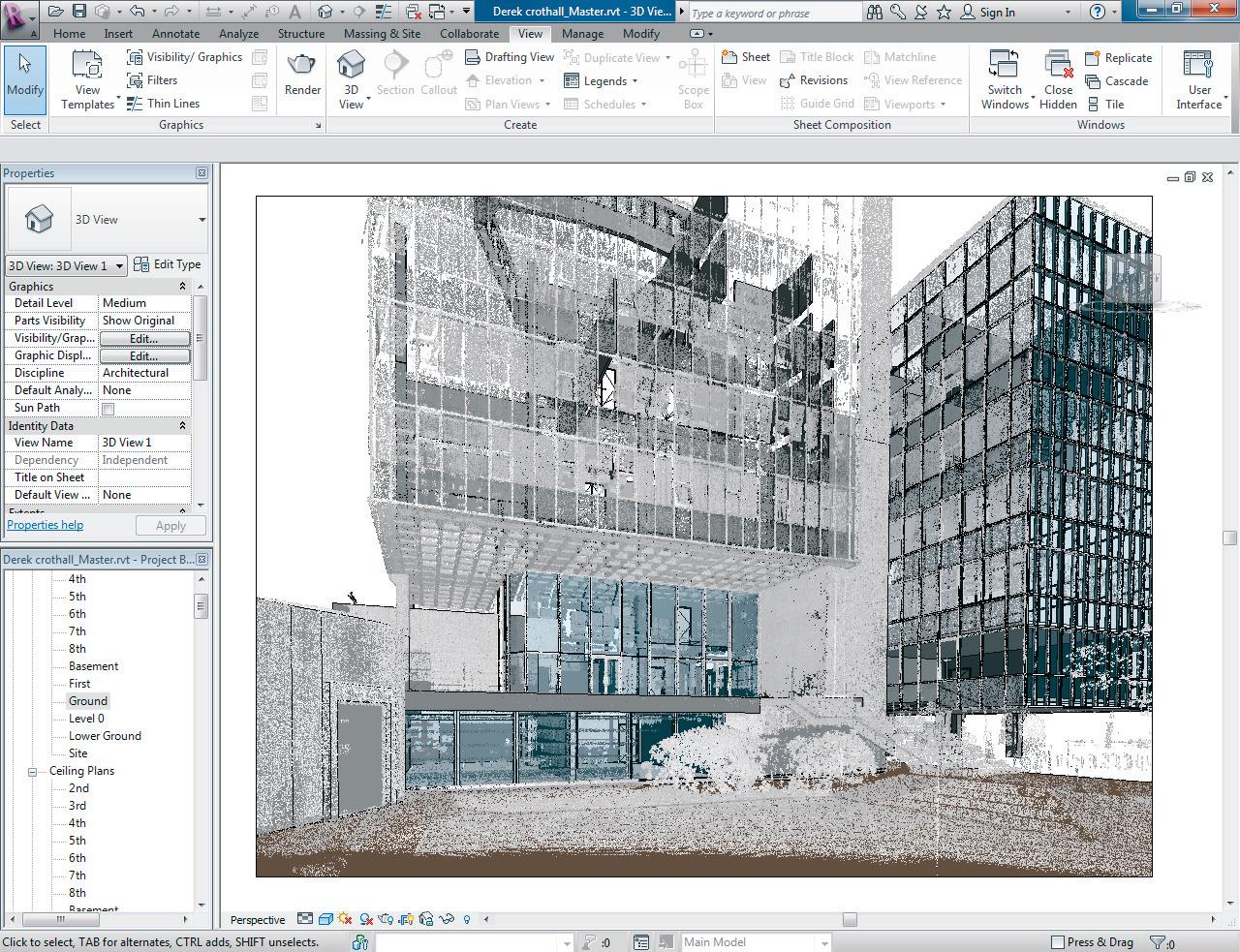
14 minute read
Scan-to-BIM ... a reality check
Building Information Modelling (BIM) is mainly focused on newbuild projects, but refurbishment and renovation requires a different approach. Using 3D Laser scanning, there is a growing interest in ‘Scan-to-BIM’. Martyn Day caught up with Steve Bury a leading UK practitioner of point cloud data and Autodesk Revit.
