
9 minute read
Een exclusief kijkje in de productievestigingen van Ceratizit
Op uitnodiging van Ceratizit bezocht de redactie van VerspaningsNieuws recent de productievestigingen in Balzheim, Kempten en Reutte. De gereedschapsfabrikant heeft de afgelopen jaren hard aan de weg getimmerd met als doel om op termijn uit te groeien tot een wereldwijd top 3 gereedschapsproducent. Om dit te realiseren heeft Ceratizit de afgelopen twee jaar veel nieuwe gereedschapsontwikkelingen op de markt gebracht. Een kijkje in de keuken laat zien hoe deze verspanende gereedschappen tot stand komen.
De reis start in Balzheim (D). Deze fabriek ontstond in maart 2018 na de fusie van de twee Ceratizit dochterondernemingen Klenk en Günther Wirth Präzisionswerkzeuge. De fabriek is gespecialiseerd in de productie van gereedschappen voor boren, ruimen, frezen en verzinken. Met ruim 450 medewerkers en 140 CNC-machines, waarvan het overgrote deel rondslijpmachines, behaalt de fabriek met een vloeroppervlak van 11.000 m2 een productiecapaciteit van 200.000 gereedschappen per maand. Daarmee wordt jaarlijks op indrukwekkende wijze ruim 300 ton hardmetaal verwerkt. Om deze hoeveelheden efficiënt te produceren is er een hoge mate van automatisering doorgevoerd. Dankzij robotautomatisering kunnen sommige rondslijpmachines tot wel 40 uur onbemand produceren. De diversiteit aan gereedschappen die in Balzheim wordt geproduceerd is groot. Zo worden hier bijvoorbeeld microboortjes vanaf een diameter van 0,1 mm tot aan boren met grote diameters (70xD) geproduceerd. Dit vergt, zeker bij de productie van kleine gereedschappen die vaak ook nog zijn voorzien van interne koelkanalen, een ontzettend stabiel bewerkingsproces. Om dit te realiseren zijn alle bewerkingsmachines aangesloten op een centraal koelsmeermiddelsysteem. In totaal wordt er zo’n 12.000 liter
De Ceratizit productievesting in Balzheim produceert ruim 200.000 boren, tappen, ruimers en verzinkboren per maand. Om dit te realiseren zijn op de productielocatie ongeveer 140 CNC-machines operationeel.
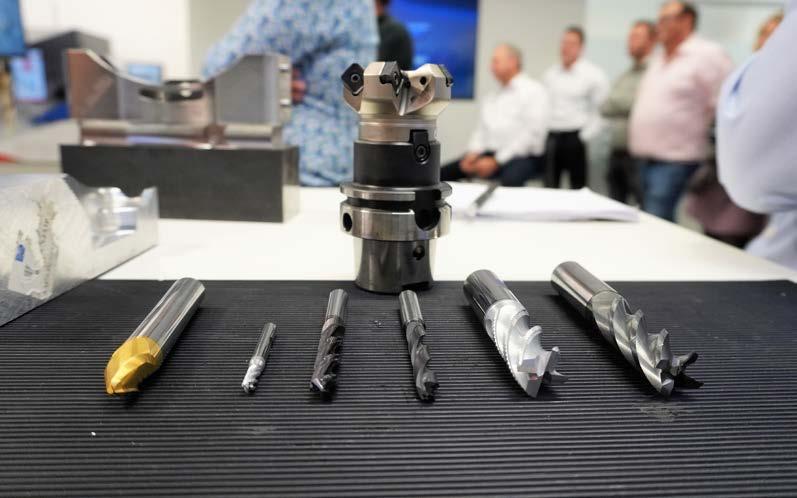
Ceratizit organiseerde recent een interessante reis naar diverse productievestigingen om te laten zien hoe hun verspanende gereedschappen tot stand komen.
