
5 minute read
Nimble parametric practice: the digital toolbox
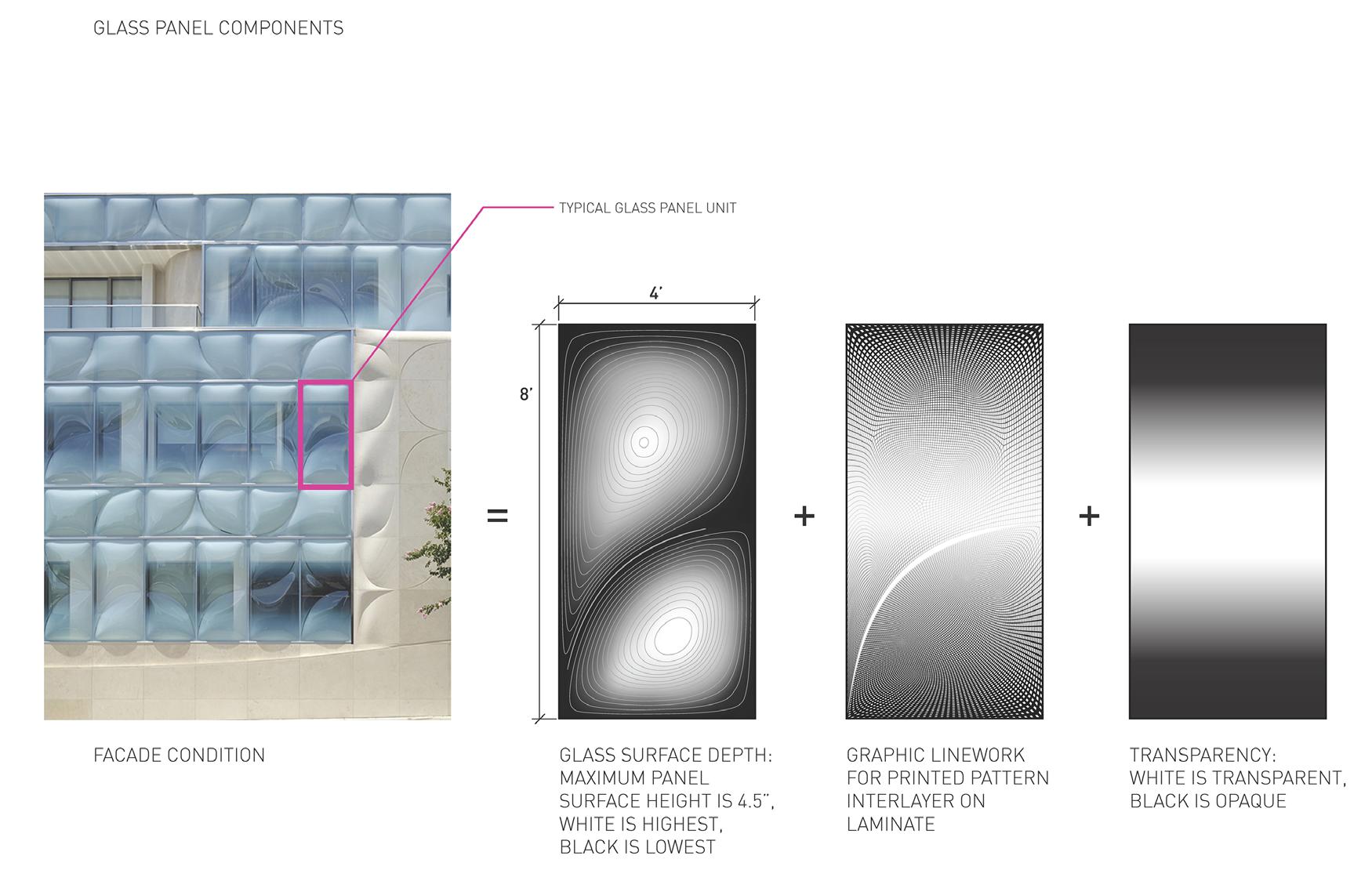
The design of each façade panel comprises two layers of slumped glass and a printed PVB interlayer with a graphic pattern and a transparency gradient.
photo by Bruce Damonte; drawing by Belzberg Architects
Although parametric design has been part of the architectural lexicon for some time, the connection between education and practice can still seem distant and obscure. Each project is unique, with its own challenges, and it can be daunting to know when and how best to apply digital design tools. As a smaller firm, we have taken an opportunistic approach, encouraging the creative use of our “digital toolbox” to enable, enhance, and proliferate solutions in small or large ways. Our nimble use of parametric design principles demonstrates the variable application and potential of these tools, proving that the tools themselves do not need to dictate the process or outcome, parametric or not.
