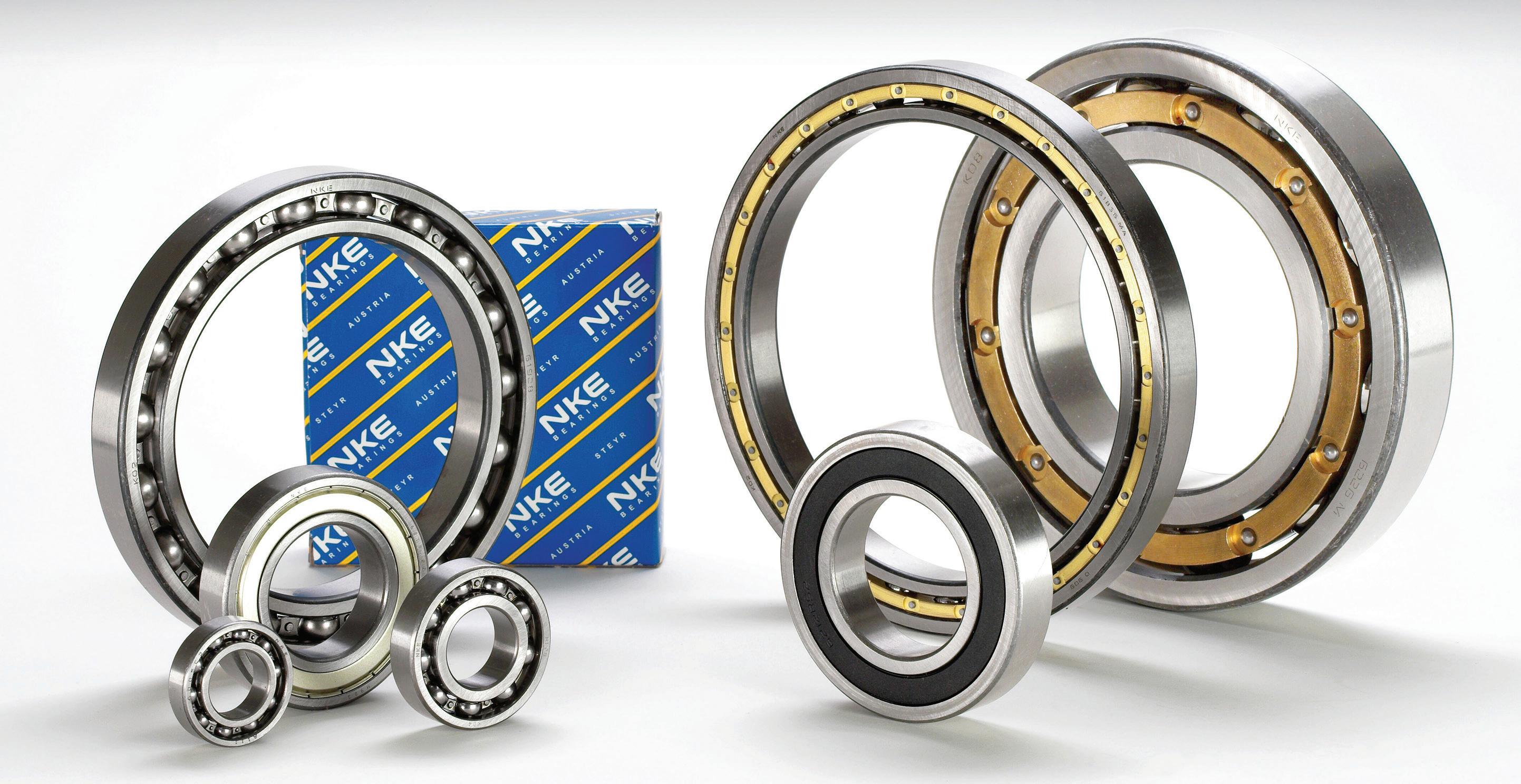
6 minute read
IoT, new materials, and lubrication: Bearing trends in 2020
IoT and predictive maintenance remain critical areas of focus and innovation for the bearing industry in 2020 — as do advances in lubrication and material science. To get a better understanding of these technologies and what developments to expect, we asked some of top bearing industry experts for their take on what’s new and what's coming from their companies in 2020.
IOT AND PREDICTIVE MAINTENANCE
The widespread adoption of condition monitoring technologies such as vibration analysis is a testament to the early adopters who pioneered their use within the industry. These technologies transformed the way we think about maintenance by providing users the ability to determine the health of an asset without interfering with its operation.
The industrial internet of things (IIoT), coupled with declining sensor costs, has further accelerated the use of these technologies and enabled remote monitoring of realtime data, automated analysis, and instantaneous alerts.
“One challenge that we see frequently is customers becoming disenfranchised with the technology because it wasn’t applied correctly to the asset and, as a result, does not provide advanced warning of faults or degradation. One-size solutions do not fit every application for the end customer. Our Perceptive Technologies teams provide a more holistic approach, including on-site and remote services for condition monitoring, diagnostics, and other hands-on services to improve a facility’s bottom line,” says Dan Phillips, director of technology monitoring and diagnostics for Regal Beloit.

