
9 minute read
Member Feature: Hayman Reese - 70 Years Strong
HAYMAN REESE: 70 YEARS STRONG
The brand says, “We know towing”
The humble tow bar is an everyday item which many Australians fit onto their cars and behind that shiny tow ball, is a multimillion-dollar industry. One market-leading brand which stands out is Hayman Reese, which in 2021 is celebrating its 70th anniversary. Harking back to the late 1940s when post-war Australia was headed by Prime Minister Robert Menzies and the Snowy Mountain Scheme was getting underway, Australians were starting to explore the country in increasing numbers. A friend asked Eric Hayman to build him a tow bar to tow his newly acquired caravan. He built two, one for his friend and another which he quickly sold at a country agricultural show. He could not have dreamed that it would be the first step towards building an Australian icon. Eric Hayman was not new to manufacturing; he had been making bicycle spokes in a small South Melbourne factory for some time. The tow bar business quickly became the focus of his attention and he set about making them in earnest. In 1972 a major milestone was reached: a large American towing products company, by the name of Reese, was on the lookout for global partners and started working closely with Eric Hayman’s business. Seven years later a new entity was formed, and Eric Hayman was appointed as the first Managing Director of Hayman Reese. As part of this partnership Hayman Reese introduced several key pieces of technology to the Australian market: weight distribution systems for safer towing and the Hayman Reese signature 50mm ‘square-hole’ Hitch Receiver tow bar. Until that time most tow bars had been a fabricated product with fixed mounting points and were not easily detachable. Hayman Reese says the 50mm square tow bar hitch was a game changer and states that it remains the Australian industry standard today. 1972 also saw the company leave South Melbourne and move to a larger facility in Dandenong. The Hayman Reese business is now located in a stateof-art engineering, manufacturing and warehouse facility in Keysborough. With over two hundred staff on site, Hayman Reese designs, tests and manufactures a wide range of products all under one roof, in what it says is the largest facility of its type in Australia. Now part of the locally owned AutoPacific Group, the Hayman Reese DNA remains at the core of the organisation. “Hayman Reese has been a keen participant in the Australian automotive aftermarket since the FX Holden went on sale,” AutoPacific Group Chief Executive Officer, Jason Kieseker, said. “Our products have been helping Australians on worksites and on weekends since the 1950s - it’s a great achievement and something we are extremely proud of.” With the loss of the local automotive manufacturing industry Hayman Reese remains one of a few local manufacturers of automotive components. “It’s a challenge we have successfully overcome through a culture of consistent improvement, having a local manufacturing capability is central to our business. It’s important both to our customers and us,” Jason said. With such a long history it’s still possible for Hayman Reese to build towbars which have not been offered for decades. The company’s Keysborough manufacturing facility still houses the original drawings and tooling to produce towbars for every current towing vehicle as well as cars now seen as irreplaceable classics. Since the very first towbar, Hayman Reese says it has strived to provide customers with everything required to equip a consumer with the safest towing solution. Each solution is sold as a complete kit, including comprehensive fitting instructions that enhance the ease of installation. The Hayman Reese journey simply started with a towbar but has expanded to include SmartClick Wiring Solutions, Brake Controllers, Weight Distribution Systems as well as application specific products such as X-Bar, a tailored design 4WD solution. Hayman Reese Towbars
Since introducing its innovative 50mm x 50mm hitch receiver style to the market, Hayman Reese says it has continued to be at the forefront of towbar innovation. The 2000s saw Hayman Reese change the way that towbars were painted. Previously, towbars were merely dipped in paint, which could allow foreign objects to destroy the paint integrity. It says its introduction of the MetalShield three stage corrosion protection system has significantly increased the longevity and quality of the painted towbar. Firstly, towbars are shot blasted, preparing a clean uniform surface free from imperfections or foreign objects. This is followed by a preprotection surface using electricity to create an adhesive bond between the raw metal and the e-coat. Finally, the towbar is powder coated to ensure maximum durability against rust and corrosion. Hayman Reese says the finished result gives its towbars a quality finish that surpasses the performance of many others in the market. Another Hayman Reese innovation in towbars is its SmartPin anti-rattle technology, engineered to combat any annoying rattle that motorists might experience. Unique to the market, the SmartPin utilises two small ‘keyways’ in the hitch receiver that the SmartPin slots into. Once the accompanying nut is tightened, the SmartPin is held in place, providing sufficient pressure against the hitch receiver and tow ball mount to prevent rattle. Hayman Reese says it pushed the boundaries again with the release of the X-Bar towbar in 2018.
