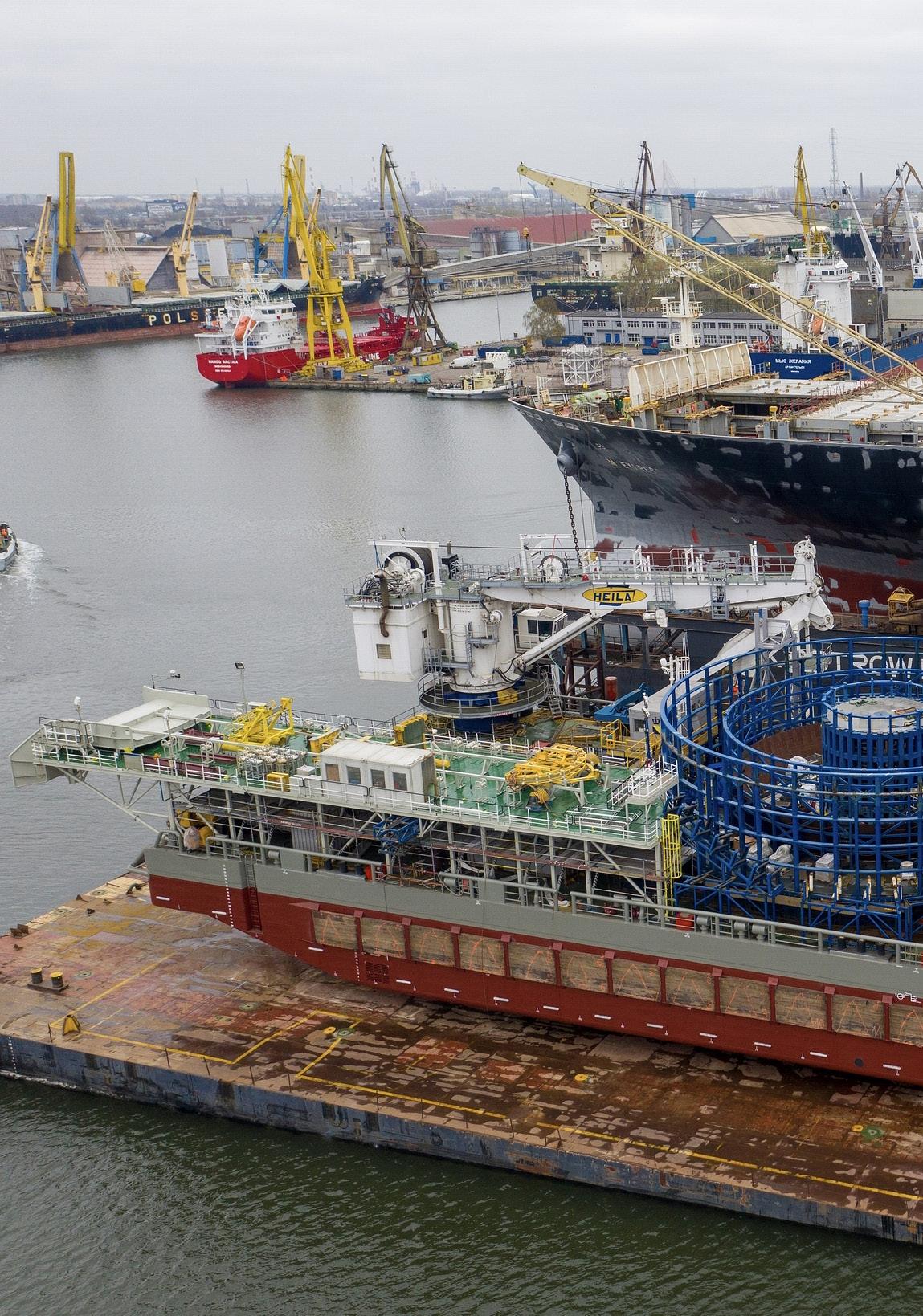
16 minute read
REPAIRS
DREDGER REPAIRS AT REMONTOWA
REPAIRS
Advertisement
During October this year, Van Oord’s 18,893 m3 TSHD Vox Amalia was drydocked at Poland’s Remontowa, Gdansk. The shipyard carried out, among others, modifications to her pipelines and dredging systems.
During the drydock work, the sea chest was enlarged and the suction pipes for the jet pumps has been modified (the system for flushing the hopper and pipes used for dredging). Due to this modification in the jet pump room several pipelines have been rerouted and modified (de-aeration of sea chest, LT pipes).
Several connections were made between a new jet-water line to the selfemptying lines to liquefy the clog issues when starting-up the self-emptying process of the hopper – the systems have been connected using GRE pipes. A new installation of a degassing system for underwater pumps on the dredging pipe system was also added, including foundations, pumps, ejectors, valves and flowmeters. In addition, the sieve installation was dismantled and original dredge pipes have been installed to their original state.
Maintenance work on dragheads was carried out, including replacement of UXO grids and nozzle bushes as well as modification of the Jet system pipes at the draghead connection. As the first task of the Vox Amalia following her departure from Remontowa was to dredge the fairway leading to one of the Polish seaports, she has been fitted with explosion-proof screens to protect the crew in the event of hazardous material (unexploded ordnances) being sucked into the system. One of the tasks was also electrical work, involving the connection of the aforementioned systems.
Earlier this year Remontowa repaired two vessels belonging to Holland’s Royal Boskalis Westminster - the 2,000 kW backhoe dredger Nordic Giant dredger and the 5,551 gt cable-layer Spirit .
The Nordic Giant is equipped with a powerful Liebherr P995 excavator, which enables dredging up to 23 m depth. During operation, the unit is supported on three anchor posts (spuds), i.e. tall steel structures that provide stability during dredging.
During the repairs, maintenance and painting work on-board the dredger’s hull, fresh water tank, deck and superstructure. Deep cracks were repaired in the lower part of the side spuds, and the bow leg had part of its lower, heavily worn structure replaced.
A time-consuming task was to dismantle more than 60 fenders, perform maintenance works on the hull, where they were installed, and reinstall them. In
Boskalis’ Spirit in Remontowa
the shipyard, the Rem-220 floating sheerleg was also used to transport the dredging equipment - booms and excavator buckets - supplied by the owner.
