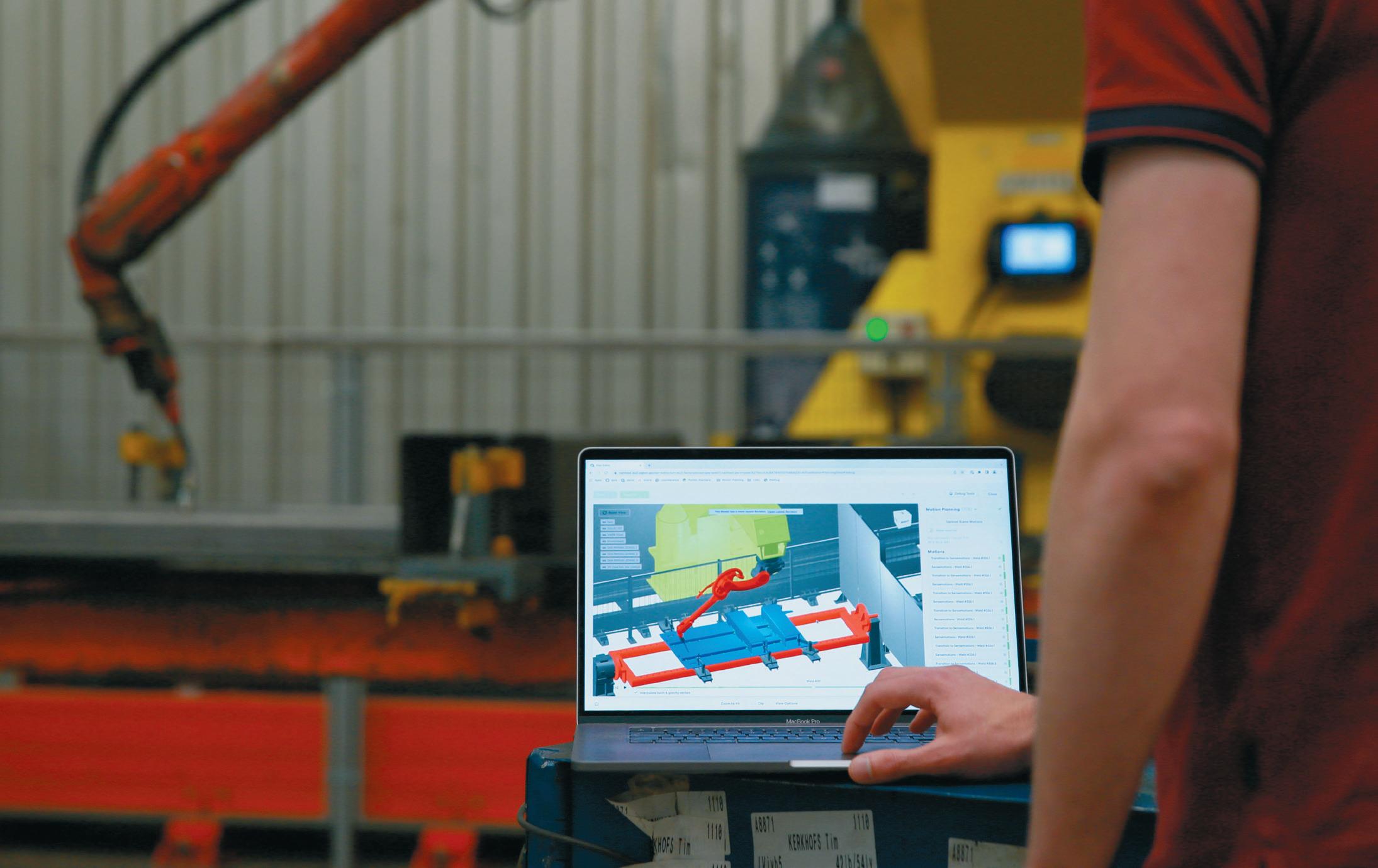
15 minute read
Inside Oqton
AHEAD IN THE CLOUDS
Software, automation and the cloud are all set to play huge roles in the future of manufacturing. Stephen Holmes speaks with Oqton CEO Ben Schrauwen about how the company is bringing together different production software tools within the 3D Systems portfolio, in order to help designers get the best out of existing manufacturing set-ups
The acquisition of Oqton by 3D Systems last year caused a stir, as many feared the former’s impressive brand-agnostic, cloudbased Manufacturing Operating System (MOS) might disappear into the closed shop of 3D System’s technology stack.
