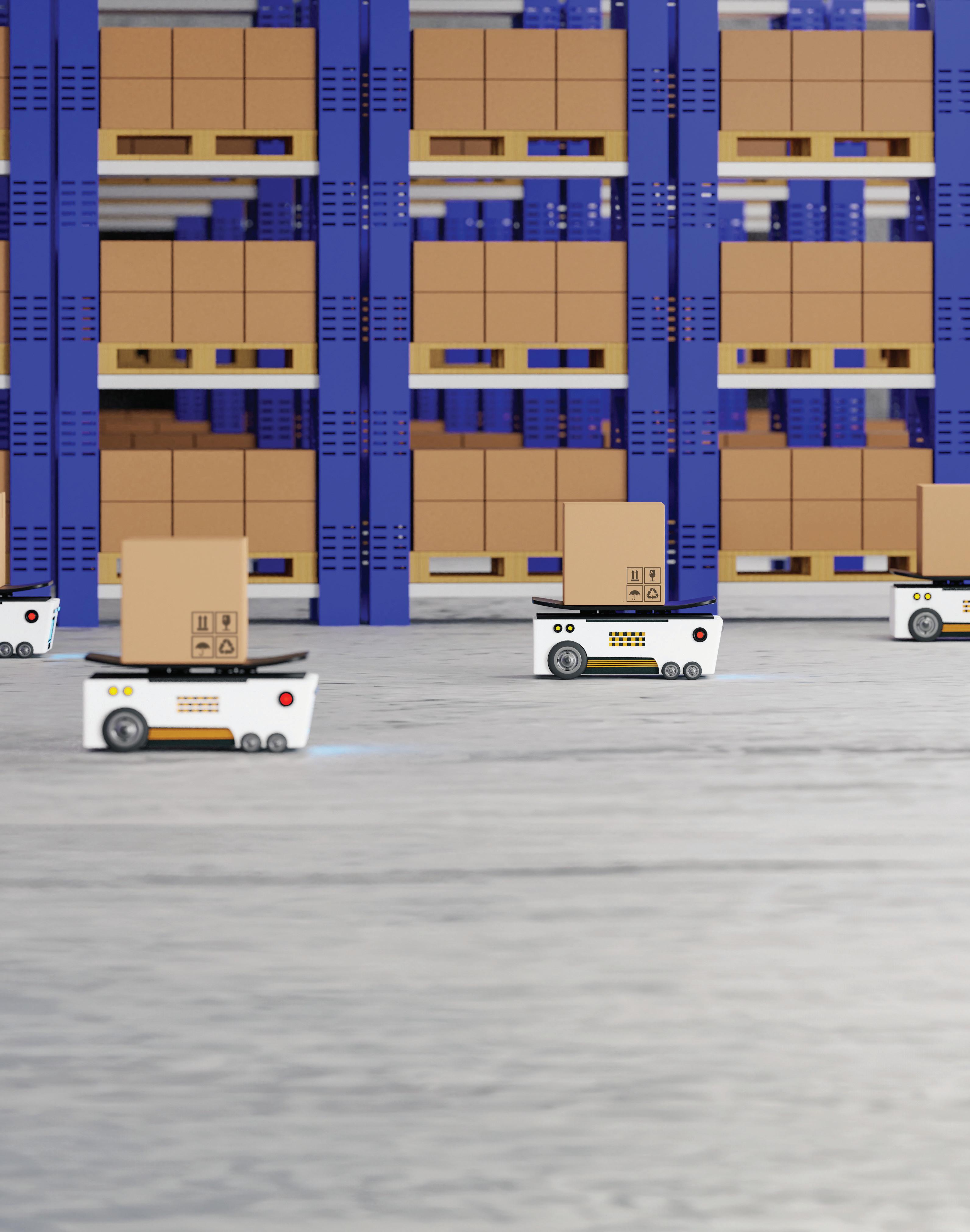
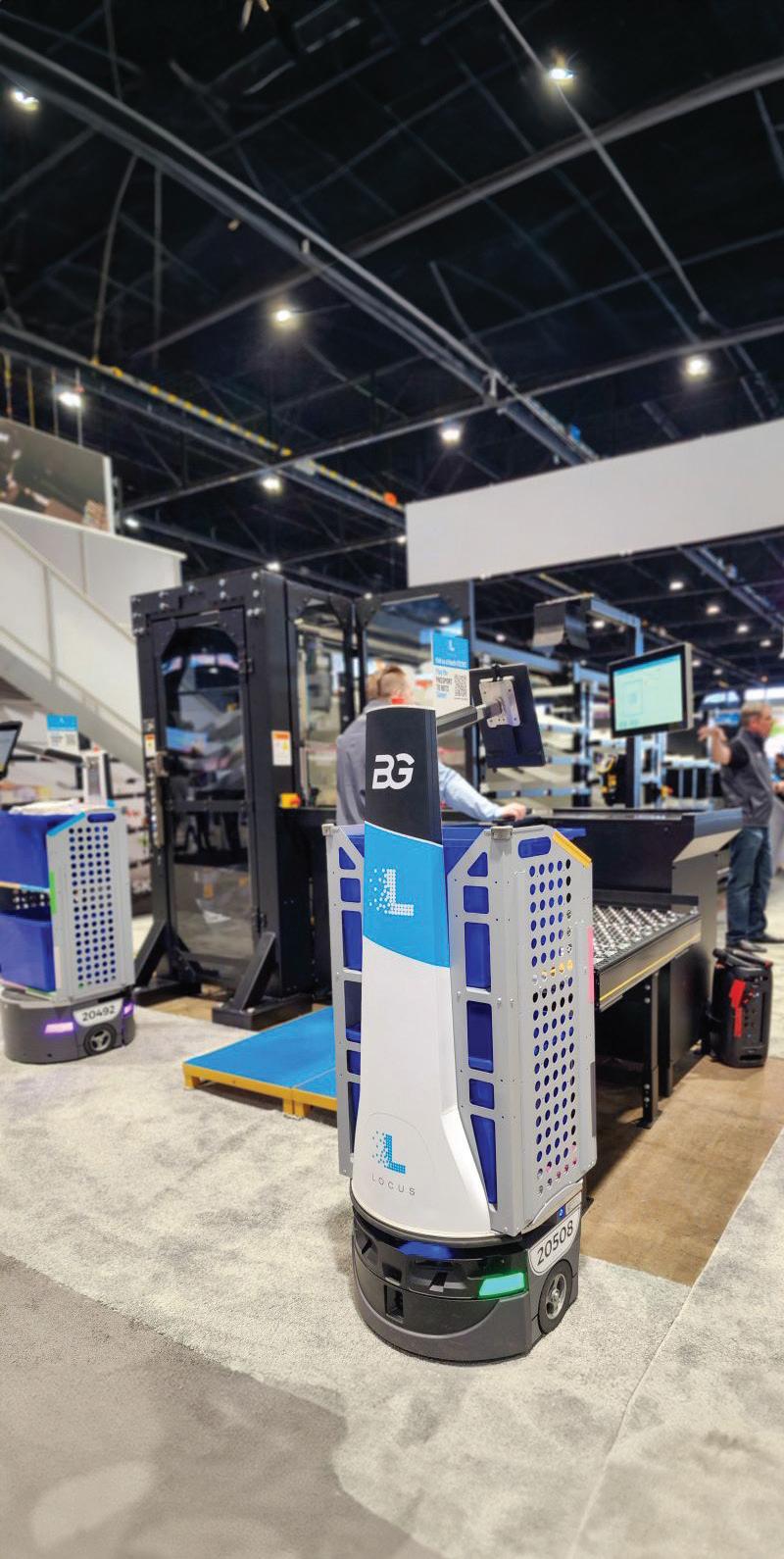
FROM repetitive stress injuries and extreme temperatures to forklift collisions, warehouses have always been hazardous environments for human workers. Robots and advanced software can benefit warehouse safety, according to Locus Robotics.
Spikes in retail and e-commerce activity, such as Amazon Prime Day, are a “major cause” of employee injuries, according to a U.S. Senate interim report.
Labor union and regulatory scrutiny join other challenges for warehouse operators, including insurance claims, recruitment and retention, damaged goods, and global competition.
“Some say that robots are replacing people, but what we’re actually doing is adding co-workers,” said Kait Peterson, vice president of product marketing at Locus Robotics. “We did a study in France because the European market is very, very conscientious about worker health and safety. We wanted to see how our robots complied with European labor and ergonomics regulations, and they came out with flying colors.”
“Our customer Boots in the U.K. has seen about a 77% reduction in workplace injuries since launching LocusBots,” said Kary Zate, senior director of marketing communications at Locus Robotics.
Introducing a new series of ultra-lightweight gear units featuring a newly engineered lightweight structure with an ultra-compact shape. Ideal for use on end of arm axes for small industrial and collaborative robots, the CSF-ULW is also well suited for general industrial machinery where weight is a critical factor. The two smallest sizes, 8 and 11, are available today. Other sizes coming soon!