The Nordic Giant is very similar in design to another vessel of this type - Hipoppotes, which was in Remontowa during 2019. As soon as the repairs were completed, the Nordic Giant was towed to Sweden to carry out dredging works related to the laying of the power cable on the seabed.
Throughout almost the entire period of repairs, the cable-layer Spirit was docked on-board the Rem Lift 25000, a semi-submersible heavy lift barge on which Remontowa prepared the vessel for the next project.
The most important task was to review all four propulsion thrusters (including two retractable azimuth thrusters). A Bioblock (sewage treatment plant) was replaced with a new one. Numerous steel renewal and piping work, as well as maintenance and painting work on the hull, fresh water tanks and other areas of the ship, such as ‘tweendeck, crane, inner part of the bulwark, railings, etc. was carried out. In turn, electrical and access work was carried out related to the
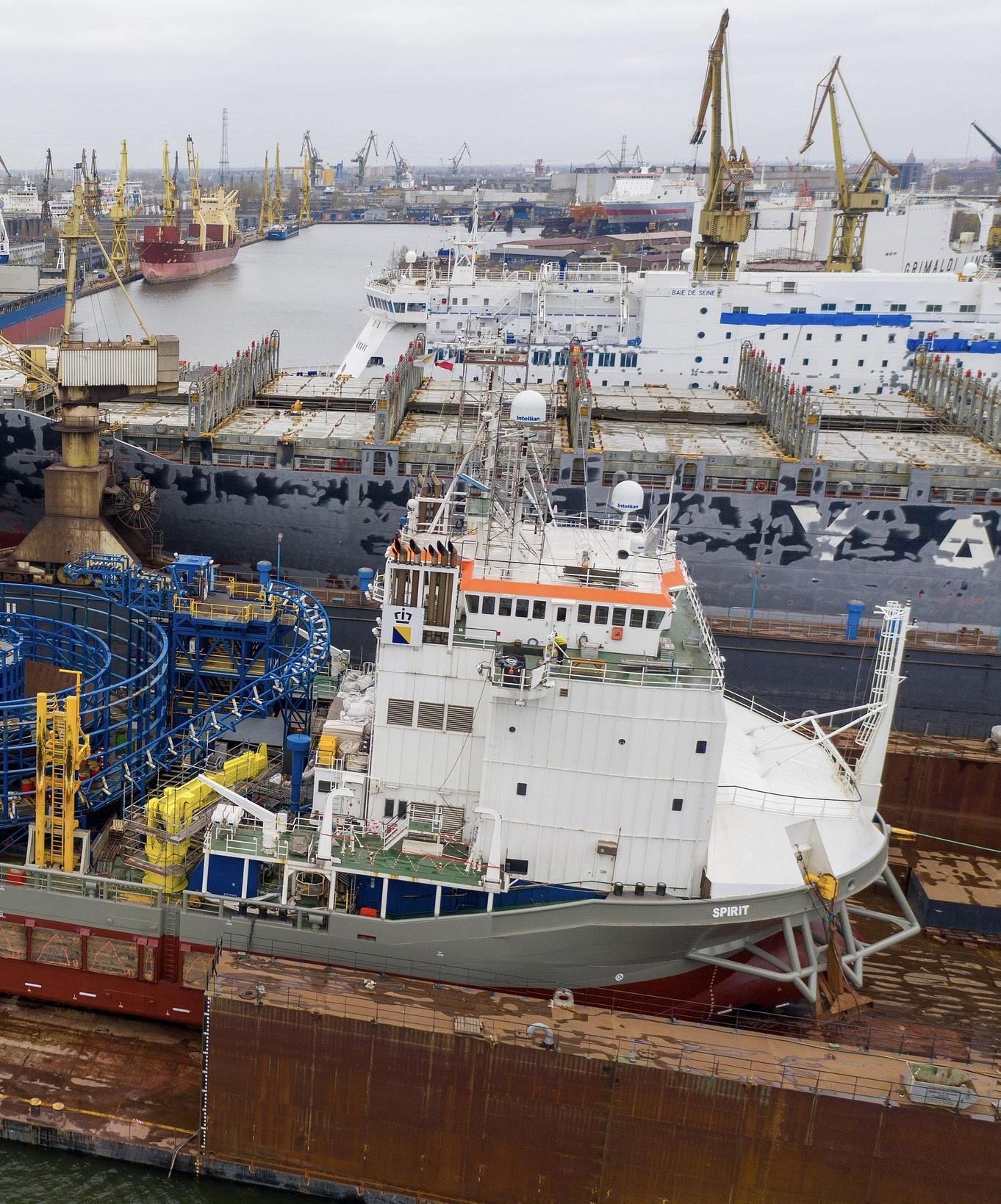
modification of the ship’s DP2 system.
Most of the ship’s areas, including tanks and accommodation rooms, were renovated. A new access to the engine room was arranged, for which part of the existing social room was modified. A lot of steel work was also completed on the open deck and on the hull (including new fendering). Some of this work was carried out for the purpose of placing equipment onboard, including the fixing of containers in which specialist equipment for underwater work was to be stored.
After the repairs had been completed, the Spirit sailed out of the shipyard towards Karlskrona (Sweden).
DAMEN COMPLETES OCEANXPLORER PROJECT
Holland’s Damen Shipyards Group has recently completed the extensive rebuild of the research vessel OceanXplorer at Damen Shiprepair Rotterdam. The vessel will contribute significantly to OceanX’s mission – to explore the ocean and bring it back to the world. In this way, the initiative aims at the building of a global community engaged with understanding, enjoying and protecting our oceans.
Upon completion of the project, OceanXplorer has become the most advanced exploration, research and media vessel in the world. As OceanX’s new flagship, she builds on the legacy of the organisation’s first vessel, Alucia and takes things to the next level. Equipped with a series of submersibles, sonar arrays, manned submarines, an ROV and AUV, OceanXplorer is able to explore and map the depths of the oceans.
The vessel is able to collect live samples and bring them aboard where they can be analysed by scientists in state-of-the-art laboratories – with the capabilities, amongst other things, to carry out DNA sequencing.