In 2014, we completed the new headquarters for the Gores Group, a 135,000-square-foot renovation of an existing office building at the western gateway of Beverly Hills. Fundamental to the success of this project was the transformation of the building’s three-story façade, for which we developed a custom, non-repeating glazing system comprising bespoke slumped glass with a printed PVB interlayer. The design intent and various parameters of this part of the project proved to be an excellent opportunity to test the efficacy of several digital tools not only in the design phase, but also in the direct-to-digital fabrication of the final product as well.
One parametric design exercise for the glazing included creating the pattern of the slumped-glass panels across the façade. In the initial design phase, we limited the number of unique panels to 10 or fewer for budgetary reasons and to streamline fabrication and installation, and we used only three discrete open-frame molds to slump the glass using gravity. To take full advantage of the open-frame mold and the variable depth this allowed, we used color-embedded meshes imported from Maya to control the depth of the curvature. The meshes were painted in Maya, and the Grasshopper plug-in for Rhino interpreted the color information from the mesh vertices to produce the Rhino iterations that helped us develop and finalize the design. We also used Grasshopper to adjust the rotation, orientation, and sequence of the panels very quickly in order to compare design options ranging from hyper-organized to randomized.
Additionally, Grasshopper was used to develop the pattern on the laminate interlayer. We adjusted the gradient, opacity, and design of the printed pattern which was used to accentuate the curvature of the slumped glass panel it sits in. The Rhino file produced the closed-curve geometry that was then exported into Illustrator, where opacity gradients were applied to achieve the desired effect. The final Illustrator files were delivered directly to the fabricators for printing and used to produce the final glazing.
Finally, Grasshopper was also used to create elevations with panel labels that served as a key for the installers. Together, these digital tools allowed us to develop the design entirely in 3D and easily translated our design vision to our collaborators (i.e. the fabricators and general contractors). It also provided inclusive and efficient means of collaboration, with which the input and feedback from our team were applied and developed through rapid iteration and their effects understood in real time.
