
1 minute read
Applications for wave springs
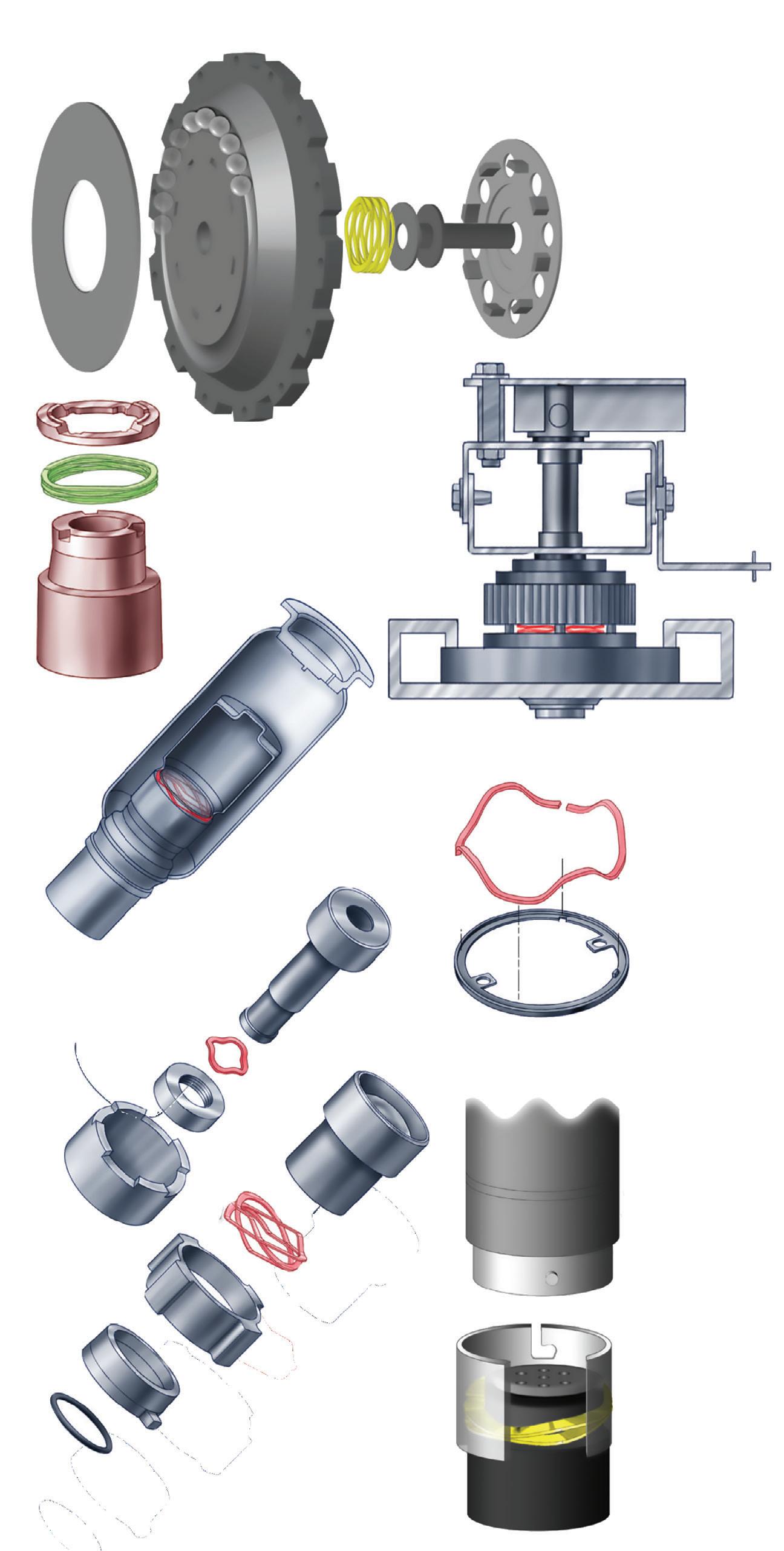
Shown here are wave-spring application examples. From top to bottom, these include clutches, automotive vehicle mirrors, rolling doors, airbag inflators, water sprinklers, general airbag assemblies, night-vision lenses, and bayonet connectors. Image courtesy Rotor Clip Company Inc.
Wave springs are essential to an ever-growing lineup of consumer products … especially in electronics, safety, and automotive designs. They’re also in nearly all motion-control applications — including gearboxes, actuators, rotary unions, and clutches.
Wave springs operate as load bearing devices. They suit applications with special space needs to take up play or compensate for dimensional variations within assemblies. They also work in designs that need loads to move either gradually or abruptly to reach a predetermined working height.
A wave spring always applies load in an axial direction. Wave springs also apply consistent loads within a small tolerance range at different work heights. These capabilities let design engineers adjust the application to meet given requirements when needed.
One wave spring is the single-turn. Versions with overlapping ends save axial space so there’s more space for travel. Here, the spring clings to the bore. In contrast, nested wave springs suit applications requiring higher forces to meet safety regulations, such as those in government or military applications. A nested-wave spring provides a higher load than a single-turn wave spring (a stamped wave washer) and uses the same radial space as a single-turn design.
Use of multiple-turn wave springs can save 50% in axial space compared to a traditional coil spring. What’s more, these springs eliminate the risk of torsional movements during compression to work height.