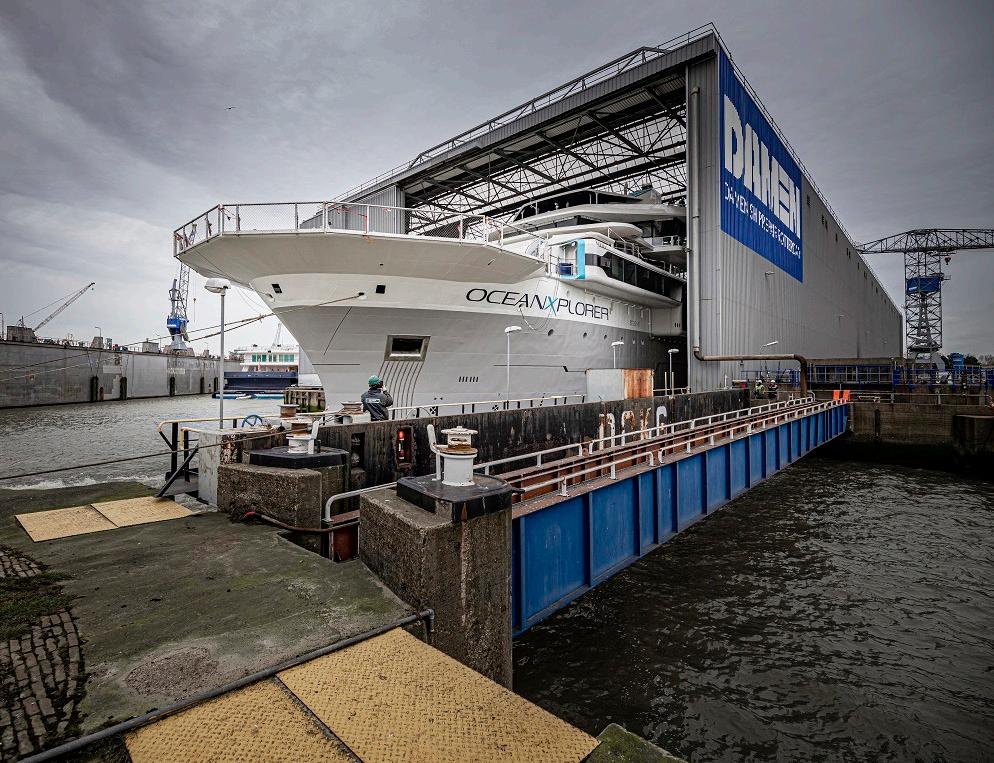
The OceanXplorer emerges from the covered berth at Damen Shiprepair Rotterdam
OceanXplorer’s outstanding research facilities are paired with Hollywood quality filming and media studios – developed in partnership with renowned filmmaker James Cameron. With this, the vessel’s findings can be live-streamed to audiences world-wide at the exact moment of discovery. Damen served as main contractor in this complex and challenging project, fulfilling an extensive scope of work that brought together various disciplines from across Damen Shipyards Group – including offshore and survey newbuild, repair & conversion and yachting specialisms.
The project required Damen to rebuild the vessel – a former offshore survey ship – in essence from the main deck upwards by stripping the existing accommodation and adding a complete new and much larger accommodation to house the new laboratories, workshops and submarine hangar. Also a fully integrated heli-hangar was added to the superstructure as well as extensions on both sides of the accommodation decks to house new cabins over the (increased) full beam of the vessel. Following the structural part, the work included overseeing the complete integration of all ship’s systems including specialist hydrographic and laboratory systems and an innovative IT infrastructure to facilitate the combination of state-of-the-art research facilities with the on-board Hollywood standard cinematography and media studios.
Damen worked closely with OceanX’s specialist teams, developing the scope of the project in
order to fulfil all requirements. This included responsibility for the interior and exterior of the vessel. The ship is unique in its combining of up-to-the-minute research facilities – courtesy of renowned naval architects Skipsteknisk – and topof-the-line interior accommodations, designed by Christina Fallah. The vessel’s additional interiors as well as its exterior were styled by Steve Gresham.
The project also required Damen to undertake a docking scope, including removal and refurbishment of azipull and bow thrusters, blasting and coating of tanks and complete overhaul and upgrading of crew accommodation.
Tjarco Ekkelkamp, project director for the ALEWIJNSE’S ROLE IN THE OCEANXPLORER PROJECT Holland’s Alewijnse has fulfilled its scope of work as main electrical contractor on the OceanXplorer project. The vessel has been undergoing an extensive rebuild at Damen Shiprepair Rotterdam (See above). OceanXplorer will continue the work of OceanX’s first research vessel, Alucia, broadening understanding of the Earth’s oceans. Alewijnse’s work on the project has involved the complete electrical refit – including installation of some 210 kms of cables.
Alewijnse’s scope of work on the project has been a broad and diverse one. For example, the company installed a far sounder to enable clear detection below the surface of the water. The OceanXplorer will operate in Polar Regions, which includes critically important iceberg detection capabilities. The company has also installed underwater lighting and an underwater telephone system, enabling communication from the vessel to submersibles.
Alewijnse installed two separate lighting OceanXplorer project at Damen said, “This has been a challenging project, the result of which we are very proud of. On the one hand, this shows the extensive capabilities of Damen as a group – the powerful synergies within our group, covering both newbuild and repair & conversion capabilities and spanning commercial vessels and superyachts. On the other, this is a vessel that represents a force for good in the world – one that will enhance human involvement, understanding and ultimately conservation of our oceans. With our strong commitment to maritime sustainability, we are delighted to have played
our part in the development of OceanXplorer.” systems – one for switching and dimming of normal light fixtures and one for controlling light temperature. Amongst other things, this facilitates filming capabilities - an important part of OceanXplorer’s mission to provide the world with greater information about our seas and oceans.
The company has upgraded the vessel’s bridge ECDIS system – including the installation of a 55-inch Touchscreen monitor – and optimised the DP2 system with the application of the latest controls and software. Alewijnse has also upgraded the vessel’s alarm and monitoring system.
