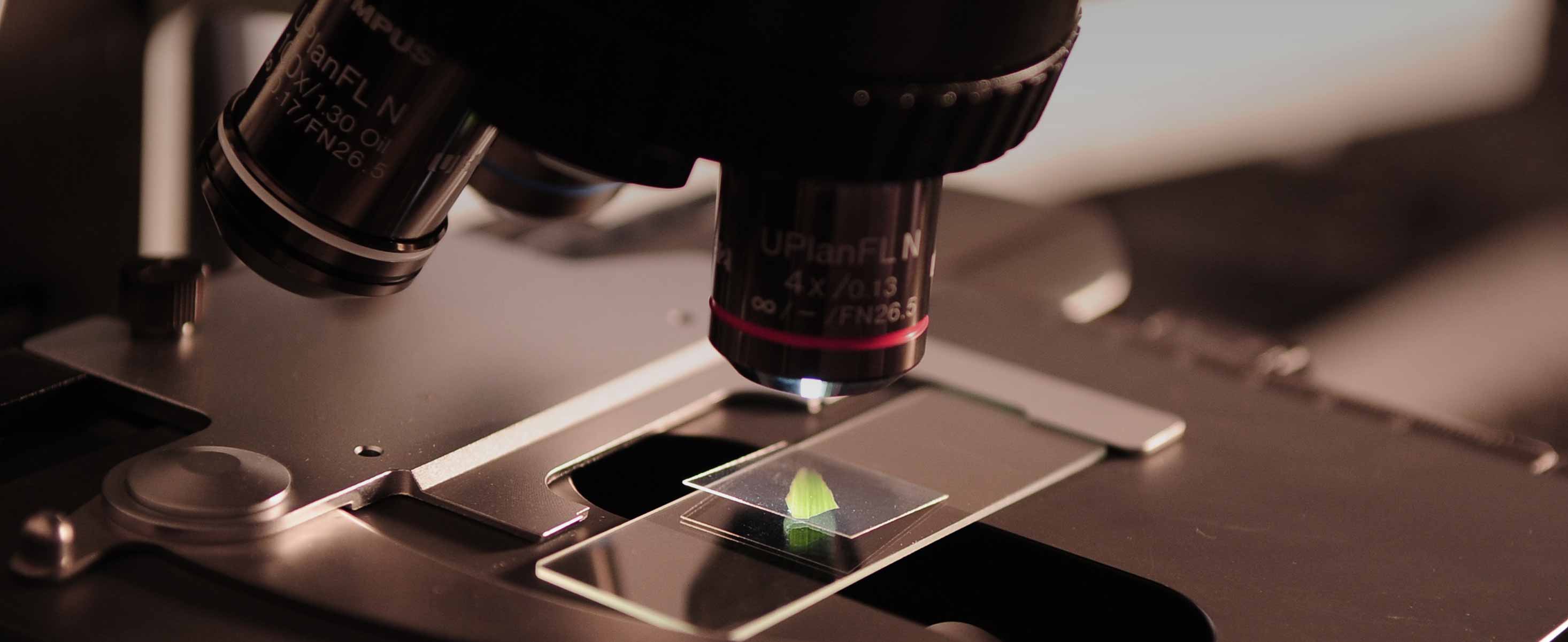
1 minute read
The basics of retaining rings
Retaining rings are fasteners that hold componentstogether on a shaft or in a housing when engaging a groove. Threemain types of retaining rings include tapered section, constantsection and spiral.
Tapered-section rings typically have decreasing thickness from the center of the ring out to the ends. They mount either axially or radially. The taper is there to ensure full contact with the groove when installed.
Constant section retaining rings have a constant width around the circumference of the ring. When installed, these rings do not maintain uniform contact with the entire component. They take on an elliptical shape and make contact with the groove at three points. Spiral retaining rings are installed into the housing or onto the shaft, making full contact with the groove and component. Their grooves are relatively shallow, so their load bearing capability is reduced. Spiral rings are often selected when full contact with the retained component or a lower axial profile is required.
Spiral rings have no protruding ears to interfere with mating components in an assembly. The ring has a uniform cross-section and no gap or lugs for a functional and aesthetically pleasing ring. Unlike traditional fasteners, retaining rings eliminate machining and threading, reducing costs and weight. Spiral retaining rings do not require special tools for removal and are supplied standard with removal notches for easy extraction from a groove.
When selecting a retaining ring for an application, several factors dictate which is most suitable. The first question to ask: What kind of assembly does the application require? Is it a housing assembly or shaft assembly?
Next, determine the main critical dimensions. These include the housing or shaft diameter, groove diameter and the groove width. Also, what is the rotational speed (usually in rpm) of the assembly? Next, determine the maximum thrust applied to the ring. Generally speaking, designers define this thrust as either a light, medium or heavy-duty load. It’s important that the design engineer define the maximum thrust because its value also helps determine if groove deformation or ring shear could be a problem. Basically, groove deformation occurs because the groove material is soft, which in turn limits maximum capacity. Ring shear, on the other hand, occurs when the groove material is hardened but the load exceeds the ring’s maximum capacity. Other factors, such as the temperature as well as the presence of any corrosive media, also dictate the most suitable choice for ring material.