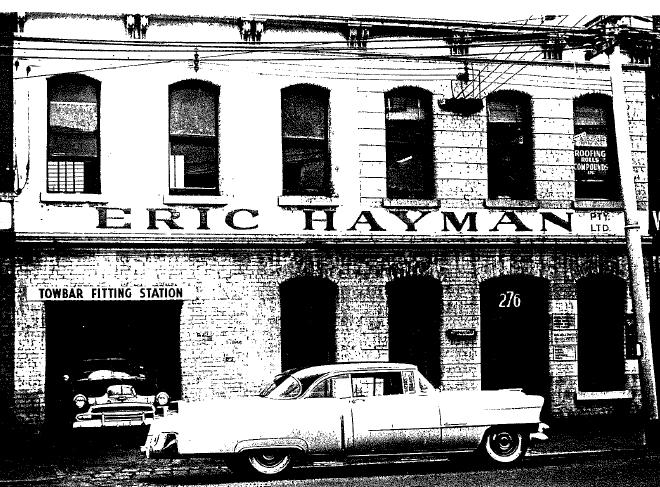
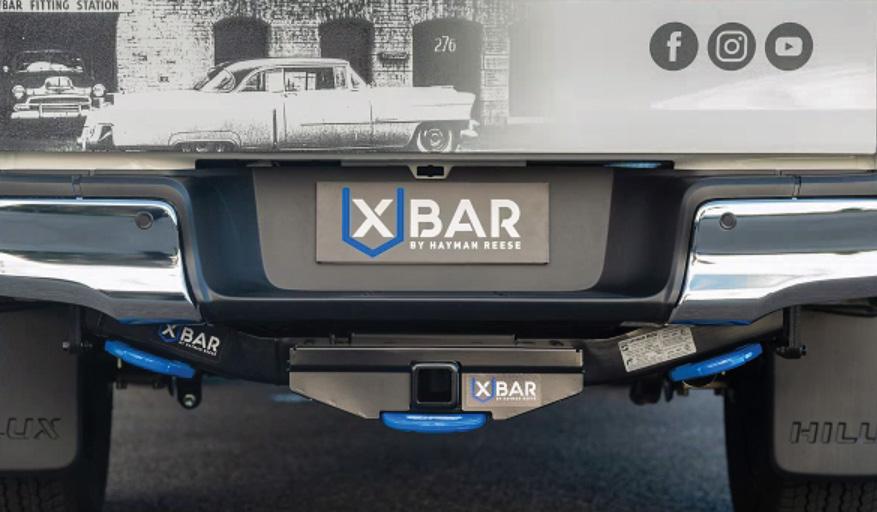
Beyond the traditional single function of towing, the X-Bar reportedly delivers on the needs of 4WD enthusiasts in terms of clearance, recovery rating and strength. The Hayman Reese X-Bar has three dedicated recovery points, rated up to eight tonnes, can increase clearance by up to 100mm and Hayman Reese says it has the strength to withstand heavy towing and recovery without compromise. Wiring Solutions
Innovation in towbars was only the start for Hayman Reese. At a similar time to the release of MetalShield, Hayman Reese also introduced what it calls the simplest solution for wiring a towbar – the Hayman Reese SmartClick wiring system. Taking the complexity out of splicing, cutting, matching and soldering wires, the vehicle specific SmartClick looms are designed to be ready to plug into the existing vehicle wiring, drastically reducing fitment time and margin for error. It is included in towbar kits for most modern vehicles. Modern vehicles can use CANbus wiring, single wire dual voltages, low voltage or even low current signals to operate the tail lights where trailer wiring connects. Determined to not allow this to be a become an issue for fitters, Hayman Reese’s wiring solutions include an Electronic Control Unit (ECU) that works by reading the status of vehicle tail lamps and powers the trailer lamps from the battery power source without generating any fault codes in the vehicle system. The ECU isolates the vehicle’s existing tail lamp circuits and transfers the power to the trailer lamps, preventing overload and providing protection against any trailer wiring faults, which is especially necessary for vehicles using an electrical control method like a Pulse Width Modulation. Paired with SmartClick harnesses, the inclusion of ECUs alleviates the fitment concerns encountered with the ever-changing intricate wiring systems in modern vehicles. Each Hayman Reese ECU carries the ACMA RCM mark (formerly known as ‘C-tick’). The RCM mark means that all Hayman Reese ECUs meet and adhere to Australian Electromagnetic Compatibility Standards and will not interfere with expensive and sensitive electronics critical to safe operation. Brake Controllers
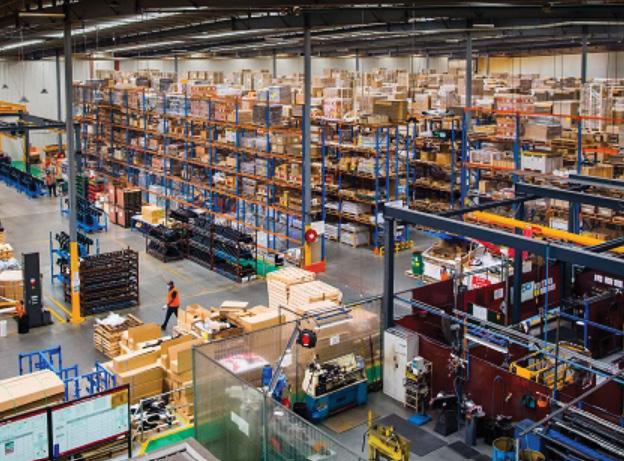
Any trailer weighing over 750kg is required by Australian law to have a braking system installed. Electric and electric over hydraulic brakes, commonly found in RVs and boat trailers, require a brake controller to control the voltage output to the trailer brakes. The Hayman Reese Guardian and Compact brake controllers utilise a proven timer-based system to increase the voltage to the trailer brakes over a length of time, increasing the braking force. Great for lighter loads or off-road towing, the robust timer-based systems still have a place in the harsh Australian terrain. The Guardian IQ and Compact IQ brake controllers take this technology one step further, using