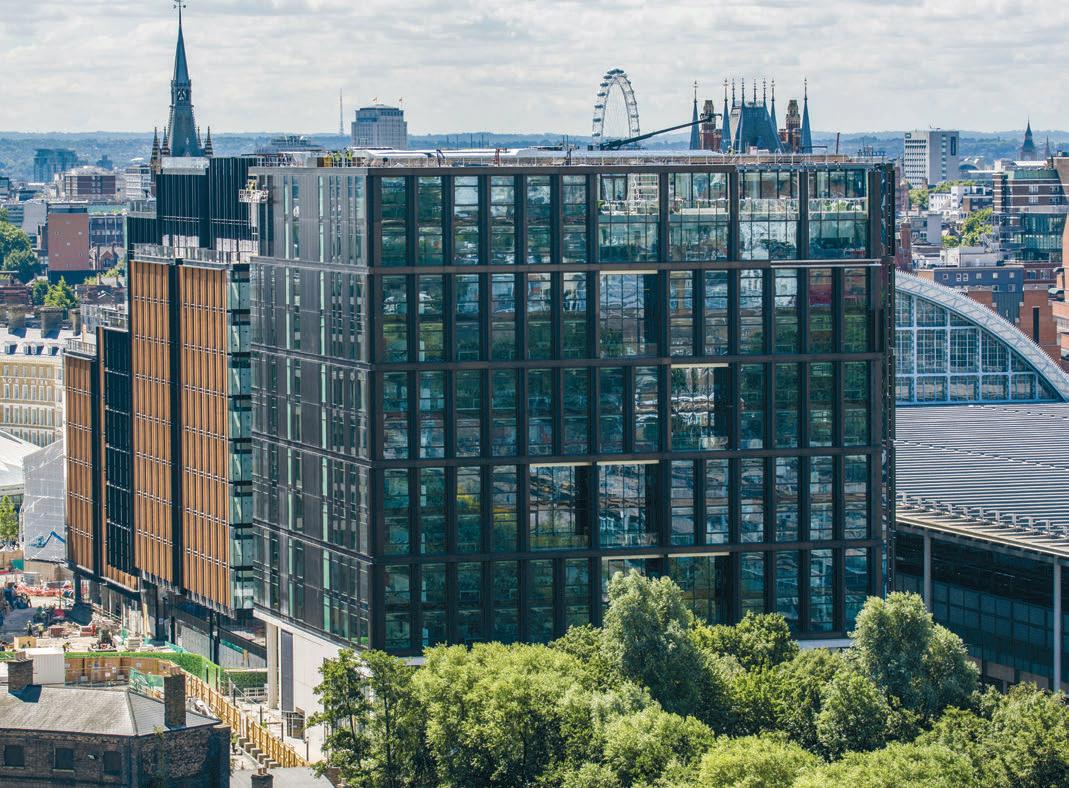
10 minute read
their stride
All in their stride
When design complications and subcontractor woes threatened to derail the build at Five Pancras Square, planning software Asta Powerproject proved its worth.
Delivering any £68 million ent time and money. “The original plan called for four-stodevelopment requires precise “I came up with a plan to construct rey-high concrete columns, on top of planning, but the build at Five some of the outer walls and reduce the cli- which we would have to land 27-tonne Pancras Square, near King’s ent’s requirement for temporary works,” steel beams, all requiring lots of tempoCross in London, required James he says. “Both we and the client produced rary framework and propping,” says Carpenter of Kier Construction’s major programmes, but we collectively agreed to Carpenter. “I believed that using steel colproject business to map out the project use just one programme, which was the umns, rather than concrete, could help us with particular care. one we produced in Asta PowerProject. build more effectively.”