The acquisition transpired to be part of a wider change in positioning for the 3D printing giant. The days of 3D Systems protecting its nascent IP for prototyping technology have made way for end-part production technology, ready to be used in diverse shop floor environments.
“It’s much more often used in heterogeneous environments. You need to make the shift to being open, and interestingly, the 3D Systems leadership team is now really pushing for that openness – openness for materials, openness for software, openness for machine
AHEAD IN THE CLOUDS

platforms,” says Ben Schrauwen, CEO of Oqton, which proudly continues to operate under its own banner and remains open to most 3D printing systems.
That brand now includes all of 3D Systems’ software products from prior acquisitions: from Geomagic’s reverse engineering and digital sculpting platform, added back in February 2013, through to Amphyon, bought as recently as May 2021, for SLS build simulation. In short, the portfolio holds a striking range of technologies.
Schrauwen excitedly points out that these fractured tools are now being brought together as a more coherent package, one that is leading the new era of 3D Systems’ openness and expansion.
“In the past, for example, 3DSprint was only for 3D Systems polymer machines; 3DXpert was only for 3D Systems metal machines. We’re taking those products and really allowing them to be used on any type of equipment – particularly with 3DXpert, the one we’re focusing on first,” he says, explaining that support is now added for systems from Trumpf, SLM Solutions, Renishaw and more.
To maintain this neutrality, Schrauwen says a data firewall between Oqton and the rest of 3D Systems has been erected, giving external OEMs reassurance when cooperating with its team of over 300 experienced staff on developing manufacturing software.
BRIDGING THE GAP
Having previously worked at Autodesk, Schrauwen is aware of the trend to package CAD software with other tools, such as CAM and CAE. But he feels that this doesn’t really solve a fundamental issue with manufacturing: that production realities are often very different from what engineers have in their minds. “And so one of the reasons I left Autodesk is really to work on this vision, where in my mind, engineering tools need to be much more closely connected to the production reality,” he says.
The Oqton CEO explains that the first step needed is to capture the production state, “which is really three different systems combined.”
These include: an MOS that captures what the operators are doing and their training levels; the IoT platform and what the machines are doing; and quality management. “These three things together really represent the current state of the production environment,” he says.
Oqton’s slick additive manufacturing automation solution has expanded to production technologies like CNC machining and welding robots, says Schrauwen. “Those are two different manufacturing technologies, where we also demonstrated that AI can lead to 100% automated preparation of these technologies, all from the core Oqton MOS.”
This knowledge can be used at the earliest stages of the development process, allowing teams to design parts that their existing production environments can support. “That’s the underlying agenda. That’s what I’m working towards and that’s why I call it a Manufacturing Operating System. Everything needs to be centred around this production capability,” states Schrauwen.
“Changing bits is easy, changing atoms is really hard. So, changing your production environment is really difficult, whereas as long as you can automate everything, it’s much easier to change a design than it is to change your production environment,” he adds.
“If you want to bring things to market more quickly, you need to design for what you’re able to do today and not for a hypothetical factory that you might have to build.”
LEAVING LEGACY BEHIND
To enable this to work, Oqton has taken the existing 3D Systems desktop software and added it to its cloud, creating a connected platform.
“The expert user can still use the desktop tools, but they are part of an automated workflow that we orchestrate through the web platform,” says Schrauwen, adding that the refresh has allowed for any poor legacy algorithms to be left behind. “We’re really bringing them to the cloud and turning them into services that allow us to automate these processes much more significantly.”
The days of OEMs shunning the cloud are now over, he says. As evidence, he points to the CIOs of automotive giants like Volkswagen and BMW, who have flipped their policies 180 degrees in as little as five years. “Cloud is now the thing they want to deploy first, because they understand that is the only thing long term that is scalable and maintainable, and that will allow them to innovate and move faster. And that’s what we’re really seeing with Oqton. Everything – the whole spectrum – is moving to the cloud.”
