
21 minute read
WIND
The Groene Wind being launched
LAUNCH OF DEME’S FIRST EVER SERVICE OPERATION VESSEL GROENE WIND
Advertisement
DEME has launched its first ever Service Operation Vessel (SOV) at the CEMRE shipyard in Yalova, Turkey, marking a major milestone in its fleet history. Named Groene Wind, the Small Waterplane Area Twin Hull (SWATH) vessel will be deployed for wind farm maintenance activities.
The Groene Wind is due for delivery in 2021 and will be directly chartered to Siemens Gamesa Renewable Energy for the maintenance of the Rentel and SeaMade offshore wind farms offshore Belgium. This is the first DP2, twin-hulled SOV in the world and the first to serve three different wind farm sites.
Investing in such a pioneering vessel also means that DEME can offer the total package of services to the offshore wind industry now - from installation right through to maintenance. DEME’s in-house newbuild team worked in close collaboration with Vuyk Engineering Rotterdam and research institute MARIN. The new vessel significantly improves safety, comfort and workability for wind farm technicians - even in the roughest sea conditions. Impressive cuts in fuel consumption The SWATH design ensures low wave impact on movements when approaching wind turbines, compared to a traditional monohull SOV. Groene Wind will enable safe crew transfers in significant wave heights. Her DP2 technology means that the vessel can hold its position in rough seas but at the same time operate with lower fuel consumption when compared to traditional SOVs. An impressive fuel consumption reduction of up to 50% can be achieved compared to a monohull SOV, further reducing the cost of wind farm maintenance.
In line with her green credentials, environmental considerations are integral to the vessel design and include a waste heat recovery system and a Clean Design notation.
Safety and comfort
At 60 m long, the SOV will be equipped with a motion compensated gangway and daughter craft to safely transfer technicians to the wind turbines. It is also designed according to the latest comfort standards, allowing the vessel to be a homely offshore base for up to 24 technicians and a nautical crew.
WIND
GREEN JADE STEEL CUTTING GETS UNDERWAY
In a strong signal highlighting its confidence in the offshore wind sector, CSBC-DEME Wind Engineering (CDWE) recently held a strike steel ceremony in Taiwan, when work officially began on its pioneering installation vessel Green Jade .
Representatives from the Hai Long and Zhong Neng offshore wind farm projects, ABS and the CR Classification Society were present at the ceremony. The vessel is the first floating DP3 heavy lift and installation vessel to be built in Taiwan and she will sail under the Taiwanese flag.
Being built at CSBC in Kaohsiung, Green Jade will feature an exceptional combination of high transport and load capacity, impressive lifting heights and green technology. The vessel has a 4,000-tonne crane capacity and DP3 capability, which will enable CDWE and its customers to transport a multitude of the next generation, multi-megawatt turbines, jackets and components in a single shipment, making it extremely cost effective.
At 216.5 m long, Green Jade has a spacious, unobstructed deck and can comfortably accommodate a crew of up to 160 people. She will be capable of installing these mega monopiles and jackets at greater water depths and her DP3 technology enables the vessel to continue operations under the most challenging conditions.
She has dual fuel engines and a Green Passport and Clean Design notation. Other environmental innovations include a waste heat recovery system that converts heat from the exhaust gases and cooling water to electrical energy, in addition to various other fuel-saving measures.
CDWE, Taiwan’s first offshore wind EPCI contractor, was established in February 2019 by CSBC, the largest shipbuilder in Taiwan, and DEME Offshore. The steel cutting ceremony is a major milestone for the joint venture, which has already secured several important contracts in Taiwan’s flourishing renewables sector.
Set to enter service in 2022, Green Jade will be deployed for both the Hai Long Offshore Wind Project and at Zhong Neng for Zhong Neng Wind Power Corporation Preparatory Office. CDWE signed Taiwan’s first comprehensive, large-scale Balance of Plant Preferred Supplier Agreement with Hai Long Offshore Wind Project in October 2019. For Zhong Neng, the contracts comprise the transportation and installation of the foundations, as well as a Preferred Bidder Agreement for the transportation and installation of the turbines.
An artist’s impression of DEME’s Green Jade
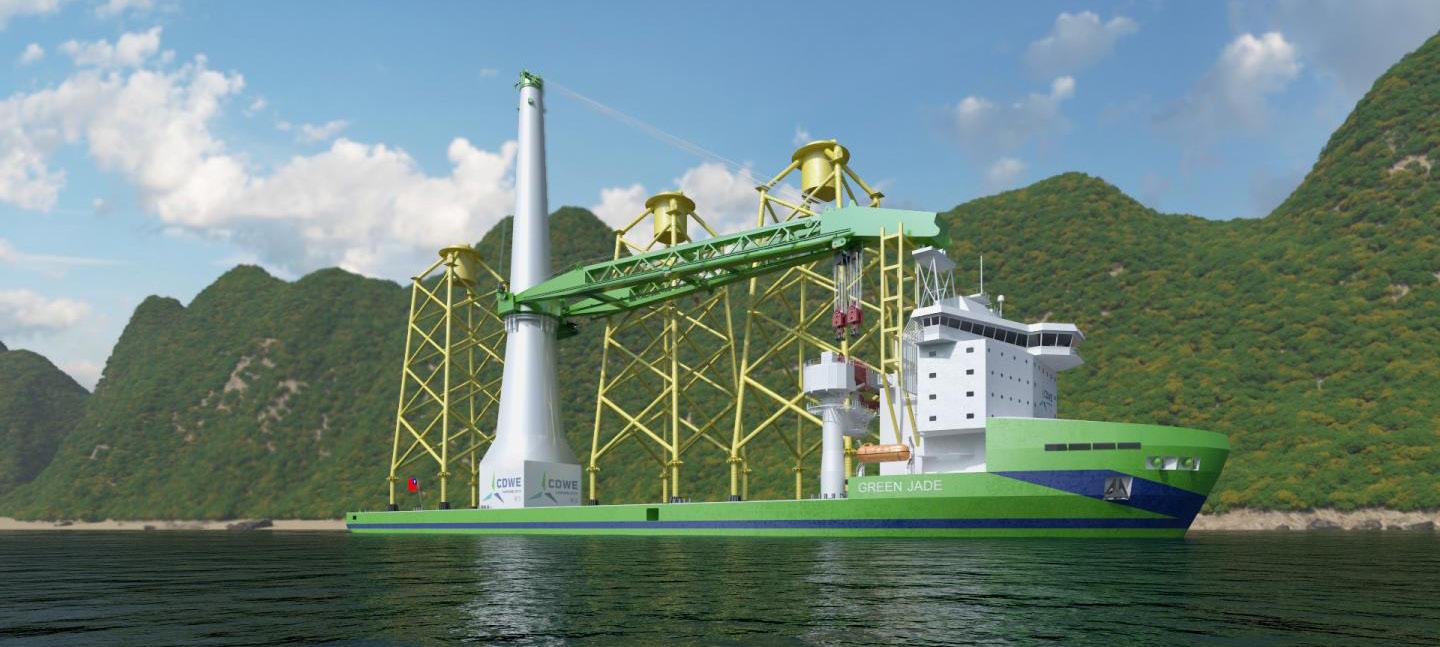
DEME engineers celebrate the loading of the last jackets

LAST JACKETS LEAVE DUBAI FOR THE MORAY EAST OFFSHORE WIND FARM
In an important milestone the last jackets for the 950 MW Moray East offshore wind farm were safely loaded onto the heavy lift vessel at Rig Metals LLC (part of Lamprell) in Dubai ready for their onward journey to Europe, under the management of DEME Offshore.
