is sending a surgical robot to the


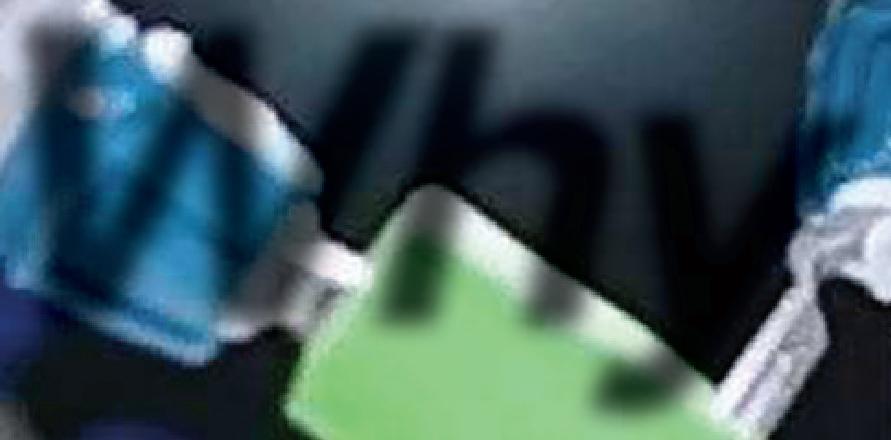

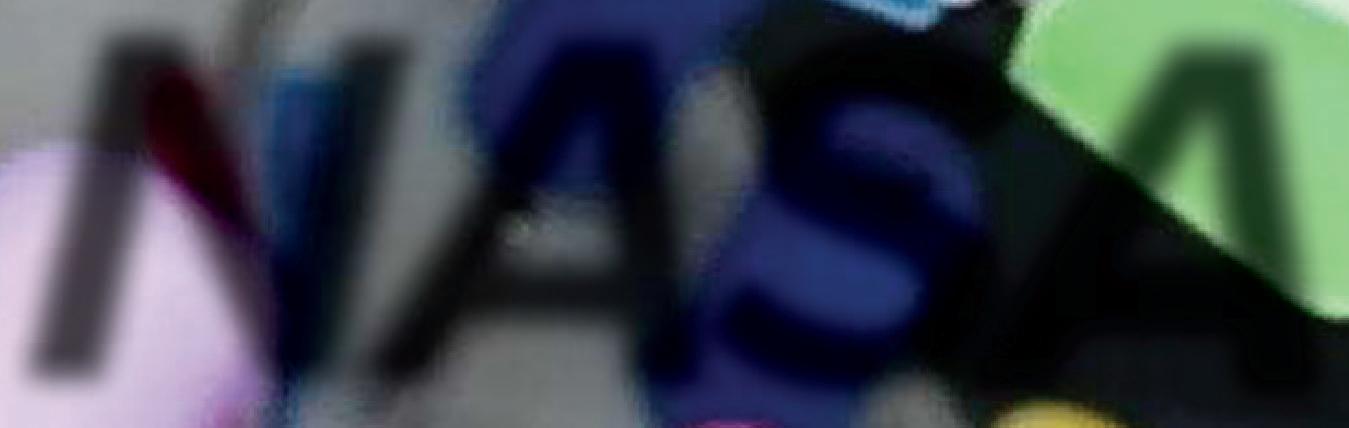
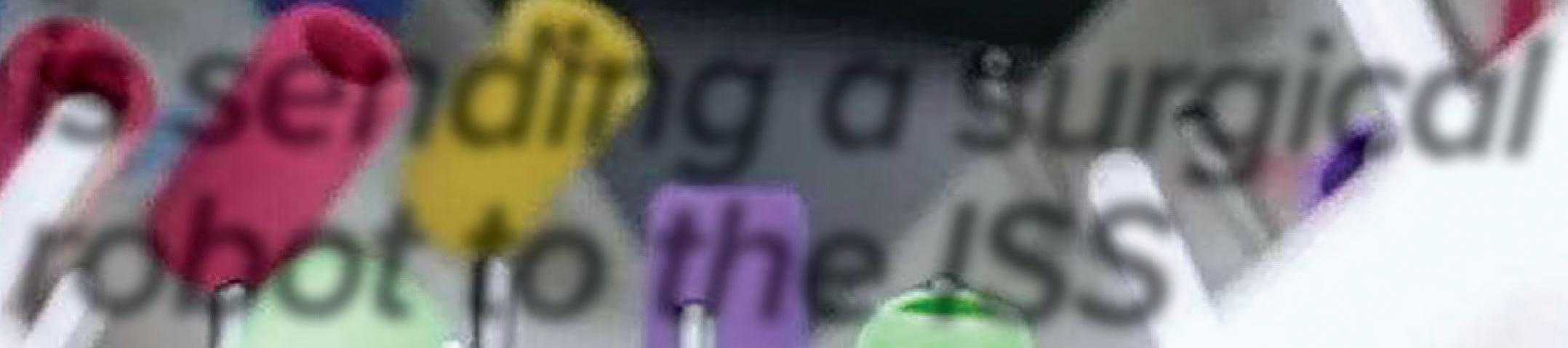
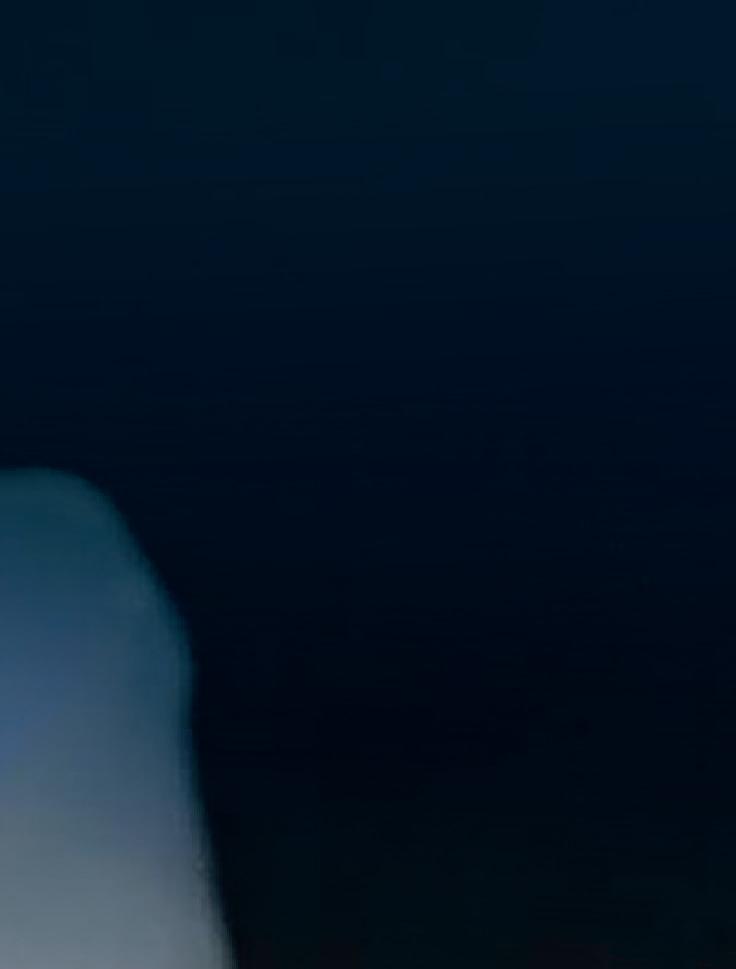

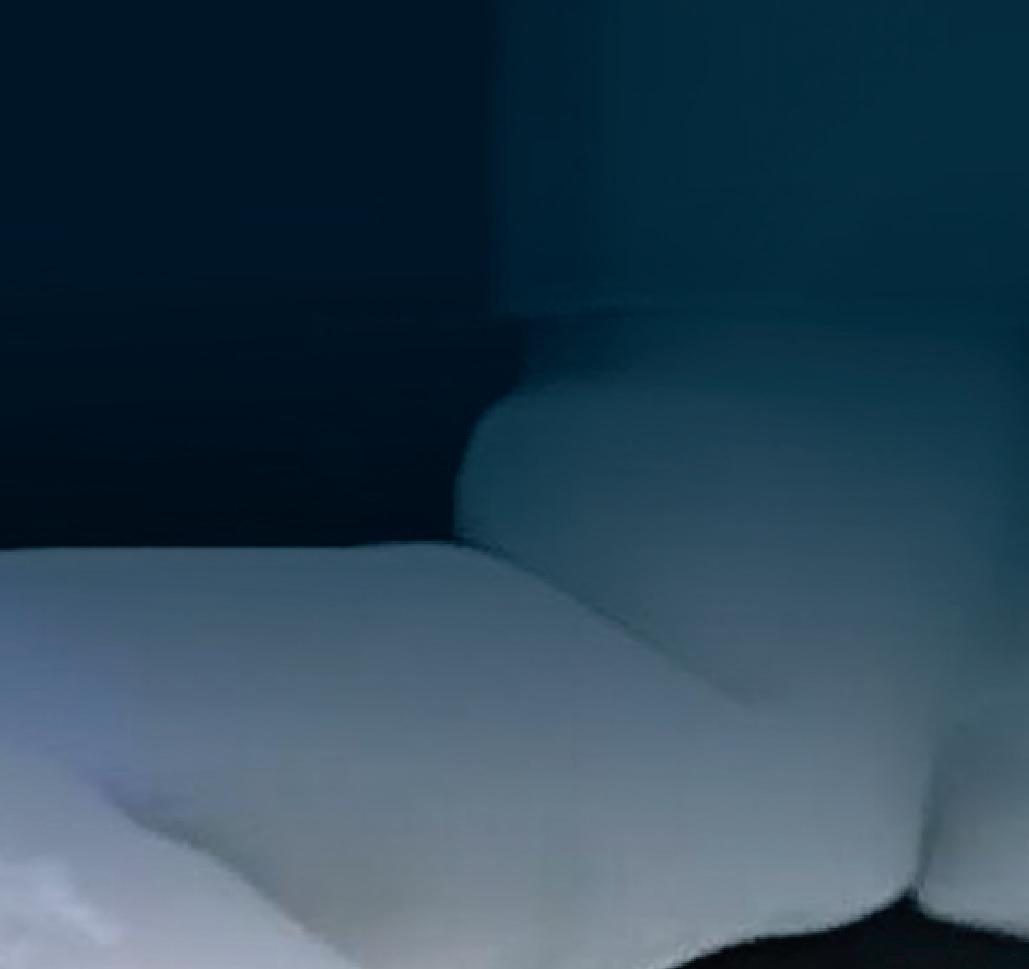


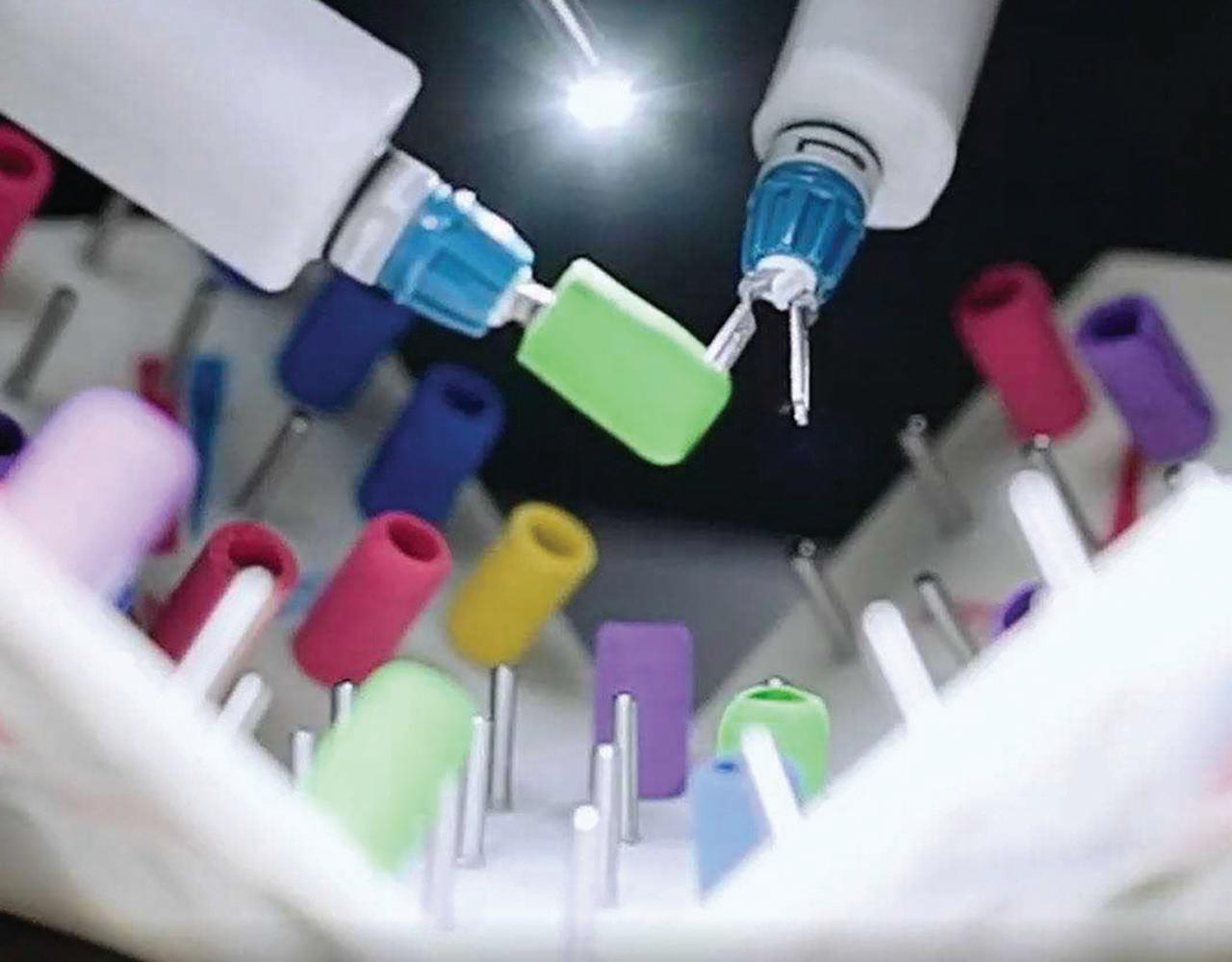
FHA-C Mini Series is a family of extremely compact
that deliver high torque with exceptional accuracy and
As part of the FHA-C Mini family, an integrated servo drive version utilizing CANopen® communication
This evolutionary product eliminates the need for an external drive and greatly improves wiring
now
retaining high-positional accuracy and torsional stiffness in a compact