• Zero Backlash
• High Accuracy
• Ultra Lightweight
• Ultra Compact
• Reduction Ratios 30:1~100:1
• Super Flat Configuration, 19mm (size 8); 21.5mm (size 11)
• Outer Diameter: φ 42.5mm (size 8);
φ 50.5mm (size 11)
• Weight: 90g (size 8), 150g (size 11)
Boots also reported that the amount of people calling in sick declined once they were no longer moving heavy steel carts, he said.
“They actually nicknamed the carts ‘widowmakers,'” Zate recalled. “Folks were turning the corner and bumping into them. And so the workers themselves were absolutely thrilled that robots changed their situation.”
“We also change the ergonomics, because walking is reduced, and there’s no lifting,” he said. “A worker at one of our customer sites said that her biggest thrill is that she’s no longer fatigued at the end of the day and that ‘I can go home and be the mother I’ve always wanted to be.'”
Not only are warehouse associates more aware of their surroundings when they’re not behind carts, but they can also focus more on picking, he said.
Locus provides native-language support for multiple languages so that when an associate wearing a lowfrequency Bluetooth tag approaches, the robot’s display automatically changes. “That also helps with their comfort and stress levels,” said Peterson.
Robots extend productivity for older, younger workers
Another benefit of automation is that it can extend the careers of warehouse workers who might otherwise be worn out physically and be unlikely to be replaced by younger generations, noted Zate.
“Only 14% of Gen Z would even consider working in a warehouse; they’re looking for something different in the long term,” he said. “Anecdotally, we’ve heard of workers inviting their family members and
friends to come work at automated warehouses. They say, “You’ve got to come to this place because first, the work is easier, comparatively. Second, we’re working with technology.’ There’s a coolness factor.”
Peterson added: “About a year ago, UPS Healthcare added robots to its fleet and had a naming contest. Some people named them after their kids, and some let their kids suggest names for the robots. We’re actually retraining people to live in the next generation of work, because the Gen Z
Position, angle and speed measurement
Contactless, no wear and maintenance-free
High positioning accuracy and mounting tolerances
At maxon, we develop and build high precision electric drive systems combining brushed and brushless DC motors, gearheads, sensors, and controllers into complete mechatronic drive systems. With our products, complex challenges like highly dynamic multi-axis positioning, synchronization or compactnesscan be solved cost-effectively and efficiently.
Engineered for peak performance, our advanced drive technology ensures unparalleled efficiency, agility, and reliability. For more go to: www.maxongroup.us
and Gen Alpha people that are coming are already familiar with multiple technologies.”
Systems must learn to mind their surroundings, says Locus Peterson also cited case studies involving cold storage, time-sensitive packaging, and multi-level mezzanines with forklifts, all of which can stress workers and affect warehouse safety.
“The key is not just scale — we have sites running almost 1,000 robots across four mezzanine levels,” she said. “It’s important to design for safety across applications and environments.”
“Somebody doesn’t put a pallet all the way into the rack, or somebody goes up high without double-checking what’s below. Somebody drops shrink wrap on the floor — all kinds of stuff happens in logistics,” said Peterson. “Our ability to design not only the robot, but also the software to be responsive and proactive to changes in supply chain environments, is a key differentiator from a safety perspective.”
While interoperability among mobile robots is a subject of standards-making efforts, Locus is working to make sure that safety is consistent among its models, said Zate. Communications with forklifts, which are sometimes manual and in different or overlapping zones, is another goal.
“Our robots can now see forklifts and have ‘no-go’ zones so they don’t go under them,” he said. “We’ve launched PIT or powered industrial truck-to-robot visibility. Not only is it robot to human; it’s robot to robot and robot to PIT that’s human-controlled.”
Locus is also working on warehouse safety with other automation providers such as Berkshire Grey around packaging, sortation, and conveyance.
“As the market matures, there’s no tolerance for someone’s science experiment anymore,” said Zate. “Buyers want a solution that’s tested, that’s reliable, and that’s secure and safe.”
Peterson noted that humanoid robots will have to prove that they
to blocked paths
Locus claimed at MODEX 2024 that its AI and LocusHub support warehouse safety. Gina Chung, Locus Robotics
provide more value than other form factors and that they don’t reduce warehouse safety.
“What does it solve, and is it doing it better than a human?” she asked. “Can we solve these problems in a different way? Mobile manipulation is a small subset.”
Operational visibility can also improve warehouse safety
Even before it deploys autonomous mobile robots (AMRs) at a customer site, Locus Robotics conducts a “concept of operations” or COO process, explained Peterson. “We take a snapshot of their operations, design out what the robots would do, and simulate that out,” she said.