Of course, each industry has its own strict regulatory framework for compliance, and it takes a lot for software like Oqton to be able to operate within these mandates. But as Schrauwen says, it also solves many IT management issues for companies that would otherwise have had to do it all in-house. Speaking with Schrauwen, it’s clear that if automation is key to the future, then Oqton might hold the key that opens the factory door to next-stage digital manufacturing. Changing bits is easy, changing atoms is really hard. So changing your production environment is really difficult whereas, as long as you can automate everything, it’s much easier to change a design ’’
(Left) Oqton’s Manufacturing Operating System is designed to handle the automation of manufacturing workflows (Above) Ben Schrauwen is cofounder and CEO of Oqton, leading its mission to enable ‘self-driving’ factories
CUTTING THROUGH THE COMPETITION
» Finding ways to outpace competitors is important. Stephen Holmes visits Guhring UK to learn how adopting digital tools in-house has reinforced its position as a market leader in precision cutting tools
Guhring is a world-class producer of precision cutting tools for manufacturing – the types of cutting and reaming tools used in CNC machines to create end-use parts for building other products.
The company offers customers a huge range of mass-produced tools, as well as custom-designed pieces built to exacting specifications. In an increasingly competitive market, the engineers at Guhring’s Specials Manufacturing Centre in Birmingham, UK, realised the company would need to innovate to maintain its position in the industry. The team initially began 3D printing polymer prototypes, which help guide customers during the design process, checking for fit and increasing buy-in on expensive or complicated projects.
●1 At Guhring, initial 3D CAD models are produced in SolidWorks ● 2 The company has now progressed to 3D printing tool bodies in metal
Parts are designed by Guhring’s team, which works alongside customers to produce tools capable of cutting the metal of particularly demanding features, or even whole parts.
An example might be found inside the cylinder head of an automotive engine, where valve seats are round and valve guides are long and thin. Guhring’s team can develop a tool capable of machining both elements in one machining ‘touch’, dramatically reducing the time needed to produce a finished component.
After producing a 3D CAD model in Solidworks, the design is 3D printed using Guhring’s Markforged Mark Two 3D printer and shipped to the customer. With the polymer prototype, the customer can better assess its potential before committing to metal, even running it in the machine spindle along the CAM-programmed path.
Should a plastic prototype collide in error, it simply snaps – unlike a metal part, which might cause thousands of pounds worth of damage. In this situation, the design process would need to be restarted, with big implications for development times and cost. Using plastic is believed to save around six weeks of development time and the cost of producing a full-metal tool.