DEME Offshore was awarded the full EPCI scope for 100 wind turbine foundations plus three offshore substation platform foundations in December 2018. To ensure a timely production flow, DEME Offshore contracted Lamprell for the fabrication of 45 wind turbine foundation jackets and three offshore substation jackets. The remaining 55 jackets were awarded to Smulders, where the works are still ongoing on the fabrication yards in Belgium and Newcastle (UK).
In another key milestone and despite the many challenges brought about by the coronavirus pandemic, DEME Offshore successfully installed the third and final offshore OTM substation on schedule last weekend.
Bart De Poorter – General Manager DEME Offshore commented, “Managing to perform the seamless installation of the third offshore substation and keeping foundation production firmly on schedule are both something we can be proud of given the unprecedented challenges we have faced. This is only possible by meticulous management, thorough preparations and by working closely with our customer and partners .”
MACGREGOR WINS ALFA LIFT CONTRACT
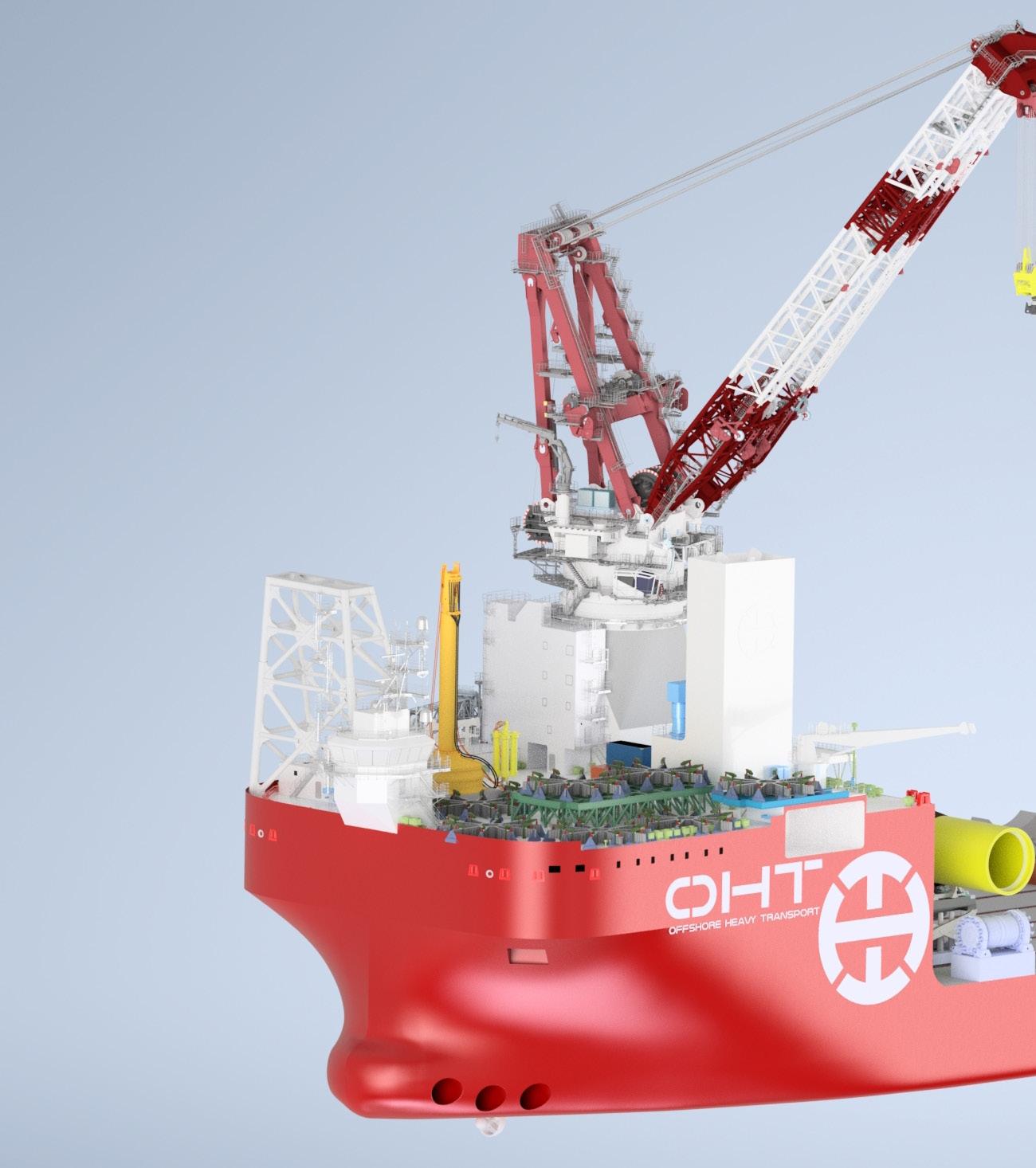
MacGregor, part of Cargotec, has received a significant order for delivery of the mission-critical system to be installed on the OHT offshore wind foundation installation vessel, Alfa Lift, being built at the China Merchants Heavy Industry shipyard in Jiangsu, China.
The monopile installation system is scheduled to be delivered during the fourth quarter of 2021. MacGregor, part of Cargotec, has received a significant order for delivery of the mission-critical system to be installed on the OHT offshore wind foundation installation vessel, Alfa Lift, being built at the China Merchants Heavy Industry shipyard in Jiangsu, China.