Tjarco Ekkelkamp, project director for the OceanXplorer project at Damen Shiprepair Rotterdam explained Damen’s contracting of Alewijnse for the electrical scope, saying, “This is a complex, specialist project. The OceanXplorer combines the characteristics of an offshore vessel, a scientific research ship and a deluxe eco-tourism cruise vessel. The many projects that Damen has worked with Alewijnse on over the years include all three of these vessel types. Therefore, we were confident in their ability to meet the challenges presented by the OceanXplorer rebuild – and this judgement has certainly proven to be correct.”
A further challenge during the project execution has been presented by the outbreak of the COVID-19 virus. Peter van Campen, Alewijnse project manager explained, “The well-being of all people working on the vessel has naturally been
our primary concern at all times. Ensuring this involved placing strict limitations on the number of people on-board the vessel at any one time. However, we enjoy an excellent collaboration with the yard and our co-workers. This carefully coordinated cooperation has ensured our ability to continue working safely during this time.” cruise vessel. The many projects that Damen has worked with Alewijnse on over the years include all three of these vessel types. Therefore, we were confident in their ability to meet the challenges presented by the OceanXplorer rebuild – and this judgement has certainly proven to be correct.” THORDON BEARINGS COMPLETES NMDC PROJECT The 7,800 kW Cutter Suction Dredger (CSD) A further challenge during the project execution has been presented by the outbreak of the COVID-19 virus. Peter van Campen, Alewijnse project manager explained, “The well-being of all people working on the vessel has naturally been our primary concern at all times. Ensuring this involved placing strict limitations on the number of people on-board the vessel at any one time. However, we enjoy an excellent collaboration with the yard and our co-workers. This carefully coordinated cooperation has ensured our ability
The bridge on-board the OceanXplorer
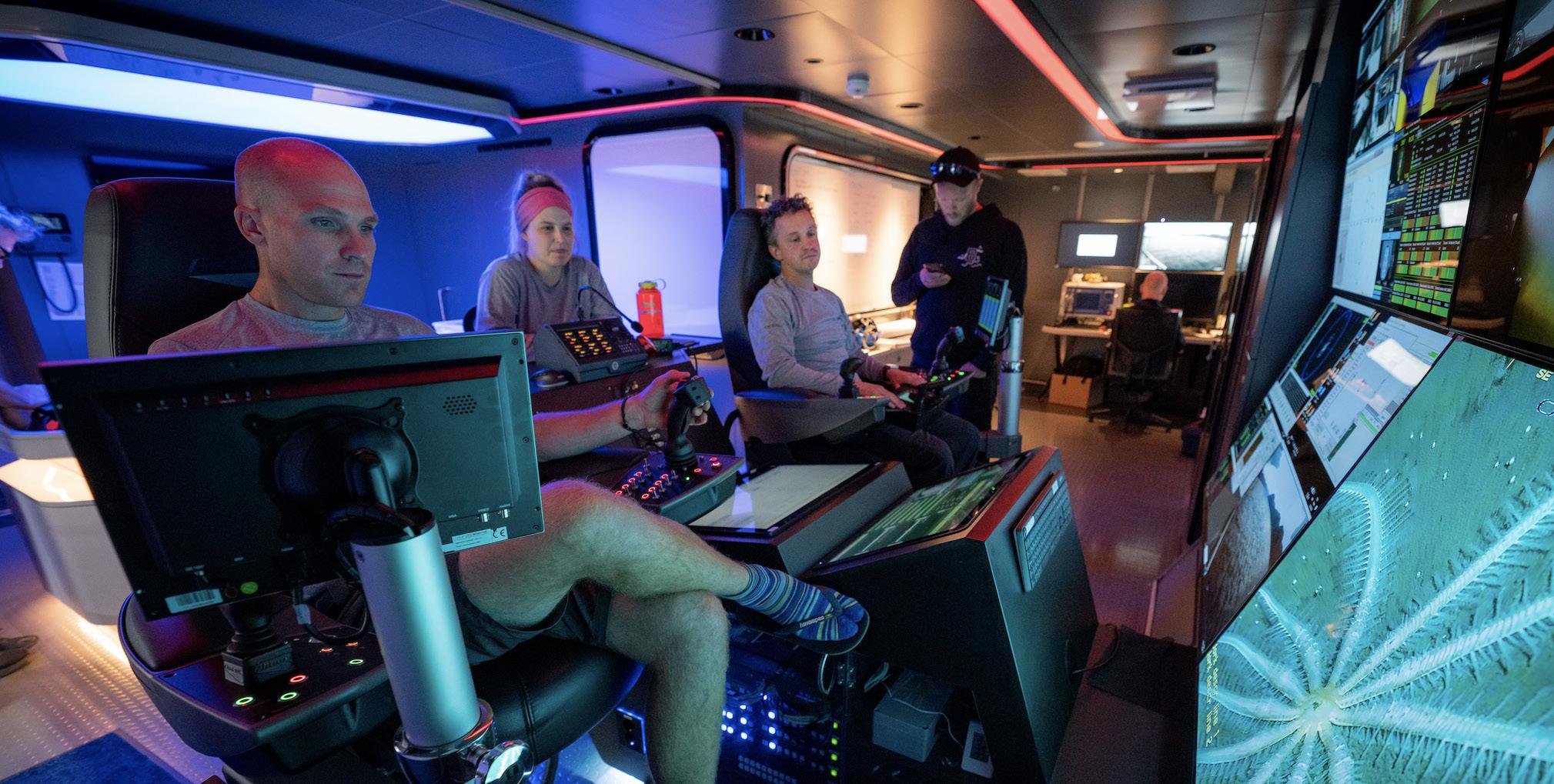
to continue working safely during this time.” Umm Al Anber, operated by Abu Dhabi-based
National Marine Dredging Company (NMDC) has completed the refurbishment of its cutterhead shaft bearings as part of an extensive refit at Dubai Maritime City (DMC).
