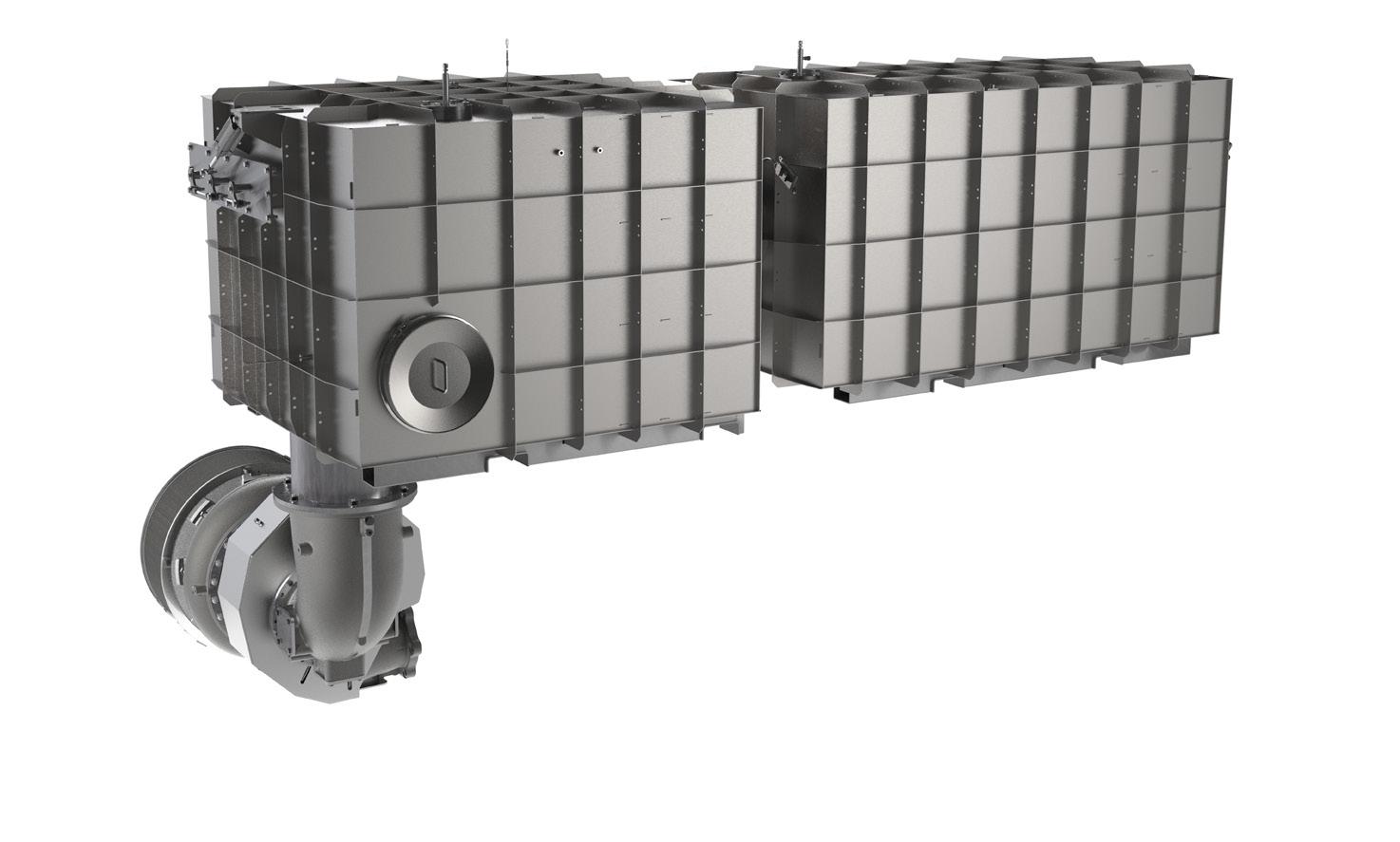
10 minute read
Emissions
KBB and Eminox combine forces
Emissions control specialist Eminox and turbocharger maker Kompressorenbau Bannewitz (KBB) have announced a major collaboration to meet increasing emissions compliance requirements for marine diesel engines. By working together, the two companies will provide marine engine manufacturers and vessel operators with a fully integrated emissions control solution, from turbo to tailpipe, to deliver clean marine diesel engines.