proportional braking technology to provide an even easier solution for consumers. Reacting to the changing velocity in the vehicle, when the brake pedal is pressed, the brake controller will adjust the voltage sent to the trailer brakes to slow the trailer with ease. The technology being used in Hayman Reese proportional brake controllers has reportedly been shown to achieve better results with many caravan stability systems and Hayman Reese says it is amongst the preferred choice of caravan manufacturers. Overall, continuing to offer both types of brake control solutions gives customers the choice to select the perfect product to meet their needs. To further facilitate the fitment of Hayman Reese brake controllers, in 2015 Hayman Reese released a range of brake control harnesses. Clicking into the existing Hayman Reese SmartClick towbar wiring harness, the brake control harness range reduces fitment time and again removes the complexity of integrating with specific vehicle wiring systems. Weight Distribution range
The concept of weight distribution is to spread the weight applied at the rear of the vehicle, when towing, more evenly across all axles. This allows for greater stability and less stress on pressure points, as the towing load is distributed across a larger area. When originally released, Hayman Reese had a ‘trunnion’ style spring bar concept. This suited most caravans at the time as they had a similar A-frame depth and coupling position. Over time, as caravans changed to accommodate the developing requirements set by the market, the traditional ‘trunnion’ style spring bars were no longer a ‘onefits all’ scenario. Rather than maintaining the status quo, Hayman Reese developed the ‘round bar’ style of spring bar, providing increased clearance around the A-frame. Presently, both styles are still sold, each within their own weight ranges: ‘Trunnion’ style accommodating consumers with a shallower A-frame or bottom mounted coupling, whilst ‘round bar’ systems meet the needs of top mounted couplings with deeper A-frames. Hayman Reese weight distribution systems have become an integral part of a towing system. The success of these systems has become so predominant over the years that the development of most new caravan coupling systems considers the integration of weight distribution as mandatory to ensure the safety of the vehicle and its occupants. SmartCode – Hayman Reese’s newest technology
Modern vehicles are becoming increasingly sophisticated with new features that need to be adjusted when towing. Hayman Reese says that without an intelligent towing solution, like SmartCODE, the vehicle will not operate at its full capability. This can result in error lights appearing on your dash, or reduced functionality including Blind Spot Detection, Adaptive Cruise Control and Reverse Park Assist. Hayman Reese says SmartCODE ensures a vehicle operates at its full capability when towing. For more information, visit www.haymanreese.com.au