Thordon Bearings’ Dubai-based distributor for the Middle East, Ocean Power International LLC (OPI), replaced the cutterhead and intermediate line shaft bearings like-for-like with Thordon’s water-lubricated Composite system. The turnkey project included shaft dismantlement, laser alignment, in-situ line boring, calibration, installation and commissioning. The 1995-built
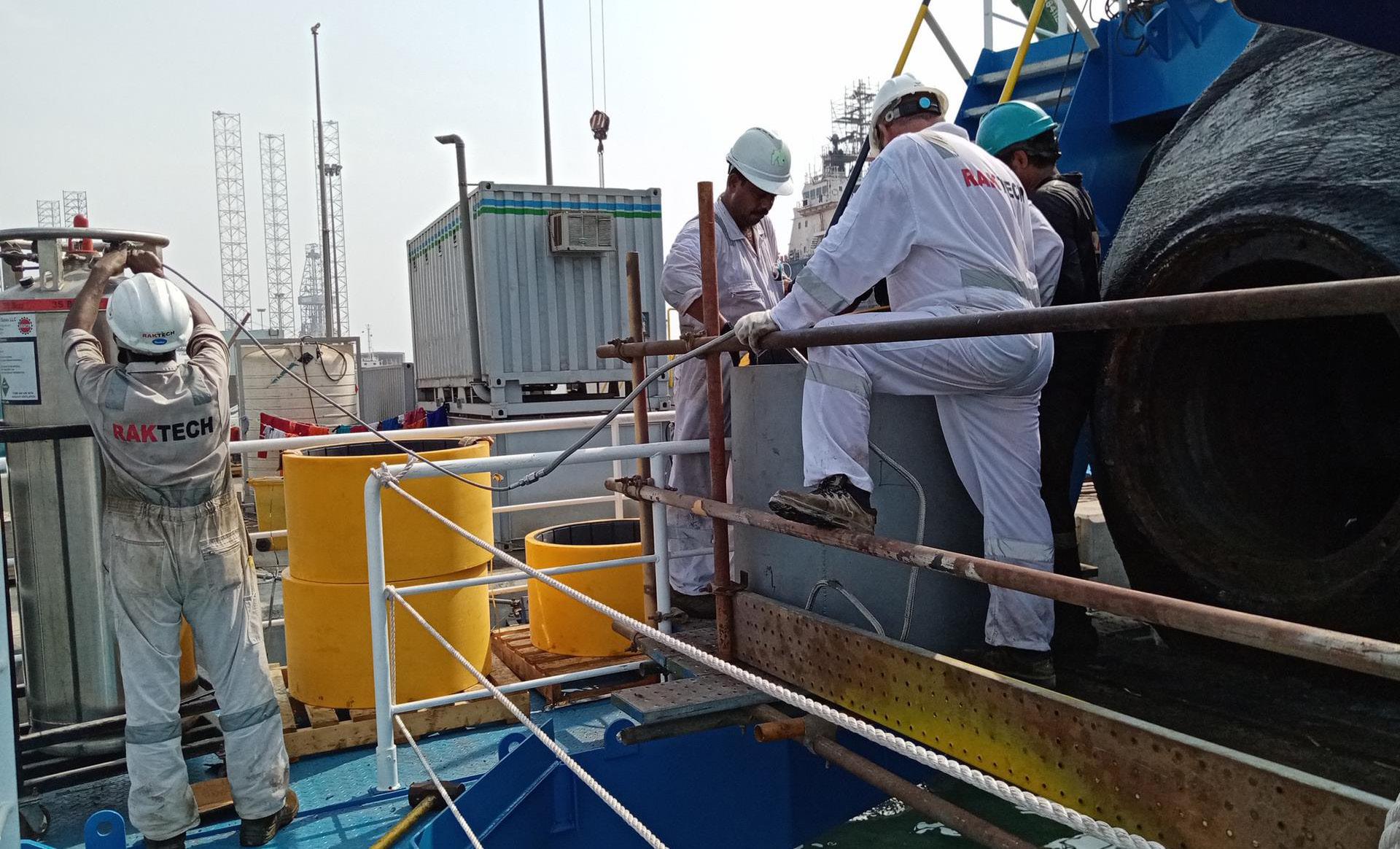
Thordon’s Composite bearings being prepared for installation
Umm Al Anber has an 800 mm diameter suction pipe and can dredge to depths of 16 m.
Mohammed Fawzy Khalifa, Fleet Manager, NMDC, said, “We have been using Thordon’s grease-free elastomeric polymer bearings since the 1990s. Compared to traditional rubber cutterhead bearings, we find that Thordon Composite reduces vessel operating costs substantially. The bearing requires no lubricating grease and extends bearing wear life fourfold, which is very impressive given the type of environments in which these dredgers operate.”
Rafid Qureshi and Ayman Saad, Managing Partners, Ocean Power International LLC, said, “Together, OPI and Thordon Bearings have been optimising the performance of NMDC’s cutterhead dredgers for more than two decades. Thordon Composite bearings are the preferred choice for NMDC dredgers.”
NMDC has converted all of its dredgers except two to the Thordon system. However, Qureshi revealed OPI is in discussions to convert the rubber bearings aboard these final two vessels. “We are also in talks to convert the intermediate line shaft bearing to Composite. Replacing worn out rubber bearings with Thordon’s ever-lasting material offers NDMC excellent wear rates, high performance in harsh, abrasive environments, and reduced OPEX,” he said.
George Morrison, Thordon Bearings’ Regional Manager, added, “NMDC – one of the world’s leading dredging companies with a fleet of more than 90 vessels – has established a strong reputation for delivering high quality projects and services. It is nice to think that Thordon’s water lubricated Composite cutterhead shaft and intermediate bearings have played an important role in that success.”
Late last year, OPI and Thordon replaced the rubber cutterhead shaft bearings on the CSAD Al Khatem and the beaver dredgers Embarka 2, Embarka 5 and Embarka 6. The projects followed the success of similar conversions to the Al Sadr, Al Mirfa, Al Hamra, Umm Al Zemoul and the beaver Dredge 2 .
After 100,000 operating hours dredging up silt, sand, rocks and stones in some of the toughest marine environments the Thordon Composite
bearing installed on the Al Mirfa’s dredge cutterhead shaft, “did not need replacing and was still in perfect working condition,” said Morrison.