The order, which is the largest single vessel contract secured to date by MacGregor, was booked in Cargotec’s 2020 third quarter order intake. The monopile installation system is scheduled to be delivered during the fourth quarter of 2021.
Scope of supply includes the engineering, procurement and construction of the monopile lifting, skidding and transfer system, which is an integral part of the installation process undertaken by employing an upending tool and motion compensated gripper frame.
The motion-compensated gripper frame will be closely interfaced with the vessel’s dynamic positioning and control system in an integrated solution developed jointly by MacGregor and Kongsberg Maritime (KM). Both companies believe that the application of automated handling solutions will increase the safety, productivity and consistency of the installation operation, resulting in substantial cost and time savings.
The Alfa Lift is scheduled for delivery in 2021 and will be the world’s largest custom-built offshore wind foundation installation vessel. She will feature a 3,000 tonne main crane, a 10,000+
An artist’s impression of the Alfa Lift
m² smart deck, capable of carrying and installing up to 14 XL monopoles/ voyage and will be able to fully submerge the main deck to a depth of 14.66 m.
“OHT is committed to continuously advancing the development of technologies within offshore wind operations, thereby enabling complex operations to be undertaken at the highest levels of safety and efficiency. The monopile installation solution is the result of applying our collective capabilities and experience to solve market challenges and achieve optimum operability for our vessels,” says Torgeir E. Ramstad, Chief Executive Officer.
“Whenever we ask MacGregor to solve operational challenges in the demanding marine environment they, together with partners, demonstrate excellent technical understanding and respond quickly. We are extremely pleased to be working together on the exciting Alfa Lift project.”
“Working closely with MacGregor, we have developed an innovative solution that improves the efficiency of foundation installation vessels by replacing lengthy, temporary mooring processes with full DP in combination with an integrated guidance system and hydraulic frame mechanism,” says Gunnar Thorsen, SVP Business Concepts, KM AS.
MHI VESTAS RAISING THE BAR IN OFFSHORE LIFTING OPERATIONS

Installation of offshore wind turbines is about to become considerably safer thanks to the new partnership struck between renowned Danish wind turbine manufacturer, MHI Vestas, and the inventor of the world’s first remote-control load orientation solution, Verton. This exciting new partnership is the first step to transform MHI Vestas’ future installation operations in terms of speed, automation, and most importantly, safety.
Working on offshore wind projects presents unique challenges due to their inherent operational complexity and offshore location, and MHI Vestas has always been committed to continuous improvement of safety standards. As a leader in wind turbine technology it is fitting that MHI Vestas turned to a breakthrough technology to improve safety and efficiency of wind turbine installation. MHI Vestas has previously announced its range of SMART Turbine products, including SMART Dampers to actively reduce fatigue loads on wind turbine towers. MHI Vestas has now signed with Verton to produce innovative new tooling to handle the SMART Dampers during WTG installation.
