
14 minute read
laser scanning
The black art of laser scanning
Building BIM-ready models from point cloud requires considerable manual construction, a skill level developed by working with and understanding fully the nature of the data. Ploughman Craven’s Peter Folwell explains.
The profile, awareness and capabilities of 3D laser scanning have grown exponentially over the last couple of years. With the UK government mandate to deliver level 2 Building Information Modelling (BIM) by 2016 for publicly funded work, and an increased market trend towards refurbishment and retrofit, there has been a greater emphasis on the use of 3D laser scanning technology and the ability to deliver BIM-ready models of the existing environment.
There has been an increased awareness of the benefits that this powerful technology can bring through the whole project lifecycle — from the ability to collect a lot of up-front accurate information for feasibility studies and planning, through to wall alignment checks at demolition, clash detection, design comparisons and monitoring during construction. Other advantages include an accurate solution for offsite manufacture, pre-fit out surveys and asset recording for facility management.
One result is an increase in the visibility of scanning manufacturers extolling the virtues of their products and ease of use for all, plus a surge in development of software abilities to handle large volumes of point cloud data. This, coupled with a decrease in costs and barriers to entry, is starting a possible trend away from the traditional surveying expertise route for delivery.
The emergence of 3D laser scanning opens up other professional’s minds to the benefits on offer but without a full understanding of the complications, limitations
About the author
Peter Folwell is a director at Plowman Craven with responsibility for survey deliverables within the BIM environment. He is involved in Survey4BIM and a founder of BIMnet.
and considerations that need to be taken fully into account, success can be limited.
There is an increasing number of users in the market, but many have limited experience and understanding of the full range of operational issues and what needs to be considered and addressed in order to achieve accurate and useable information.
Plowman Craven has been associated with 3D laser scanning technology for over 14 years now, both utilising it and helping to develop it. In recent years, we have completed numerous high profile BIM associated projects within different market arenas, delivering both laser scan data and BIMready models. We are now in a position where we have a highly experienced understanding of the full technical applications, workflows required, issues and a comprehensive catalogue of lessons learned. 3D laser scanning technology provides a number of considerable advantages and benefits when collecting data in an existing environment, particularly in complex, architecturally challenging and safety restricted situations. Collecting data rapidly, in 360 degrees, with speeds of up to 1,000,000 points a second provides an instant record and a complete data set in order to extract 2D information or build BIM-ready models.
However, it is a line of sight technology and, contrary to popular belief, it does not go through walls or ceilings.
It sounds a great solution but what needs to be considered in order to achieve the desired outcome? Right tools for the job There are many scanners on the market at different cost prices and capabilities. These could be static, airborne, vehicle mounted and even handheld. It is critical to understand what each can deliver and the most appropriate use. The right choice of tool can have a profound effect on the project cost and also accuracy of the data. Quality control The real black art of 3D laser scanning is knowing what is likely to be going on ‘under the bonnet’ and understanding how to achieve optimum performance and the required results.
Angles of incidence: Geometric considerations and location to reduce glancing
Surface reflectivity: Different surfaces and conditions produce a varied quality
Scanning speeds: Gauges the intensity and volume size of the point cloud
Quality settings: Filter settings that influence the level of noise in the data
Target ranges: Consideration of distance
The emergence of 3D laser scanning opens up other professional’s minds to the benefits on offer but without a full understanding of the complications, limitations and considerations that need to be taken fully into account, success can be limited
to target features related to instrument capability and geometrical baseline/control
Calibration: Continuous monitoring of instruments set up and operational state
Operational procedures: Workflows/ continuous training to ensure efficiencies and accurate/usable data.
The above are all quality considerations but data control is key. ‘Cloud to cloud’ registration of a number of data sets is appropriate for certain scenarios but for complete integrity, target control and relation to a control network is essential for overall accuracy and data confidence. The importance of this methodology is not always recognised outside of particular professions. Capabilities, capacity and liability Data collection utilising laser scanning technology is a measurement surveyor’s core activity and skill set. Workflows and training are aligned to continually provide information in many varied formats to ensure the understanding on how best to represent ‘real’ geospatial scenarios within a design environment. Ultimately, there has to be considerable responsibility, reliance and trust to deliver accurate information that will provide the platform for designs, construction and manufacture processes.