Advertisement
Aimed at medium speed engines over 1MW power, the new market-leading solution brings together KBB’s expertise in marine turbocharging and air handling with Eminox’s proven EMx exhaust after-treatment system (EATS) technology.
Customers will benefit from a complete, integrated solution, refined to their specific needs for both existing (retrofit) and new engines. The end-to-end solution includes the design, manufacture, installation, certification and, the breadth of knowledge and expertise from KBB and Eminox will ensure customers are supported with service, maintenance and aftersales.
This integrated project management and full in-house solution removes the need for engine manufacturers to assemble components from multiple suppliers or undertake their own costly testing and type/class approval certification. The KBB Eminox solution is optimised for specific engines which increases performance efficiency and the effectiveness of emissions reduction.
As part of the maritime industry’s commitment to achieving a zero carbon future, diesel engines are subject to IMO Tier I and Tier II regulations. Additionally, every vessel entering specific emission control areas (ECAs), including the Baltic Sea, North Sea and North American ECAs must meet much stricter IMO Tier III targets, with tighter nitrogen oxide (NOx) emissions requirements. For vessels to be compliant when operating on European Inland Waterways Stage V regulations apply.
Future legislation, including an update to the marine Stage V regulations and IMO IV are expected to set dramatically lower NOx emissions targets and introduce controls on particulates from the early 2030s.
“Diesel engines are the backbone of the marine industry, making it vital to optimise their performance to lower emissions as we move to a zero carbon future,” said David Phillips, Engineering Director, Eminox. “Working with KBB, we’re committed to helping achieve this. We’ve developed a complete, integrated solution for the maritime industry that builds on the proven strengths of diesel while reducing harmful emissions, preserving investment in existing engines. Given the need to plan for the long-term, now is the time for marine operators and engine manufacturers to accelerate their emissions reduction journey by working with partners that can provide an in-house solution for all their needs.”
Built to meet the demands of marine environments, the Eminox/KBB solution is designed for over 20 years of service, lowering operational costs, and positively supporting the resale value of engines and vessels. It is future-proofed and upgradeable as and when legislation changes. A fully serviceable solution, replacement parts are available through KBB’s global service network.
“Operators and engine manufacturers understand the need to meet more stringent marine emissions requirements, but achieving compliance has previously been complex and costly,” said Dr. Roman Drozdowski, Managing Director, KBB. “Our combined solution brings together two trusted, experienced suppliers to the industry and is built to fully address all emissions requirements, now and in the future. Together, we look forward to helping customers around the world meet maritime standards while reducing the total cost of ownership of their diesel engines.”
KBB turbochargers are on-board many ships owned by large and traditional owners, such as Maersk and Evergreen. Some 2,000 ST-EP single stage units are now in operations. Roman Drozdowski re-iterated his commitment to GHG emissions reduction at an interview with SORJ at the recent Europort exhibition, “KBB turbochargers are proven technology and can be utilised on engines as the maritime world moves into non-diesel propulsion systems. These new forms of fuel include LNG, hydrogen, methanol and ammonia.”
The KBB EMx-powered marine and power generation exhaust
Emission projects at Wärtsilä
Finland’s Wärtsilä has received marine sector commercial certification for compliance with the EU’s Stage V standards. The Stage V legislation, which came into force in 2020, tightens restrictions on non-road engines and equipment, and sets stricter limits on emissions, especially particulate matter (PM) and nitrogen oxide (NOx) emissions. The certification applies to the total solution, including the Wärtsilä 14 engine and exhausts after-treatment system.