Managing Director of Verton, Trevor Bourne, said that the benefits integrating Verton technology to create this specialised tooling for MHI Vestas are significant. “Working on offshore sites is difficult enough and is further complicated using taglines to control loads during lifting operations. Our Columbus 7.5 SpinPod will be capable of precisely controlling the orientation of the custom lifting yoke and its load, including setting and holding a desired orientation, even under the most challenging conditions.
“Our remote-control solution completely removes the need for taglines and for workers to be near the landing area of loads, greatly improving safety and reducing the number of workers required. The precise orientation control will also enable lifting operations to be completed faster, which is very important in an environment where every minute saved is highly valuable.”
MHI Vestas Chief Technology Officer Torben Hvid Larsen said of Verton’s technology, “With this partnership with Verton, we are introducing the next generation of load orientation equipment to MHI Vestas’ toolbox. This technology will enable us to increase our offshore handling capabilities and make our product and associated handling
MHI Vestas and Verton are partnering to transform MHI Vestas’ future installation operations
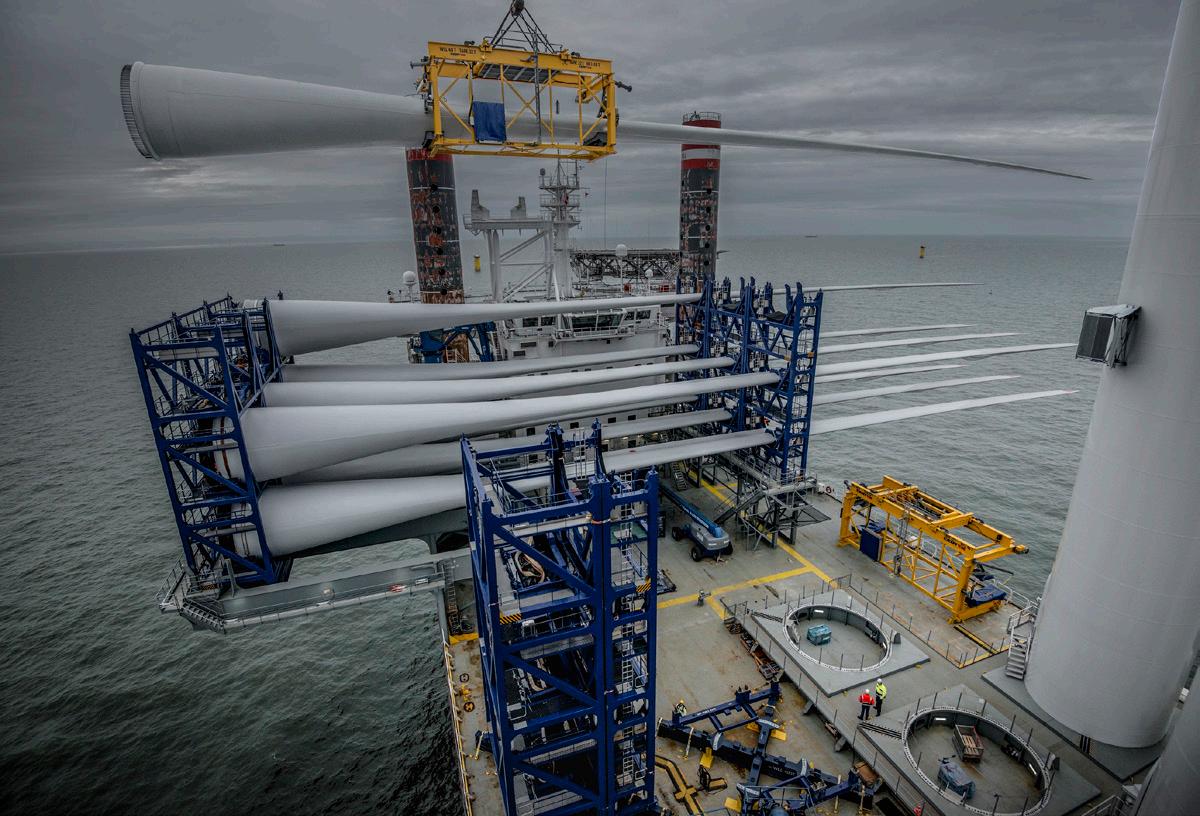
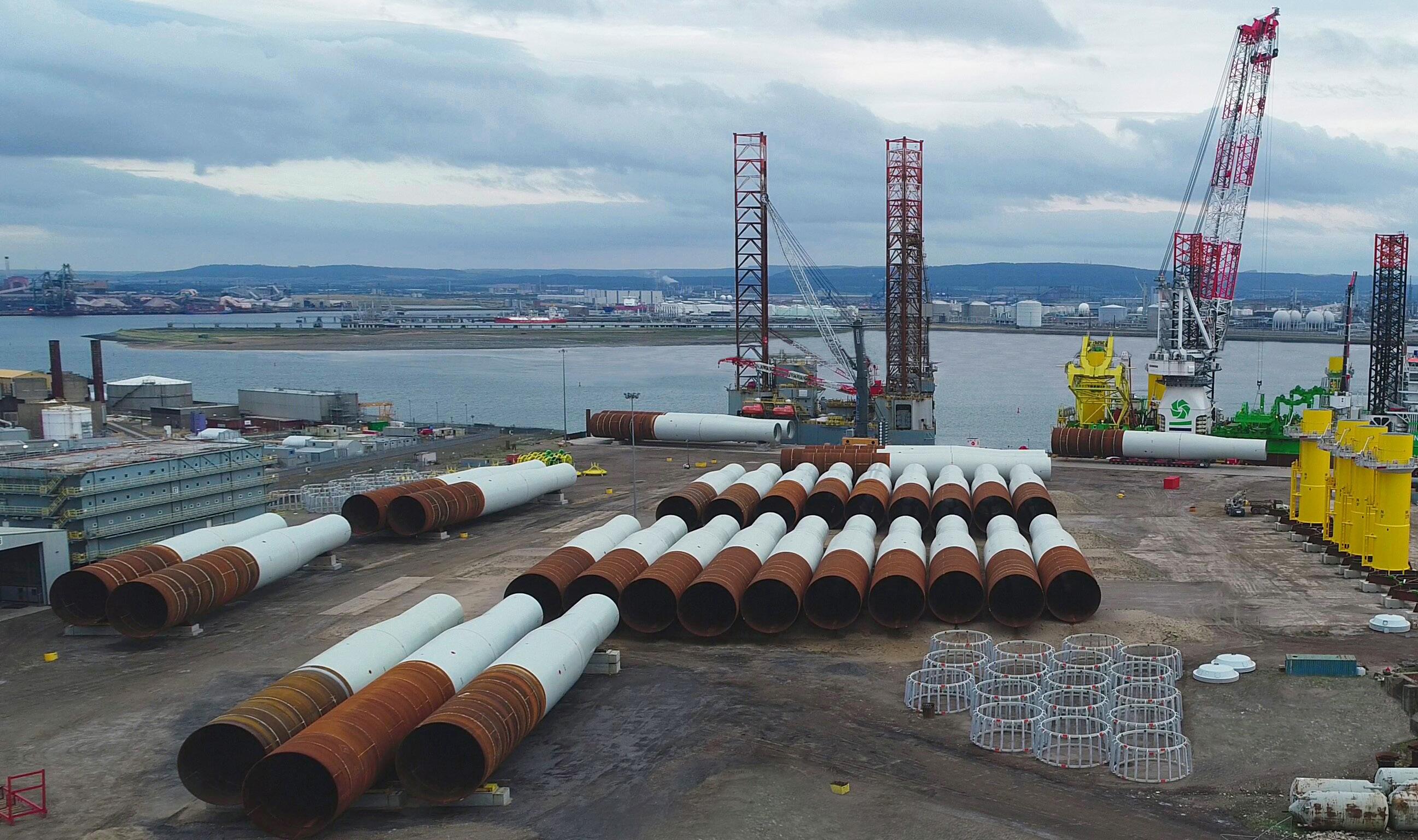
procedures smarter, safer and more flexible.”
Verton’s products are reinventing lifting operations in every area that counts. Its SpinPod technology provides the only comprehensive solution to the significant problems associated with using taglines - by making them obsolete. Verton is not only solving issues relating to safety and productivity, but also adding smart
ABLE UK WINS ORDER FOR DOGGER BANK PROJECT
Some 120 new skilled jobs are being created at Able Seaton Port, Hartlepool during the construction phase of Dogger Bank Wind Farm as the yard was recently confirmed as marshalling base for service equipment, installation and commissioning activities, as well as a further 120 skilled jobs to be based offshore and at the Port of Tyne for Operations and maintenance of the wind technology to provide HD video and on-board sensors, IoT connectivity, superior data analytics, and much more.
“Verton is providing a solution for a difficult and dangerous job, making it safer, faster and smarter,” said Mr Bourne. “It’s a necessary improvement to ensure people can come to work and then go home safe, every day.”
turbines once the wind farm is operational.
Renewable UK’s Deputy Chief Executive Melanie Onn said, “Coastal communities in Hartlepool and Port of Tyne are set to reap massive economic benefits with hundreds of new jobs on offer at a time when we need them most, as the world’s biggest offshore wind farm is built in UK waters, demonstrating innovative technology with these powerful turbines. Job creation is a key part of the UK’s offshore wind success story, with clusters of companies setting up for business in ports all around the UK.
Dogger Bank Wind Farm and GE Renewable Energy recently announced contracts confirming the 13 MW Haliade-X turbine for the Dogger Bank A and Dogger Bank B phases of the world’s largest offshore wind farm.