The concept of Scan-to-BIM sounds like something out of science-fiction. Take one building, laser scan millions of points in minutes and produce a ‘point cloud’. Next, import that into your BIM tool, which automatically recognises doors, walls, windows, ceilings, and spaces and you get an intelligent 3D BIM model out the other end. Unfortunately, it is science fiction; it is just not yet possible.
With a growing refurbishment market, Scan-to-BIM is getting a lot of coverage in the industry and now, with nearly every major CAD software developer supporting point cloud data within their base systems, the hype has never been greater.
As one of the UK’s emergent surveying experts offering a Scan-to-BIM service, Steve Bury of Bury Associates in Worcester, has a much more realistic view of what is possible.
Formed in 1997 Bury Associates has been supplying Revit models from survey data since 2006. AEC Magazine spoke to Mr Bury to get a sense of where the scanto-BIM market has developed and where it is now.
This eight storey university building was scanned and modelled with 300 laser scans. Bury Associates then used the scan data to create the final fully parametric Building Information Model in Autodesk Revit
Laser-scan workflow Martyn Day With laser scanners and point cloud data now featuring heavily in your Scan-to-BIM service, how has your surveying workflow changed over the years? Steve Bury We were using standard data collection methods — total stations with AutoCAD — and then taking these DWG files into Revit and building our BIM models from there. Now we also use laser scanners, which measure millions of points per second; measuring millions of points across whole building surfaces, as opposed to a total station that is just measuring precise specified points on key features.
Laser scanners are like a blunderbuss they just get everything, while a total station measures what you want — the corners of the room, the height of the room, the position of the door etc.
While sometimes it’s quicker to use the old methods, rather than the laser scanner, the great advantage of scanning is its speed on site. You collect absolutely everything very quickly. While there will be blindspots as laser scanners work on line-ofsight you get most things. But we still use a tape measure and all measurements have to tie it into a survey control.
We survey with a GPS system; it’s accurate to within a centimetre or two and we use that to get a datum, which links back to Ordnance Survey data and we put that on an Ordnance Survey grid.
Here, we tend to knock off the first three digits of the reference because Revit doesn’t like these huge co-ordinates. Then we travel through the building taking measurements, referring back to the grid system, so we build an accurate survey of the building. Then we bring the laser scanners in and we tie into those control points.
We effectively create layers of scan data built on an accurate grid system. When you laser scan a job, you take a number of scans and these add together within that accurate grid system.
We also put up reference targets throughout the building. It means you can freely move around with the laser scanner to capture point clouds and bring them all together back at base on the computer and the software automatically recognises the targets, spheres and chequer boards we have put up.
While this process is automated you still need the human eye to make sure everything is set up okay. If there’s an error then the
whole model can be out because they reference one another, so we check every scan prior to adding it to the master survey coordinate database.
For this we use the Faro registration and viewing software program called Scene, which comes with the Faro laser scanners. We also use PoinTools as an add on to AutoCAD and Rhino especially, for editing the point cloud and removing the noise. This can be ghosting from cars going past or anything else which moves within the laser scan. Specialist point cloud tools MD It is interesting that you continue to use specialist third party point cloud software, despite AutoCAD and Revit now having point cloud capability. What do you think about the relatively new Autodesk point cloud engine in AutoCAD? JB Well, It’s as good as the one that’s in Revit [laughter]. They have got a long way to go. Autodesk is buying up new technology to improve its offerings but the software we use, PoinTools, sadly, has been bought by Bentley Systems and perhaps that’s a real problem, as for a long time we were waiting for the PoinTools interface with Revit. I guess that isn’t going to happen now because Bentley and Autodesk are competitors. I’m looking forward to seeing what Autodesk does with Alice labs, another point cloud company which they acquired recently. Data deliverables MD In terms of deliverables, you offer everything from standard 2D CAD drawings to full Revit BIM models. With a growing fascination with laser scanning, and the price of laser scanners dropping considerably, are architects now asking for just the point-cloud data? SB In my opinion it’s a waste of time and there’s a real lack of understanding about point clouds. I blame Autodesk and perhaps the resellers for minimising the reality of the huge amount of effort it takes to import point cloud and convert back to something useful.