Stage V certification is required for engines powering the European inland waterways vessels, which together comprise a fleet of approximately 17,500 ships. The first deliveries of the certified Wärtsilä 14 engine will be for two new passenger ferries being built for the Switzerland’s General Navigation Company (CGN) by Shiptec AG. The ferries will operate between Switzerland and France across Lake Geneva, with the first vessel expected to
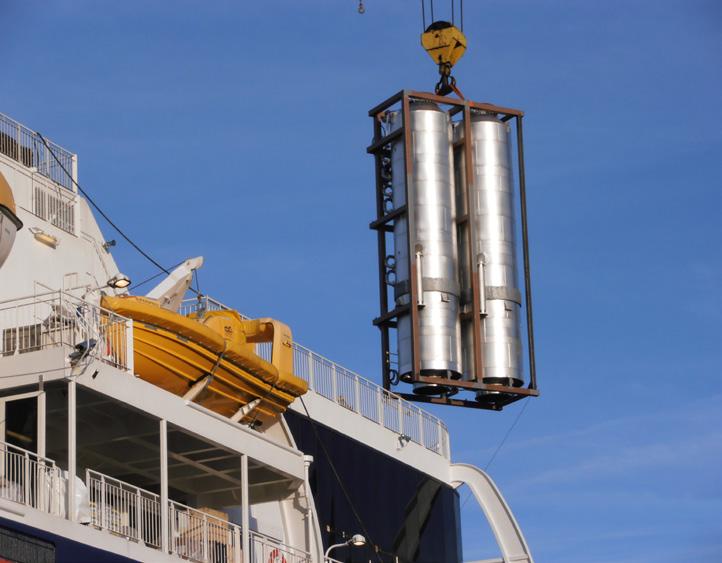
Wärtsilä will retrofit exhaust gas abatement technology on two Trasmed GLE S.L. owned passenger ferries
commence operations in December 2022.
Meanwhile, Wärtsilä, in co-operation with Silverstream Technologies, will install Silverstream’s proprietary Air Lubrication System, the Silverstream System, on a trial basis on a large containership owned by A.P. Moller - Maersk. The trial will examine possible improvements to the ship’s overall efficiency, focusing on the reduction of fuel consumption and associated emission levels. The programme will have a special emphasis on the potential application of the System for methanol-fuelled Maersk vessels. The ultimate aim of all three companies is to support efforts to decarbonise shipping operations.
Wärtsilä’s carbon neutrality target covers direct GHG emissions from the company’s own operations, including the Research & Development and factory engine testing areas as well as purchased energy.
Wärtsilä has launched its new IQ Series exhaust gas treatment system, designed by its Exhaust Treatment business unit in Moss, Norway. The IQ Series is the latest advancement in maritime exhaust gas treatment technologies, and it features several improvements that make the technology especially well-suited to container vessels, satisfying the increased demand in scrubbers as a compliance option from the containership market segment.
The IQ Series scrubber uses an innovative design that allows the same exhaust gas cleaning results to be achieved within a smaller footprint. The scrubber takes up 25% less space, is 30% lighter, and has 35% less volume, which minimises the impact on a vessel’s cargocarrying capacity, and therefore its profitability. This makes the new scrubber particularly beneficial on containerships, where space is a key commercial priority. Additionally, the scrubber – which can be configured to use between 20 and 70 MW of power depending on vessel requirements – features the same modular design as Wärtsilä Exhaust Treatment’s other exhaust gas cleaning solutions.
This means that the IQ Series can be upgraded with further technologies that enable other pollutants to be tackled within the stack, including exhaust gas recirculation (EGR) to cut NOx, a black carbon filter to cut particulate matter (PM), a depluming unit to cut visible steam from the stack, and even a carbon capture and storage (CCS) module that Wärtsilä is currently developing in its Moss test facility.
IQ Series is also a more environmentallyfriendly option for owners and operators looking at the impact of their investment decisions, with Wärtsilä manufacturing the technology using 50% recycled steel.
Wärtsilä Exhaust Treatment will install its open loop exhaust gas abatement technology on two roll-on/roll-off passenger ferries owned by Spanish company Trasmed GLE S.L., which is part of the multinational logistics company Grimaldi Group. Trasmed GLE S.L. has selected four of Wärtsilä’s I-SOx open loop scrubbers with exhaust de-plume systems for the ro/ pax vessels Volcan del Teide and Ciudad de Granada which operate in the Mediterranean Sea.