The contract award, which is subject to Dogger Bank A and B reaching Financial Close, includes
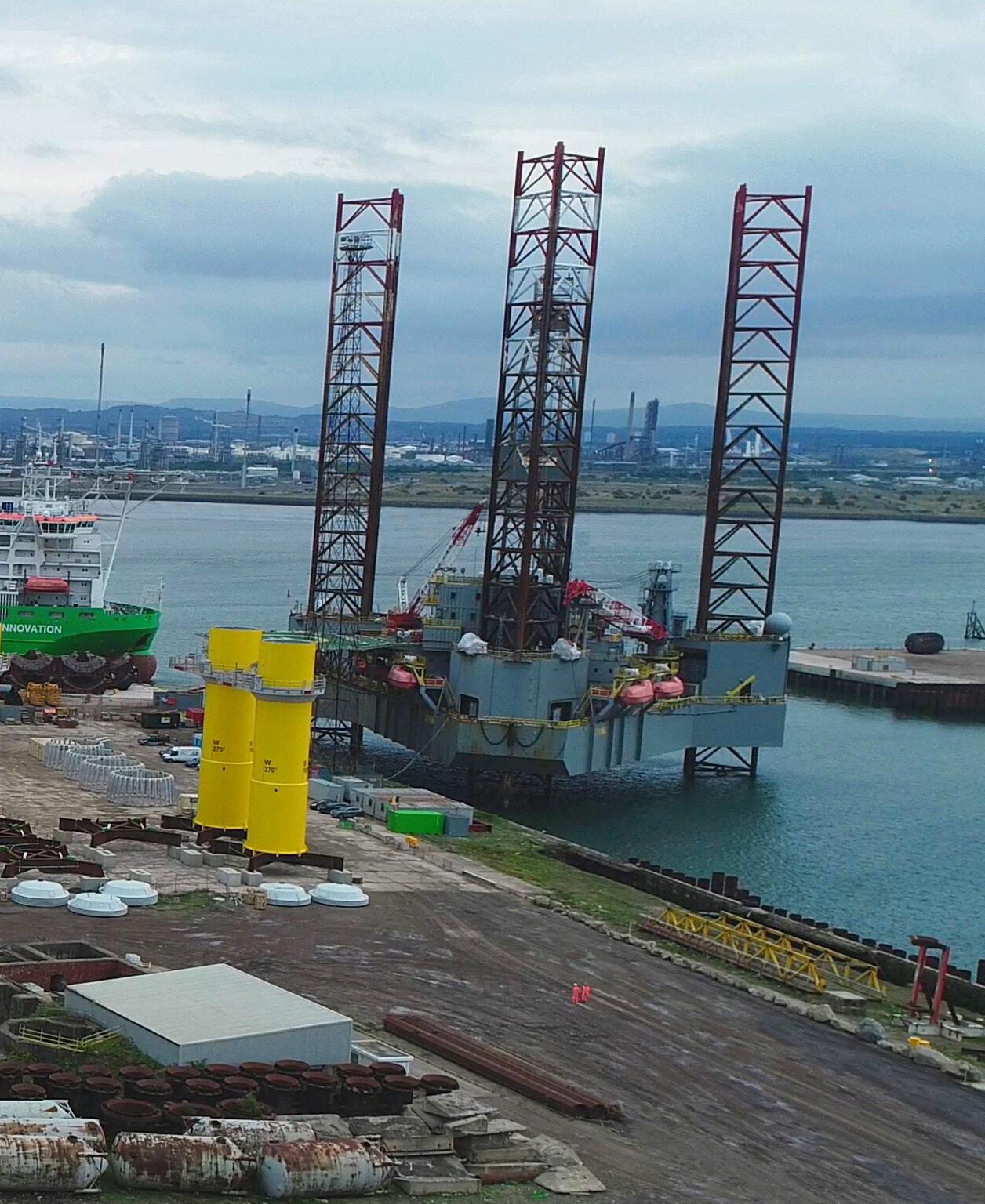
Turbine pre-assembly will take place at Able Seaton Port
an order for 190 Haliade-X 13 MW offshore wind turbines to be installed off the north-east coast of England, split evenly at 95 turbines for each of the first two phases of Dogger Bank Wind Farm.
The installation of these turbines will be the first time ever a 13 MW Haliade-X is installed in the world. One spin of the Haliade-X 13 MW can generate enough electricity to power a UK household for more than two days.
As part of the agreement GE Renewable Energy will establish its marshalling harbour activities at Able Seaton Port in Hartlepool which will serve as the base for turbine service equipment, installation and commissioning activities for Dogger Bank A and B. This will see the delivery of component parts for each of GE’s Haliade-X 13MW wind turbines to the specialist port, including the nacelle, three tower sections and three 107 m long blades, for pre-assembly onsite at Able Seaton prior to transport out to the North Sea for installation. Turbine installation is expected to commence in 2023 at Dogger Bank A.
The contract announcement also included a five-year Service and Warranty agreement supporting operational jobs in the maintenance of the wind farm. This agreement for Dogger Bank phases A and B will account for around 120 out of the total 200 long term jobs that will be based out of the Port of Tyne where the wind farm’s new Operations and Maintenance base will be located. GE’s Service team will be co-located with the Dogger Bank Operational and Maintenance team at Port of Tyne.
Dogger Bank Wind Farm is a joint venture between SSE Renewables, who are leading the construction of the wind farm, and Equinor, who will operate the 3.6 GW project during its lifetime of at least 25-years. The project is located over 130 kms off England’s north-east coast and will be capable of powering up to 4.5m UK homes each year when complete in 2026. Due to its size and scale, the site is being built in three consecutive phases - Dogger Bank A, Dogger Bank B and Dogger Bank C. Each project is expected to generate around 6 TW/hr of electricity annually.
Peter Stephenson, ABLE UK’s Executive Chairman, commented, “We have enjoyed a long and constructive relationship with GE Renewable Energy culminating in today’s announcement – it’s a massive vote of confidence for the company and the UK. Our sustained investment at Able Seaton Port means we can provide a bespoke and tailor-made solution for Dogger Bank.
“We are delighted that 120 skilled jobs will be based here at the Port, in this exciting and growing industry. The offshore wind sector will increase four-fold by 2030 through the Sector Deal, and with the increasingly demanding targets for low carbon power generation, there is an unparalleled level of market visibility. Combine this with the sectors’ extraordinary efforts in terms of developing new products and significantly reducing costs, this industry is set to become a dominant factor in a post COVID-19 UK economy.”
