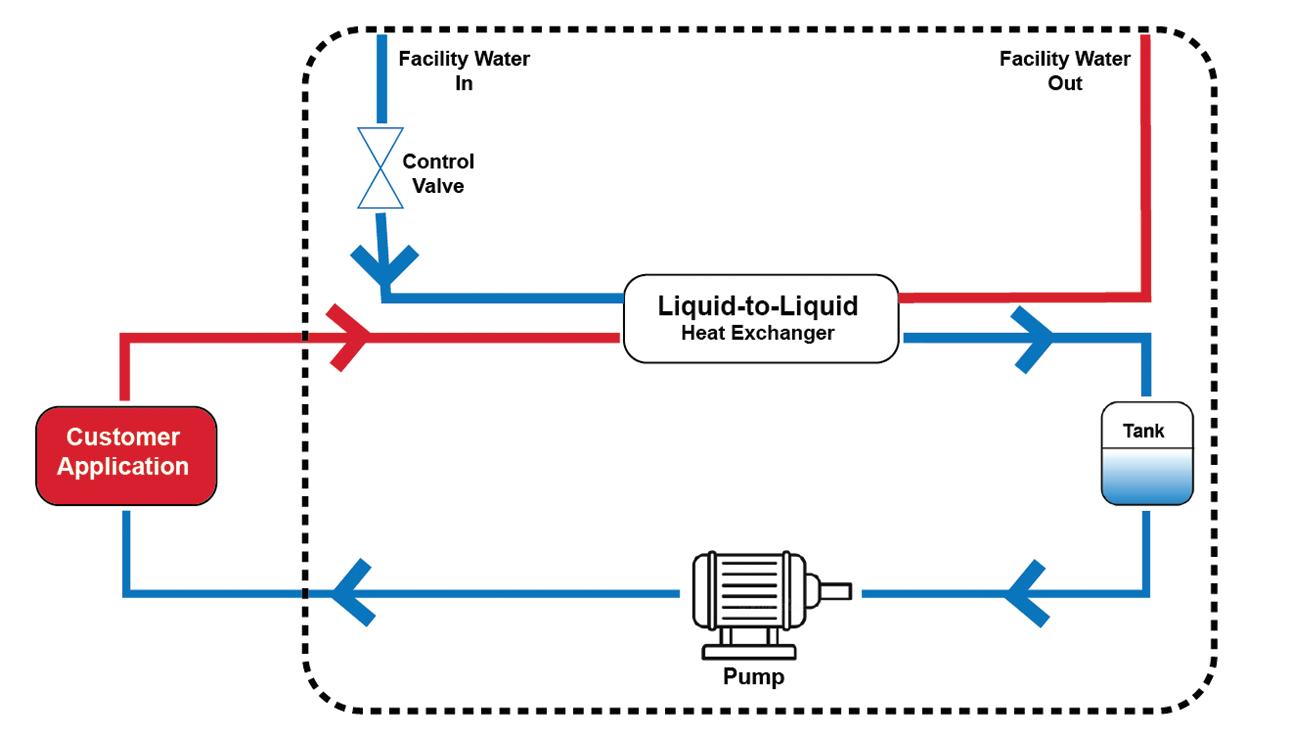
7 minute read
Liquid cooling for precise temperature control
Greg Ducharme • Laird Thermal Systems
Electronics that generate a lot of heat in a small volume often benefit from swapping a cooling fan for a system based on a liquid coolant.
The specific heat of water is higher than the specific heat of air—about 4,200 J/kg°C vs. 1,005 J/kg°C. This is another way of saying that air performs better as a thermal insulator than as a thermal conductor. That, in a nutshell, is why liquid cooling can be more effective than air cooling. Liquid cooling systems can dissipate a large amount of heat in densely packed electronic enclosures to facilitate more complex system designs. Liquid cooling systems combine a high capacity for transferring waste heat with a high coefficient of performance (COP, the ratio of useful cooling provided to work required).
There are two types of liquid cooling setups. First are l iquid heat exchanger systems. They use either a liquid-to-liquid heat exchanger or a liquid-to-air heat exchanger to cool the coolant in a liquid circuit. In the first case, the coolant is often cooled below ambient temperature using a facility (often called primary) coolant loop. Alternatively, the aircooled system will cool the coolant to near ambient temperature.