Teams must embrace a multileveled approach to product development and employ “deliberate innovation” that flows from the ideation stages all the way to commercialization.
Enrique Romo | VP of research and innovation
Medical
Everyone wants to be innovative, but rarely is innovation a lightning strike of genius - especially within the robotics industry. Instead, it is an intentional process and methodology. This process is refined and modified over time to enable an organization’s ability to think creatively and execute effectively.
This is particularly important when you are solving problems in robotics that have many variables and cannot be clearly defined. Today, revolutionary leaders in robotics development are not only building solutions to obvious problems, but they are also committing to understanding and addressing the challenges associated with non-obvious opportunities. To execute effectively against these commitments, the teams must embrace a multi-leveled approach to product development and employ “deliberate innovation” that flows om the ideation stages all the way to commercialization.
Over the past few years, I’ve been fortunate enough to put this thinking into practice as my teams at Noah Medical work to identi gaps in healthcare that can be solved through the implementation of cutting-edge robotic systems. We have landed on a four-part strategy that has been refined and modified, but it has remained remarkably true to its original structure. It has helped us prime our innovation pipeline, quickly generate robust proofs of concept, and streamline product development efforts. We have expedited our overall timeline, identified and mitigated risk up ont, saved on expenses, reduced our processes, and are now standing on the cusp of having our first product commercialized, another in development, and the next being conceptualized and road mapped.
These four tenets of robotics innovation have become our north star.
By necessity, attacking multiple gaps in the marketplace means we’ll have different products in different stages of development. We designed our innovation teams to mimic this reality so we could support each stage of development appropriately.