The Haliade-X 13 MW turbine is an enhanced version of the successful 12 MW prototype unit which has been generating power in Rotterdam since November 2019 and recently secured its provisional type certificate from DNV-GL. This prototype unit, which set a world record in January 2020 by being the first wind turbine to produce 288 MW/hr in one day, will start operating at 13 MW in the coming months as part of its ongoing testing and certification process. The uprated 13 MW Haliade-X will continue to feature 107 m long blades and a 220 m rotor.
HORNSEA TWO MONOPILE INSTALLATION STARTING
Offshore work, for what will become the world’s largest offshore wind farm, is set to ramp up in the coming weeks. Ørsted’s Hornsea Two will surpass its predecessor Hornsea One by generating 1.4 GW of clean energy once complete in 2022. Monopile work is due to commence at the wind farm location some 89 kms off the Yorkshire coast in the UK with DEME’s offshore installation vessel Innovation .
Besides the Innovation, the Pacific Orca will also begin work on location next year to support construction. Both are heavy-lift jack up vessels which use the crane lifts and manoeuvres the heavy foundation components.
In total, 165 monopiles and transition pieces will be installed at sea in preparation for the site’s 8.4 MW turbines. With a height from sea level to blade tip of 204 m, the turbines will also feature new 82 m long blades which are currently being fabricated at the Siemens Gamesa Renewable Energy blade factory in Hull.
Patrick Harnett, Hornsea Two Programme Director for Ørsted, said, “Even during these challenging times, we’re still able to take these important next steps towards the construction of this game changing wind farm. We’re extremely pleased to once again work alongside suppliers who share our vision for a greener world and look forward to the upcoming milestones that will continue to pave the way in terms of innovation for offshore wind.”
A selection of 30 transition pieces are being manufactured at EEW OSB’s factory in Teesside, with the first load out having recently been completed, whilst Danish based Bladt are supplying the additional 135 components.
Bart De Poorter, General Manager DEME Offshore, comments, “After months of detailed

DEME Offshore’s Innovation
planning and by working in close collaboration with Ørsted and our suppliers, we are delighted to kick-off the offshore installation works at Hornsea Two. We have approached this complex project as true partners, which has been crucial considering the unprecedented circumstances we are dealing with. Not only are we confronted with the challenges brought to us by the Coronavirus but we had to overcome the setback when the new offshore installation vessel Orion had a crane accident before she was delivered to DEME. We very much look forward to continuing our close partnership with this Client so we can achieve the safe delivery of this exceptional wind farm.”
Zero-emission operations can be a reality already today and do not have to be a future option, says Norway’s Ulstein. The yard’s second hydrogen hybrid design for the offshore wind industry, the Ulstein J102 zero emission wind turbine installation vessel (WTIV), can operate 75% of the time in zero emission mode. Using readily available technology, the additional cost is limited to less than 5% of the total CAPEX.
Most new jack-up designs are featuring a battery hybrid system in addition to diesel gen
sets, with a future option for hydrogen powered fuel cell system. The downside however of a highpower battery energy storage system (BESS) is its heavy weight and cost. That is not beneficial for a WTIV design, where weight savings are essential for minimising Elevated Weight and optimising the Variable Deck Load.
Rather than to opt for technology to be matured to perfection and make a design that is prepared for future hydrogen powered fuel cells, Ulstein has taken the pragmatic, yet realistic approach. “We have carefully analysed the operational cycle of WTIVs and looked at the power demand in the various modes of operations”, says Ko Stroo, Product Manager at Ulstein. “This analysis showed that approximately 75% of its time, a WTIV is in jackedup position performing crane operations. Using a combination of a hydrogen fuel cell system and a relatively small battery energy storage system (BESS) is then sufficient to meet the overall power demand on-board and crane peak loads.’
“The same design philosophy as on our first hydrogen powered SX190 design, resulted in a much more attractive business case when applied to a turbine installation vessel,” states Edwin van Leeuwen, managing director of Ulstein’s Rotterdam design office.
The hydrogen hybrid system of the Ulstein J102 design has been developed in such a way, that future developments in hydrogen technology can easily be fitted into the vessel without major modifications. “The limited availability of hydrogen bunker infrastructure in ports is often seen as a major hurdle. With our modular storage lay-out, we want to break the chicken and egg dilemma”, continues Stroo. “It creates flexibility to operate the vessel world-wide, even when bunker infrastructure is not yet present.”
“The strong focus on renewable energy and emission reduction to meet world-wide climate goals should also be reflected by investments in cleaner operations when installing offshore wind turbines,” says Edwin van Leeuwen. “Hydrogen is one of the most promising zero-emission fuels for offshore vessels and we want to be leading in developing sustainable ships.”
Main features of ULSTEIN’s J102 hydrogenhybrid zero-emission design are:
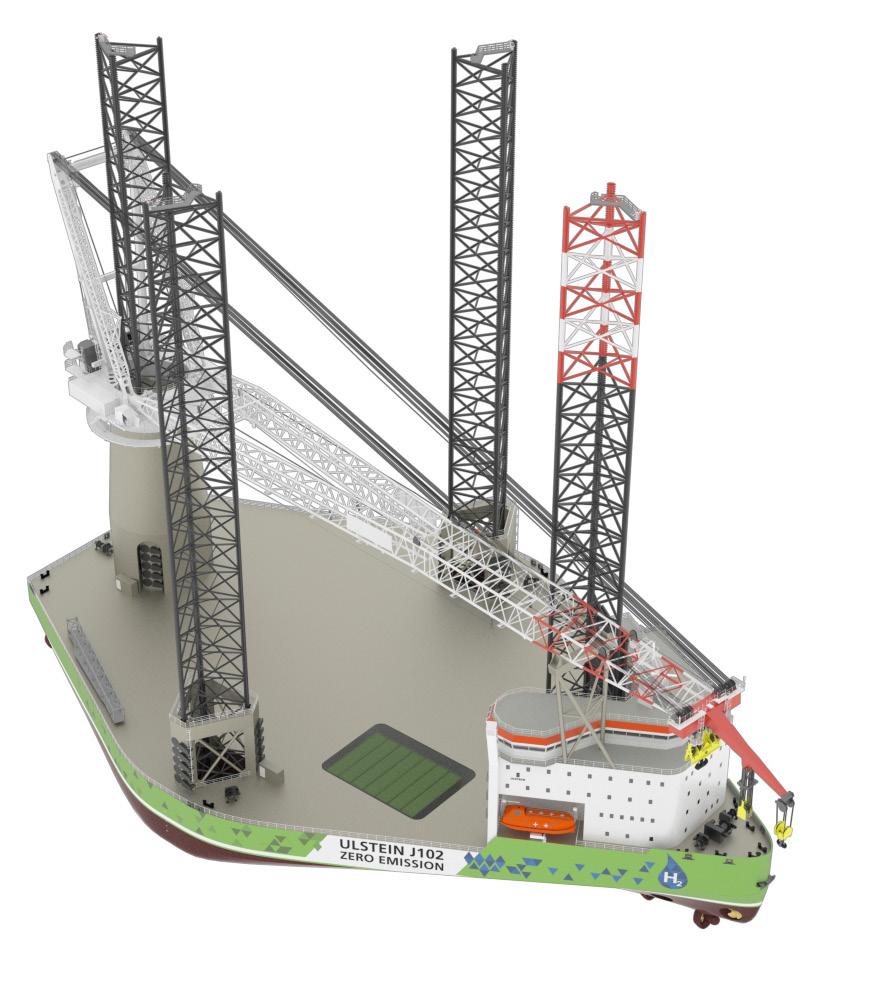
The Ulstein J102 zero-emission turbine installation vessel
• CO2 reduction/year - 4,000 tonnes • Emission reduction/installation cycle - 25 % • H2 fuel cell system - PEM fuel cell • H2 storage system - 7 x feu compressed H2 • Battery energy storage
KEPPEL SECURES CONTRACT IN THE OFFSHORE RENEWABLE ENERGY INDUSTRY
Singapore’s Keppel Offshore & Marine has secured a contract valued at approximately Sing$600m from an energy company for the engineering,
procurement and construction of a vessel for the offshore renewable energy industry. This is in line with Keppel Corporation’s Vision 2030, which includes seeking opportunities in providing renewable energy solutions.