When we go on site and do a laser scan we could easily generate over 6GB of data. On some of our larger projects we’ve taken over 300 scans, which ended up being over 20GB of data. Nobody can handle that — the data sets are just so incredibly large.
While it may look spectacular, because it’s the real world in dense points, it’s actually really dumb data. To manipulate it and actually do something useful with it is a completely different issue. It’s a skill to take that huge amount of information and produce what the client actually wants, which could be a 2D drawing or a 3D BIM model.
We’re getting people asking for the point cloud data because they don’t understand what it involves and then they’ve seen a video on the web and think their CAD system can import it. Scan-to-BIM automation MD There’s a perception in the industry that Scan-to-BIM is an automated process. What would you say in response to this? SB If the marketing is to be believed it’s automatic! This is a real problem for setting expectation. People expect miracles from surveying with a laser scanning. To be honest, getting the real world into a BIM system was an industry afterthought.
When Revit was designed, or any other BIM system, no one gave any serious consideration as to how you would bring in
laser scan data. BIM systems are highly Proprietary formats intolerant, they don’t like staircases going MD I have been to a number of scanning through walls or any mistakes that can be events and heard first hand from firms that made on site surveying. There is an have invested heavily in working out a Scanassumption that Scan-to-BIM has come to to-BIM methodology. One of the problems the forefront and is an automated process with using many bits of hardware and softwhen it’s absolutely not! ware has been the explosion of proprietary
While there are some applications on the file formats and some have even employed market, which offer some interpretation of full-time ‘data wranglers’ to create paroles the cloud, basically finding vertical faces of data in the right format for each project and defining them as walls, we have tried participant. Do you have similar issues? most of them and have come to the conclusion that they all have a long way to go. SB Scan-to-BIM is a minefield at the
It’s a bit like voice recognition software moment. We’re helping an American firm on your phone. When I first got my latest scan and model a major building in San phone I tried to send a text saying to a Francisco. We are getting data off them in friend I was approaching Kidderminster, all sorts of formats, so we’re constantly havwhat he got was a text saying ‘I’ve got ing to jig things around and convert data. dementia!’ While it’s all possible, it just adds time.
It’s the same with automatic recognition The few of us that are producing surveys software. If the building is perfectly rectan- in a BIM format are doing it in Autodesk’s gular with flat walls and no objects in the Revit. We don’t sell ourselves as so much a way, it’s fantastic. But if you’ve got a real BIM company, more that we can deliver in building with real things going on in it, Revit. However we get requests from firms they don’t know what to make of what they using other BIM tools. We bid on one job in find in the point cloud. Revit does really like buildings with straight lines and nice clean walls, but try going to an old stone walled building in the Cotswolds and it’s totally ‘‘ People expect miracles from impractical. surveying with a laser scanning. Modelling standards To be honest, getting the real MD When it comes to delivering a world into a BIM system was an Revit BIM model, every individual industry afterthoughtcompany seems to operate to their own standards. Lines, circles and arcs in 2D drawings are generic ’’ but the intelligent components in Revit which the architect was using ArchiCAD. need defined families and consistency. As they couldn’t find anyone using that What are your experiences of this? system they were looking for a surveyor to SB From the work I’ve seen the standards IFCs to export it back into ArchiCAD. vary greatly, especially on the level of detail, We don’t know how that project eventuto some very rudimentary modelling. That ally ended up but all I can say is that we’re may very well be fit for purpose but the doing a job for that client now and they just problem is there are no standards yet, stan- wanted a 2D drawing as a deliverable. We dards of quality. have a long way to go before IFCs are the
I have two major projects on my desk at DXF of the industry, we are a very long way the moment; there were no specifications off. I’m not even sure if it’s the right direcwhatsoever when it comes to the standards tion. It causes me great concern and I can of the BIM model they want, just ‘a Revit see all sorts of problems in the future if we model’. We know we will do a proper job don’t get common standards. but we may be pricing against somebody who is going to build a very rudimentary Scanning in vogue Revit model. MD There’s a huge ‘wow factor’ and mar-
