
10 minute read
Hyundai Adds to Wheeled Excavator Line-Up
news Hyundai Adds HW150A CR to Wheeled Excavator Line-Up
Hyundai Construction Equipment is building upon the success of its growing A-Series range of wheeled excavators, with the launch of the compact radius HW150A CR.
Following the launch of the larger HW170A CR, the HW150A CR promises to become the flagship of the A-Series wheeled excavator range, in answer to the growing demand for a more utility and service oriented wheeled machine in the 15-17 tonne segment. The HW150A CR joins the established HW140A, HW160A and the compact radius HW170A CR in the Hyundai lineup, providing a specification and operating weight to suit every application. The larger HW210A sits in a class above, though it delivers the same combination of controllability and productive power. Already a popular choice with leading national rental businesses and contractors, the Hyundai A-Series machines have taken operator comfort and control to a new level, delivering a highly productive excavator, with attractive total cost of ownership for customers. The HW150A CR uses the same Cummins B4.5 diesel engine as the HW140A, HW160A and the HW170A CR, with an output of 129kW (173hp) at 2,200rpm. The engine drives a Bosch Rexoth load sensing hydraulic system and a fully hydrostatic, four-wheel drive powertrain.
Stable construction
As with the other models in the A-Series range, the upper structure has been repositioned on the lower chassis, contributing to a reduced tailswing, while increasing stability during travel and improving lifting and digging capabilities. A new swing bearing design offers improved stability and durability, while new, lighter mud guards, cover the whole wheel, turning with the wheel when steering. Safety valves are available on the ram lock cylinders on the front, steering axle. The extremely short swing radius allows the machine to confidently work within confined job sites, without risk of impact. The HW150A CR features an automatic digging brake, that locks the front axle oscillation and the service brake, allowing the operator to start work as soon as the machine stops travelling. The lower attachments, including dozer blade and front and rear outriggers, are fully interchangeable. The rear parallel-frame dozer blade has an increased range, delivering additional stability while digging or lifting and boosting productivity in site clearance. The additional reach also provides space around the wheels for maintenance. Preparation for a towing hitch is offered as an option.
Cab design
All A-Series excavators benefit from the latest Hyundai cab design, with improved steps for easy access. The cab features increased glazing on the door and roof hatch, for improved visibility and the upper and lower windscreen glass comes with larger, parallel wipers for improved coverage. The cab features Hyundai’s 8” touchscreen display, for access to all machine functions and controls settings. There is also a Jog Dial Module and function switches, to navigate menus within the touchscreen. Despite its compact radius dimensions, the engine cover size has been reduced, to further improve visibility to the rear of the machine. Wheeled A-Series models feature Hyundai’s Advanced Around View Monitoring (AAVM) system, that uses cameras to provide the operator with a 360 view of the machine on the in-cab monitor. The system includes Intelligent Moving Object Detection (IMOD) alerting the operator to the presence of other workers or objects within a 5m range of machine operation. The steering column has been improved, with three-way adjustment that allows any operator size to get comfortable. Proportional joystick controls are standard and joystick steering with directional control can also be specified as an option. All working functions are at the operator’s fingertips, with ramlock switches and directional control integrated into the lever head. Cruise control and an optional ride control function are available for smoother travel, with less operator effort required. The excavator boasts a revised pedal layout and an improved floor mat to make it easier for the operator to clean the cab floor. Forward, neutral and reverse can now be accessed through a switch on the servo lever, rather than through an additional pedal, further improving space on the cab floor.
NI Water Completes Major £10m Investment in Belfast
NI Water has completed a £10m programme of work at Belfast Wastewater Treatment Works. It is the first phase in a continued programme of work at the plant, which will protect the environment, support development and aid economic growth in the city.
The extensive project completed by Murphy Dawson-Wam JV, with McAdam Design providing project management support, saw the construction of two new treatment tanks at the Duncrue Road site – equivalent in volume to six Olympic-size swimming pools – to cope with current and shortterm future wastewater requirements. Mark Brownlee, Senior Project Manager at NI Water, said: “Due to constraints in investment over the past 20 years, many parts of the wastewater and drainage infrastructure serving greater Belfast are now having to operate at or over their original design capacity. “The two new treatment tanks that have been completed here will provide much-needed additional secondary treatment capacity and augment the existing process to ensure that the discharge to Belfast Lough remains compliant with Northern Ireland Environment Agency standards. The new assets will also facilitate essential improvements within the associated sewerage networks and will enable maintenance works to be undertaken in the other treatment tanks at a future date. “This significant investment by NI Water will ensure our key wastewater treatment works for Belfast remains compliant, in advance of the next phase of the main ‘Living With Water Programme’ commencing.” Contained within a site area of around 180,000 square metres (almost 2 million square feet), Belfast WwTW was designed to treat a domestic and trade population equivalent of 290,000. The current works was built in 1991 to replace the original Victorian works which dates back to the early 1900s. The extended wastewater treatment works will now have the capability of accommodating a population equivalent of almost half a million people.