Keppel O&M is able to provide a variety of design and construction solutions for the offshore OFFSHORE WIND To meet the future requirements of the offshore wind industry in the overall project logistics and turbine related O&M activities, Spanish engineering company Marcelo Penna Engineering and Safeway, the Dutch specialist in the design and manufacture of offshore transfer equipment, renewable energy industry. It is currently building converter stations and substations to support the offshore wind energy industry in the German sector of the North Sea and in Taiwan. It delivered and has a stake in Blue Tern, one of the world’s largest and most advanced multipurpose offshore
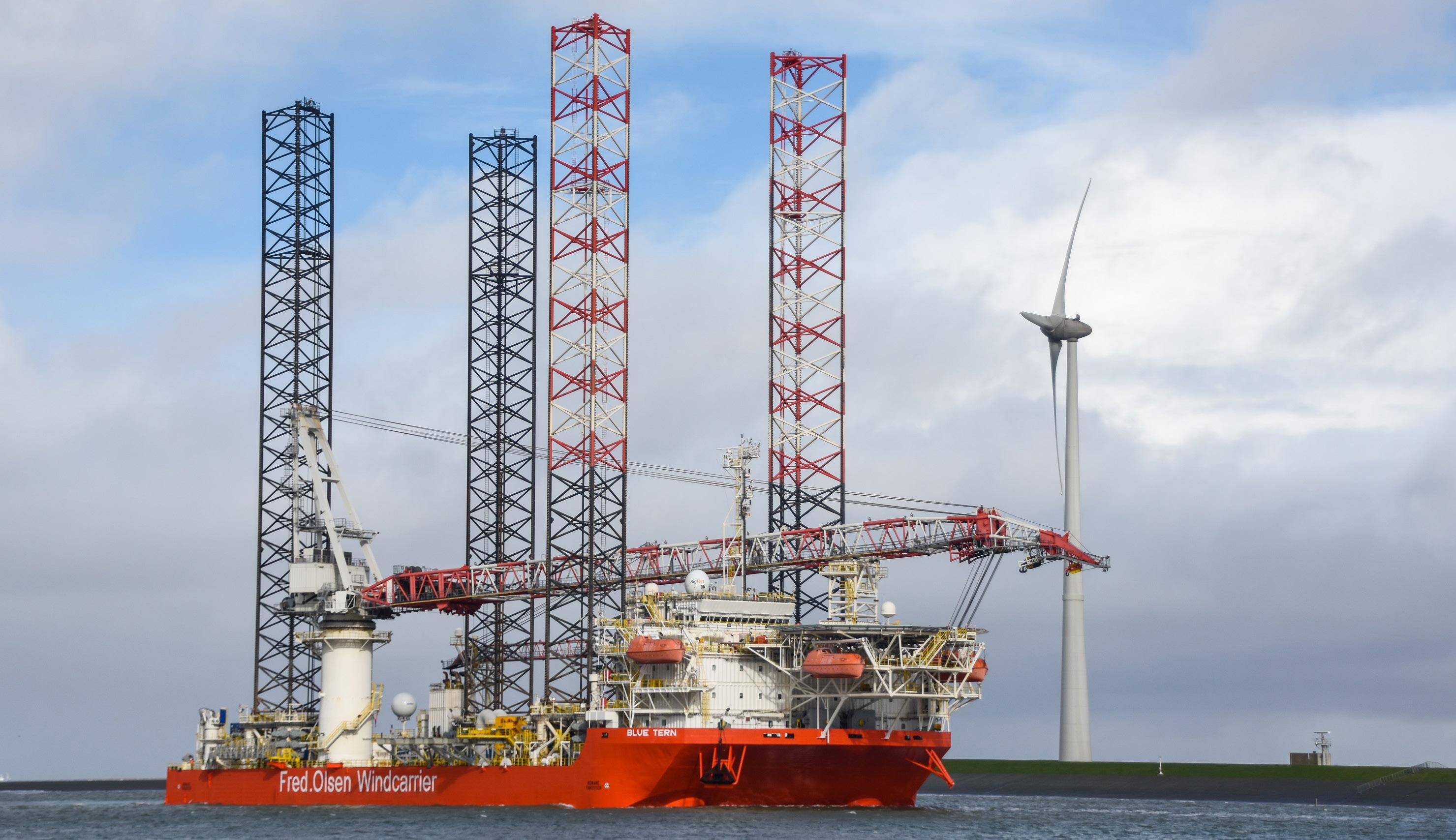
The Blue Tern
SOV/GANGWAY-CONCEPT ENSURES UNRIVALLED WORKABILITY IN
wind turbine installers for the UK North Sea. have joined forces to design an intelligent Service Operation Vessel with a very high focus on crew comfort, safety, reliability and workability in combination with lowering costs.