koelsmeermiddel per minuut in de fabriek rondgepompt dat constant op 25 oC wordt gehouden. Dit zorgt voor een hoge thermische stabiliteit. Hier in Balzheim worden ook gereedschappen gemaakt speciaal voor de luchtvaartindustrie. Dit zijn vaak speciale tools, zoals ‘step-tools’ die meerdere bewerkingen in één procesgang kunnen doen. Deze gereedschappen moeten bovendien aan hogere kwaliteitseisen voldoen. De gereedschappen die in Balzheim worden geproduceerd worden na een grondige reiniging direct voorzien van een coating. De coating die onder een temperatuur van 400 oC tot 500 oC wordt aangebracht, is essentieel voor de standtijd van het gereedschap. In totaal kan Ceratizit inmiddels kiezen uit meer dan 120 verschillende coatings om precies de perfecte eigenschappen te realiseren die nodig zijn voor een bepaalde toepassing. In Balzheim bevindt zich verder het Innovation Center. Met behulp van vier CNC-bewerkingscentra worden hier zowel standaard als speciale gereedschappen ontwikkeld en onder spaan getest.
Kempten Technical Centre
Na Balzheim ging de reis verder richting het Duitse Kempten. Hier bevindt zich niet alleen het nieuwe logistieke centrum (zie kaderstuk), maar ook het Technical Centre waar Ceratizit onder andere productpresentaties en trainingen geeft. Op moment van schrijven wordt er in Kempten hard gewerkt aan de bouw van een nieuw pand, waar het Technical Centre nog meer aandacht krijgt met meer bewerkingsmachines. Tijdens het bezoek aan het Technical Centre presenteerde Ceratizit diverse gereedschappen live onder spaan. Veel aandacht ging uit naar High Dynamic Turning (HDT) met behulp van Freeturn. Deze technologie heeft Ceratizit in 2018 voor het eerst voorgesteld en wordt nu steeds vaker in de praktijk toegepast. FreeTurn is een allround draaigereedschap dat gebruikt kan worden op multitasking machines en CNC-draaimachines met een freesspil. Door de gereedschapshouder van het FreeTurn gereedschap in de freesspil te plaatsen, is het mogelijk om het gereedschap te draaien en dus de aanvalshoek van het gereedschap continue te veranderen. Hierdoor kan er met één gereedschap een volledig werkstuk gedraaid worden. Het grote voordeel is dat er minder gereedschapswissels nodig zijn, waardoor de productietijd met wel 30% gereduceerd kan worden. “FreeTurn werd vier jaar geleden voorgesteld, maar we merken in Nederland en België nu pas dat de
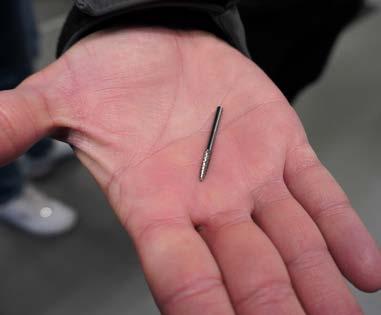
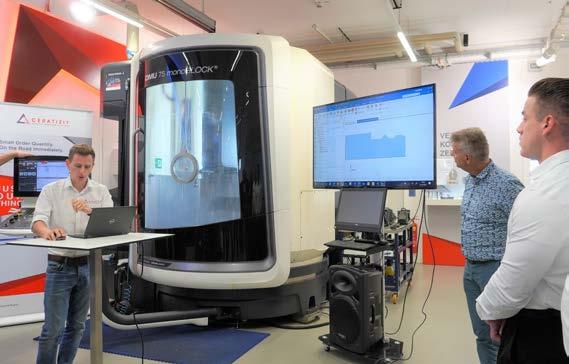
In het Technical Center in Kempten geeft Ceratizit productpresentaties en trainingen. Tijdens het bezoek werden diverse nieuwe gereedschappen gepresenteerd. Speciale aandacht ging uit naar het programmeren van High Dynamic Turning met FreeTurn.
eerste bedrijven interesse tonen. Dat heeft te maken met het feit dat er best veel komt kijken om FreeTurn werkend te krijgen. Niet alleen moet je over een hightech machine beschikken met voldoende bewegende assen om het FreeTurn gereedschap optimaal te kunnen benutten, maar ook het programmeren is tot voor kort vaak een te grote uitdaging gebleken”, vertelt Tinus Zuetenhorst, directeur van Ceratizit Nederland & België. Door ontwikkelingen in CAM is FreeTurn inmiddels veel toegankelijker geworden. Tijdens een demo liet Ceratizit zien hoe je eenvoudig een DXF-file kan importeren en met een paar muisklikken een CAM-programma kan genereren. Met behulp van simulatie is vervolgens het programma te controleren en te finetunen.