However, Guhring felt it could do more with its 3D printing technology. The team was already fans of the company’s Markforged Mark 2, and were fully trained in its Eiger build and process software, so they approached reseller Mark3D to find out what else was possible.
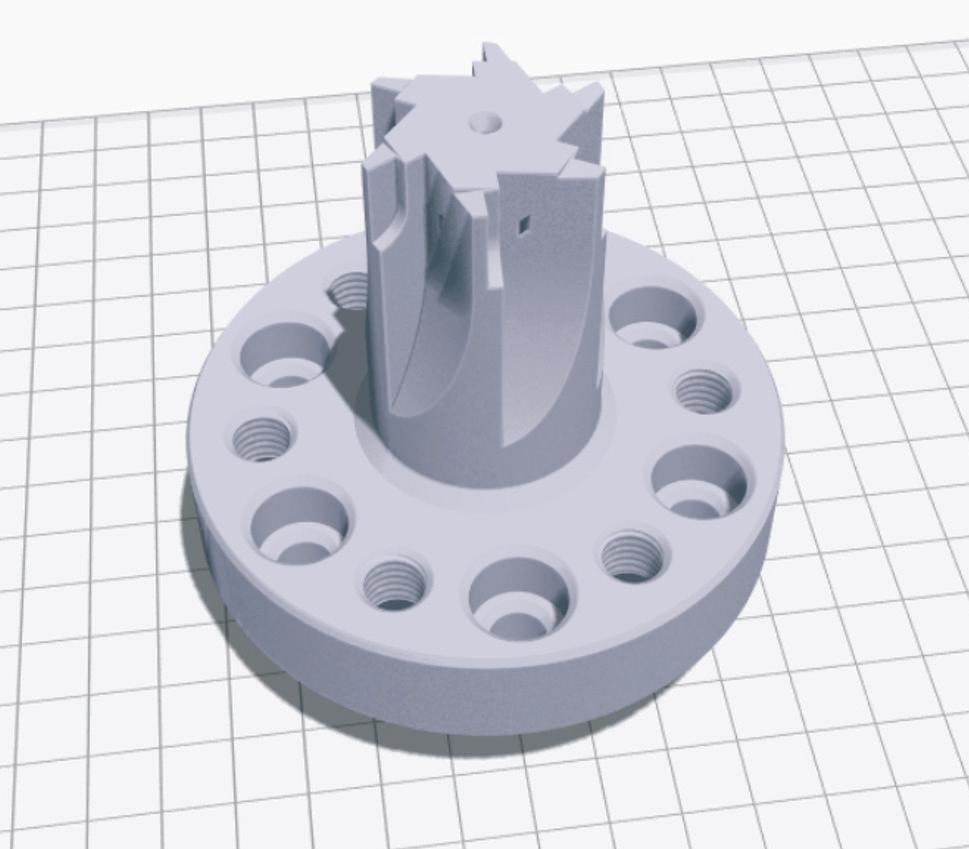
CUT IT OUT
The steel blanks used to create custom tool bodies are painstakingly machined in multiple stages. To these, cutting tips are attached by a skilled Guhring employee, hand-braising a slither of Polycrystalline Diamond (PCD) into a machined pocket on the tool.
Mark3D proposed 3D printing a tool body in metal, using a Markforged Metal X 3D printer. The Guhring team was initially sceptical.
A prototype design was worked up in Solidworks, which instantly got the development team thinking. The heat generated by the machining process is what blunts tips, so in Solidworks, the team was able to place coolant channels
CUTTING THROUGH THE COMPETITION
inside the 3D-printed tool body, directing coolant onto the cutting surface in whatever configuration was needed and prolonging the life of the tool.
The pockets for the PCD tips previously had to be machined and were therefore curved. Now 3D printed as right angles, these offered much better support for the tip. Already accustomed to using the Eiger user interface for the Mark 2 3D printer, the team used it to further develop the tool design for the Metal X, assigning extra wall thicknesses where the part would need to be machined back to meet tolerances and adding a lattice infill that reduced the part weight by nearly 40%.
The prototype part was sent to be 3D printed and post processed at Mark3D on the Metal X, an FDM process that prints a green part from filament, before it is post processed and sintered.
For the Guhring prototype, the process means a 15hour print time, followed by post processing – a 12-hour wash and four hours drying. Then, it is sintered in the benchtop Markforged oven for 27 hours, resulting in a 99.89% solid metal part.
“What’s important to remember here is that Guhring is one of the biggest sintering companies in the world,” says Mark3D managing director Ian Weston, noting that it has ovens so large that it drives forklift trucks into them. “So, when we introduced the [Markforged sinter oven] to them as a technology, they just smiled!”
With the PCD tips braised into place, it was time for testing the part on a milling machine in front of the Guhring team. The first test was over a favourable vertical cutting path – drilling down into the stock material – and it worked as well as a steel part.
Growing in confidence, they decided to pocket out a hole, putting the tool under increased sideways load, where any kicking could snap it. The tool continued to work diligently, clearing material along its path. As a final test, the operator cranked up the spindle speed as far as it would go.
Everyone was over the moon, says Weston, given that the tool survived, outperforming everyone’s expectations, and making his client the first in the world to do this with Markforged technology.