The outcome of the collaboration is the DP2 MP625 SOV combined with the recently
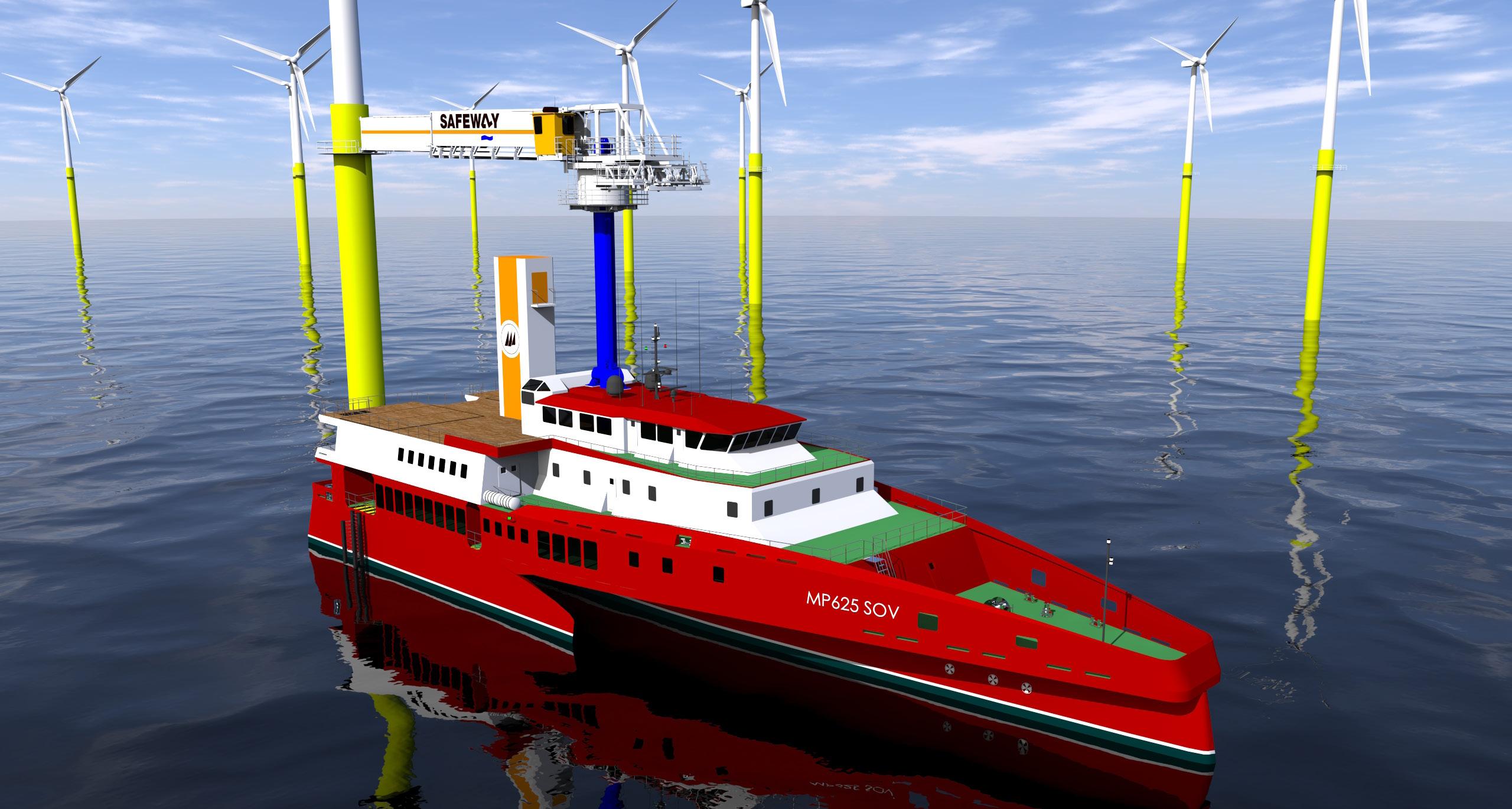
introduced Safeway Gannet 3D motioncompensated offshore access system with its unique features such as ‘zero impact bumpering’ or ‘hover-mode’ and roll compensation capability.
A big advantage of this cost-saving engineering solution is that the SOV can stay in a wind farm, even in the roughest sea conditions. And thanks to the distinctive Safeway Gannet 3D motion compensated gangway, the floating duo is able to offer a degree of safety, flexibility and effectiveness previously unseen in the international offshore gangway industry. Various simulation tests have shown that the Spanish/ Dutch combination has proven an unrivalled workability throughout the year.
“For both our companies innovation was the key driver behind this partnership. Our common goal was to come up with a high-quality design and cutting-edge technology that would minimise construction and maintenance costs, maximise operational efficiency at sea and reduce any unplanned downtime,” explained Marcelo Penna, CEO of Marcelo Penna Engineering.
“And we are confident that the MP625 SOV and Safeway’s Gannet gangway will become a popular combination in the demanding and fast-growing SOV market.”
The trimaran hull feature of the SOV gains extra value in case of high seas, as the reduction of speed is almost zero compared to a calm sea state. The design allows for up to 21 knots of maximum speed while providing full comfort for
An artist’s impression of the MP625 SOV
personnel and cargo transfers (between 1,000 and 2,000 kg) with up to 3,5 m waves, compared to the industry norm of heights - 2.5 m.
“Our Safeway Gannet 3D motion-compensated access system was developed in response to evolving requirements for fast, safe and efficient walk-to-work systems such as those being sought by Equinor and its partners for the massive offshore wind farms they plan to build on Dogger Bank,” added Wijnand van Aalst, CEO of Safeway. “Vessel and gangway must be able to connect and transfer personnel and equipment in a significant wave height of 3.5 m Hs, while the SOV must also be more compact than those built to date for services in the North Sea.”
With a length of only 64 m the MP625 is around 20 m smaller than SOVs built to date. In addition the vessel will be equipped with three strong diesel engines each of them being coupled with two electric engines offering a hybrid solution and a total output power of 4.4 MW. By equipping the SOV with lithium batteries, the vessel will be capable of remaining in DP for up to 12 hours in silent mode. All these solutions imply a very low fuel consumption. By offering the international offshore wind market this intelligent and futureproof SOV/access system concept, Marcelo Penna Engineering and Safeway aim to support wind farm developers in the realisation of projects that contribute to the transition to renewable energy.