“This is due to the bearing’s black homogeneous material, GM2401, which is fused to a stiff, high strength (yellow) polymer sleeve to provide unprecedented performance and environmental safety. Thordon Composite bearings are available for a wide range of shaft diameters in both tube and stave configuration.”
Meanwhile, Venables Machine Works, a large manufacturing and machining firm based in Saskatoon, Saskatchewan, Canada, has been appointed as an authorised distributor and service provider for Thordon Bearings’ industrial bearings portfolio.
The formal agreement follows a ten-year collaboration in which Venables provided sales and engineering support to Thordon’s customers across Manitoba, Saskatchewan and Alberta.
Scott Groves, Regional Manager, Thordon Bearings, said, “We have enjoyed a partnership with Venables in the Canadian Prairies for several years, manufacturing Thordon finished parts and providing excellent service and value to our customers. Because of this service and capability, Thordon looked to Venables when the territory became available. We are very pleased to have Dustin Maffin and his team handling our pump and industrial business in the area.”
The company, which will focus on Thordon’s SXL and XL polymer bearings and engineered
Composite cutterhead bearing installed on the Umm Al Anber
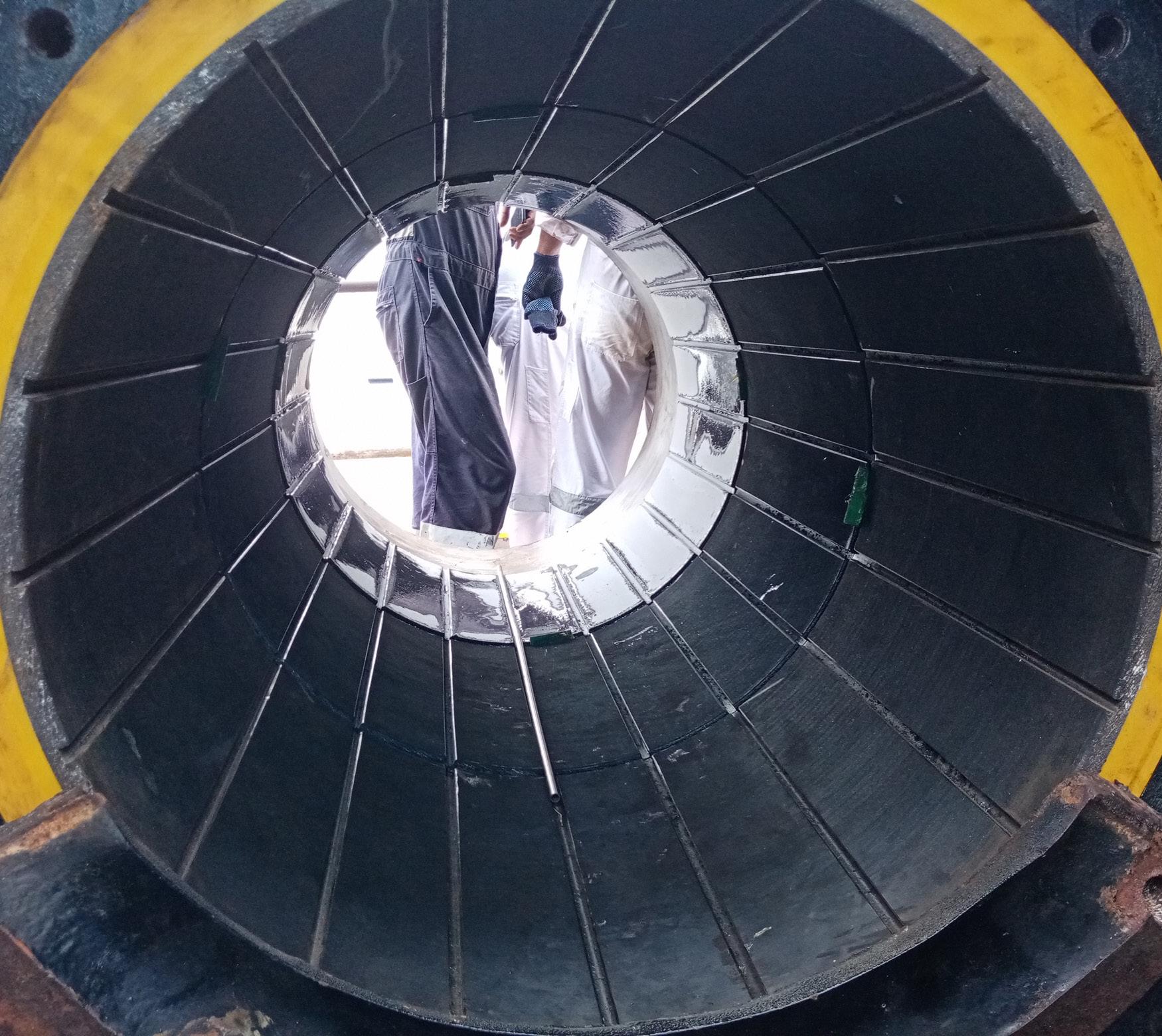
thermoplastics, ThorPlas-Blue and ThorPlasWhite, has a successful history providing custom pieces for Canada’s steel mills, the region’s mining industry and generally supporting industrial pump and machinery repairs.
CFS COMPLETES GLOBAL OFFSHORE PROJECT
UK’s Complete Fabrication Services (CFS), based in the North East of England has supported Holland’s Royal IHC to deliver a major conversion of Global Offshore’s 11,472 gt multi-purpose offshore support vessel Normand Clipper. The work was carried out alongside in the Port of Blyth.
The Normand Clipper was built in 2001 as a Cable Laying and Repair Vessel. She underwent a major conversion in 2005 to a deepwater subsea construction and umbilical lay DP vessel. Having been acquired by Global Marine Group it will now be deployed to support cable lay operations within the renewable energy and oil & gas sectors.
Global Offshore, part of the Global Marine Group, were awarded a contract for cable installation and burial of the Pentland Firth East submarine cable, a new 35 kms, 33 kV power cable, which will connect mainland Scotland to Hoy. Royal IHC was appointed as main contractor for the extensive conversion and upgrade of the vessel for this assignment. The extensive works included five winches ranging from 2.5 tonne to 20 tonne, some with anti-heave compensation, an integrated deck control station, two 15 tonne cable tensioners, a 25 tonne quadrant deployment frame with associated steel work and a fully integrated control system – all to be completed whilst berthed in the Port of Blyth.