The remainder of both systems consist of a pump to circulate the coolant, often a tank to give the pump a constant supply of coolant, and a liquid circuit to transfer coolant from the heat source to the liquid cooling system.
Second are liquid chillers (recirculating chillers). They use a compressor system instead of a liquid heat exchanger assembly. A chiller uses a vapor compression mechanical refrigeration system that connects to the coolant system through a device called an evaporator. Refrigerant circulates through an evaporator, compressor, condenser and expansion device. The evaporator functions as a heat exchanger such that heat captured by the process coolant flow transfers to the refrigerant. As the heat-transfer takes place, the coolant evaporates, changing from a low-pressure liquid into vapor. The coolant then flows to a compressor, which ensures the pressure in the evaporator remains low enough to absorb heat at the correct rate and raises the pressure in outgoing coolant vapor to ensure its temperature remains high enough to release heat when it reaches the condenser. The coolant returns to a liquid state at the condenser. The latent heat given up as the refrigerant changes from vapor to liquid is carried away from the environment by a cooling medium (air or water).
Liquid cooling systems have several advantages over conventional air-cooled systems:

Liquid cooling systems can dissipate a large amount of heat. For example, in a medical X-ray system, a liquid heat exchanger system cools the coolant in a liquid circuit by the use of a liquid-to-air heat exchanger. The system contains a pump that circulates coolant and a liquid circuit to transfer coolant from the heat source to the liquid cooling system. An expansion device enables the cooling circuit to be completely sealed from the outside environment and compensates for the thermal expansion of the fluid over its wide operating temperature range.
High heat-pumping capacity: Liquid heat exchangers can reduce the thermal resistance of conventional heat sink fan dissipation mechanisms by a factor of 10 or more. This is due to the poor thermal properties of air versus coolants such as water. The value of the air heat transfer coefficient depends on parameters that include air velocity, air temperature, geometry of the surface in contact with the air, and others. For natural/ free convection, the value of heat transfer through air can be between 5 - 25 W/(m 2 K) and for forced convection from 25 to 250 W/(m 2 K). Contrast this with the heat transfer coefficient of water, 500 to 10,000 W/(m 2 K).
High heat-flux density: Heat flux density is a flow of energy per unit of area per unit of time. Liquid cooling systems can remove up to five times more heat per square area than conventional air cooling systems. This factor becomes advantageous in densely packed electronics without a lot of space for air flow.
High COP: In a compressor system, dividing heat extracted from the evaporator by the work done by the compressor gives the system coefficient of performance. For example, if an application requires cooling a heat load of 3 kW, a standard compressor-based refrigeration system typically requires around 1 kW of energy to provide the proper cooling, which is more efficient compared to other technologies. (Note that COP is typically not used as an efficiency yardstick for air cooling systems.)
Heat routing: Liquid cooling allows a small heat exchanger to sit at the heat source, which then routes heat away through a liquid circuit. This can be advantageous in densely packed electronics compared to conventional air-cooling systems. Air fans, for example, push air through the system, but the air they circulate can be well above ambient temperature if there are other hot electronics in close proximity.
Rapid cooling: Cooling time is a function of cooling capacity. Because liquid cooling systems have larger cooling capacities than conventional heat-sink fans, they can dissipate heat more quickly.
Lower noise: Systems having one kilowatt or more of heat to dissipate require large fans to get the job done. The resulting air cooling system tends to be noisier and more prone to vibration than the equivalent liquid chiller.
Liquid cooling systems can use a variety of fluids such as water, deionized water, glycol/ water solutions, dielectric fluids (fluorocarbons), transformer oil, hydrofluorocarbon (HFCs) refrigerants and natural refrigerants. The coolant that is right for a specific application depends on its qualities and thermophysical properties.

Probably the most well-known example of liquid-to-air cooling is the radiator-based system used to dissipate engine heat in vehicles.
Perhaps the most obvious properties to consider are the fluid’s phase transitions (boiling and freezing) and the chemical breakdown of the fluid’s chemistry. For example, ordinary water as a coolant is susceptible to biological fouling. Algae, bacteria or fungi can form depending on the system’s exposure to light and heat and the availability of nutrients in the wetted components. The resulting slime or biofilm can reduce the heat transferred between the fluid and wetted surfaces
In the same vein, some water-based coolants may include antifreeze agents such as propylene glycol or ethylene glycol. Propylene glycol is much less toxic than ethylene glycol, and also has a higher specific heat. But it has lower thermal conductivity and higher viscosity. Usually, system designers try to keep the concentration of glycol low because of the superior performance of water over either glycol type.