Each vessel will have four scrubbers installed, one on each main engine. The scrubbers are flexible to enable MARPOL Annex VI sulphur cap compliance, by scrubbing 3.5% HFO down to the 0.5% limit. Wärtsilä’s scrubbers will also enable Trasmed GLE’s vessels to operate at a lower 0.1% sulphur limit to meet both worldwide and ECA regulations. The installations will take place in 2022 and marks the first time that Wärtsilä has conducted a ro/pax scrubber retrofit in the region. The partnership strengthens the long-standing relationship between Grimaldi and Wärtsilä to install scrubbers in many configurations across Grimaldi Group’s business units.
First methanol-fuelled towboat operational
US-based Maritime Partners, in co-operation with Elliott Bay Design Group, e1 Marine, and ABB, have announced that the Hydrogen One, the world’s first methanol-fuelled towboat, will join Maritime Partners’ fleet and become available for charter in 2023 to meet the pressing demand for sustainable towboat operations.
Decarbonising the towboat sector poses substantial challenges, particularly due to towboats’ inherent size, space, and weight limitations. Batteries are only suitable if you operate on fixed routes and can recharge daily, and a towboat’s limited storage capacity restricts the use of pressurised or cryogenically stored gases as fuels. There are also very few dockside facilities to load such marine fuels, which severely constrains a vessel’s range and functionality.
The Hydrogen One will be IMO 2030 compliant, and meet all requirements of the US Coast Guard’s Subchapter M regulations. The ship has been designed by Elliott Bay Design Group using proven, efficient technology throughout, from ABB’s electrical power distribution and automation to e1 Marine’s methanol-to-hydrogen fuel cell, and it will be able to perform at standard operational speeds for up to 550 miles before it needs to refuel.