Having worked successfully with Global Marine Group over the years, CFS was approached by Royal IHC, to fabricate and install a number of strategic structural equipment items on-board the vessel.
The Normand Clipper
CFS was able to turn around the RFQ in two days with the scope of works including the fabrication, painting and finishing of: • Two overboard Chutes • Deck support tables for the chutes • Roller tables • Grillages • CPS tables • Quadrant deployment rail system • Overboard quadrant (DNV GL certified)
This represented a six figure project for CFS - fabricating and installing over 100 tonnes of fabricated class approved steel components. CFS was able to deliver this successful project during the COVID-19 world-wide pandemic - ensuring complete safety of their team and of their stakeholders, no mean feat when considering the operational challenges experienced by the industry during the crisis.
Darren Carlisle, Managing Director, CFS said, “This was a very large and complex project that required very tight deliveries, however it was one that suited our fabrication and mobilisation capabilities. Our open and proactive
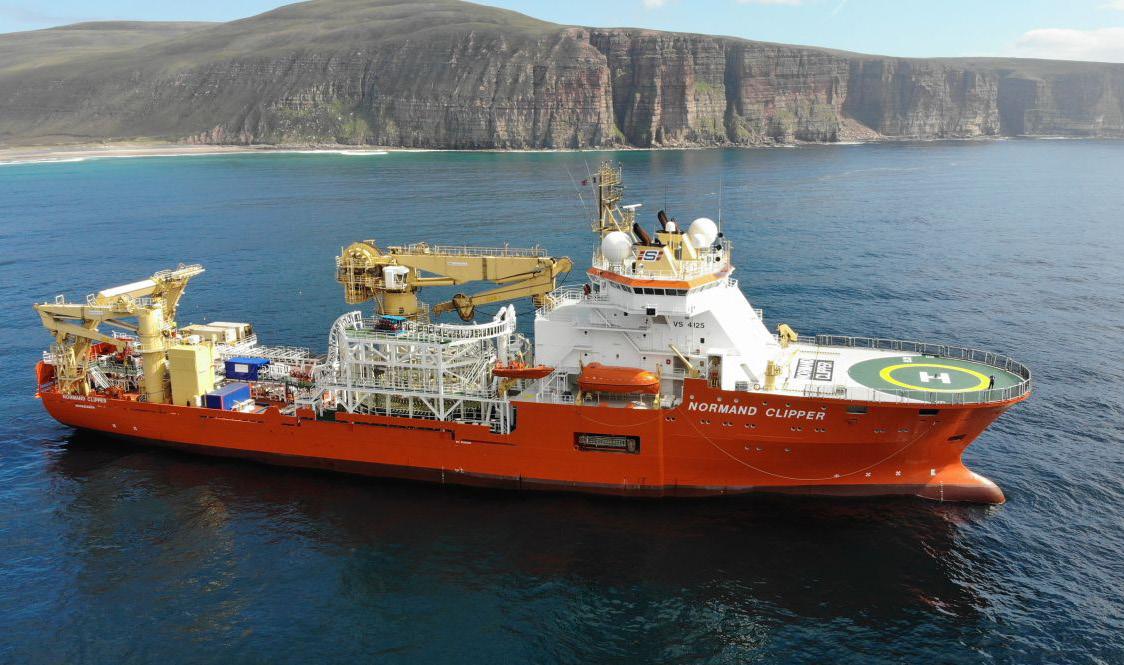
communication with our client, stakeholders and supply chain enabled us to deliver this fantastic project during a very challenging time with the global pandemic.”
CFS will carry out further modifications on the Normand Clipper when she returns to the Port of Blyth after completion of her second assignment installing a power cable across the Pentland Firth Strait.
DREDGER REPAIRS IN A&P
Despite the challenges of Covid-19, A&P Group has continued to be in high demand by dredger operators. A&P Tees has played host to several dredgers in recent months, continuing to build on its reputation as a centre of excellence in the field.
Tees & Hartlepool Port Authority’s 1,458 m3 TSHD Cleveland County drydocked for four days in the summer months for steel repairs, while Hanson Aggregate Marine’s 4,600 m3 TSHD Arco Dijk drydocked for three days for urgent
mechanical works. UK Dredging’s 3,900 m3 TSHD UKD Bluefin recently departed A&P Tees following the completion of significant maintenance works.
Tarmac continues to utilise A&P Tees for the company’s fleet of TSHDs, with the facility completing a successful repair and maintenance docking of the 3,840 m3 City of London. The 2,793 m3 City of Westminster was recently in drydock number five for repair and maintenance work. A&P’s Falmouth facility has also welcomed the 1,418 m3 sisterships City of Cardiff and City of Chichester for maintenance and repair works
Chris Davies, Business Development Manager for Marine at A&P Group said, “Providing urgent support to dredger clients is essential to keep these important vessels fully operational. A&P is particularly well suited to the dredger market thanks to its prominent river location, two drydocks, 240 m of jetty frontage, workshops, cranes and secure tanker berth, as well as the trusted expertise of our team.”