“We also launched LocusHub at MODEX. It’s our data intelligence platform for customers to look at trends over time,” Peterson said. “Companies were desperate for a solution and recognized that they had fewer injuries. As we get bigger, we’ll have even more anonymized data, as we recently surpassed 3 billion picks.”
Wilmington, Mass.-based Locus won a 2024 RBR50 Robotics Innovation Award for passing 2 billion picks last year.
“Most of the operators are asking, ‘How do we meet these SLAs [service-level agreements] and keep our productivity up? How do we get the most out of our workforce that’s dwindling?'” said Zate. “They look at warehouse safety as a soft benefit. Connecting that information with their HR [human resources] teams will help them to see the benefits across the board.”
One of the benefits of Locus’ robotics-as-a-service (RaaS) model is that it handles all of the maintenance, upgrades, and repairs, said Peterson. So when a warehouse safety update is pushed out through LocusHub, customers can automatically get them, she said.
“Within our LocusHub platform, we’re making predictive recommendations, but there’s still human interaction, and the human still has to make a decision about the data that the AI is presenting,” Peterson said. “Just because people could see their supply chain from end to end, if the data was crappy, it didn’t do anything for them. That’s why AI will be big for things beyond using ChatGPT to slot inventory orders.” RR
• Inline planetary gearbox with very short overall length
• Conforms to industry standard wheel sizes
• Rotating hub with dual wheel bearings eliminates overhung load and supports very high payloads
• Fully sealed, maintenance free
• Customized design with modified GAM gearbox
• Meets the demanding shock and reversing loads, as well as overhung load, of an automated parking robot wheel drive.
• Standard GSL Strain Wave (harmonic) robotic gearbox
• Custom housing and mounting flange provides mounting surface and pilot to directly mount wheel
• Developed by GAM in collaboration with Customer
• Custom planetary gearbox developed by GAM for motor manufacturer
• Custom motor rotor shaft with an integral sun gear (gearbox input) reduces the overall length.
• Wheel mounts directly to spline output shaft
• Planetary gearing with offset input shaft
• Stub shaft opposite the output simplifies adding encoder or brake
• Well-suited to narrow track gauge where a coaxial drive would not work
The Robot Report Staff
Mobile robots have become an essential part of the automation landscape in recent years. For end users, they offer flexibility, scalability, and efficiency for various industries and applications. But what do customers actually want from mobile robots, and how do they evaluate and select different technologies and vendors?
Interact Analysis, a market research firm, recently revealed the results of its 2024 Mobile Robots Buyer Survey. The global survey covered the preferences, expectations, and challenges of end users of mobile automation. The company talked to 300 buyers and users of mobile robots, covering different company sizes, sectors, and regions.
With the survey, Interact Analysis hoped to shed light on the current and future adoption of mobile robots,
the factors that influence purchasing decisions, and the pain points and benefits of using mobile automation.
The survey showed that mobile robot adoption is growing across different industries, but not at the same pace in each sector. Ninety-five percent of respondents said they already use some form of mobile automation in their facilities, such as automated forklifts, platforms, conveyors, and autonomous mobile robots (AMRs). This proportion, however, varied greatly by company size and sector.
Larger companies, with revenues over $1 billion, were more likely to use mobile robots than smaller ones. Manufacturers, especially those in the automotive, electrical, and semiconductor sectors, were also
more likely to use mobile robots than retailers, third-party logistics (3PLs), or other industries.
71% of respondents said they only partially automated their workflows with mobile robots, indicating there is still room for improvement and expansion of mobile automation.
When it comes to emerging technologies, artificial intelligence was the most commonly mentioned emerging trend that customers were interested in, specifically when it came to mobile automation.
On the other hand, customers weren’t very familiar with the VDA 5050 standard for communication and interoperability. Only 20% of respondents said they were fully aware of it, and only 8% said it was or would soon be a mandatory requirement in their purchasing decision-making between mobile robots and fleet
managers developed by the German Association of the Automotive Industry (VDA).
Customers more concerned with cost than loyalty, says Interact Analysis Interact Analysis’ survey revealed that cost and integration difficulties are the main barriers and drivers of mobile robot adoption, and that these were two major factors for both technology and vendor selection. The most common reason for not using mobile robots was the high price or perceived lack of return on investment (ROI), followed by environmental factors such as floor suitability, space constraints, or climate.
Customers are not loyal to one mobile robot brand or type, according to the survey. Instead, they would rather use multiple brands and types for different workflows and facilities.
On average, respondents used
Interact Analysis’ survey gave insights into what end users expect from autonomous mobile robots.