We think there’s a lot of work to be done keting behind scanning technology at the to define good standards and procedures moment. How has this impacted your data for getting survey data into Revit. We have deliverables? developed in-house standards and are aimmodel the building in Revit and then use ing to promote the specification that we’ve SB All the time now, people are dictating to written by sending it out to architects and us how we do surveys saying that they other people using Revit in the industry as want a laser scan survey, even if we think no one else is doing it. it’s not appropriate. In the 30 years I’ve been doing this job, until today, people never came up and said to me ‘I want you to do a survey in this way, using this methodology or technology’. The deliverable and what they wanted was always an accurate set of drawings. They now may want a Revit model but now I’m being told to do this I have to laser scan the job.
We did the whole of Manchester Central library. We chose not to scan it; we used conventional survey instruments and our own data collection methods that we developed, and from that we created a 3D BIM model.
You can define a wall with a start and end point, a height and a thickness but now with clients specifying laser scanning, we are being forced to measure 10 million points across that wall! It’s too much information and information that will never get used.
There are ways you can take that laser data and produce useful things; 3D panoramics, like Google Street view, [for example]. [This would be] far more useful to the architect than the raw point cloud. You could see how many plug sockets, fittings, how many light sockets etc. If you want the raw point cloud, of course we will supply it, but it should not be considered to be THE deliverable. We’ve had a number of people say we’ll do it ourselves. They only end up doing that once because unless you’re handling that type of data (point clouds) every day, you just can’t get competent at doing it.
You can’t just use Revit to edit point clouds; you have to use other pieces of software in order to extract the information.
One of the fantastic things about scanning is that it captures everything, so with historical buildings if it should burn down or suffer damage, if it were to be laser scanned, there would be an accurate record of what was there before, carvings or mouldings etc.
Photographs only go so far, but if you had a laser scan of it, you would have everything you need to reconstruct that building. You could even use the data to create moulds to make replica interior decorations. The cost of purely scanning and holding that data isn’t that high. Complete BIM MD One of the core concepts of BIM is that architectural, structural and service data is captured and used as a collaborative platform. With so much work going in at the start to build a BIM model at the survey stage, how are these other elements incorporated in Bury Associate’s work?
SB We never have much knowledge of what will be done to the building. We’re there at the start of the project, we measure up the building and [produce] the surveyed information, and that’s it.
I think that’s going to change and particularly when it comes down to M&E and steelwork, we should all be working together at the start to produce that initial BIM model, where they can add that expert knowledge about supporting walls, steel walls, struggle elements etc. That has not happened. It’s something that is in the plan for our business in the future we will offer a service, which is more forensic, looking at asbestos, looking at drainage.
At the moment we are also investigating radio-controlled helicopters with cameras on to inspect roofs. This will help us complete the BIM model, as with standard scanners on the ground we can’t see those details. We’ve been trying Autodesk 123D catch, which has been a bit hit and miss but from what we’ve seen of it, it has great potential. We hear you can get really quite good precision out of it but have not achieved that yet. The cost MD With the extra amount of work involved in laser scanning, point cloud editing and then constructing a Revit BIM model, how much extra does it cost to get a BIM deliverable over a traditional set of 2D survey drawings? SB It obviously depends on the size of the building and its complexity. I’d say as a ballpark, it’s 30%-50% more to have a 3D BIM model. This sometimes causes misunderstandings with customers getting quotes, as they think that we are collecting the same information to create surveys to produce 2D drawing deliverables as to create a 3D model.