Our initial product discovery phase is led by our product management team in close collaboration with internal technology champions. This phase is focused on blue sky brainstorming and market research. They are tasked with identifying the areas of highest opportunity or need and framing potential solutions. More ideas go to the cutting-room floor than make it on through our pipeline.
Next, our research and innovation (R&I) team is responsible for executing our phase zero stage that is focused on generating the initial definition and concepts that we believe will address the unmet needs and market opportunities. The R&I team consists of a fully independent, cross-functional team from all engineering disciplines, clinical, and marketing. This team takes a nascent idea and builds it into a robust prototype ready for engineering and pre-clinical testing. During this phase, it is also expected that all major risks are identified and mitigations are proposed, including convergence on major architectural decisions.
Finally, our research and development team will execute the product development and commercialization phase that will require them to formalize the development effort, finalize the product definition, work within design control processes, generate a technically sound and manufacturable design, and transform the proof of concept solution into a world-class product. During this phase, it is also critical to continue to solicit feedback from all users who will interact with the product and react to any gaps that need to be addressed. Once the design is frozen, a series of
major tasks such as design verification, validation, and regulatory submission will require strategy and discipline to execute properly.
Importantly, each of these groups is deliberately kept separate and independent from each other, even housed in different facilities. This is so they can remain focused on their very specific tasks and avoid being distracted by or pulled into the problems of another team. This does not mean that no communication or ideas flow between the teams. We encourage crosspollination between programs through formal and informal interactions.
We instinctively expected that this phased approach to innovation would require different behaviors and personality types, along with different rules of engagement. We did not fully grasp how distinct the hiring profiles for each group would actually be. What became immediately clear as we set these early, smaller teams in motion is that each necessitated a certain type of personality and attitude about uncertainty.
For example, our R&I phase zero group needs to operate with a skunkworks or sandbox team mentality. It needs engineers who are comfortable getting started with a strong problem statement but little product definition. They have to be OK taking big swings and missing or pursuing a vision then quickly coursecorrecting.
This stands in stark contrast to how the product development phase needs to be executed, which is guided by a project
charter, formal definition of the product attributes, upfront understanding of the risks and appropriate mitigations, a welldefined project timeline, design controls that are in line with our regulatory strategy, and processes bounded by our internal standard operating procedures. This phase requires the team to operate in a focused, disciplined, and highly collaborative fashion.
This range in personality type forced us to set up multiple hiring profiles for our engineering positions across the multiple phases. The places we recruit, the interview process, and the onboarding all vary according to each set of requirements. Answers to questions like “do you enjoy trying to find solutions to hard problems that may never become commercialized?” help us funnel people into the appropriate group.
To help focus our teams once they’re in place and staffed, we rely on product managers to help identify the most underserved problems in healthcare. They perform deep analysis to understand the pain points of various disease states, including a lack of capability, dexterity or reach by physicians or instrumentation. Or whether a requirement for proficiency is so high that a certain indication most often leads to a referral to a more specialized treatment center, delaying treatment for patients. They also match this against competition in the marketplace, the opportunity for reimbursement by payers, global market potential and other practical realities.
The end result is a thorough analysis that helps us prioritize which opportunities we will pursue. The lesson
The Harmonic Gearhead® gearbox design allows for backdrivability while ensuring highefficiency performance, maximizing elapsed operational time before recharging is necessary. High-capacity cross roller bearing supports heavy payloads.
Up to 95% Efficiency
Innovative ring gear inherently compensates for interference between meshing parts, ensuring consistent, low backlash for the life of the gearhead.
A Cross-Roller bearing is integrated with the output flange to provide high moment stiffness, high load capacity and precise positioning accuracy.
Quick Connect ® motor adaptation system includes a clamshell style servo coupling and piloted adapter flange.
Flanged output is standard for convenient, stable wheel mounting.
for us was to maximize value for patients, physicians, institutions, and payers, and to avoid building robots for the sake of robots. Avoiding the trap of innovating in search of a problem is paramount.
