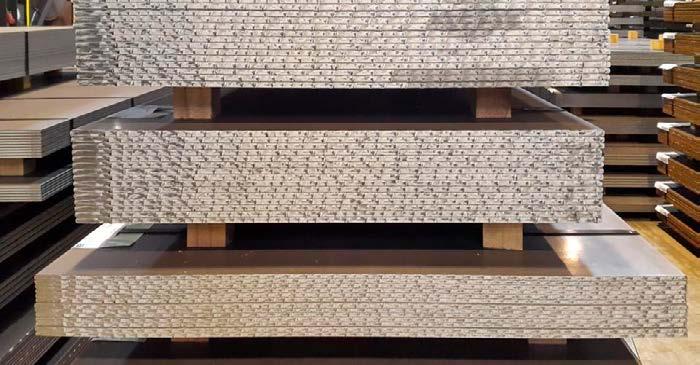
3 minute read
Krachtig decoilen
Na het richten en op lengte snijden, worden de platen automatisch verpakt in de nieuwe decoillijn die momenteel bij Maastricht Service Center wordt opgebouwd.
In het Maastricht Service Center in Feijen, een dochter van Tata Steel Nederland, is begonnen met de installatie van een nieuwe state-of-the-art lijn voor het richten, op lengte snijden en automatisch verpakken van plaatmateriaal.
Met de nieuwe lijn bereidt Tata Steel zich voor op de toenemende vraag naar slijtvaste en hoogwaardige staalsoorten, met name in de markten voor apparatuur in de bouw, mijnbouw en landbouw. Dankzij de nieuwe decoillijn kunnen deze staalsoorten sneller, nauwkeuriger en op een duurzamere manier verwerkt worden. De afgewerkte platen zullen worden geleverd aan klanten in Duitsland, Oost-Europa, de Beneluxmarkten, het Verenigd Koninkrijk en de Scandinavische regio.
Hoge plaatkwaliteit
De ingebruikname van de nieuwe decoiler, geleverd door FIMI, staat gepland voor medio 2024. Vanaf dat moment kunnen coils met een hoge treksterkte sneller en nauwkeuriger worden verwerkt. De lijn zal bijvoorbeeld coils verwerken met een gewicht tot 40 ton en een vloeigrens tot 1600 N/mm², met de hoogste beschikbare hardheidsniveaus, in breedtes tot 2150 mm en diktes van 1,5 mm tot 13 mm, lopend tot 40 m/min. Dit maakt het de krachtigste lijn die door FIMI is ontworpen en geproduceerd voor het verwerken van materiaal met ultrahoge treksterkte en vloeigrens met hoge diktes. Het resultaat is een hoge plaatkwaliteit en het vermogen om te voldoen aan de toenemende technische eisen van toekomstige staalsoorten. De door de lijn verwerkte eindproducten zullen een hoge vlakheid hebben van minder dan 3 mm/m, tot zeer krappe maattoleranties (minder dan ± 2,5 mm tot 12.000 mm plaatlengte).
De premium producten die bij Feijen worden verwerkt, zijn onder meer het slijtvaste staal Valast 450 - gebruikt in landbouw- en bouwmachines, kippers en trailers - ultrahogesterktestalen (UHSS), waaronder het Ympress-assortiment van Tata Steel van S700 tot S1100 en hoger, en Boron -Mangaan (MnB5) staal voor toepassingen in bijvoorbeeld landbouwmachines.
Geautomatiseerde functies
De hoge kwaliteit van de afgewerkte plaat wordt mogelijk dankzij de kracht van de nieuwe lijn, maar ook door geautomatiseerde functies die het proces duurzamer maken. De geautomatiseerde functies en toepassingen omvatten: geautomatiseerd laden en draadsnijden, een geautomatiseerde robot-ontbandeenheid en geautomatiseerde dikte- en maatmeting. De nieuwe decoilinglijn zal drie levellers bevatten, waarmee de invoer van de coil volledig geautomatiseerd kan worden zonder fysiek contact, wat de veiligheid van de operators garandeert. Het borstelproces voor het ontkalken van de stalen strip omvat een intelligent afzuig- en filtersysteem om de uitstoot van fijnstof te minimaliseren. Op camera's gebaseerde in-line meettechnologie zal een geautomatiseerde controle van de oppervlaktekwaliteit en plaatafmetingen mogelijk maken. Twee stapelstations maken non-stop bewerkingen mogelijk met een stapelnauwkeurigheid van plaat tot plaat van 2 mm. Daarnaast komt er een geautomatiseerde plaatweging en etikettering. Verder omvat de geavanceerde stapeltechnologie een airbagsysteem voor geluidsreductie en schokabsorptie, waardoor de geluidsemissie wordt verminderd tot maximaal 85 dB wanneer de platen op elkaar worden gestapeld.
High-tech richtproces
Het hart van de lijn wordt gevormd door FIMI's richttechnologie: FIMI heeft een high-tech richtproces ontwikkeld speciaal voor koolstofstaal met hoge sterkte, gebaseerd op het gebruik van alle levellers die op de lijn zijn geïnstalleerd. Dit systeem, dankzij een combinatie van buig- en trekspanning op de strip, garandeert een progressieve, efficiënte richtprestatie van de ingang tot de uitgang van de lijn en minimaliseert de belasting op elke afzonderlijke leveller. Het instellen en verdelen van het koppel tussen de levellers is volledig geautomatiseerd. De belangrijkste factor voor het egaliseren van materialen met ultrahoge vloeigrens is FIMI's gepatenteerde TDDS (Torque Dynamic Distribution System). Dit is gebaseerd op de toepassing van speciale slipkoppelingen op elke uitgangsas van de aandrijfeenheid verdeler als verbindingselementen naar de assen die de beweging naar de richtrollen overdragen.