This is a general problem with customers understanding of BIM; the costs are front loaded towards the start of the design process. We’re still creating 2D CAD drawings to supplement the BIM model because BIM in the whole refurbishment and renovation market is still in its infancy. Thinking about it, it’s still new for newbuilds as well!
■ buryassociates.co.uk
1 and 2 In 2010 Ryder Architecture was commissioned by Manchester City Council to redesign the interior layout of this Grade II listed library. Bury Associates produced the 3D model, which would form the foundation for the BIM process. It contained complex areas of detail, including intersecting vaulted ceilings following the curve of the building 3 Here the benefits of getting a BIM model back at the survey stage over a set of 2D drawings are clearly obvious. Models can be quickly sectioned and voids identified in the building
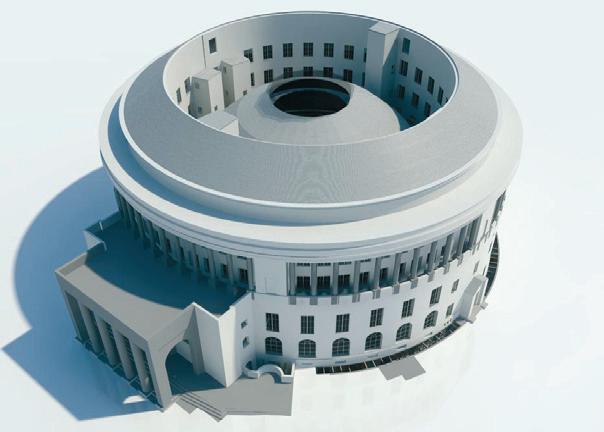
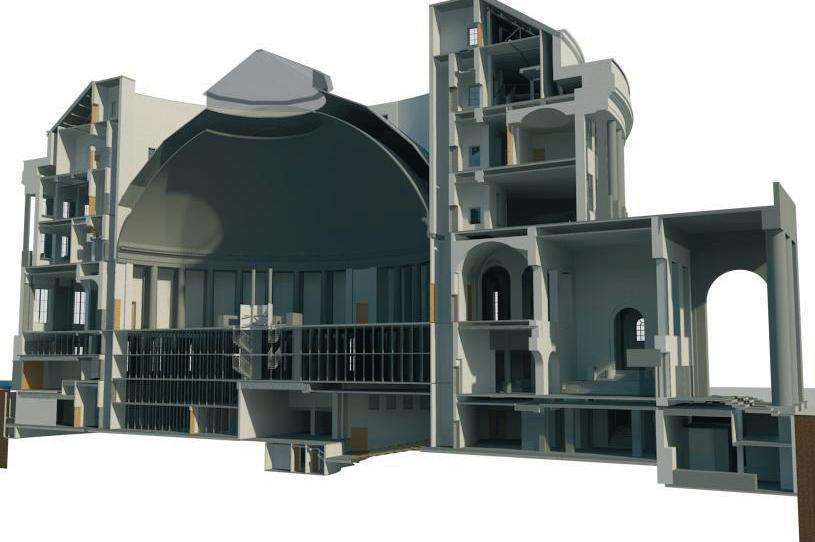
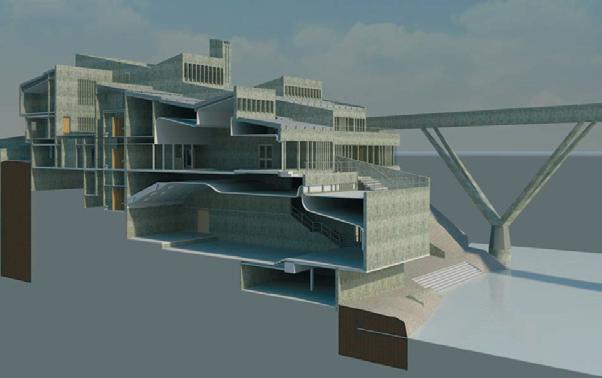