The complex core requirements for this This was a lot clearer to understand, in He used Asta Powerproject to compare 14-storey, mixed-use community, destined terms of how you format bars and links, the two approaches in detail and see how to house London Borough of Camden and we ended up planning the whole of they would work in practice, when it came facilities and offices, included a 10-storey the early enabling works for ourselves to issues such as access to the site, for atrium, a cantilevered central stairway and the remediation contractor.” example. and basement facilities that included two This enabling phase hit a few road- “Using the software I could show both swimming pools and a gymnasium. bumps, however: although Kier was able to options and overlay them on the baseline,
As if all that wasn’t enough to contend start work after just four months, and to show the benefits of changing the with, the mid-project collapse of subcon- ahead of schedule, the remediation work scheme and structural design. I could tractors responsible for the steel frame took longer than expected. As Carpenter show clearly that, if we built it the other and cladding of the build added way around from the bottom up, to the challenges. Carpenter was involved from the outset as a construction man‘‘ Asta Powerproject allowed all parties it would drastically reduce the need for temporary works, saving both time and money.” ager and was subsequently to clearly understand the issues, but appointed project manager, more importantly, how we were going Big project, big team going on to receive a gold medal at the Construction Manager of to achieve the handovers Such a complicated, multi-faceted development required a large the Year awards. He won the prize not just for delivering the ’’ team that included many different specialist subcontractors. In building, but also for his skillful handling explains: “We used Asta Powerproject to all, there were 35 site-based managers and of the issues it presented. He used Asta help with re-sequencing not just the the number of operatives on site hit a peak Powerproject throughout, to help him mit- enabling works, but also some of our early of 410 people. That included employees of igate risks to the project, re-plan in the key sectional handover dates. The software some 50 different subcontractor firms. event of unexpected changes and keep allowed all parties to clearly understand Keeping everyone informed, so they could everyone involved informed and engaged. the issues, but more importantly, how we act as a single delivery team, was absowere going to achieve the handovers.” lutely critical. Getting a head start The architect’s design for Five Pancras Carpenter held regular monthly planThe original plan at 5 Pancras Square was Square presented challenges from the out- ner sessions with all subcontractors, for Kier to move in and begin work after set. Due to the inclusion of two swimming using Asta Powerproject: “We would remediation of existing gasholders was pools at basement level, columns weren’t mark up progress using the software and completed by the client, Argent. Carpenter an option for the basement space or the review the next month or six weeks on got stuck in, doing whatever he could to triple-storey entrance areas. Instead, an screen,” he says. facilitate during that early phase through ‘upside-down’ approach was envisaged, in In addition to these meetings, there were workshops and meetings. In the process, which a steel frame would be created for also collaborative ‘Last Planner’ meetings, he realised that it might be possible for the first four storeys, with a 10-storey con- using a Kier methodology. “At Last Planner Kier to start work earlier and save the cli- crete frame above. meetings, I would put charts on the wall to
Five Pancras Square: a 14-storey, mixed-use community for the London Borough of Camden
ensure buy-in for different areas, from different subcontractors. Things like groundworks and the roofing were complicated, so we would make sure all the subcontractor managers were there, along with site teams. When several people contribute, you get a much clearer answer about how you can actually build something,” he says.
“Our team would mark up the progress in Asta Powerproject at least weekly,” he continues. “The good thing about that is that you can see almost ‘as built’ progress. It’s a great tracker of what’s actually happened. Sometimes, if you have to investigate why something isn’t progressing as expected, it’s good to see progress highlighted above the planned baseline, and see actual dates and impacts.”
On a couple of occasions, Carpenter and his team spotted potential fragmentation of the steelwork installation, for example. “With Asta Powerproject, you can break out or highlight the bars for a particular section of works, and see what’s going on. When the steelwork subcontractor wasn’t working consistently, we could see it in the programme.” Rethink – not once, but twice With the insolvency of not one, but two major subcontractors during the project, the team had to move swiftly into recovery mode twice during the course of the project.
“When the steelwork contractor went into receivership, it created a whole series of re-planning activities. They were due to be on site early on, for between three and four months. Delaying their work would have a critical impact on other activities,” says Carpenter.
“We lost almost 12 weeks so, to recover, we not only re-programmed lots of work in Asta Powerproject, but also resequenced the whole concrete frame that would go above the steel frame. We used the resource features of the software to work out how to bring on more resources in key areas, to speed up critical activities and to prove where the new critical path was. We recovered about six weeks by doing that. Although the client knew we were suffering delays because of the subcontractor insolvency, we were able to use the software to show them exactly what we planned and demonstrate precisely how we were going to recover the time.”
The team was back in recovery mode when the cladding subcontractor went bust, about half-way through the two-year build. Having come up with ideas to enable internal works to continue, despite cladding work ceasing, Carpenter says that they once again turned to the software to help prove their case: “We planned for temporary waterproofing outside, and then inside re-sequenced some of the floors. Instead of building them in sections, we put the work together differently, and with Asta Powerproject, we were able to prove that it would save several weeks and the investment upfront would save money in the long run.”