An additional consideration is the compatibility of the coolant with the materials at hand. Although stainless steel is usually excellent when there is a chance of corrosion, it also has a rather low thermal conductivity compared to other metals such as aluminum or copper. Aluminum and its alloys have good thermal conductivities ranging from 160-210 W/(m 2 K). But aluminum tends to be susceptible to corrosion or pitting from impurities in unpurified water. Even mixed distilled water, glycols form acidic compounds under oxidation that can corrode wetted surfaces and create organic acid byproducts.
There are other considerations when high power levels are involved. Cooling fluids cannot be permitted to facilitate arcing from high voltages to ground or to other surfaces. Similarly, coolants must have low electrical conductivity when working with voltages in the tens of kilovolts as for applications such as X-ray tube cooling. Dielectric fluids such as XG Galden or Fluorinert are employed for these purposes because they exhibit dielectric strengths in the tens of kilovolts per 0.10 in. A fluid with low electrical conductivity can build up static charge as a result of flow electrification. Fluids having a resistivity of 2×10 11 Ω-cm or more (equivalently, 50 pS/m or less) are considered to be susceptible to static buildup. Deionized water, for comparison, has a lower resistivity.

A conventional compressor-based refrigeration system contains four fundamental parts: the evaporator, compressor, condenser, and expansion device. The evaporator (cold section) is a heat exchanger where the refrigerant interfaces with the process fluid (air or liquid coolant in the case of a chiller) and evaporates (boils) from a liquid to a gas. During this change-of-state from liquid to gas, latent energy (heat) is absorbed at a constant refrigerant temperature. The compressor acts as the refrigerant pump and recompresses the gas. The condenser expels both the heat absorbed at the evaporator and the heat produced during compression into the ambient environment while the refrigerant returns to a liquid. The expansion device meters the amount of refrigerant flow while creating a reduction in refrigerant pressure to the point where it is ready to evaporate again. Compressor systems offer a more desirable setpoint range than air-based heat exchangers and can use 30% to 35% less power than a thermoelectric system. Modern compressorbased liquid cooling systems also offer much quieter operation in smaller and lighter packages compared to that of previous generations.
Ideally, the coolant fluid is inexpensive and nontoxic with exceptional thermophysical properties and a long operating life. The ultimate goal of maximizing coolant properties is to improve heat transfer between the fluid and the heat exchange surfaces it touches. Assessing the heat transfer coefficient directly in these cases requires use of correlations developed to calculate the coefficient for various specific geometrical conditions. In these correlations, two dimensionless parameters have dependence on the fluid properties. The Rayleigh number is associated with buoyancy-driven flow, also known as free convection or natural convection. The Prandtl number is the ratio of momentum diffusivity to thermal diffusivity.
The process of assessing a particular fluid in an application can be cumbersome, particularly when there are several kinds and orientations of heat transfer convection surfaces in question. Short of a full thermal analysis, designers may use a less rigorous approach involving a figure of merit, such as the Mouromtseff number, to give a simpler basis for comparing fluids by taking into account some or all of the physical properties.
Because liquid cooling systems can be quite complex, the optimal liquid cooling solution is often a variation of a standard solution or a custom configuration. There are many unique attributes that must be taken into consideration depending on the application. Many applications require precise temperature control of multiple liquid circuits, or multiple pressure settings to accommodate both low and high-pressure drop conditions.
All in all, liquid cooling systems such as those devised by Laird Thermal Systems are designed to maximize temperature stabilization at above, below, or equal to ambient temperature. Systems are compatible with water, water- glycol, transformer oil, or various corrosion inhibitors. Liquid cooling systems from Laird Thermal Systems can be found in the analytical, medical, industrial and semiconductor markets.
References: Coolant application note, https://www.lairdthermal. com/sites/default/files/ckfinder/files/resources/ Application-Notes/Common-Coolant-Types-and- their-uses-in-Liquid-Cooling-Systems/Common- Coolant-Types-and-their-Uses-in-Liquid-Cooling- Systems-Appnote.pdf
Thermal wizard online spec tool, https://www. lairdthermal.com/index.php/thermal-wizardpeltier-home