For Threads, a new seven-story commercial building we designed in Mexico City, we sought to re-assess the role of the façade in office buildings and designed a series of vertical fins that weave in and out of the structure, appearing to penetrate the glazing as it shapes interior niches and exterior balconies. This series of triangular members runs the height of the project, dissolving the solidity of the building envelope. The project’s origins were in Maya, where the curvature of the fins was developed and modeled as a 3D mesh surface. The drive curves were extracted from that mesh and exported to Rhino, where, using Grasshopper, the curves were extruded as triangular geometries and their 3D forms defined. Here again, the use of Grasshopper allowed us to adjust the proportion and size of the fins as parameters changed during the development stage. Although the fins appear to be contiguous, each vertical line is divided by floor, which we modeled manually in Rhino taking into account construction tolerances. Using Grasshopper, we translated each one-story segment from the
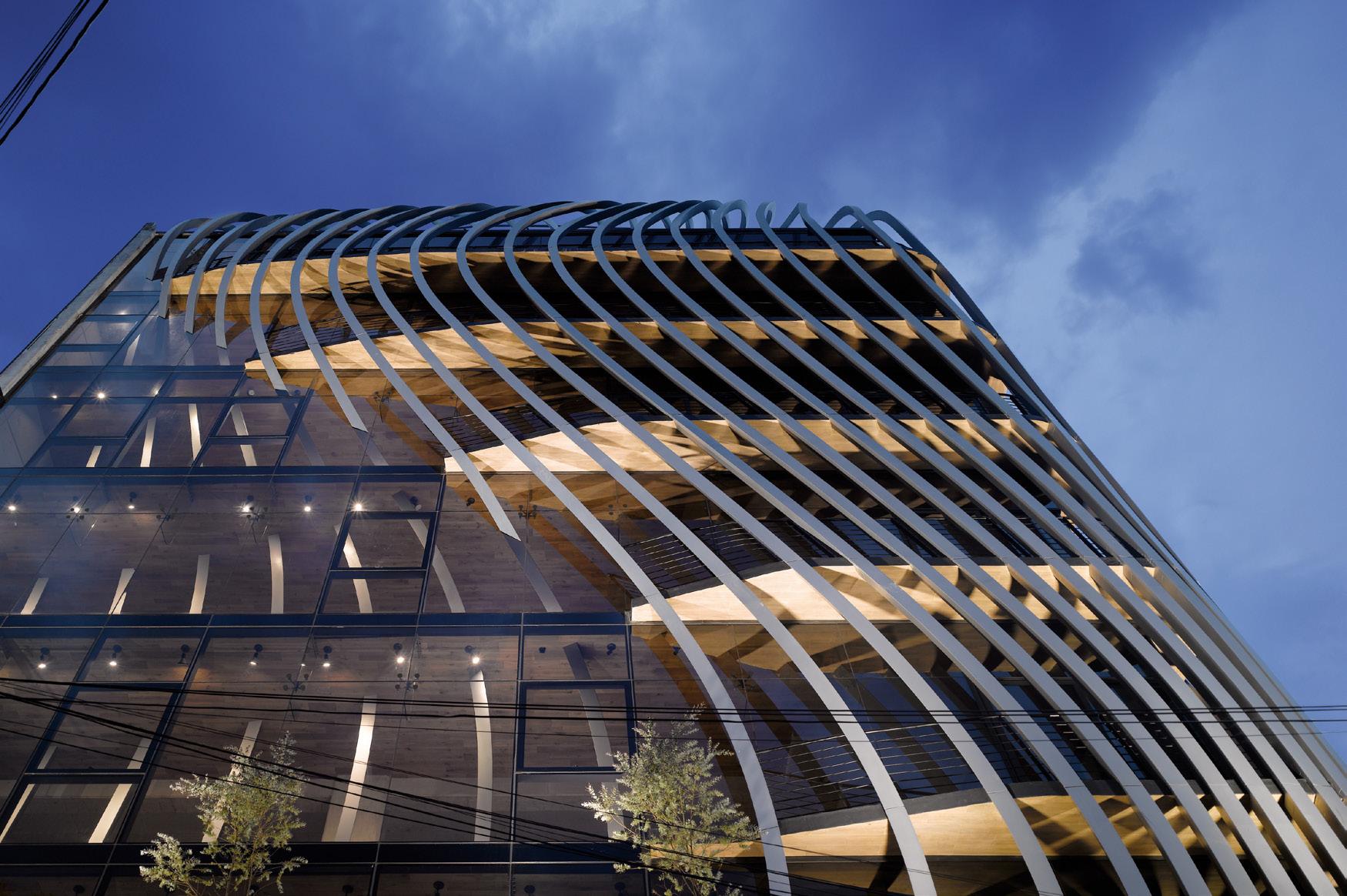
The fins of Threads appear to penetrate the glazing and floor plates.
photo by Roland Halbe
3D model into its unrolled 2D components, creating the file our fabricators worked from to make the fins. The software also enabled us to output critical information related to installation, i.e. the exact rotation of the triangular members. Our digital design methodology was critical to the success of our crossborder collaboration, again allowing for an efficient feedback loop and rapid iterative process and creating a bridge between the design, fabrication, and construction processes.
As a design firm, parametricism is not our focus. Instead, we believe in developing a digital toolbox that allows us to enhance our ability to problem solve and develop creative solutions for our projects, clients, and collaborators. Early analysis on a project helps identify which parts of the process are best suited for a parametric approach — from fabrication to design documentation, for instance. Like any kit of parts, once you familiarize yourself with the various tools at your disposal, they become part of your arsenal and can be deployed where best suited. We encourage you to use the tools to your advantage; small or big, they can be used to elevate the design, fabrication, or construction process.

Leese and his team were able to output critical details from Grasshopper to ensure a high level of precision in the installation of the fins at Threads to achieve the appearance of continuity.
photo by Roland Halbe
Author Bios:
Kristofer Leese Leese excels in parametric design, advanced modeling and scripting and has been developing his design practice at Belzberg Architects since 2011. Leese most recently presented at the Int’l Conf. of Advanced Building Skins in Bern, Switzerland.
Carol Choi is a Director and Technical Writer at Belzberg Architects. She helps contextualize and translate complex design ideas in visual and written form for a broad audience. Her work has been published in Europe and North America and she is currently overseeing a forthcoming Belzberg Architects monograph to be published by Rizzoli New York.