One of the philosophies we’ve deployed as part of our quest to build great products has been that of practical discomfort. We understand that engineers will generate better solutions if they can empathize with all the users that will interact with our product. We want them to internalize the pain points and identify the hidden opportunities. We intentionally put our engineers in non-traditional or uncomfortable situations that mimic the reality of physicians, patients or other product stakeholders to spark creative thinking.
For example, one of our most recent improvements in accuracy and user experience was the direct result of asking some of our software engineers to participate bedside at our cadaver labs. I would anticipate that not many software engineers in the medical device industry have spent much time bedside at cadaver labs, but observing and participating directly in the procedural workflow sparked the software team’s imagination in ways we didn’t fully appreciate until their moment of practical discomfort. The result was a more elegant user interface, improved accuracy, and improved user experience that will eventually differentiate our products.
These ideas on their own are not new; however, incorporating them all into an overarching strategy creates an ecosystem of constant conceptualization,
innovation, development and commercial transition that allows an organization to not only solve a robotics market problem, but also think about the next robotics one concurrently. RR
About the author Enrique Romo is VP of research and innovation at Noah Medical, a San Carlos, Calif.-based developer of medical robots. Romo is responsible for the strategy and execution of the company’s earlystage initiatives. He has over 20 years of engineering and leadership experience in medical device companies, including roles at NeoGuide Systems, Hansen Medical and was employee number 8 at Auris Health, which was acquired by Ethicon/JNJ. Romo received a B Sc. Mechanical Engineering from CalPoly.
Virtual Incision’s miniature robotic-assisted surgery (RAS) platform, MIRA, will be heading to the International Space Station (ISS) in 2024. MIRA will be testing its skills in space by simulating activities performed in surgery.
MIRA will work inside a microwave-sized experiment locker, performing tasks like cutting simulated tissue and manipulating small objects. The miniature platform weighs around 2 lbs, making it ideal for the tight spaces typical of a space mission.
“The Virtual Incision MIRA platform was designed to deliver the power of a main ame robotic-assisted surgery device in a miniaturized size, with the goal of making RAS accessible in any operating room on the planet,” John Murphy, CEO of Virtual Incision, said. “Working with NASA aboard the space station will test how MIRA can make surgery accessible in even the most faraway places.”
MIRA is currently in the final stages of its U.S. clinical trial under an Investigational Device Exemption to support U.S. Food and Drug Administration (FDA) market authorization. The system is not available for sale yet.
Shane Farritor, co-founder and chief technology o cer at Virtual Incision, has spent nearly 20 years developing a miniaturized robotic-assisted surgery platform.
| University of NebraskaLincoln
Inside the MiRA robot
Virtual Incision has said that MIRA has two key advantages. First, it can be inserted through a small incision, enabling doctors to perform abdominal surgery in a minimally invasive manner. Secondly, the technology could allow surgeons to work remotely — perhaps someday repairing an astronaut’s ruptured appendix on a mission to Mars or removing shrapnel om a soldier injured by an IED thousands of miles away.
The robotic platform is able to obtain full-quadrant access without needing to dock and re-dock an external platform. Instead, it’s inserted through a single port, and held in place with an adjustable stand that attaches to an operating room table. It weighs around 2 lbs., making it ideal for space travel.
Unlike many other RAS platforms, MIRA can be cleaned and sterilized between cases without any special equipment. The platform includes MIRA, a surgeon console and a companion cart.
“NASA has ambitious plans for longduration space travel, and it’s important to test the capabilities of technology that may be beneficial during missions measured in months and years,” Shane Farritor, co-founder and chief technology officer at Virtual Incision, said. “MIRA continues to push the boundaries of what’s possible in RAS, and we are pleased with its performance so far during clinical trials. We’re excited to take it a step further and help identify what could be possible in the future as space travel is becoming more of a reality for mankind.”
The project is driven by a grant NASA awarded to the University of NebraskaLincoln, where Farritor serves as a professor of engineering, through the Established Program to Stimulate Competitive Research (EPSCoR) at the University of Nebraska-Omaha.
Farritor led research at the University of Nebraska-Lincoln on the potential use of surgical robots in space. He cofounded Virtual Incision with Dmitry Oleynikov.
“NASA has been a long-term supporter of this research and, as a culmination of that effort, our robot will have a chance to fly on the International Space Station,” said Farritor.