Surveyors are becoming more ingrained into the BIM process and are beginning to play a larger role, in collaboration with other stakeholders, outlining and assisting employer’s information requirements and BIM execution plans. Data collection expertise, and having a real understanding of capabilities, can bring additional valued knowledge to the table, reducing risk on the projects. Data management We are all aware that software and hardware capabilities are developing at a rapid rate and the ability to handle large data sets is improving exponentially, especially on the cloud, but it is hard to keep pace, and with cross-business IT demands, it is difficult to justify having the most appropriate or latest software or hardware.
Raw point cloud data can produce enormous file sizes which need to be manipulated and managed. Giga-bytes of point cloud data from a single setup will contain erroneous and unwanted data that needs to be cleaned and registered. This is not an automatic process!
The use of these very large datasets can often be a real burden to the design team and on more than a couple of occasions we have heard horror stories of abandonment of the data altogether. In order to avoid this scenario CAD software capabilities are important, but key will be how the data is broken down into manageable portions for efficient handling.
Building BIM-ready models from point cloud is not yet an automated process and requires considerable manual construction — a skill level developed by continually working with and understanding fully the nature of this data. Effectively, the dataset is a powerful archive of information that can be accessed and enhanced continuously throughout the lifecycle of a project. Understanding its history and make-up provides the ability to manage the information more effectively and be of greater use to all stakeholders. It allows for more cost effective solutions. For example, it may be more efficient to build a less detailed model at the start of the process, but have the capacity to return to the data to model in greater detail in critical areas at a later stage.
Having managed and gained a full understanding of the true nature of the point cloud, real value can be gained in utilising the data for other purposes, such as heritage recording or obtaining asset information, particularly when the detail can be enhanced with digital photography. 3D laser scanning and delivery of BIMready models can provide a data solution for many aspects of the BIM process. As the awareness of 3D laser scanning continues to grow so does the misinformation about its capabilities and where its applications lie. It can be a powerful tool in the right hands and answers a multitude of scenarios but you have to be sure you know what you have, and what you are doing. Just because the data may look right, it does not mean it is right.
In order for 3D laser scanning technology to have a major influence in BIM development and deliver what can realistically be achieved, it is necessary to have a comprehensive understanding, not just in relation to the real benefits of the technology itself, but also to the ‘black art’ of using it.
Autodesk Gallery Paris
Autodesk’s One Market headquarters in downtown San Francisco is charged with inspiring innovation. It is used for monthly, themed ‘Design Night’ events and engagement with start-ups and the local community. It also acts as a design gallery for the display of customers’ work.
Outside the Bay City area, and in Europe in particular, however, ‘Autodeskers’ have long complained of a lack of similar outreach facilities. But in October Autodesk capitulated in style, opening a pop-up gallery in the heart of Paris. The free threeweek event was held at the Galerie Nikki Diana Marquardt on the edge of Marais.
Autodesk branding was kept to a minimum, alongside a combination of interactive and static displays. The space had a 3D print zone and Fablab, an artist in residence and evening events. It showcased customers’ work in architecture, product design, fashion, automotive, aerospace, 3D printing and laser scanning. Autodesk’s top brass flew in for customer meetings and evening events with talks on a wide variety of design topics.
With over 1,500 visitors in the first four days, Autodesk is considering other pop-up galleries in Germany, Italy and the UK. Local projects were prominently displayed alongside attractions from Pier 9, which is likely to be replicated at future events. Welcome, Spark Visitors were given a chance to try out Autodesk’s new 3D printer, Spark, which was designed in the UK and made at Pier 9. Autodesk is using Spark as a testbed for its own 3D printer software development and to promote its brand. It is expected that at some point, fabrication will be moved to a provider with great capacity. Pop into 3D printing Autodesk gallery showcased a snapshot of innovations currently shaping design from small-scale jewelry to giant infrastructure projects. It was inspiring and educational and, above all, there was no hard sell, which made it a relaxing entry point for industry folk and the public alike. It is a shame the pop-up element means that it will never be in town for long. One wanders what ever next for Autodesk? From this successful gallery outing, I would expect another to pop-up sometime soon.
Pop-up Pop Art
HyperGreen Tower The first thing attendees saw on entry to the gallery was a highly detailed 3D printed model of the HyperGreen Tower, by Jacques Ferrier Architectures. Standing 246 metres tall, the tower design has a curved, concrete, exterior lattice facade that acts as the building’s primary structural system. The design featured solar cells, wind turbines, a geothermal heating system and a rain water harvesting system. San Francisco Museum of Modern Art The highly impressive San Francisco Museum of Modern Art expansion building took up a whole wall with a façade relief specially created to show the design’s styling and innovative fabrication techniques.