We were delighted that the tool was able to exceed everyone’s expectations ’’
Guhring is one of the biggest sintering companies in the world and can drive forklifts into them. So when we first introduced the desktop Markforged sinter oven to them, they initially just smiled ’’
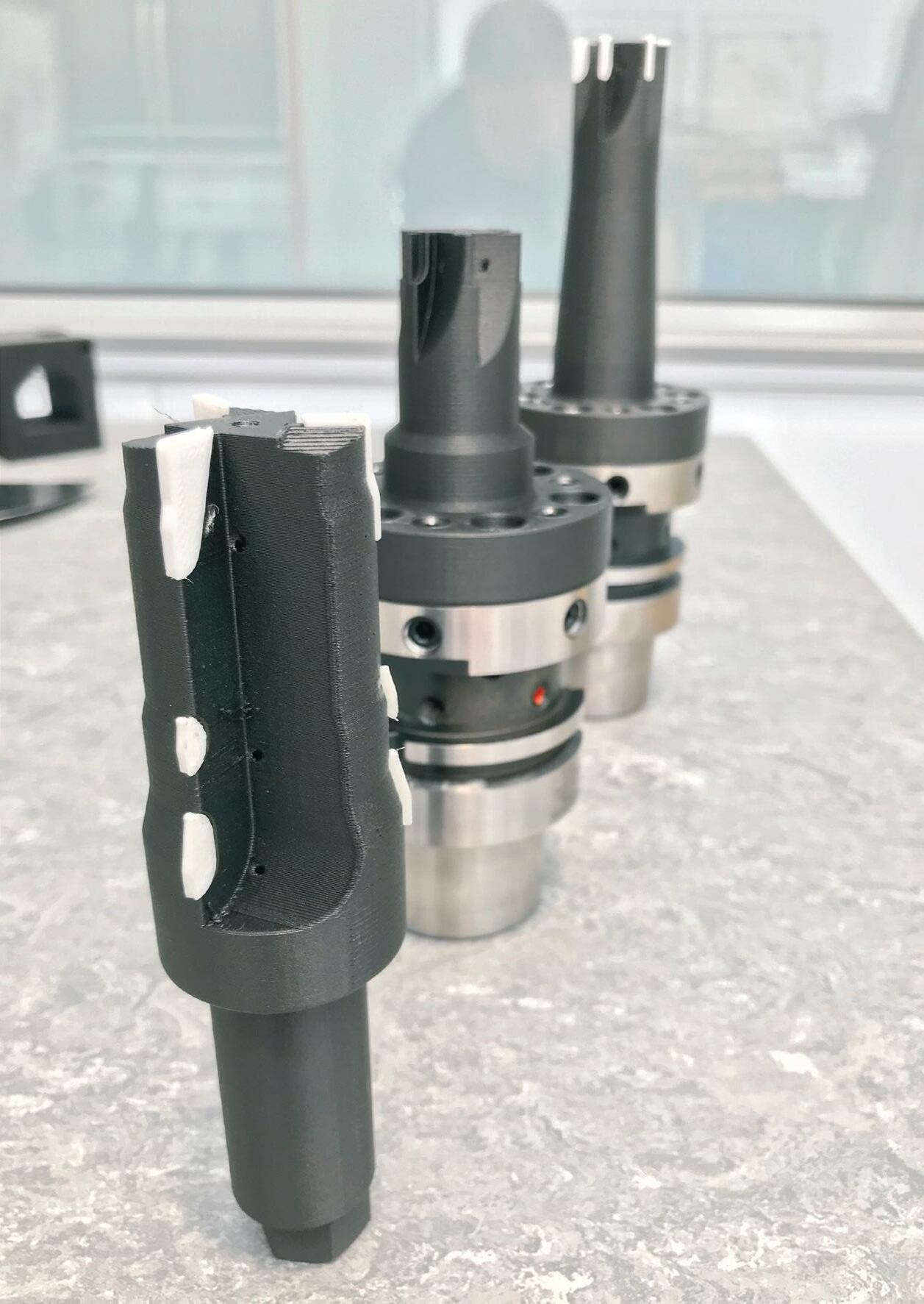
CHANGING OPINIONS
All the Guhring staff still recall that first test as a groundbreaking moment. Since then, the development of further 3D-printed parts has been fast, with new benefits being unearthed.
By reducing the weight by some 40%, there’s less load on the machine tool, extending the life of the CNC machine. Tool designs previously were capable of machining 12 to 13 parts per hour now get through 40 parts and can still be returned to Guhring to be retipped with new PCD, rather than needing an entirely new tool, saving money and waste.
The H13 tool steel printed on the Metal X comes out of the oven case-hardened, and early reports from customers suggest that it lasts longer than machined and heat-treated steels.