Final fit-out, environmental excellence The final phase of the two-year project included the complete fit-out of the leisure centre, library, café and more. On the office floors, the contract originally specified only the toilets, lift lobby and stairs for full fit-out, with a CAT A fit-out of the offices. The client, however, altered its
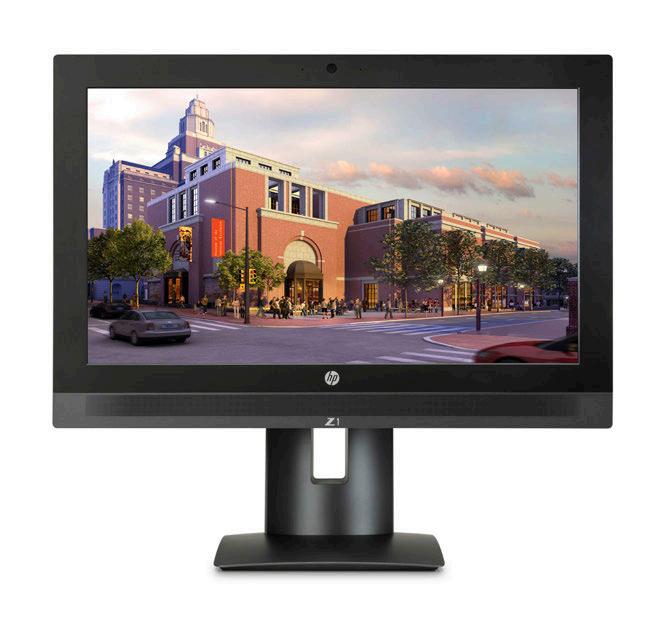
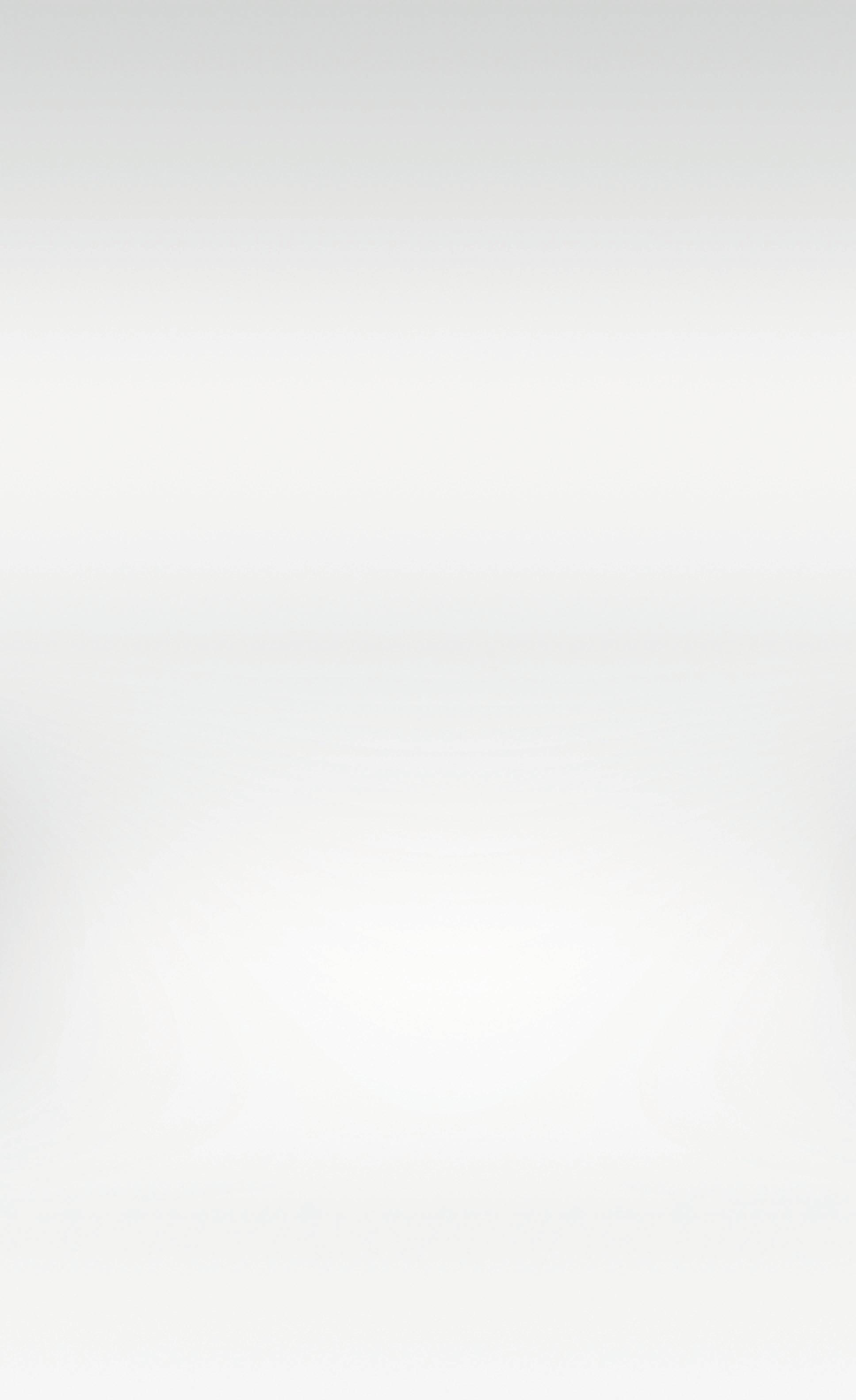
At Five Pancras Square, a steel frame was created for the first four storeys, with a 10-storey concrete frame above
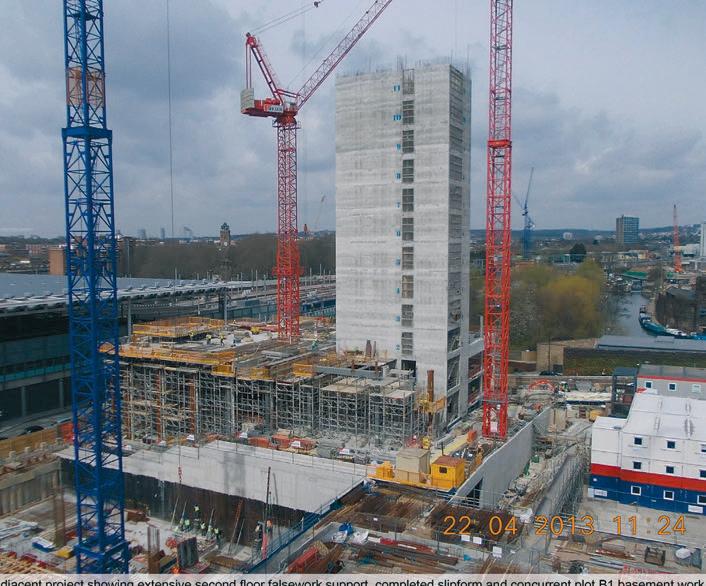
requirements and requested a full CAT B proved key to maximising credits. “Using Asta Powerproject, we created a turnkey fit-out. “We built BREEAM in from the start, tracker programme to make sure we
That called for further re-planning exer- with the client and also with London could check the progress on all the suscises with the client, using Asta Borough of Camden. Everyone agreed it tainability activities each month. That Powerproject to demonstrate the need for a was a key target. Every month at our client was important, because for some key deadline extension, says Carpenter. “We meetings, we would show the tracker credits, we had to do specific things halfagreed to the full fit-out to include data programme, highlight anything coming way through; there was an interim and power cabling, ceilings, meeting up and flag up other potential credits, assessment around transport systems, rooms and breakout areas, so that [the including the latest dates for their for example. This initiative had its own premises] were ready to move into. It was inclusion.” critical path! We also saw there were finely tuned – we finished on the Friday, For example, at tender stage, Kier looked some potential extra credits for design Camden moved in on the Monday and into the potential for using recycled and other things, so we set milestones in there were 400 people working in the aggregates and discounted them on cost order not to miss those opportunities. building by the end of the following week.” grounds – but later on, it revisited that Tracking these milestones with Asta