Methanol is a common towboat cargo, and it is available in 88 of the world’s top 100 ports. This availability enables you to refuel safely almost anywhere without the need for costly diversions. The Hydrogen One’s use of e1 Marine’s reformer technology generates hydrogen from methanol on-demand, which also makes it considerably safer than transferring and storing hydrogen directly, and the ship’s crew will require minimal additional training to use the technology.
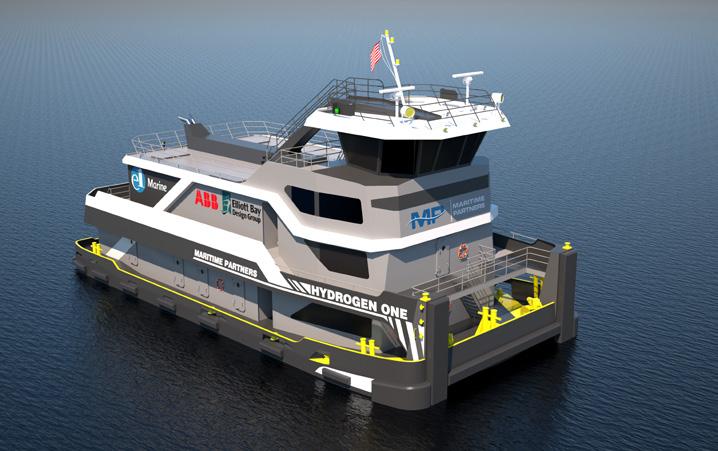
An artist’s impression of the Hydrogen One
Government funding for Tyne ferry project
UK’s Royston Marine has secured Government funding for a collaborative project to examine the potential of new technologies to reduce the
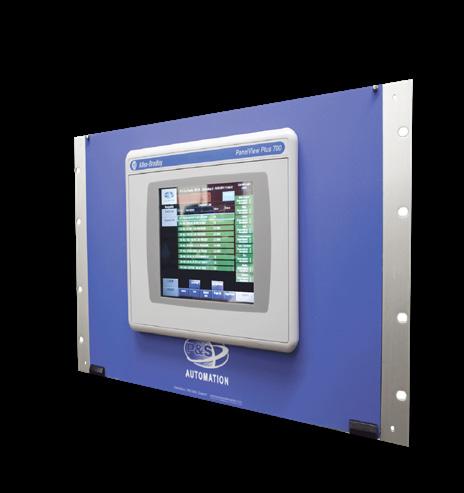
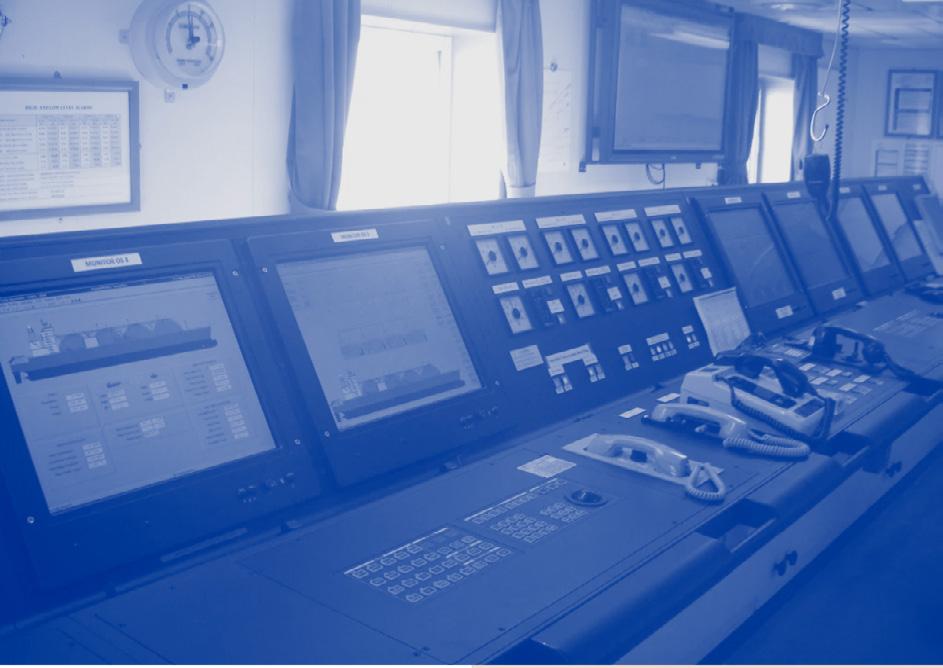
carbon footprint of river ferry services. The move will see the UK-based firm working in local partnership with Newcastle University and ferry operator Nexus to look at ways to decarbonise the operations of the cross-Tyne Shields Ferry service, which transports 500,000 passengers annually across the River Tyne between North Shields and South Shields.
Specifically, the CLEANFERRY project aims to quantify the carbon footprint of the ferries’ existing propulsion systems and assess the viability and cost benefits of retrofitting or upgrading these with advanced technology to deliver efficiency savings, lower carbon emissions and improve fuel consumption.
The project will combine the in-service Electronic Fuel Monitoring System (EFMS) capabilities of Royston with Newcastle University’s marine research expertise and the vessel operational and public service experience of ferry operator, Nexus.
CLEANFERRY is part of the Government’s wider Clean Maritime Demonstration Competition, funded by the Department for Transport and delivered in partnership with Innovate UK, with a £20m package, designed to position the UK at the forefront of green shipbuilding and maritime technology. This is also supporting 55 projects across the UK including initiatives in Scotland, Northern Ireland as well as across England.