David McGinley, Chief Executive Officer of Cammell Laird Ship Repairers and Shipbuilders and Atlantic & Peninsula Marine Services, said,
The City of Cardiff in drydock in A&P Falmouth
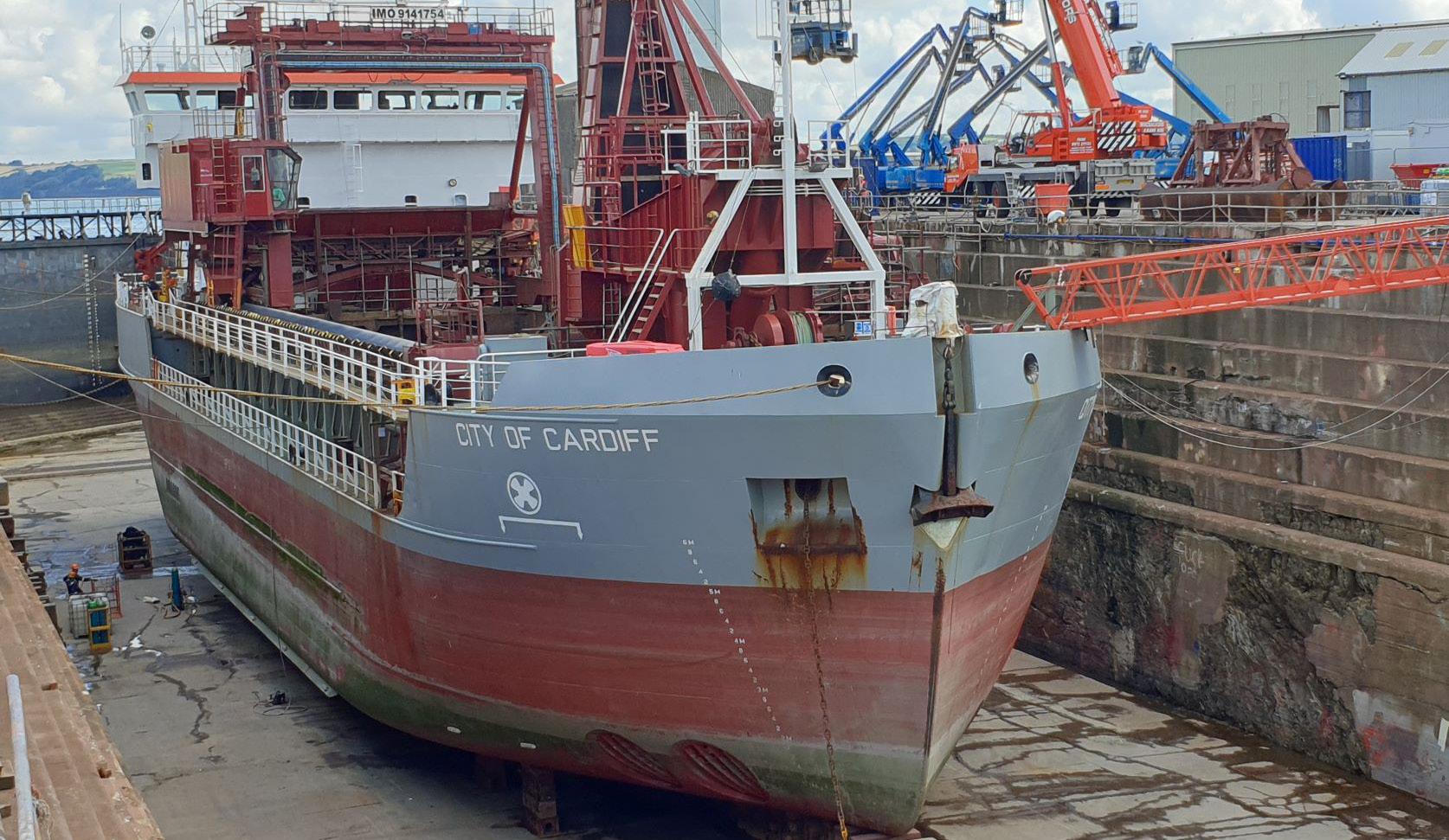
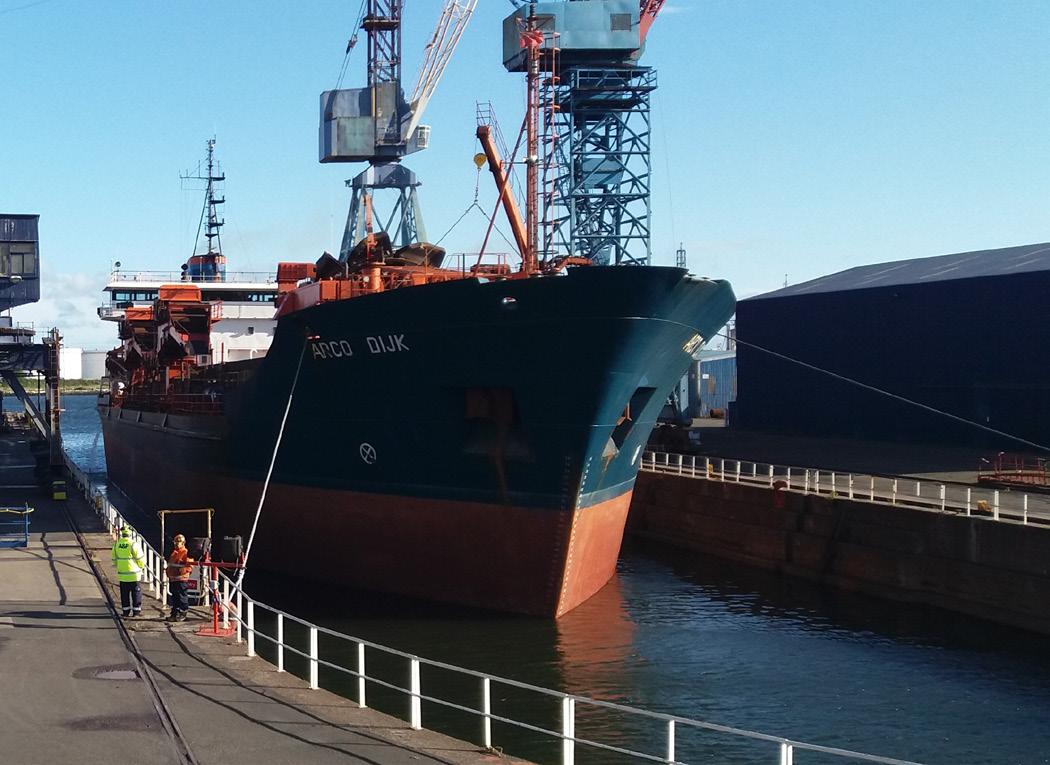
The Arco Dijk in A&P Tees
“Dredging keeps our waterways and ports navigable, so it’s essential that A&P supports operators by keeping their vessels in the best condition and minimising downtime. Our onsite fabrication capabilities, focus on pre-planning and exacting project management play a pivotal role in making this possible and extending dredger life significantly.”