The ability to 3D print tools with more freedom means that designs have become more elaborate. This includes an incredible design for a drill that, due to a hollow drum through its centre, automatically ejects the swarf as it cuts it from inside of an engine cylinder.
Despite what appears on paper to be a long post processing methodology to realise the final parts, compared with traditional manufacturing, lead times have dropped from over six weeks for a new tool, down to a week or two.
Equally, R&D work is less costly and less error-prone, giving the team confidence to try out new ideas.
Guhring’s custom work is winning back old clients and drawing the attention of new ones, while helping increase the visibility of the company’s existing products and services across the board – all thanks to its team being willing to pioneer a new technology to gain a cutting edge.
(Above) Prototype polymer tools built on the Markforged Mark Two 3D printer (Below) Tool weight is reduced by around 40%, allowing more design freedom

Lightweighting might be the focus of major hype right now, but its downstream impact promises to be truly exciting, writes Stephen Holmes, who’s admiring some lattices before they get hidden from public view
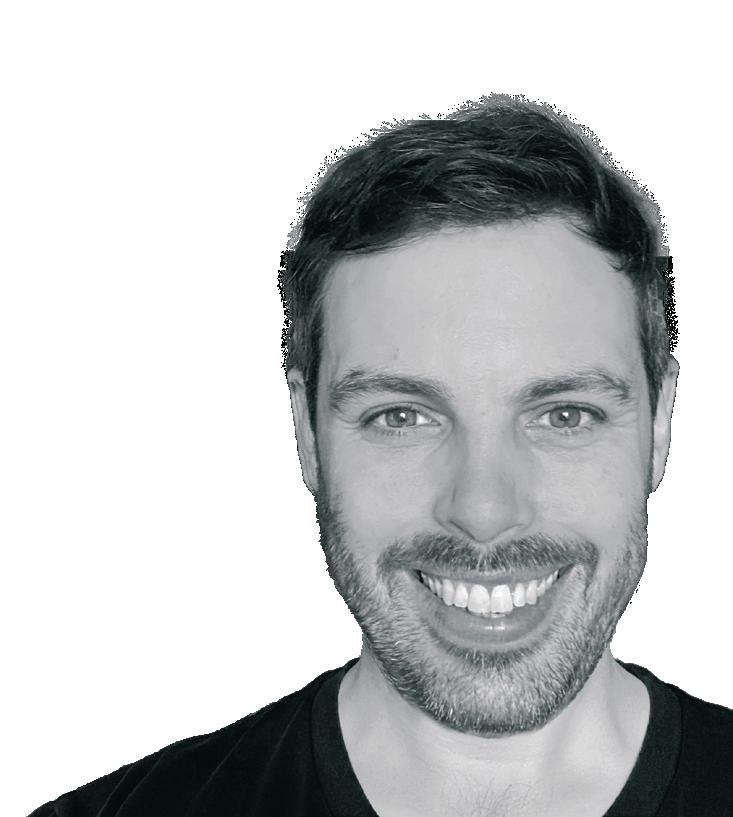
Lightweighting is currently a sexy engineering topic, already mentioned several times in the pages of this issue. That’s because designers have always looked to use less material and make products lighter — but the combination of today’s optimisation technology and additive manufacturing has thrown this mission into overdrive. Everything must be lighter, just like everything had to be smaller in the 1990s, curvier in the 2000s and thinner in the 2010s.
In fact, ‘topology optimisation’ and ‘lattice infills’ are now terms you might find in a review of a consumer product, in much the same way as its author coos over composites, user interfaces and connectivity. Lattices are now much-hyped features of shoes, saddles and car seats.
With their almost-butnot-quite organic forms, parts that are built using simulation-driven algorithms are visually so outside of the current norm that, whatever your thoughts on them in terms of styling, there’s no doubt they catch the eye.
But for me it’s all a bit ‘Dieter’ — a case of function over form. That’s why some of the less flashy uses of lightweighting are actually the most impressive, and it’s exciting to think of the impact they will have. LATTICES TAKE THE STRAIN Take, for instance, the case of Guhring’s drills, featured on p54. Here, a lattice-filled design helps maintain the part strength, but the resulting weight loss has even greater impact downstream.