Nebraska engineering graduate student
Rachael Wagner adjusts the MIRA surgical robot.
| University of Nebraska-Lincoln
For nearly 20 years, Farritor and his colleagues have been developing the tiny surgical robot. The company has attracted more than $100 million in venture capital investment since its founding in 2006.
During the next year, Farritor and engineering graduate student Rachael Wagner will write software, configure MIRA to fit inside
MIRA, a miniature robotic-assisted surgery platform, weighs around 2 lbs, making it ideal for space travel.
| Virtual Incision
a space station experiment locker and exhaustively test the device to make sure it’s robust enough to survive launch and its systems will perform as anticipated in space. Then, they will wait a year or so for the robot to get its turn aboard the station.
In a previous experiment, retired NASA astronaut Clayton Anderson took the robot’s controls while at the Johnson Space Center in Houston, directing MIRA to perform surgery-like tasks in an operating room 900 miles away at the University of Nebraska Medical Center in Omaha.
Although Farritor anticipates MIRA will function on its own in 50 to 100 years, this mission’s goal is not autonomy, but to fine-tune the robot’s operation in zero gravity.
The device is being programmed to work autonomously to conserve space station communications bandwidth and to minimize the amount of time astronauts spend with the experiment.
“The astronaut flips a switch, the process starts and the robot does its work by itself,” Farritor said. “Two hours later, the astronaut switches it off and it’s done.”
“As people go further and deeper into space, they might need to do surgery someday,” Farritor said. “We’re working toward that goal.” RR
The drive wheels on Autonomous Mobile Robot platforms benefit from the inherent characteristics of harmonic planetary technology; primarily, smoothness of travel, backdrivability, and an e ciency curve that does not degrade over time. The integral cross roller bearing construction contributes to an excellent balance of torque density, sti ness, and radial load support in a compact and reliable package. Available in dozens of standard reduction ratios, these low backlash drive trains include motor adaptation as required.
Today’s AGVs must be compact and functional robots which are able to move vertically and carry heavy loads. These AGVs cannot fail, and so the choice of their motorization is crucial. There are 5 key points to consider when motorizing an AGV.
Harmonic
1. Choose compact motorization where possible - Drives must fit into restricted spaces, as they are sometimes integrated into existing trucks. A small footprint is critical for applications in logistics.
2. Focus on ease of use – select a plug-and-play solution.
3. Opt for fast delivery of your motor solution
4. Base the design on modularity - Not all AGVs do the same job and therefore having the flexibility to select a solution to match needed specifications is essential.
Prioritize safety – select motor options with integrated sensors.
maxon’s IDX motor has a diameter of only 56 mm, its performance is equivalent to that of a motor with a footprint 25% larger. The IDX motorization thus combines performance in a compact size and ideal for AGVs.
Go to Drive.tech for more details. Visit www.maxongroup.us for more maxon solutions.
Dunham Ridge
MA 01915
maxon precision motors, inc.
Dever Drive
MA 02780
Phone: 508.677.0520
Advancing innovation for over 100 years
NEWT is committed to being the premier manufacturer of choice for customers requiring specialty wire, cable and extruded tubing to meet existing and emerging worldwide markets. Our custom products and solutions are not only engineered to the exacting specifications of our customers, but designed to perform under the harsh conditions of today’s advanced manufacturing processes.
Cables we specialize in are LITZ, multi-conductor cables, hybrid configurations, coaxial, twin axial, miniature and micro-miniature coaxial cables, ultra flexible, high flex life, low/high temperature cables, braids, and a variety of proprietary cable designs. Contact us today and let us help you dream beyond today’s technology and achieve the impossible.
Contact info: New England Wire Technologies www.newenglandwire.com 603.838.6624
Silicon Carbide (SiC) has made its mark in bringing faster, a smaller, and more reliable components than its fellow semiconductors to market. While SiC components have been around for a couple of decades, there is still a lot to learn and a lot to consider when choosing the most suitable WBG semiconductor for your device.
LET US HELP with tutorials, from looking at how WBG semis stack up in power conversion efficiency to an overview of SiC FETs and MOSFETs.
our EE