3.4 different mobile robot brands, and 123 brands were mentioned in total, reflecting the fragmentation and diversity of the market.
ABB was the most mentioned brand, followed by OMRON, KUKA, and Locus Robotics. However, when survey takers were asked which brand they consider based in class, the answers varied by industry and applications Interact Analysis plans to share those results at a later date.
Customers did indicate they prefer to use the same mobile robot brands across different workflows in the same building, but not necessarily across different buildings or facilities in their network. This suggests customers care little about robot interoperability within a facility.
When selecting a vendor, the most important factors were the vendor’s track record, integration expertise, and local/on-site support, followed by the
stability and size of the vendor. Price and product range were less important than the vendor’s reputation and service, the survey found.
Chinese vendors were not very popular among customers, with only 20% of respondents saying they had used or would consider using them in the future. The most common reasons for not considering Chinese vendors were security concerns, performance issues, safety issues, and legal reasons.
The survey found the most common reason for needing to automate was the desire to reduce operating costs, followed by the need to improve reliability and accuracy. Surprisingly, a lack of labor was not one of the biggest reasons for automation.
When selecting technology for an automation project, the lowest lifetime cost and the ease/speed of integration were the most important factors, followed by system flexibility and performance.
When automating, customers expect a quick return on investment (ROI) and smooth implementation from mobile robots. Eighty percent of respondents
Position sensors for stroke measurement in hydraulic cylinders
Compact safety rotary encoders for position and speed measurement
Dynamically compensated inclination sensors for precise angle measurement
expected an ROI within three years, with most of those expecting it between 18 months and three years. 3PLs typically expected a quicker ROI than other sectors.
Customers typically measure the success of robot implementation by a variety of different metrics. The most common metrics used to measure the success of mobile robot implementation were ROI, productivity, throughput, accuracy, and cost reduction.
Before making a final purchase, customers also expected to see the automation system in action, either through an in-house demo, a reference site visit, or a visit to the supplier’s demo center.
During the purchasing and implementation process, the most common pain points were operation slowdowns, routing and tasking difficulties, and problems with integrating with internal software.
© Interact Analysis 2024
Once a robot was operational, the most common pain points were lack of maintenance prediction, costly downtime, and too much manual intervention required.
Major barriers to adopting mobile robots are lack of available budget and other competing priorities. Interact Analysis
“The survey provides valuable insights for mobile robot suppliers and integrators who want to better understand and serve their customers,” said Ash Sharma, chief commercial officer and vice president of research for robotics and warehouse automation at Interact Analysis. RR
The GML is a planetary gearbox designed specifically for Wheel Drive applications. The rotating hub design, along with dual wheel bearings, eliminates overhung loads, allowing the gearbox to accommodate very high loads — ideal for pulleys or wheel drives.
• Directly mount a wheel to the output flange and pilot on the rotating gearbox housing
• Motor mount customized to your motor, no coupling needed
• Fully sealed and maintenance free
• Compact inline design with very short overall length
• Available in 3 sizes with optional wheel
GAM Enterprises, Inc.
801 E. Business Center Dr. Mount Prospect, IL 60056
888-GAM-7117 | 847-649-2500
www.gamweb.com
info@gamweb.com
The new FBS Series gear unit features an extra large hollow shaft with a compact outer diameter that is ideal for robots and machines requiring complex cabling to pass through the axis of rotation. It includes large cross-roller bearings, enabling the load to be mounted directly to the output and is available in two sizes (25, 32) and three reduction ratios (30:1, 50:1, 100:1).
Scan the QR code for more information on the FBS Series Hollow-Shaft Gear Unit.
Today’s AGVs must be compact and functional robots which are able to move vertically and carry heavy loads. These AGVs cannot fail, and so the choice of their motorization is crucial. There are 5 key points to consider when motorizing an AGV.
1. Choose compact motorization where possible - Drives must fit into restricted spaces, as they are sometimes integrated into existing trucks. A small footprint is critical for applications in logistics.
2. Focus on ease of use – select a plug-and-play solution.
3. Opt for fast delivery of your motor solution
4. Base the design on modularity - Not all AGVs do the same job and therefore having the flexibility to select a solution to match needed specifications is essential.
5. Prioritize safety – select motor options with integrated sensors.
maxon’s IDX motor has a diameter of only 56 mm, its performance is equivalent to that of a motor with a footprint 25% larger. The IDX motorization thus combines performance in a compact size and ideal for AGVs.
Go to Drive.tech for more details.
Visit www.maxongroup.us for more maxon solutions.
Phone: 508.677.0520
www.maxongroup.us info.us@maxongroup.com