The complex design by Norwegian/US practice Snøhetta was created by cutting huge panels in foam by computer controlled wire. Using these foam patterns as moulds, fibreglass castings were made for façade construction.
These were treated with a special coating and were shipped to site using the foam moulds as protection, resulting in a very light and expressive cladding system.
Smoke Dress — Anouk Wipprecht Ms Wipprecht’s 3D printed dress has builtin LED lighting. Should you stand too close to the wearer, the built in sensors trigger the lights to flash, warning the interloper to move away. Should this fail to get a reaction, the dress emits a cloud of dry ice smoke from a necklace/tube. This is either for the wearer to escape into the fog or to irritate the ‘close talker’. Airbus concept plane Airbus set out to revolutionise the structural design of aircraft. The concept plane, beautifully 3D printed and flying over the gallery, has ultra-long slim wings, semi-embedded engines, a U-shaped tail, and lightweight body to improve environmental performance.
The bionic structural lattice was optimised by computer to provide the maximum strength for the greatest amount of natural light through a biopolymer membrane, eliminating the need for windows. Not a design for those who suffer vertigo. Nike analysis and 3D printed trainers Nike is leading the charge in 3D printing. It has convinced superstar athletes to undergo motion capture in their typical sports. The movement is computerised and simulation and analysis done on the pressure and stresses in their footing. This information is then used to create custom shoes, tuned to the way athletes move.
Nike has also started 3D printing shoes and cleats into the soles of football shoes to get optimum traction on the turf. Using Selective Laser Sintering (SLS) with a proprietary material, Nike has created a fully functional plate and traction system in a fraction of the traditional timeframe and at a fraction of the weight. Hacked 3D printer and tattoo machine One of the more unusual items on display at the gallery was a hacked Makerbot 3D printer that has been reappropriated as a tattoo device. Replacing the extruder head with a needle, the device uses a dismembered fake arm attached with some doodles on it. Apparently the device and concept took just eight hours for students to make and a volunteer has already got ‘inked’ by the machine. Renault Twizy For all who remember Sir Clive Sinclair’s C5, this is probably what it should have been. An electric urban two-seater built for lightness and distance, although I am not sure about the lack of windows in the doors and what that would mean in British weather.
We have actually seen one on the road, so there is a market of sorts.
Makers ‘Makers’ Bertier Buyt of leFabShop, and Gary Cige of Usine.io offered advice on 3D printing, fabrication and finding work spaces.