Naast FreeTurn kreeg ook het nieuwe MaxiMill - Slot-SX sleuffreessysteem de nodige aandacht. Het gereedschap is ontwikkeld om het bewerken van sleuven en groeven efficiënter en betrouwbaarder te maken. Dankzij een optimale koelmiddeltoevoer biedt het gereedschap tot diameters van 250 mm een optimale spaanbeheersing en een hoge proceszekerheid. Naast de prestaties van het MaxiMill - Slot-SX sleuffreessysteem is ook de eenvoudige bediening een opvallende eigenschap van het gereedschap. Het gereedschap maakt gebruik van de gepatenteerde SX-montagesleutel bij het wisselen van wisselplaten. Dankzij zijn hefboom versnelt deze sleutel het wisselen en behoudt het altijd de juiste klemkracht. Hierdoor wordt overbelasting en vervorming voorkomen, waardoor slijtage aan de wisselplaatzitting wordt verminderd.
80.000 wisselplaten per dag
Na Kempten ging de reis nog iets verder zuidelijk, namelijk naar het Oostenrijkse Reutte. Op deze locatie worden de wisselplaten en hardmetalen staven van Ceratizit geproduceerd. Het hele proces, van de voorbereiding en het mengen van de poeder tot aan het vormen en persen, het sinteren, de afwerking en de verzending en recycling vindt hier plaats. Om een indruk te geven: dagelijks worden
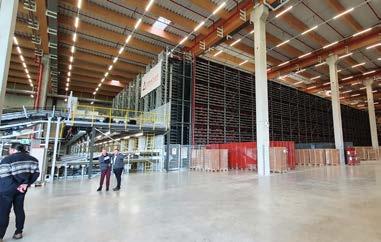
Het geautomatiseerde logistieke centrum in Kempten heeft maar liefst 300.000 opslagposities. Dagelijks vertrekken hier 4.000 pakketten.
Wat we vaak niet beseffen is dat achter de belofte ‘Vandaag besteld, morgen in huis’ een groot logistiek apparaat schuil gaat. Zo ook bij Ceratizit. In het hart van dit logistieke apparaat bevindt zich het gloednieuwe logistieke centrum in Kempten (D). Dit logistieke paradepaardje van Ceratizit is met een vloeroppervlak van maar liefst 50.000 m2 een indrukwekkende verschijning.
Het logistieke centrum in Kempten herbergt maar liefst 90.000 verschillende gereedschappen die direct uit voorraad geleverd kunnen worden. De gereedschappen die hier dagelijks vanuit de verschillende productielocaties binnenkomen worden opgeslagen in het geautomatiseerde magazijnsysteem met ongeveer 300.000 opslagposities. De gereedschappen zijn in de fabriek al voorzien van barcodes, zodat ze automatisch door het systeem herkend worden. Met behulp van shuttles worden de gereedschappen vervolgens
Het nieuwe MaxiMill - SlotSX sleuffreessysteem voor het bewerken van sleuven en groeven is eenvoudig uit te rusten met wisselplaten dankzij de gepatenteerde SXmontagesleutel.

hier 80.000 wisselplaten geproduceerd. De wisselplaten en staven worden gemaakt van een wolfraamcarbidepoeder. Samen met kobalt en andere adhesieve poeders, zoals bijvoorbeeld titaniumcarbide of één van de overige 80 hardmetaalsoorten, wordt met behulp van een vier tot negen uren durend mix-proces en een warmtebehandeling het uiteindelijke hardmetaalgranulaat verkregen. Tijdens de rondleiding werd duidelijk dat er in mijnen maar liefst 1.000 kg stenen moet worden verwerkt om tot 8 kg granulaat te komen. Maandelijks wordt er in Reutte 160 ton hardmetaal granulaat verwerkt tot wisselplaten en staven. Dit geeft dus goed weer waarom Ceratizit veel investeert in recycling en duurzame productieprocessen.