With such a large development, Powerproject meant that they the main Asta Powerproject programme grew to in excess of 2,500 lines over the course of the ‘‘ We built BREEAM in from the start, never fell off the radar. It kept it front of mind for everyone, and became a focus for decisions.” build. However, it was also used with the client and also with the This use of the ‘BREEAM to create some additional vital London Borough of Camden. Everyone Tracker’ was a first for Kier as plans and programmes, as Carpenter explains: “We used agreed it was a key target well as for its client Argent – but it is unlikely to be the last, Asta Powerproject not just for the main programme, but also to ’’ says Carpenter. He’s personally been using Asta Powerproject plan other things like key safety elements. option, prior to the decision date shown since 2000 and it’s been the company’s We also used it to help us hit our on the tracker. “We went through the standard on everything from large resiBREEAM Outstanding target – and we concrete mix design with the contractor, dential developments to RAF facilities, were delighted to get 97.6%, the highest sat down with the concrete supplier and prisons. [score] for any building of this type.” Hansen, and found that we could in fact Five Pancras Square was a weighty proj-
BREEAM (Building Research get more than 25% recycled aggregate in, ect to undertake, complex and challenging Establishment Environmental Assessment at less than a quarter of the cost we had throughout. Yet Carpenter was able to Methodology) is the world’s most compre- originally assumed,” says Carpenter. prove the power of planning in overcomhensive environmental assessment method The team had a significant list of ing even quite extreme delays and found and rating system for buildings. Within the desirable targets to hit if it was to meet its ways to innovate, not only for the client, scheme, some credits relate to building pro- goal of outperforming other UK buildings. but also to prove Kier Construction’s comcess, some to materials and others to how “We couldn’t afford to miss a single mitment to sustainability. buildings operate. Getting ahead of it credit,” says Carpenter. ■ astapowerproject.com