Full evaluation of lubricant in progressed and sealed radial deep-groove ball bearings is one of the most underestimated factors in the use of rolling-element bearings. Deep-groove ball bearings such as these from NKE have various seals and grease variants for different operating conditions.
Regal Beloit has also just launched a new mobile app (Regal PT Mobile App) on iOS to allow customers to register bearing products and schedule maintenance, with access to maintenance instructions and guides to help them in the application of the bearings.
At Fersa, the MOSS Bearing system incorporates sensors to measure variables such as temperature, vibration, humidity, loads or speed, and others.
“Automakers are still a bit reluctant to use the bearing as a sensor, but we see opportunities in the industrial market for sensoring and mechatronics ... from the agricultural business to mechanical drives for the wind industry,” says Sergio Santo Domingo, R&D director at Fersa Bearings.
The electric future will affect bearing requirements, as an electric vehicle has up to 90% fewer moving parts compared to combustion-engine cars. The mechanics are simplified, which implies a change in the way of working. Energy efficiency and reduction of fuel consumption are aspects increasingly demanded by users and manufacturers. Fersa expects to see increasingly efficient bearings in the short term, which may even be different from the standard versions of the product in terms of dimensions and assembly.
LUBRICATION ADVANCES
The full evaluation of a lubricant in pregreased and sealed radial deep groove ball bearings represents — besides the topic of bearing clearance — one of the most underestimated issues in the use of rolling element bearings. On the one hand, design engineers must assess the best possible lubrication to minimize friction and metallic contact under realistic operating conditions. On the other hand, any lubricant is subject to aging during operation, depending on the actual operating conditions.

Optically and metal detectable bearing materials such as those shown in this Timken bearing are helping manufacturers meet the highest standards for food safety.
“Most often, the lubricant’s performance is degraded to the extent that it has reached the end of its service life well before the rolling element bearing itself. Again, the actual operating temperature plays a significant role in this context,” says David Schaljo, head of application engineering at NKE Austria.
An evaluation of the lubricant is recommended for most applications in cooperation with the lubricant manufacturer and supported by the bearing manufacturer. But new greaseless alternatives are also an option that’s gaining traction in 2020.
Another option is Polymer Solid Lube (PSL) — a bearing lubrication innovation that is gaining popularity with food makers and equipment manufacturers as the Food Safety Modernization Act (FSMA) continues to transform the nation’s food safety system.
PSL is a microporous polymer structure impregnated with oil that fills the free volume in the bearing between the races, rolling elements, and cage. During bearing rotation, the solid polymer releases the appropriate amount of oil to lubricate the rolling elements and raceways.
As an alternative to traditional lubricants, PSL makes it possible to improve food safety and reduce maintenance demands by never having to re-grease critical bearings. In other cases, where certain types of sealed and greased ball bearings cannot be re-lubricated, PSL can still provide longer life and greater reliability compared to these options.
“Timken has conducted cost-of-ownership studies that demonstrate the increased service life of a solid lube bearing versus a standard greased bearing. Typically, a solid-lube bearing will have 25% to 30% more oil by volume than a similar bearing using grease to let the solid-lube bearing to operate longer based on the added lubricant capacity,” says Steven Boyd, senior application specialist with Timken.
In addition, solid lube acts as a secondary sealing element by keeping contaminants that have passed through the bearing’s primary seal away from the rolling elements.
There are other options for avoiding the problems of traditional lubrication. “The maintenance-free self-lubrication aspects of igus bearings are key to their use in material handling and automation applications,” says Nicole Lang, iglide Product Manager for igus. They're also suitable for electric vehicles, where weight is an key factor. In the food industry, self-lubricating bearings work in kiosks and settings for food preparation.”
Lang's company has also invested heavily in expanding its 3D printing capabilities. “Our SLS printing service allows small batches — and customers can design and order on our website. We configure everything right on down to bearing service life. It’s a very quick process, and customers can have parts shipped to them in days. The products are made with igus materials and developed and engineered by us. That’s a major development in the world of bearings,” adds Lang.
MATERIAL SCIENCE LEADS
Materials are key to ensuring food safety. Detectable materials are helping to ensure food safety by helping food and beverage makers improve foreign particle detection probability in their plants. Anywhere machines operate in close contact with food, there is the risk of contamination from adjacent moving parts.
“Timken uses polymers that are optically detectable as well as bearing inserts with all stainless-steel components for metal detectability ... and our engineered polymer bearings are both optically and metal detectable,” says Boyd. Timken now has bearing housed unit options that include optically detectable blue thermoset housings and metal-detectable bearing cages for meeting USDA and FDA requirements, as well as implementing critical HACCP processes in their facilities.
Single bearings are reaching their limits in terms of material, heat treatment, or geometry performance. So to go beyond those physical limitations, bearing makers are developing coatings and thermochemical processes. Coatings such as DLC or Zirconium Carbonitride increase wear resistance, fatigue durability, and reduce friction during bearing motion. New mechanical processes such as surface texturing help bearings survive aggressive environments and dry lubrication conditions.
Component materials must also satisfy the unique challenges of electric motors ... because electric motors can rotate at higher speeds than combustion engines, and any electrical leakage can lead to bearing failure.
“At Fersa, we're working on a Hybrid Bearings range with ceramic components to satisfy the needs of this vehicle type — including electrical insulation, high rpm, and reduction of vibrations,” says Santo Domingo.


Conventional bearings (top require periodic relubrication while food-safe bearings using PSL like this Timken bearing (bottom) can avoid the risk of grease purge and contamination altogether.