
8 minute read
Ductile iron pipes prove their worth in hydropower projects [ TECHNOLOGY
from zek HYDRO 2021
by zek Magazin
DUCTILE IRON PIPES PROVE THEIR WORTH IN ALPINE HYDROPOWER PROJECTS
More than ever before, hydropower plant operators are choosing sophisticated pipeline solutions for their penstock. Indeed, the ductile cast iron pipes made by Tiroler Rohre GmbH (TRM) have been a trusted solution for small-scale hydropower plants for almost 60 years. Over time the company has installed a total pipe conduit length of around 1,200 kilometres; or the equivalent of a pipeline from Milan to Hamburg. TRM’s ductile iron pipes have been installed at numerous power plants in recent years, guaranteeing durability, good commercial value and operational reliability.
Ductile iron piping forms the technical backbone of several modern hydro-electric power stations in Switzerland, Germany, Austria, Italy and Scandinavia. The long-standing Tyrolean manufacturer TRM has become an indispensable option for solutions suited to topographically tough terrain.
LAUFENBERGERBACH HYDROPOWER PLANT Laufenbergerbach hydropower plant in Carinthia is a recent typical reference project. The station commenced operation at the close of last year. The Tyrolean piping specialists at TRM provided trusted DN400-format ductile iron pipes for the approximately 500 metres long penstock in Radenthein. The connections prevent lengthways pressure slippage and the new pipe conduit can transport up to 208 l/s to the machine room. Large sections of the routing for the penstock passed through a densely-populated residential area, necessitating the installation of several elbow sections. Furthermore, the routing had to navigate multiple obstacles. It was necessary to core-drill through an approximately 2-metre-thick protection wall, 3.5 metres below the surface, right by the water collection basin. As the pipes were being installed it again became clear how essential simple pipe handling is for commercially viable installation. The patented restrained VRS®-T connections facilitate rapid installation, making it possible to complete whole sections of pipeline relatively quickly. In the case of the Laufenbergerbach station, the pipeline was completely installed in under four months – and the pressure test was passed at the first attempt.
photo credits0: Pliessnig The penstock at Röllbach hydropower plant in Switzerland is around 1.2 km long and built using ductile iron pipes made by the industry specialists TRM, and connector-secured to prevent lengthways sliding.
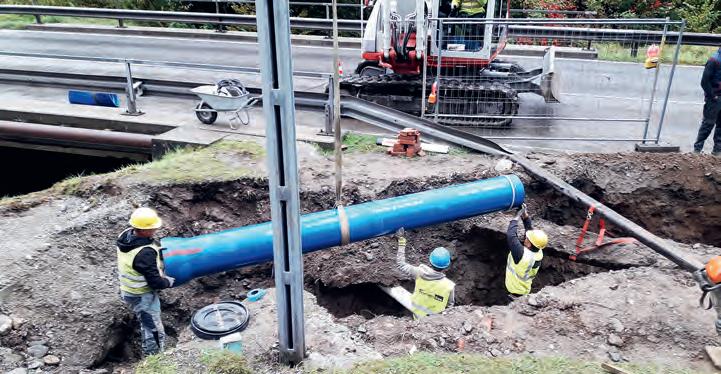
photo credits: EW Martin Zeller AG
The penstock of Laufenbergerbach hydropower plant was rerouted through a densely populated residential area. RÖLLBACH HYDROPOWER PLANT Another reference project of the past few months was completed several hundred kilometres further west in Röllbach, in the Swiss canton of St. Gallen. The project to rebuild and modernise the small-scale hydropower plant was implemented using high-pressure DN400 and DN500 piping along a 1.2-km route in extremely difficult terrain. While most of the original welded steel pipe conduit ran above ground, the new ductile iron piping was devised to run underground all the way. Due to the extremely rocky nature of the material under the surface, it was necessary to blast open a channel along around 80% of the route. The decision-makers chose a solution involving an outer coating of cement mortar to ensure the pipes were installed safe and secure in the rocky ground, thus protecting the penstock from damage often caused by such underground conditions. The inaccessibility of the project site in Flums meant that in the summer of 2019 almost all the pipes had to be manoeuvred into place by helicopter. A transport helicopter was deployed to convey the individual pipe sections from
While installing the pipe sections in Flums a heavyduty helicopter was used as a means of transport and as a lifting device.