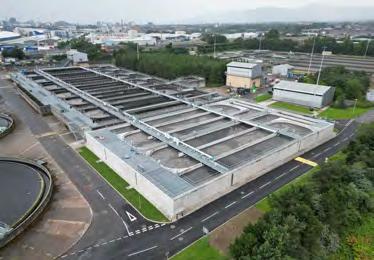
Up until a few years ago, the HiDROMEK brand was not at all familiar in this part of the world, even though the machines work in more than 100 countries on six continents; indeed, by the end of 2020 more than 50,000 Hidromeks had been sold around the world, a figure that continues to rise significantly as operators become more aware of the build quality and reliability of this multi award winning brand.
And those awards keep coming. This year alone Hidromek has won prestigious IF Product Design and Red Dot awards. So what is it that attracts awards and customers? And why are more operators here adding Hidromeks to their fleets? Let’s look at three of the manufacturer’s most popular machines. Although only relatively new to the manufacturer’s product portfolio, the latest member of its backhoe loader family, the HMK 62 SS, has been designed to exceed customer expectations, offering high performance, versatility, operational comfort and safety. It is a compact but reliable and strong machine even in the toughest conditions and with long working hours – and it can accomplish tasks that would normally require two different machines, a mini excavator and a mini loader. With a spacious and comfortable cab, the compact size of the machine, ability to turn 360 degree on its own axis, banana boom of backhoe, and standard additional auxiliary hydraulic lines make the HMK 62 SS ideal for urban constructions and agricultural applications where the space is often limited. At the heart of the HMK 62 SS is a 59hp Kubota turbocharged diesel engine which offers aggressive performance, fast cycle times and quick response which makes life easier on working sites, while a simple and reliable gear type hydraulic pump gives 61 lt per min hydraulic flow to the loader, backhoe and auxiliary hydraulic lines; a high efficiency hydraulic oil cooler enables the HMK 62SS to work longer and harder in higher ambient temperatures. One of the characteristics that makes the HMK 62SS different is the superior performance of the front loader. Thanks to the bucket and arm breakout force of the HMK 62 SS, the machine drives the load without being stressed. Also, the unique banana boom geometry makes it easy to work in places where the space is often limited. Machine direction is controlled by the joystick located on the left side of the operator seat, while a joystick located on the right side of the seat allows the operator to execute loading tasks precisely. The rear window can be easily opened monolithically and provides excellent visibility for the operator. Thanks to the additional button on the side console, the operator can move the machine forward and reverse while in excavation position which increases the productivity. As standard equipment, quick coupler adaptors on the front boom shortens the attachment shifting time so that
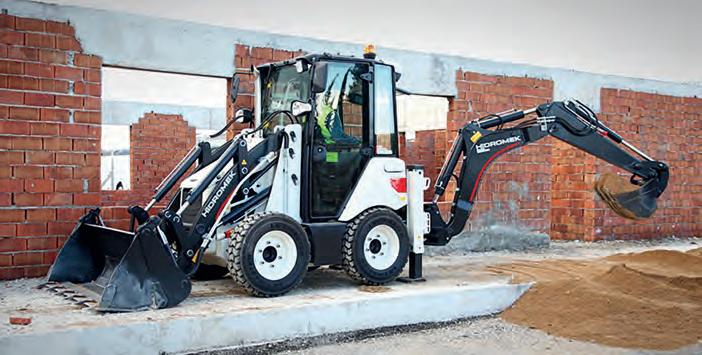
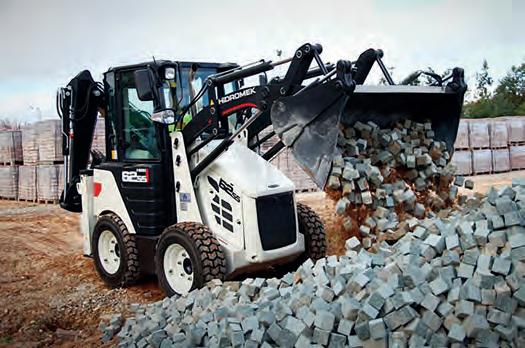
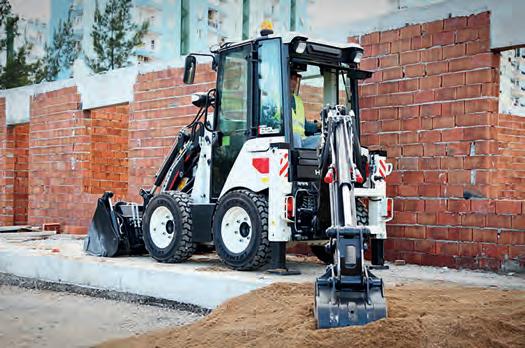

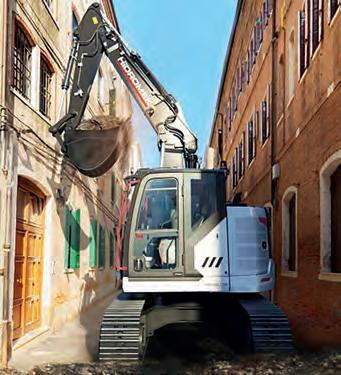
the machine can stay in work longer, contributing to better productivity. HMK 230LC