Om van het granulaat een wisselplaat te maken zijn er nog een aantal stappen nodig. Met behulp van een persmachine wordt het granulaat in een matrijs onder een druk van 1.5 ton in de vorm geperst. Ceratizit heeft ruim 4.500 verschillende matrijzen in gebruik en met elke matrijs kunnen er 50.000 wisselplaten worden geproduceerd, voordat er onderhoud nodig is. Op het moment dat de wisselplaat uit de vorm komt is het nog erg bros. Zo bros zelfs dat het met de hand is te breken. Tevens is op dat moment de wisselplaat nog zo’n 20% groter dan het eindproduct. Pas na een sinterproces van gemiddeld 18 uur bij temperaturen tussen de 600 oC en 1.600 oC verkrijgt de wisselplaat zijn sterkte. Door het sinterproces krimpt de wisselplaat ook tot de gewenste afmeting. Vervolgens wordt de coating aangebracht. Het coatingproces duurt tussen de zes en 24 uur, afhankelijk van het type coating (CVD of PVD). In het geval van een CVD-coating kost het 1 uur om een laagje van 1 micrometer aan te brengen. Een coating heeft een maximale laagdikte van 20 micrometer. Na het coaten is de wisselplaat aanbeland bij de laatste productiestap, namelijk het naslijpen en borstelen van de snijkanten. In totaal zijn er 60 slijpmachines operationeel om deze klus te klaren. De wisselplaten worden vervolgens automatisch gecontroleerd en verstuurd naar het logistieke centrum in Kempten.
richting de juiste plaats in het magazijn gebracht. In totaal kent het systeem 259 shuttles die de gereedschappen van het ene station naar het andere brengen.
Efficiënt en foutloos picken
Het magazijn is voorzien van zogenaamde sorteer- en inpakstations. Hier worden bestellingen door een magazijnmedewerker verwerkt. De gereedschappen worden wederom dankzij barcodes en shuttles aangevoerd, waardoor de medewerker een vaste werkplaats heeft. Omdat door deze oplossing medewerkers niet meer zelf op zoek gaan in het magazijn, wordt er een hoge efficiëntie gerealiseerd. Bovendien voorkomt het systeem ook de kans op fouten en vermiste items. De sorteer- en inpakstations zijn namelijk voorzien van een zogenoemd 'put to light system'. Met behulp van lichtsignalen en displays worden magazijnmedewerker door het pickingproces geleid. Het systeem geeft precies aan hoeveel items er gepakt moeten worden, in welk bakje ze liggen en bij welke order de items horen. Zo is de foutmarge tot een minimum gereduceerd. Daarnaast is er nog een extra controle ingebouwd. Weegschalen controleren automatisch het gewicht, zodat het systeem weet of de juiste hoeveelheid gereedschappen zijn gepakt.
Hoge automatiseringsgraad
In totaal vertrekken er dagelijks vanuit Kempten 4.000 pakketten naar klanten over de hele wereld. De slechts 125 medewerkers die het logistieke centrum draaiende houden laten zien hoe geautomatiseerd het magazijn is. De drijvende kracht achter de operatie is de SAP Extended Warehouse Management (SAP EWM) software. De software is direct aangesloten op het geautomatiseerde magazijnbeheersysteem en legt de basis voor een hoge automatiseringsgraad en de digitalisering van de hele supply-chain. In de toekomst verwacht CERATIZIT de processen, zoals het picken van orders verder te automatiseren met behulp van robots. Ook aan toekomstige groei is gedacht. Het gebouw heeft namelijk voldoende ruimte om een identiek magazijnsysteem tegenover het bestaande magazijn te plaatsen.