photo credits: EW Martin Zeller AG
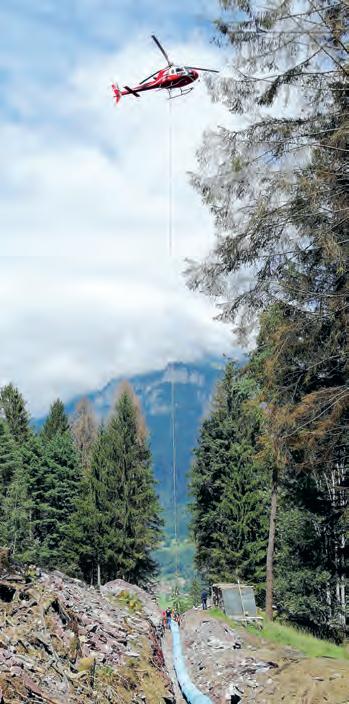
the depot to the point of installation. Installation was implemented as follows: First of all, a 200-m trench was excavated for the pipeline, after which the helicopter brought the individual lengths of pipe to the assembly staff on site – and was also used to lift and ease the pipes into position, so each only had to be handled once. This meant the entire turnaround procedure involving the helicopter, from picking up the first section of pipe – delivering and positioning – returning to the depot for the next, took around five minutes. VRS®-T connectors ensured each section could be rapidly attached, and secured to prevent slipping out of position. Subsequently, the pipe trench was filled in again with an excavator. The plant has been commissioned last March. It can process three times the previous volume of water and supplies the canton of St. Gallen with around 2.65 GWh of clean, green electricity.
DUERNBACH I HYDROPOWER PLANT As well as in the Swiss village of Flums, the changeover of the high-pressure descent pipeline from steel to ductile iron was also successfully achieved in the Pinzgau region of Salzburg Province. The operators of the environmentally friendly electricity producer, E-Werk Lechner, whose Duernbach I power plant had been in operation since 1948, had been faced with a problem. Several small leaks had already begun to appear over the years, a problem that had been ameliorated by installing spiral pipes. However, not long back disaster struck as a pipe burst in an extremely inaccessible section of the penstock, forcing the management to take a fundamental decision to replace the over 60-year-old steel pipeline with modern, long-lasting high-pressure ductile iron piping – from TRM. The main and most important reason given by the Salzburg plant’s operators for this move was the speed at which the pipeline could be replaced. The faster the pipes were installed, the shorter the downtime for the plant. Indeed, provided installation is coupled with the requisite know-how, TRM’s piping system can guarantee remarkably reduced installation times. This was observed in practice when the plant operators worked as a family to complete the first 120-m section of pipeline channel in just three days. The section of pipeline in question was situated in some of the steepest terrain along the entire penstock, on a hillside with gradients of up to 50%. One positive effect became immediately apparent as soon as the initial section was successfully installed: The machine room manometer showed a 0.2-bar pressure rise! This confidence boost provided the plant operators with even greater motivation for the installation of the remaining piping along the route; which of course was also implemented using TRM’s iron ductile pipes.

PISCHINGBACH HYDROPOWER PLANT The Prince of Liechtenstein Foundation also chose to invest in environmentally and temporally sustainable solutions. In the Styrian village of Kalwang the local council authorised the building of the first small-scale hydropower plant on the previously unexploited Pischingbach river. The plant went online just a few months ago. There were plenty of reasons for the management to choose TRM quality for the construction of a total of 1.6 km of penstock, but the real deal-makers were the high-pressure tolerance and speedy availability of the products on offer. The requisite rerouting of the pipeline channel meant navigating a high point and a low point, in turn necessitating air extraction and draining. The entire DN400 pipeline was installed using the patented slide-secure VRS®-T system connectors. A metal bolt and a weld bead at the narrow end of each following pipe section create a connection that can be subjected to extreme forces and pressures. Depending upon the diameter of the pipe sections, the infrastructure can cope with up to 200 kN of traction. What’s more, this solution also renders the inclusion of concrete abutments obsolete, significantly accelerating the speed of installation achieved by the site team. One key benefit for the operators of the Pischingbach power plant was the possibility of conducting installation via the trusted ‘open & close’ method. So, particularly in poor weather conditions, the channel was only excavated for a single pipe section, and subsequently re-filled. This helps to minimise the risk of landslides and allows the original earth to be filled back in very quickly, in turn facilitating the rapid regrowth and recovery of the local vegetation. All pipeline installation work was conducted in 2019. The new Pischingbach power station has been in nor-
Routing of the 1.6-km DN400 penstock for the Pischingbach power plant.
photo credits: Stiftung Fürst Liechtenstein The operators of Duernbach I in the Salzburg region managed to route the entire pipeline themselves.
photo credits: EW Lechner
mal service since the spring of 2020, and in a regular operating year can produce around 1.2 GWh of clean energy.
DURABLE, SAFE, SUSTAINABLE The ease of installation, stability and flexibility of the pipes, as well as the tried and trusted collar connectors, were decisive benefits that won over the operators of the small-scale alpine power station. Another factor influencing the decision was the extreme longevity of ductile iron pipes. One pillar of this durability is the anti-corrosive protective layer on the surface. TRM now provides a large portfolio of coatings for a broad range of requirements, types of burden and underground conditions. Active protection from corrosion is applied to the outer surface in the form of a thermal zinc spray coating. A passive corrosion guard is provided by applying an additional protective layer. Coatings in common use include sealing layers made of polyurethane or epoxy. Another frequently used coating solution is cement mortar cladding – a very suitable means of material protection, particularly in harsh terrain and rocky earth. Moreover, it’s undeniable that the stability of modern penstocks has also become a legal insurance issue. Hence, it’s a logical consequence to observe that operators are also placing their faith in the tried and tested VRS®-T connections – a system that is restrained against lontudinal forces can be caused by pressure and stress dynamics. Despite being rigidly resistant to pressure, the system is extremely flexible. Such conduits can survive subsidence or landslides intact. 100% of the material used for TRM’s ductile pipes comes from recycled waste steel for a positive environmental impact and exceptional sustainability – aspects Christian Lechner, operator of the Duernbach I plant confirms are steadily growing in importance for hydroelectric power plant managers: “We’re an Austrian company with strong roots in the area and have established a reputation for sustainable activity over several years, so it only logical that we would choose TRM pipe systems.”

Pipe bridge constructed for Laufenbergerbach hydropower station with TRM iron piping.
phto credits: zek
TRM PIPE SYSTEMS
Secure water supply. Thanks to reliable partners.

Safe water supply. www.trm.at