Unit 22C & D, West Station Industrial Estate, Maldon, Essex, CM9 6TS enquiries@pandsautomation.com 01245 322777
IAS Monitor Upgrade • Automation System
Maintenance & Repair Calibration Replacement & Upgrade
• Alarm & Control Systems
• Power Management Systems
• Uninterruptable Power Supplies
• Variable Speed Drives
Alarm & Control System Designed for drop in replacement of Decca Isis Systems
UK AGENTS FOR:
WWW.PANDSAUTOMATION.COM
The scope of work will see the installation of a state-of-the-art monitoring system to provide baseline emissions’ readings in line with the UK’s clean maritime plan - which identifies ways to tackle air pollutants and greenhouse gas emissions - and review the feasibility and
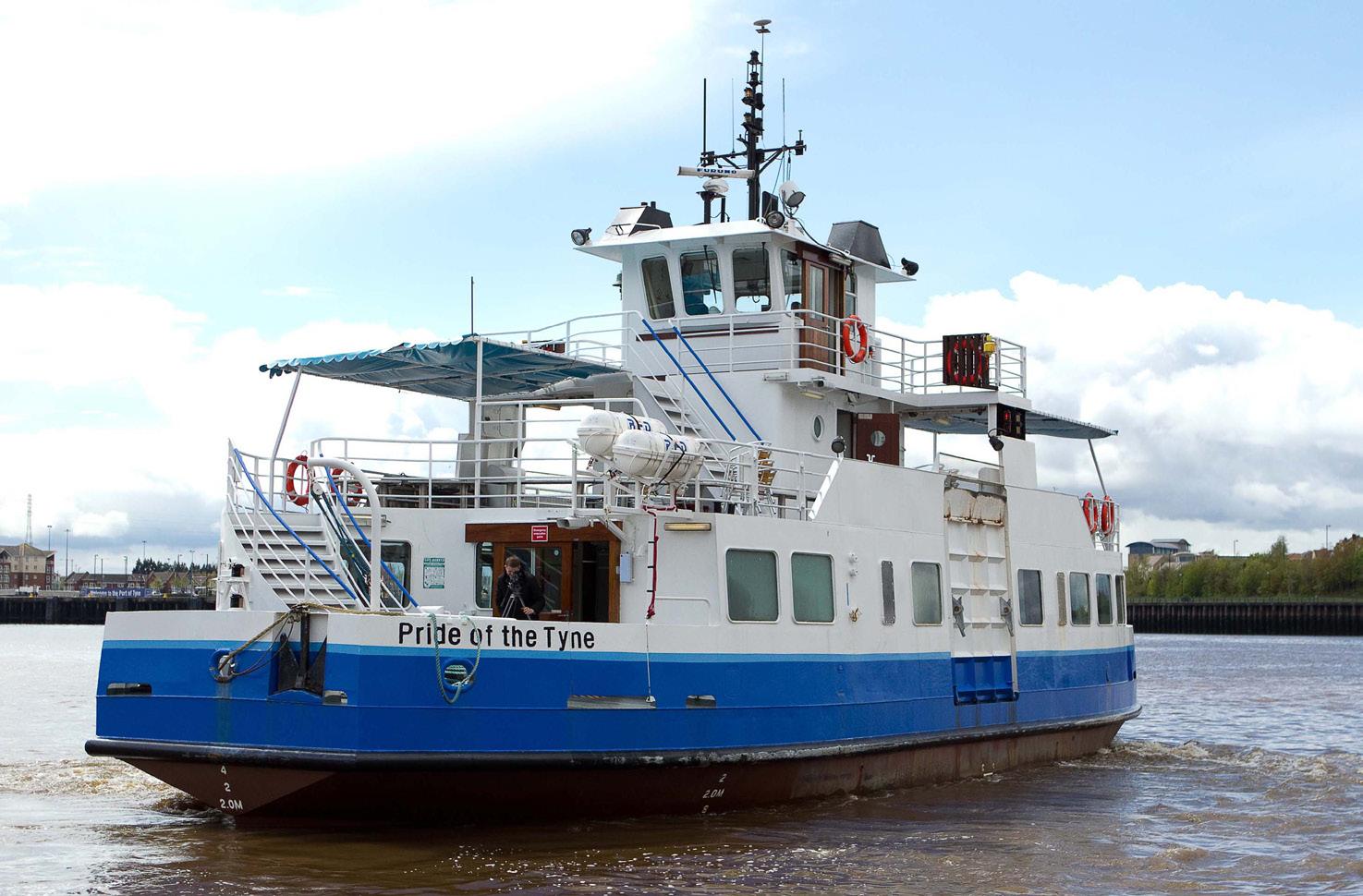
Royston is working on a project to look at ways to decarbonise the operations of the Shields Ferry service impact of compatible technical and operational solutions to cut harmful greenhouse gas emissions. This will be followed by the creation of a route map for a follow-up technology solution.
Technologies such as enginei are advanced fuel monitoring systems that can be installed as part of a suite of digital marine technologies, helping fleet owners and operators to improve the operational efficiency and energy management of their vessels. It incorporates onboard flowmeter and sensor technology, which provides the ability to acquire comprehensive real time engine and vessel performance measurements beyond the usual RPM, GPS and fuel inputs to take in a wide range of other engine control unit outputs.
The data is displayed live through a touch screen bridge display and transmitted remotely to a web portal where the interface enables the rapid production of intuitive online reports and trending graphs, as well as providing alerts and map dashboard tracking with weather overlays, showing a detailed operational profile for a vessel. SORJ