While the noise on the Internet seems to identify the Maker movement as mainly American, it was clear from my visit to Paris that there are many people around the word with the same ambition.
The gallery featured a wall of eight MakerBot Replicator 2, 3D Printers, an Mcor 3D printer and a Roland VersaStudio printer/cutter.
There was a display area for printed parts and some kits for visiting children to assemble. Robot programming An interactive robot with pen attachment. Through a visual interface users can ‘program the robot’ to draw on wooden squares.
Over time these build up to be complex art patterns. It aims to show that in the future Robots will not always need to be programmed prior to performing tasks.
Designviz
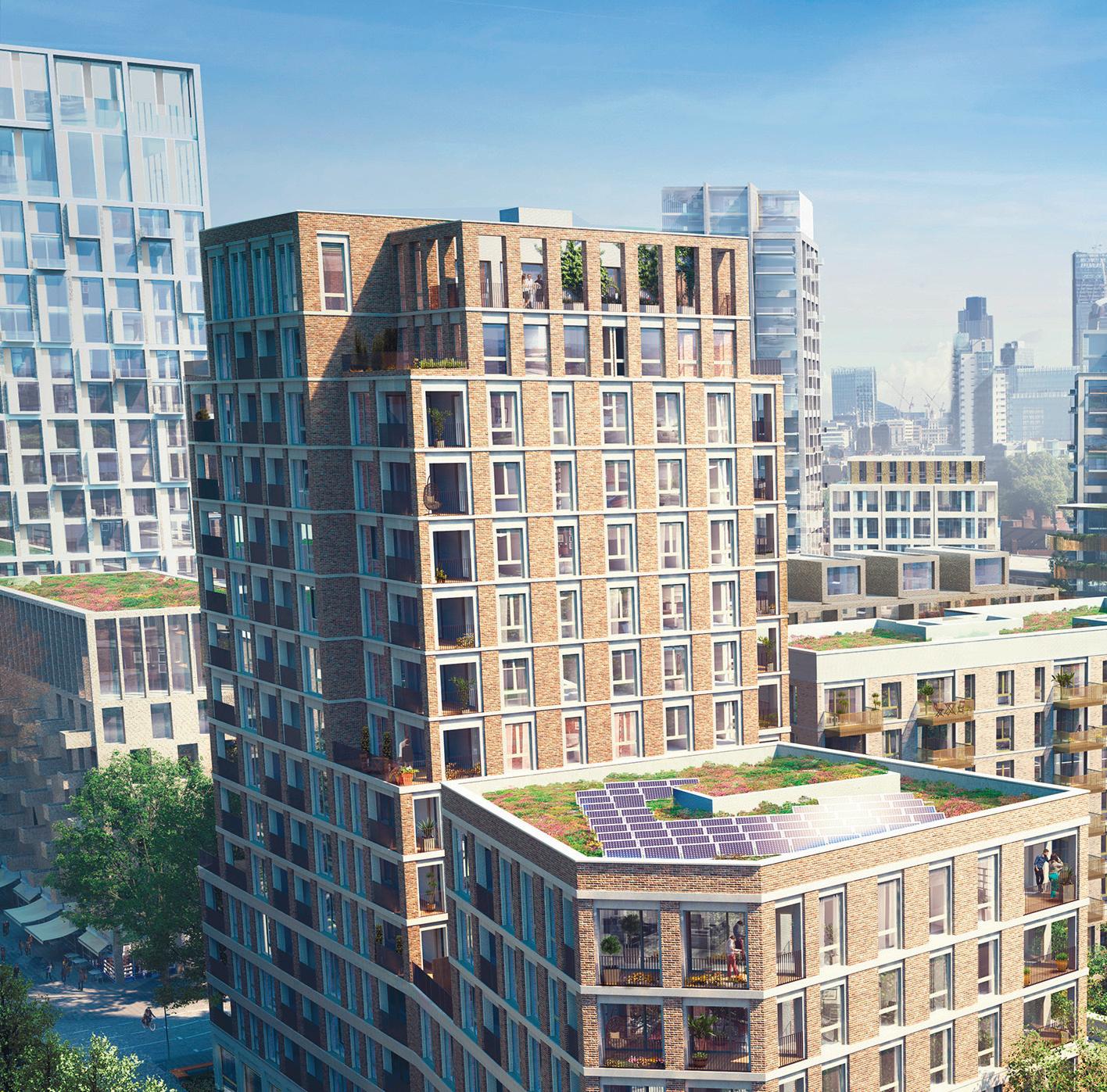
Elephant Park Citiscape Digital
Footage of real-life actors merged with 3D architectural models to create slick a visualisation reminiscent of a short film.
Elephant Park is a new residential site south of the river Thames in London’s borough of Elephant and Castle.
Designed by MaccreanorLavington Architects, the residential project features a collection of modern buildings that range from three to 16 storeys in height, surrounded by communal green space.
Cityscape Digital produced 15 stills and a four-minute film for the project. It worked with a film crew and green-screen technology to add in real actors to the virtual building.
MaccreanorLavington Architects provid-

ed 3D SketchUp models for the main structures, and 2D landscaping drawings, plus further details in 2D CAD. Once the 3D models were built, with details, textures and colours, the green-screen footage could be dropped into its virtual surroundings.
A motion capture system was used to track the cameras that recorded the live footage. This data was fed into the 3D model, which could accurately reproduce the camera paths using the render camera angles, giving natural movement and scaling to the finished video.
By using real people the video was made less clunky than traditional fly-throughs with mannequins, and the resulting effect is more like a short film, something increasingly demanded by Cityscape’s clients.
Cityscape used 3ds Max and The Foundry’s Modo for modelling in 3D, and rendering, and composing animations in Nuke. Modo is most commonly used for animation and product design visuals. Cityscape designers reported a “simplistic, artistic feel” it brings to workflow.
Cityscape found that it can be faster for models to be built straight in Modo working from 2D plans, rather than trying to import and edit sketched 3D files from architects that may have walls or parts missing.
One of the drawbacks to working in Modo is that there is no model history to make detailed changes with. However, Cityscape is adamant this is a ‘quirk’ that the team has become used to within its workflow.
As a trade-off, Modo is popular with designers due to its ability to progressively preview light and textures in the rendering, being able to see what the designer is doing on the fly greatly speeding up the workflow.