A lighter part puts less strain on the CNC machine on which it’s used, meaning faster machines operating at less stress. If this sort of tool body becomes commonplace, it will in turn have an impact on CNC machine makers, which could find that they are able to reduce the material needed to build machines, lowering costs.
One of my favourite recent uses of lightweighting is to be found at Ocado Engineering, the technology arm behind the UK online grocery fulfilment company. Earlier this year, the company announced it had optimised the design of its latest 600 Series robot, using HP 3D printing to produce more than 300 of its parts. As a result, the robot is five times lighter, making it significantly faster at picking up your avocados and sourdough, and more cost-effective to manufacture and run than previous models.
The downstream effects are that the lighter robots make the planning of Ocado’s fulfilment sites easier. The lighter robots use less electricity, boosted by reduced refrigeration requirements, since faster robots move products around before they lose their chill. The gantries on which robots and stock move can be lighter too, meaning Ocado’s warehousing operations can move into a wider variety of buildings. While the trickle-down of technology from Formula 1 cars to family hatchbacks is a slow one (aside from some dubious examples like BMW’s topology optimised boot hinges), agricultural and heavy machinery makers are ahead of the curve.
If it’s traditionally big, heavy and slow, then the performance benefits of lightweighting are much greater than on an already skinny supercar. And as long as they maintain the necessary strength to plough or shovel all day, then big lumps like earthmovers and tractors get payoffs that are measured in more than potatoes.
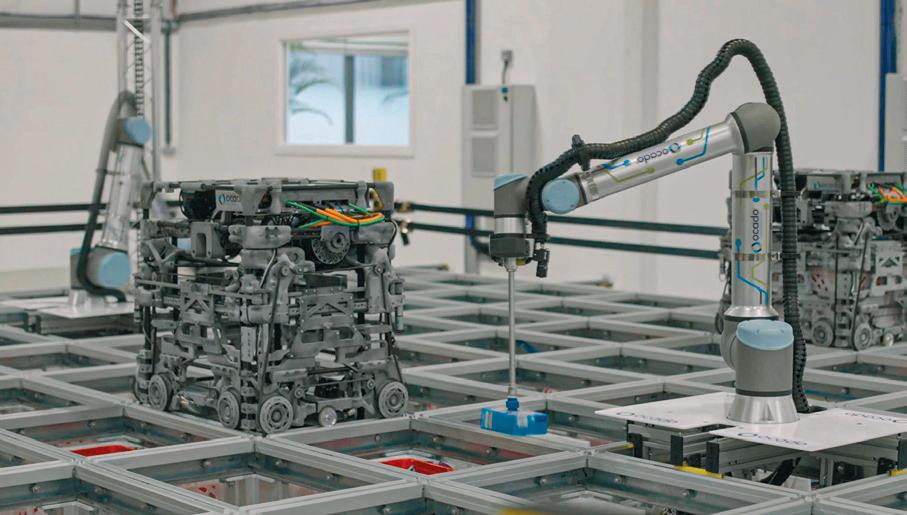
HYPE AND HEYDEYS
Soon this ability to cut weight using innovative algorithms and additive processes will lose its novelty. We’ve seen a similar change of image with 3D printing: in its 2014 heyday, we were promised we’d be 3D printing a spare kidney in time for the weekend on our kitchen tables by now.
But today, 3D printing is working away behind the scenes, helping manufacturers to build custom jigs and fixtures on their factory floors, saving them huge sums of money in the process, and slowly graduating to building end-use parts, as calculations around cost, efficiency, quality and assurance all begin to add up.
In a similar fashion, many of the great successes of lightweighting are likely to be hidden away from mainstream praise, all the while contributing to better products.
So, while many of us flinch when looking at optimised designs and naked lattices laid bare for all to see (and a nightmare to clean), we should probably be enjoying this odd period in the timeline of design.
Lightweighting robots at Ocado is set to have a huge effect on productivity and energy efficiency (Credit: Ocado Engineering)
GET IN TOUCH: After managing an issue delving deep into algorithmic design, Stephen will now return to renovating his knackered 1870s house. If you hear anyone insisting “the Victorians were great engineers”, then feel free to bring them round for a look. On Twitter, he’s @swearstoomuch