Meanwhile, the ever popular HMK 230 LC crawler excavator at just over 23 tonnes also features high quality components, smooth hydraulics and strong build, while offering outstanding performance by working faster, more productively and more efficiently. As with all models in the H4 Series, an automatic stop system through configurable idling and stopping times provides fuel saving by stopping the engine after the machine is on idle. The automatic stop system helps to keep operational costs to minimum in these days or rising fuel prices, and, of course, contributes to saving the environment. Another notable feature is the “safe fuel transfer pump” which stops the pump automatically when the tank is full; this feature gets activated also when the pump does not transfer fuel for 30 seconds, and ensures that the pump stops automatically. The machine comes with an 8 inch touch control panel conveniently positioned where the operator can easily control the machine’s features. The touch control panel which includes an integrated music system allows the operator to adjust the hydraulic flow required for attachments without leaving the cab - and he can save this information for up to 20 different attachments. HMK 145 LC SR
Dynamic, innovative, compact – that perfectly describes the HMK 145 LC SR short radius crawler excavator, which also belongs to the H4 Series. With a short swing radius, this operator friendly, compact machine offers excellent maneuverability, especially on work sites that have limited or narrow spaces. Powered by a high performance Isuzu 105hp (78,5 kW) engine, it is ideal for a wide range of applications such as in construction, landscaping, material flooring and levelling. The heated, air suspended seat with its 35 degrees adjustable backrest angle, enables the operator to work comfortably and without getting tired for long working hours. Other features, as with all H4 Series excavators, include proportional control pedals and joysticks, throttle control dial, and an operator touch screen. All the controls are placed on an operator console integrated into the seat, a console that can be moved independently of the seat, allowing you to find the best and most comfortable working position, while the air conditioning system can automatically adjust itself according to the ambient heat located in the cab which benefits from the use of six silicone dampers to absorb noise, shock and vibration, further adding to a comfortable working environment. Another notable feature with all H4 Series excavators is Hidromek’s Opera Control System, an easy to use interface that facilitates communication between the operator and the machine. The operator can easily switch between menus in Opera, change settings, such as hydraulic flow, and check the status of the machine, including pressure, temperature and engine load. The information and warnings on the instrument panel are always easy to see and control, thanks to the positioning of the Opera interface.
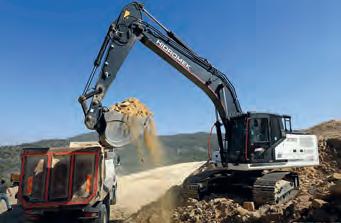
www.hidromek.com
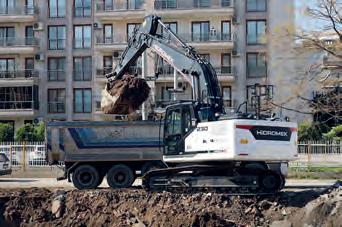
