency. However, this adjustment is limited to the upper range of flow, with the use of inefficient blow-off required to ensure the compressor does not go into a damaging condition called surge. Centrifugals can also operate using load/unload style control and have minimal unloaded power consumption. This can be a good energy efficiency measure. Efficient control of systems using multiple centrifugals requires coordination of the modulation controls and load/unload to ensure the compressors are kept from blowing off and that the compressors operate at their most efficient discharge pressure.
The centrifugal air compressor is an oil-free compressor by design. The oil-lubricated running gear is separated from the air by shaft seals and atmospheric vents.
Dynamic compressors are most often used on sizeable compressed air systems. These units are most efficient where large continuous flows of compressed air are required. They are primarily used for continuous, stationary service in industries such as oil refineries, chemical and petrochemical plants, and natural gas processing plants.
6 COMPRESSED AIR PROBLEM SIGNS

Figure 1. The differential gauge on this filter indicates a pressure loss problem. Photo by Ron Marshall.
Is your compressed air system in trouble — and if it was, how would you know? Fortunately, there are some common signs that will give you some hints as to the health of your system. Here are six things to watch for.
1. Low Pressure. Having adequate pressure is most important in an air system. If there is a constant low pressure, or periods of time where the pressure falls — only to recover again a short time later, these are bad signs. Have your service professional check on the compressor settings to ensure they are set and coordinated properly. If this does not fix the issue, then long-term monitoring with data loggers may tell you the cause. Often times, pressure differentials in filters or piping can cause pressure issues, or the lack of compressor capacity.
2. Hot temperatures. Is the ambient temperature in your compressor room noticeably hot? Is the discharge air pipe of the compressor too hot to touch? These are signs that there is a cooling issue that needs attention. Blocked filters, clogged coolers or even improper ventilation design can all be causes. High temperatures prematurely age compressor components and lubricants — and they overwhelm air drying systems. If you have temperature problems, you should get them fixed right away.
3.High or low compressor amps. Have a qualified person check the amps of your compressors. If the input amps when fully loaded is significantly higher or lower than the nameplate rating of the main compressor motor, this is a sign of a problem. Too high will burn out the motor and may be a sign of high internal pressures. Too low shows the compressor may not be putting out full capacity, a sign of inefficiency or internal problems.
4. Long unloaded run times. Does one (or several) of your compressors spend many hours running unloaded? Check the compressor hour meters to find out. Long unloaded run times are a sign of poor compressor sizing (too big) or improper coordination. Sometimes this problem can be solved by simply placing the compressor in “auto mode” (a push of a button) which may save thousands of dollars per year.
5. Water or oil in your pipes. Do you have free water or oil in your compressed air pipes? This contamination will work its way into your expensive compressed air equipment and tools — or worse, it will ruin your finished products. Failed filters or drains, temperature problems, overloaded dryers or internal compressor problems can all cause these problems. Have a qualified service person look at the issue and repair it.
6. Many audible leaks. Take a walk through your plant during a period of low production. Can you hear audible leakage? Typically, between 15 to 30% of the compressed air made by your compressors will be wasted due to leakage. If you have no leak management program, this number could be above 50%. And in worst case scenarios, more than 80% of the compressed air will be wasted. Save yourself some energy costs by declaring a ban on air leaks — and taking action to fix all the ones you can hear!